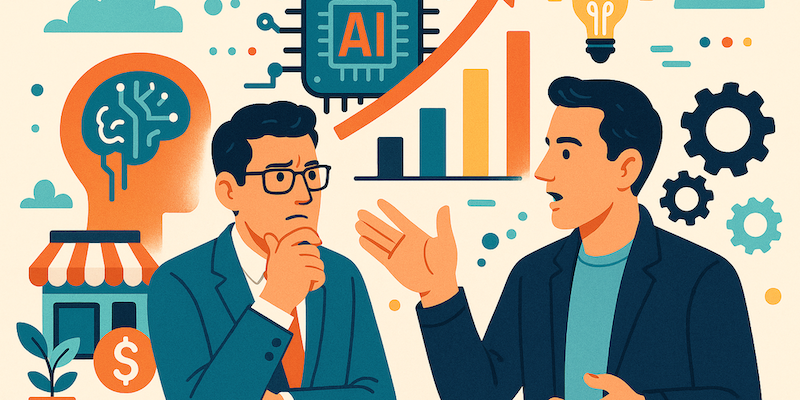
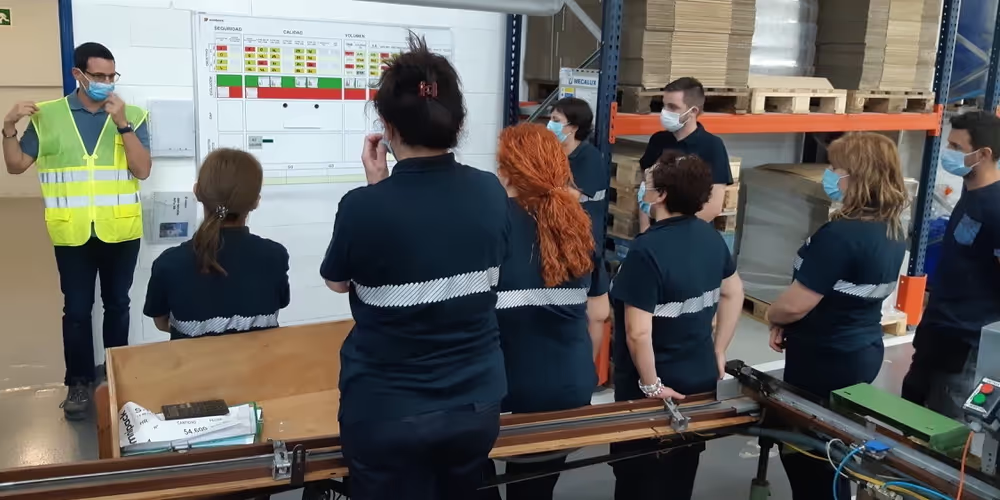
INTERVIEW – AI will shrink companies and workflows, challenging human relevance. In a world of accelerating technological disruption, Lean Thinking and adaptability are more important than ever.
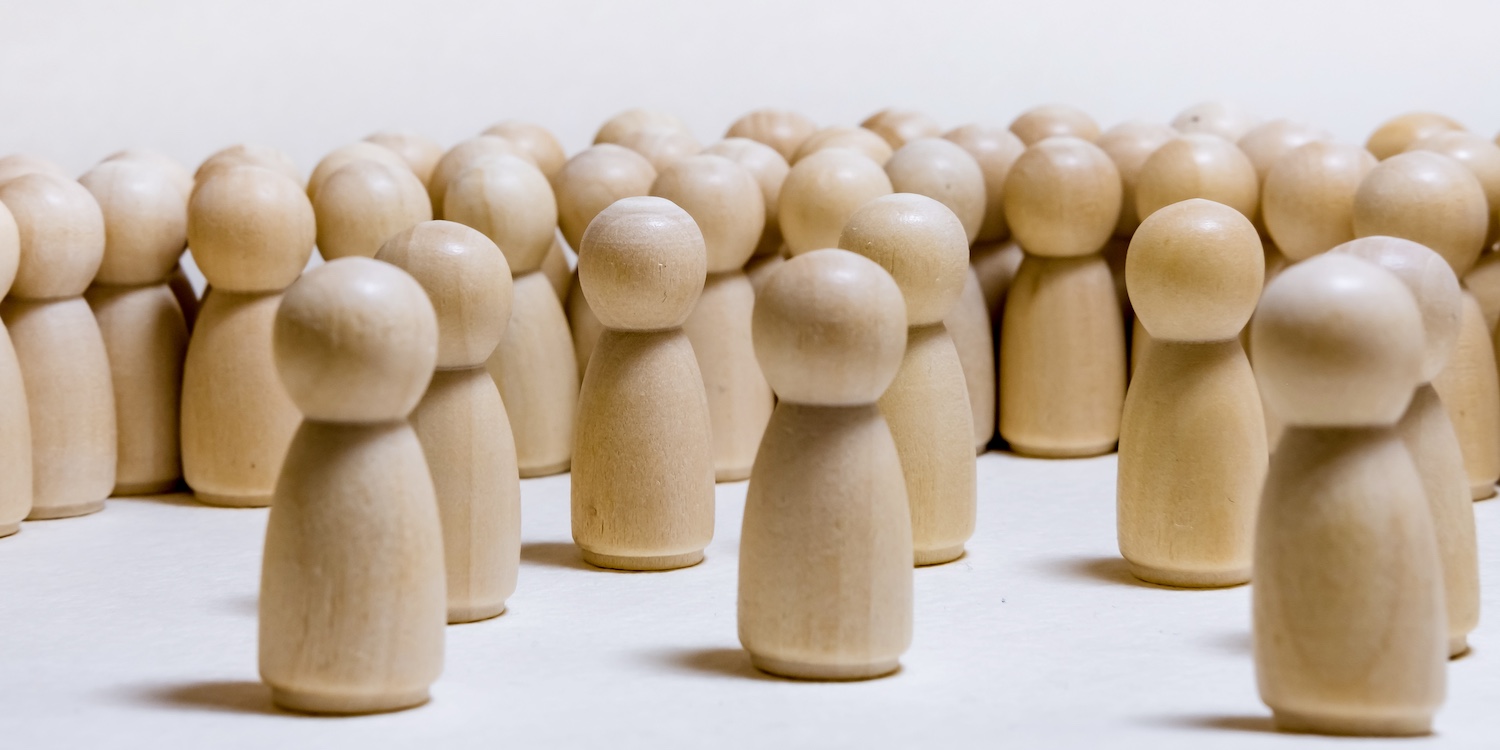
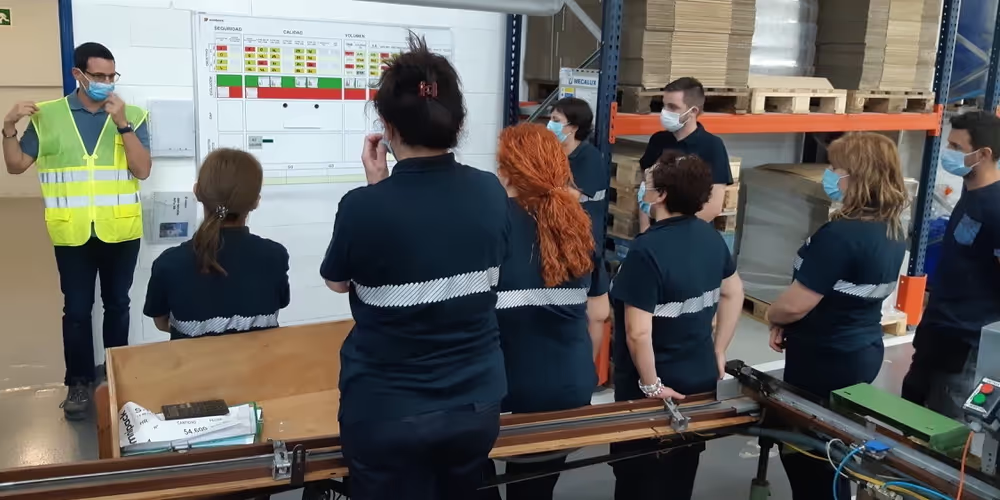
FEATURE – This student’s research confirms that lean efforts stall when culture lags. Case evidence shows fear, poor communication and top-down tools breed resistance, but participatory leadership fosters resilient lasting outcomes.
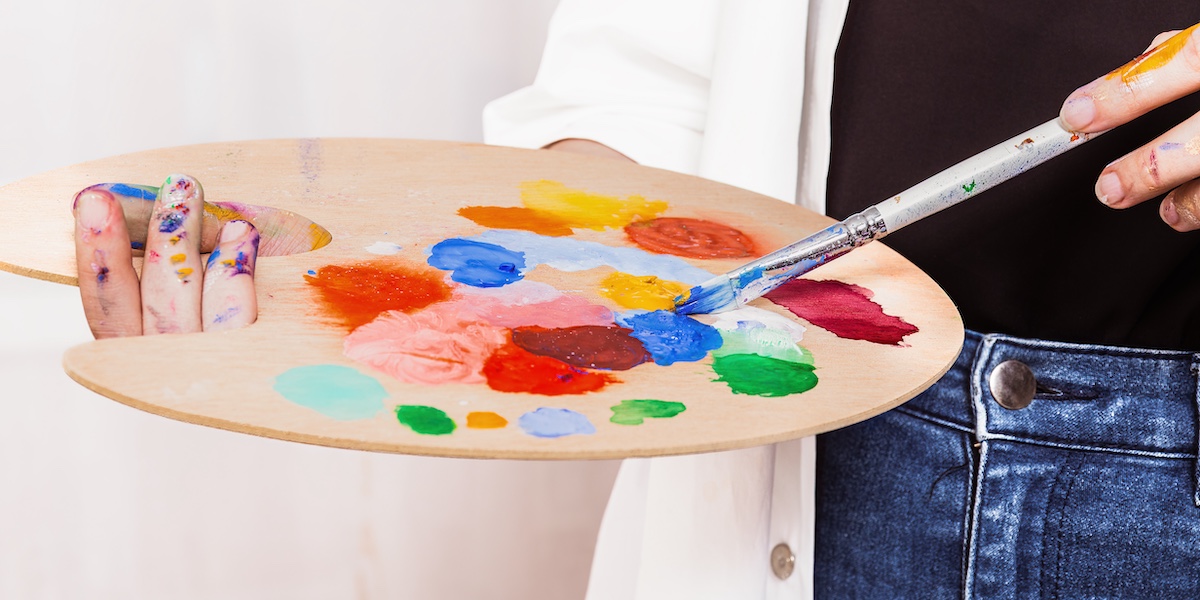
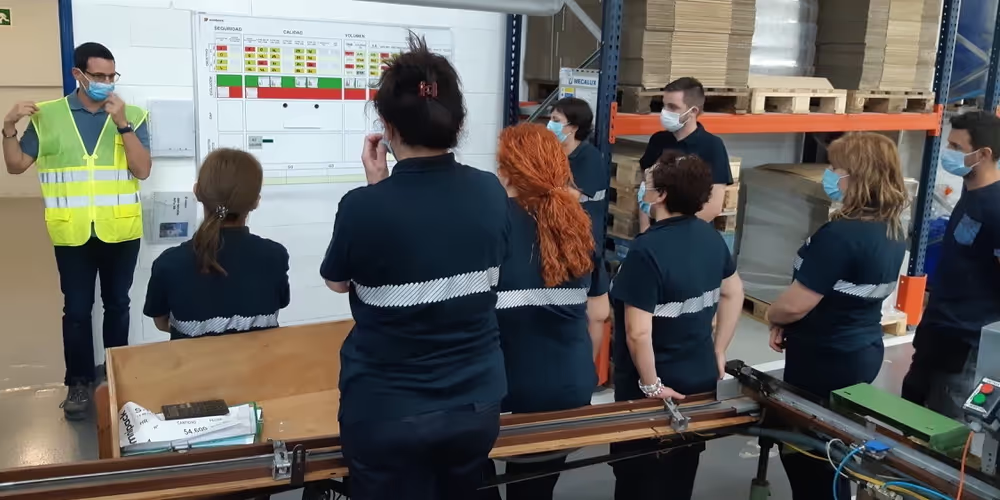
FEATURE – Embracing lean is like painting: tools are colors, respect for people is the brush, and true change blends both with intention.
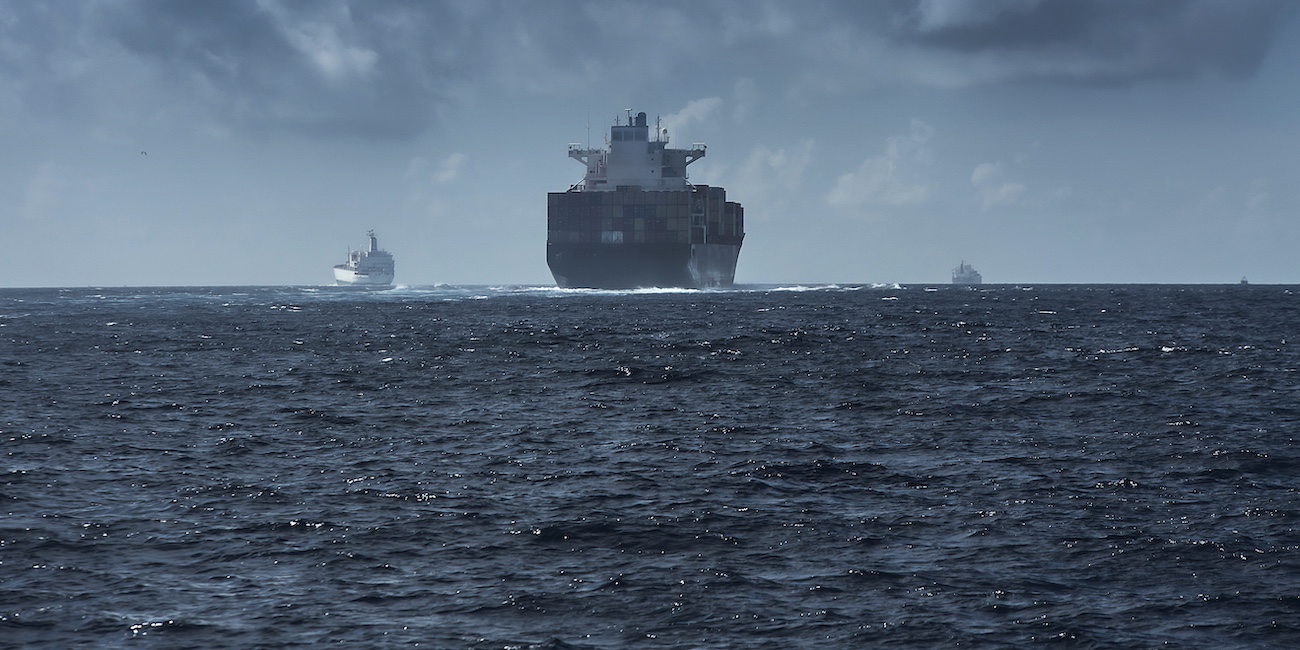
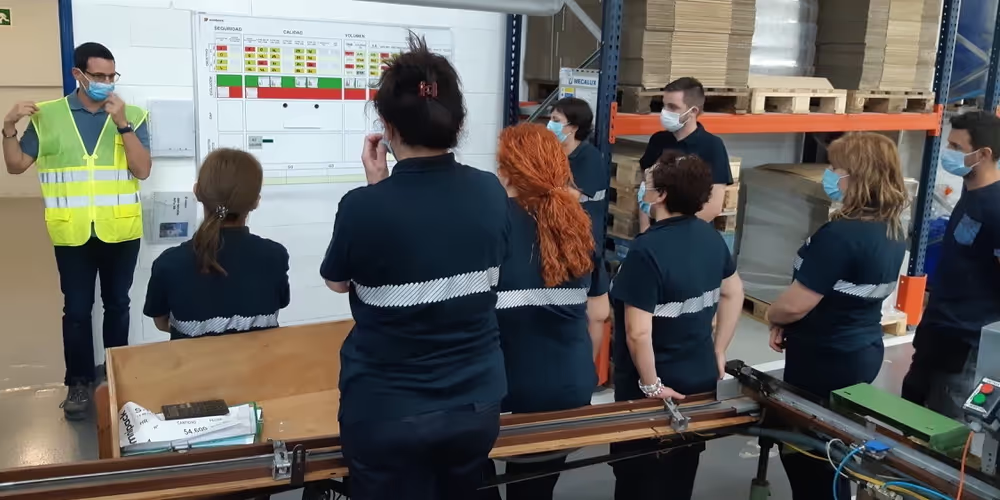
FEATURE – Lean Thinking remains vital—but must now adapt to disruption with resilience, flexibility, and human-centric systems, says the author.
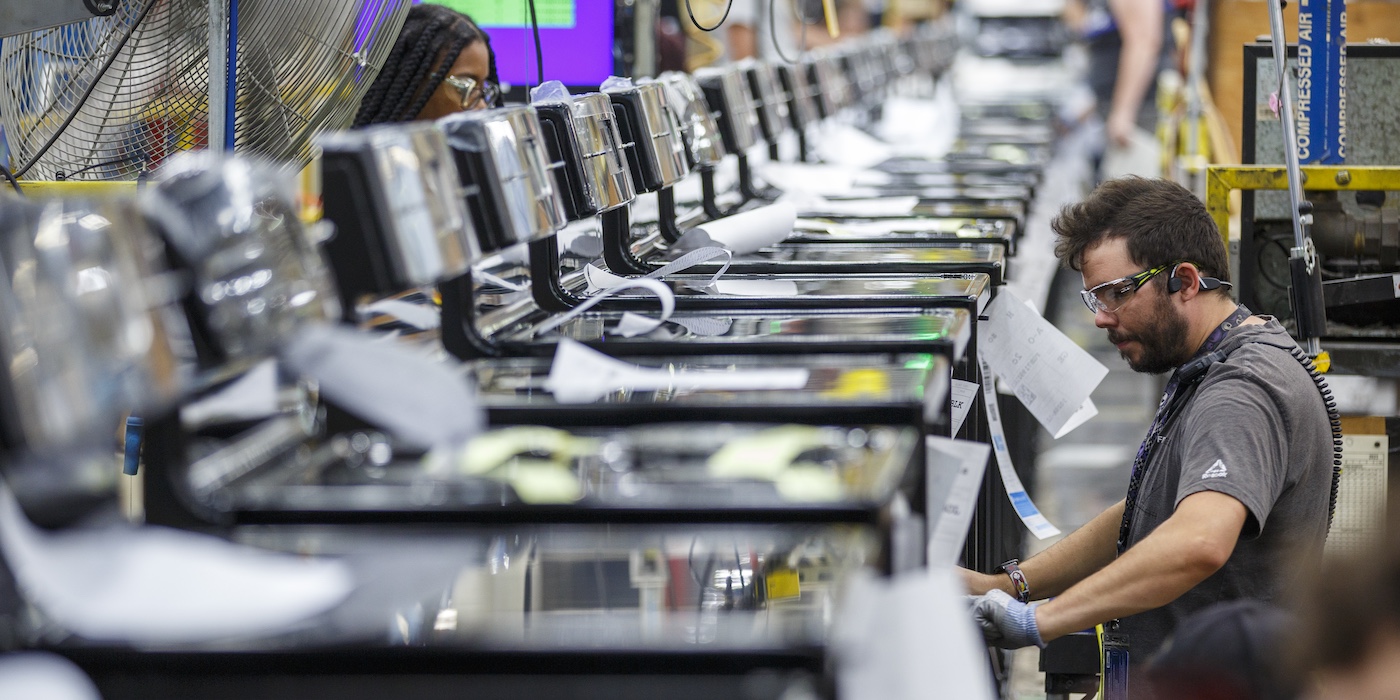
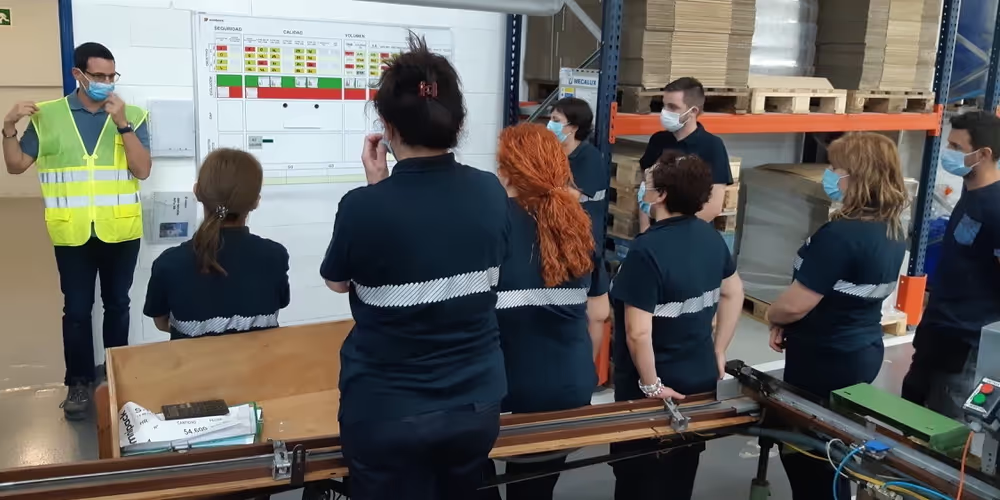
INTERVIEW – Learn how Lean Thinking helped GE Appliances improve performance, develop people, and build a resilient, customer-focused, and learning-driven organization.
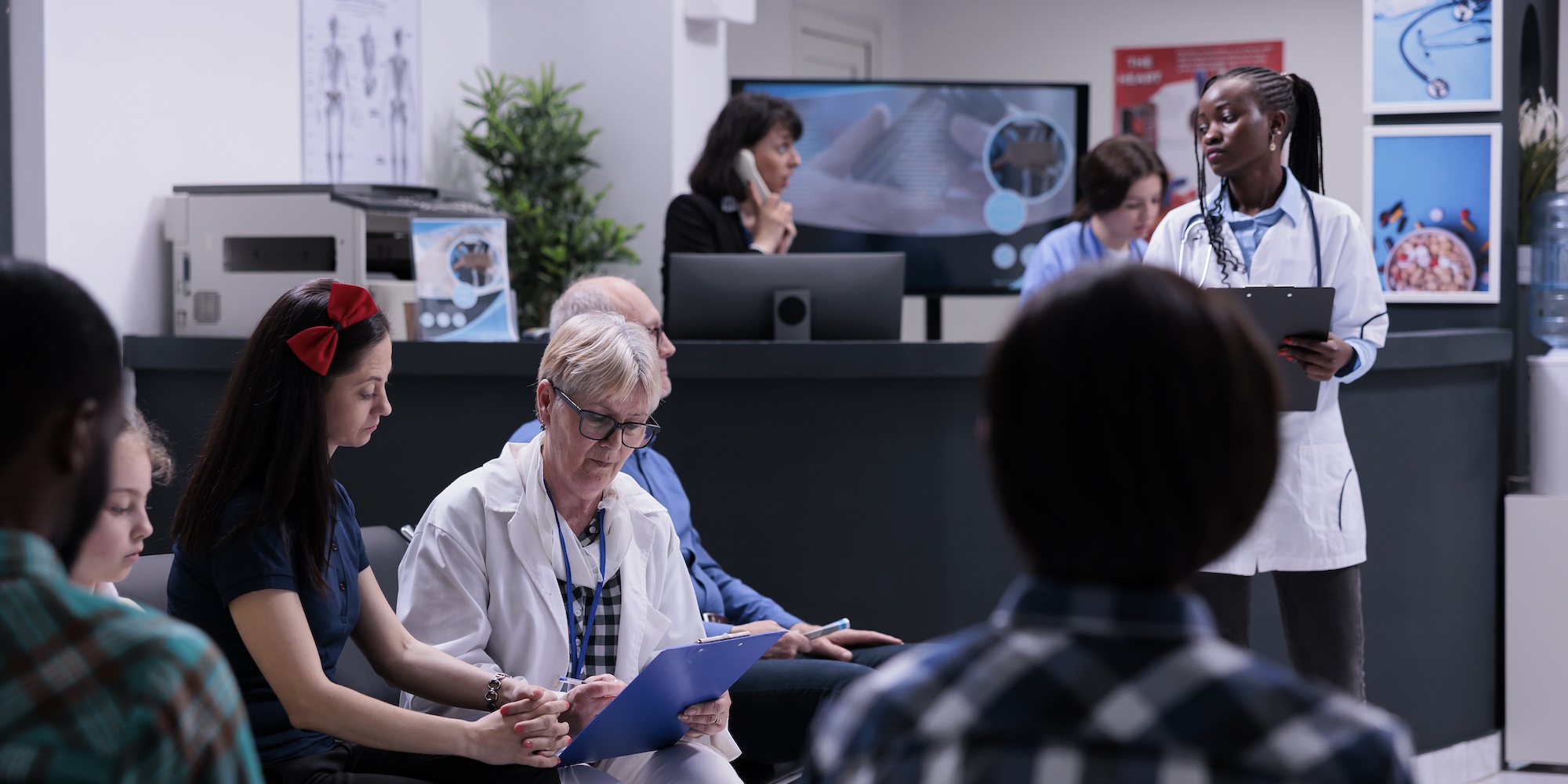
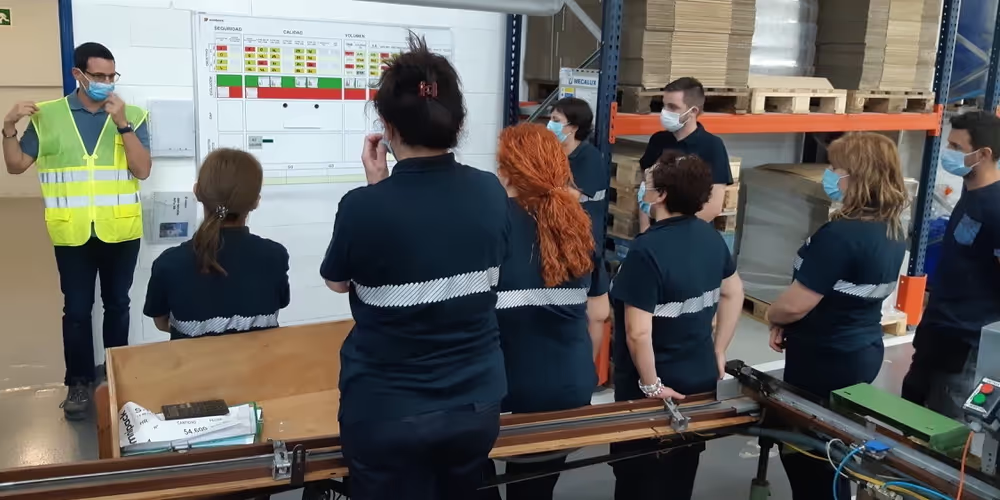
FEATURE – Many lean initiatives fail because managers lack an understanding of how adults learn. The authors discuss why execs need clear strategies that link improvement efforts to human capital development.
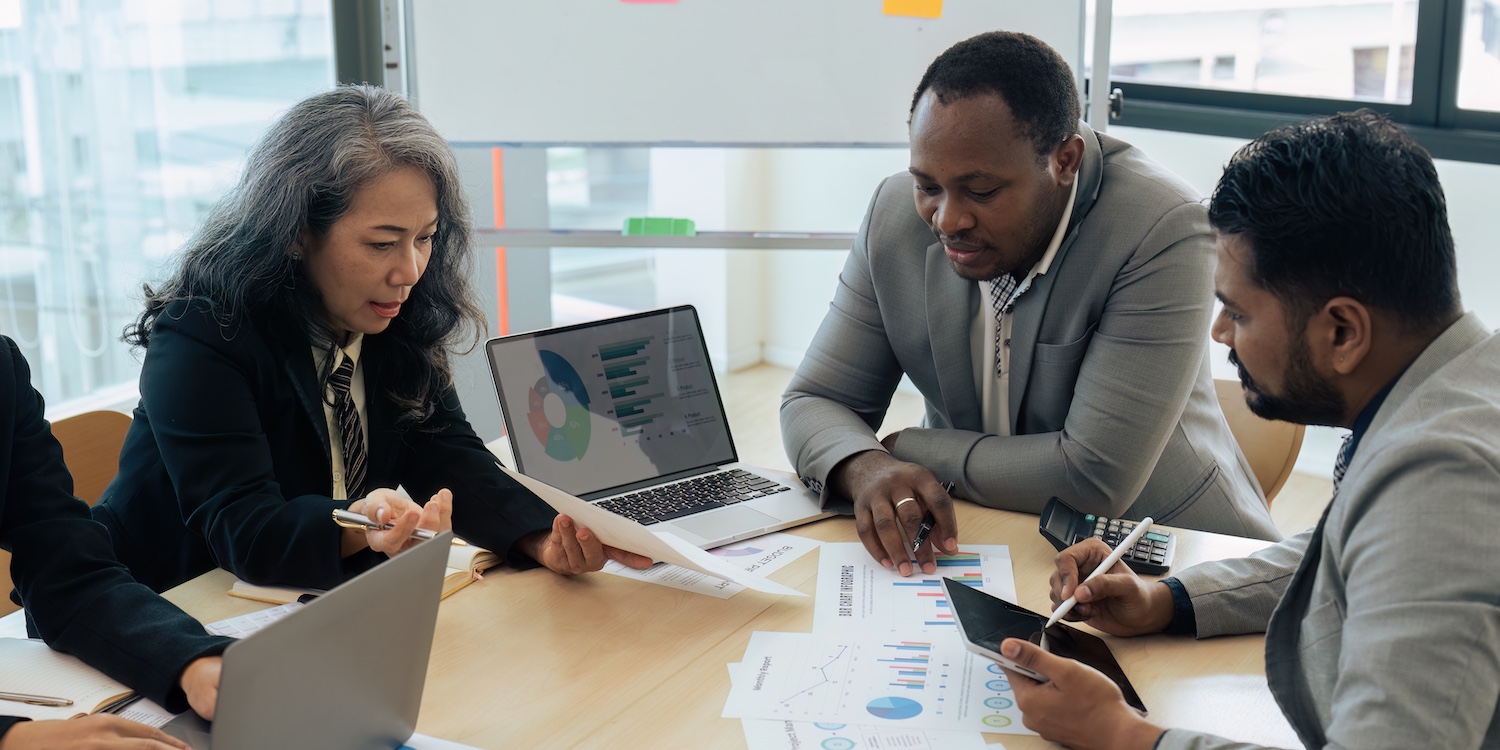
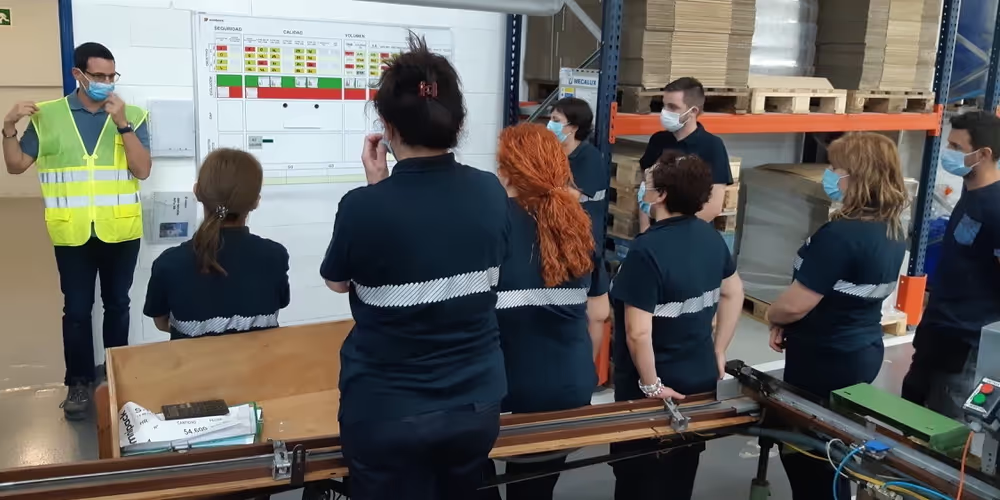
CASE STUDY – The story of improvement at China-based asset management company Hengbaishi is a great reminder of the universality of lean principles.
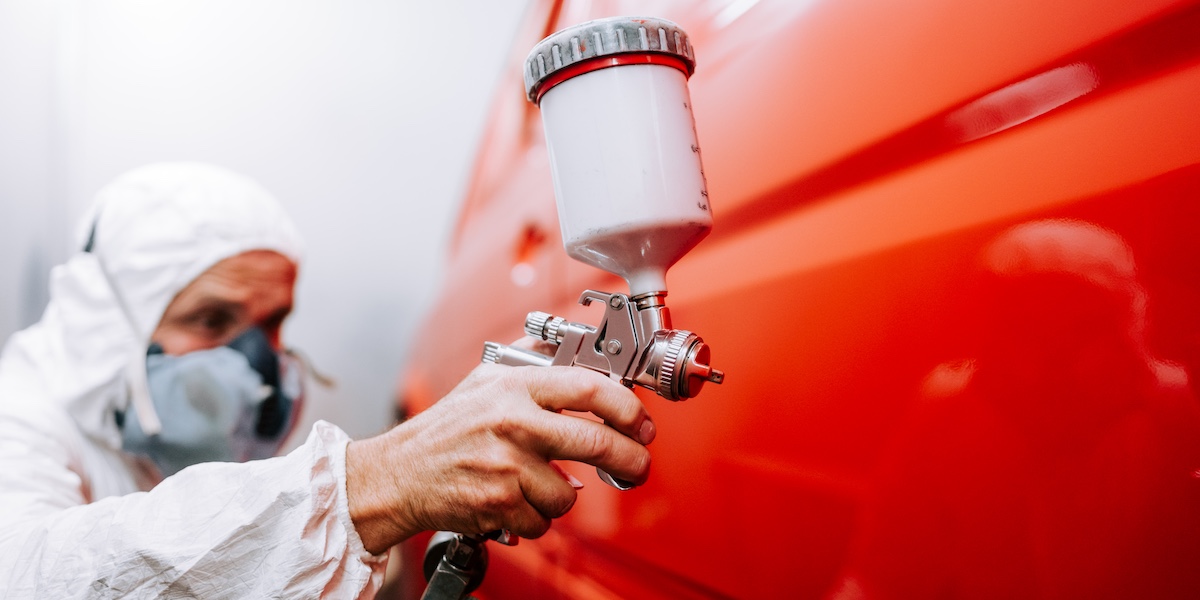
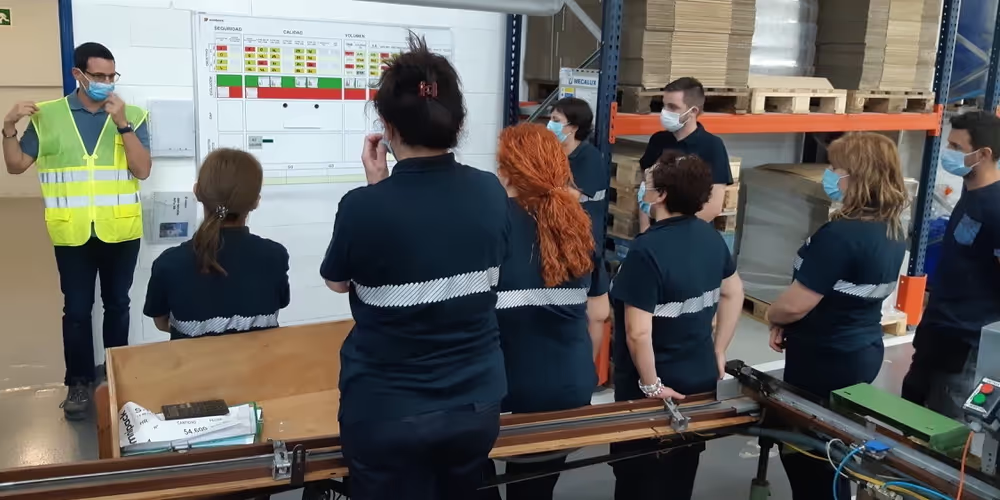
FEATURE – Collaboration with suppliers, rather than a merely transactional relationship, has to power to transform a company’s operations, fostering innovation and building resilience.
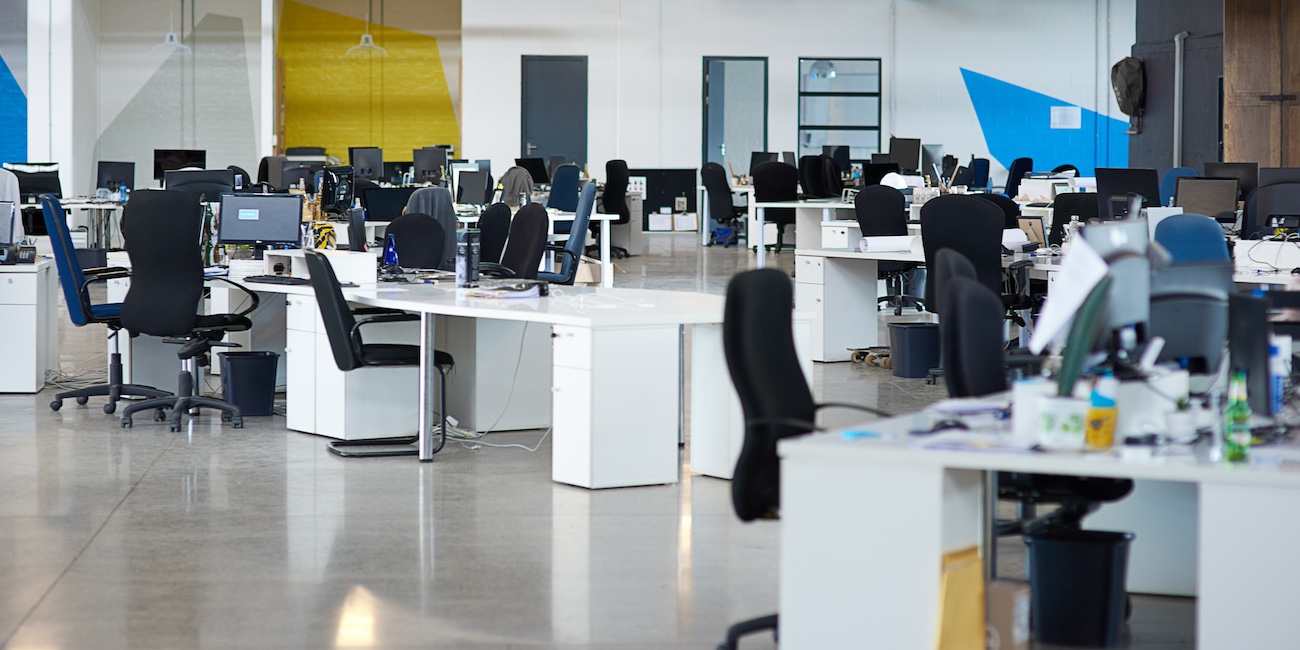
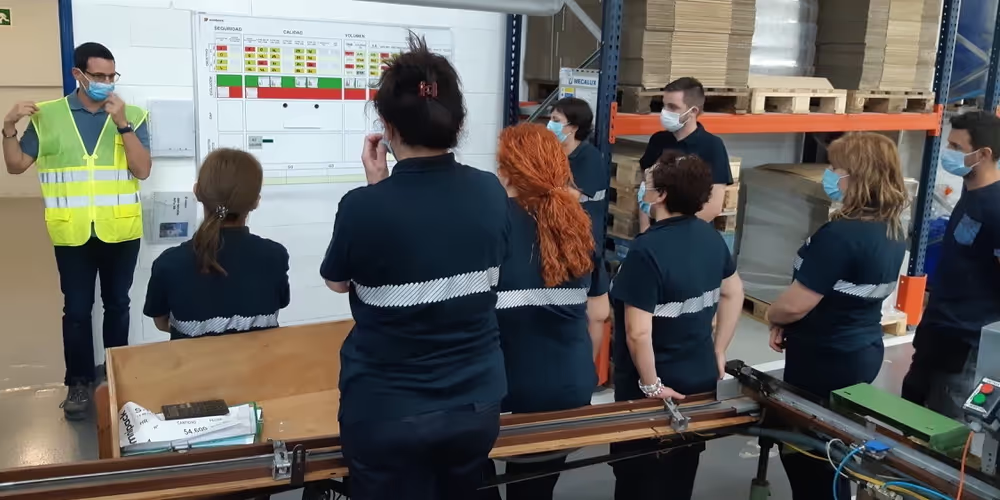
FEATURE – Attracting, developing and retaining talent has become a pressing issue in the corporate world, as new generations show skepticism towards traditional management. Lean is the answer, say the authors.
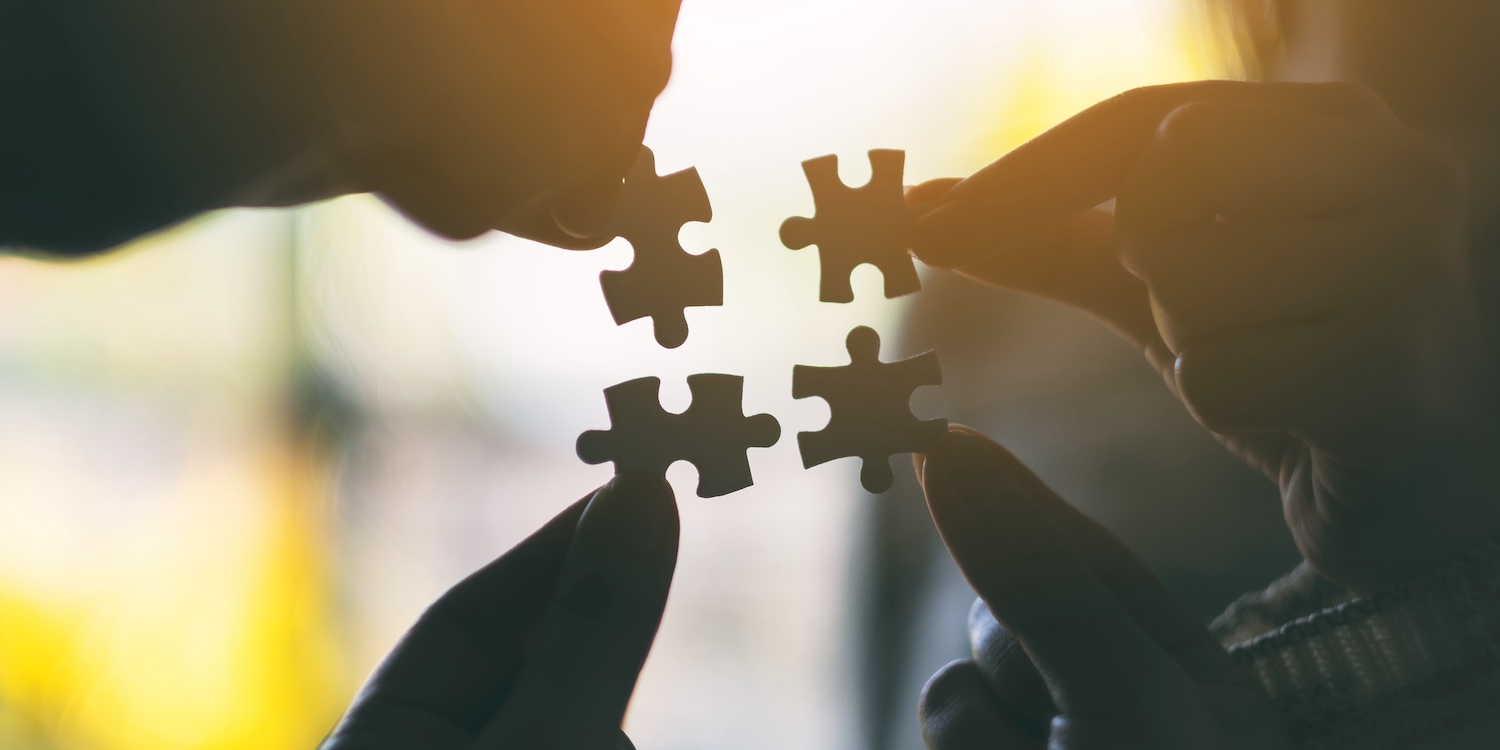
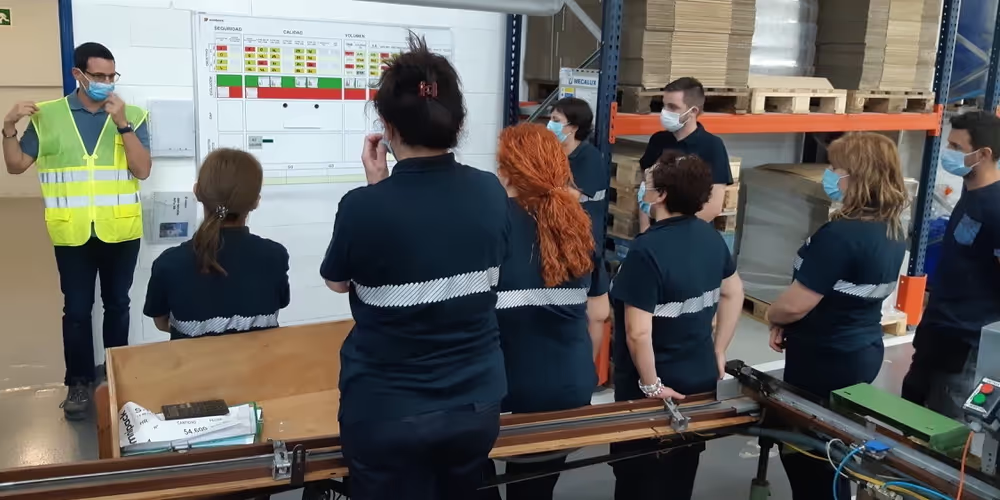
FEATURE – To boost the “adoptability” of Lean and sustain it over time, it’s necessary to develop institutions that support our improvement efforts without making processes more bureaucratic.
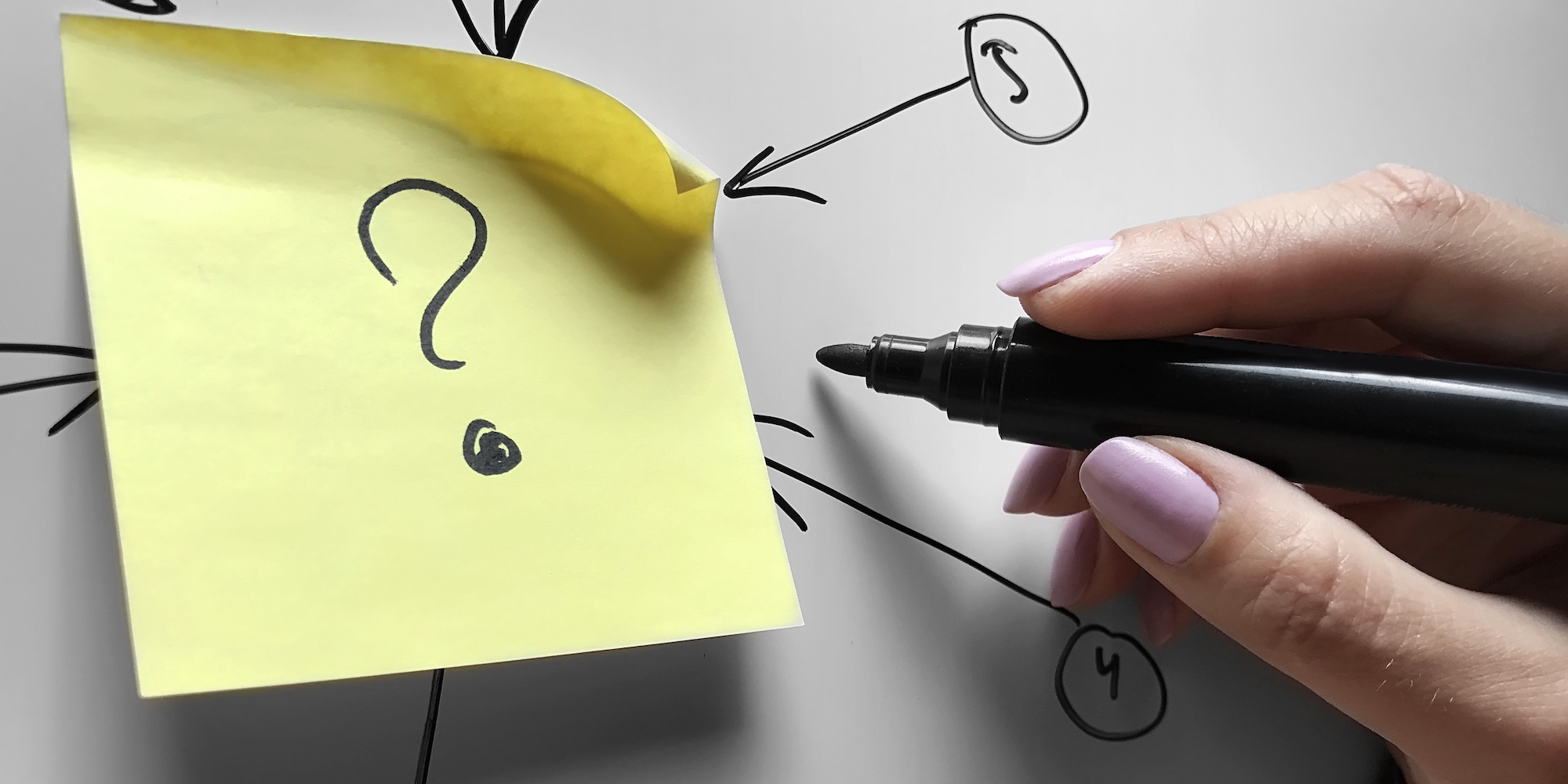
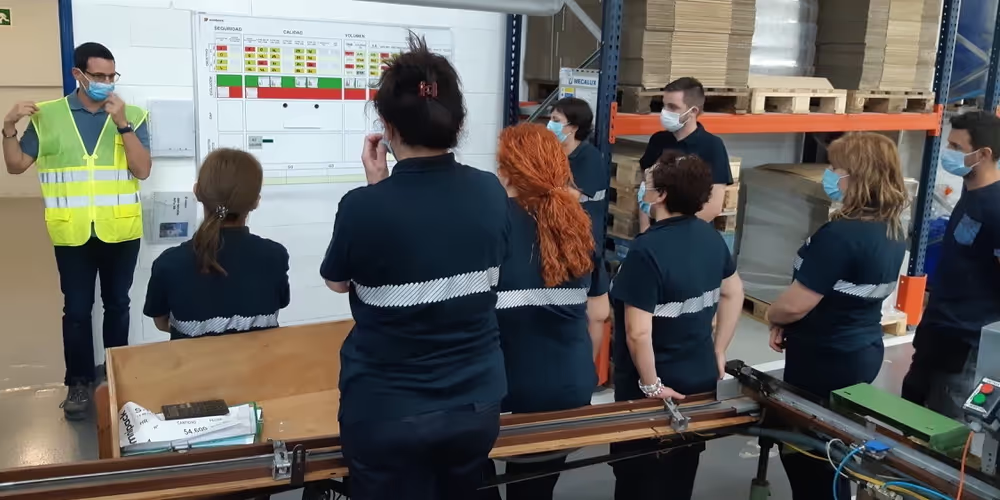
FEATURE – In this new series, the author taps into LEI Hungary’s experience with lean transformations to highlight the most common mistakes people make when approaching the A3 framework.
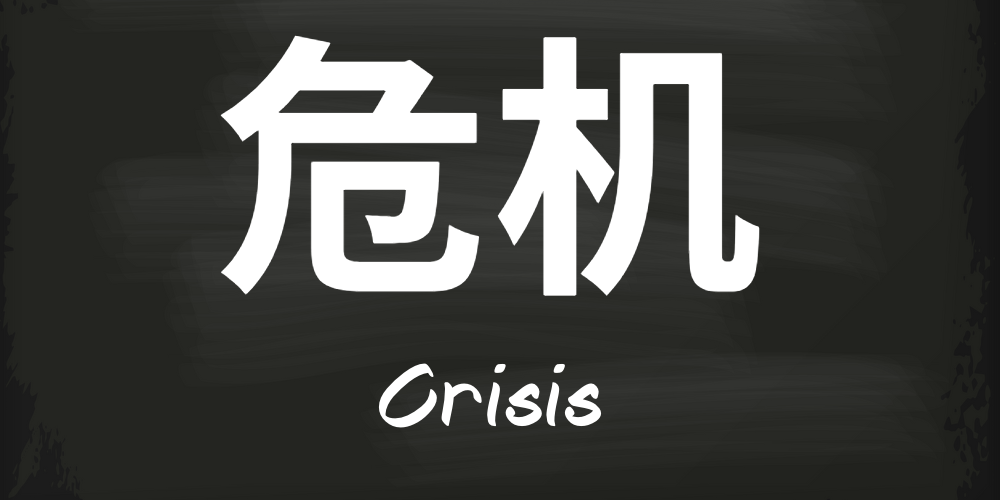
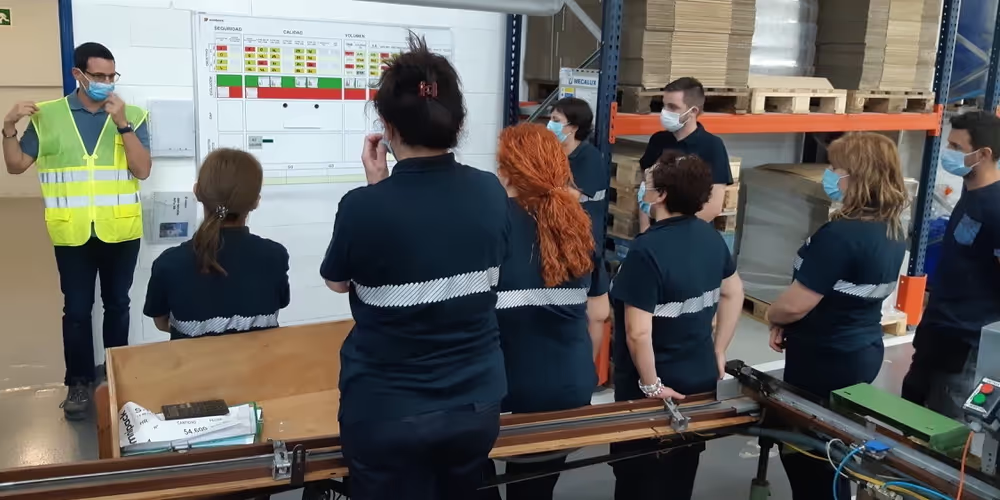
FEATURE – In this article, Michael discusses the four levers that organizations can work on to thrive in good times… and bad times.
