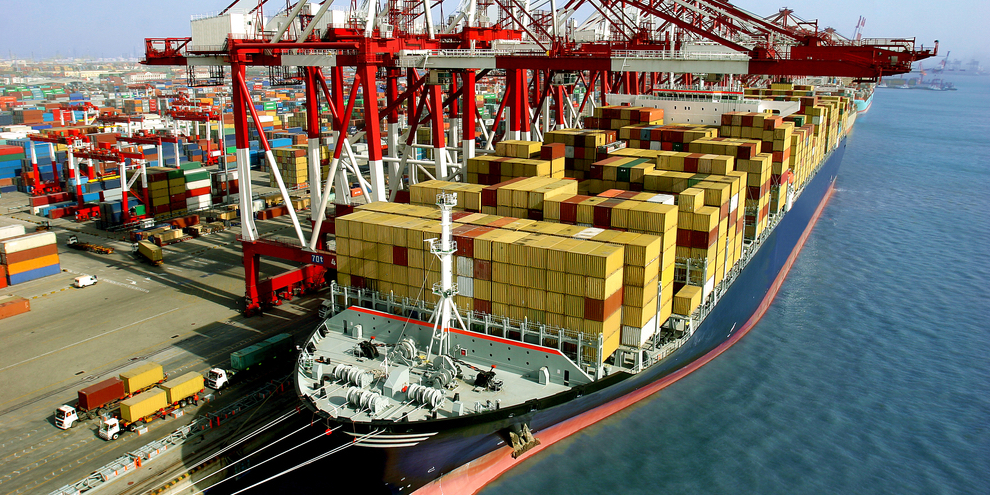
Once More, All Together Now: “JIT is …”
FEATURE – As global supply chains suffer ongoing disruption, the author addresses the misconceptions on Just-In-Time that keep appearing in the media.
Words: John Shook, Chairman, Lean Global Network
Just-In-Time means, first of all, “in time”. As in… not late. No shortage, no stockouts. Once you know you can achieve that – no stockouts – you try to have in your supply chain “just enough”. Not too much, not too little. Not too soon, not too late.
I’ve lost track of the number of articles that have appeared over the past year blaming global shortages on JIT. Such articles, like The World Is Still Short of Everything. Get Used to It, invariably include interviews with experts who are quoted out of context. If you read the experts’ comments shed of the reporters’ interpretations, you rarely find condemnation of JIT, per se.
Another recent article had the catchy title of “How the World Ran Out of Everything” and featured a photo (similar to the one above) of a veritable Mount Everest of shipping containers and asserted that JIT shipping is at the center of what has gone awry: “Just-In-Time is running late”.
How can that image of shipping containers stacked mile-high and the description of convoluted far-flung supply chains possibly appear to anyone like anything remotely resembling something called “Just-In-Time”? Answer: it can’t, unless you are not taking the matter seriously.
MISCONCEPTIONS
The misunderstandings on JIT come from a variety of sources. To mention a few: schools still teach “supply chain optimization” as a set of algorithms divorced from the messiness of real-world operations; IT companies are invested in (and the world is enamored with) tech solutions, such as the supposedly turn-key ERP systems that for almost 50 years now have failed to deliver on their promises; business leaders still possess mindsets steeped thoroughly in the paradigm of mass production with narrowly focused ROI thinking (lucidly broken down over two decades ago by Prof H. Thomas Johnson of Portland State University).
Misunderstandings started from the beginning, actually. The first book on the topic in English – Zero Inventories by Robert “Doc” Hall – featured excellent and ground-breaking content but had an unfortunate title. Hall knew the title was wrong, but in the traditional publishing industry, the publisher decided titles. The content was revolutionary, the title was catchy – too many business leaders never got past the cover.
Rather than merely complain about misunderstandings, I should acknowledge that there are two intractable challenges here. First, the underlying fundamental mindset of lean value stream management differs radically from conventional (mass) thinking – from “more is better” to “just enough – as does the associated conviction that lean is a learning system, designed to enable learning at each step of the way. Secondly, the profound knowledge that comprises lean thinking and practice is so rich that the deeper you choose to go as a learner, the deeper lean thinking will take you. So, additional levels of meaning and applications continue to unfold. Wrestling lean ideas down at any point in time can be frustrating to those who seek to do so, because there is always more to discover.
