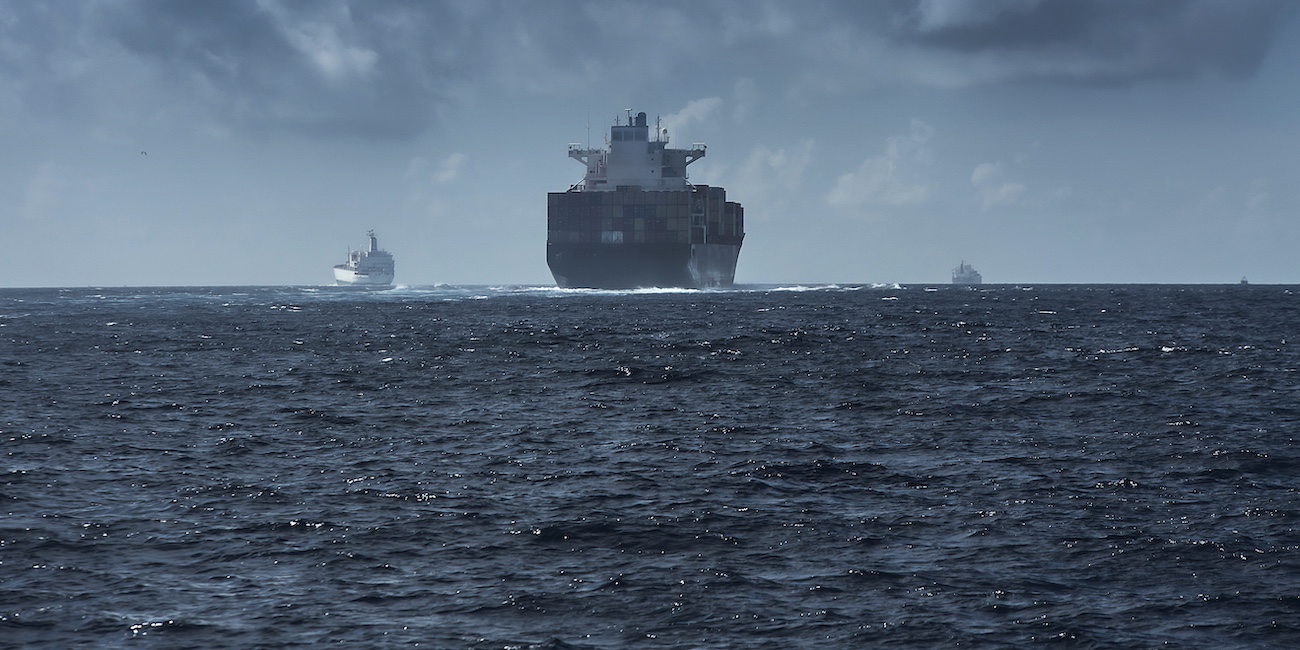
Lean in a chaotic world
FEATURE – Lean Thinking remains vital—but must now adapt to disruption with resilience, flexibility, and human-centric systems, says the author.
Words: Jim Womack
For decades, Lean Thinking has been a powerful force for transformation—helping organizations build stability, reduce waste, and create value through continuous improvement. But today, we find ourselves in a rapidly changing world, one where stability is no longer the norm. So, here’s a question I want to explore: how do we, as lean practitioners, adapt Lean Thinking to an era of disruption and uncertainty?
I’ve spent much of my career studying Lean and sharing it with the rest of world, always with the belief that organizations can be designed to perform better, eliminate waste, and improve continuously. What I’ve come to realize, however, is that the world in which these principles were developed was relatively stable. Yes, there was always competition, always the need to improve, but the underlying assumption was that the external environment wouldn’t change so dramatically or so often that it would upend entire industries overnight.
That assumption no longer holds true. Today’s businesses are facing geopolitical instability, economic shifts, rapidly evolving technologies—especially artificial intelligence (AI)—and new societal expectations about work and employment. As lean practitioners, we must shift our mindset from optimizing within stable conditions to adapting for survival in a volatile world.
CHANGE IS HAPPENING FASTER THAN EVER
Just in the time I’ve been preparing this talk, I’ve seen dramatic shifts taking place. One of the companies I admire most—one that has deeply embedded Lean into its operations—recently had a sobering discussion. With potential new tariffs being introduced, they suddenly found themselves needing to stand up major manufacturing operations in the United States, much faster than they had ever planned.
And this isn’t just a one-off case. Across industries, companies are dealing with geopolitical shifts, trade restrictions, labor shortages, and new regulatory pressures. Add to that the changing nature of work itself—with employers and employees having abandoned any sense of mutual obligation—and the challenge becomes even greater.
Technology is accelerating all of this. AI, in particular, presents a paradox for lean thinkers. On one hand, automation and AI-driven decision-making could eliminate massive inefficiencies. On the other, much of the technology appears designed to eliminate people rather than empower them. For decades, we in the Lean Community have insisted that Lean is not about laying off workers—it’s about creating more value with the same people. But now, we find ourselves in a world where entire workforces could be displaced by technology that is being developed not because it must be, but simply because it can be.