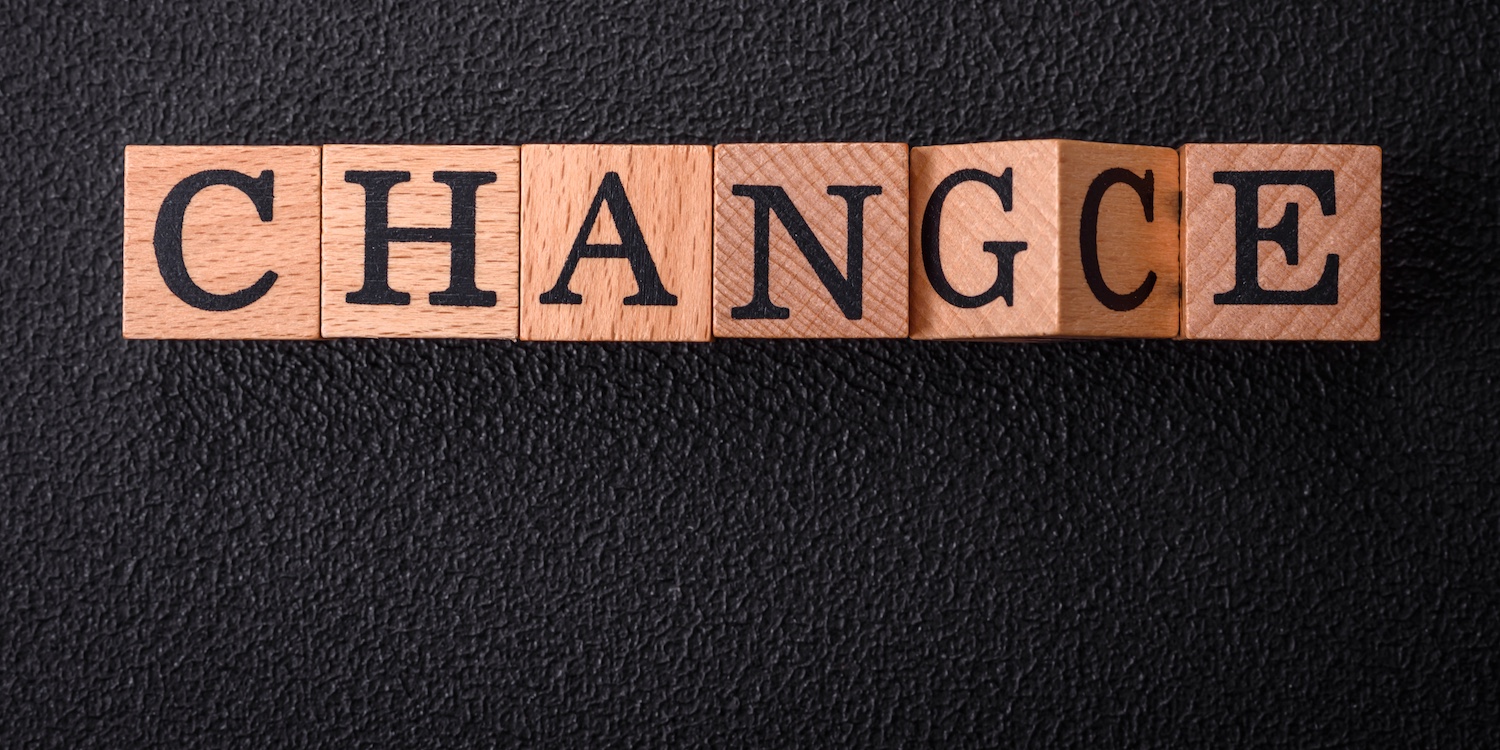
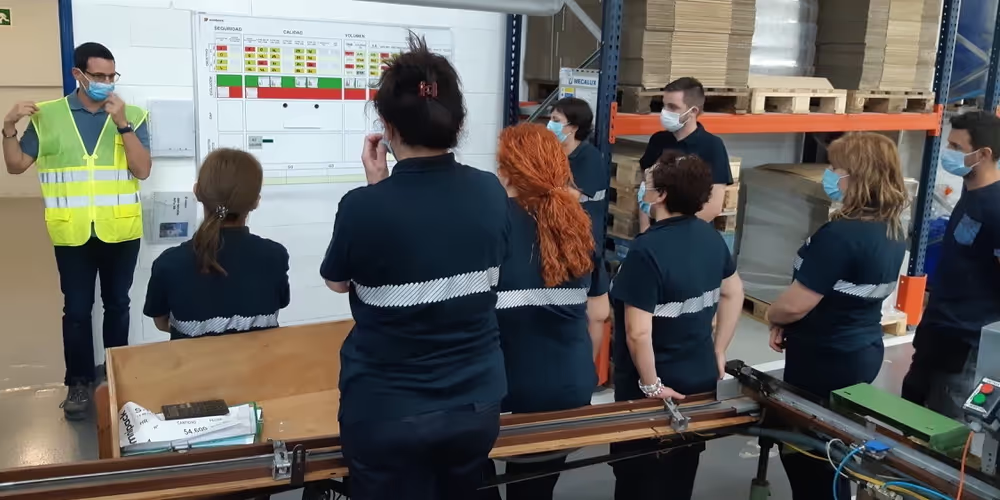
FEATURE – Ahead of his presentation at next week’s Lean Global Connection, Jim Womack explains why Lean is made for a world in turmoil but urges us to strike a balance between immediate response and thorough understanding of the problem.
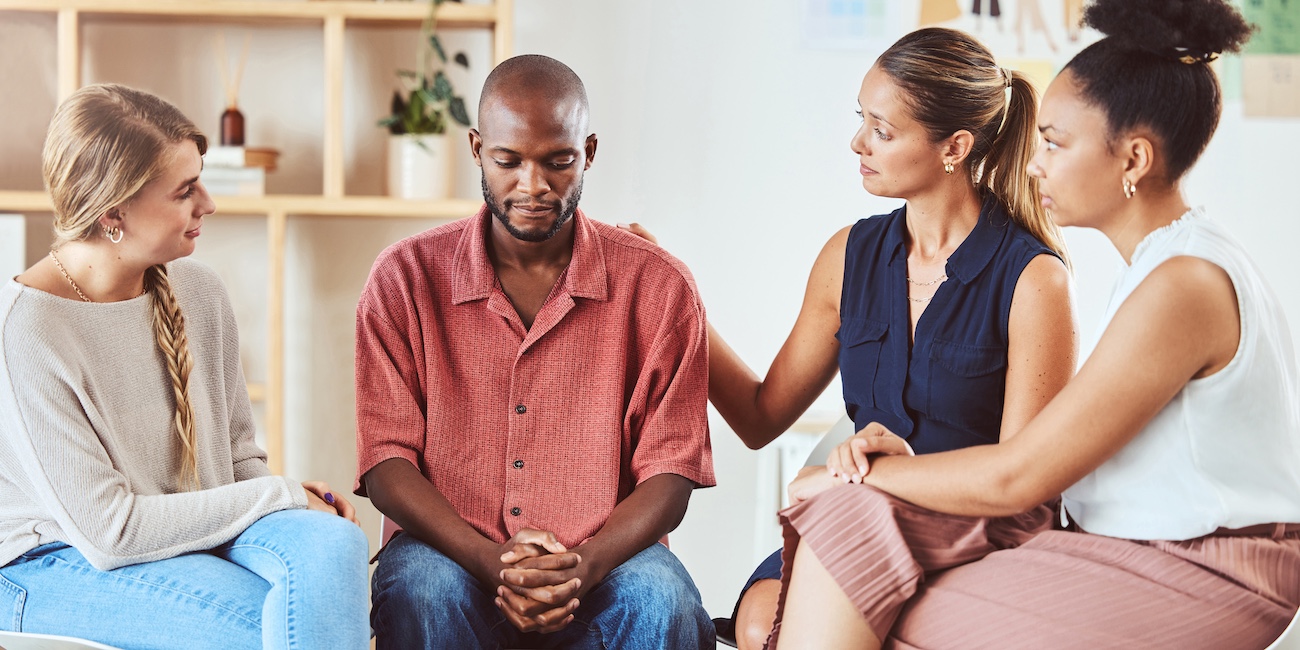
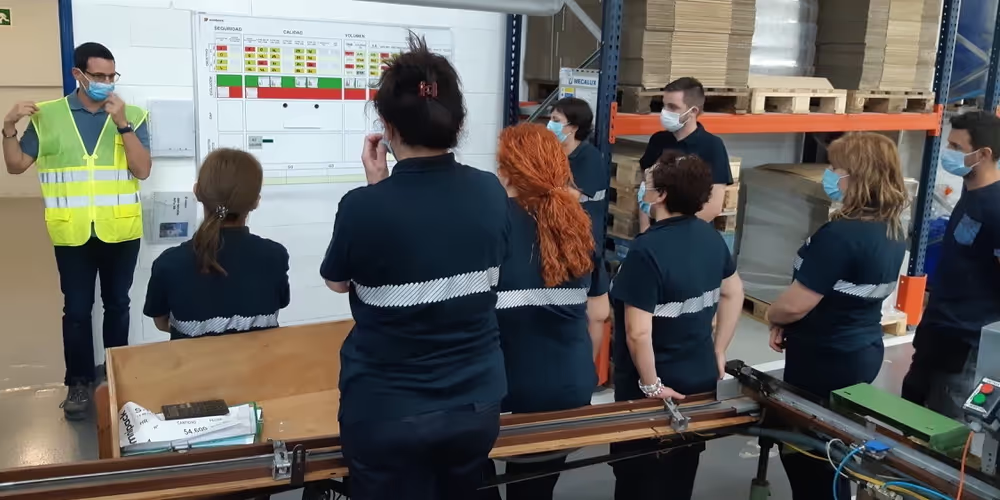
FEATURE – What is psychological safety? What is it not? This article explores its advantages and foundational elements, and how organizations need to transform their leadership to achieve this evolution in management.
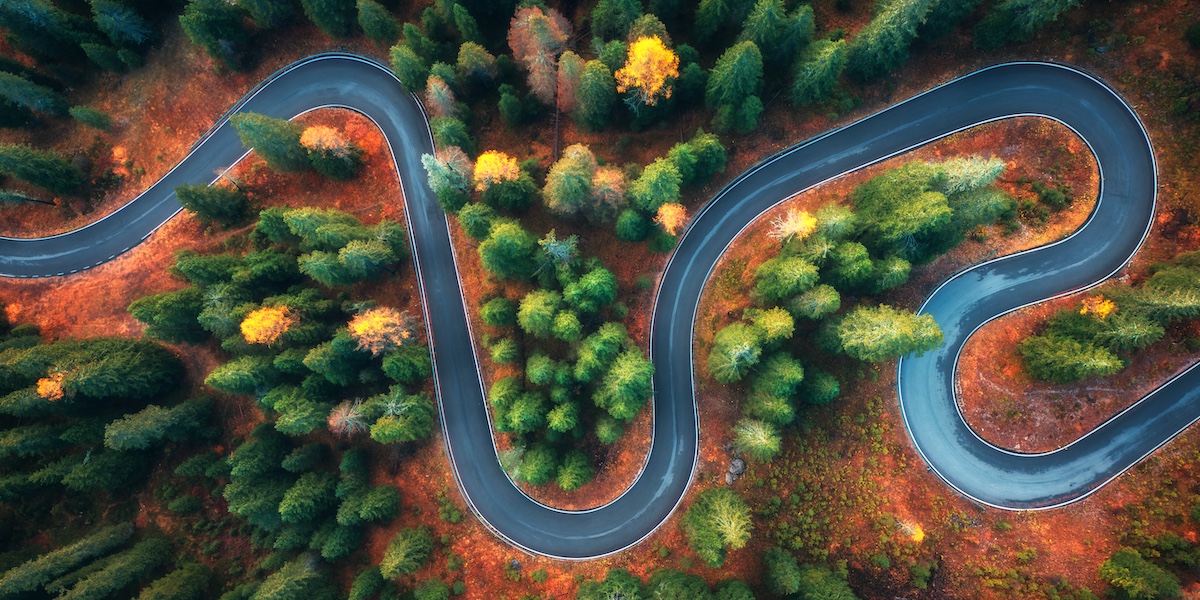
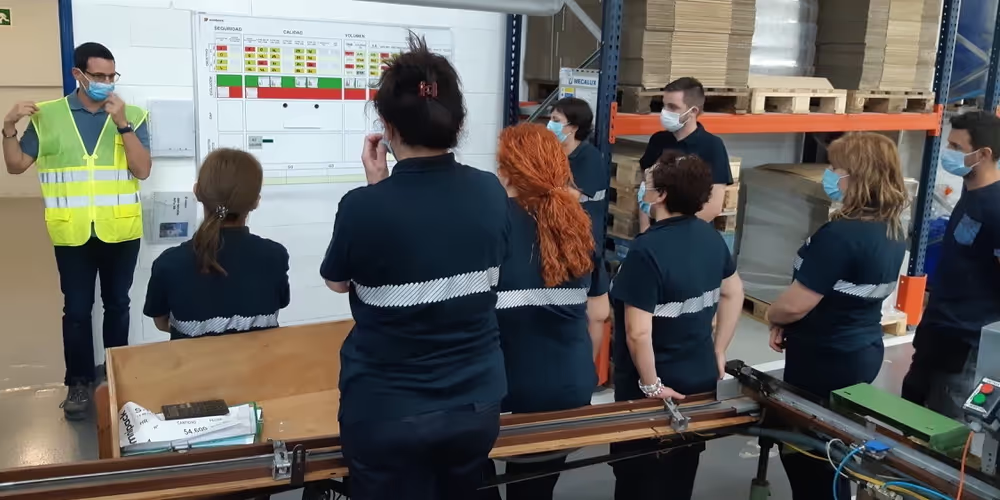
FEATURE - Projects or programs? The authors discuss why Lean Thinking should go beyond piecemeal operational improvements, as a transformative strategy that balances today’s demands with future adaptiveness.
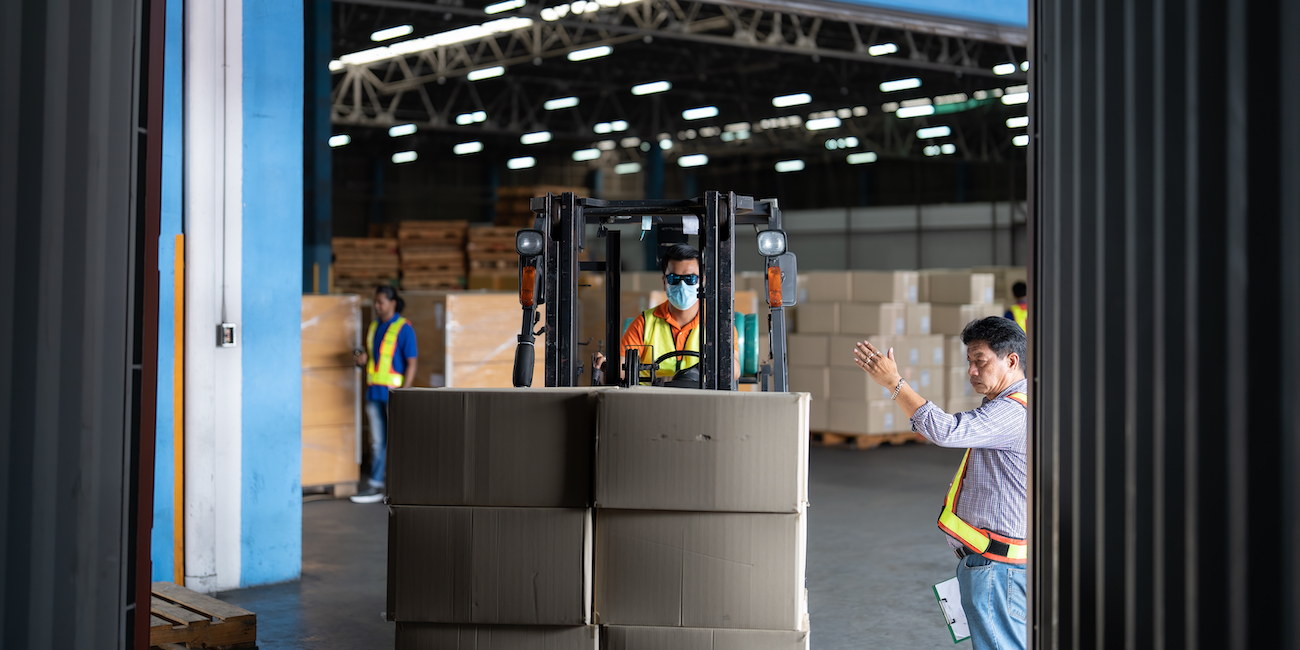
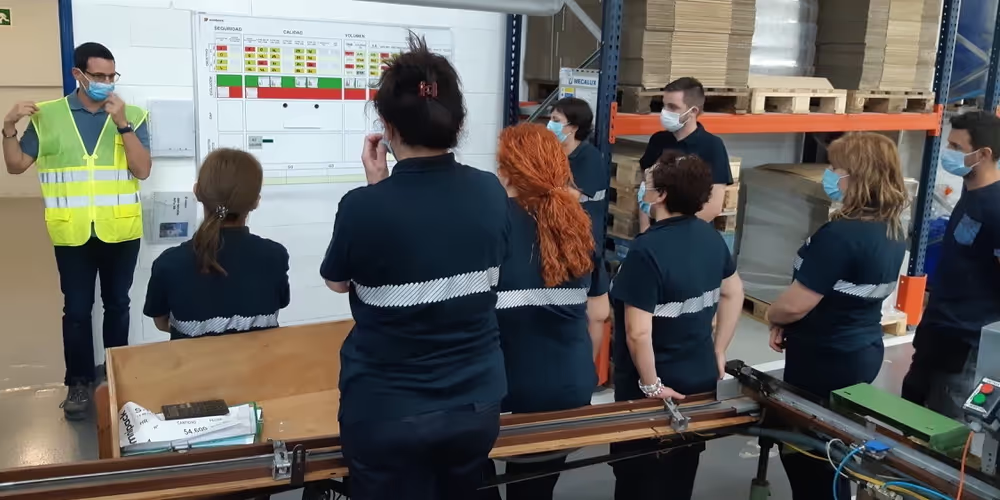
FEATURE – There is more to logistics than an ancillary process that supports the rest of the company. But then, why do we never have a plan for it, like we do for manufacturing?
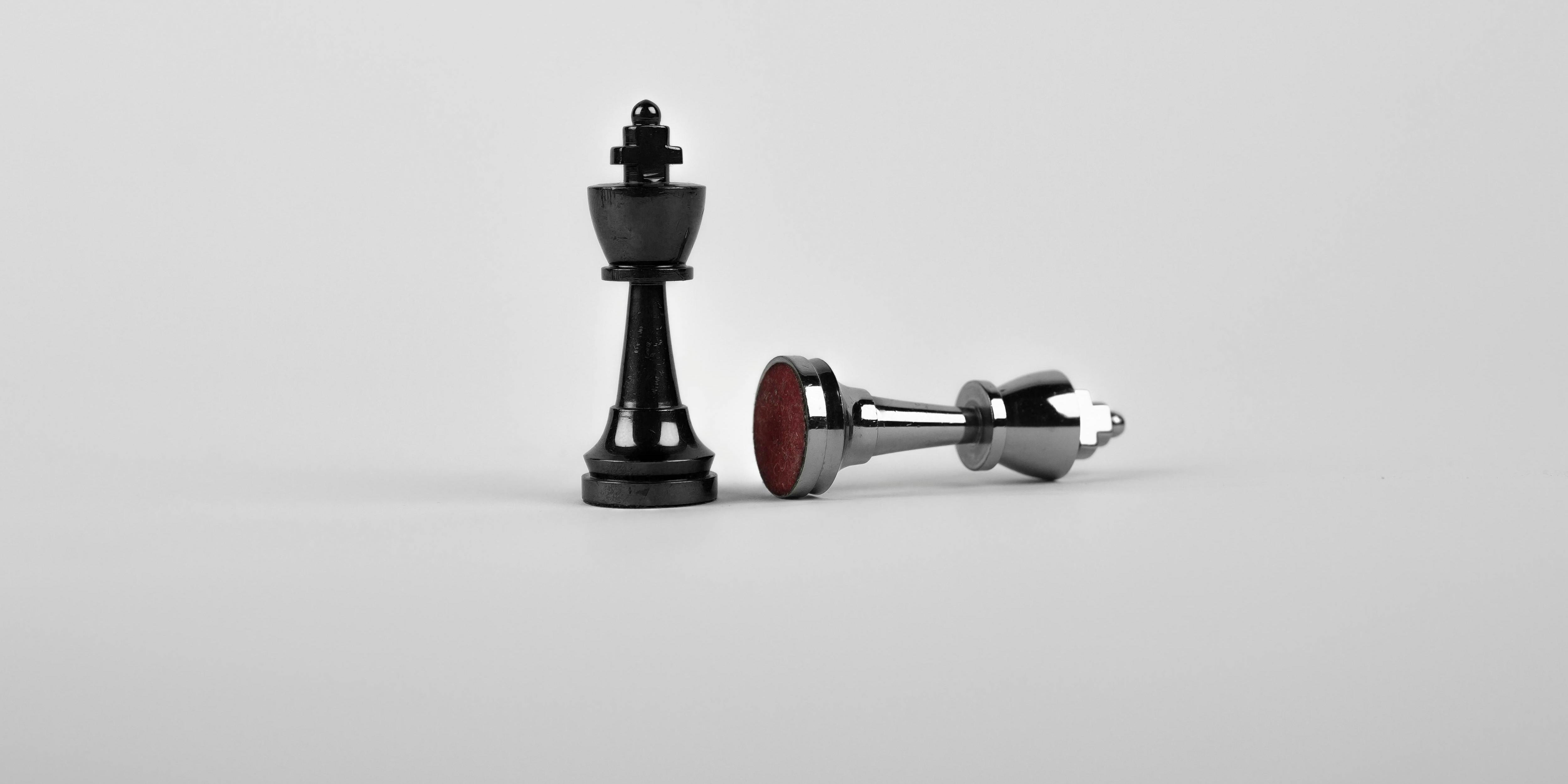
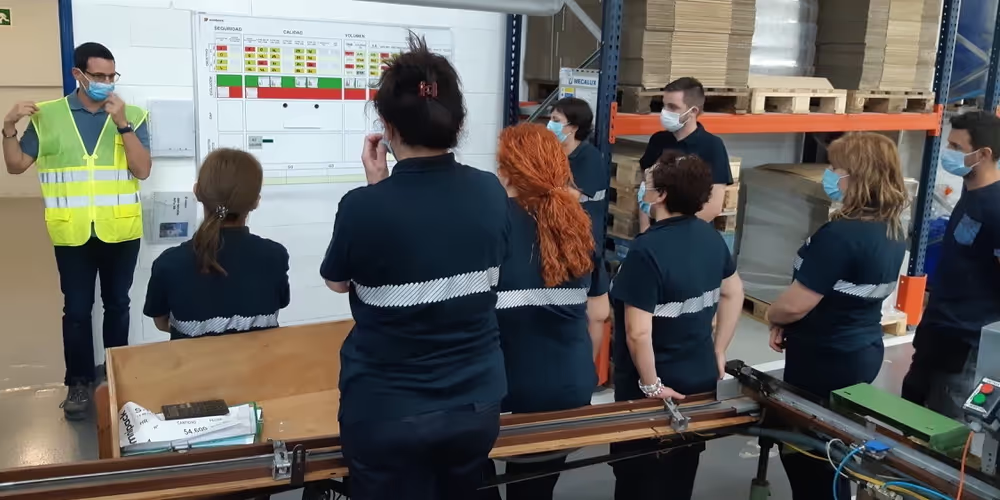
FEATURE – To successfully transform, we need to change our “theory of success”. The authors discuss the obstacles managers face along the way.
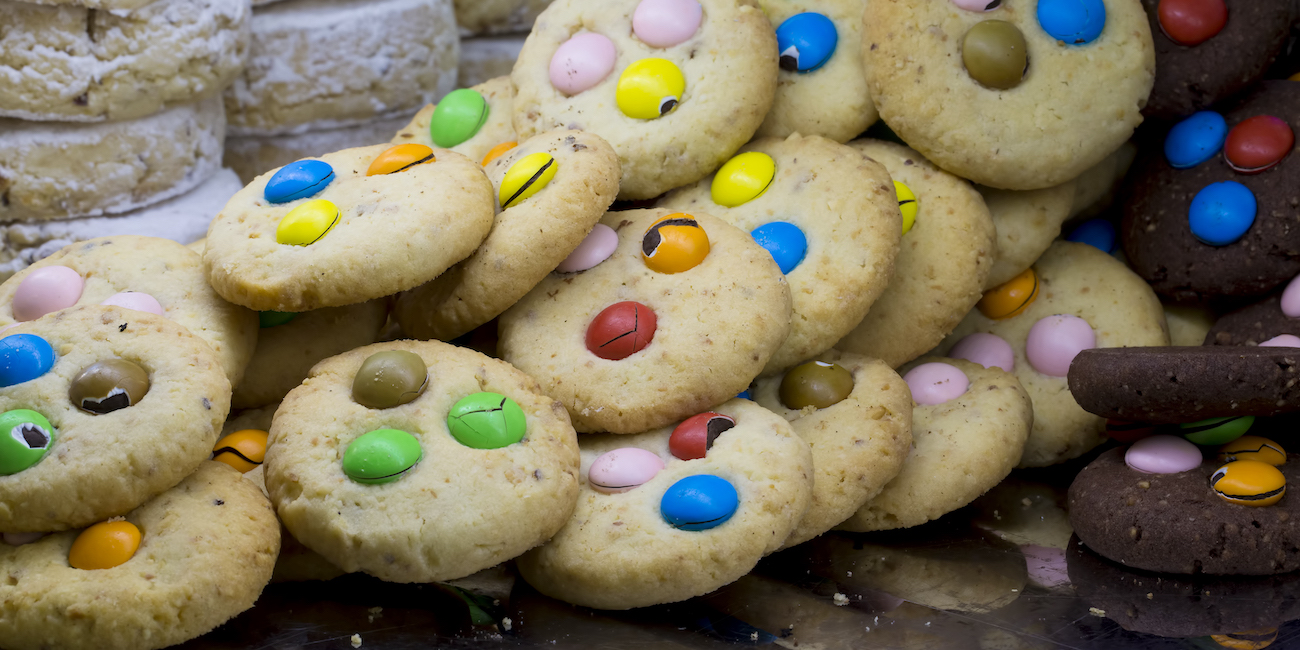
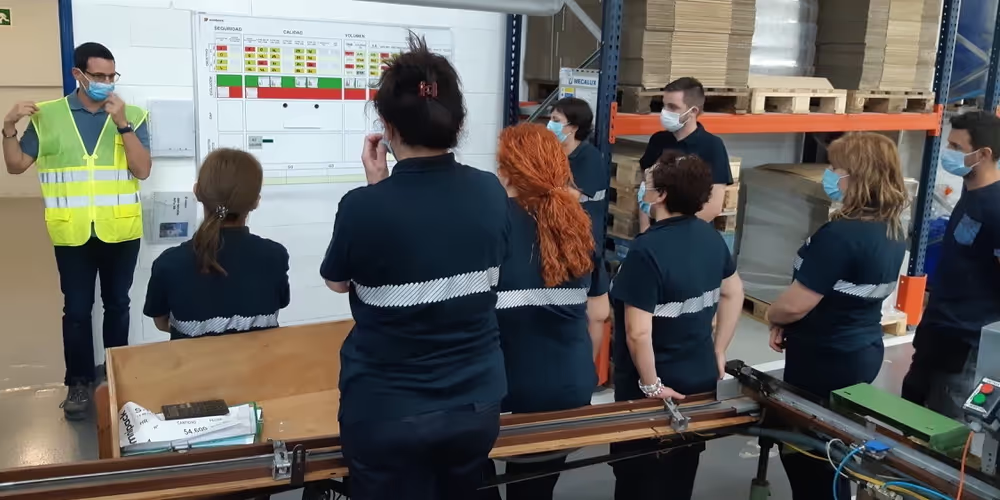
FEATURE – The successful project discussed in this article shows how Lean Thinking can bring huge benefits to small and medium enterprises and paves the way to a new way of looking at lean coaching.
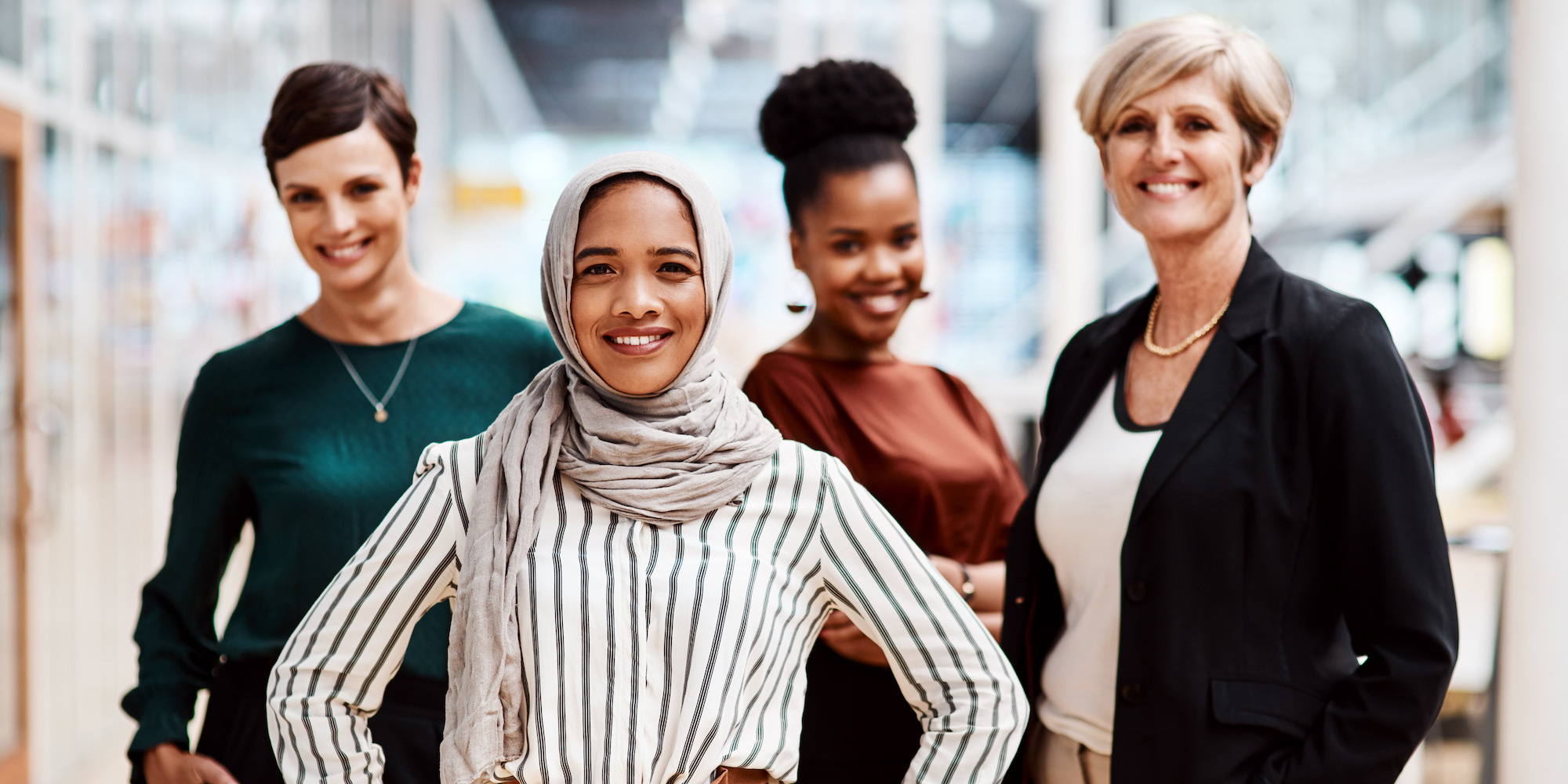
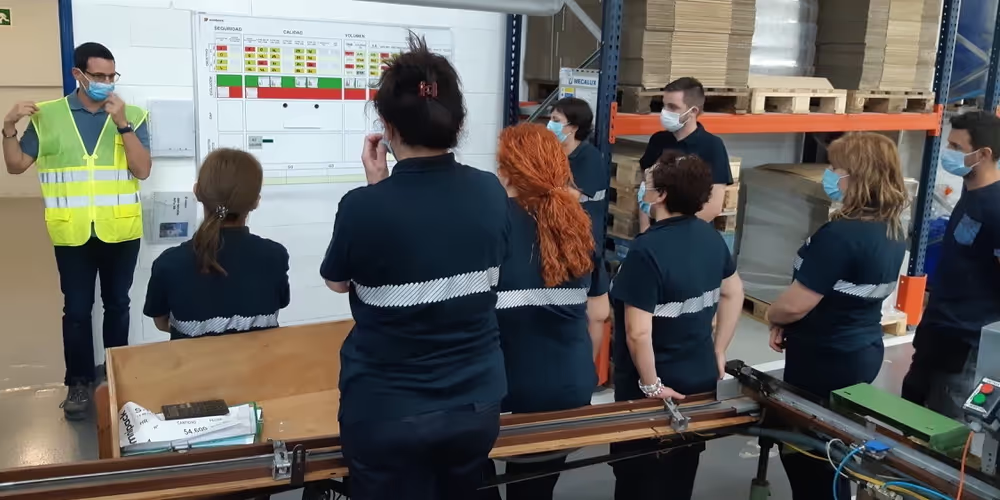
FEATURE – This article applauds the tenacity of women leaders and seeks to illustrate how they motivate others to take on the sustainability challenge through lean practices.
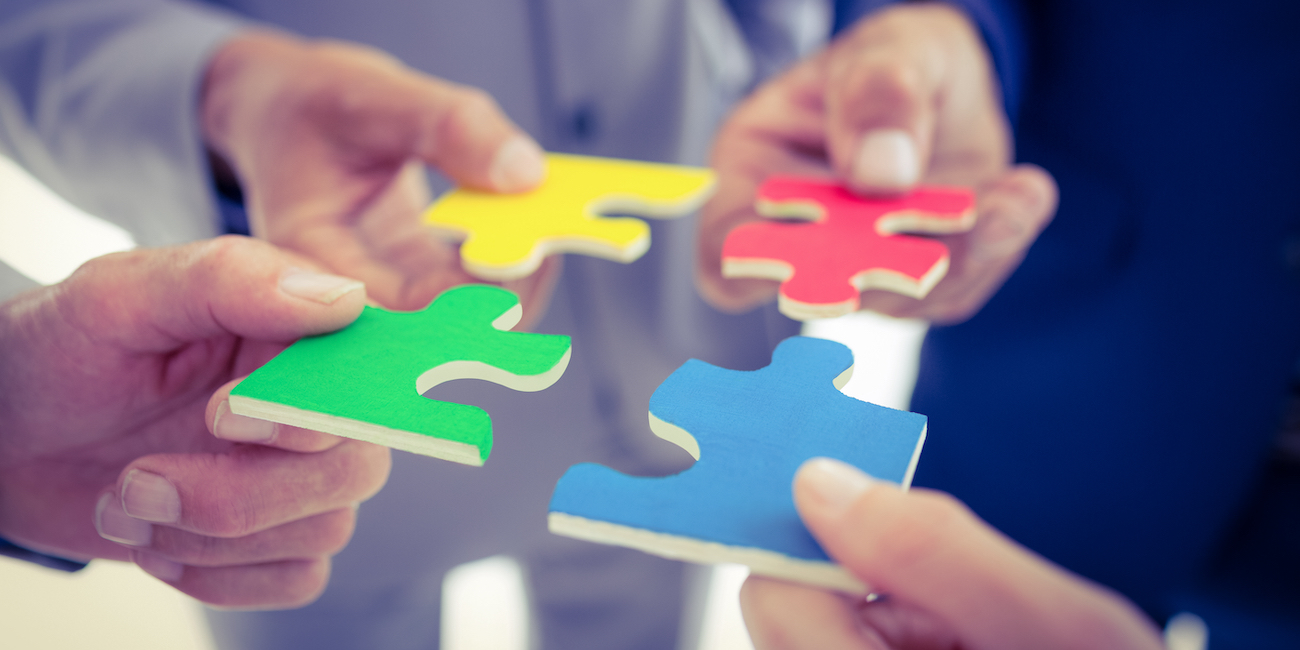
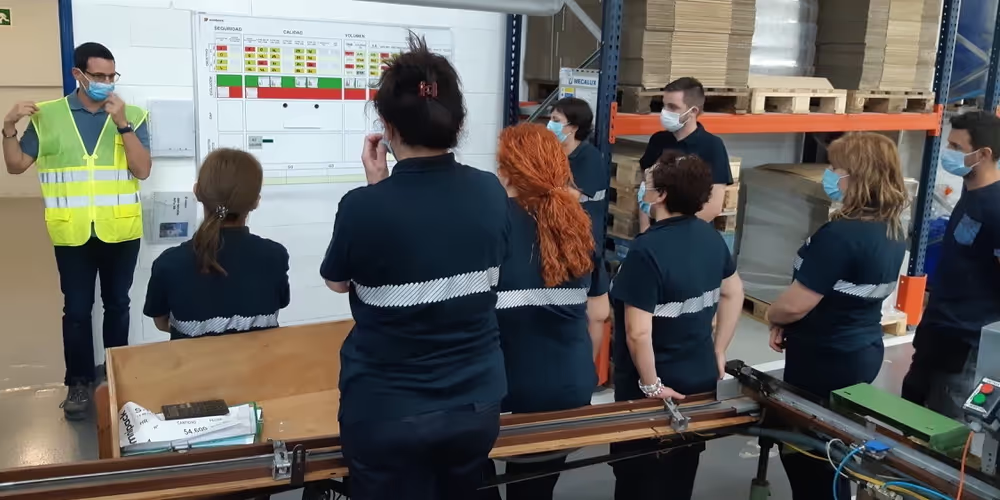
FEATURE – In an excerpt from his new book, the author discusses the importance of building collaboration in your teams and explains why this is the only way to consistently deliver value.
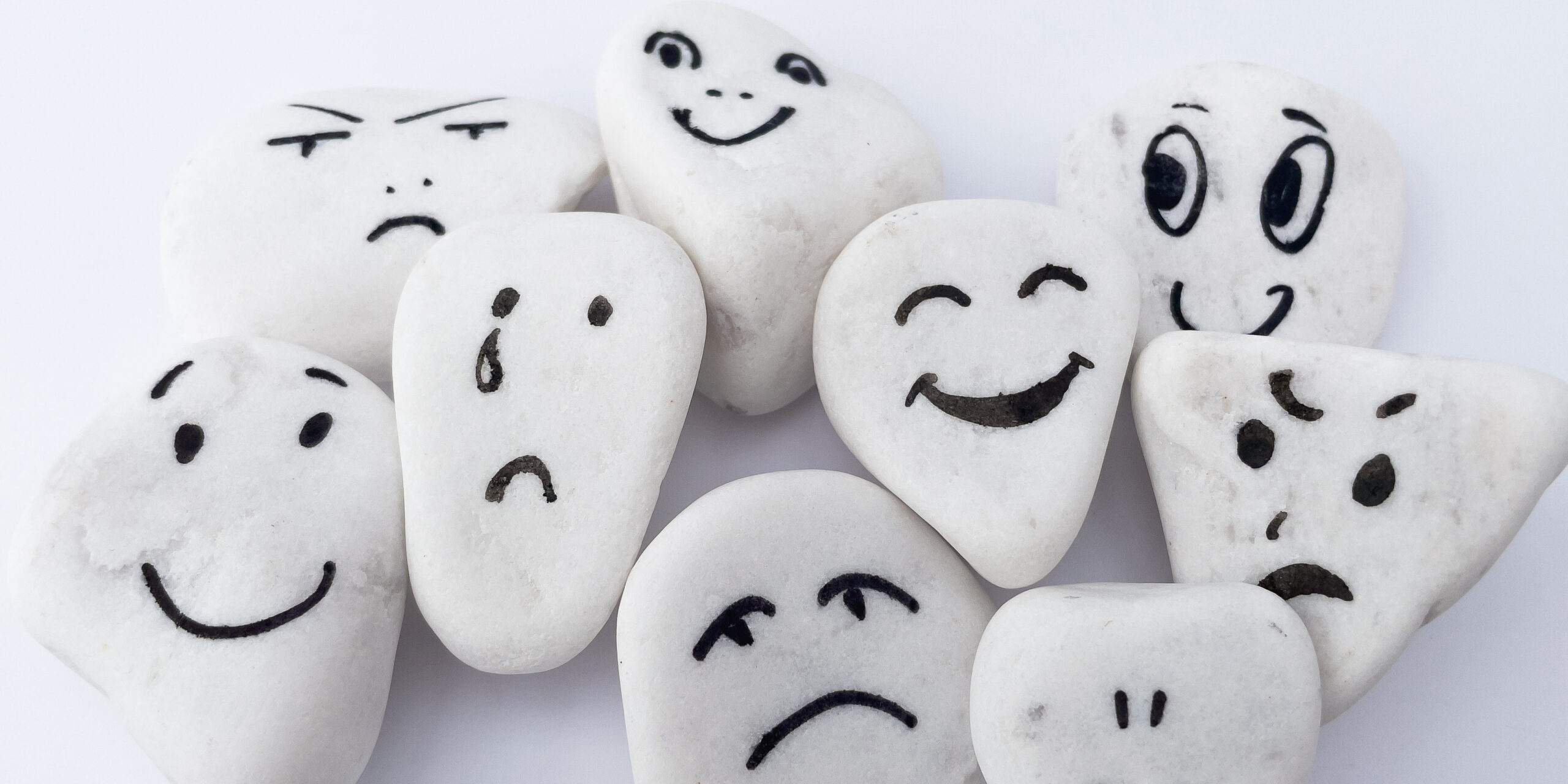
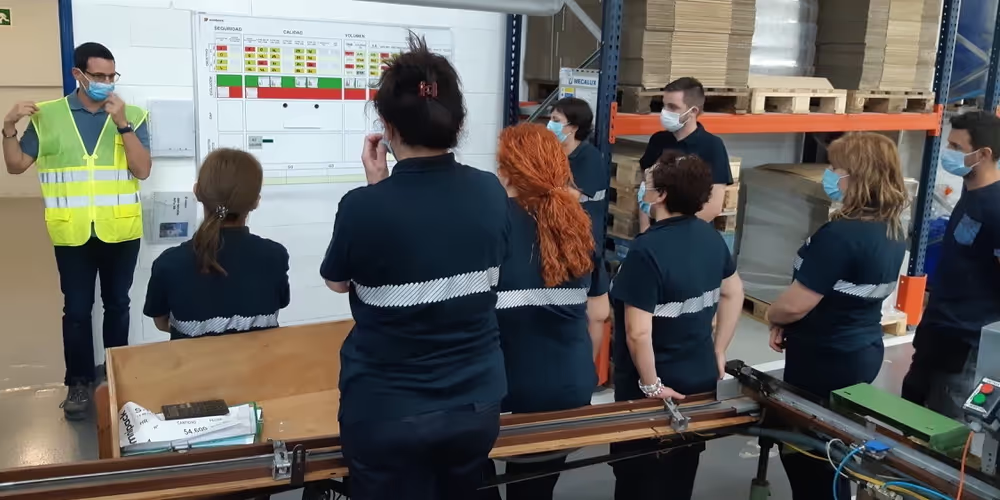
FEATURE – They say lean is all about people, and yet emotions – something we all feel and express daily – are largely absent from the lean discourse. The authors discuss the role they play in a lean transformation.
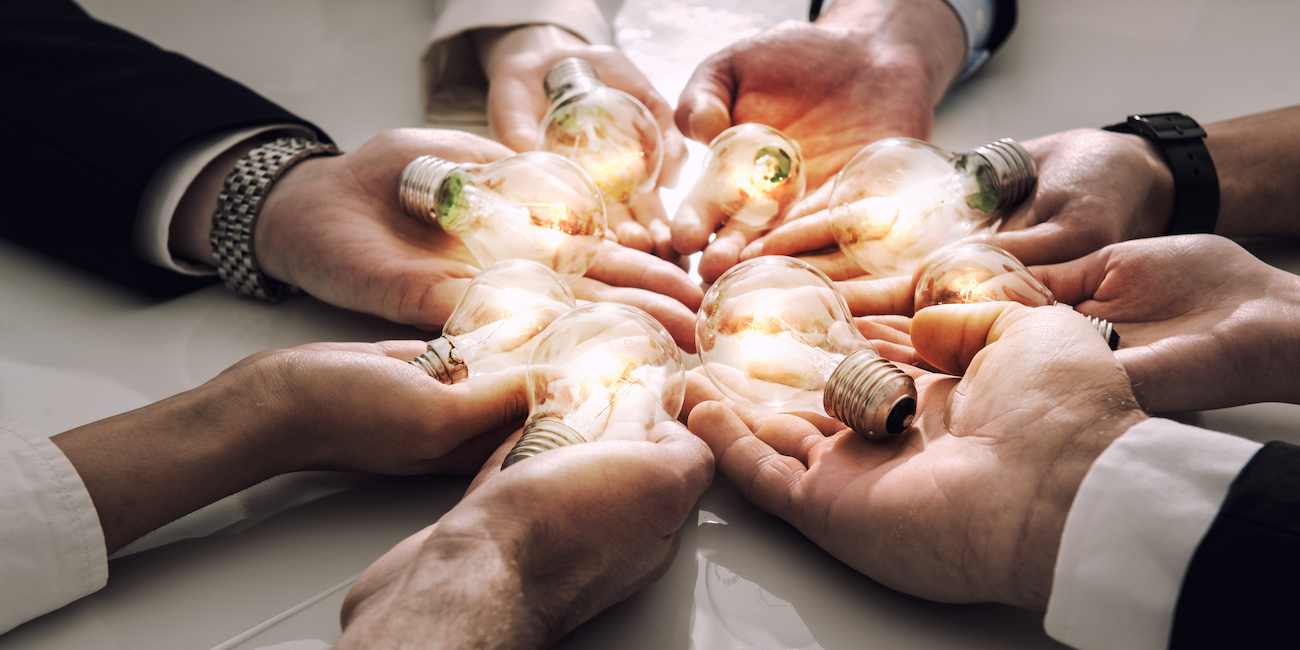
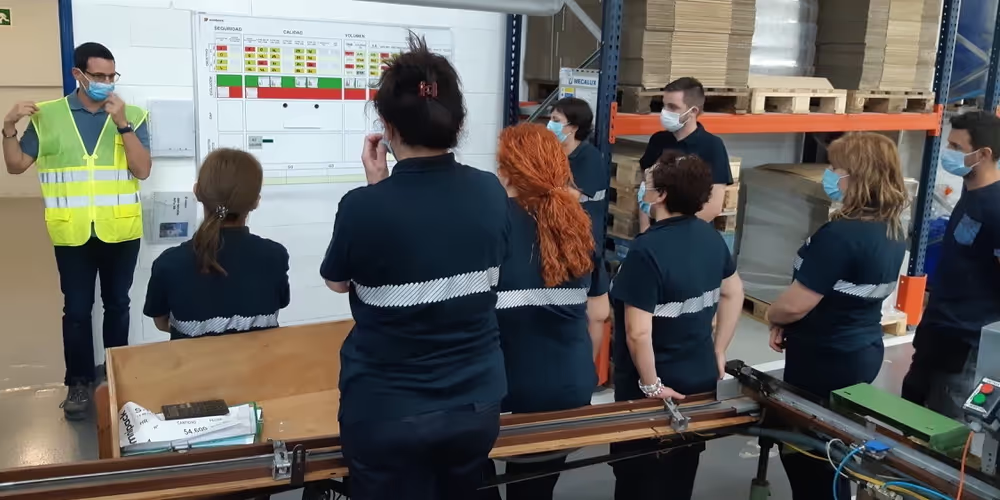
ROUNDUP – Knowledge sharing is a powerful enabler of lean change. In this roundup, our editor discusses the benefits of yokoten and shares a few examples.
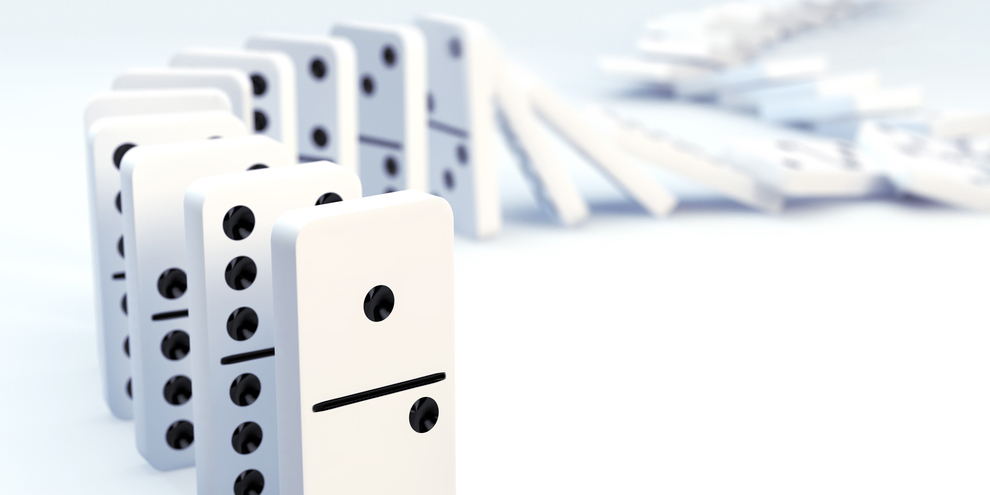
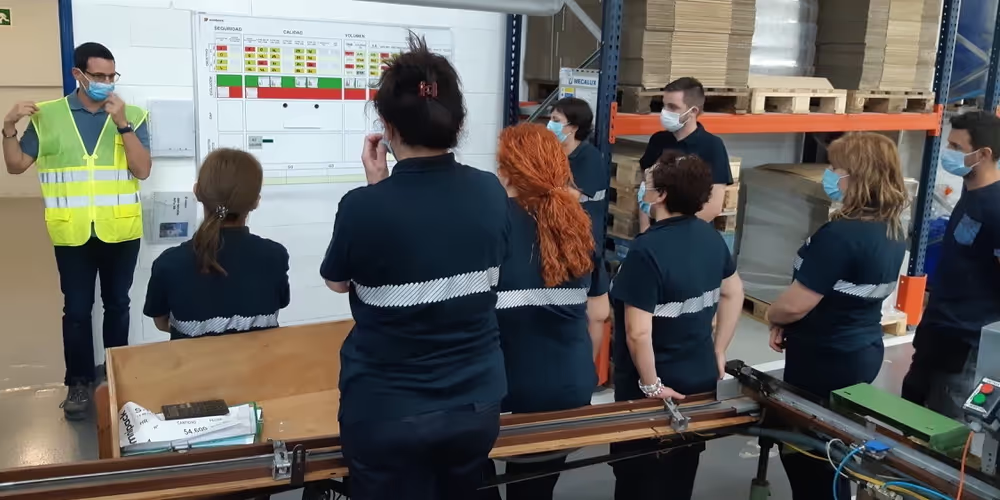
FEATURE – The only way for lean to succeed is to change a leader’s behavior so the rest of the organization will change too and people get the support they need to become problem solvers.