“JUST ENOUGH”
“Toyota rethinks its JIT system” is another bit of misinformation. Indeed, in a way Toyota “rethinks its JIT system” every time it ships a product. JIT, as all dimensions of lean, are intended to allow for constant learning and improvement, especially at the front lines of value-creating work. However, the fundamental thinking of JIT is not “reconsidered”, rather it is confirmed by the decision to stockpile four months of critical components prior to the shortages that the company saw coming. That action was totally consistent with JIT and is enabling the company to lead the global industry in sales again this year, even surpassing GM in its home North American market.
Having said that, while Toyota pioneered JIT and its resulting lower inventories, it is nice to now see the auto industry finally tackling its massive finished goods problem. For the better part of a century, auto makers (including, by and large, Toyota) operated on a model that presumed an inventory of several months of completed vehicles. Incredible! Horrific! It is excellent to see that paradigm getting crushed by the twin forces of pandemic-induced shortages and the welcome movement to direct sales, pioneered by new entrants like Tesla and Rivian, which obviates the need for huge amounts of finished product inventory in the field. Rivian shipped its first vehicles last month; each vehicle has a customer’s name on it when it exits the assembly line, and the company intends to operate with zero finished goods inventory (perhaps vindicating the original title of Doc Hall’s book).
It is true that JIT aims to hold less at each point throughout the system. Holding just enough – not more, not less – enables responsiveness. However, what is “just enough” (for an unexpected look at that topic, check out the wonderful book Just Enough by Azby Brown) is a function of various characteristics (per the above) including stability and predictability, as well as business decisions regarding capacity installation. The current global shortages are essentially a function of demand volatility and problematic decisions regarding what capacity to install where. The headlong rush to use China as capacity base for everything is rightly being challenged. It’s about time.
Once more, all together now: JIT aims to ensure the right item is in the right place at the right time in the right quantities. It achieves that aim by seeking a deep understanding of supply chain dynamics, generally, and the characteristics of each item in each supply chain, specifically, and applying to them a defined set of value stream management principles and practices. Practitioners ask, what is the predictability and variability of each item at each spot along the chain? How can lead-times be made shorter and deliveries more reliable and responsive? Frequent movement of smaller amounts fits hand-in-glove with empowering the front lines to own their own, self-initiated experiments. Long-distance, convoluted supply chains driven by black-box IT systems fight against this intent, so extended enterprise decisions regarding capacity installation (where and how much) are critical to creating an enabling structure for a true JIT system to work effectively.
As to the question of inventory amounts, the more reliable and responsive the process of supply, the lower the inventory can and should be. When variability, instability, and uncertainty are high, inventories should increase accordingly as efforts are doubled to stabilize the situation and/or understand the variation. The principles are easy enough (if woefully misunderstood), but implementation can be wickedly complex. Some resources that can help include the classic JIT Factory Revolution by Hiroyuki Hirano, Christoph Roser’s recent comprehensive review of the “pull” aspect of JIT All About Pull Production, and Art Smalley’s practical guide for factory applications, Creating Level Pull.
JIT IS THE SOLUTION, NOT THE PROBLEM
Some of the experts quoted in anti-JIT articles do, correctly, condemn narrowly focused cost-cutting approaches as the demon underlying the global supply mess we are in. Indeed, these approaches negatively impact the health of the supply chain, the profitability of a company, and the fulfilment of customer needs. A lose-lose-lose situation. In the “World is Still Short of Everything” article referenced above, one expert observes that, “There is genuine uncertainty here”, while Harvard’s Wally Shih laments, “We have this vicious cycle of all the natural human instincts responding and making the problem worse.” It’s true that genuine uncertainty is high and human instincts are making matter worse. But the causes of those problems have nothing – zero, nada, zip – to do with JIT. JIT is not a cost-cutting strategy/practice. It is a strategy/practice to build a resilient supply stream with no (minimum) shortages and no (minimum) waste. This leads to lower costs, higher profitability, and happier customers. The very description of the supply chain philosophy needed today. A win-win-win situation.
Just-In-Time starts with “in-time”. I don’t think that should be so hard to understand. The concept is classic Drucker, really: effectiveness before efficiency. But, difficult to grasp or not, it is true that it is difficult to achieve, and in today’s world is getting harder. Rather than the cause, JIT is in fact the cure for today’s supply chain ills.