At the same time, climate change is introducing a level of unpredictability we’ve never seen before. Businesses are no longer just planning for normal market fluctuations; they must now prepare for supply chain disruptions caused by wildfires, hurricanes, droughts, and more.
Given all of this, the natural inclination might be to say, Well, maybe Lean itself needs to be rethought. But that’s the good news. We don’t need to rethink our fundamental beliefs and methods. What we do need is a new orientation—a new way of applying Lean to help organizations navigate chaos while maintaining the stability needed for long-term success.
WHY TOYOTA KEEPS WINNING
I want to highlight an example of how the lean mindset can help companies navigate uncertainty rather than be crushed by it.
A few years ago, the entire automotive industry became fixated on the idea that battery-electric vehicles (BEVs) were the only future for transportation. CEOs, policymakers, and analysts all declared that by 2035, we’d see nothing but BEVs on our roads. Major manufacturers rushed into the space, eager to prove they were “all in” on electrification.
Except for Toyota.
Toyota took a different approach. Rather than betting everything on one technology, they pursued a portfolio of solutions: improved hybrid vehicles, plug-in hybrids, hydrogen fuel cells, hydrogen-powered internal combustion engines, and BEVs.
At the time, they were ridiculed for this. People accused them of being behind the times, of resisting change. But Toyota wasn’t resisting change; they were managing uncertainty. They knew that markets, technology, and infrastructure would evolve in unpredictable ways, and they didn’t want to be caught without options.
Fast forward to today, and suddenly the narrative has shifted. The auto industry is realizing that BEVs alone may not be the perfect solution for every customer or every market. Toyota’s diversified approach has left them far better positioned than companies that went all in on a single technology.
This is the kind of thinking that lean organizations must embrace. Rather than trying to predict the future, we should be preparing for multiple possible futures.
RECOVERY OVER ROBUSTNESS: THE NEED FOR FAST ADAPTATION
For years, companies have been told to stockpile cash and resources as a buffer against uncertainty. And while financial stability is important, it is not enough.
Toyota’s philosophy has never been about looking for ways to predict every possible adverse outcome or simply weathering storms. Instead, they focus on recovering quickly when disruptions occur. That means:
- Developing human capital—training employees to solve problems and make fast decisions
- Creating adaptable supply chains rather than relying on fixed, rigid systems
- Investing in resilience rather than just preparing for a specific set of crises
During the COVID-19 pandemic, for example, Toyota showed how this philosophy works. While other manufacturers scrambled to deal with supply chain shortages, Toyota had built up a network of adaptable, problem-solving employees who could quickly pivot and keep operations running.
That ability to recover—not just endure—is what separates a truly resilient organization from one that is merely prepared for the last crisis, but not the next one.
SCALING LEAN: THE MISSING PART
Chaotic conditions often require big changes, fundametal make-overs of our organizations. In what I like to call the nail it, scale it, sail it cycle, our main challenge as lean thinkers is scaling Lean effectively.
We are great at nailing it—building MVPs, designing new systems, running pilot projects, and solving initial problems. We are also great at sailing it—sustaining Lean in mature, stable organizations. But when it comes to scaling it—taking an initial success and rapidly rolling it out across an entire enterprise or industry—we struggle.
I’ve worked with startups in autonomous vehicles and AI-driven industries that had brilliant ideas but couldn’t implement them at scale because they lacked structured operating and management systems. Without them, the best ideas in the world won’t go anywhere. Unfortunately, it turns out that standing up such systems is pretty hard, and this is a gap in the Lean movement that we need to address.
THE LEAN DREAM: A STABLE PLATFORM FOR VALUE CREATION
In 1950, following a financial crisis that nearly destroyed Toyota, the company was forced to split into Toyota Motor Sales and Toyota Motor Company. This humiliation led to a powerful resolution: "Never again." Toyota set out to build a stable platform for value creation—one that would ensure long-term success for customers, employees, suppliers, and investors.
Their dream was to create lifelong relationships:
- Customers for life by always being the best option.
- Employees for life through continuous development and new challenges.
- Suppliers for life by fostering mutual growth and improvement.
- Investors for life by delivering sustainable, long-term value.
Unlike companies focused on short-term gains, Toyota prioritized resilience, ensuring it could sail smoothly through economic turbulence. The result? In 74 years, Toyota has never laid off a permanent employee due to financial downturns—a record few companies can match.
Some call this dream impossible, but I refuse to believe that. Why shouldn’t every organization strive to create a stable foundation where all stakeholders win? This vision remains my North Star—and it should be yours too.
FINAL THOUGHTS
The world still needs Lean Thinking—whether it realizes it or not.
We, as Lean practitioners, have a responsibility to help organizations navigate uncertainty, build resilience, and create value even in turbulent times.
Our challenge is not to rethink Lean, but to rethink how we apply it in an era where stability is no longer guaranteed.