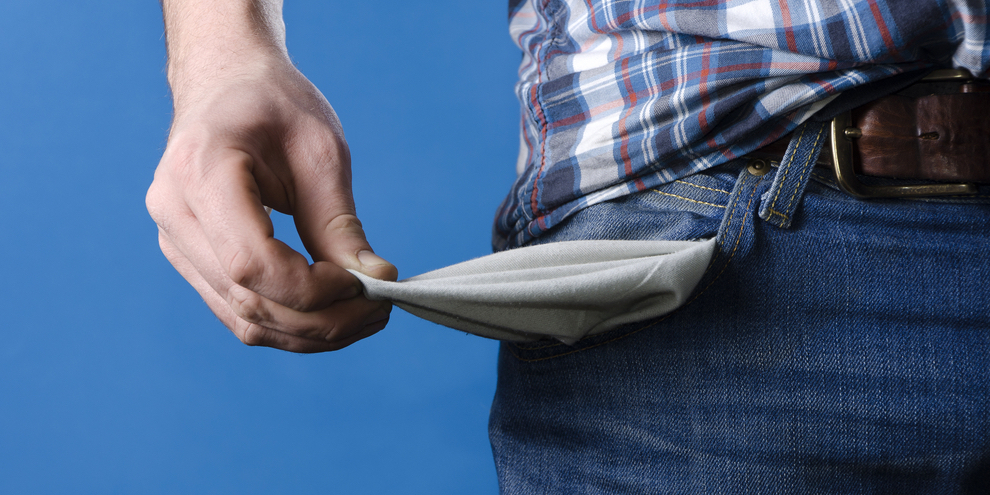
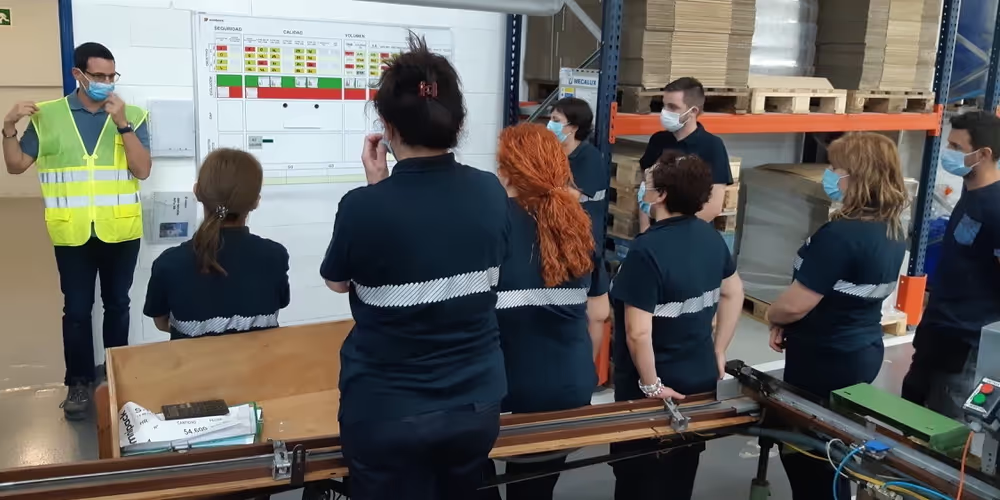
FEATURE – As inflation bites, the author offers us an insightful take into what it really means to understand a company’s costs. Hint, it doesn’t involve passing them on to customers.
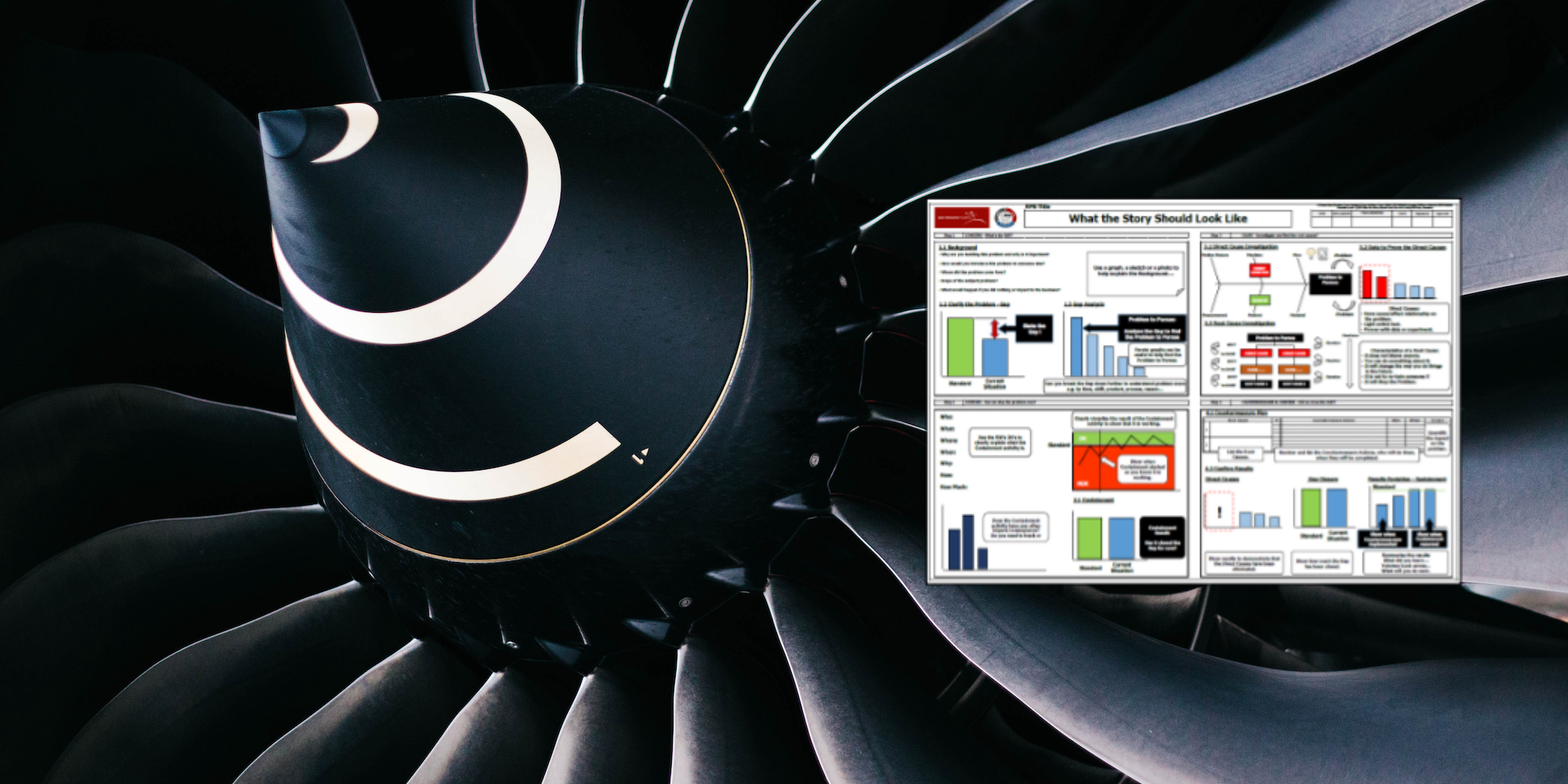
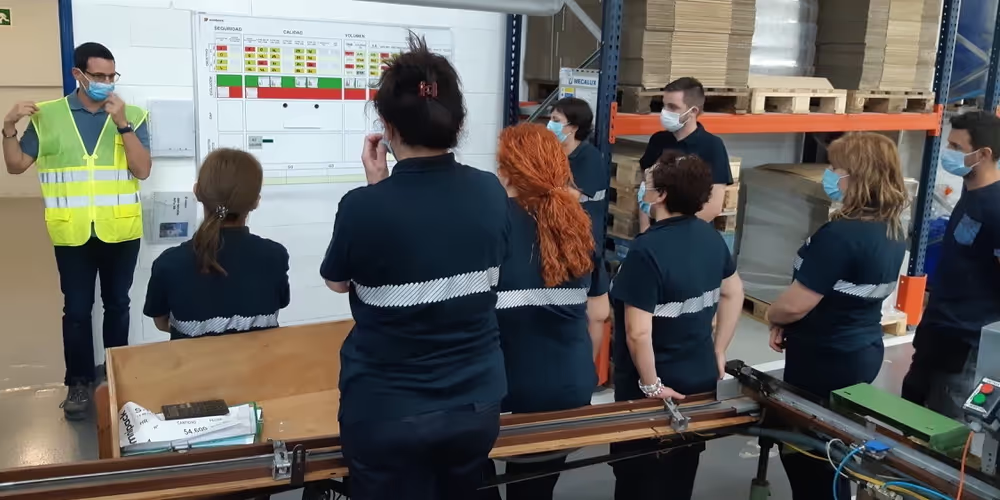
INTERVIEW – From hospitals to start-ups, lean principles have been applied far beyond their origins at Toyota. This article discusses how lean can be applied to learning – specifically, how we can apply lean learning to learning lean.
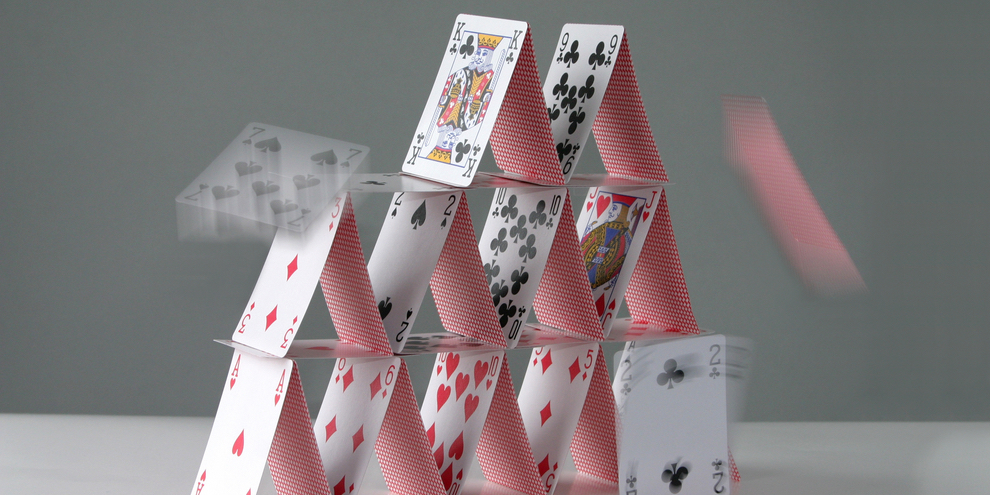
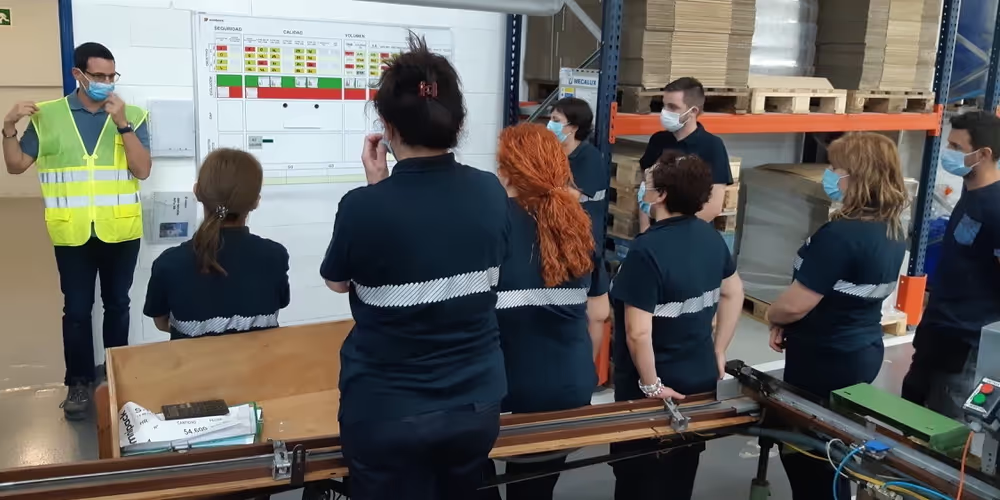
FEATURE – Drawing inspiration from his research into the causes of failure of transformations, the author discusses how these can directly be linked to the most common misconceptions on Lean Thinking.
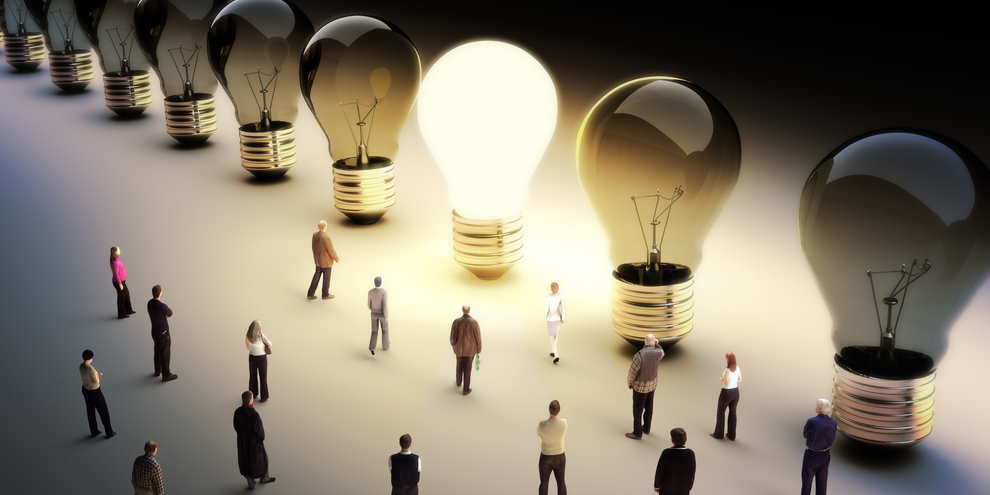
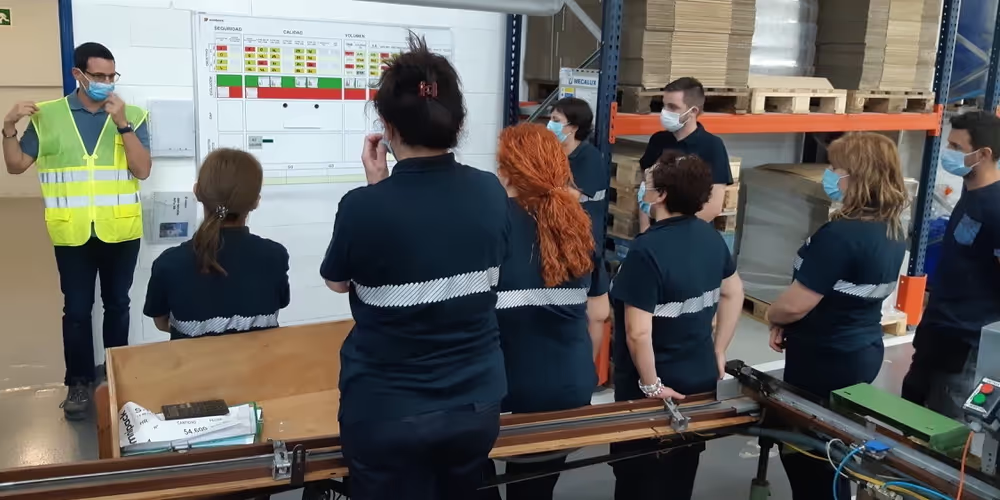
FEATURE – In this compelling theoretical piece, the author reminds us how in a lean organization relations are structured around learning opportunities rather than execution. This is what ultimately enables a company to grow.
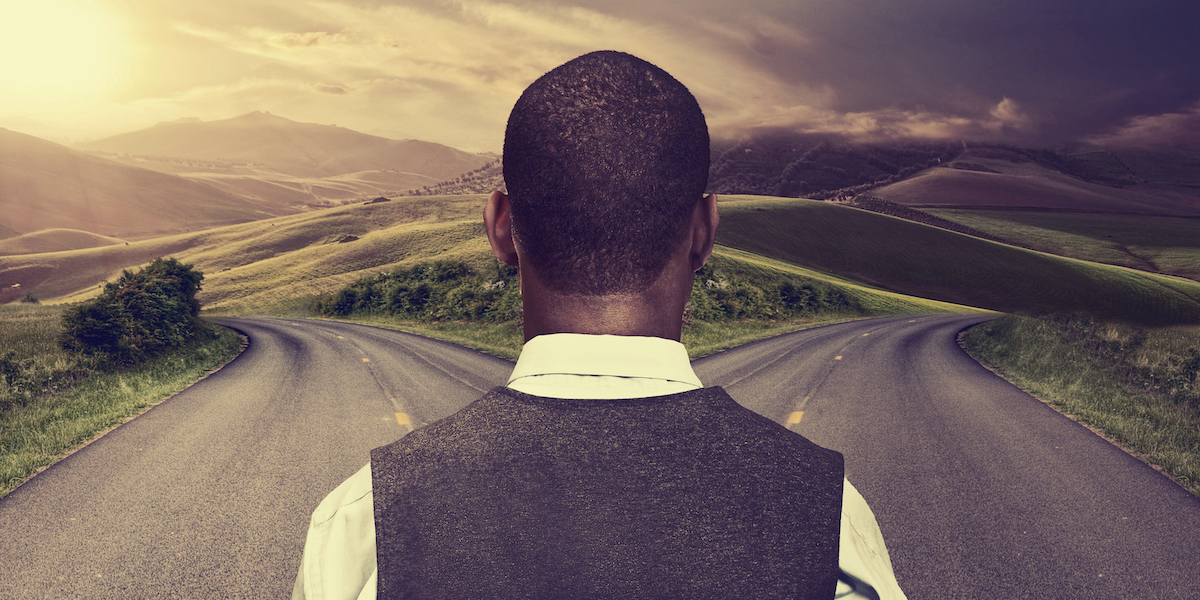
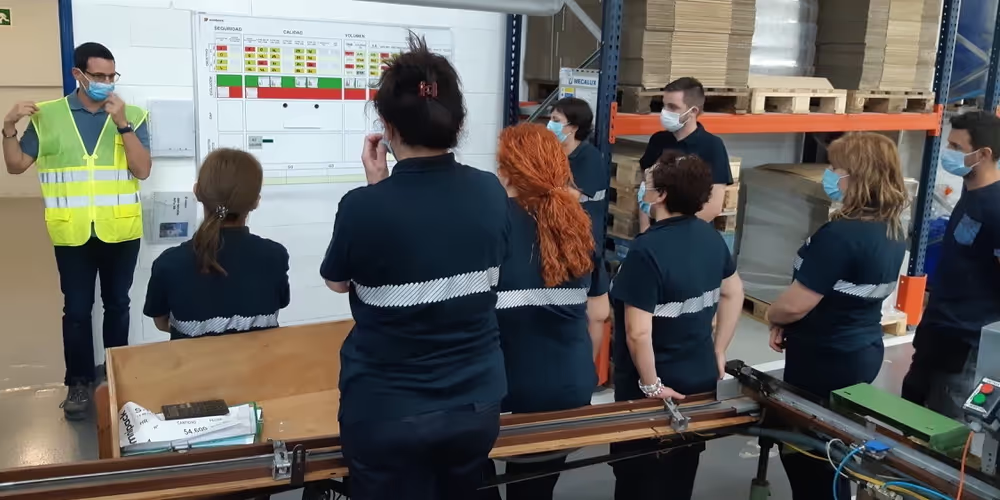
RESEARCH – The author reflects on several highly-ranked academic publications to paint a picture of salient lean knowledge, both past and present, and suggests several avenues for future lean research.
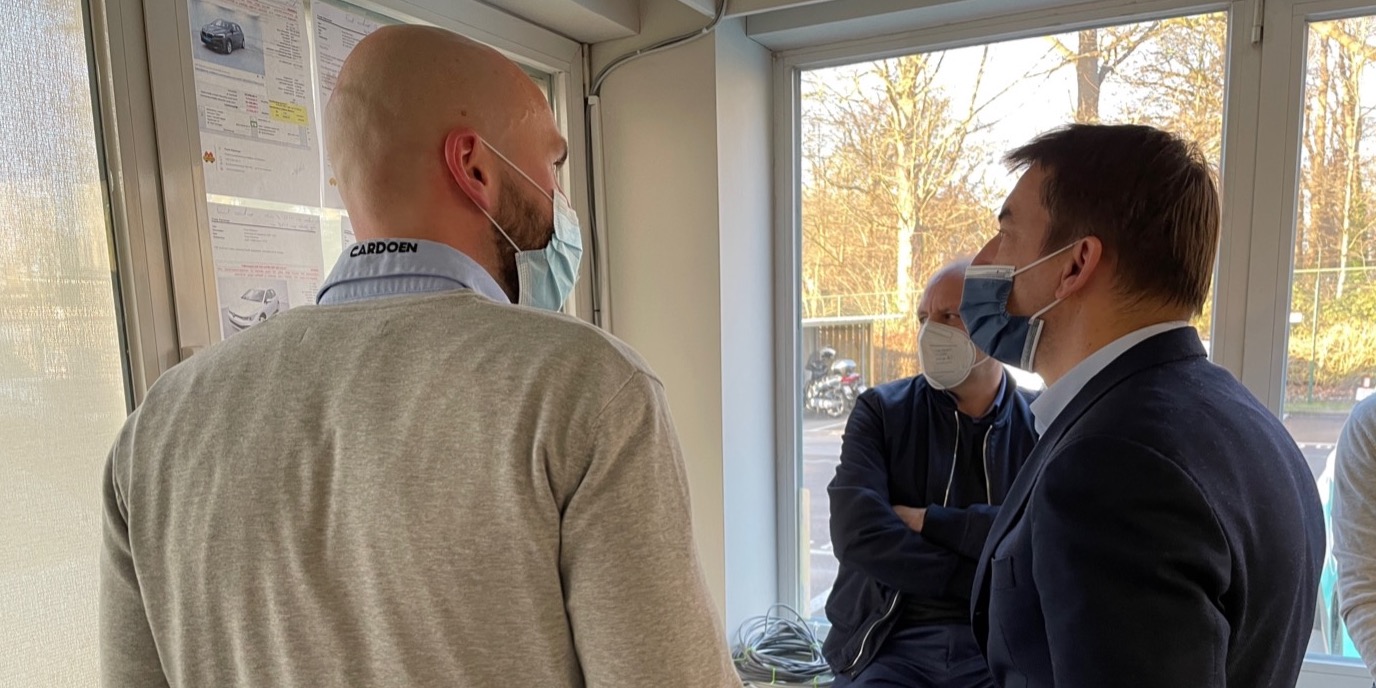
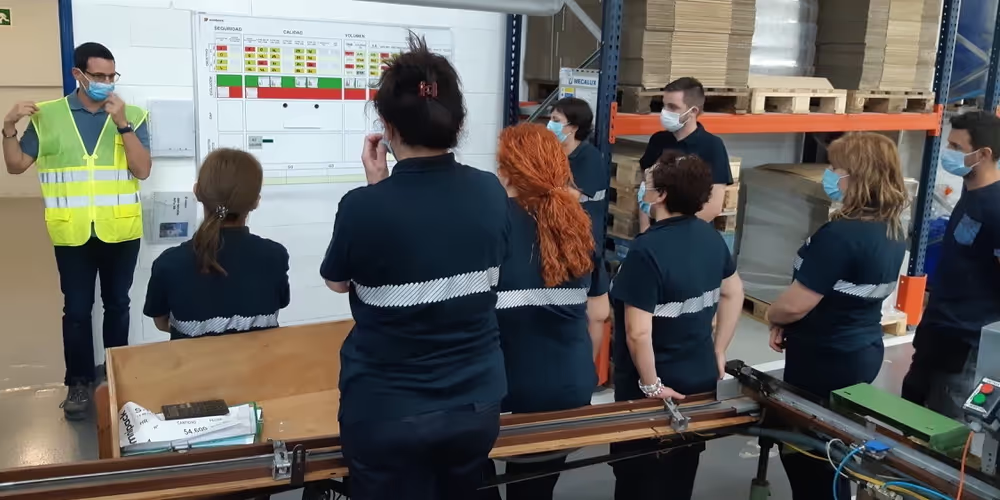
FEATURE – Lean Thinking is about voluntary participation, not audits that are meant to ensure compliance. The authors explore the advantages of pursuing cooperation rather than control.
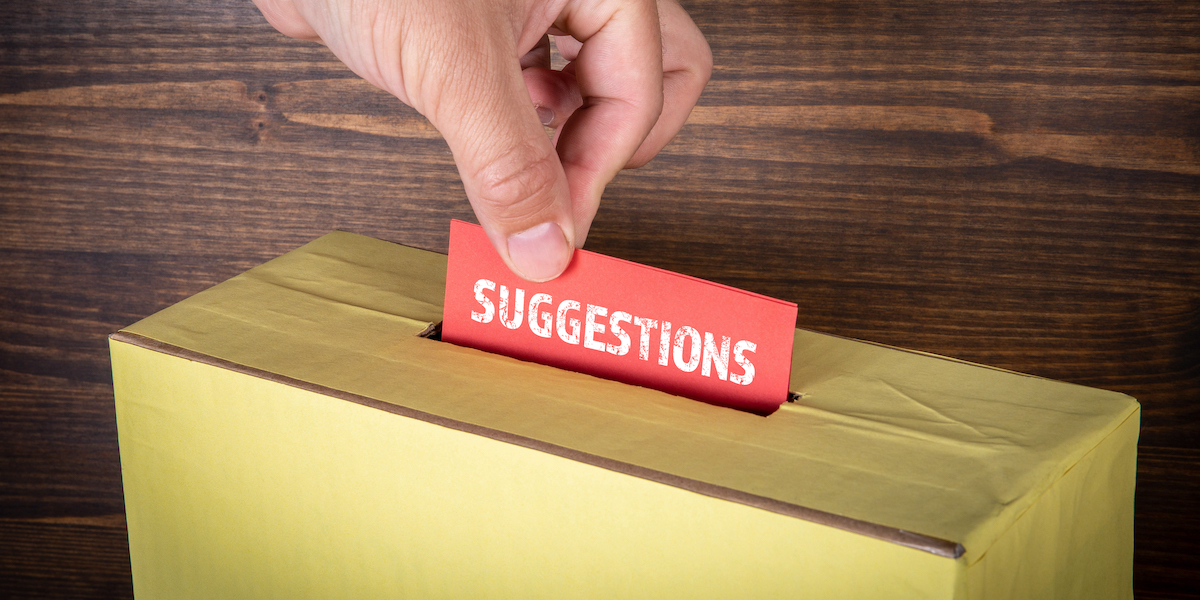
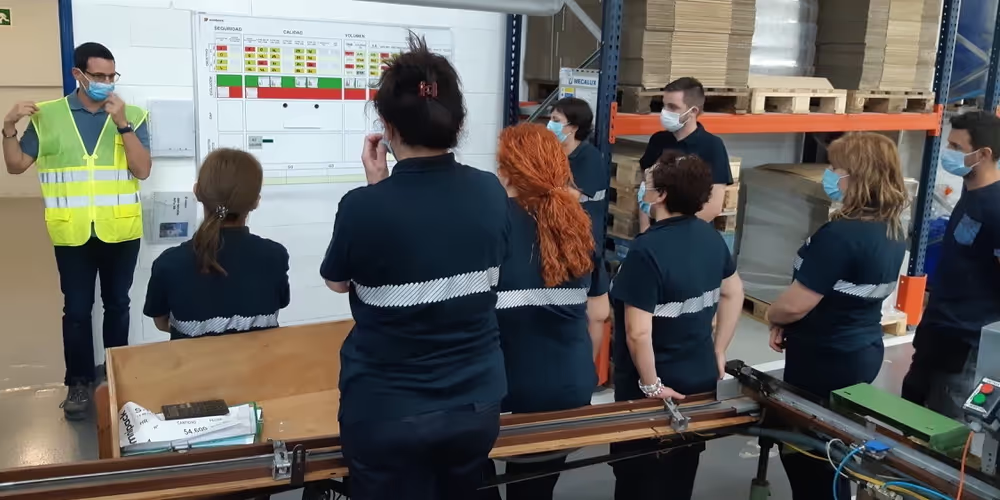
FEATURE – At Toyota, led by senior executives, suggestion schemes have contributed to decades of improvement. This article explores why they are so effective and encourages you to try one out for yourself.
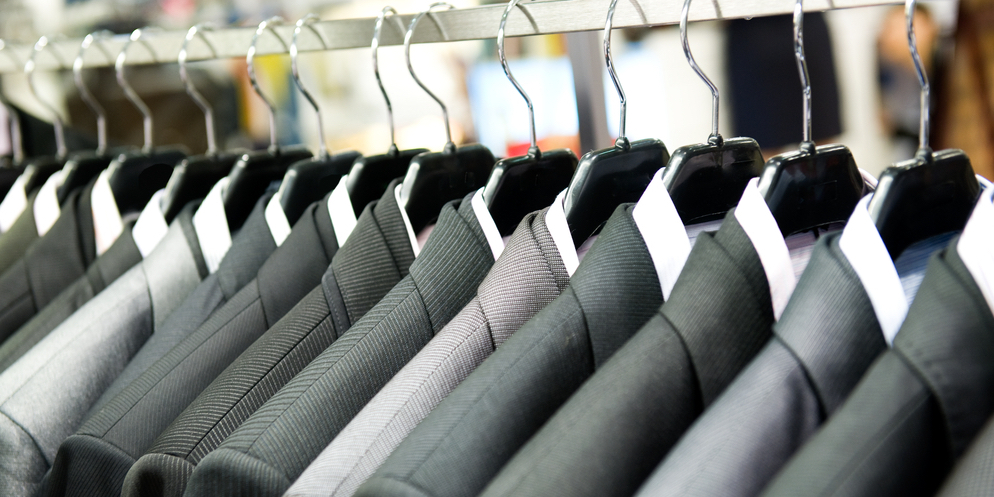
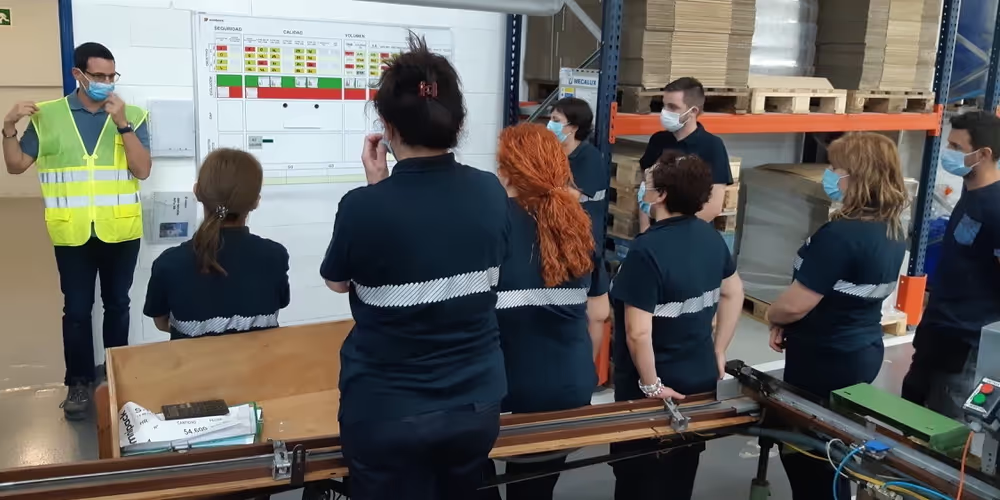
FEATURE – Lean provides everyone with a framework to learn continuously and do an ever-better job. Without this understanding, an executive will not be able to steer the organization in the right direction.
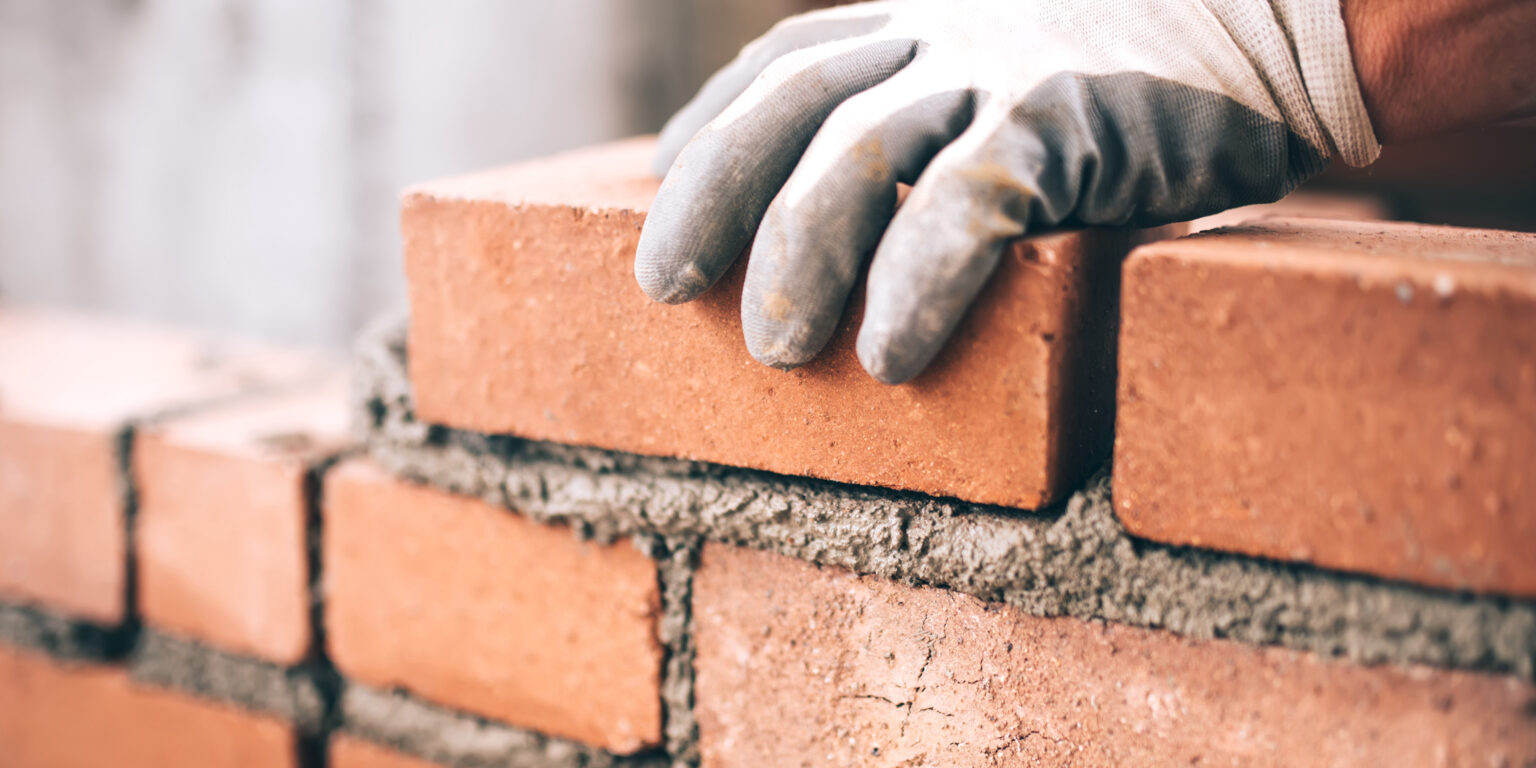
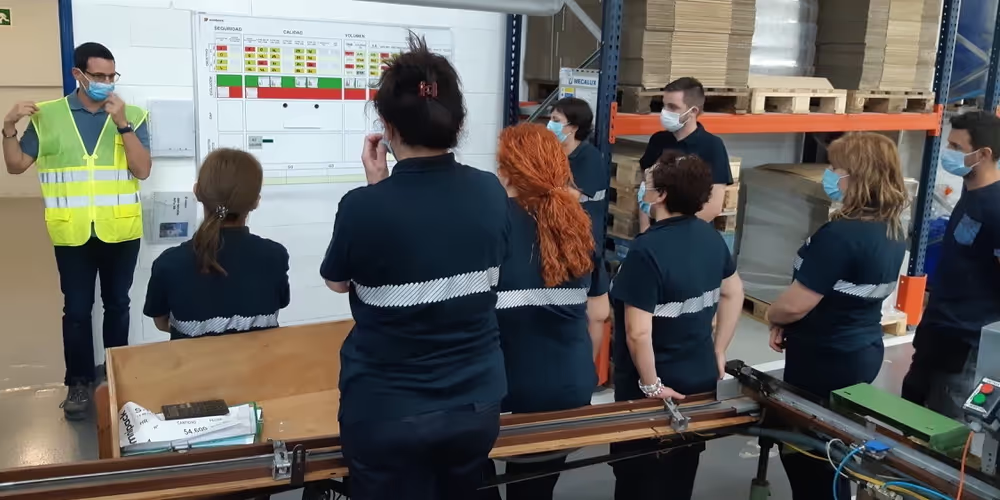
FEATURE – When we emphasize systems and roles but fail to encourage and support kaizen, we cannot expect to tap into the full potential of Lean Thinking as a cognitive revolution.
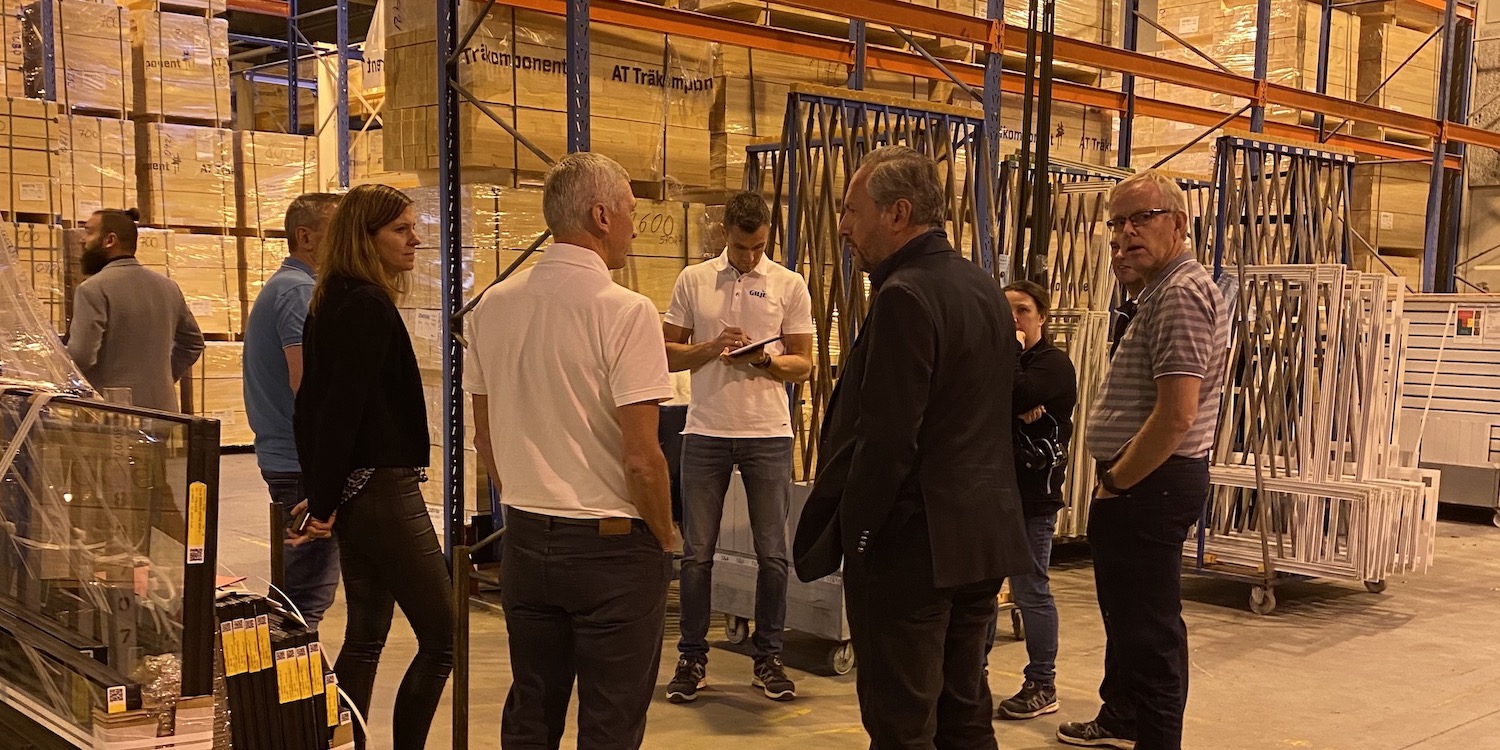
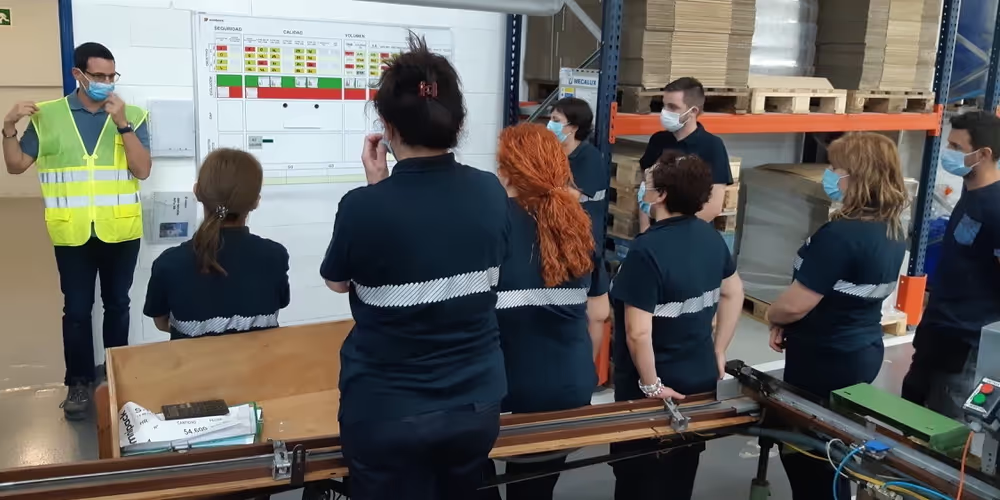
FEATURE – Fresh from a number of visits to Norwegian gemba, the authors share their reflections and discuss the importance of making the information flow visible.
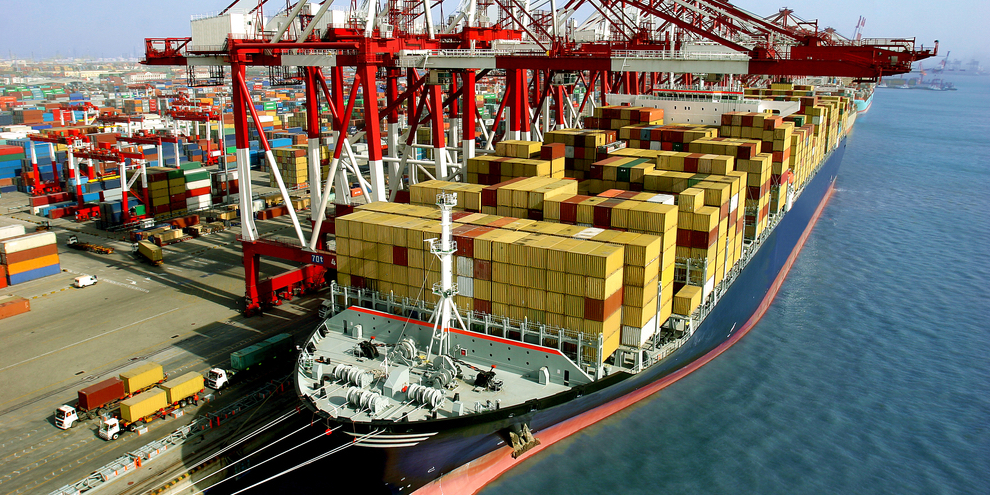
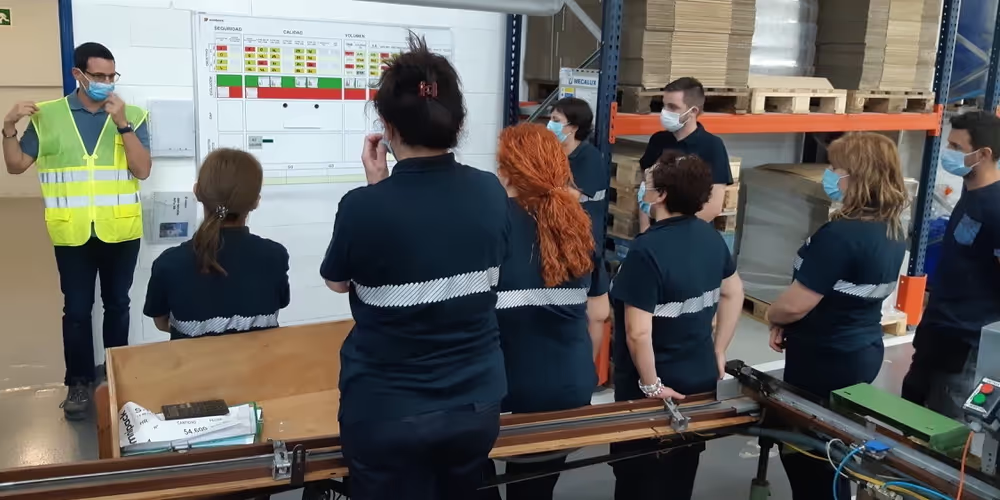
FEATURE – As global supply chain suffer ongoing disruption, the author addresses the misconceptions on Just-In-Time that keep appearing in the media.
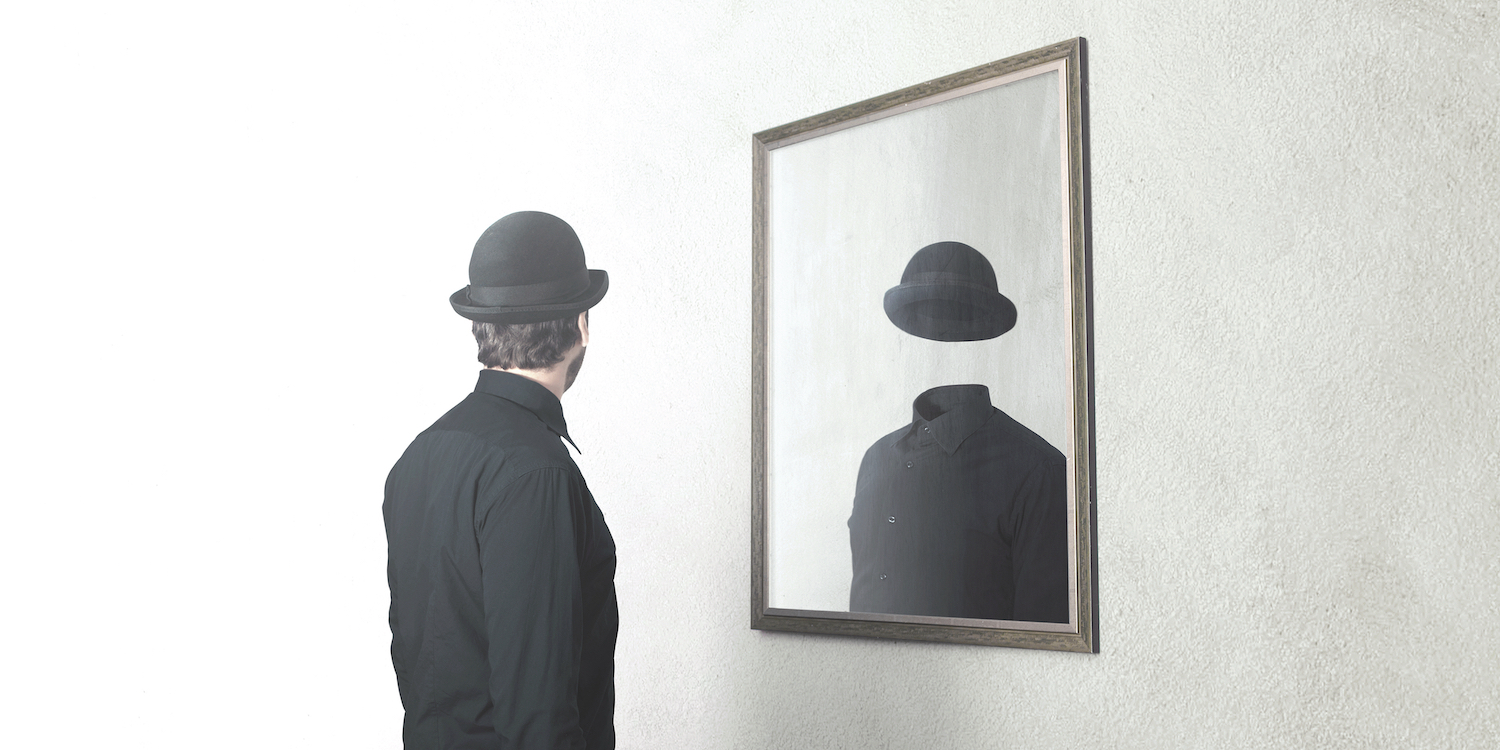
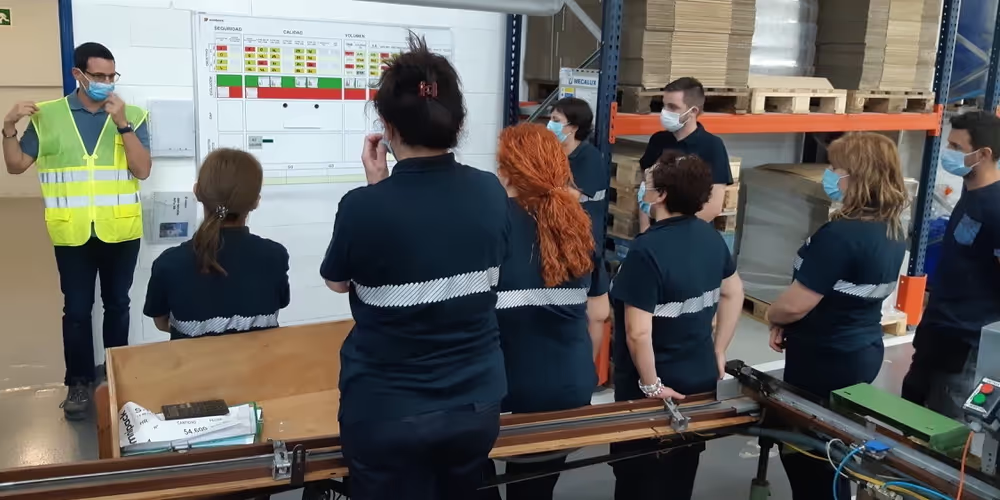
FEATURE – The gemba tells us more than we think. The authors discuss what we need to look at during our walks to understand the impact of non-manufacturing functions on the overall process.