THE AUTHOR
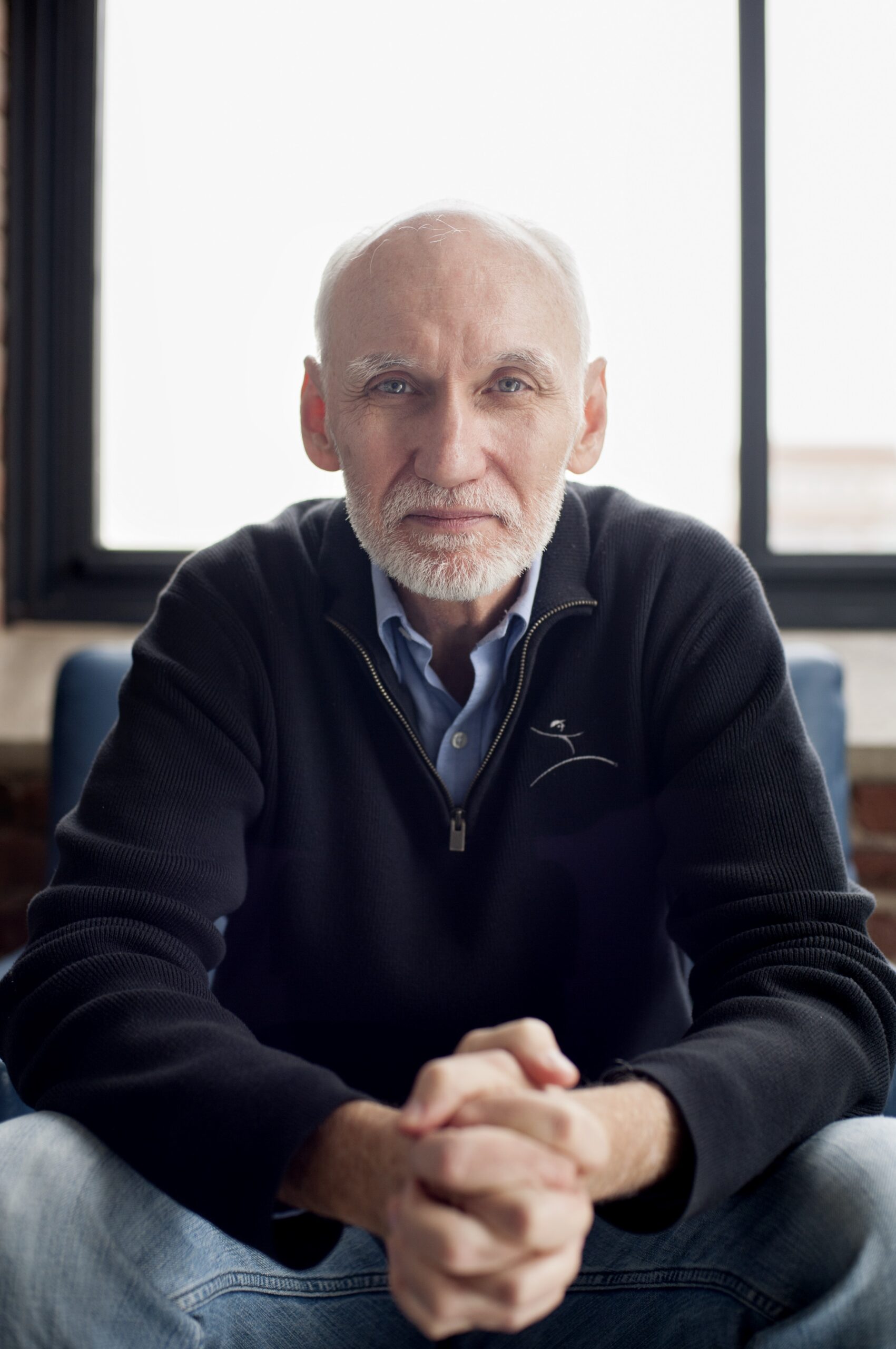
Read more
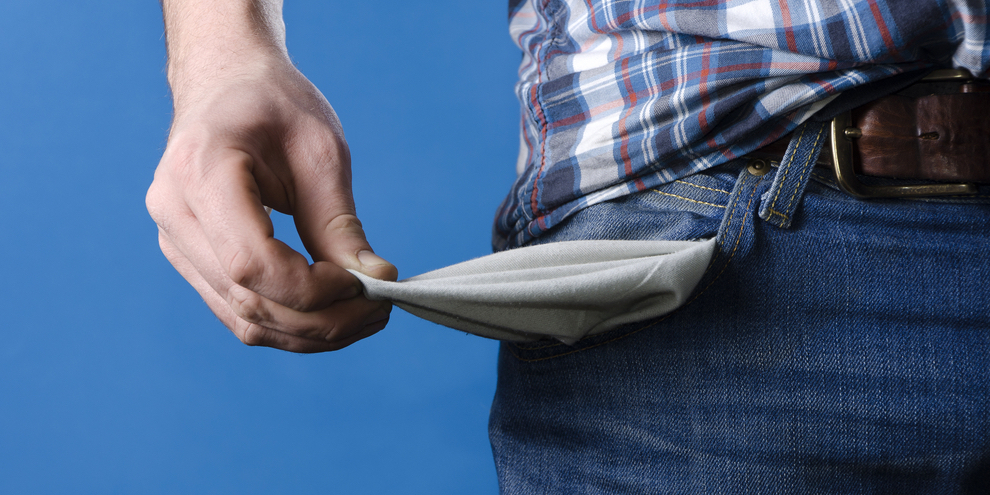
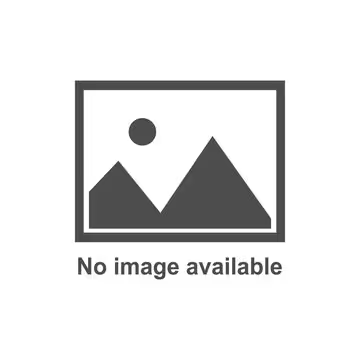
FEATURE – As inflation bites, the author offers us an insightful take into what it really means to understand a company’s costs. Hint, it doesn’t involve passing them on to customers.