Let’s embrace the chaos—not fear it—and sail forward together.
This article is a summary of Jim's presentation at last year's Lean Global Connection! We are back this year with the fifth edition of our flagship event!
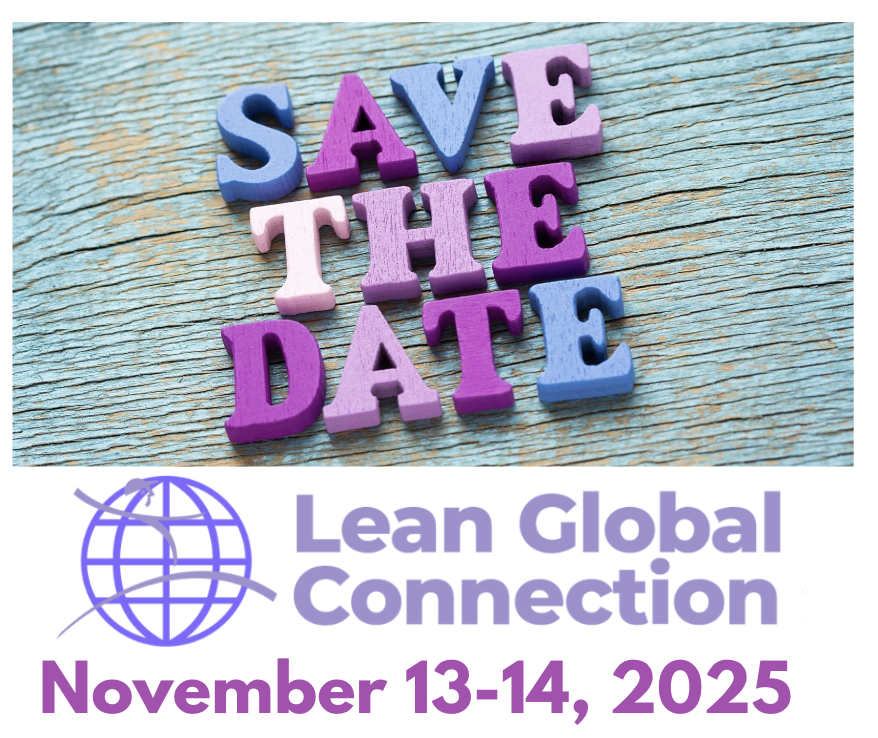
THE AUTHOR
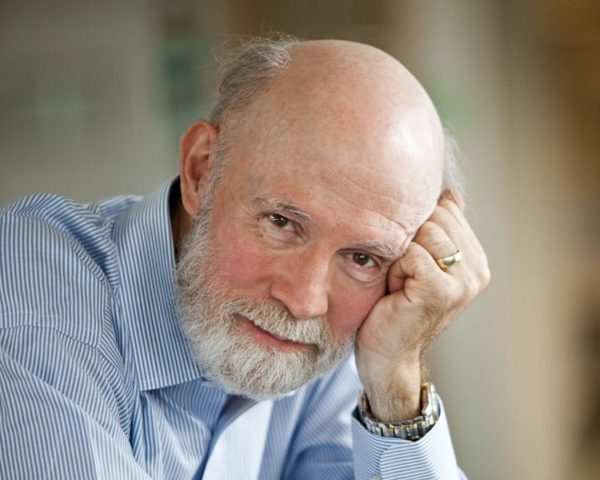
Read more
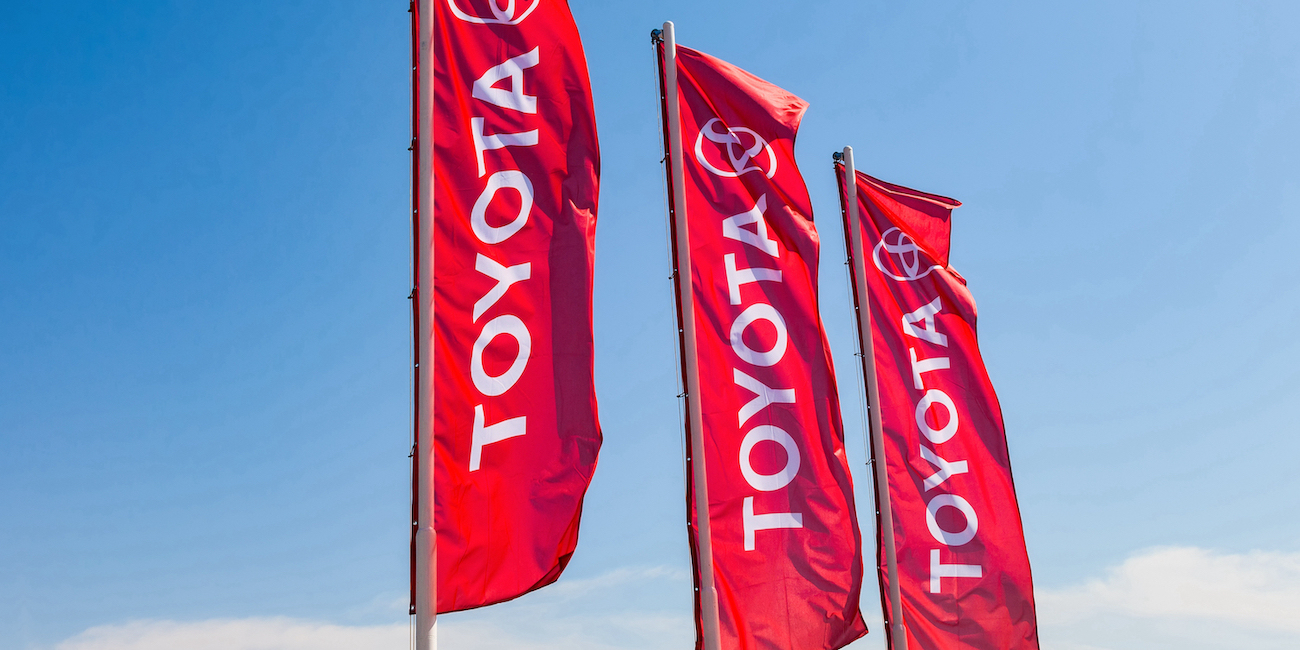
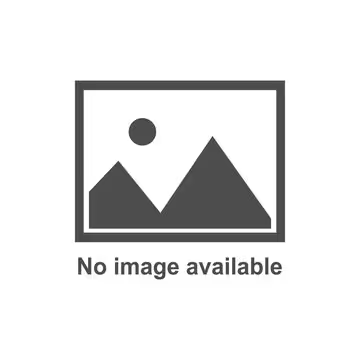