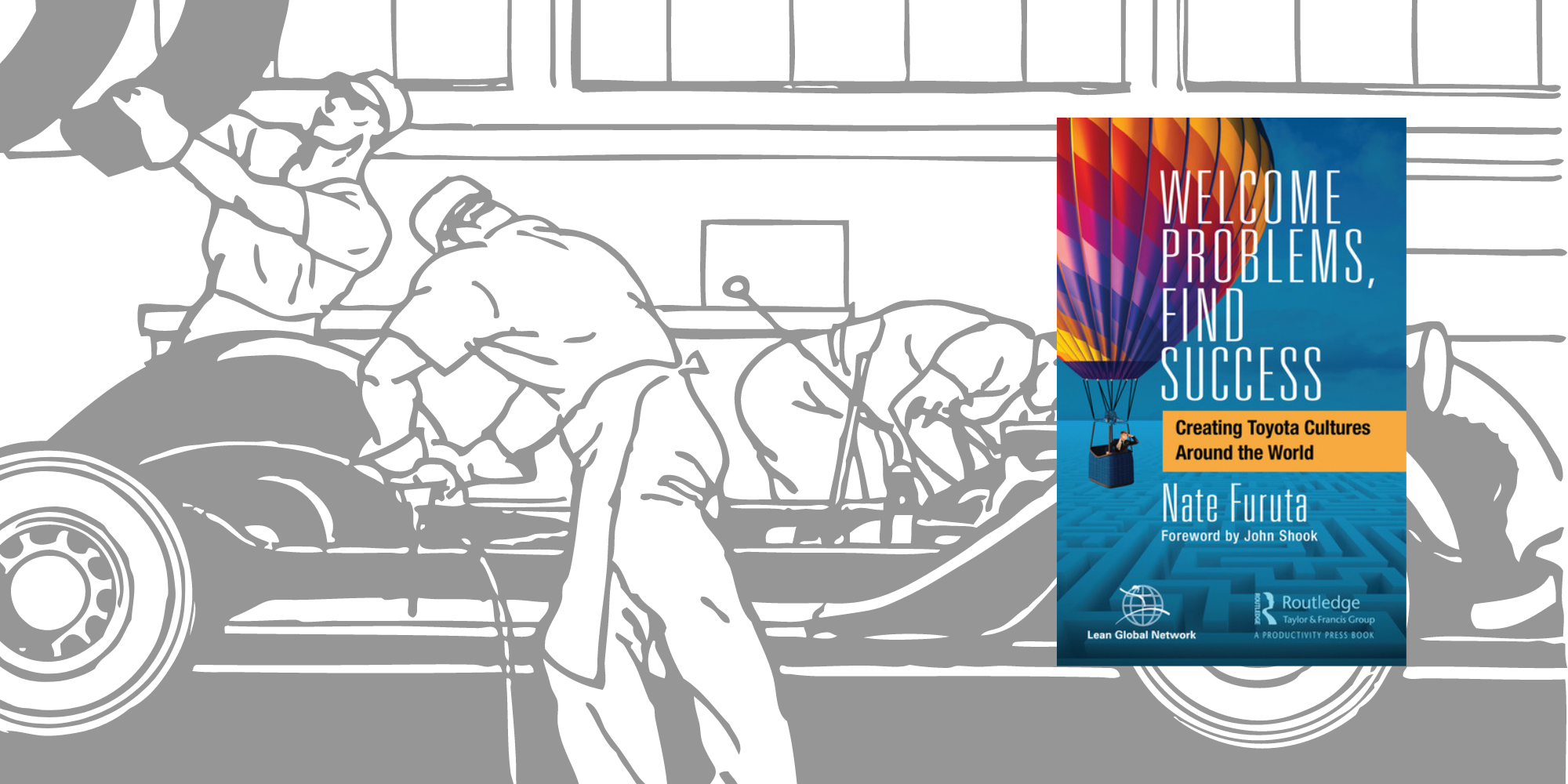
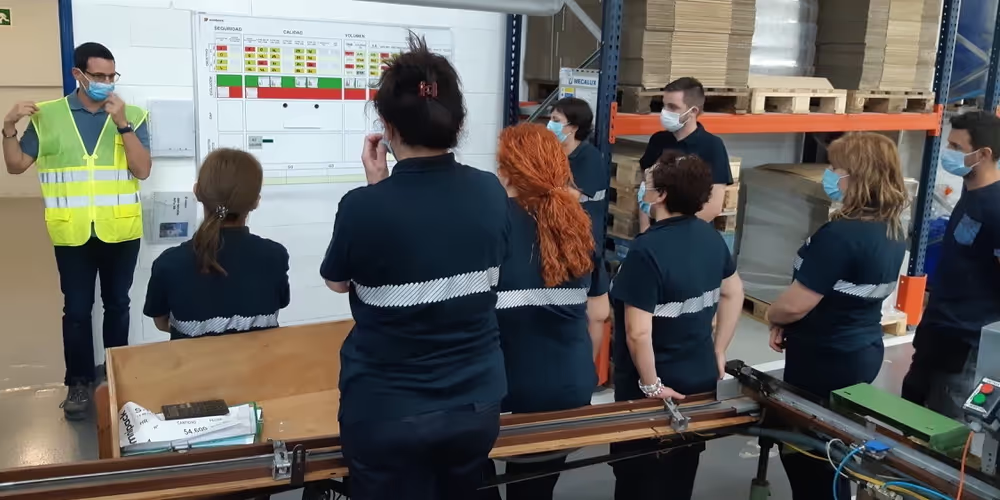
FEATURE – The Lean Global Network just published a new book by Kiyoshi “Nate” Furuta sharing compelling examples of how Toyota principles and culture can be effectively spread to new environments.
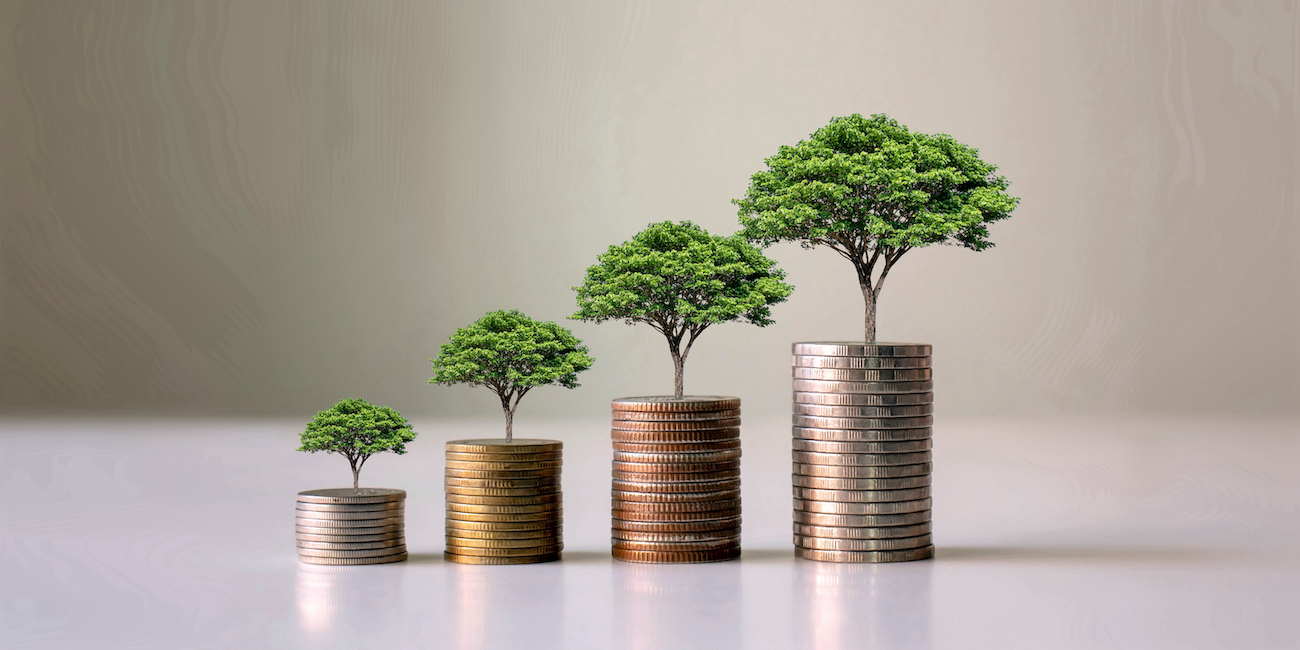
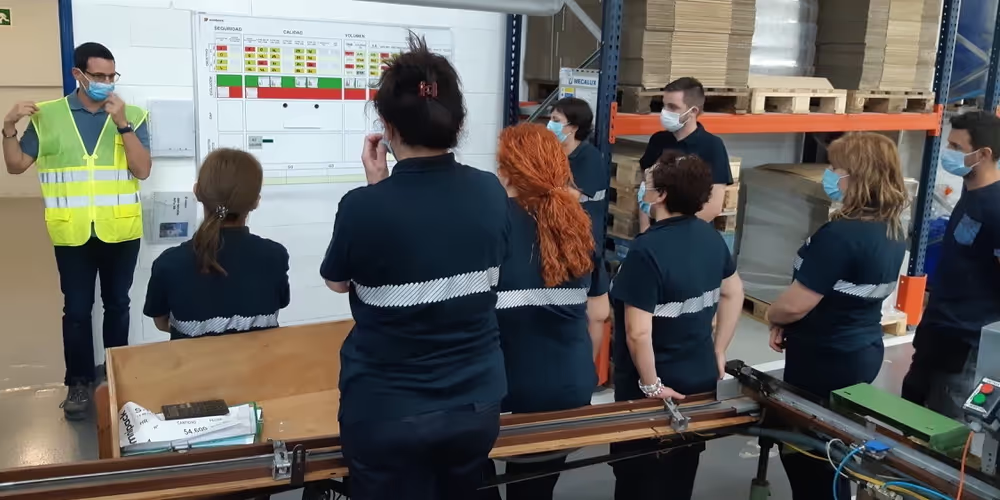
FEATURE – The impact of humankind on the environment is now beyond dispute. Yet, too little is being done to adapt our business models. This compelling read explains why we need to create prosperity beyond profit.
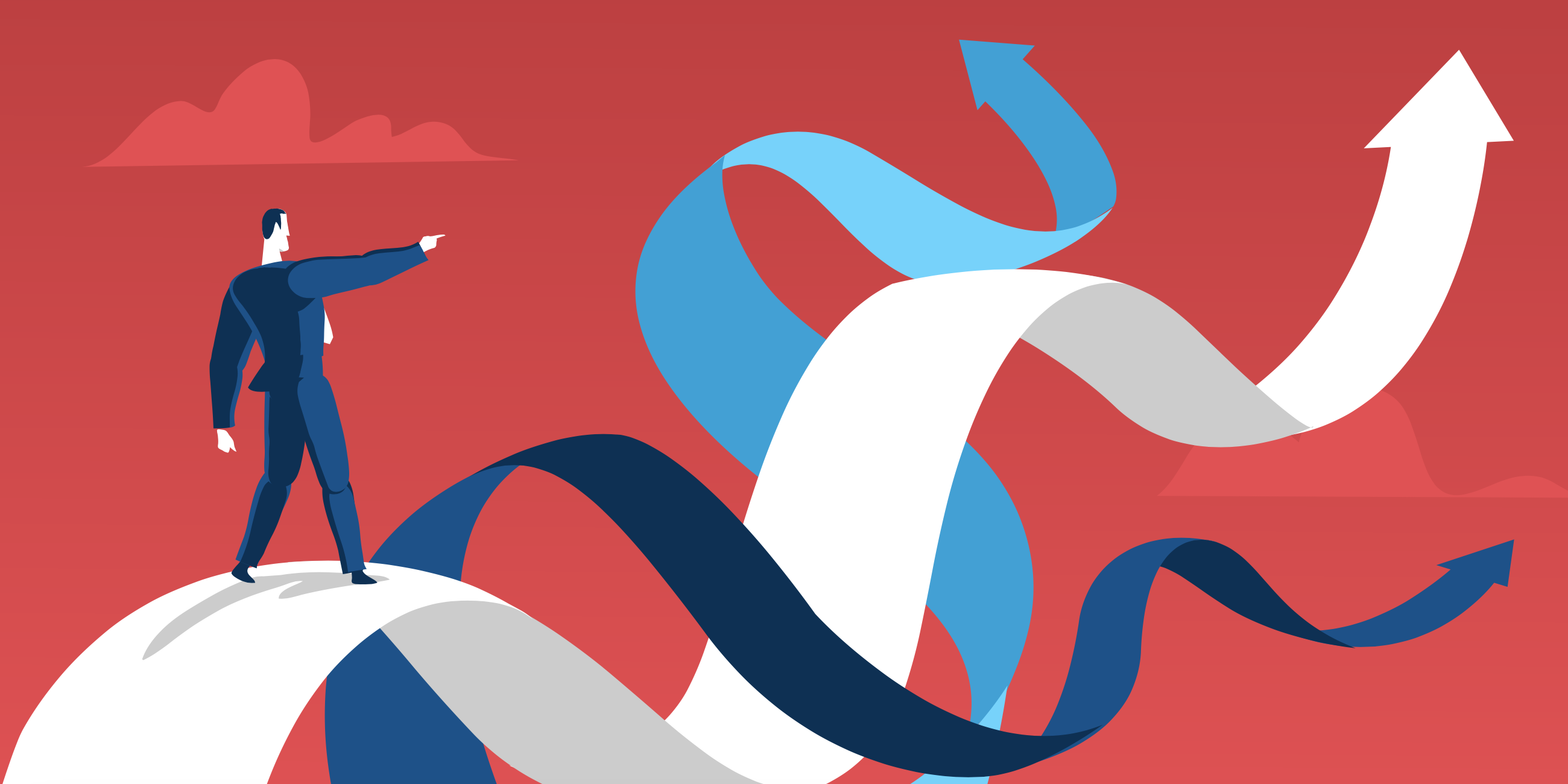
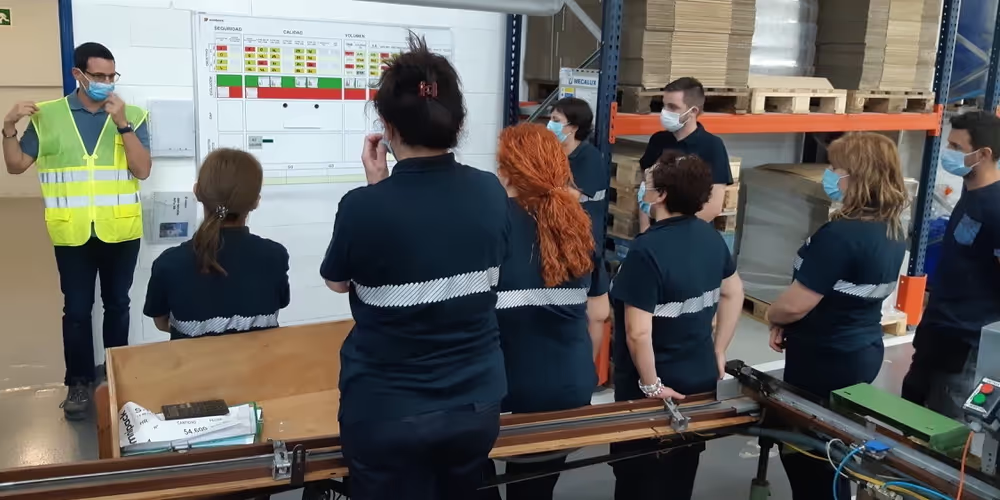
FEATURE – As lean thinkers, our focus is on problem-solving. The author explains why effectively solving problems depends on our ability to make the right decisions and suggests the lean community plays closer attention to this.

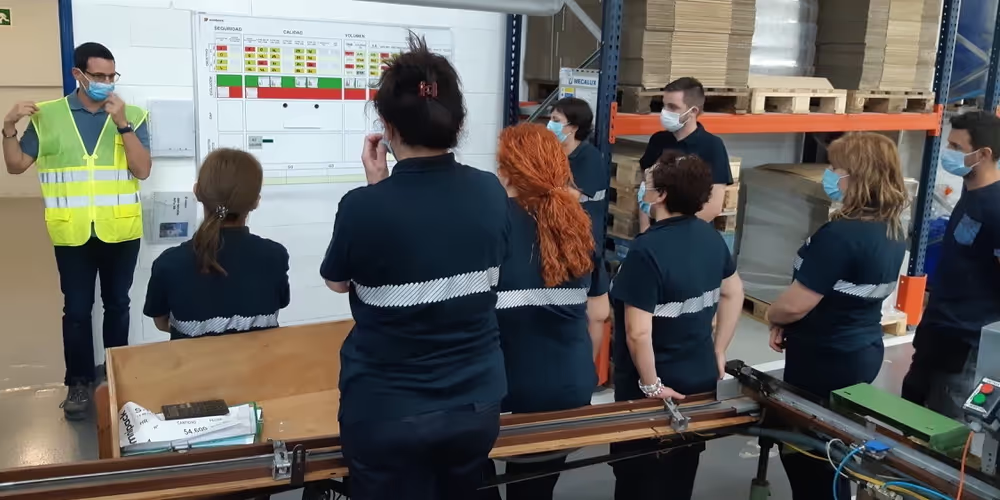
FEATURE – Reflecting on Nomura-san’s recently published book on radical quality improvement, the author encourages us to embrace the spirit of “Dantotsu” to meet the challenges we face as a society.
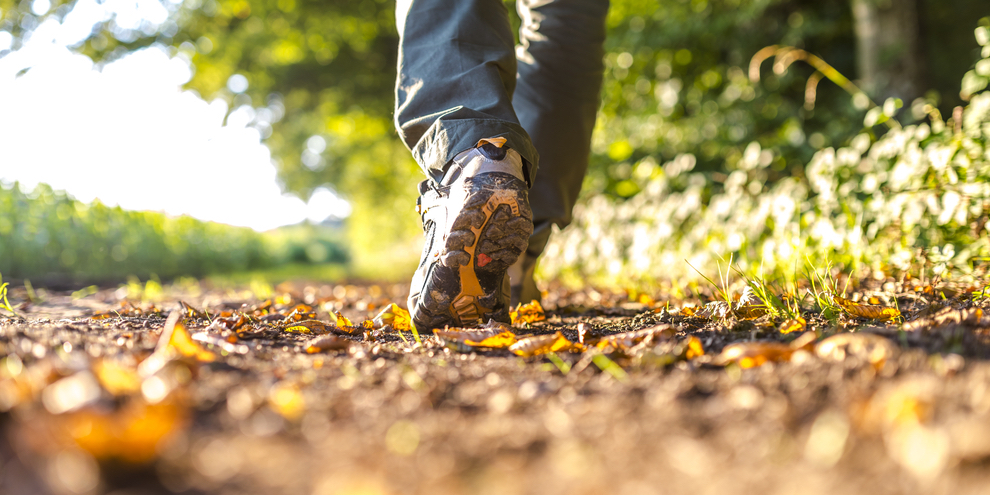
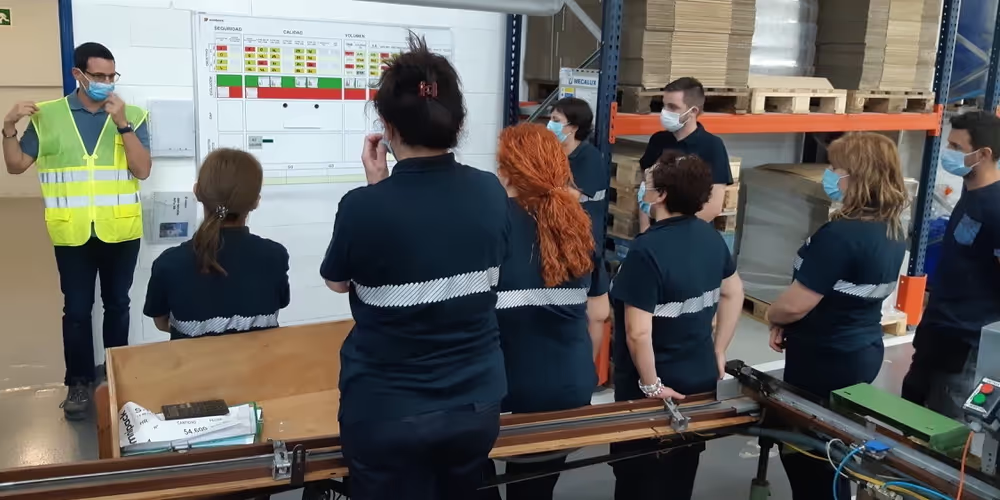
FEATURE – The author describes Lean Thinking as a path of discovery and explains why attempts to define it “once and for all” are destined to fail.
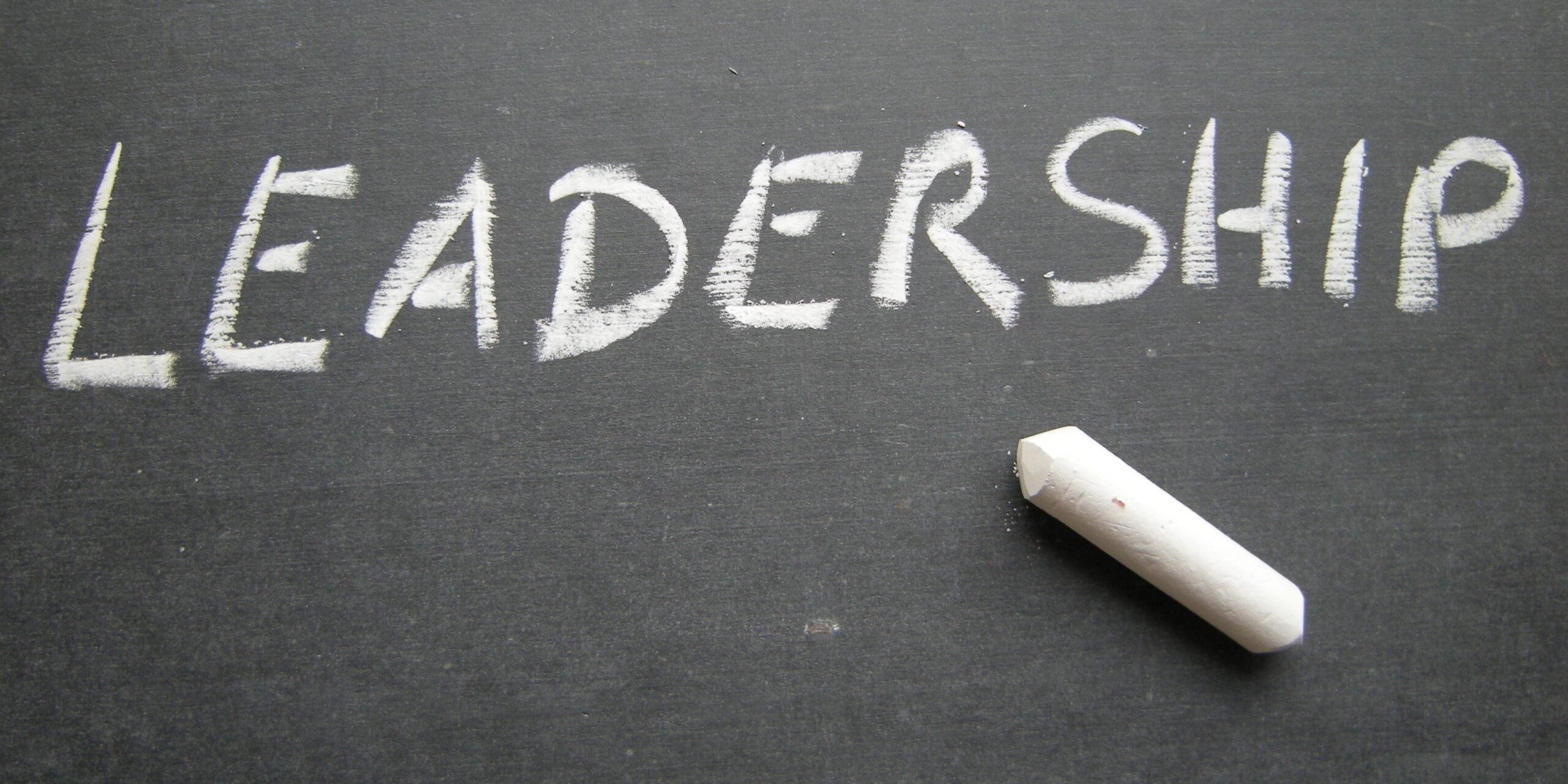
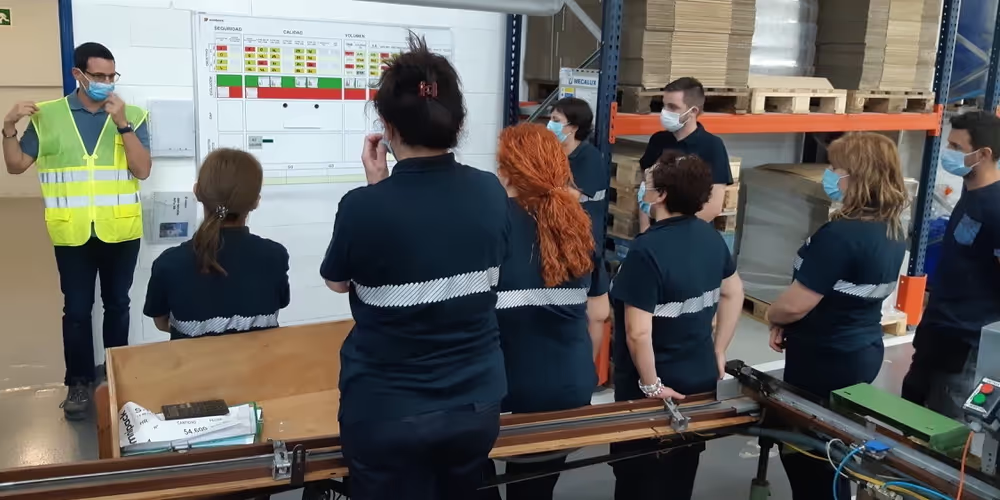
FEATURE – The author reflects on the importance of standardized work in her daily life as a manager and explains why one can’t expect to run a company only using reports.
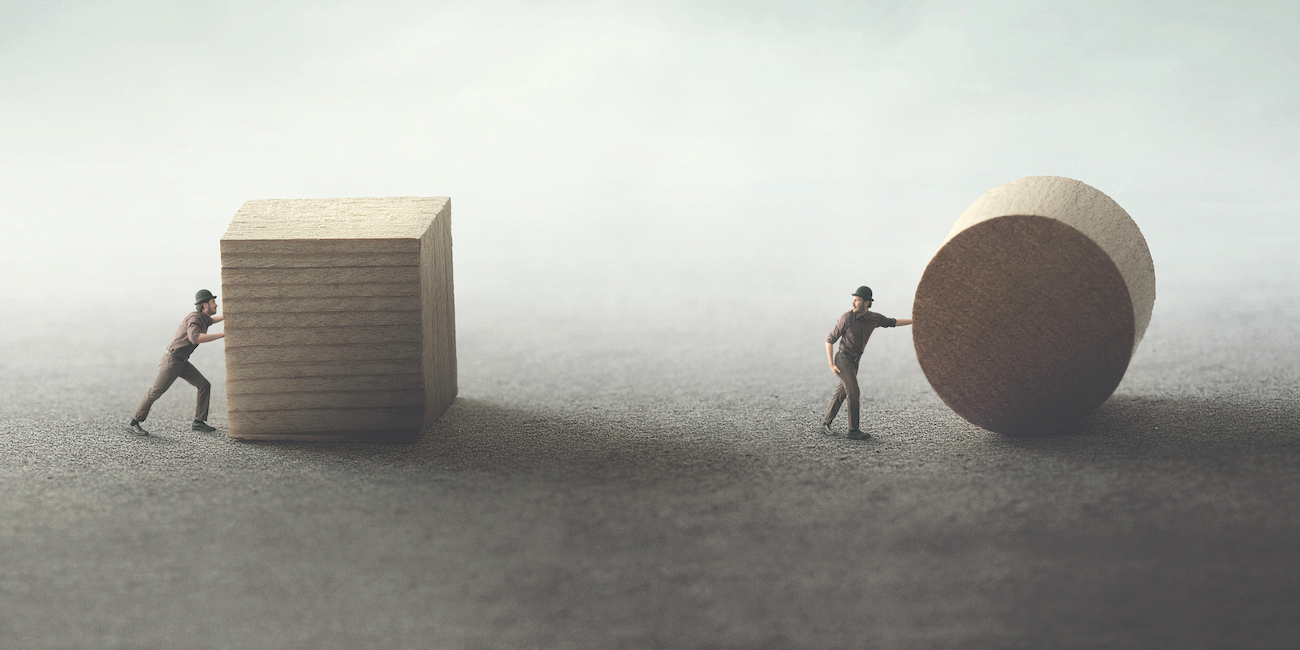
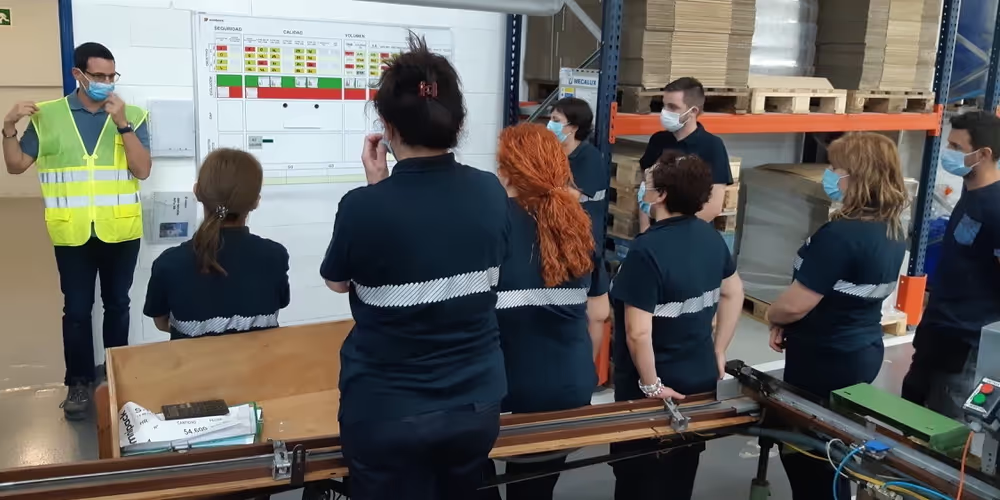
FEATURE – Looking back on the lean journeys he's seen firsthand, the author concludes that a true lean transformation occurs when you establish lines of mentoring to the Thinking People System.
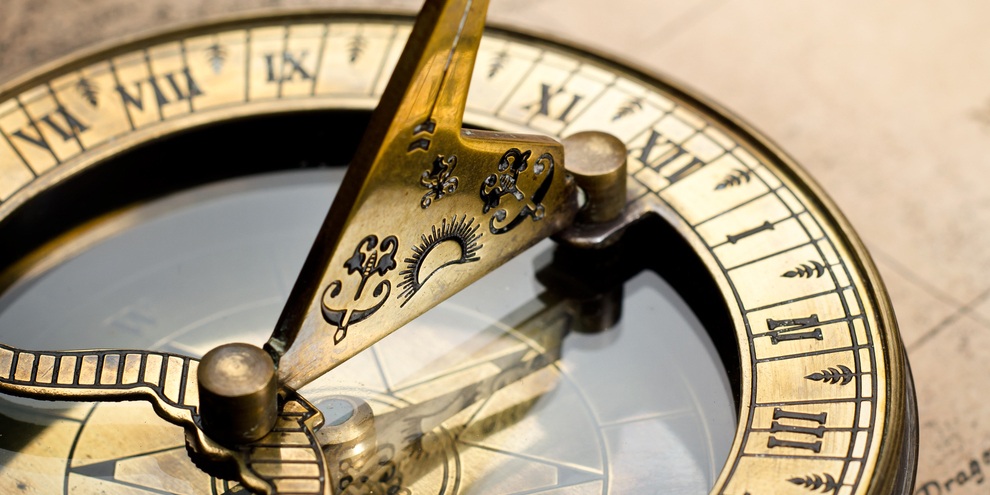
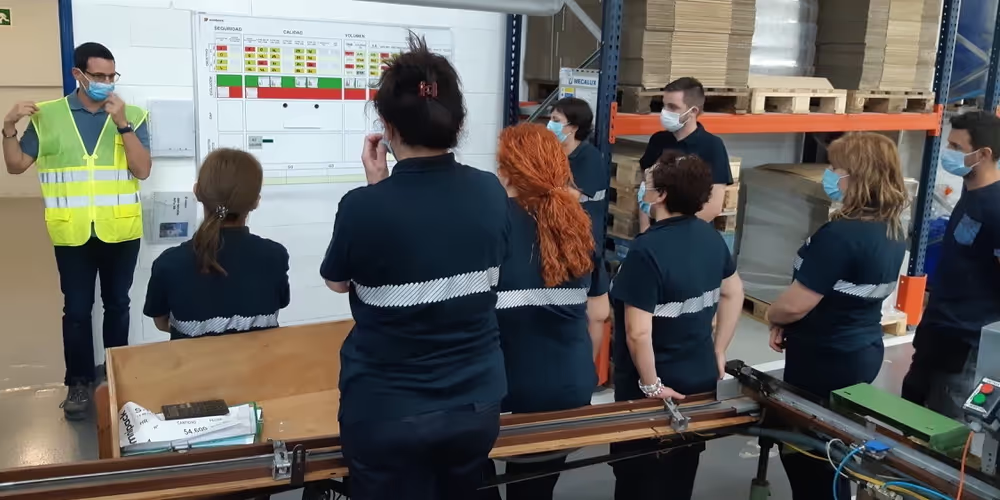
INTERVIEW – The extraordinary events of the past year have encouraged lean organizations around the world to ask deeper questions about purpose and value creation, says Josh Howell.
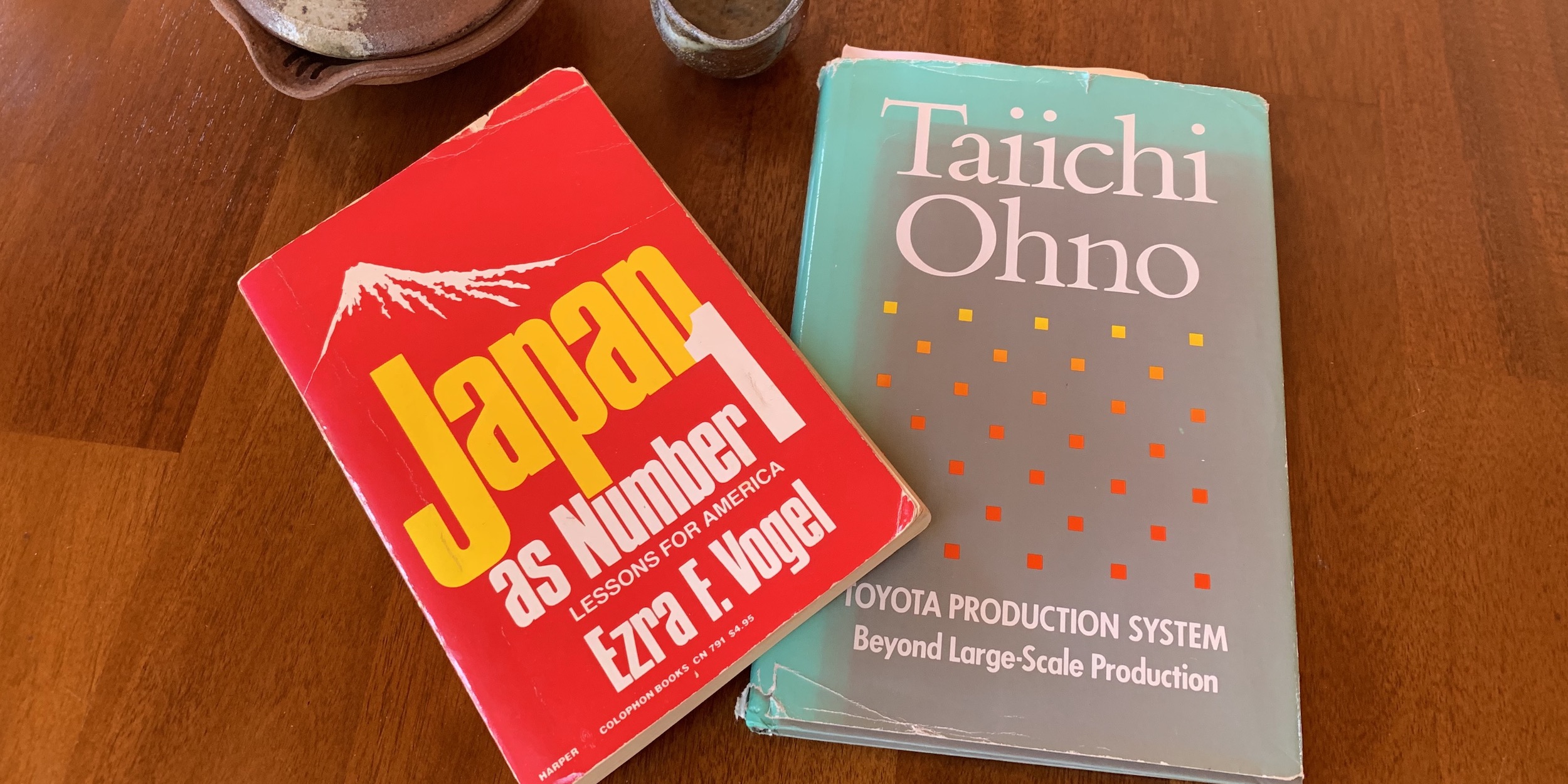
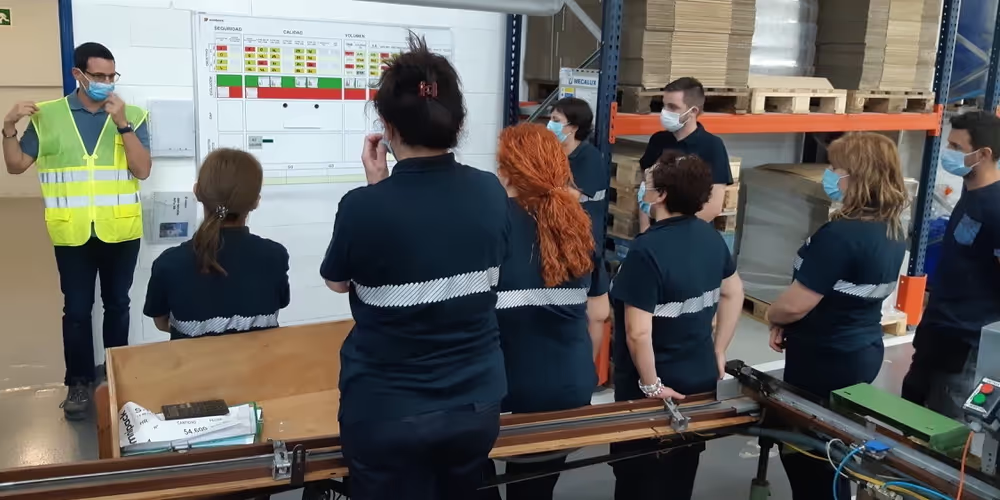
FEATURE – John Shook remembers the work of Ezra Vogel and Norman Bodek and discusses how, in their own way, each of their contributions help us to understand the Toyota Production System.
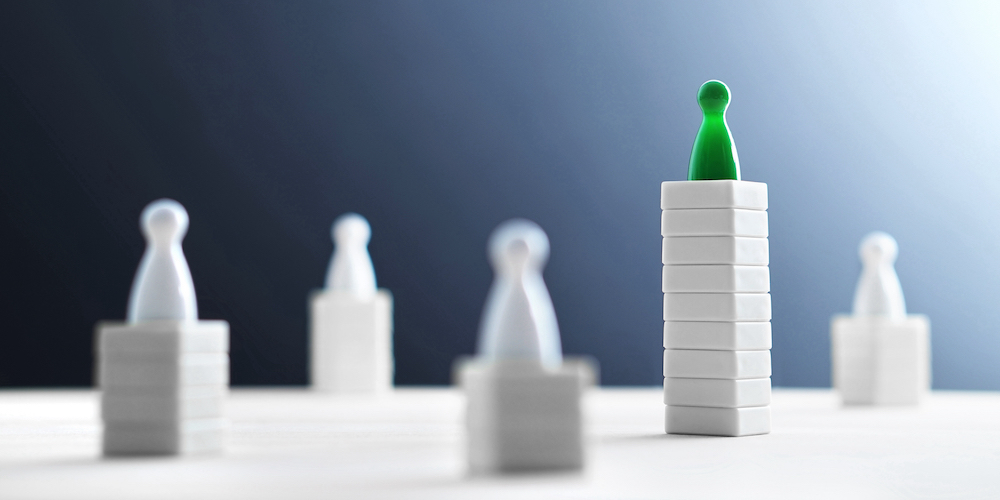
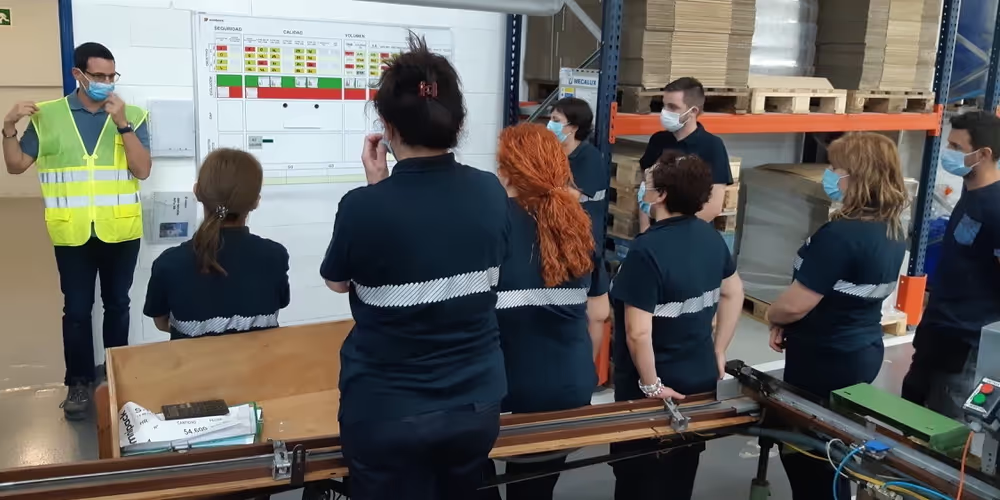
FEATURE – Lean represents a strategy to understand what needs to be improved, the critical skills that must be developed to solve a specific problem – whether it’s a quality defect or a pandemic.
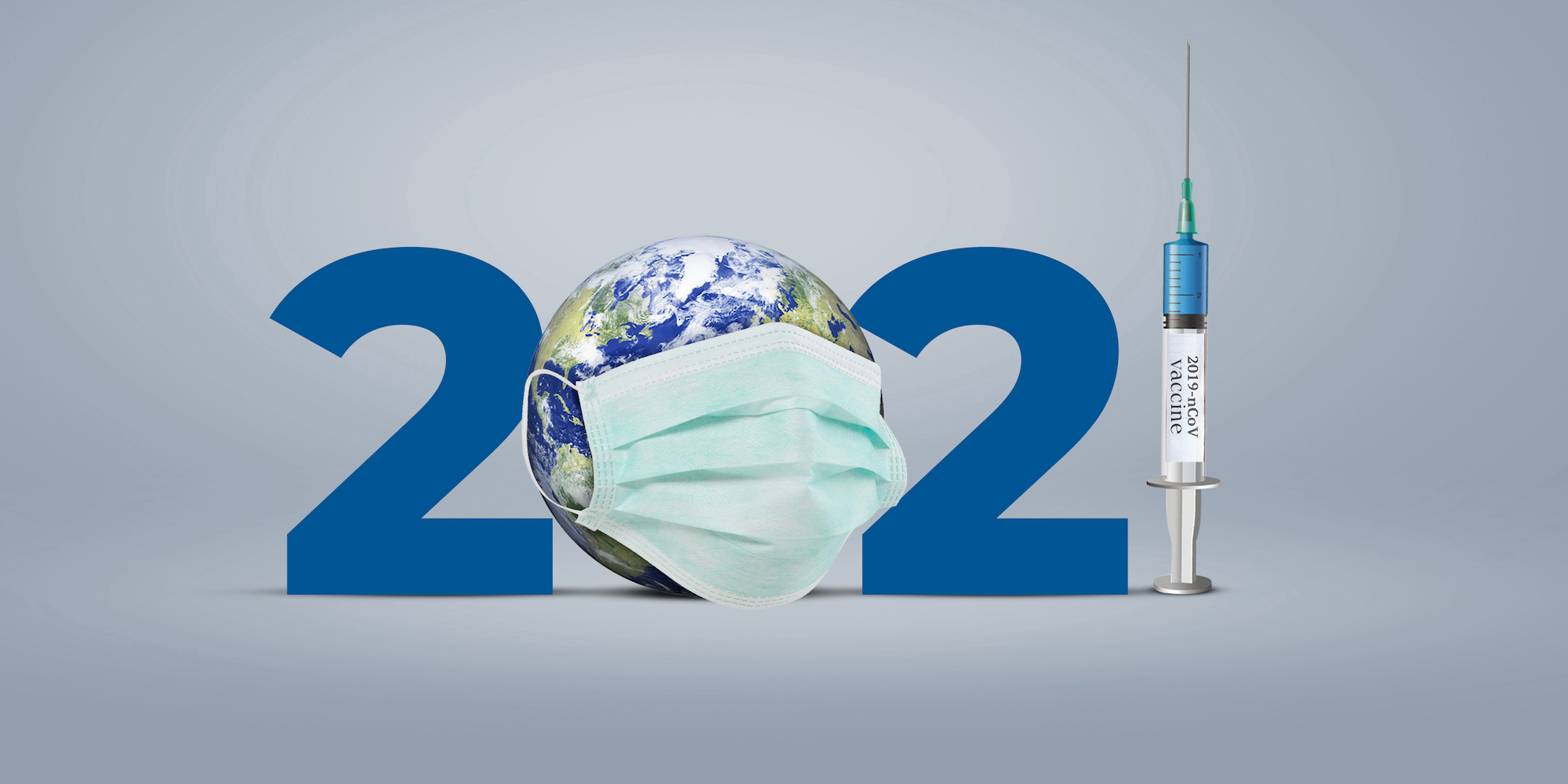
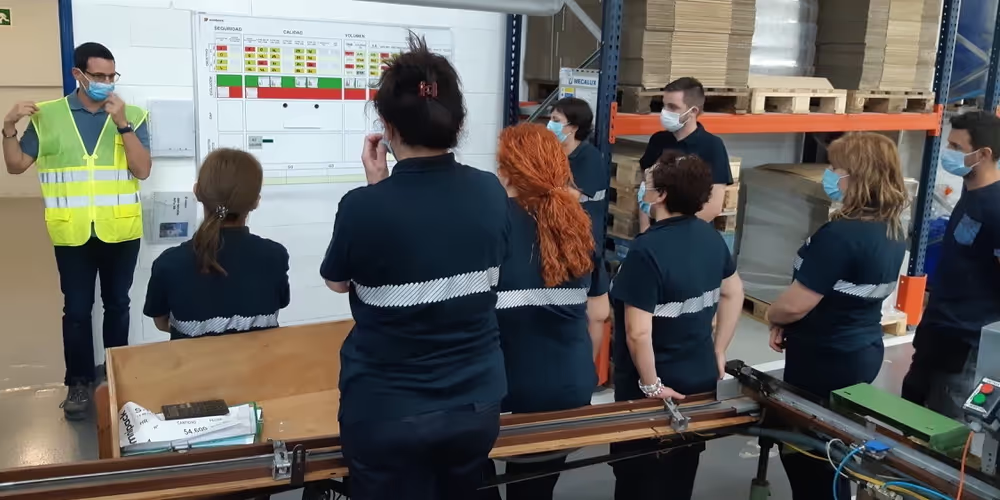
FEATURE – As 2020 finally draws to an end, our editor reflects on the year that was and discusses why the Lean Community is a such an important source of inspiration and hope.
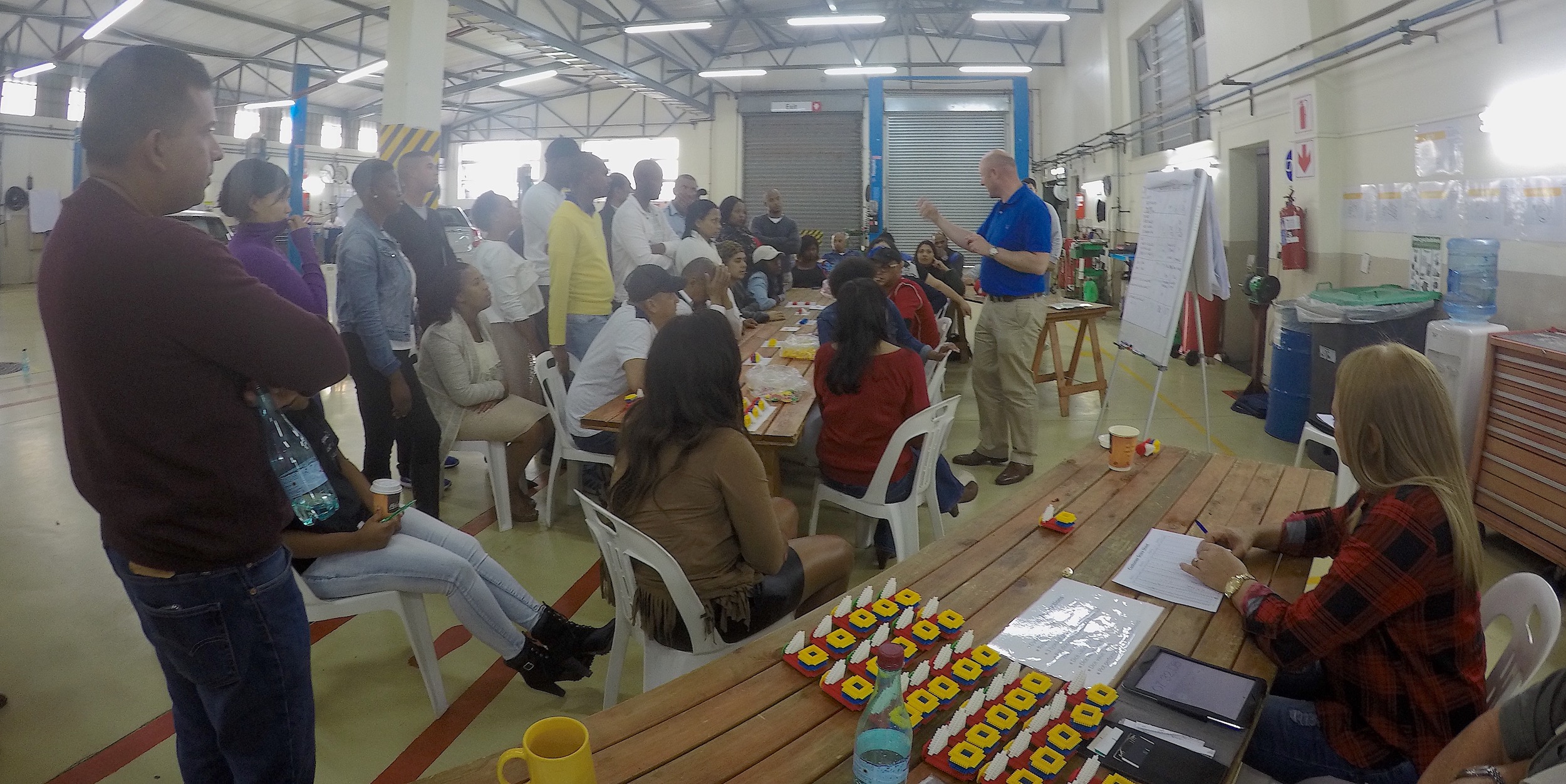
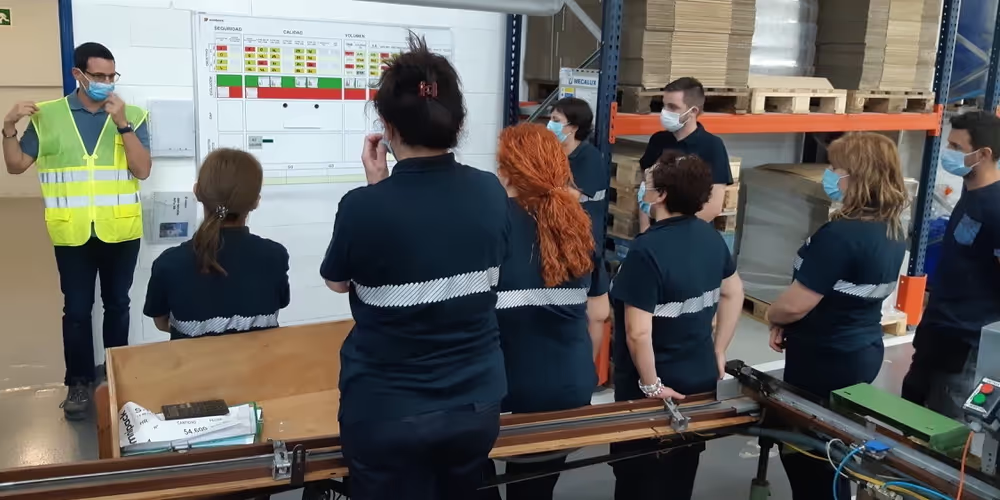
INTERVIEW – The Lean Enterprise Academy just launched the Lean Learning Journey, an online platform from which practitioners can pull the practical knowledge they need in their lean transformation.
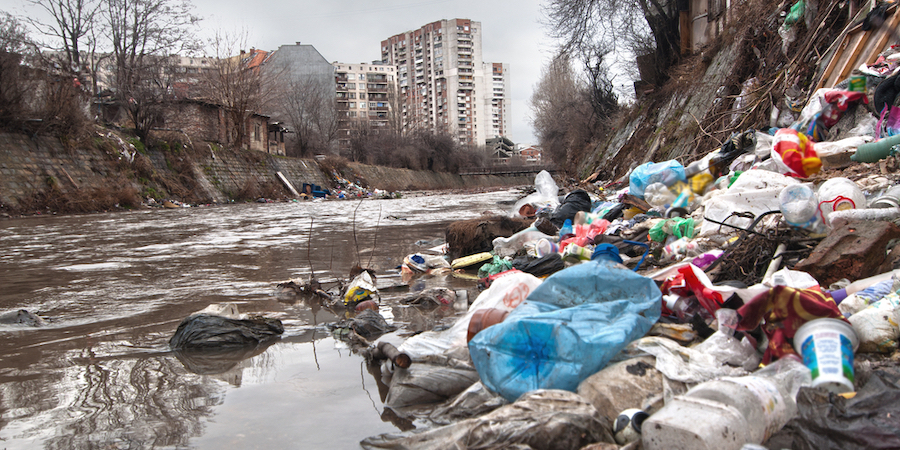
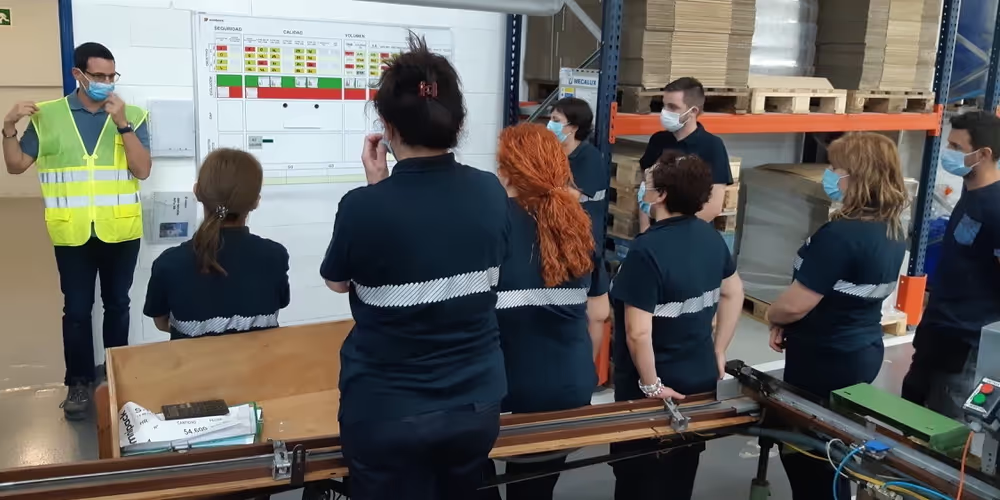
FEATURE – The transformational power of Lean Thinking allows us to see it as a way to solve some of the world’s biggest problems. Dan Jones explains why it can represent an alternative to our exploitation-based system.