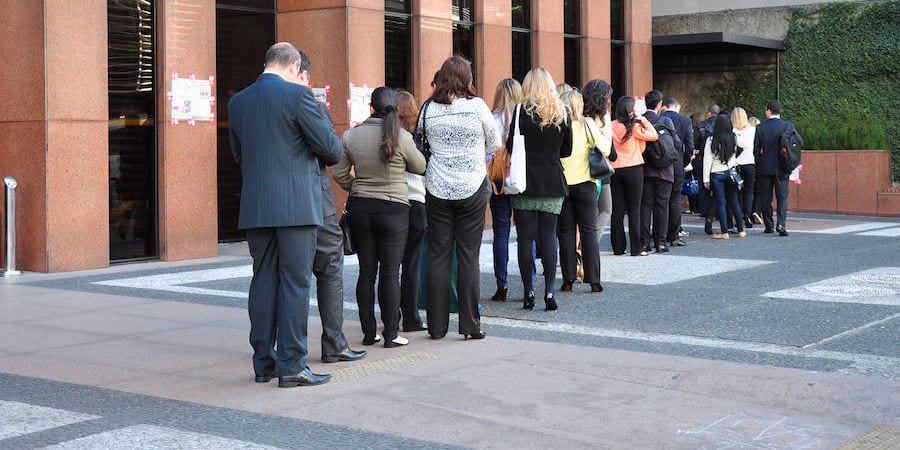
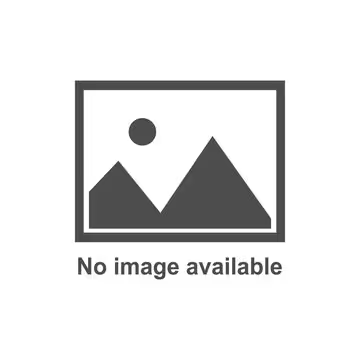
WOMACK’S YOKOTEN – What does a lean employer look like? In this month’s column, the author reflects on the long-term commitment to employees a company engaged in lean thinking should make.