INTERVIEW – Looking back at the time he spent at Toyota, Mark Reich reflects on his experience working with Nate Furuta and on his legacy exporting Toyota cultures around the world.
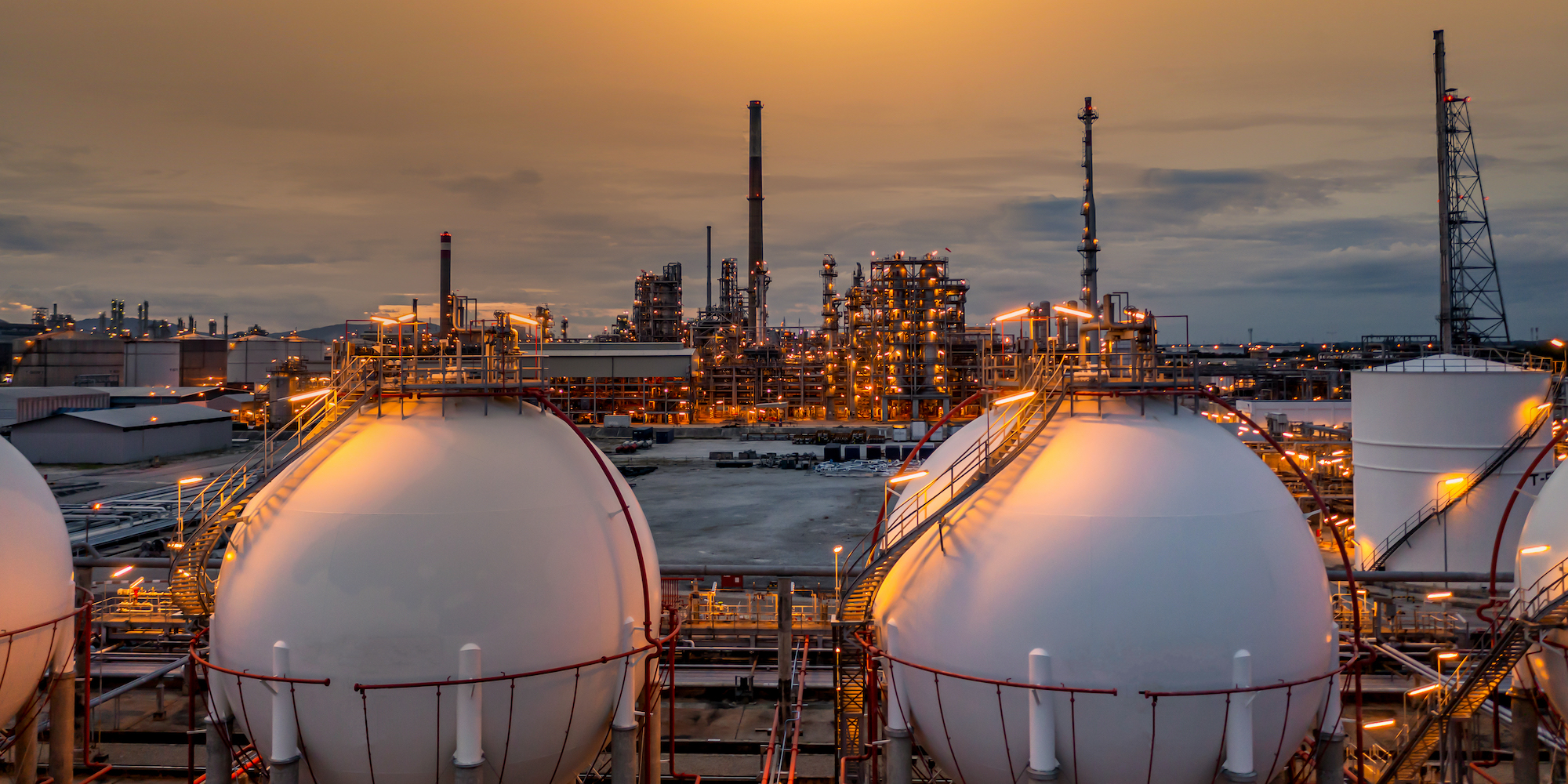
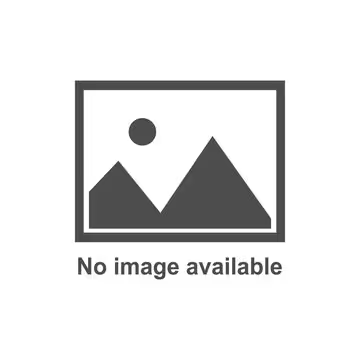
CASE STUDY – By leveraging Daily Management (DM), Supergasbras was able to change its trajectory and add more value to the customer in a critical sector for society.