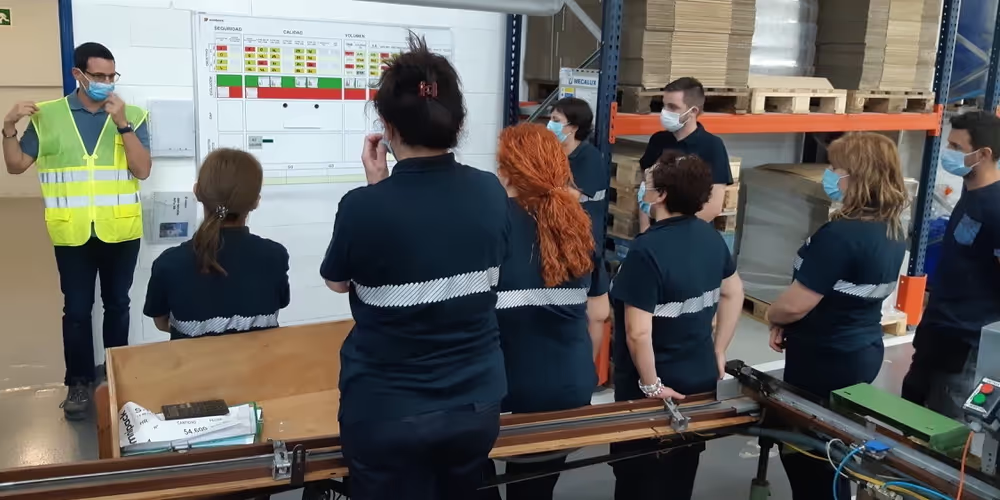
FEATURE – In business, the word “turnaround” refers to radical changes in the direction a company is moving toward. Here’s why Lean Thinking can increase the chances of success of such endeavors.
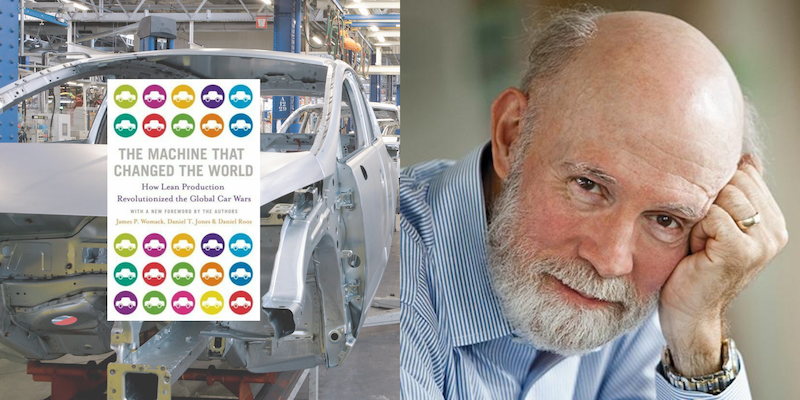
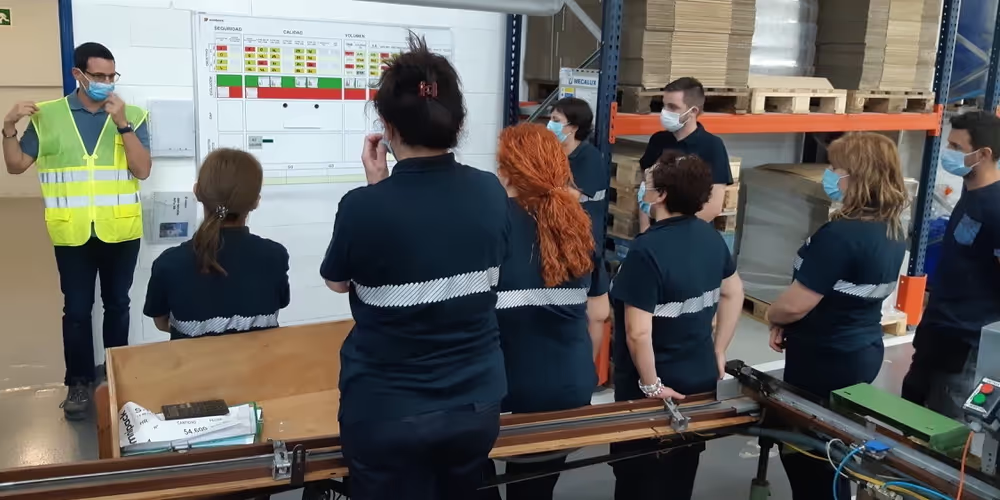
INTERVIEW – Thirty years ago, a book introduced lean thinking to the world, started a global movement and transformed business forever. Our editor caught up with one of the authors.
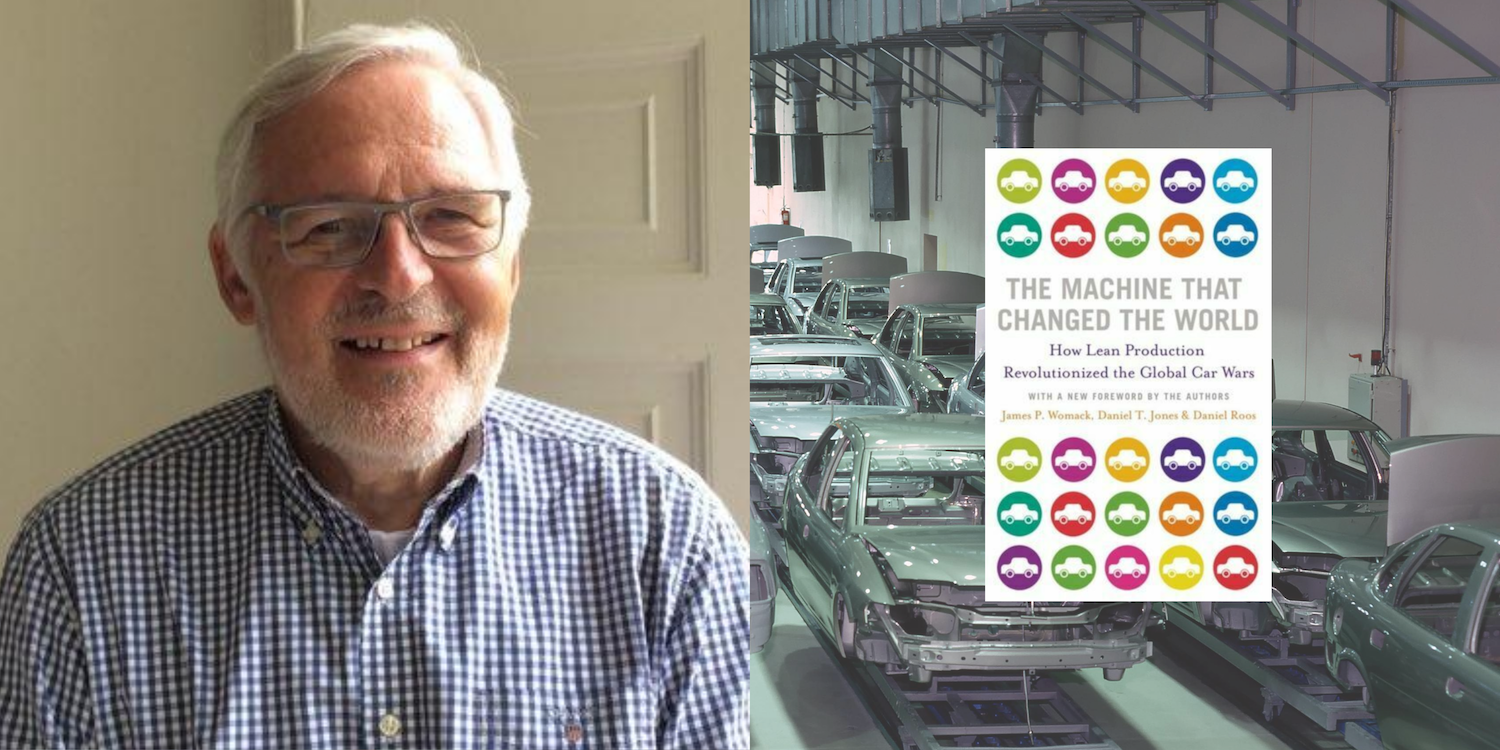
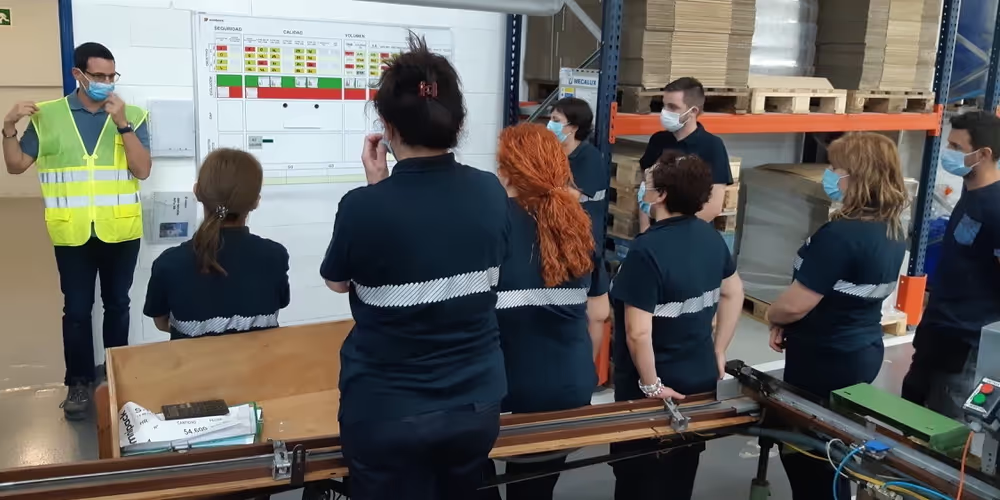
INTERVIEW – In the fall of 1990, a book was published that would kickstart a revolution in business. This week we are catching up with the authors to understand where we are and where we are headed. First up, Daniel Jones.
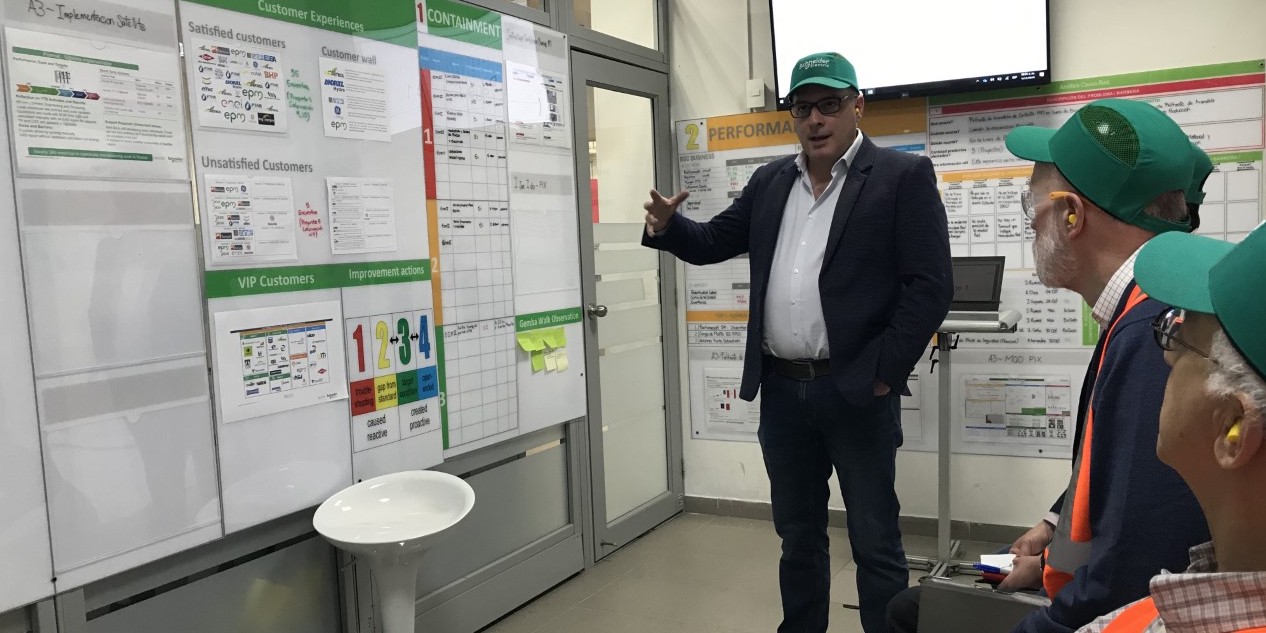
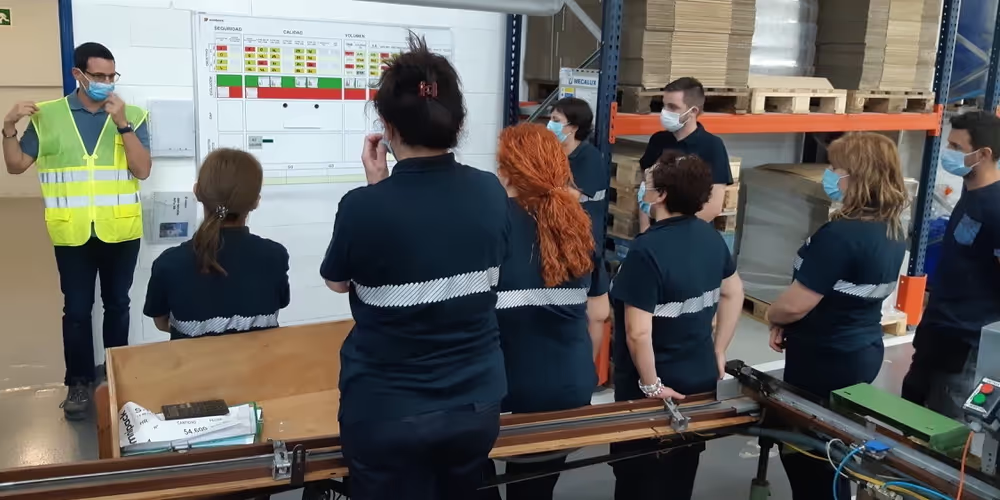
FEATURE – A lean management system is necessary to effectively run a business. Can Art Smalley’s four types of problems framework help such a system to focus on what’s really important?
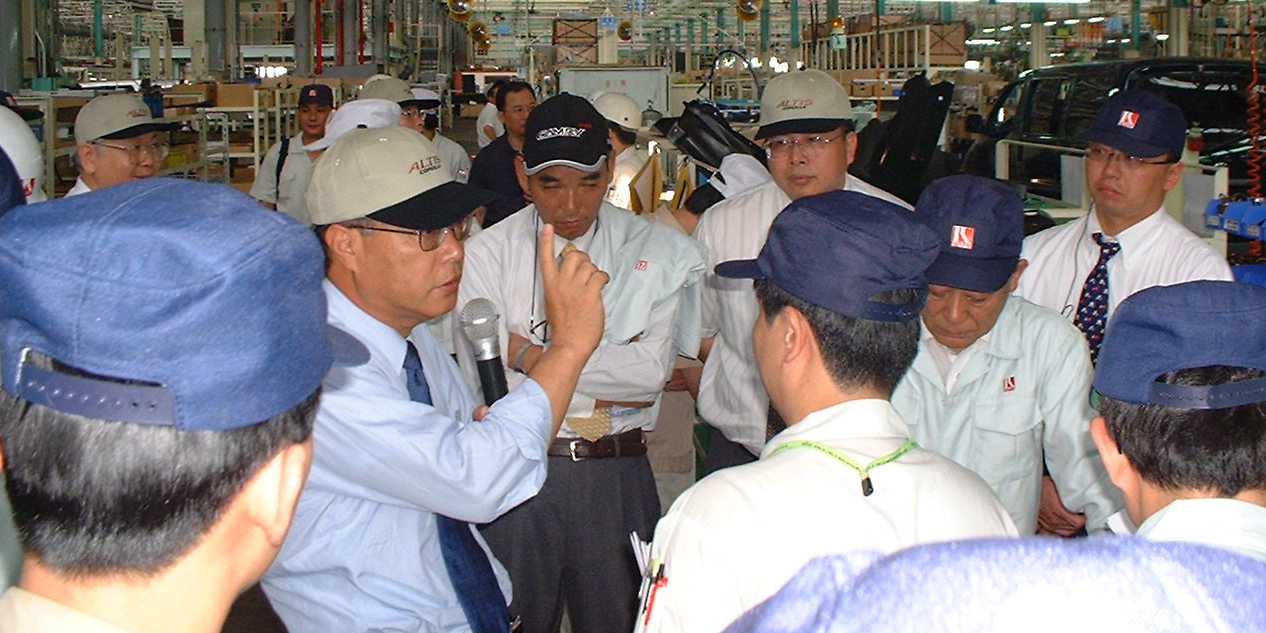
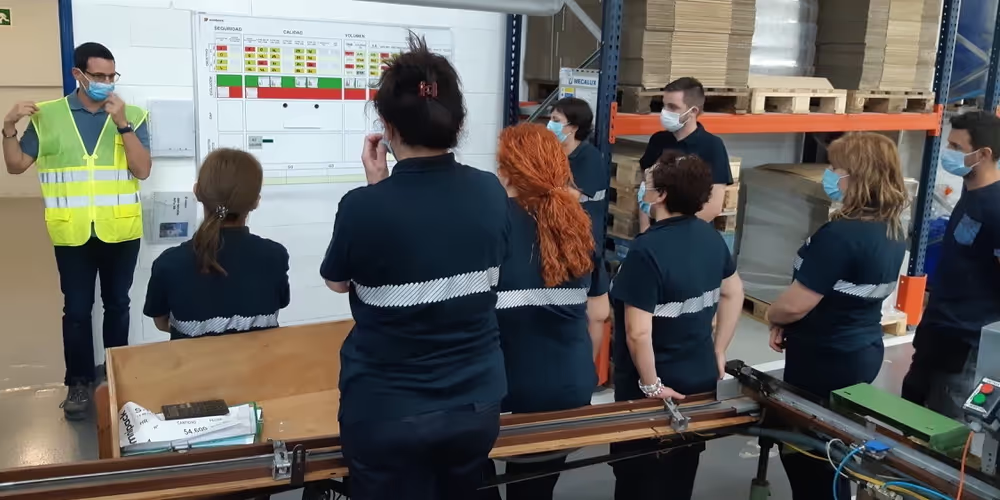
FEATURE – This intimate account looks back at the time one of the authors spent working with Harada-san and how it shaped his career and encouraged him to spread TPS knowledge.
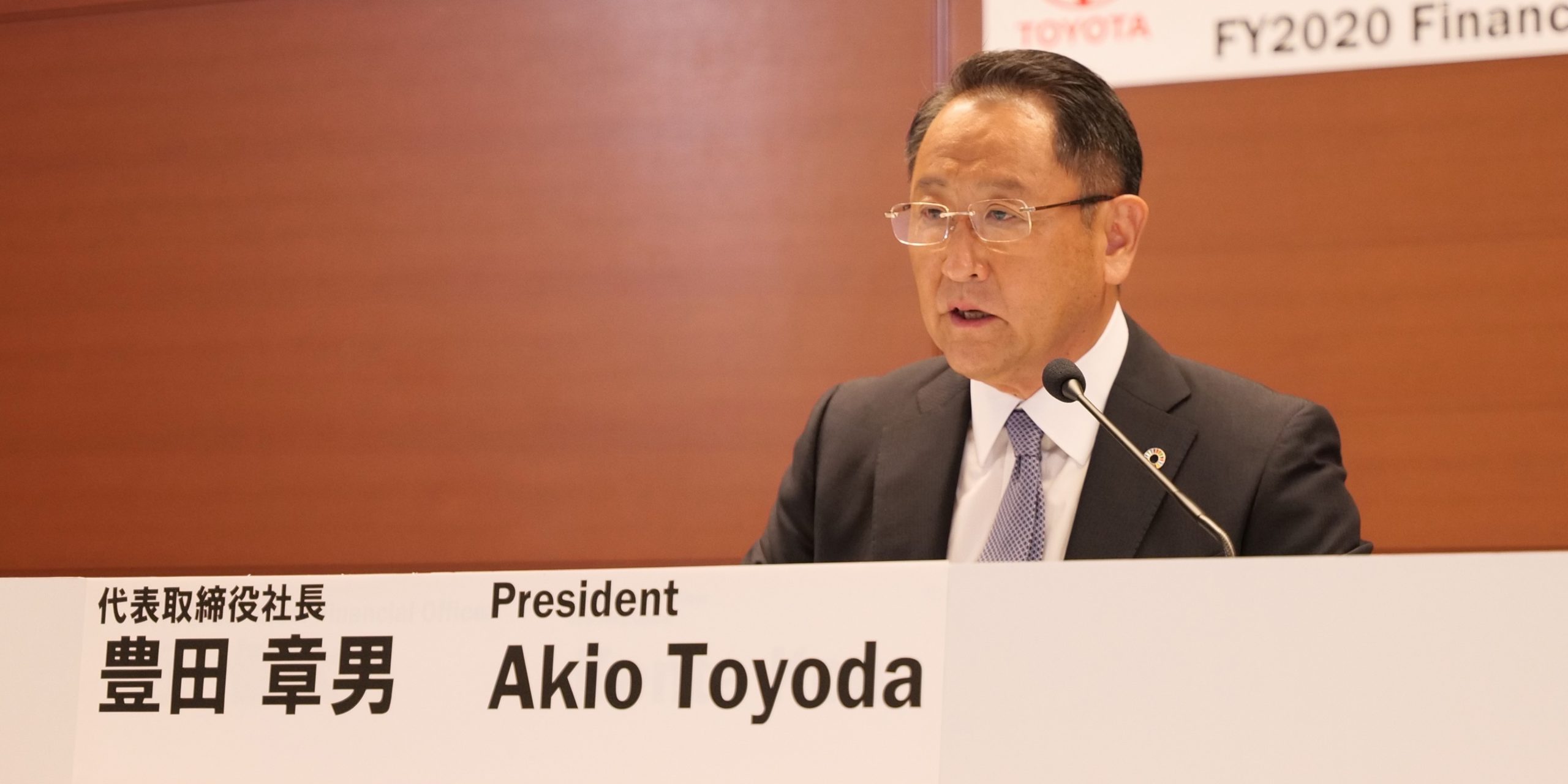
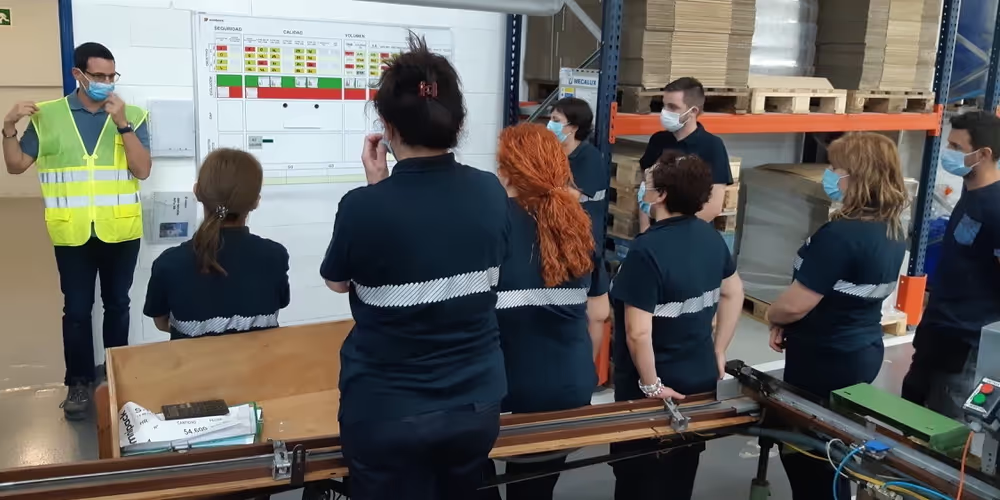
FEATURE – Akio Toyoda’s May 12th press conference to present Toyota’s financial results offers great insights into how the company is reacting to the pandemic, say Jeff Liker and John Shook.
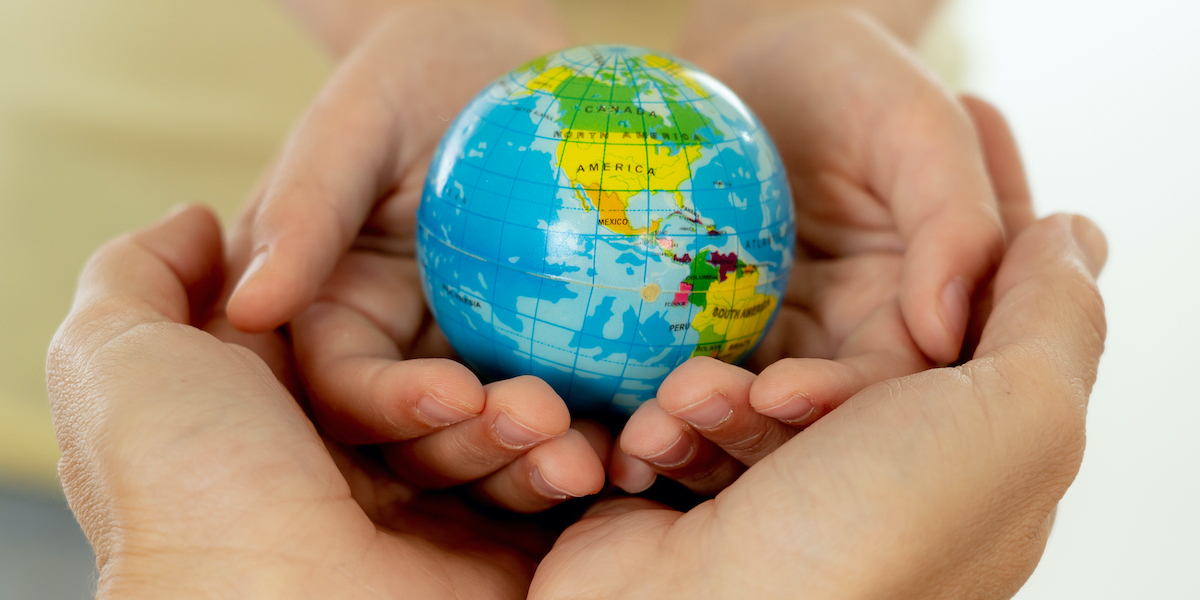
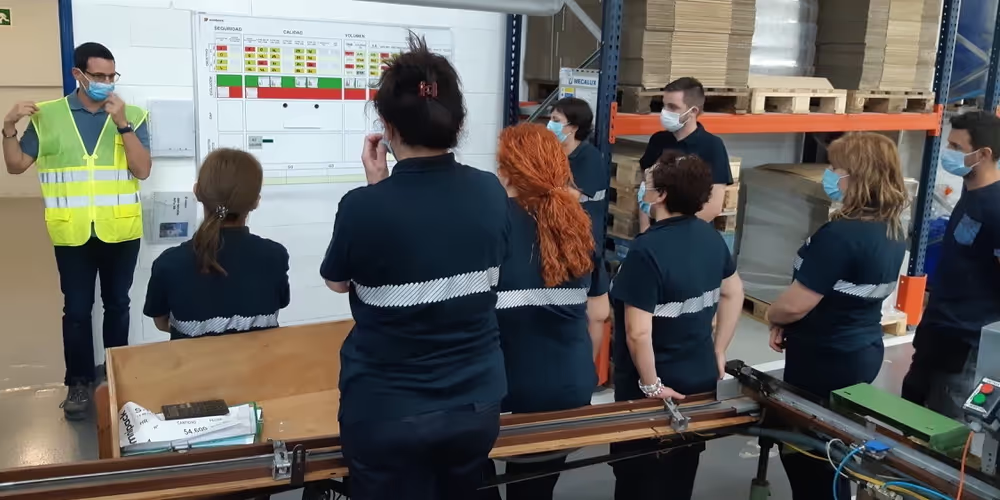
FEATURE – Looking to the future, the author encourages us to challenge obsolete ideas and seize the opportunity provided by Lean Thinking to make the world a better place for all.
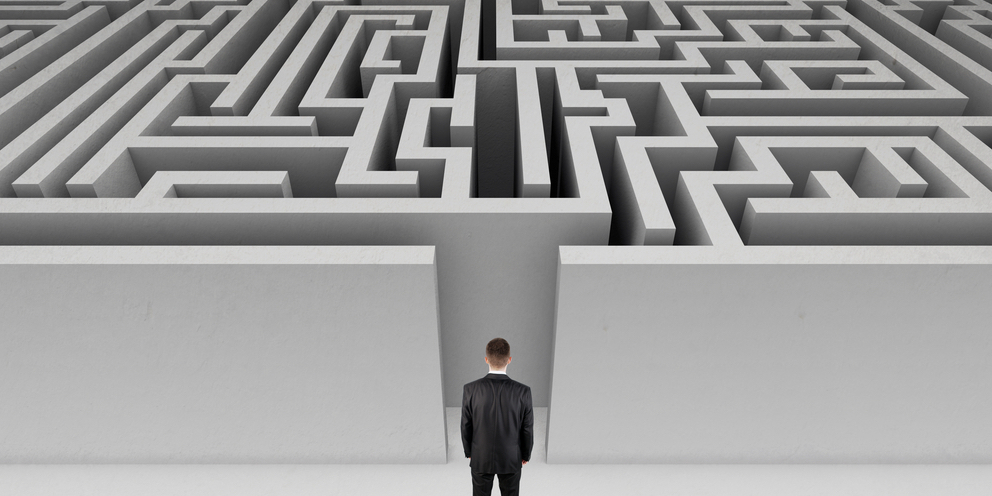
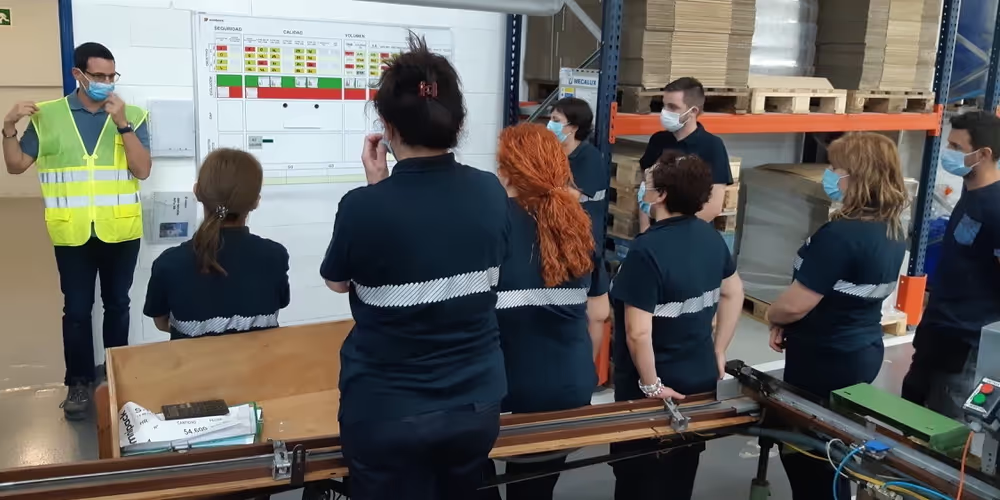
FEATURE – As businesses struggle with disruption and an uncertain future in the midst of the Covid-19 crisis, the author suggests they turn to lean daily management and get into an experimentation mindset.
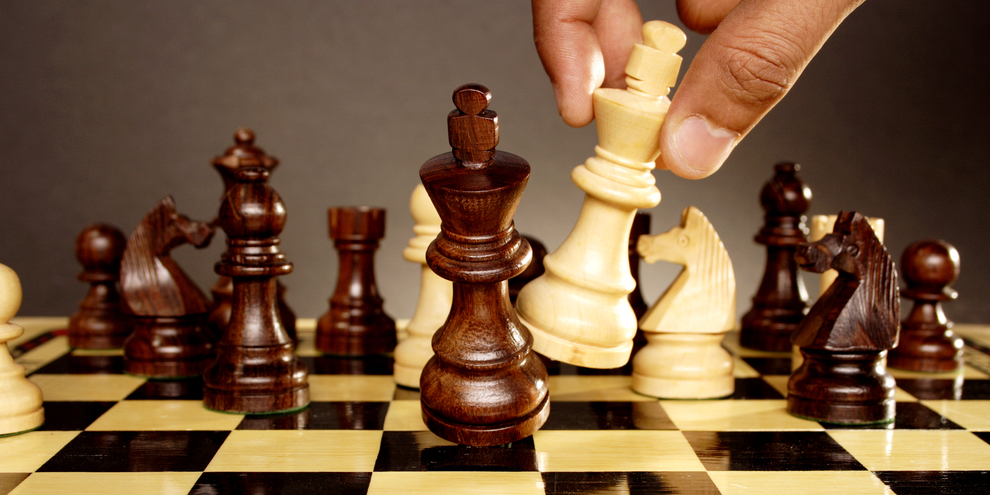
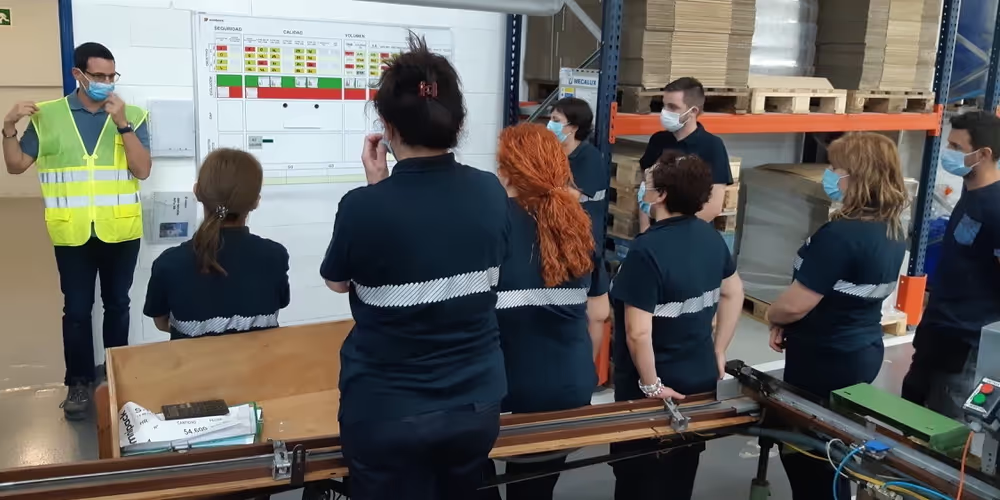
ROUNDUP – In the last roundup on lean tools and concepts of the year, our editor collects and curates the best articles on strategy deployment (hoshin kanri).
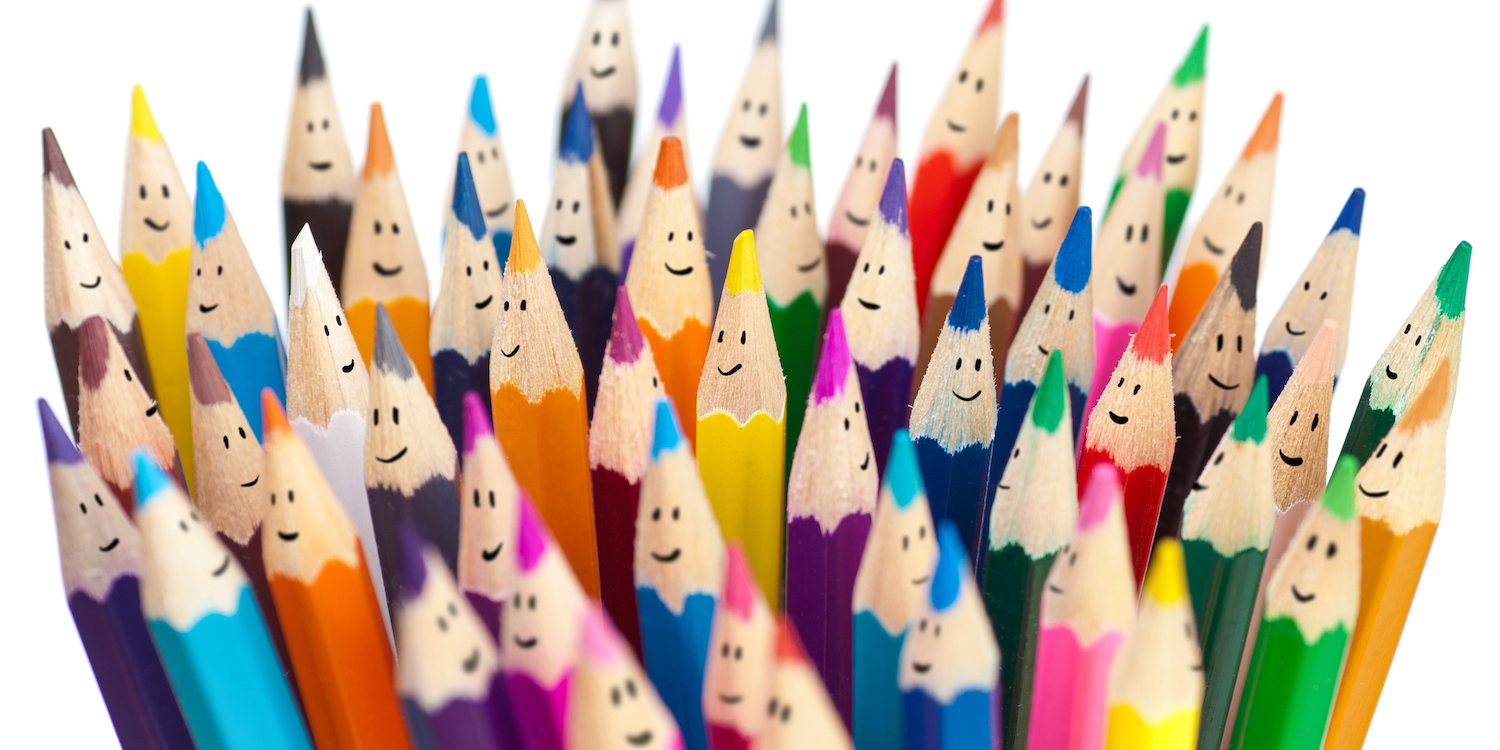
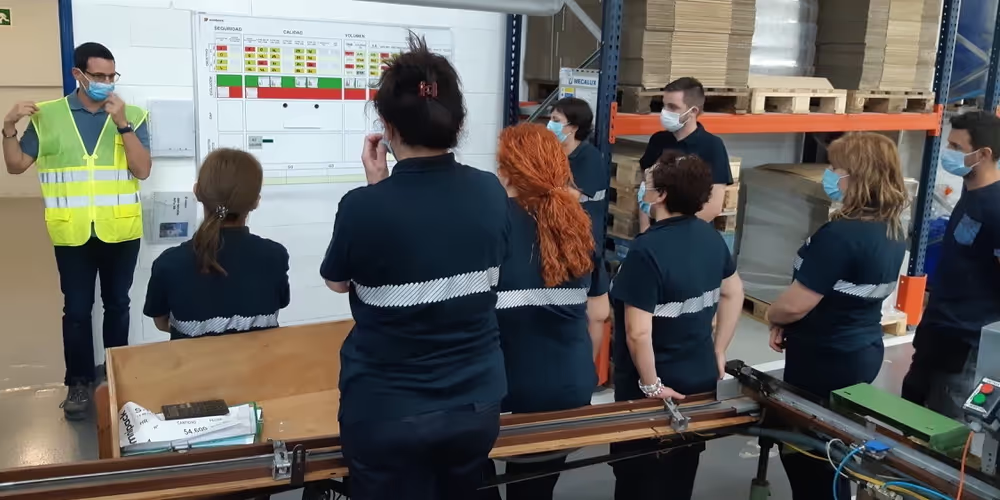
COLUMN – As individuals, how do we relate to the Lean Community? And what motivates us to stubbornly continue down the improvement path, often against all odds?
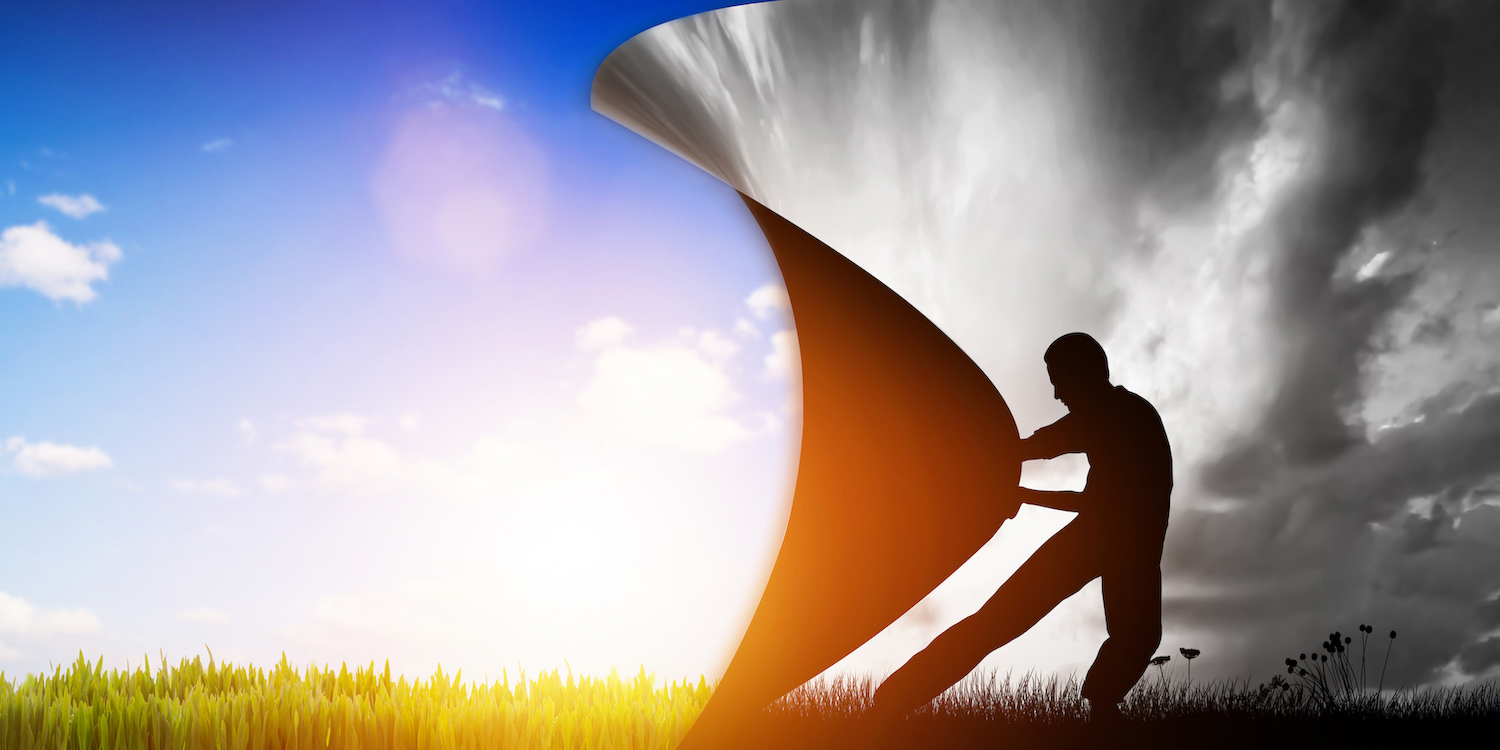
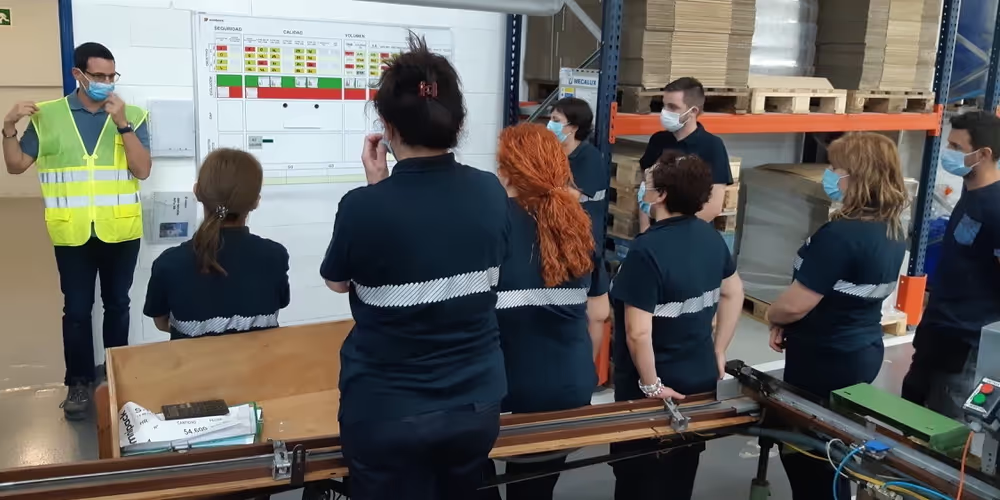
FEATURE – The author discusses how the daily practice of lean thinking develops perseverance and the grit a leader needs to improve an organization.
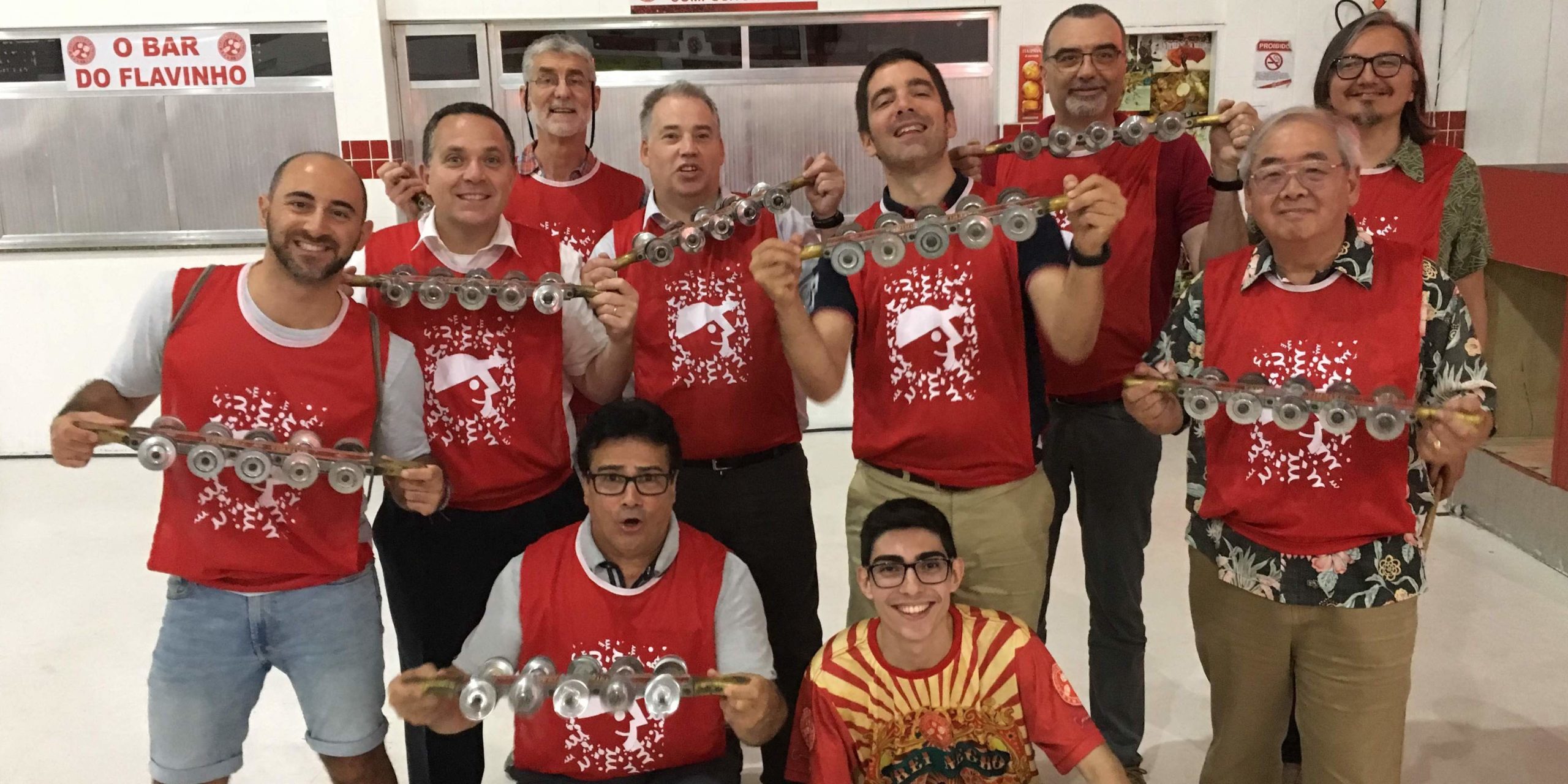
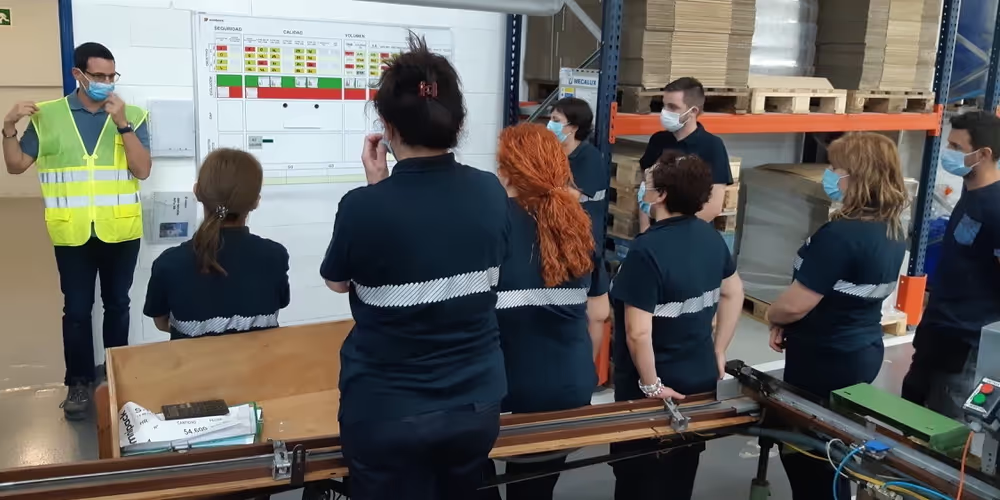
FEATURE – Much like lean management, attaining perfection in music requires constant practice. The author looks back at his musical past and at a recent Lean Global Network samba gig.
