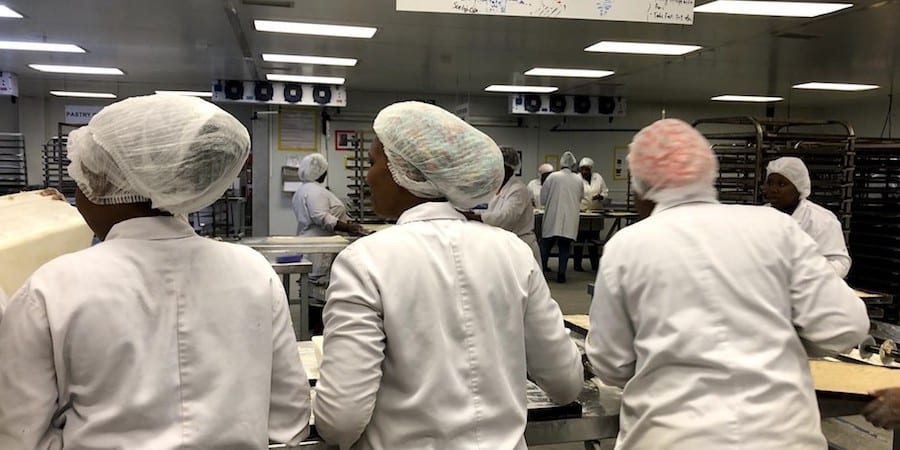
This bakery found out how inspiring lean books can be
FEATURE – How reading lean books empowered people and transformed the managerial culture at an industrial bakery in the Western Cape Winelands in South Africa.
Words: Stephan Drees, Operations Manager, Nibbly Bits, with Norman Faull, Chairman, Lean Institute Africa
It wasn’t that long ago – less than three years, in fact – that the shopfloor staff of our industrial bakery dubbed us managers with unspeakable nicknames linked to a European military leader and unmentionable dictator. And it was not just that I am French and my colleague, Production Manager Bernd Strauss, is German. It was more a reflection of our management styles.
Back then, Nibbly Bits – out of our bakery in the quaint town of Wellington we produce biscuits and rusks for a high-end, national retailer in South Africa – was going through a tough period, including a two-week strike reflecting the discontent about wages and working conditions. The CEO, Andre Haasbroek, and I did some soul-searching, trying to find a new management style, away from traditional command-and-control, that would restore both profitability and morale. In a tentative step at the time, I signed up to attend a two-day public workshop of the Lean Institute Africa. It was in early July 2015 that my lean journey began.
Something in the workshop struck a note of relevance and optimism in me. I decided to send some of my colleagues, including Bernd, on subsequent courses, and more advanced courses. I myself signed up for them more than once! Slowly, over 12 to 18 months, I accumulated a group of 10 or so Nibbly Bits managers who had a common introduction to the concepts of lean thinking.
In the first year or so, we didn’t see a lot of actual performance improvement. We tried 5S, and aspects of the Toyota Kata, but they did not “stick”. Then we had another look at the Lean Transformation Framework with its five dimensions and decided to focus on our management system and on changing our culture. And on getting our people onboard.
In the picture below, you can see me behind my desk: note the references on the wall and desk to the Lean Transformation Framework, the famous The Manager’s job at Toyota slide, and Daniel Kahneman’s book Thinking Fast and Slow.
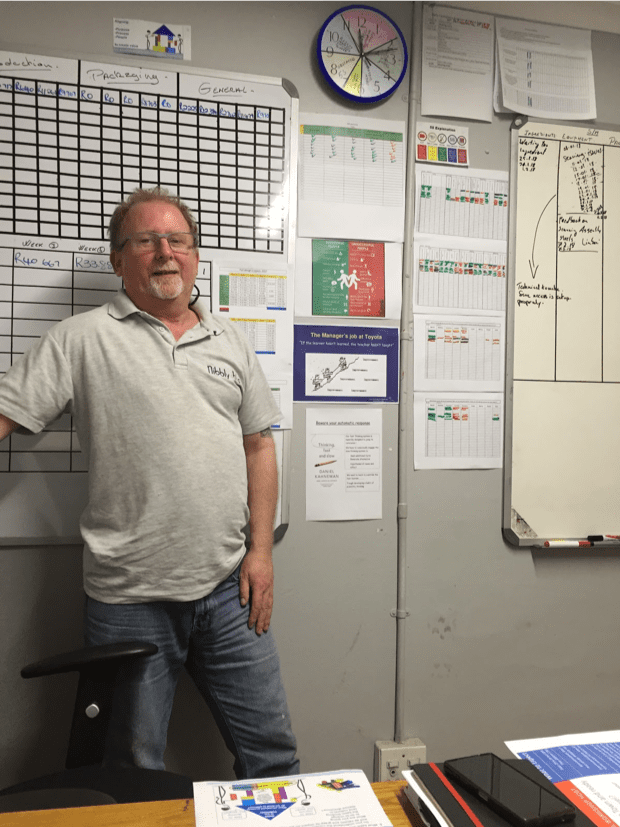
At one point, our CEO gave me a copy of Carol Dweck’s Mindset. I was 50 years old and had read about two books in my life – and I cannot recall their titles. Like Bernd, I trained as a pastry chef, but that book changed everything. Now I read voraciously. On the wall beside my desk I keep a poster of my reads since then. There are 27 covers now; a month ago, there were 22.