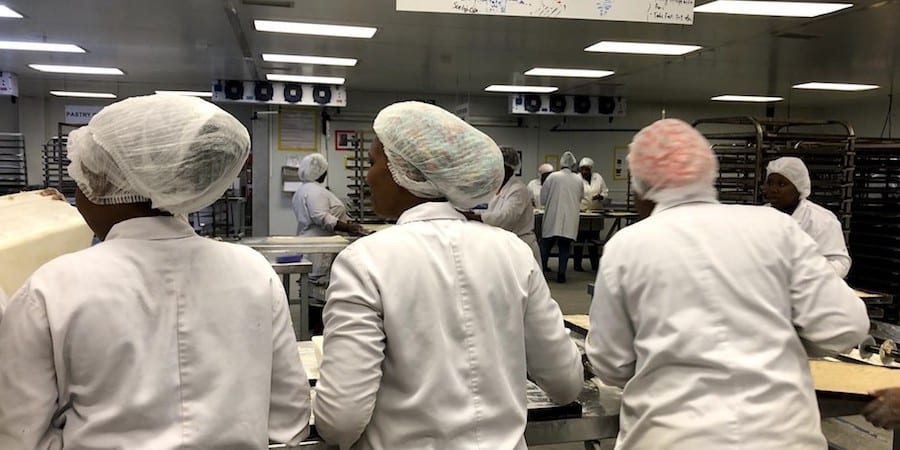
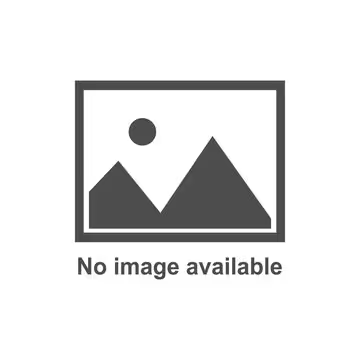
FEATURE – How reading lean books empowered people and transformed the managerial culture at an industrial bakery in the Western Cape Winelands in South Africa.
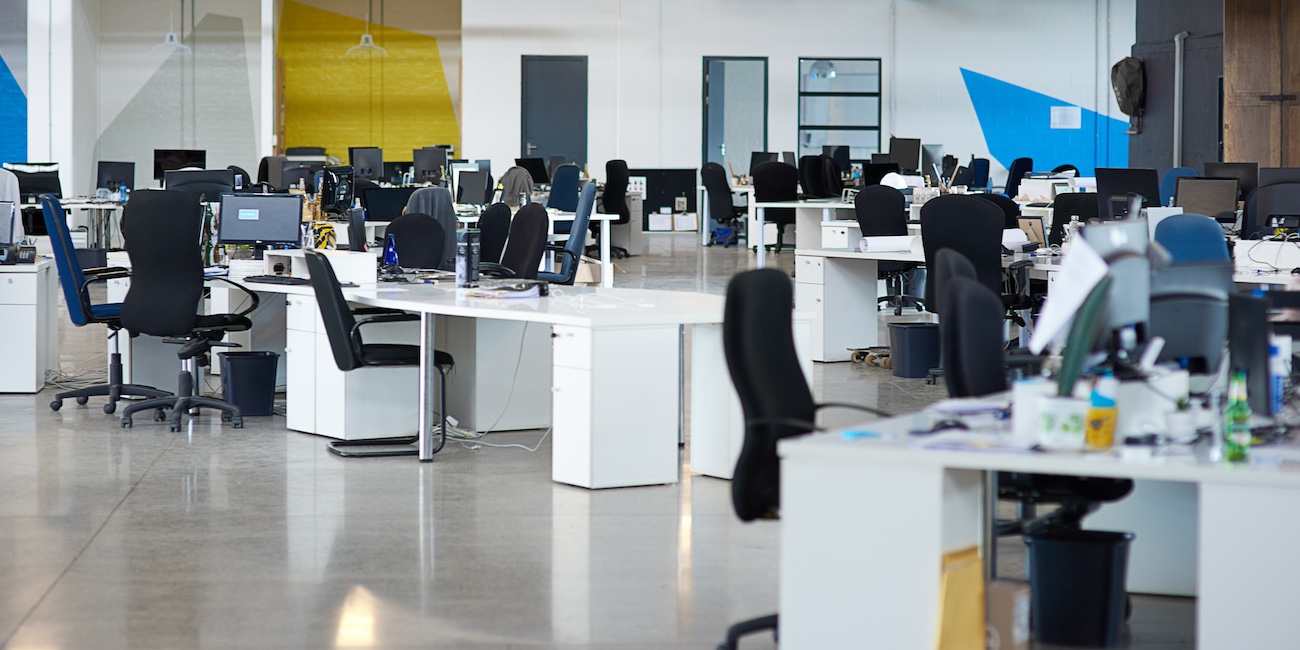
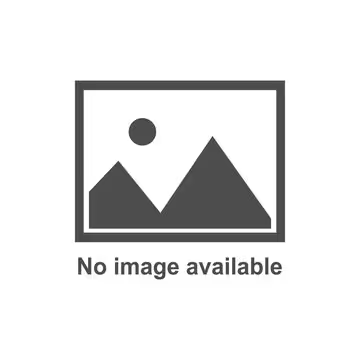