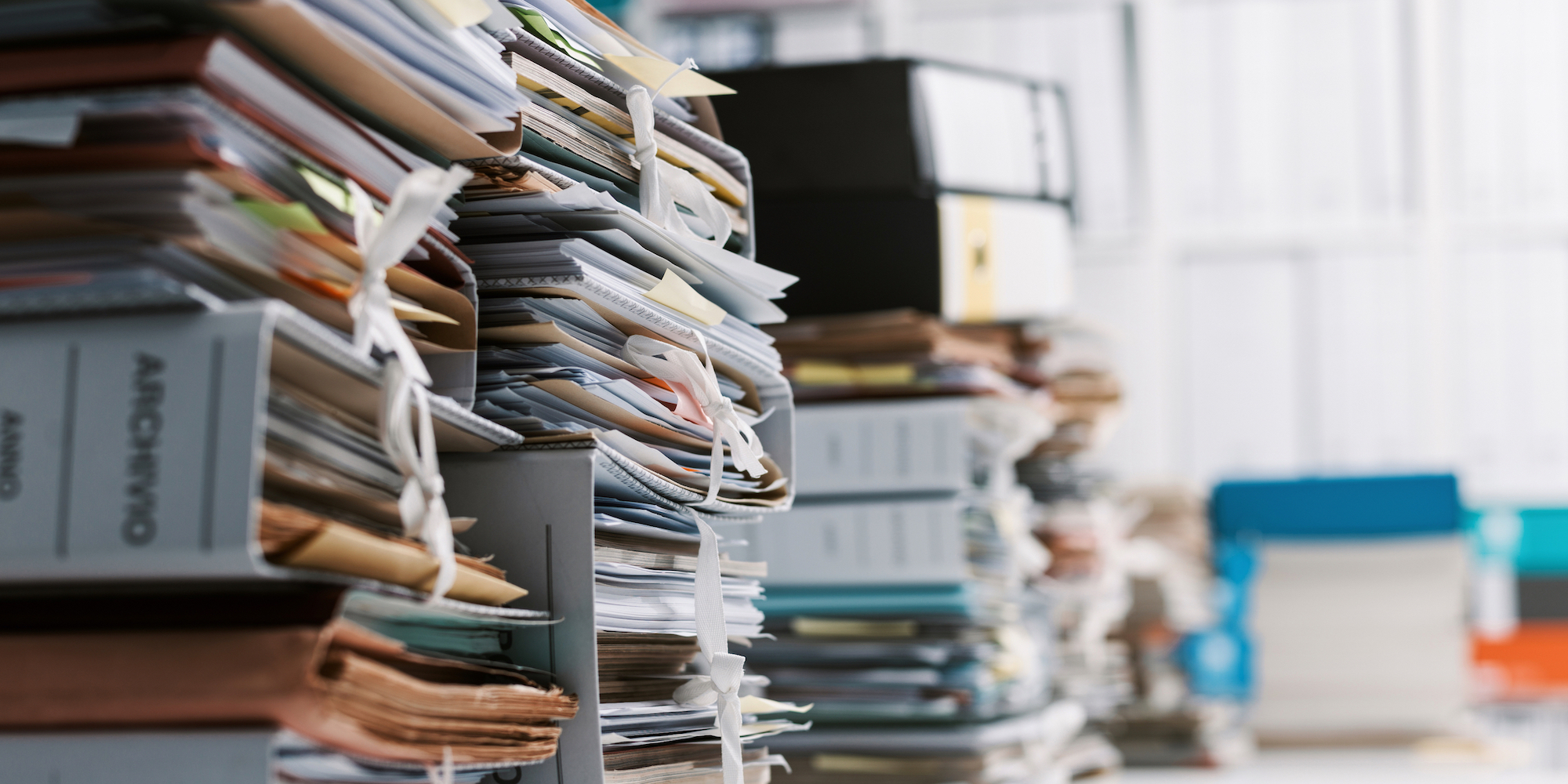
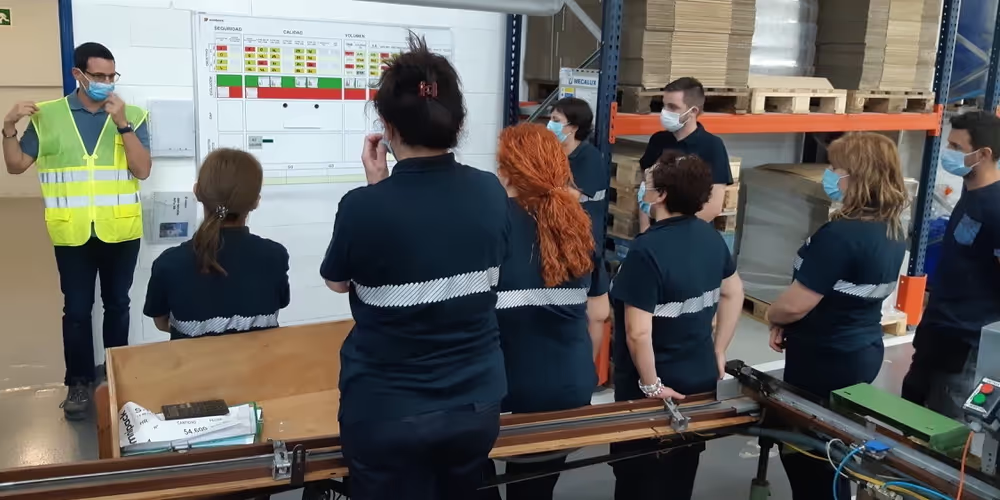
FEATURE – As our social systems grow, we need an effective way to manage them. This makes bureaucracies an inescapable part of life for our society and businesses. But how can we mitigate their negative effects?
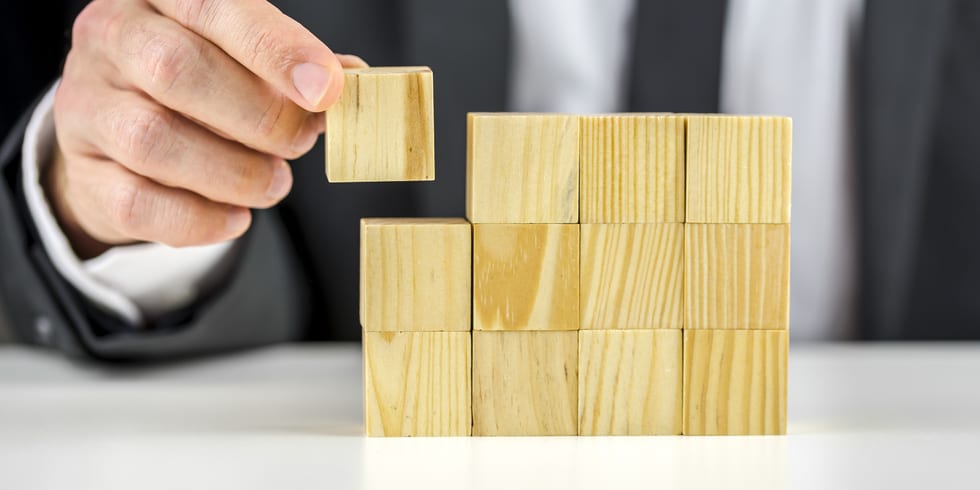
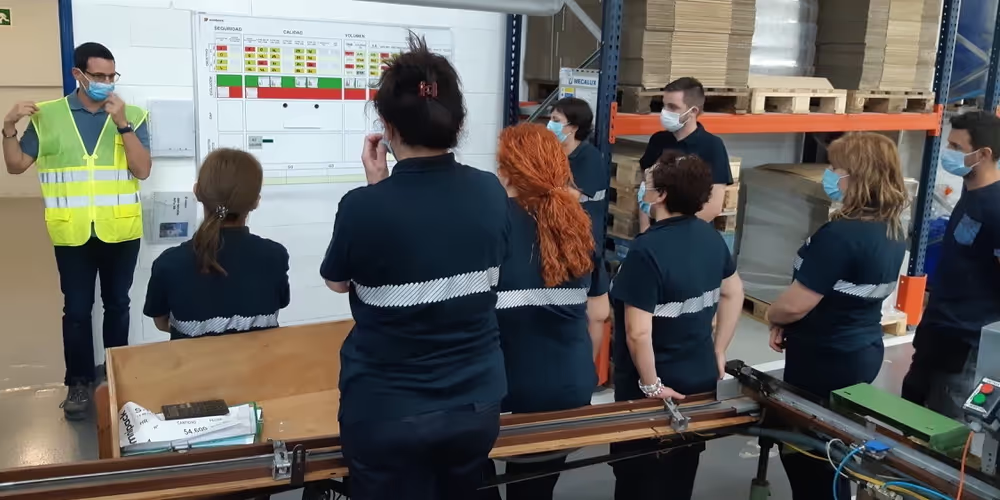
FEATURE – In this compelling read, the author discusses lean thinking as a system for learning that challenges our assumptions and tells us why blindly applying “best practices” takes us nowhere.
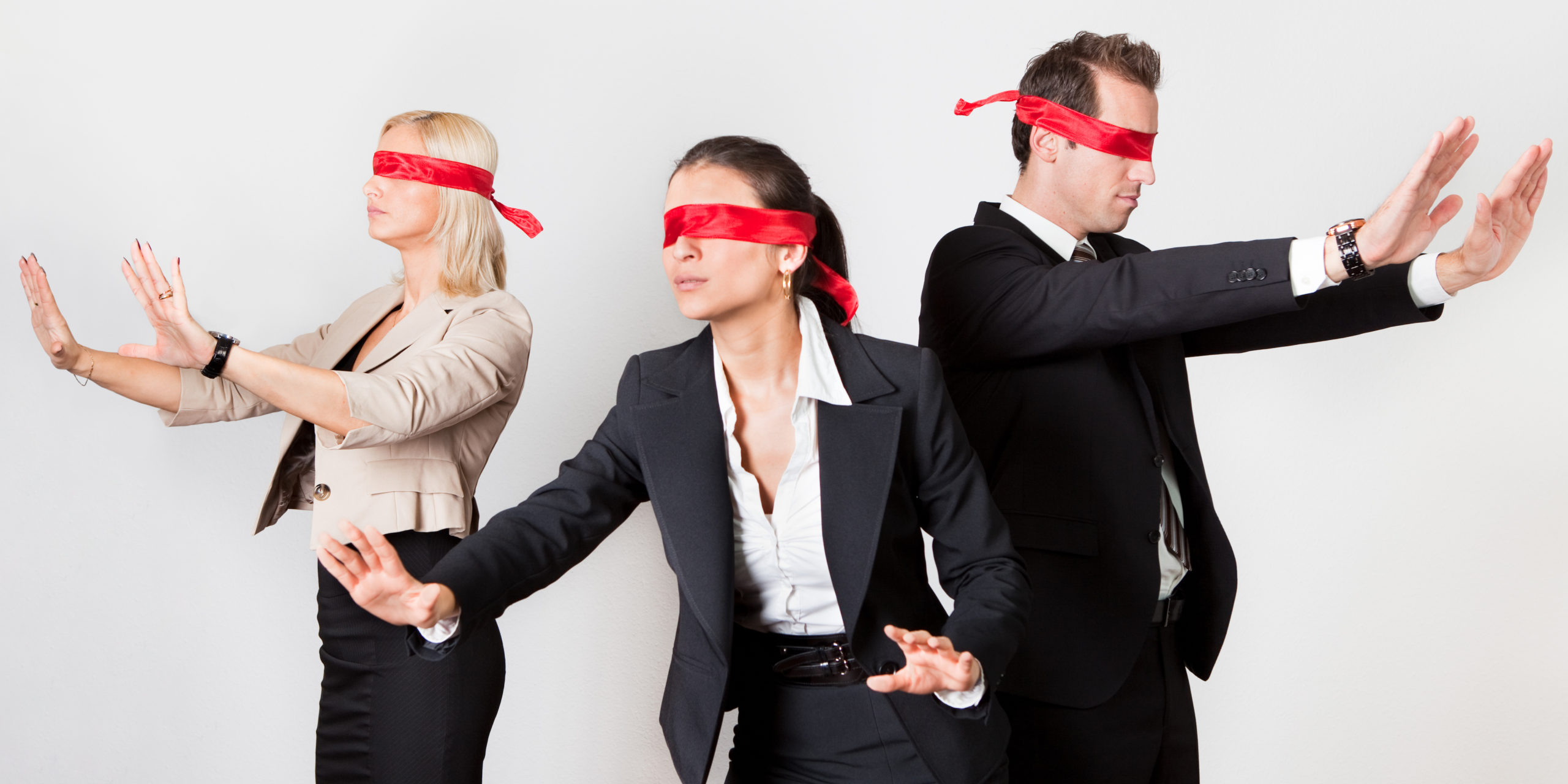
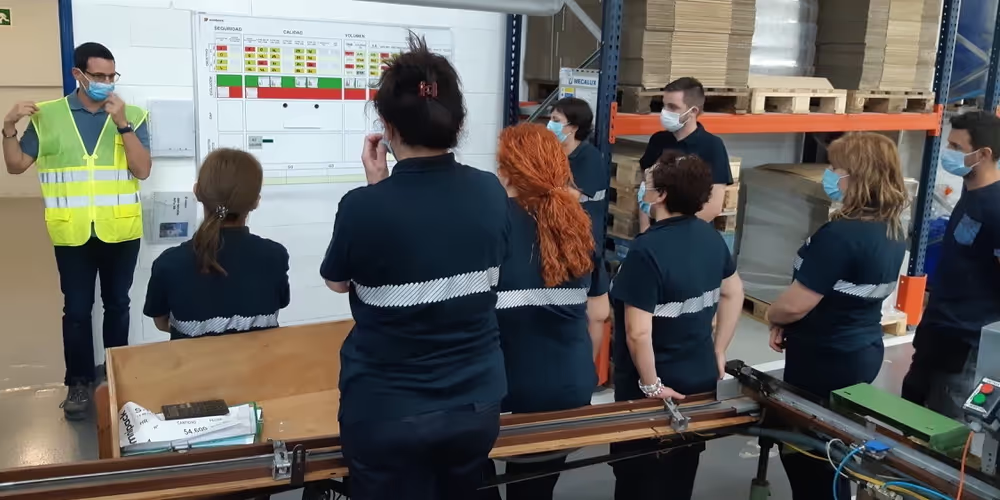
FEATURE – While at Starbucks, the author learned the importance of collaboration among the key functions of Operations, HR and Finance to advance a lean transformation.
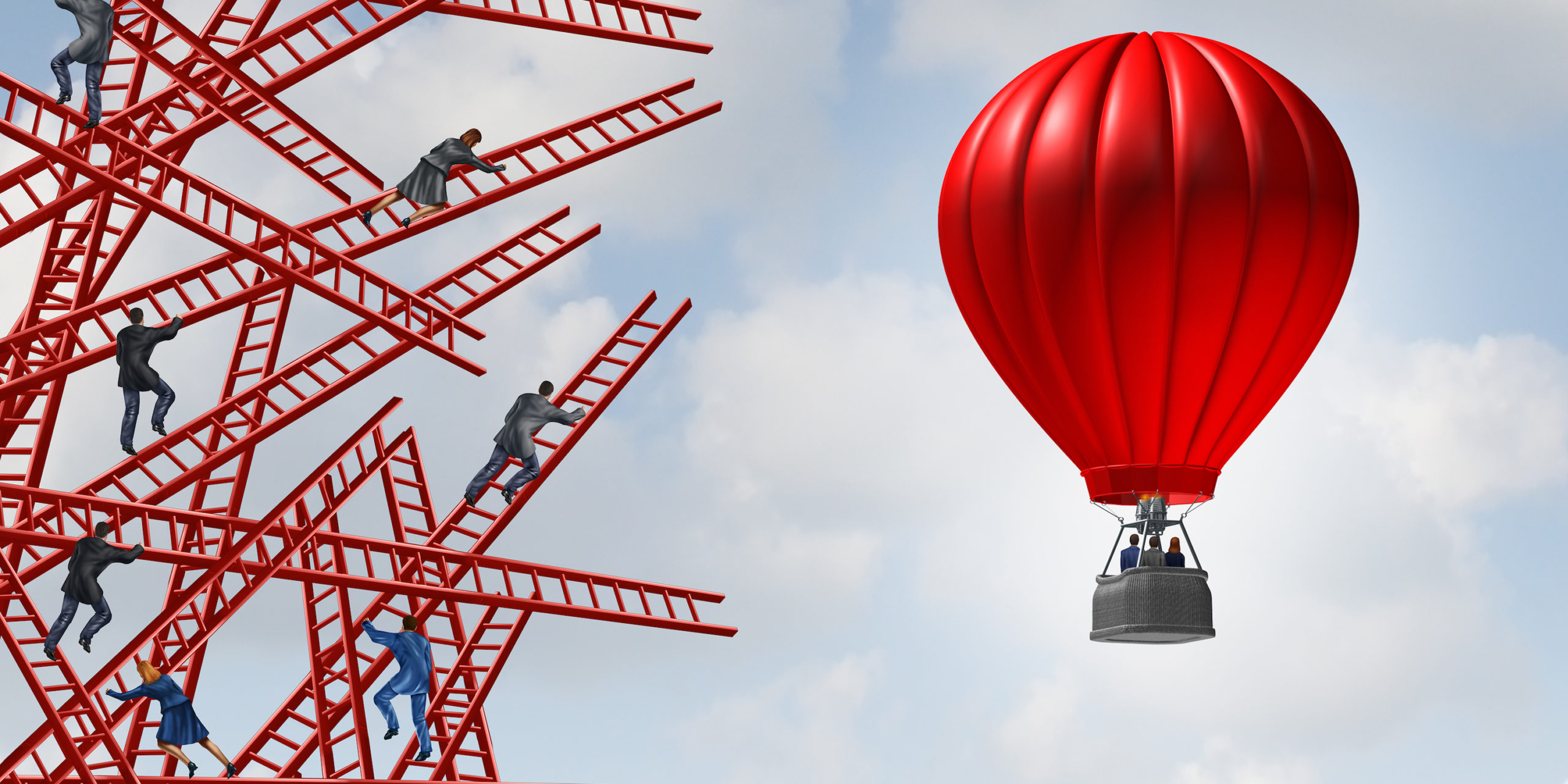
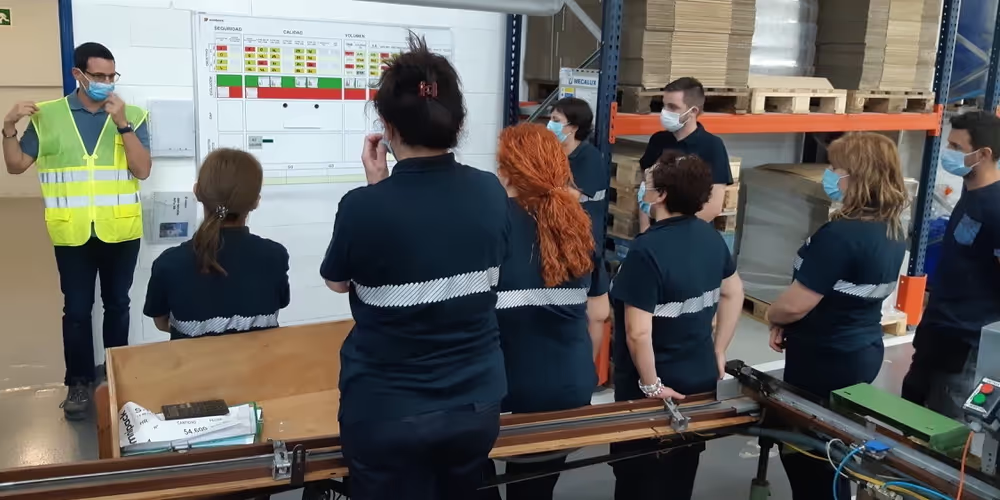
FEATURE – In the age of complexity and disruption, flowing value to customers as quickly as possible is critical. The new Toyota Flow System strives to address this issue.
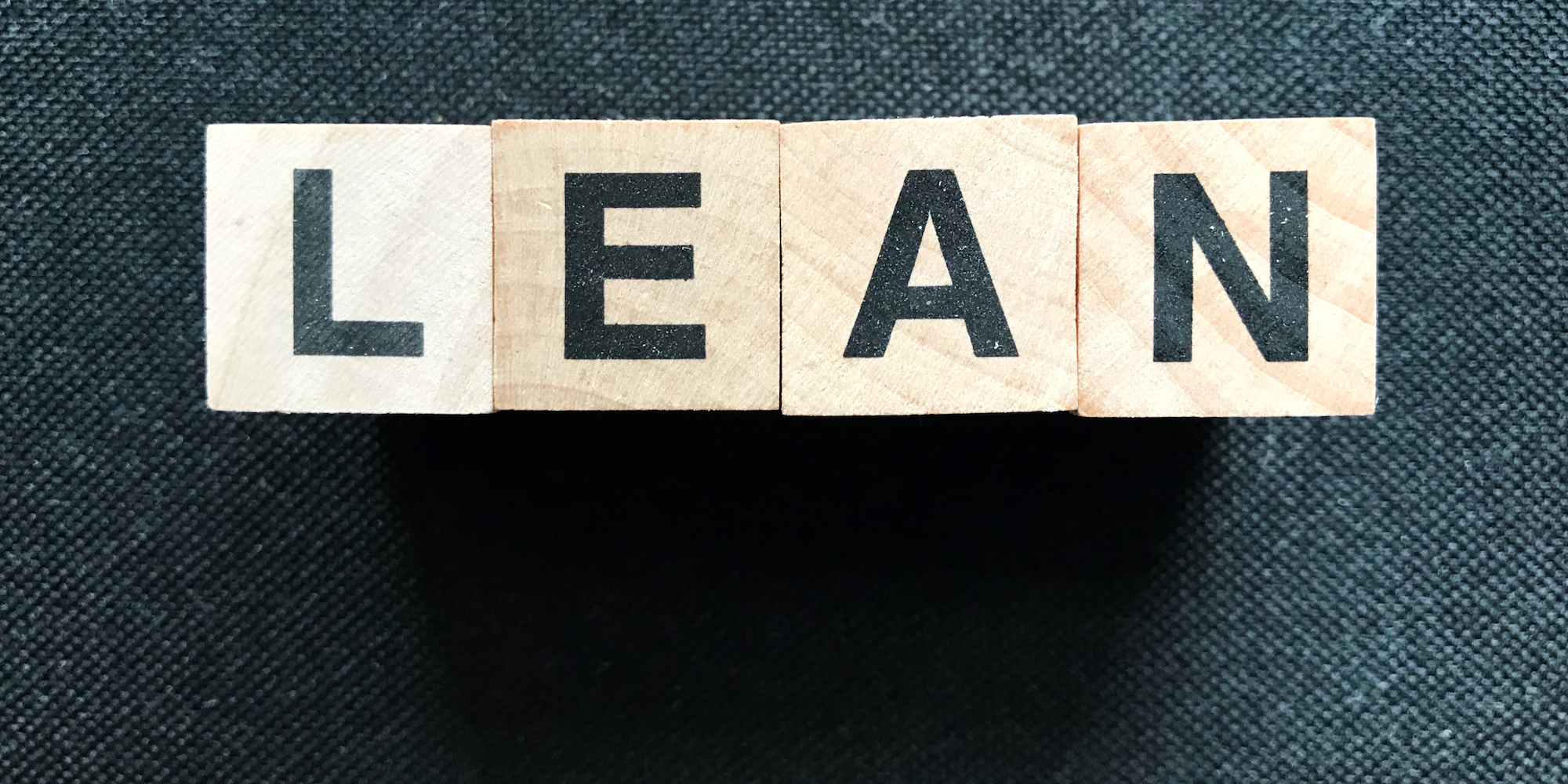
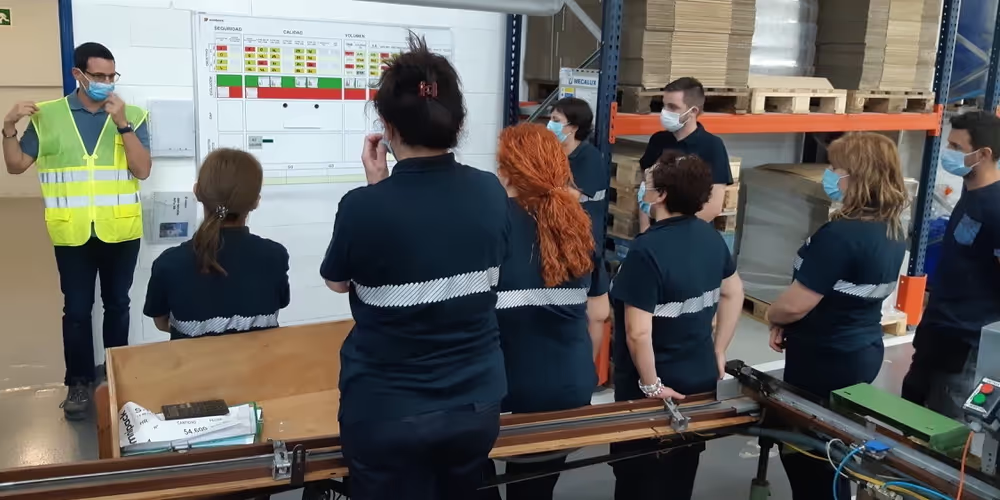
FEATURE – In this article, the author reflects on how his understanding of lean thinking evolved over time – as did the way he defined it.
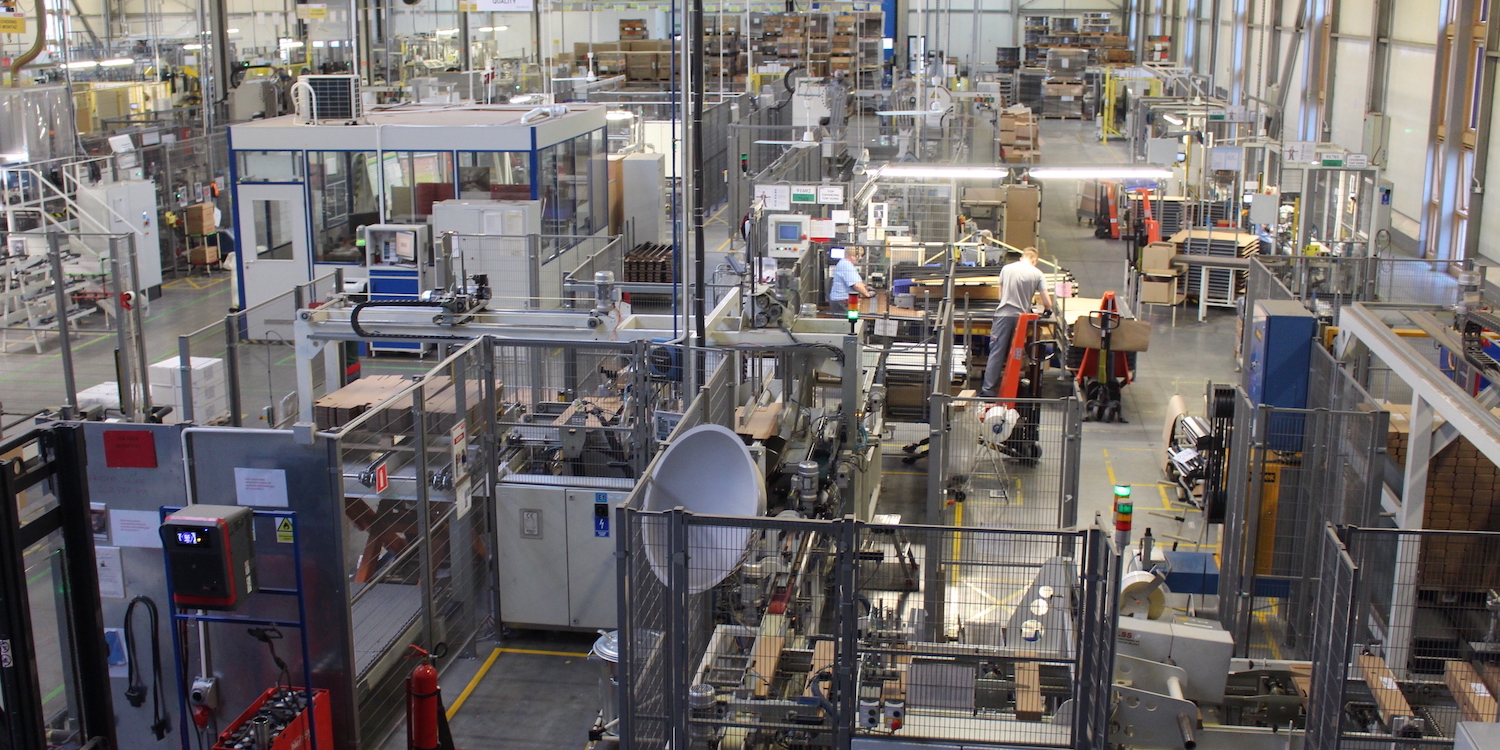
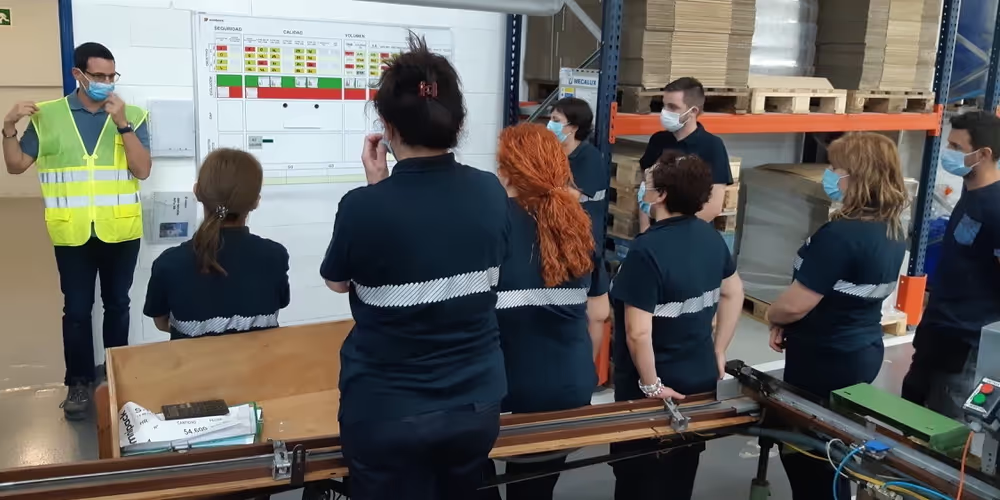
FEATURE – Successfully engaging people and building a solid daily management system is allowing a Velux factory in Poland to fulfill its strategic goals.
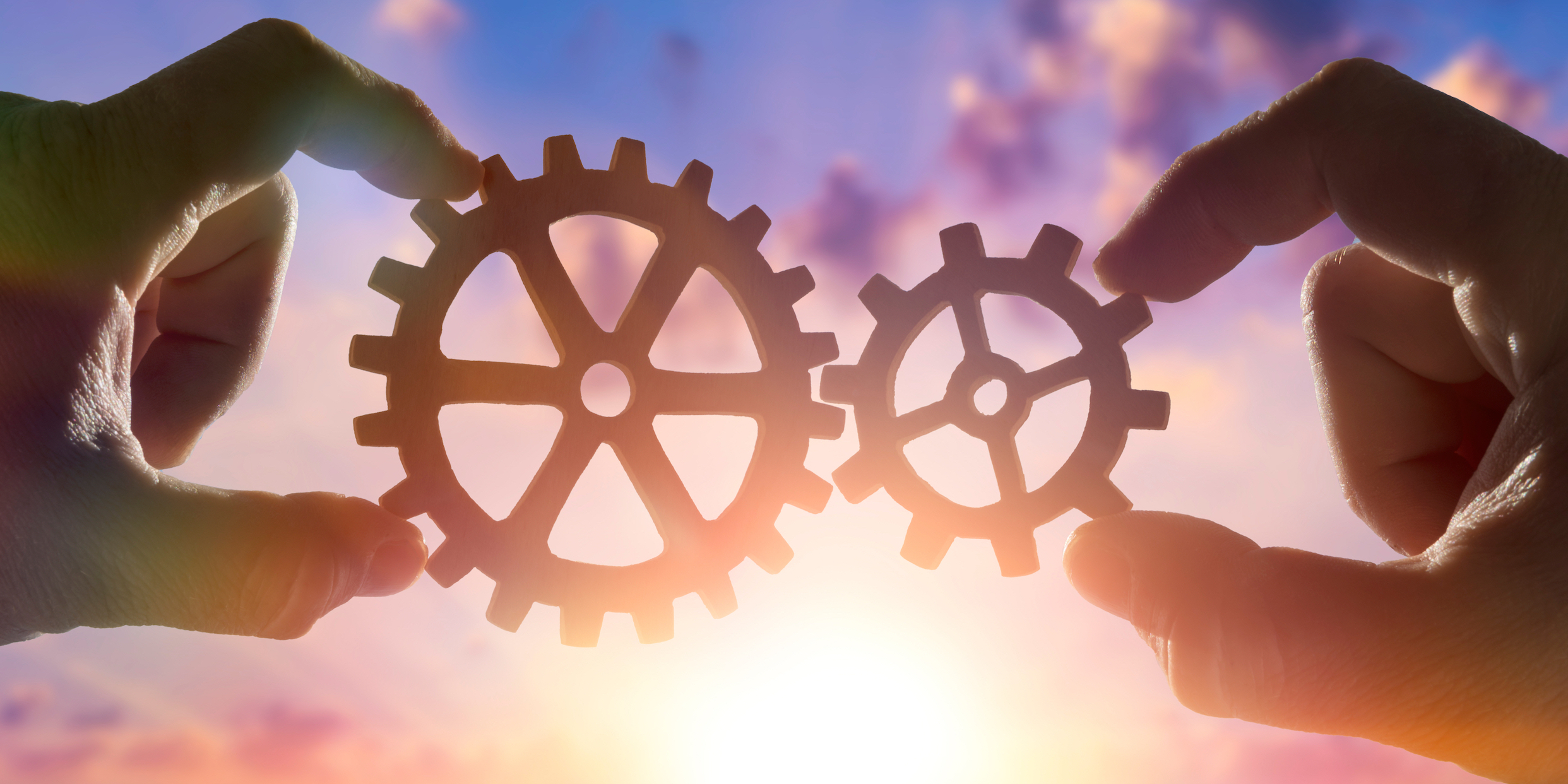
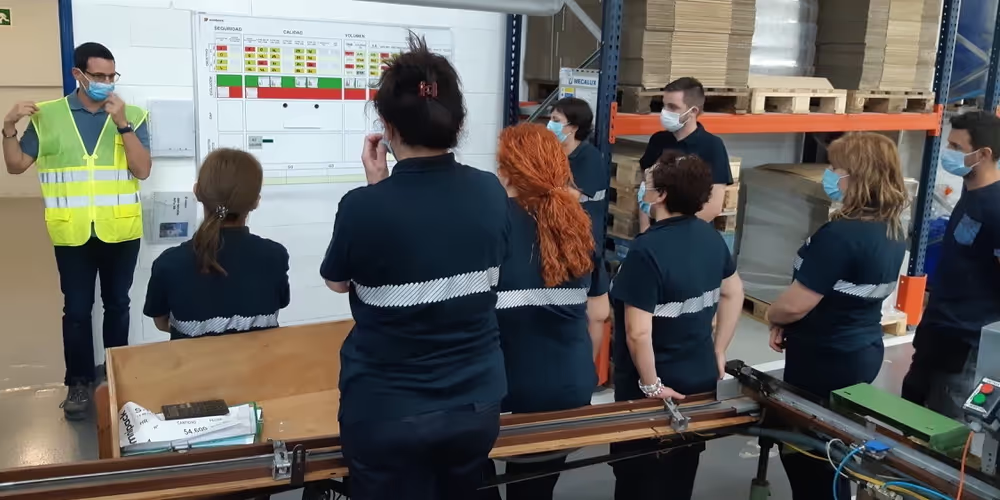
FEATURE – One of the things making lean thinking so hard to explain in general terms is its dual nature as both an organizational and managerial approach. The authors explain how to handle this tension.
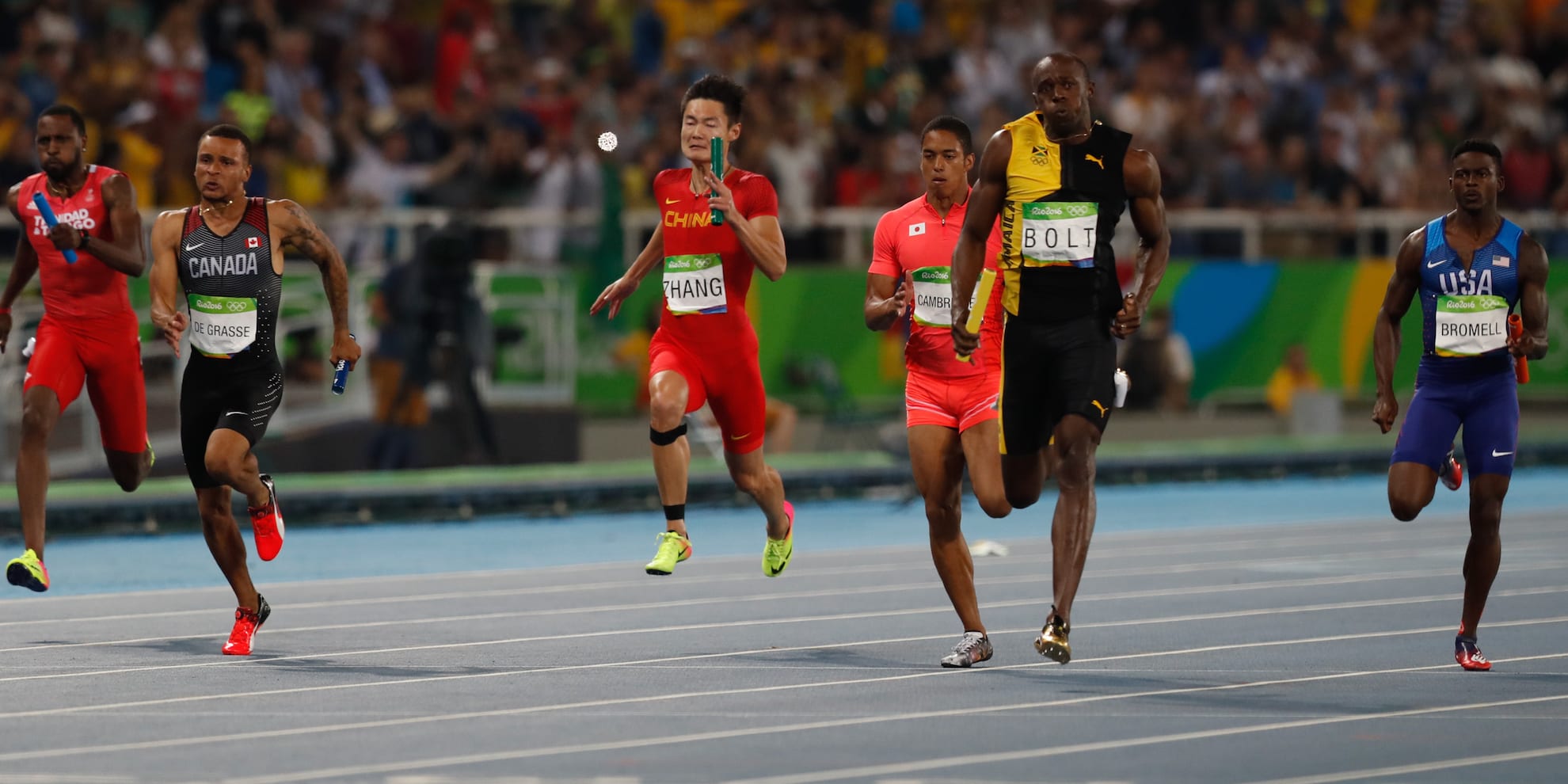
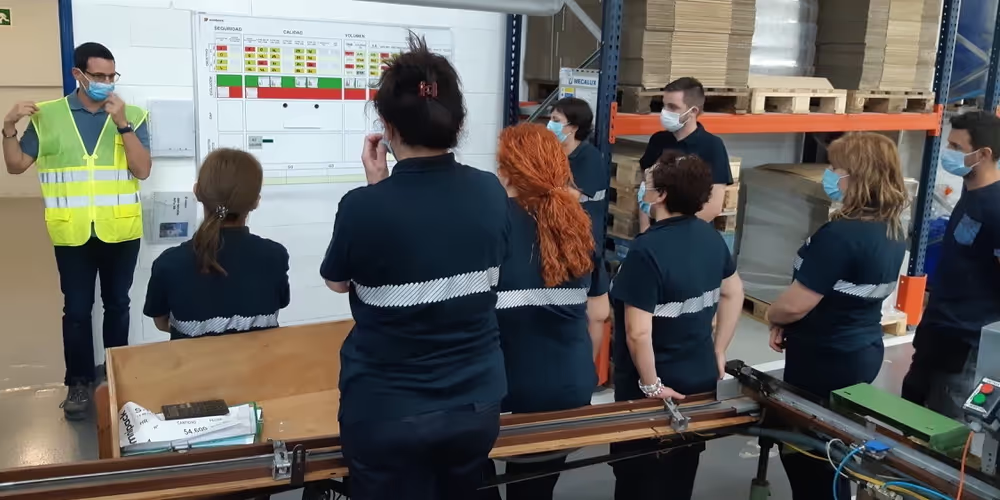
FEATURE – At the 2016 Olympics in Rio, the Japanese Men’s 4x100m relay team went from being the underdogs to winning a silver medal by apply lean problem solving.
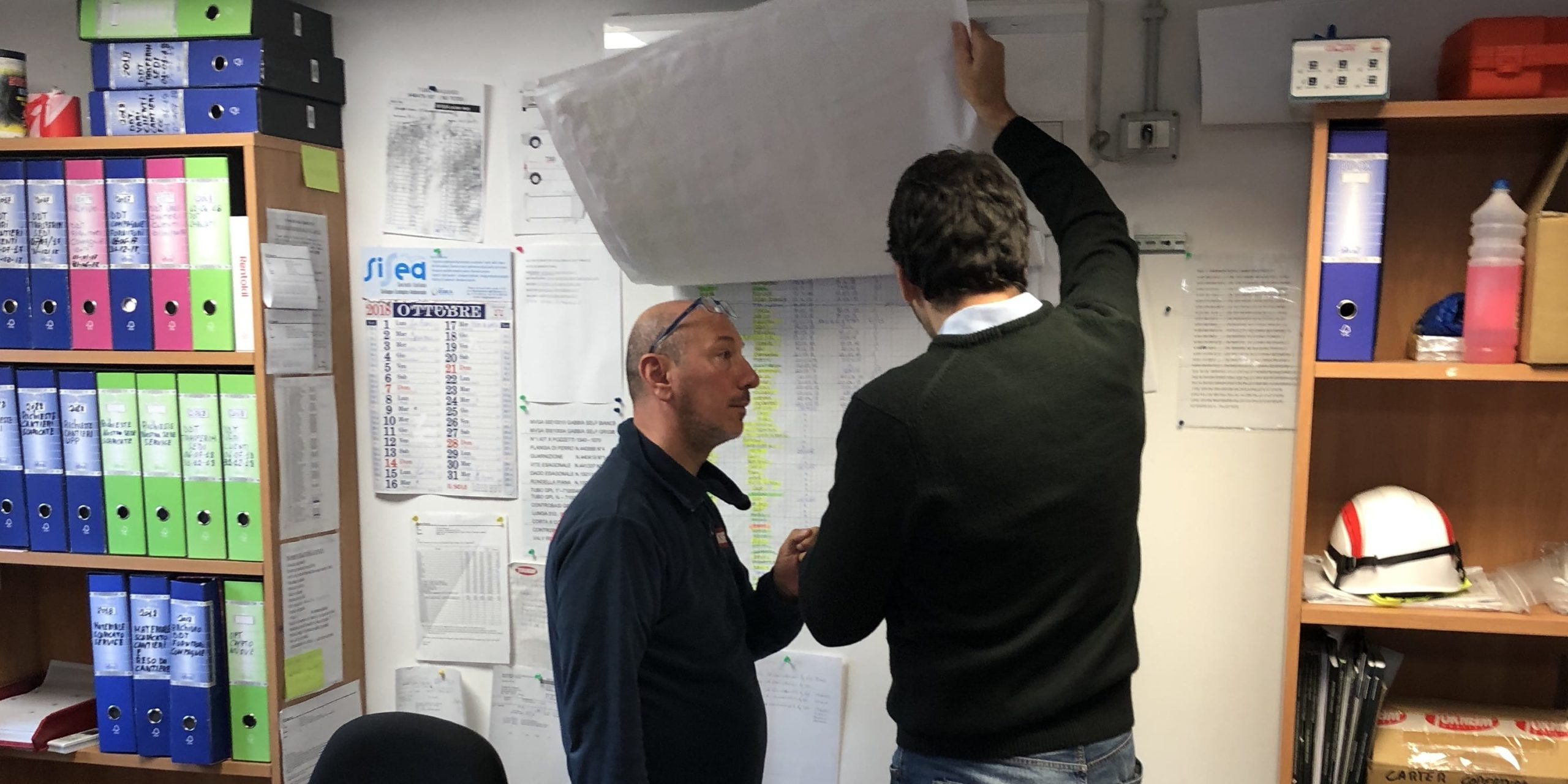
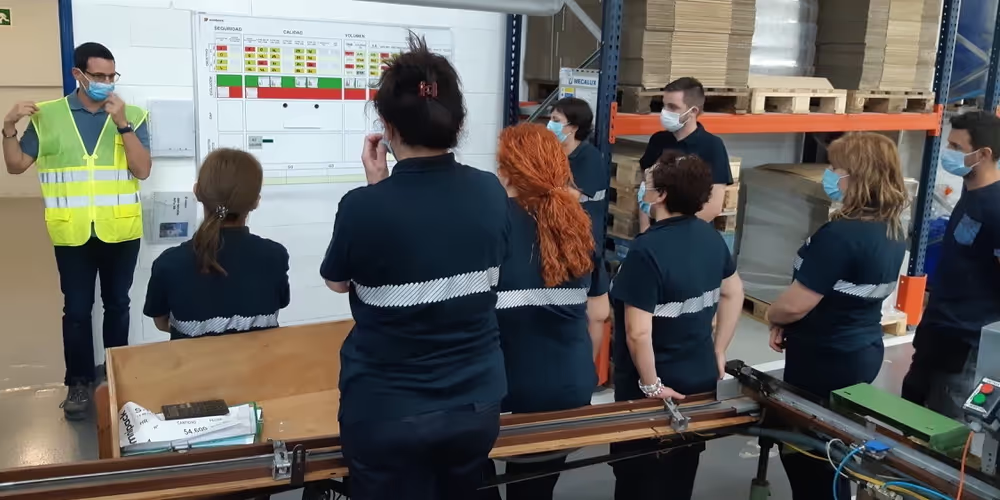
FEATURE – Innovation is a process and lean thinking allows that process to take place, by empowering everyone in the company to think creatively about solving customer problems.
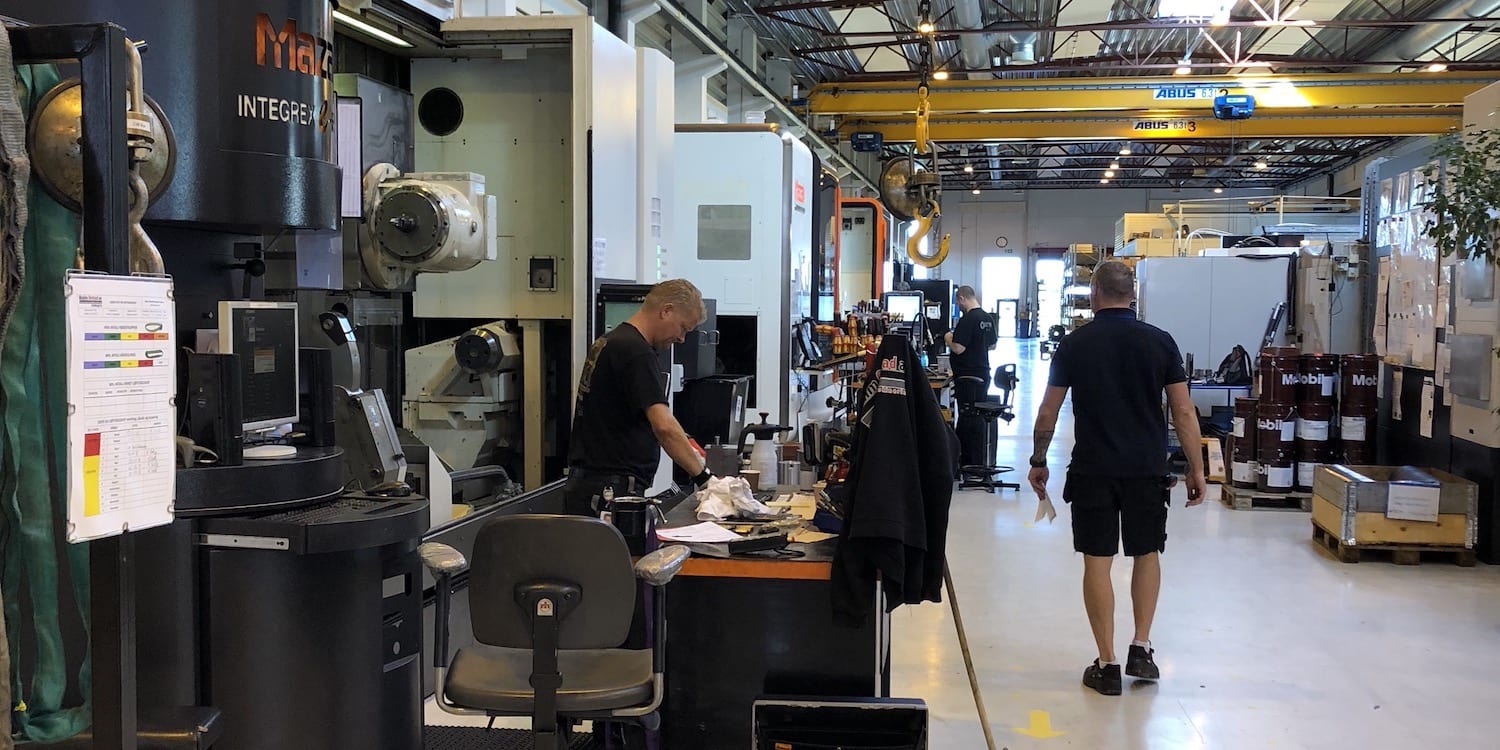
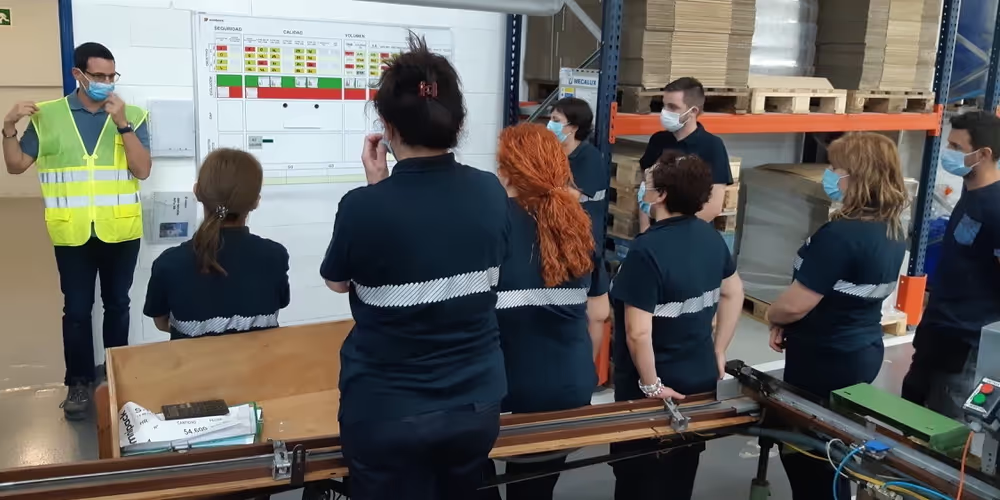
FEATURE – This Norwegian company has come back from the brink of bankruptcy by rallying its people around a common set of values, by leaning out its processes and by involving its leadership team.