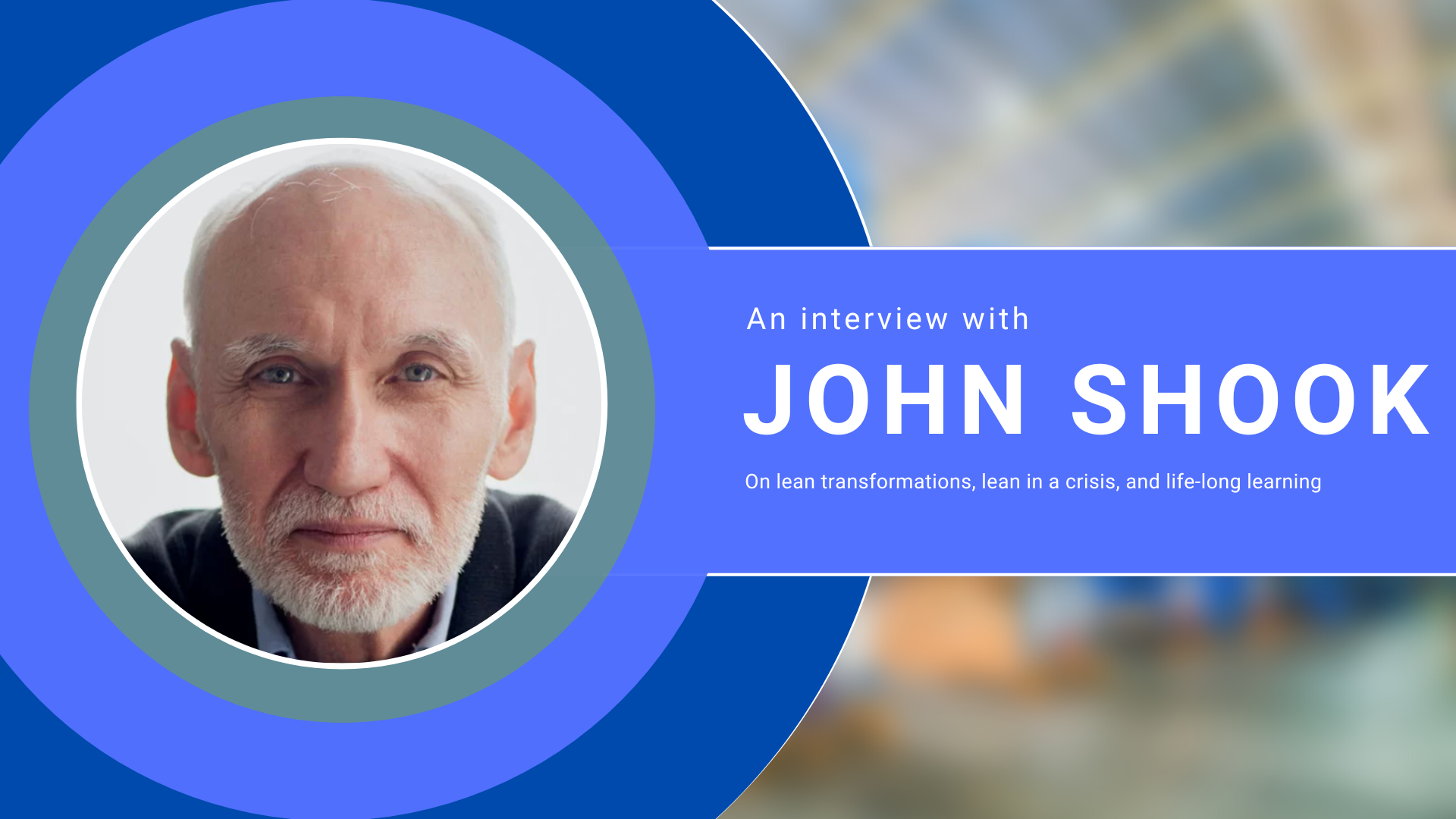
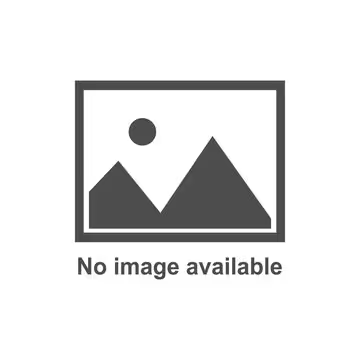
VIDEO INTERVIEW – We recently caught up with John Shook at the Lean Healthcare Academic Conference in Stanford and asked him to share his thought on the questions we need to ask ourselves in a lean journey and on lean in turbulent times.