FEATURE – Attracting, developing and retaining talent has become a pressing issue in the corporate world, as new generations show skepticism towards traditional management. Lean is the answer, say the authors.
Read more
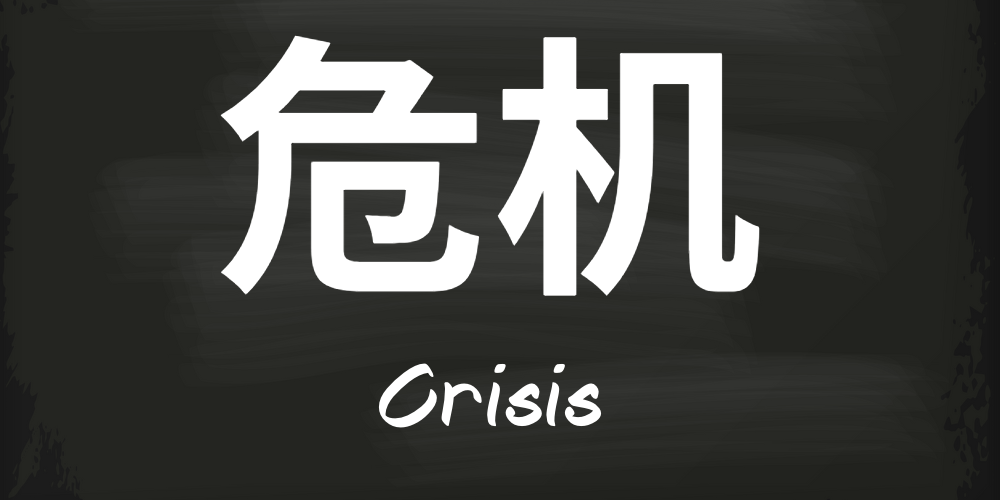
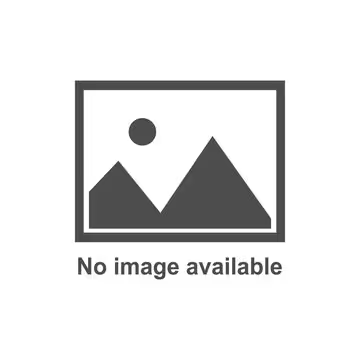
FEATURE – In this article, Michael discusses the four levers that organizations can work on to thrive in good times… and bad times.