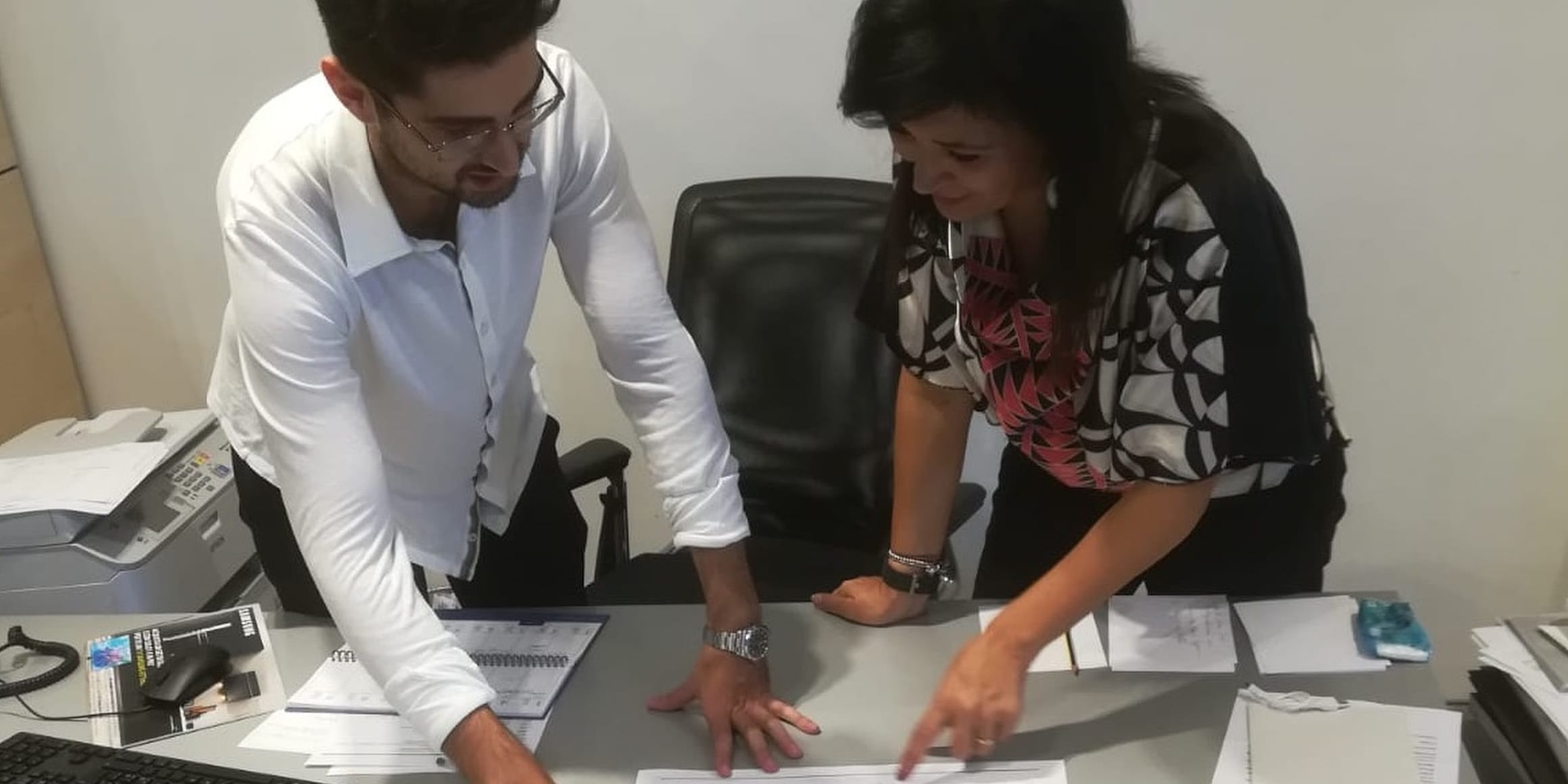
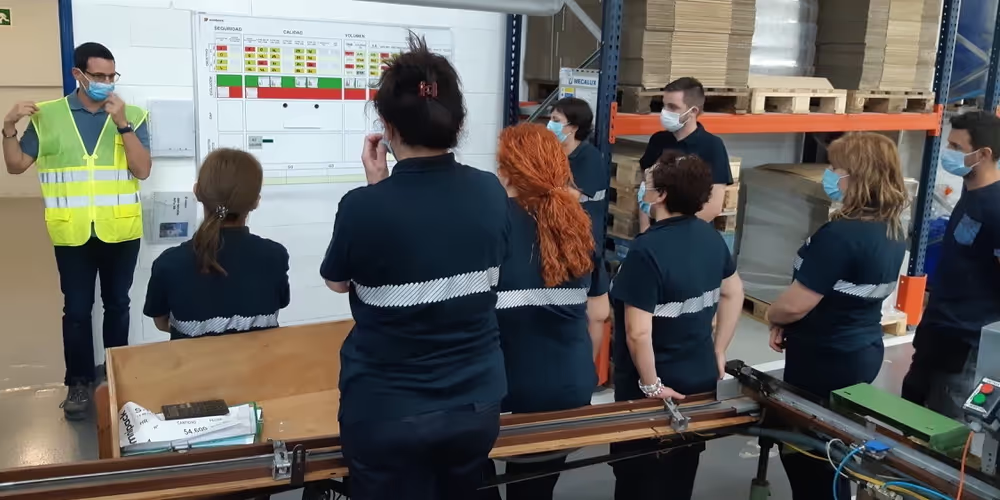
FEATURE – The belief that standardization kills creativity can be a severe hindrance in a lean transformation. The author discusses how he convinced his team of architects to give standards a try.
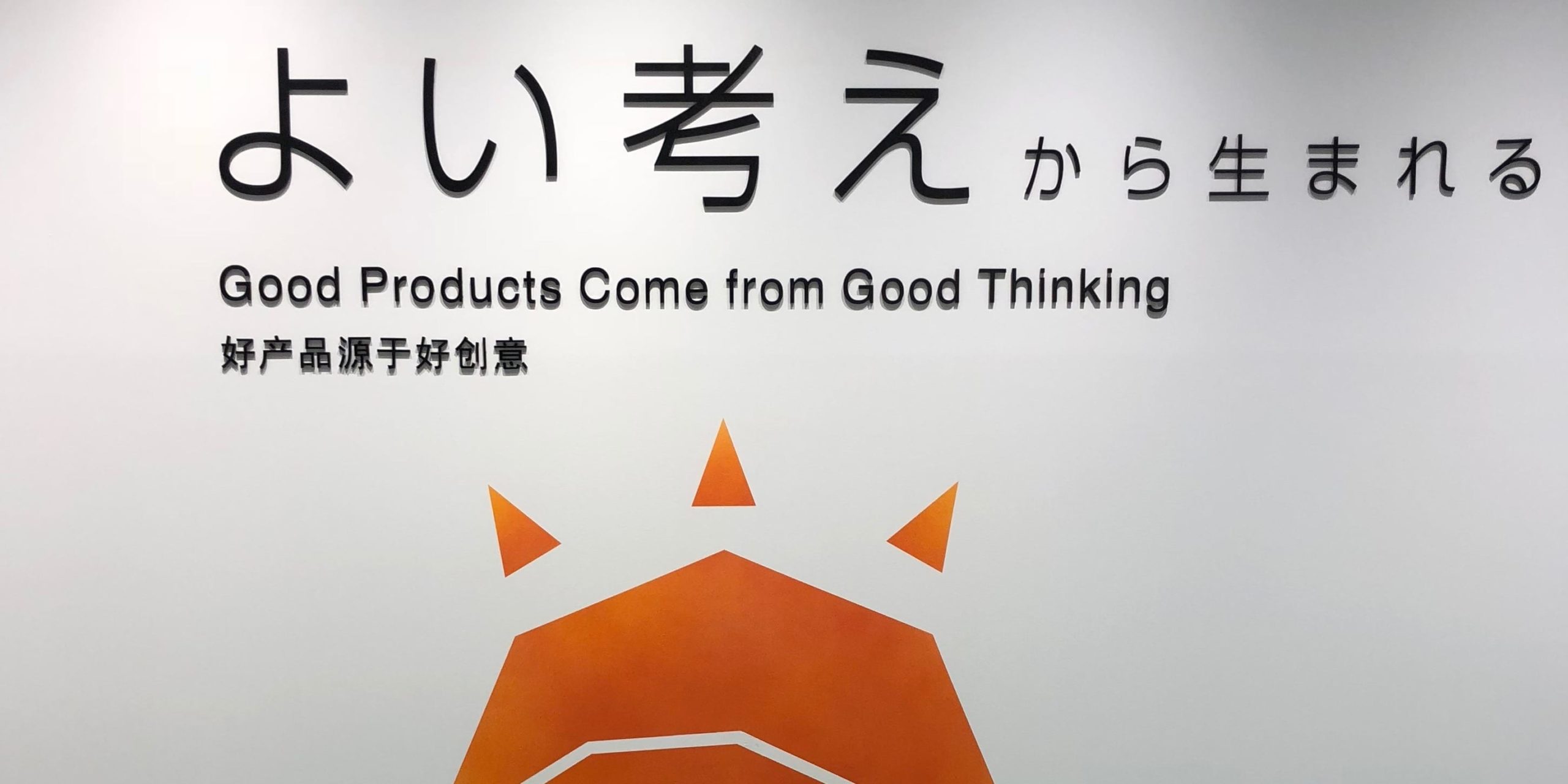
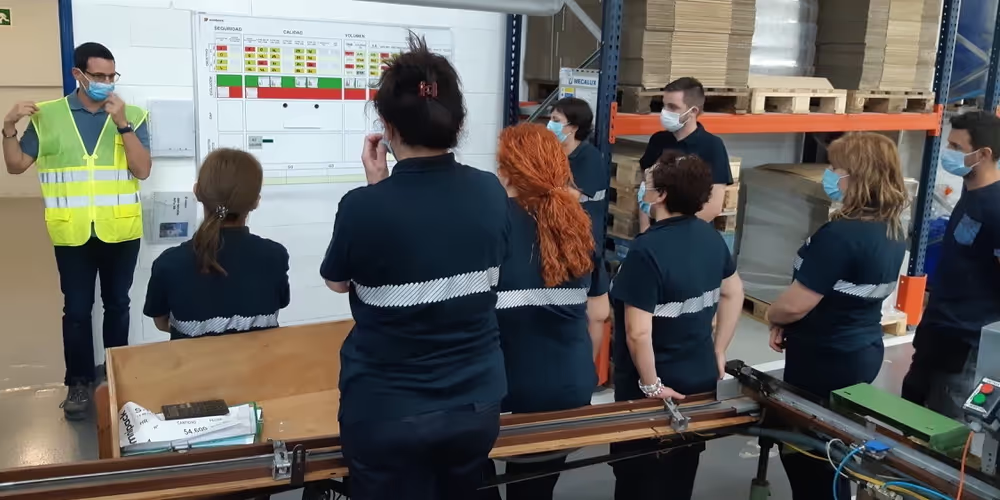
FEATURE – Following a recent visit to Toyota, the authors strive to challenge popular beliefs and shed a light on the underlying philosophy that has made TPS a success for over half a century.
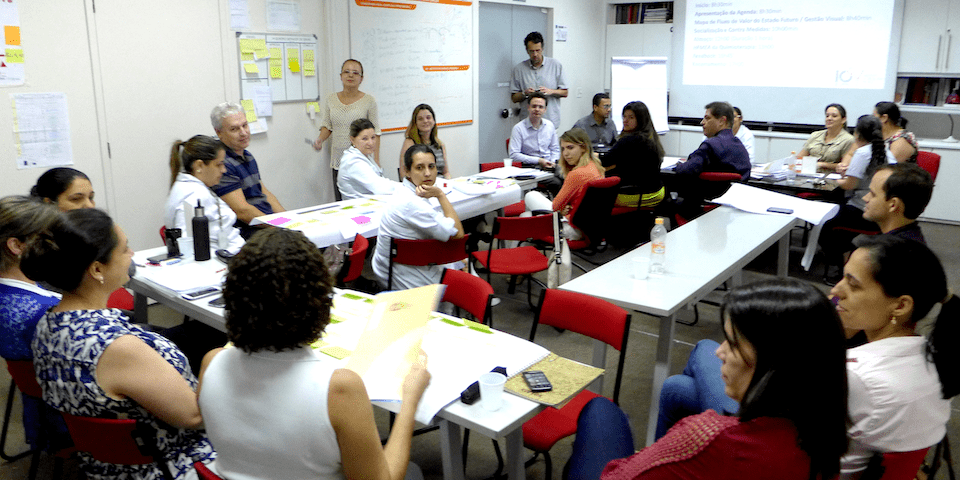
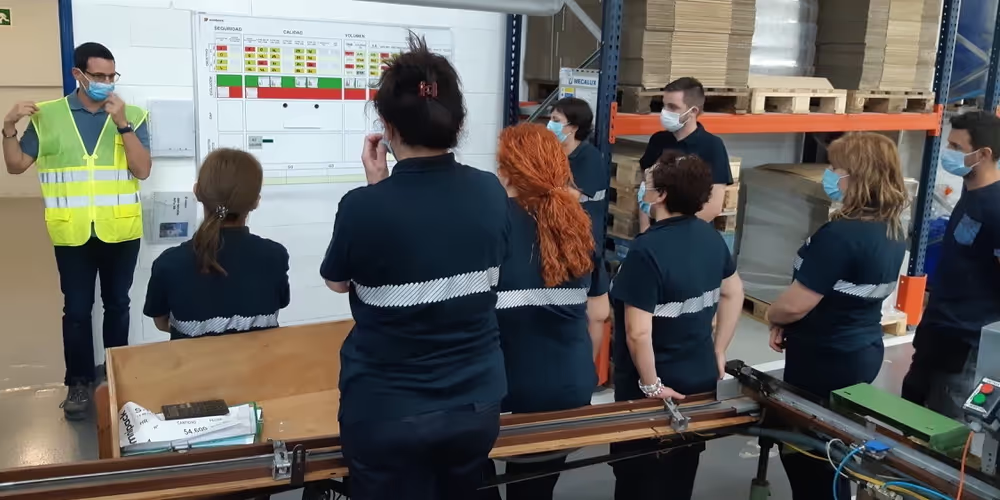
FEATURE – The power of cross-pollination: learning from a manufacturing company has helped a cancer treatment center in Brazil to thrive in its lean transformation.
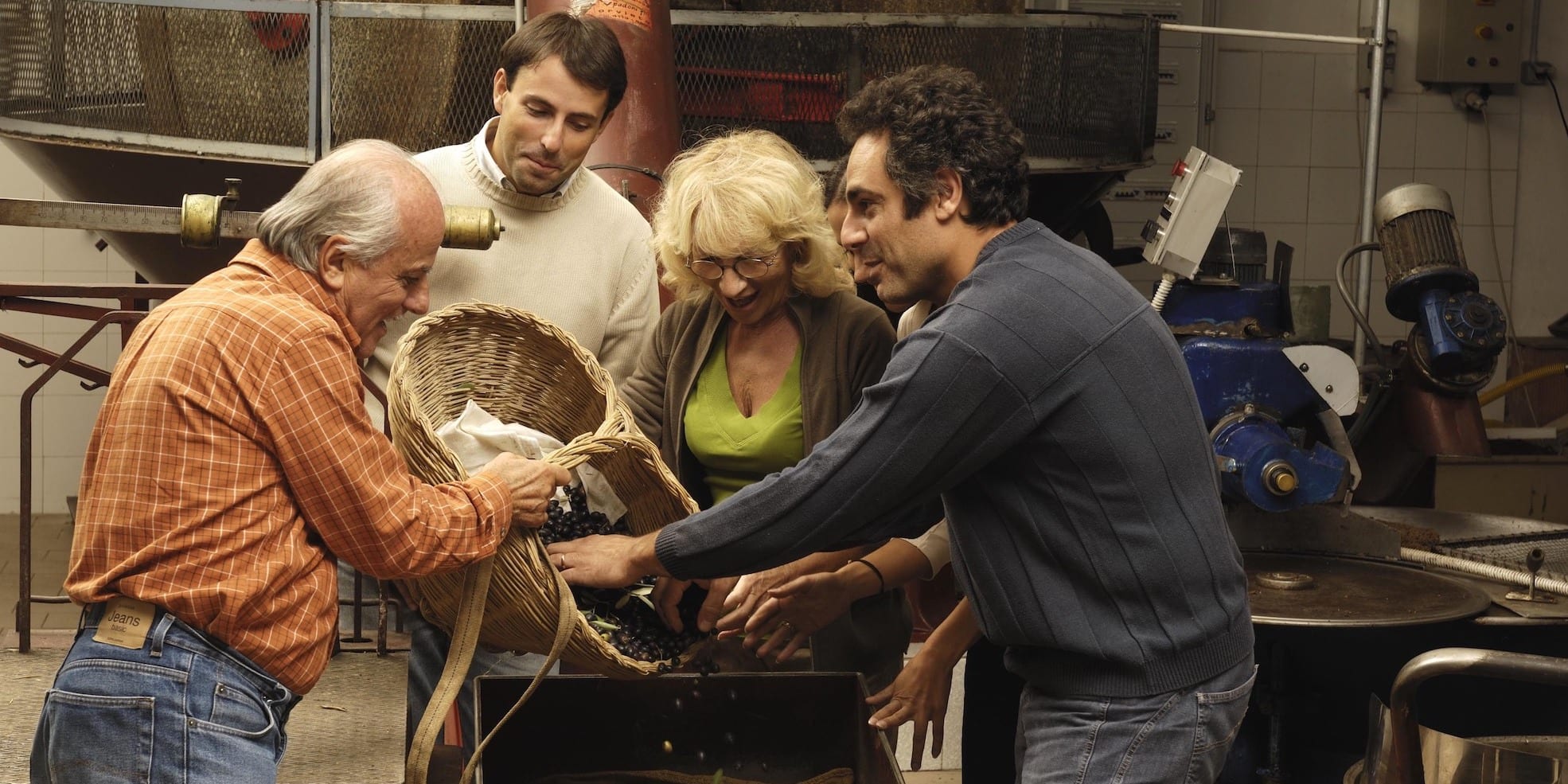
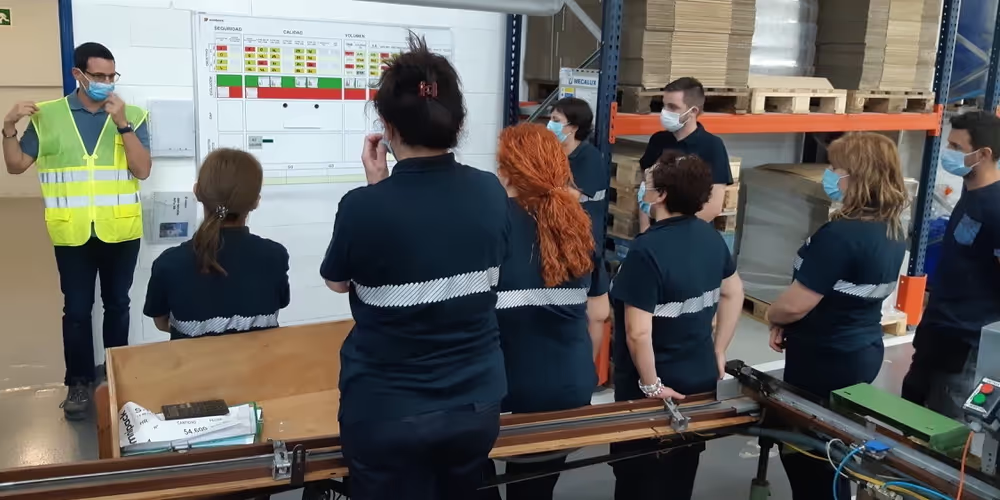
WOMACK’S YOKOTEN – The author discusses the benefits that the many family businesses making up our economies can harness from embracing lean management.
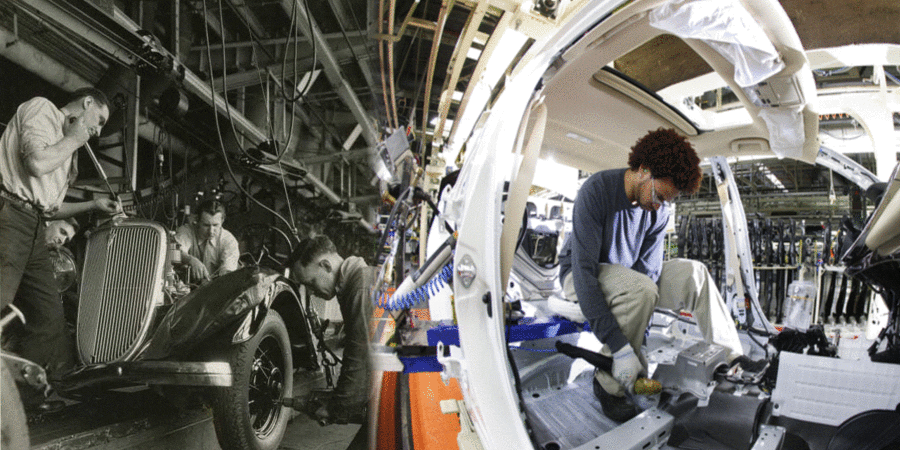
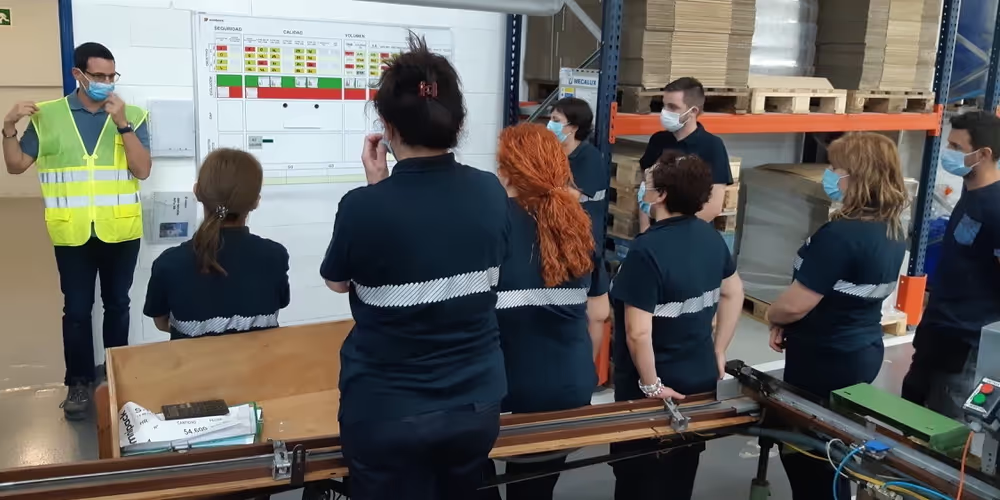
FEATURE – The author offers an overview of the ingredients that made lean thinking what it is, of the 30 years of incubation it underwent at Toyota, and of its diffusion from 1980 onwards.
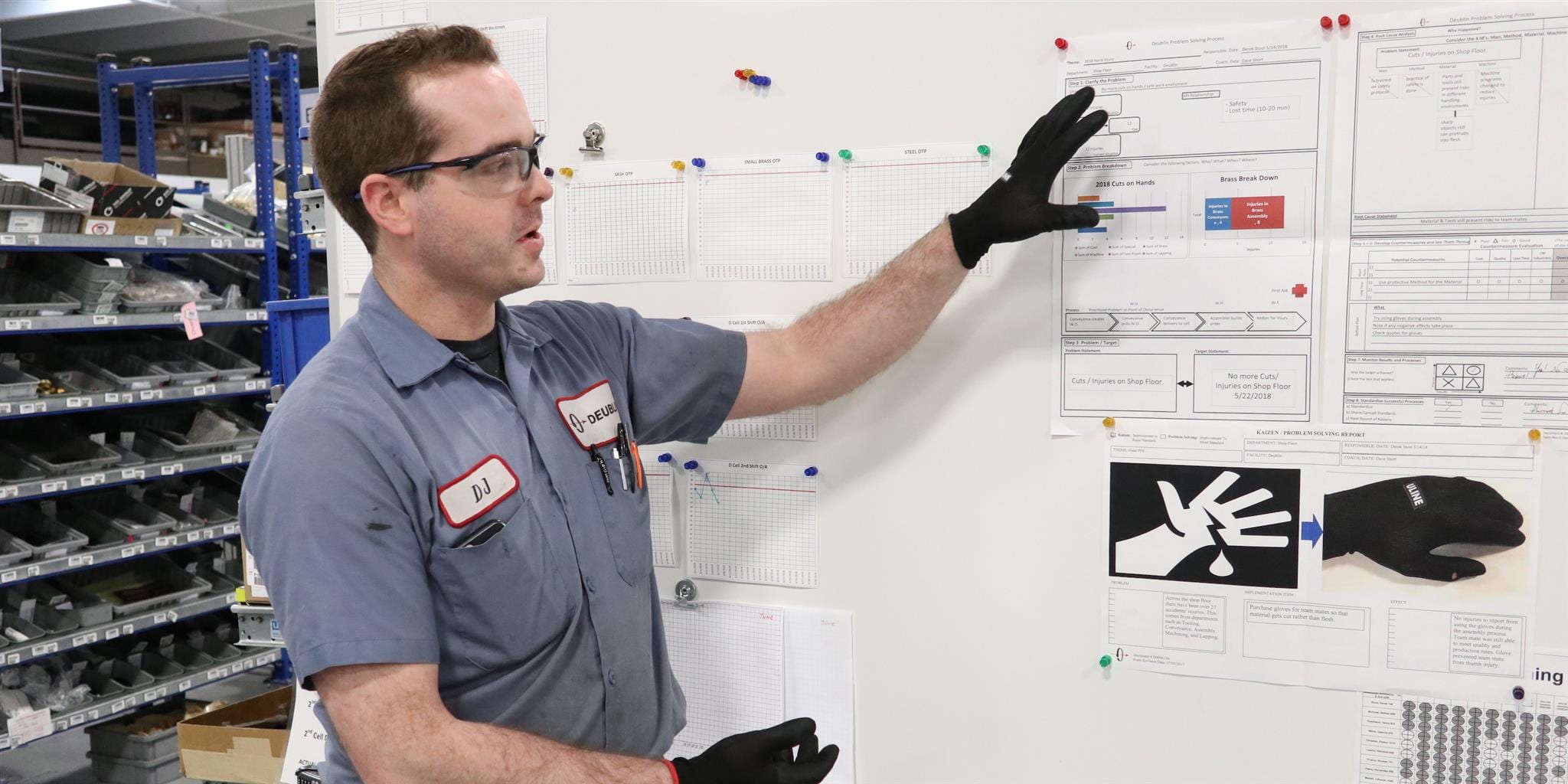
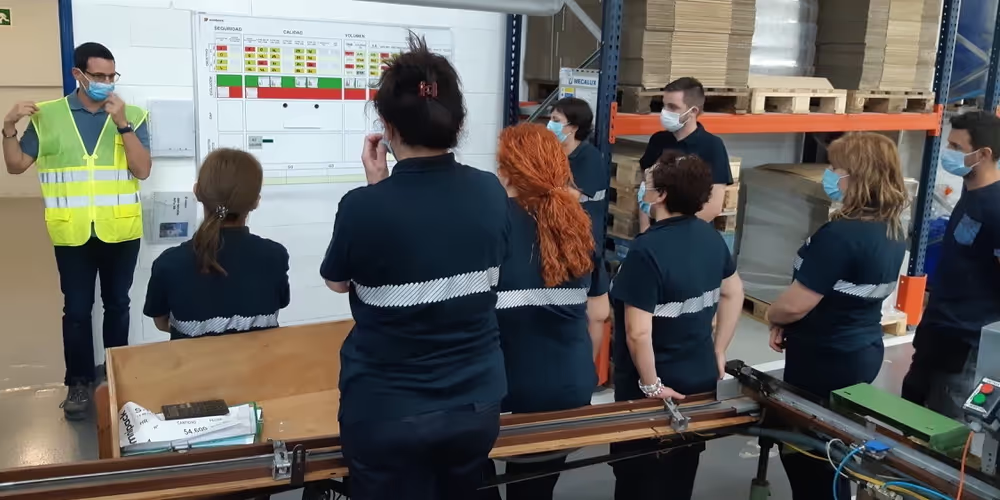
WOMACK’S YOKOTEN – The author visits a company that has sustained lean for a decade. In trying to understand how they did it, he finds how fundamentally the management system has changed.
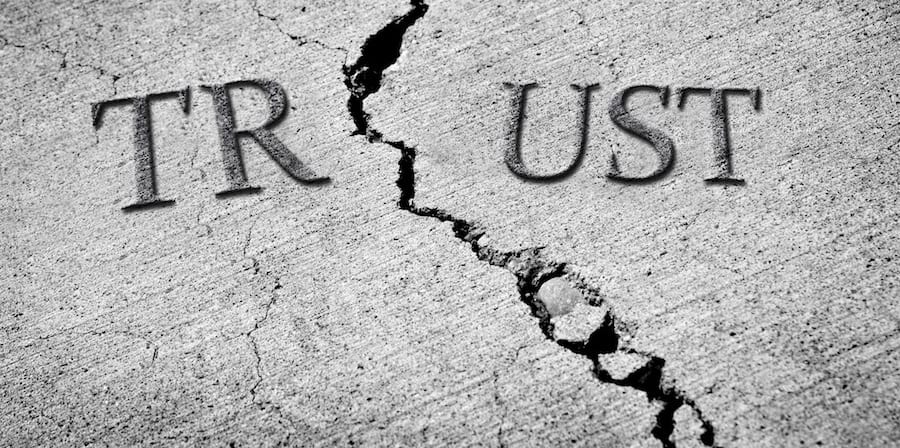
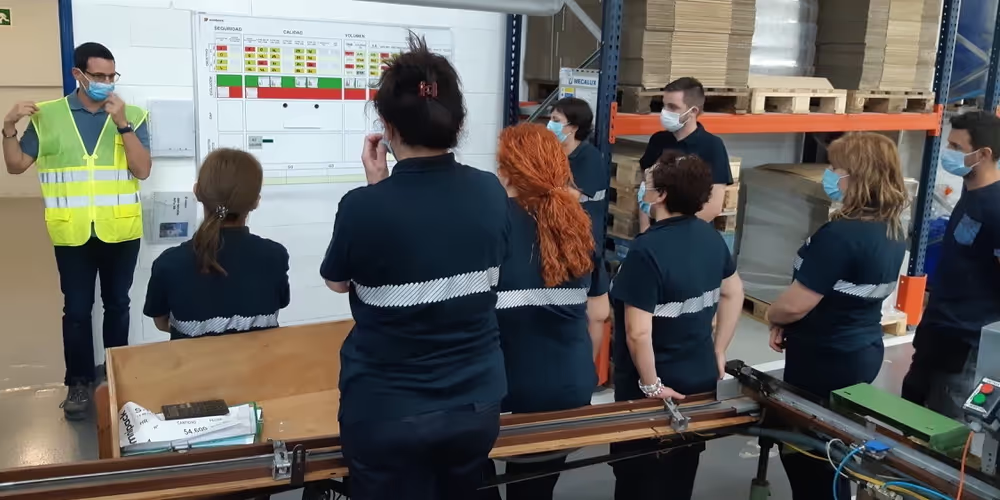
FEATURE – In this interesting piece, the author explains why living up to the ideal of mutual trust is hard, and how lean tools can help us build a workplace based on respect.
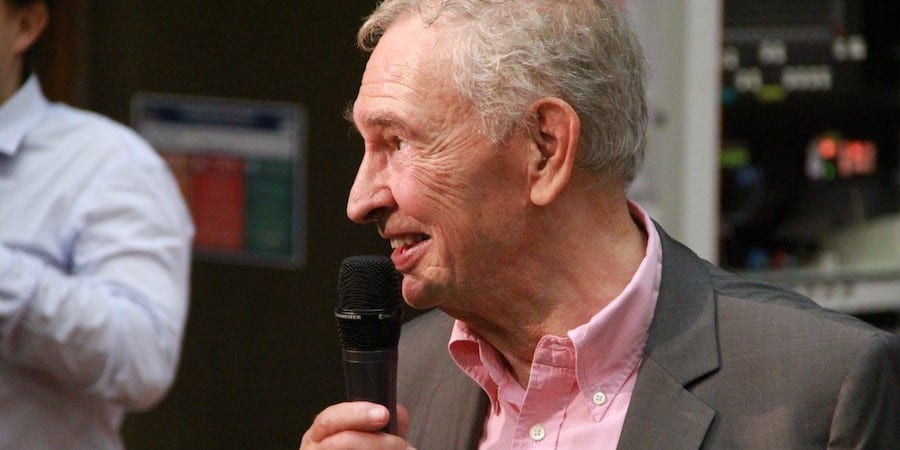
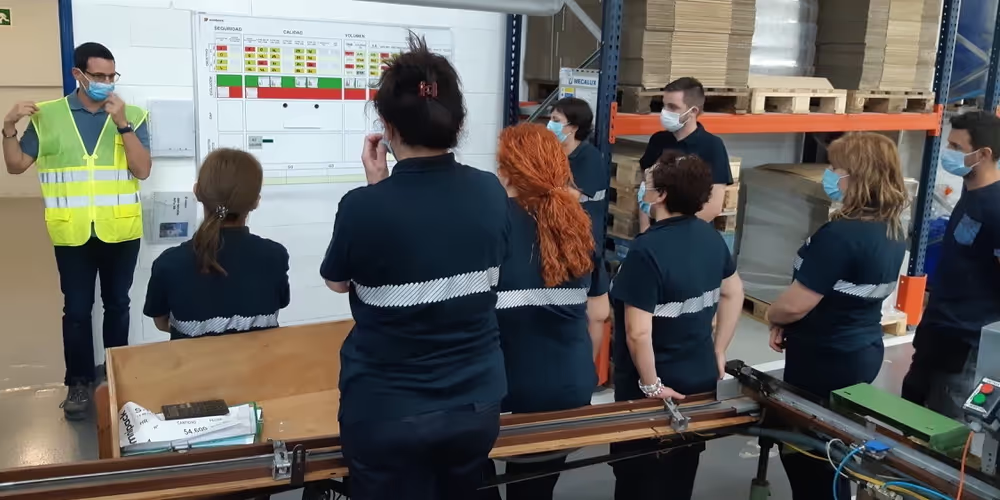
INTERVIEW – Having started to explore TPS in the mid-1970s, Freddy Ballé is one of the great pioneers of our movement. Here, he shares what he learned about Toyota over the past 40 years.
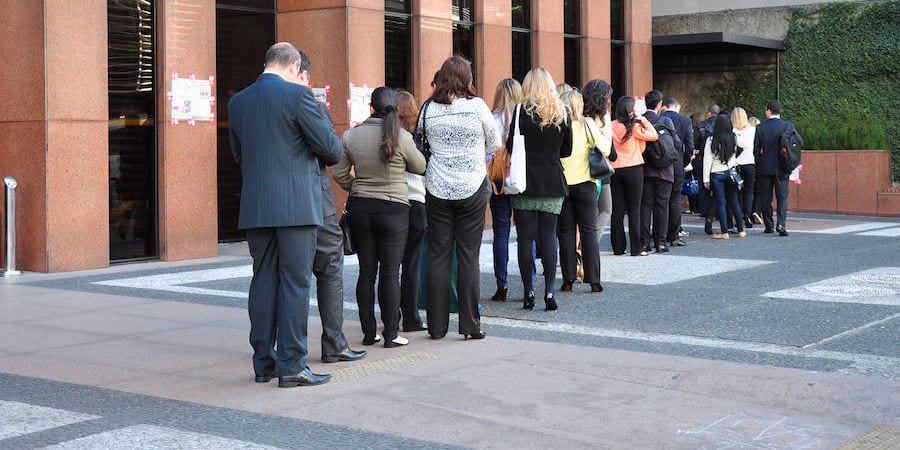
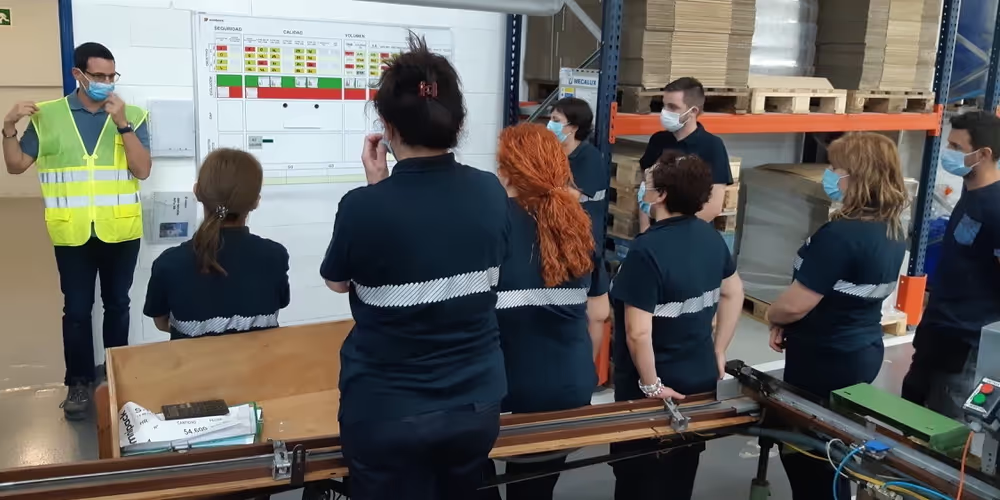
WOMACK’S YOKOTEN – What does a lean employer look like? In this month’s column, the author reflects on the long-term commitment to employees a company engaged in lean thinking should make.
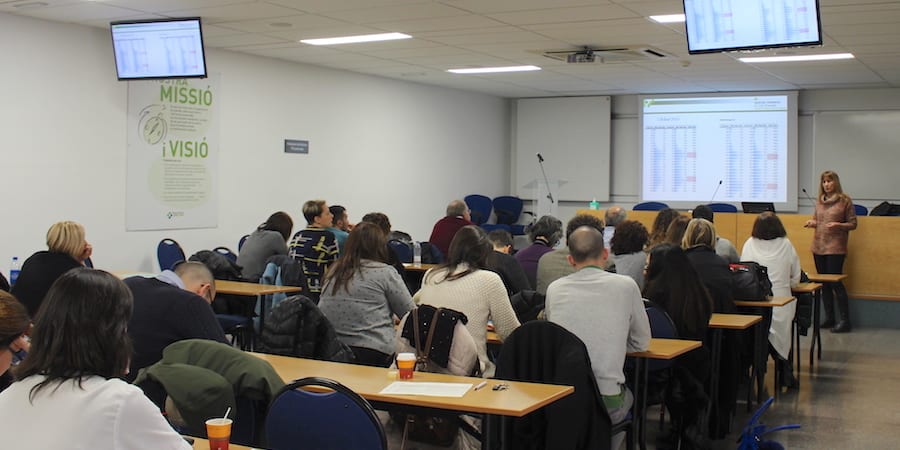
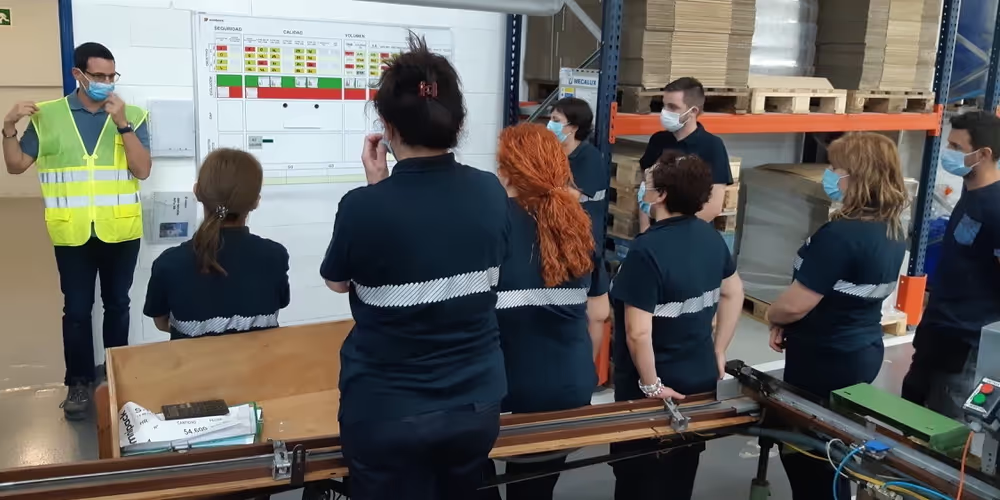
FEATURE – By bringing organizations together to regularly share updates on their lean journeys, Instituto Lean Management has managed to create a flourishing lean healthcare community in Catalunya. But hospitals aren't the only ones benefitting.
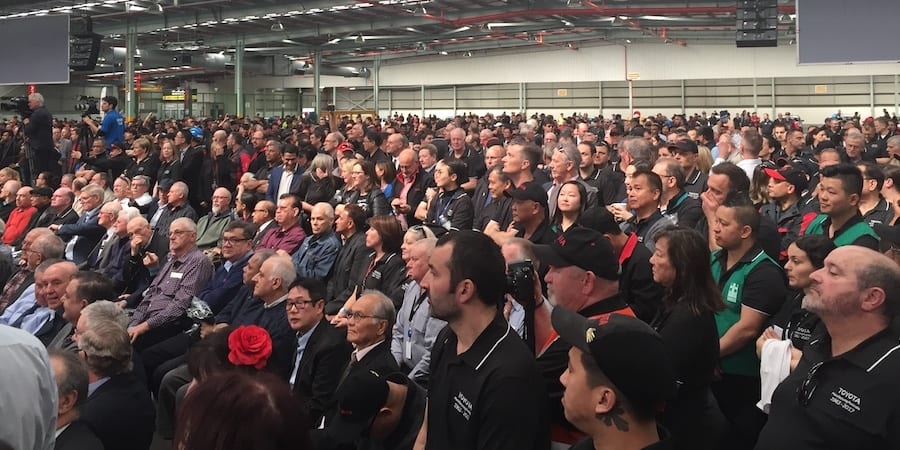
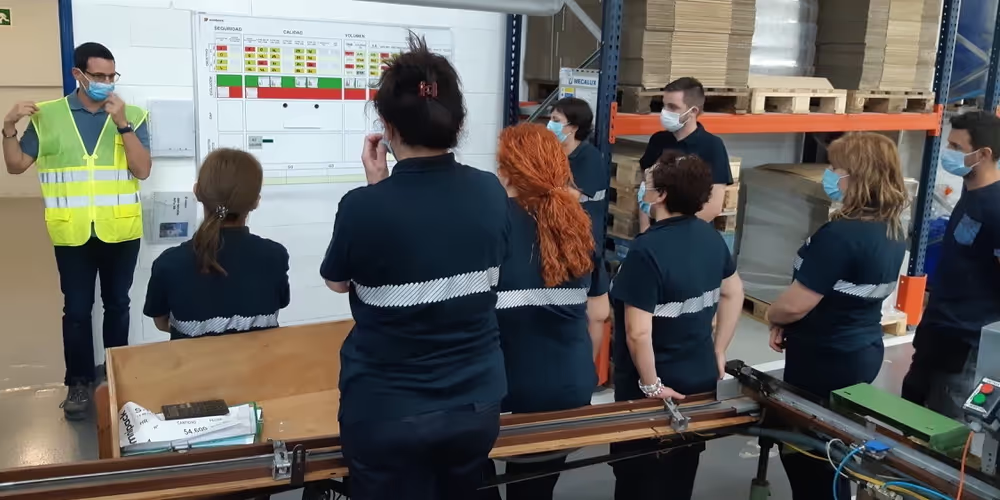
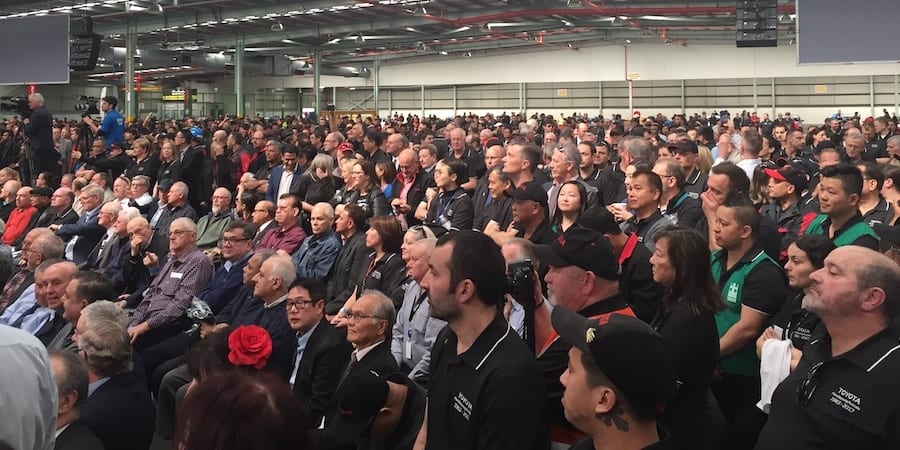
FEATURE – Last year’s shut-down of Toyota’s Altona plant in Australia moved us all. Here, the former Divisional Manager of Manufacturing offers a first-hand account of how the company made the most of a terrible situation.
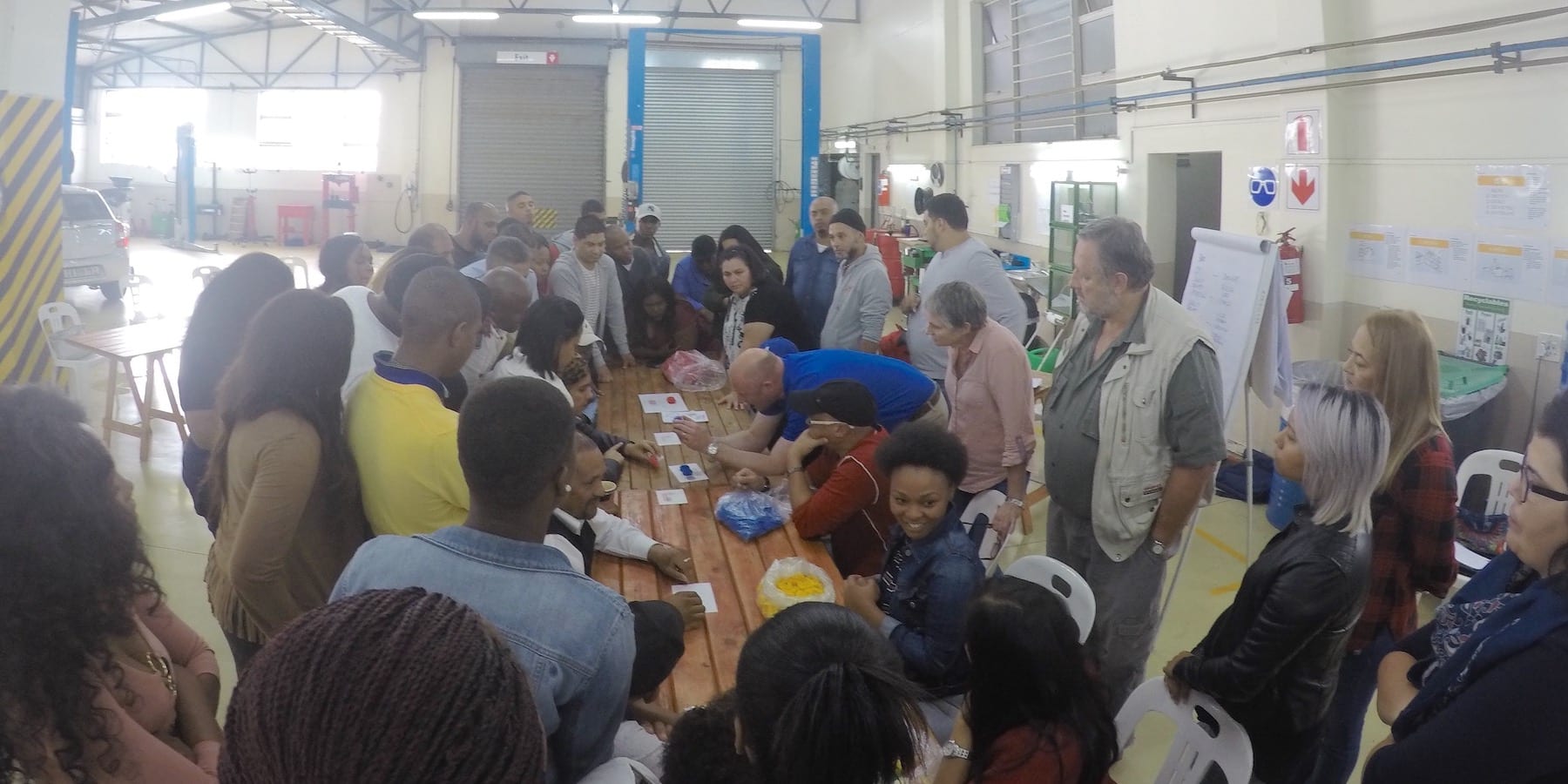
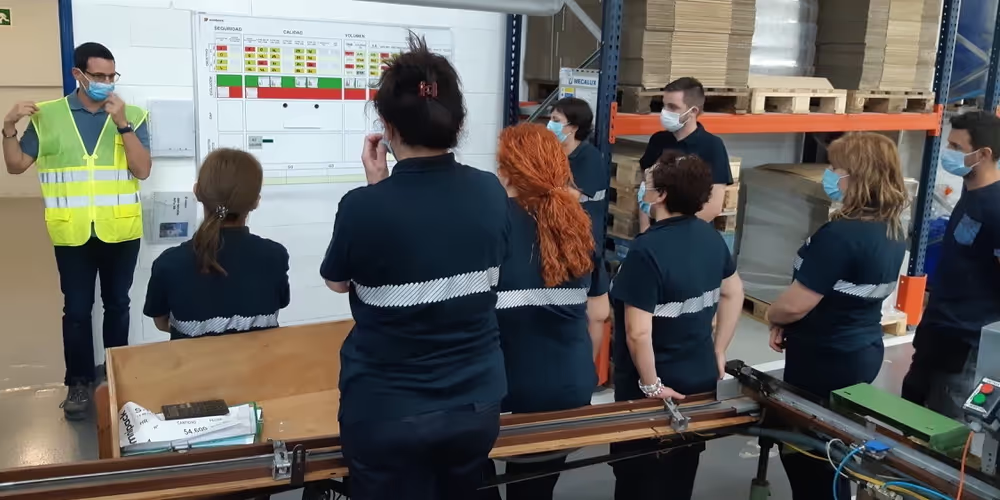
FEATURE – The principal of the Halfway Ottery dealership explains how their lean culture based on respect and improvement is not only changing the business, but transforming the lives of people in the townships.
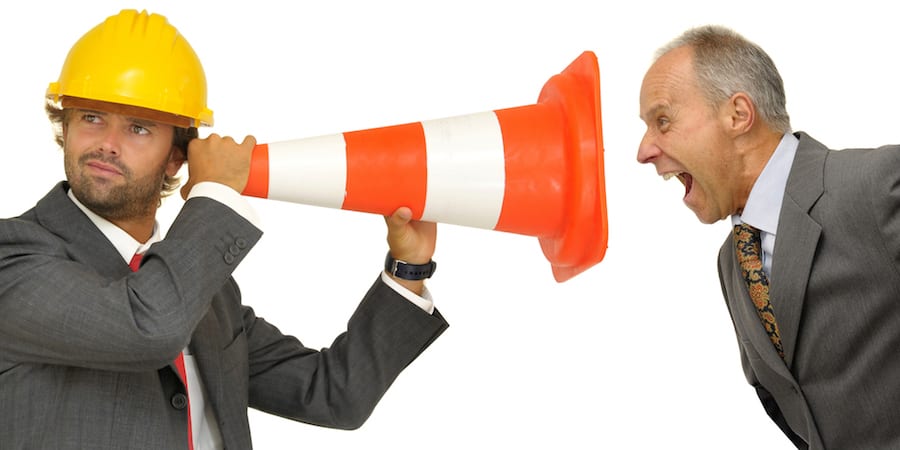
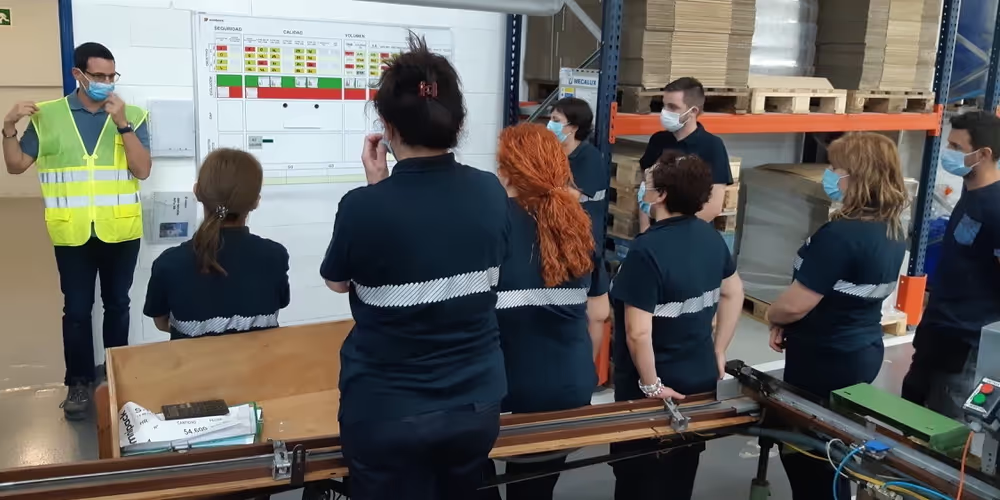
FEATURE – Lean has now been around for quite some time, and its impact on business world is hard to dispute. But what does it tell us about traditional management practices?
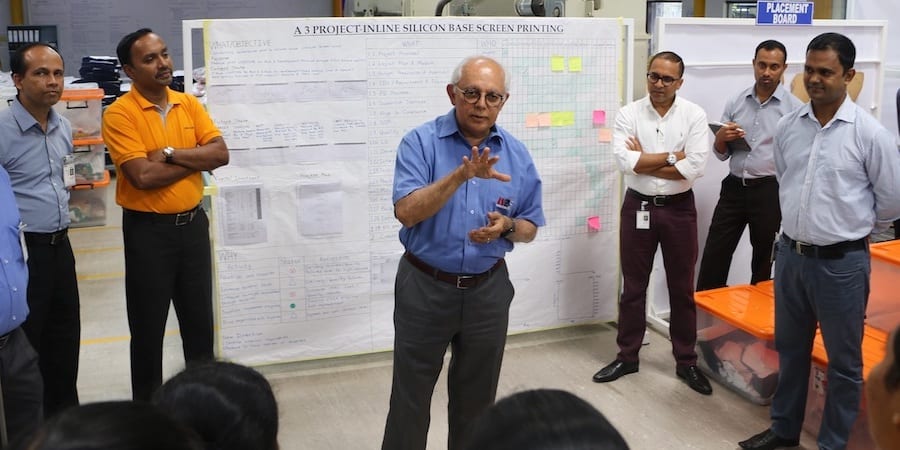
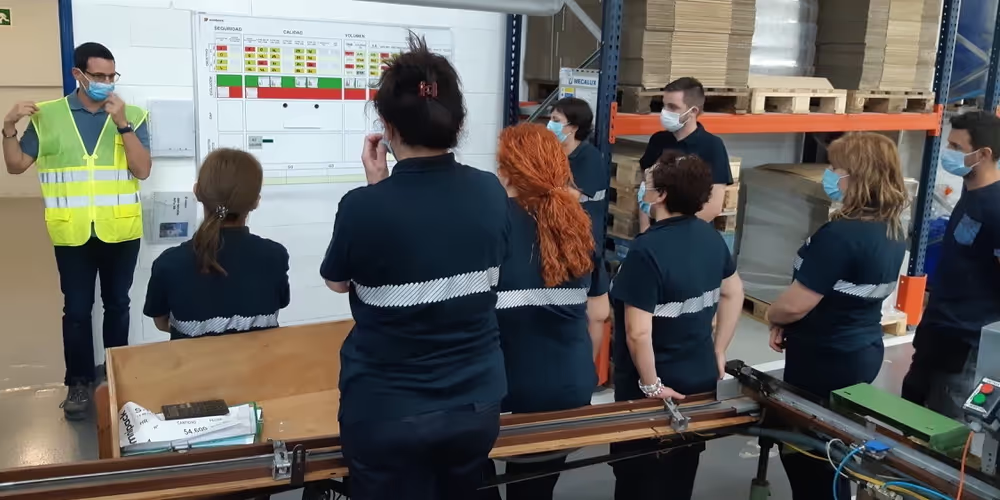
INTERVIEW – Prior to his talk at this year’s Lean Transformation Summit, the CEO of a large apparel manufacturer tells us about the company’s lean journey, and its impact on Sri Lankan society.