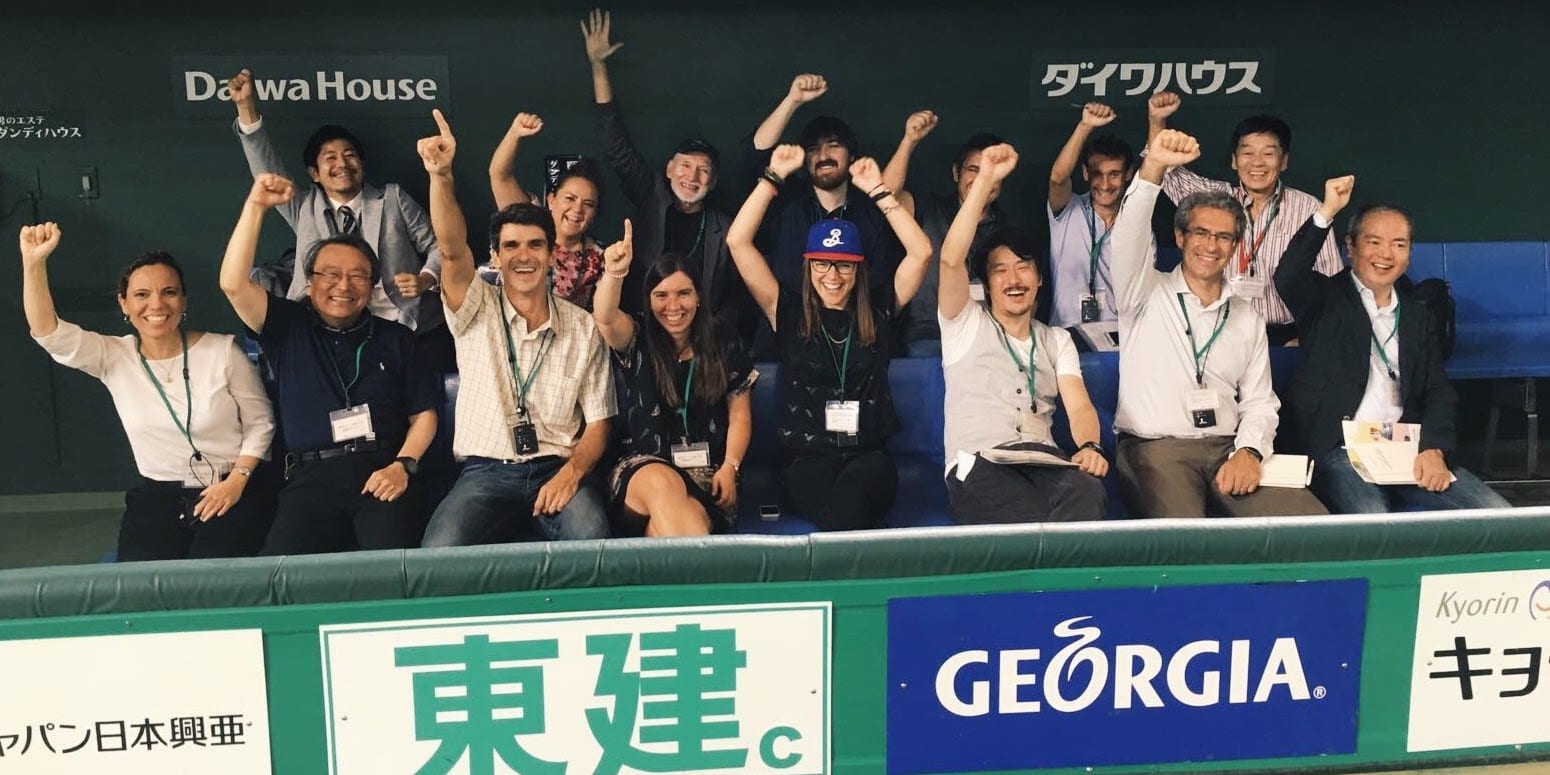
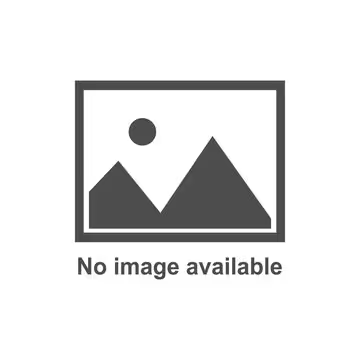
FEATURE – Study tours in Japan are an increasingly popular learning tool for lean practitioners. The author reflects on the first ever tour she ran and on what it left people with.