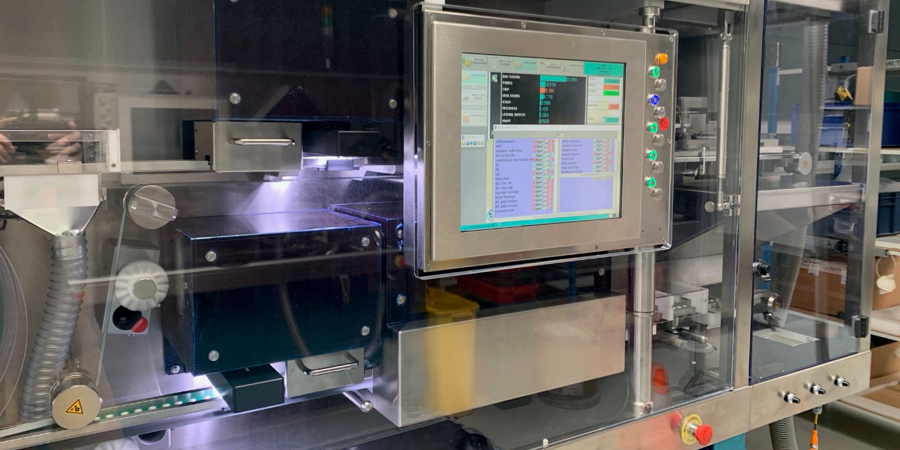
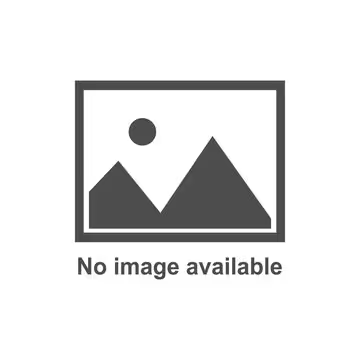
NOTES FROM THE (VIRTUAL) GEMBA – In this new series - one new article every week during the Covid-19 crisis) - the author asks companies how they are reacting to this health emergency. First up, Proditec.
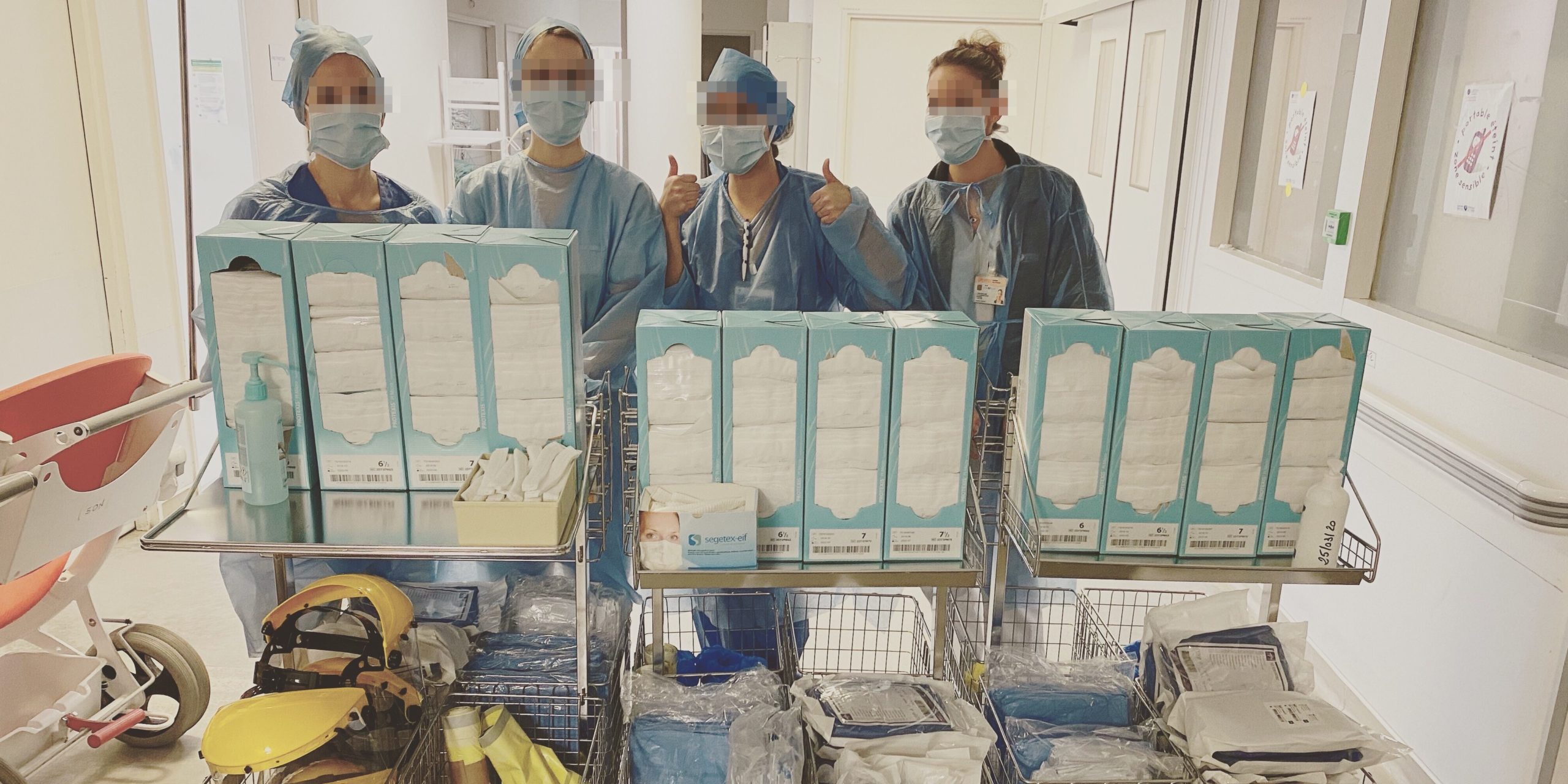
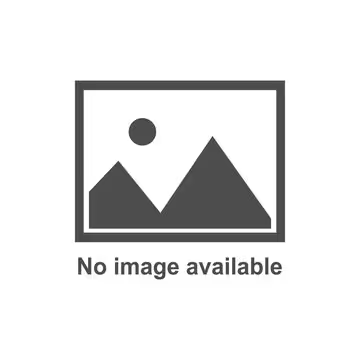
NOTES FROM THE (VIRTUAL) GEMBA – This small manufacturer is relying on Lean Thinking to keep the business running during the Covid-19 crisis, overcome the disruption in its supply chain, and even innovate.