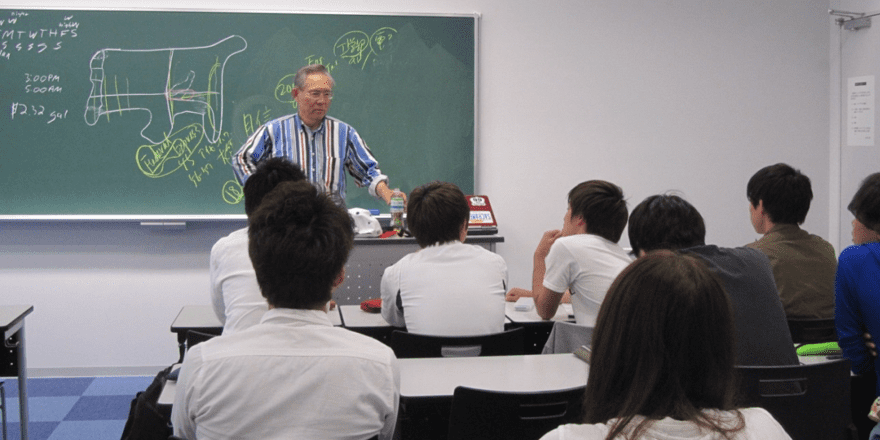
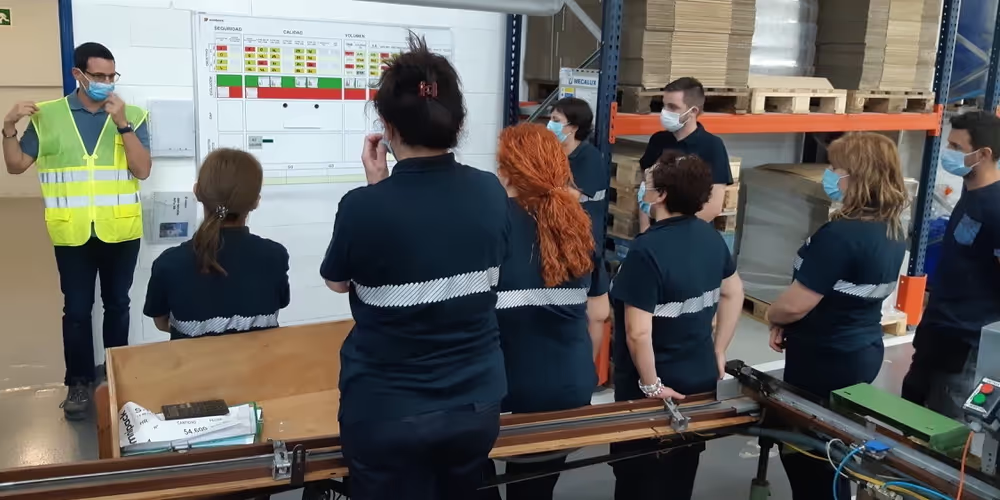
INTERVIEW – In this Q&A with Catherine Chabiron, Toyota veteran Isao Yoshino discusses NUMMI, management at the company, and how to change the mindsets of leaders.
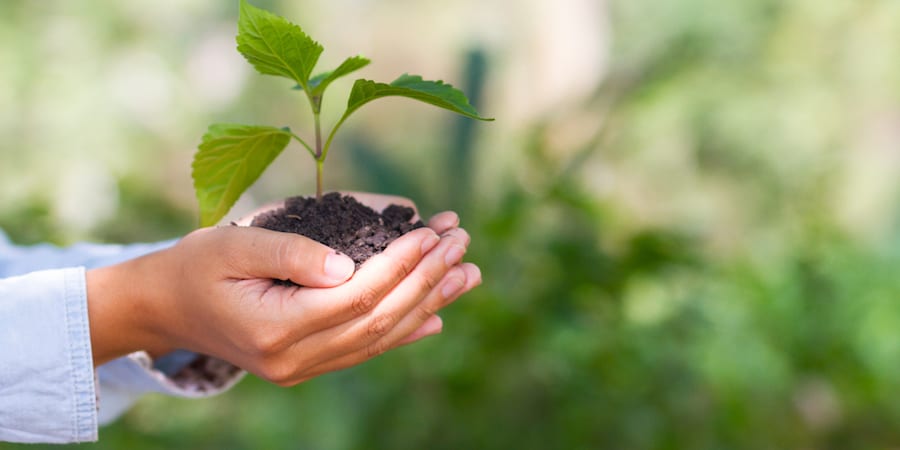
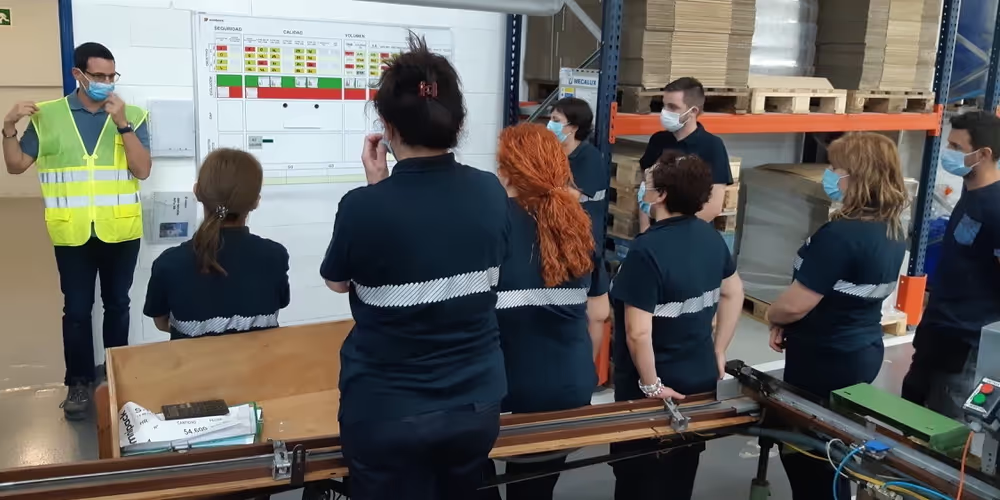
WOMACK’S YOKOTEN – Ahead of the holidays, for his last column of the year, the author reminds us of the power of sharing. Go out and spread the lean word!
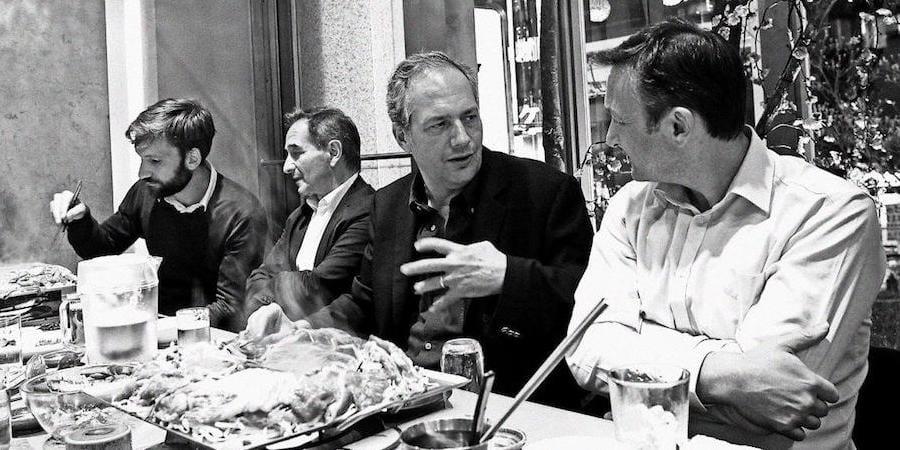
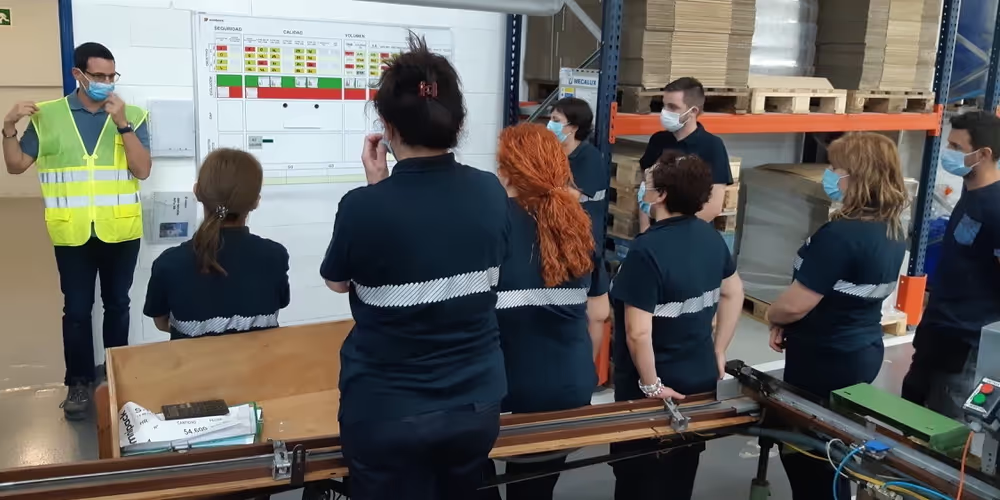
FEATURE – Following a visit to a Toyota supplier in Japan, the authors reflect on the nature of kaizen and explain why we might be looking for it in the wrong place.
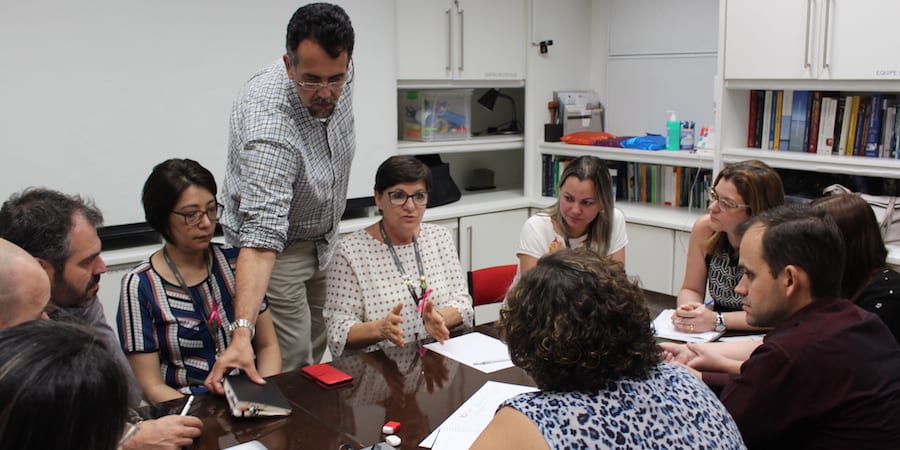
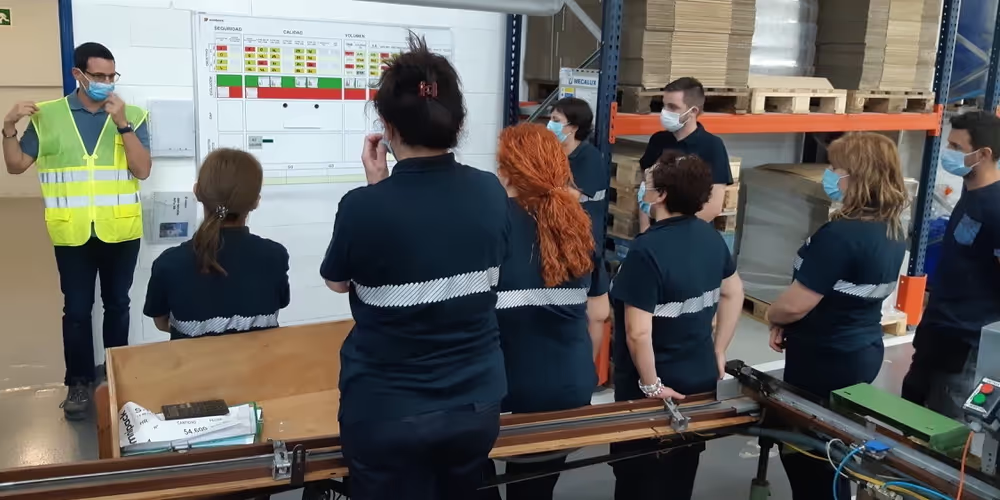
VIDEO - The CEO of a cancer center in Brazil gives us a tour of the their obeya room, taking us through their strategy deployment and explaining how it supports their mission of reducing the burden of cancer.
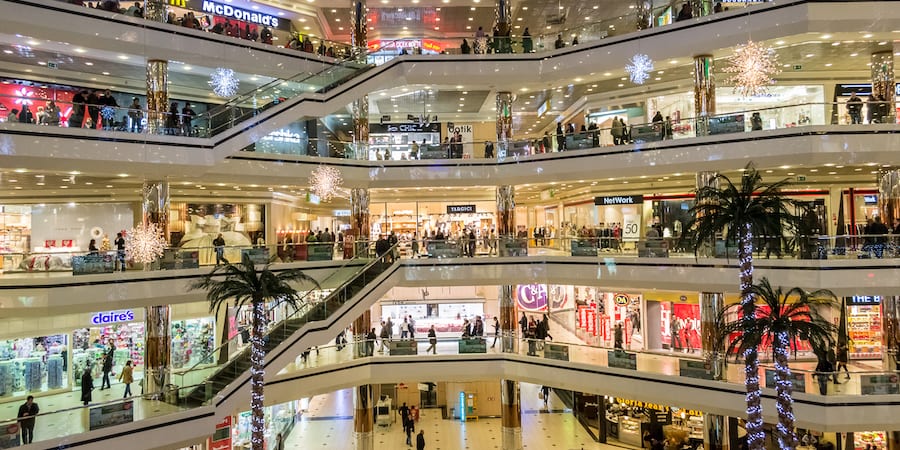
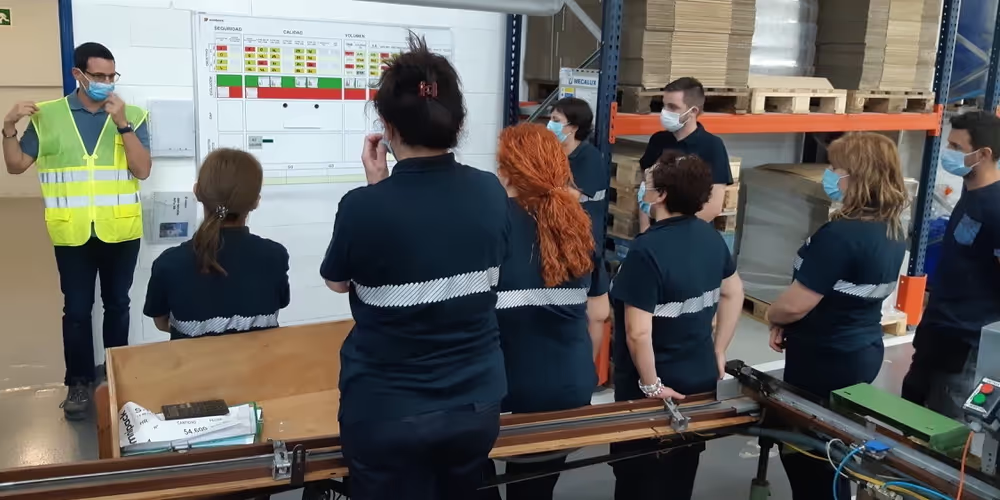
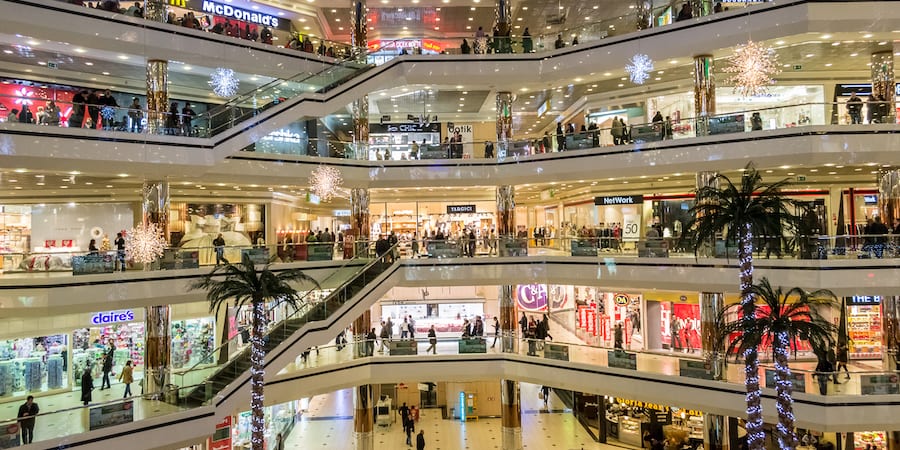
WOMACK’S YOKOTEN – Toyota’s commitment to employees reminds us that it is impossible to tap into the full potential of lean without providing people with stable, gratifying employment.
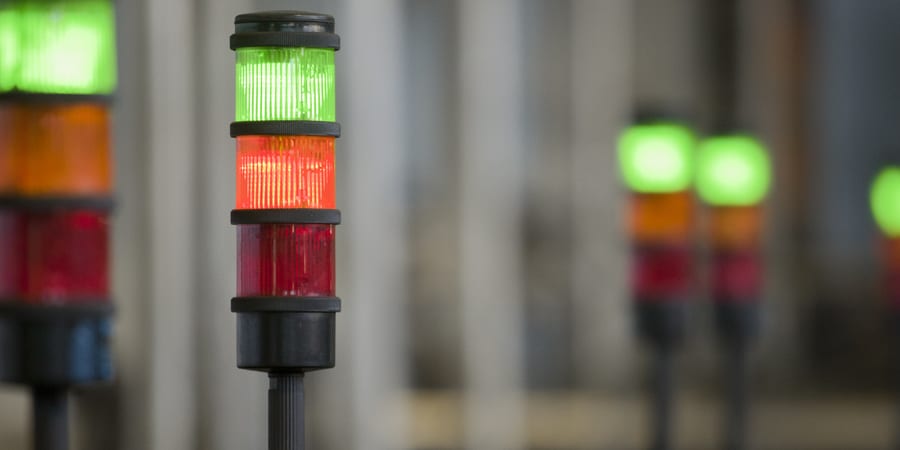
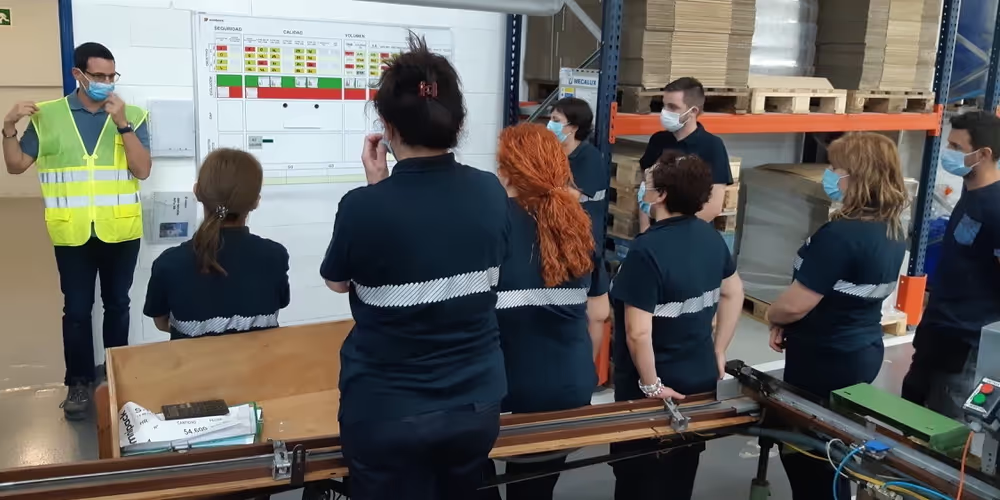
INTERVIEW – Catherine Chabiron sits down with Marc Onetto, a former executive with GE and Amazon, to discuss Jidoka and its profound effects on the way people work and think.
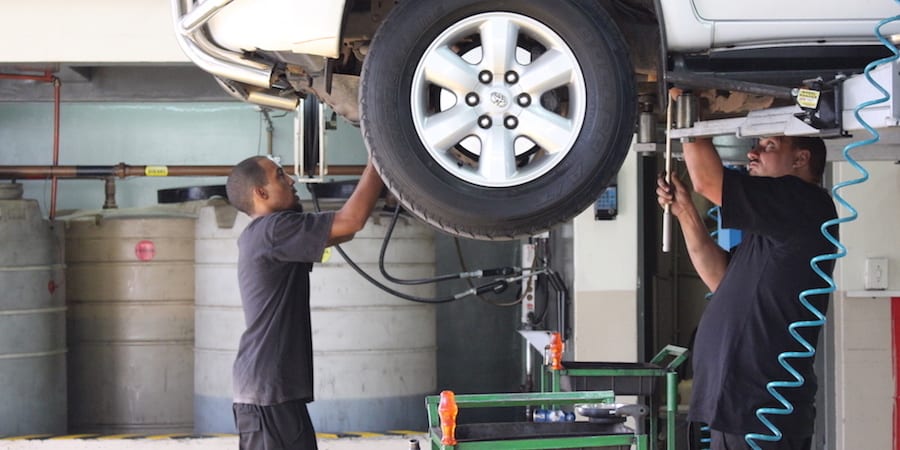
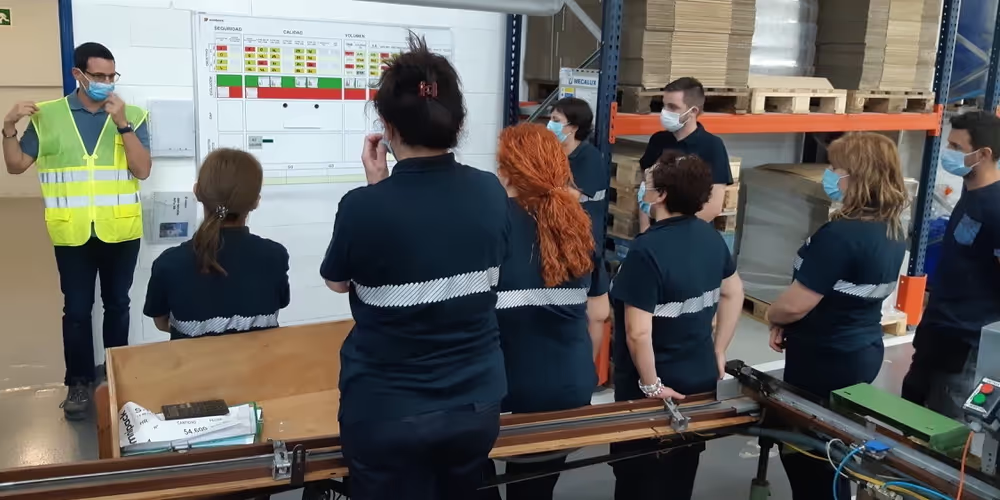
DOCUMENTARY – In PL’s first ever documentary, we share the story of a chain of car dealerships in Africa. Watch and learn how people development and lean leadership made for one of the best turnarounds you’ll ever encounter.
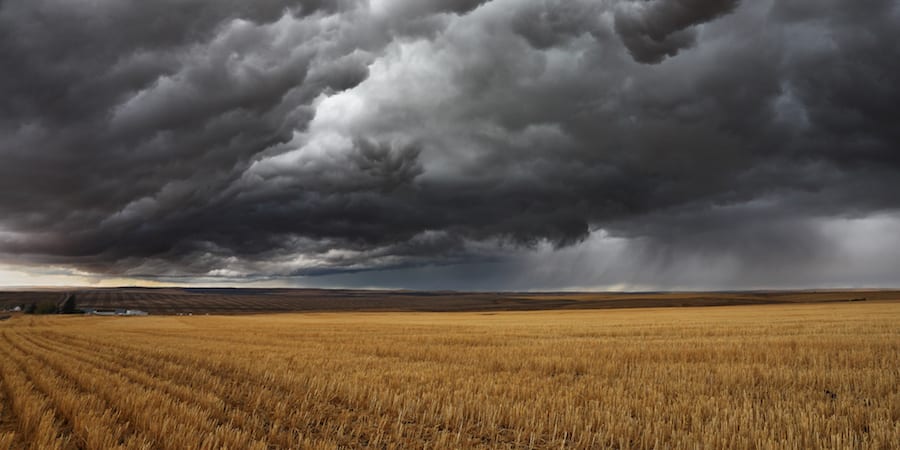
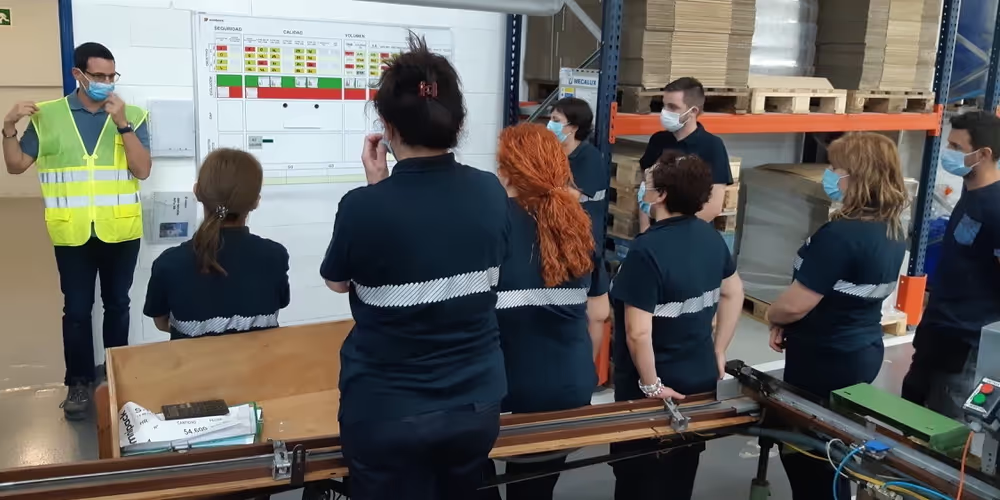
YOKOTEN – Lean has changed the world in many ways, even though the original vision of its founding fathers has failed to materialize. Jim discusses why, as a movement, we shouldn’t give up and review our strategy instead.
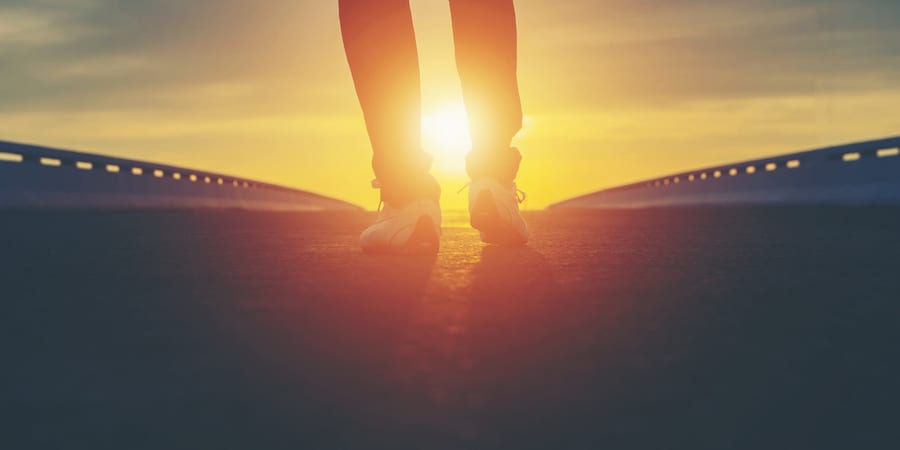
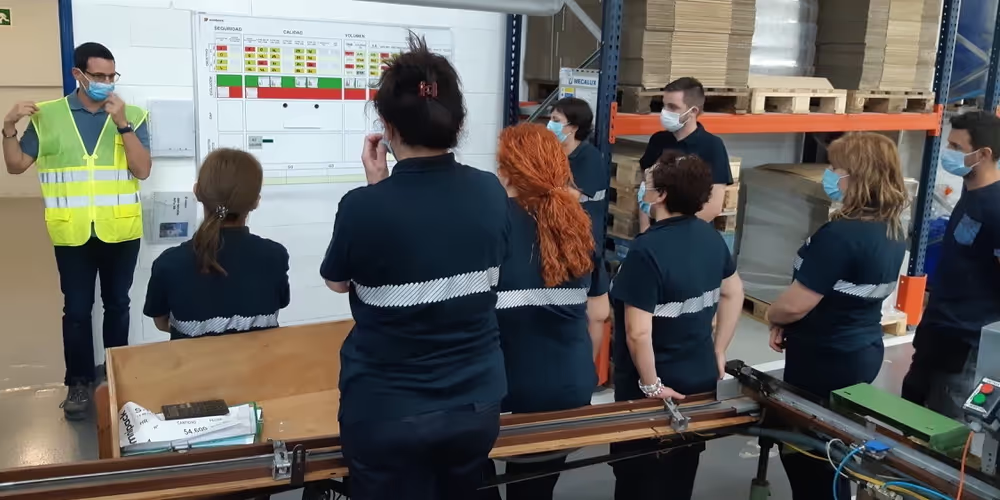
FEATURE – Lean is a people-centric system for learning that acts as an alternative to traditional management and financial capitalism. It represents the best strategy a company can adopt to meet the needs of the future.
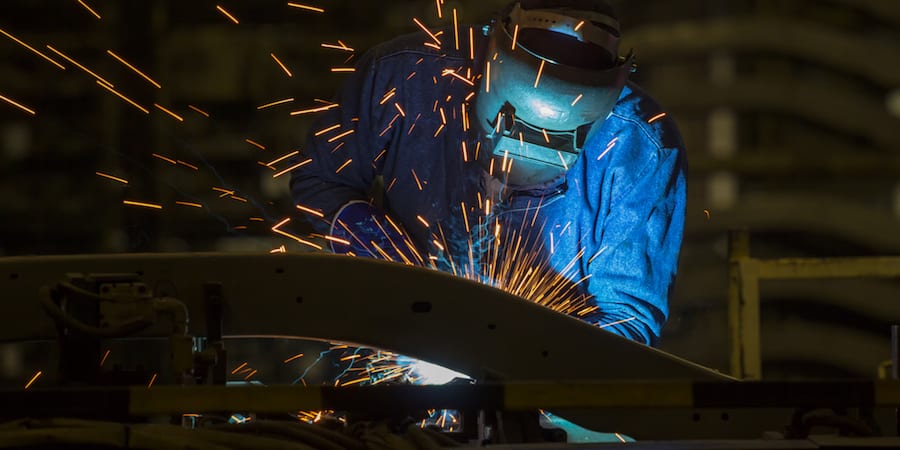
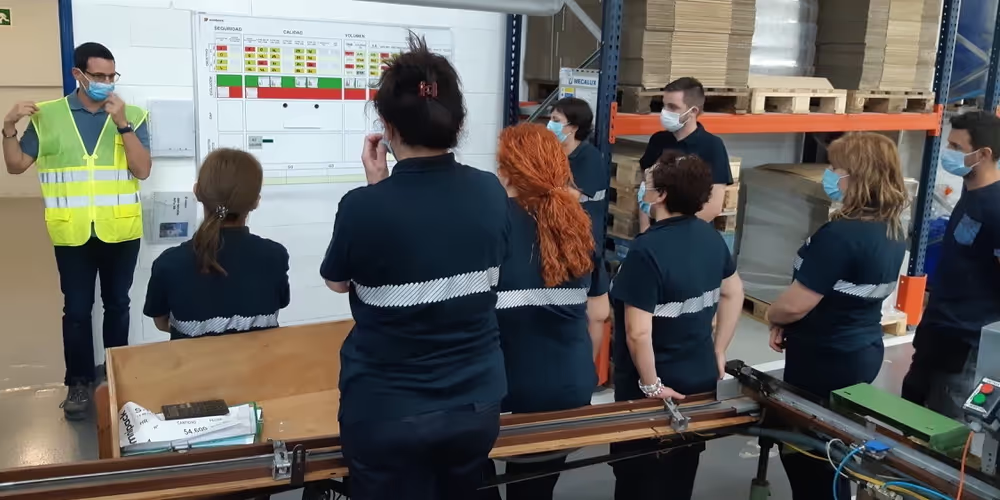
FEATURE – Through this intimate anecdote from her days at Toyota Motor Manufacturing Kentucky, the author tells us of her experience with standardization… and of the deep leadership lessons hiding behind it.
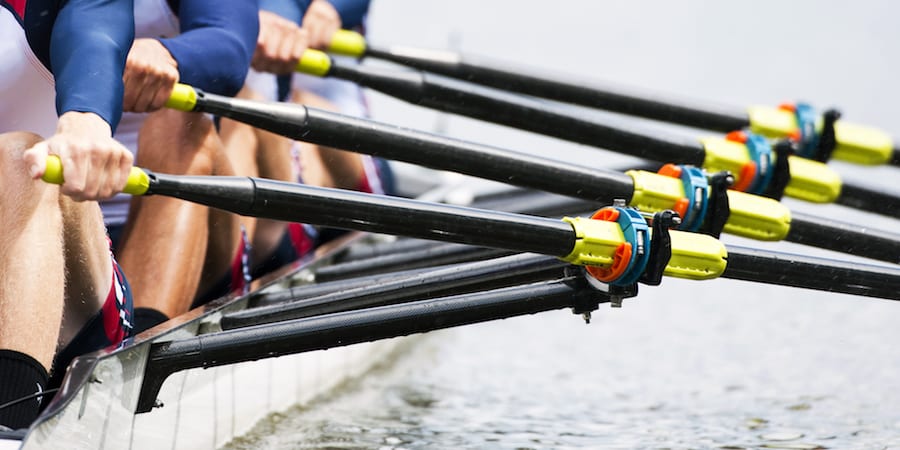
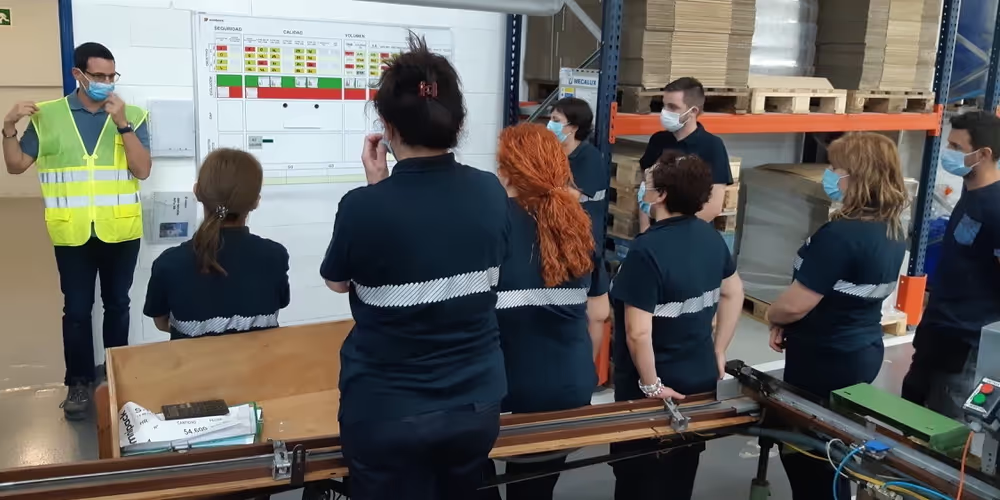
FEATURE – Continuously studying the challenges we meet and the responses we devise, lean gives us endless opportunities to learn. The author goes back to basics, reflecting on some core lean premises.
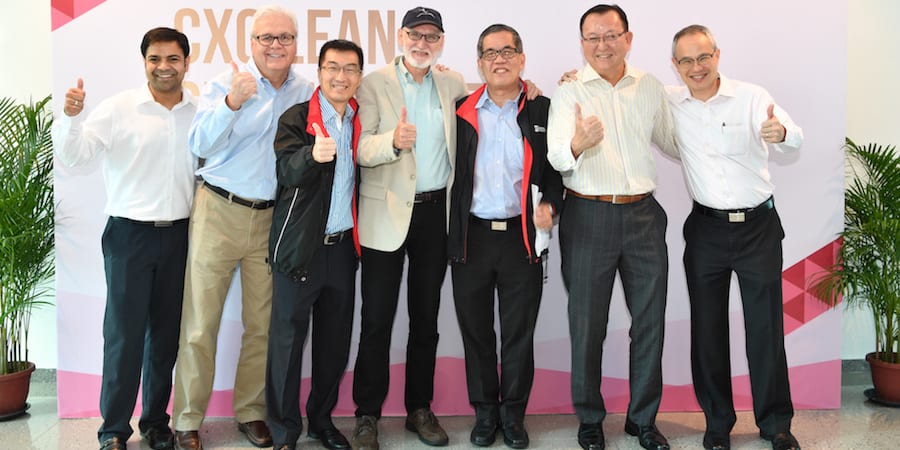
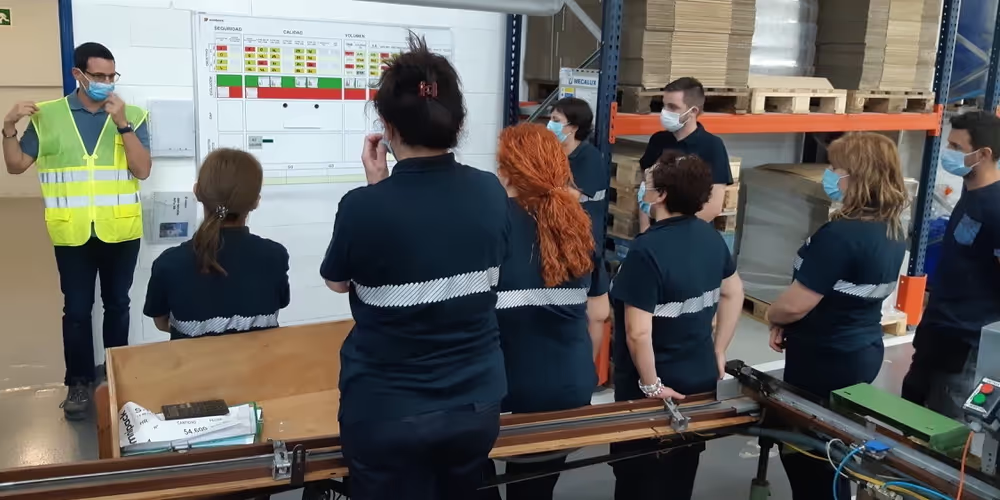
FEATURE – Last year, the Lean Global Network entered a partnership with the Singapore Institute of Technology to bring lean capabilities to local SMEs. Along the way, we discovered an alternative approach to academic teaching.
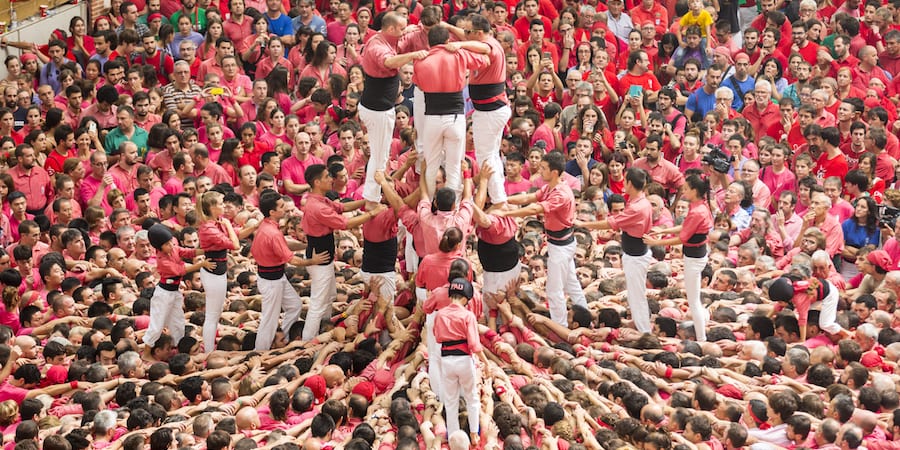
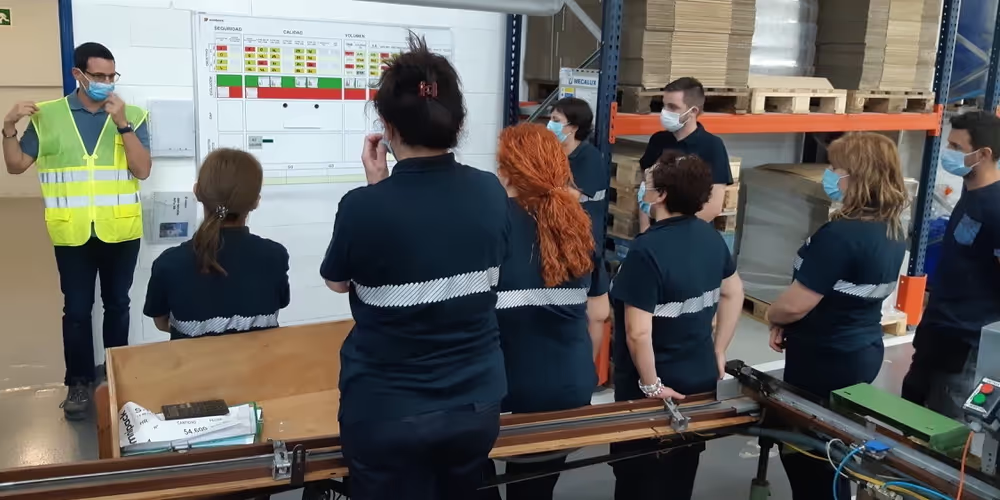
WOMACK’S YOKOTEN – The author looks at hoshin planning, A3 thinking and daily management as the three key elements of a lean management system, and highlights the related behaviors that will allow lean to thrive.
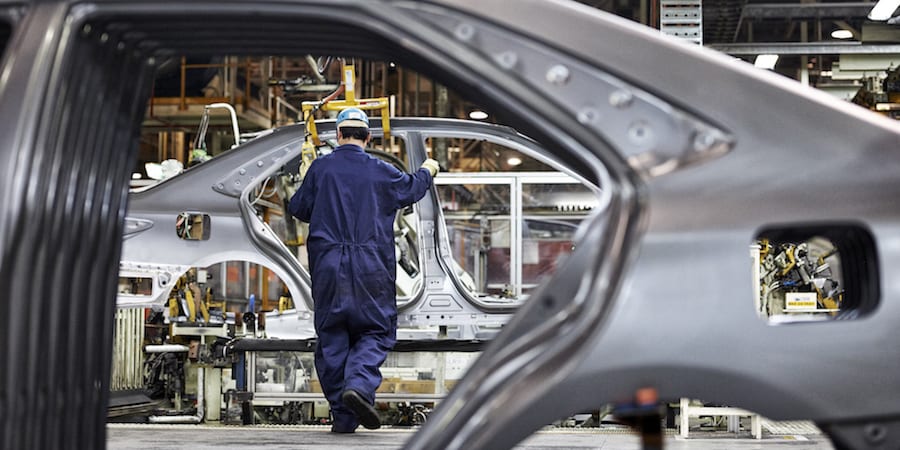
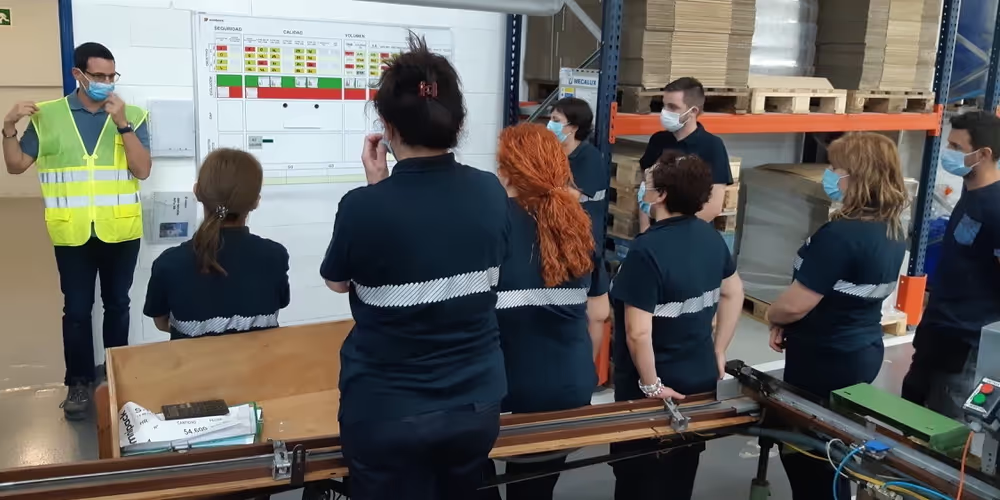
WOMACK'S YOKOTEN – On October 3, Toyota will cease its manufacturing operations in Australia, but the way it is managing the transition - in the leanest way possible - holds great lessons for us all.
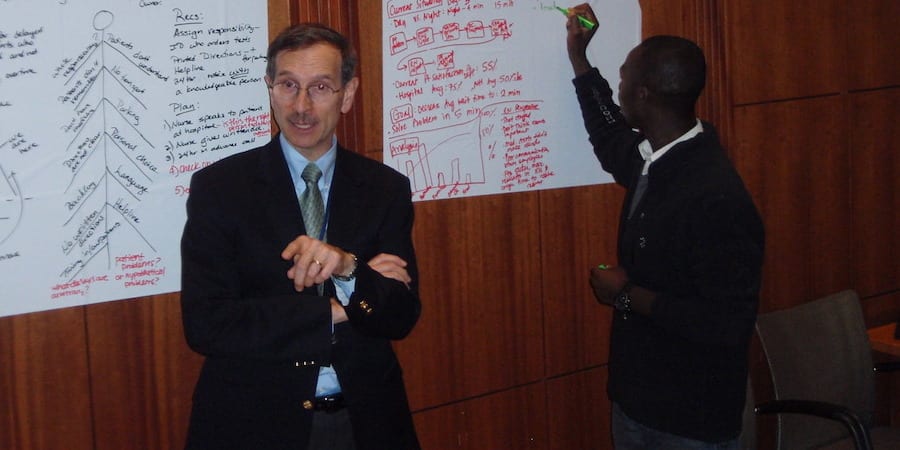
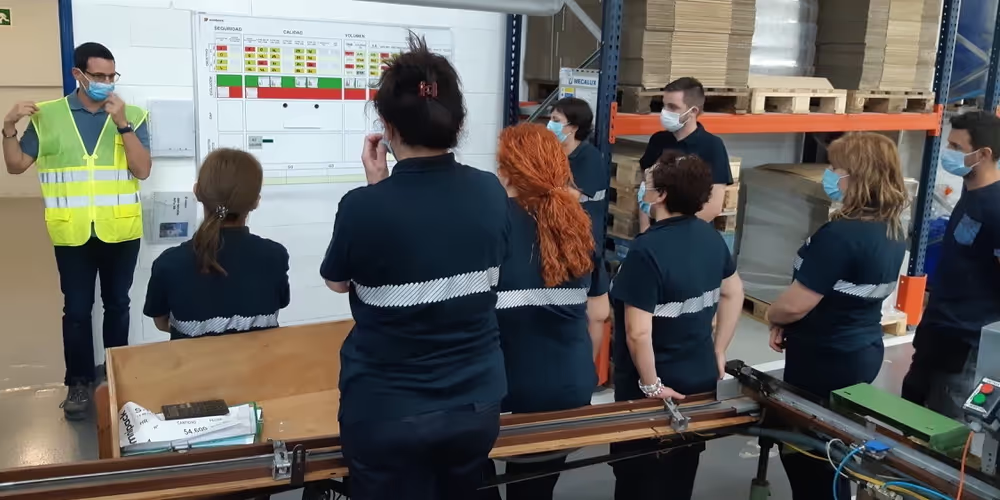
PROFILE – Another month, another inspiring profile of a lean practitioner. We were impressed by Dr Billi’s deep conviction in the idea that, first of all, leaders must be learners. You will be too.
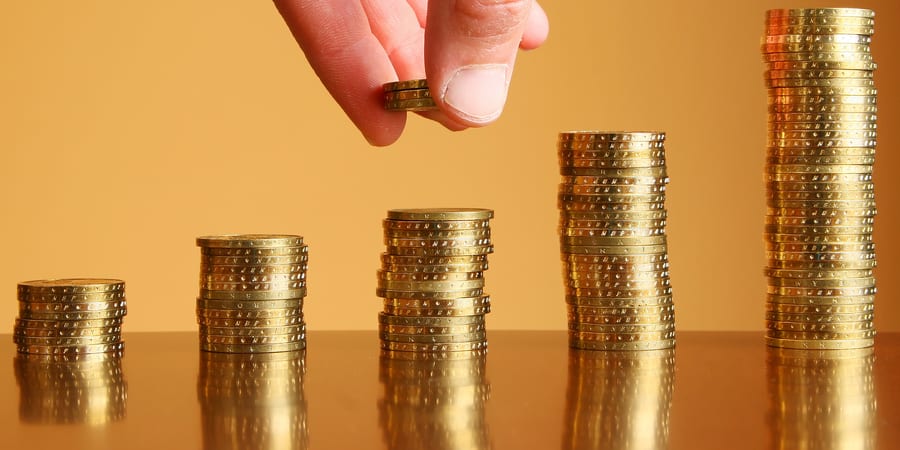
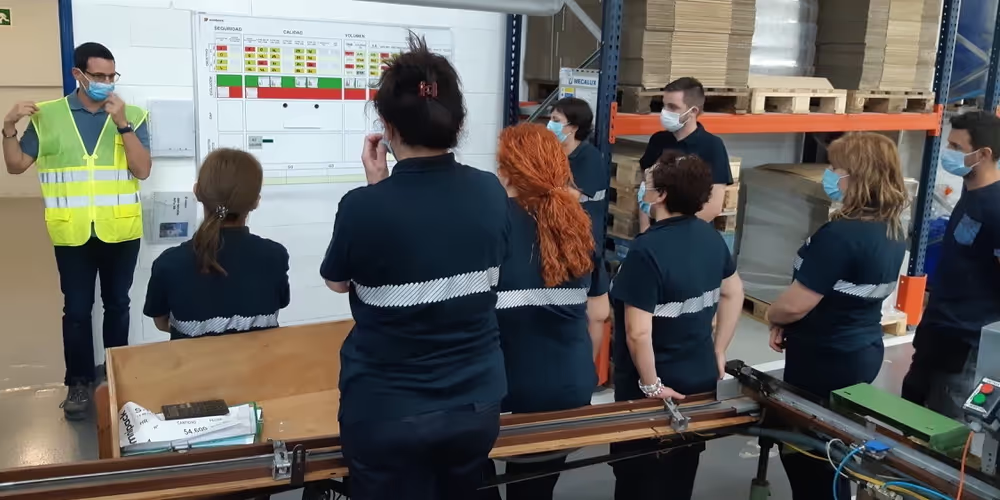
RESEARCH – What kind of financial results can a SME owner expect from a lean transformation? To find out, the author of this interesting research analyzed the performance of 100 Italian small and medium-sized companies.
The idea of “lean management” can refer to both individual managerial behaviors and, more in general, the set of principles and practices characterizing the adoption of lean thinking in an organization.
In the first case, lean management is closer in meaning to the idea of “lean leadership” and entails the development of behaviors that foster continuous improvement at the front line, such as respect for people, asking questions (rather than providing answers), going to see to really understand the work and the causes of problems, and scientific problem solving. In the second instance, lean management describes the lean philosophy more in general.
In its more general meaning, lean management – or lean thinking, if you prefer – derives from the Toyota Production System and is now recognized as a superior management approach that, through continuous improvement, customer focus, teamwork and relentless people engagement, leads to great results in terms of quality, performance, delivery, and cost. The promise of lean management is to create the most value for customers using the least possible amount of resources. As an approach to running a business, it brings benefits to all parties involved, from customers to employees, suppliers to wider society.