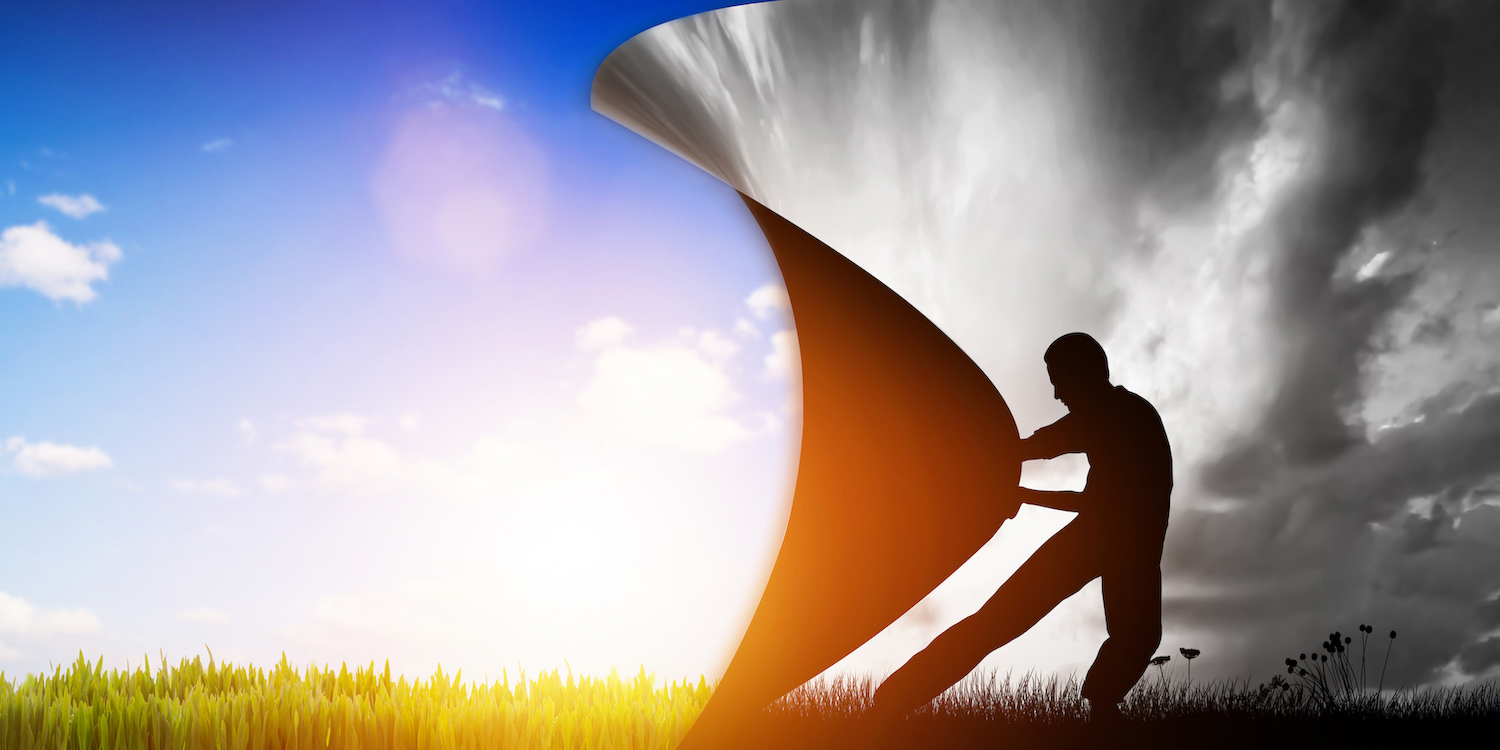
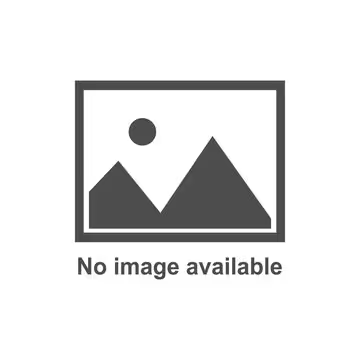
FEATURE – The author discusses how the daily practice of lean thinking develops perseverance and the grit a leader needs to improve an organization.