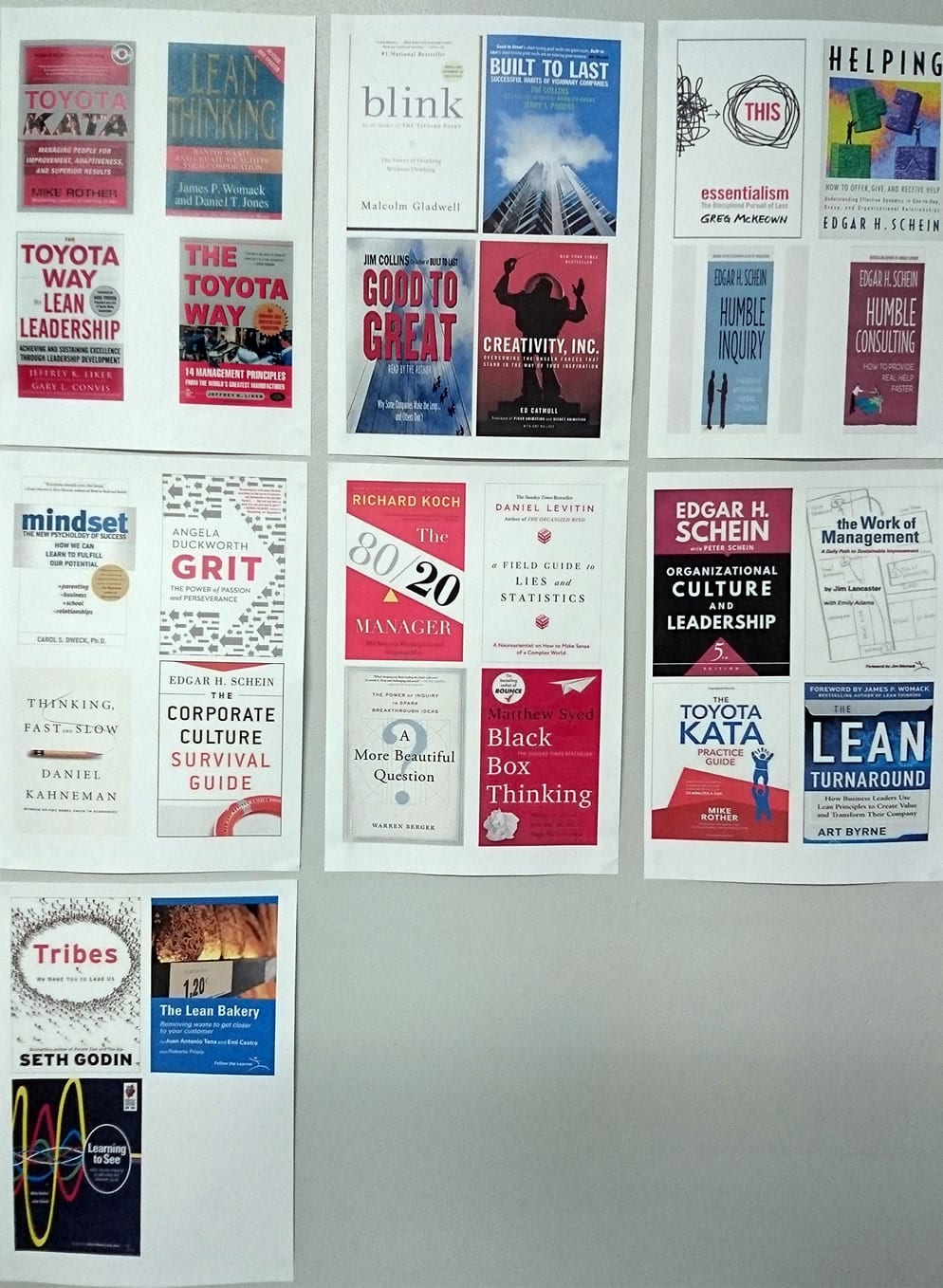
I also passionately encourage my colleagues to read, acquiring some of the books in audio version so that ‘reading’ can happen for them on the commute to and from work. We have even built into our morning production meeting a Book talk feedback slot – shown on the photograph below of the clock face that displays the standard meeting agenda. I invite three different shopfloor workers into the meeting every day, so that they can see how the planning of the day is done and how the obstacles to better working and better products are addressed. In every one of these meetings, I expect feedback based on the book Mindset. Together with Jim Lancaster’s The Work of Management, this title has become “compulsory reading” for my team.
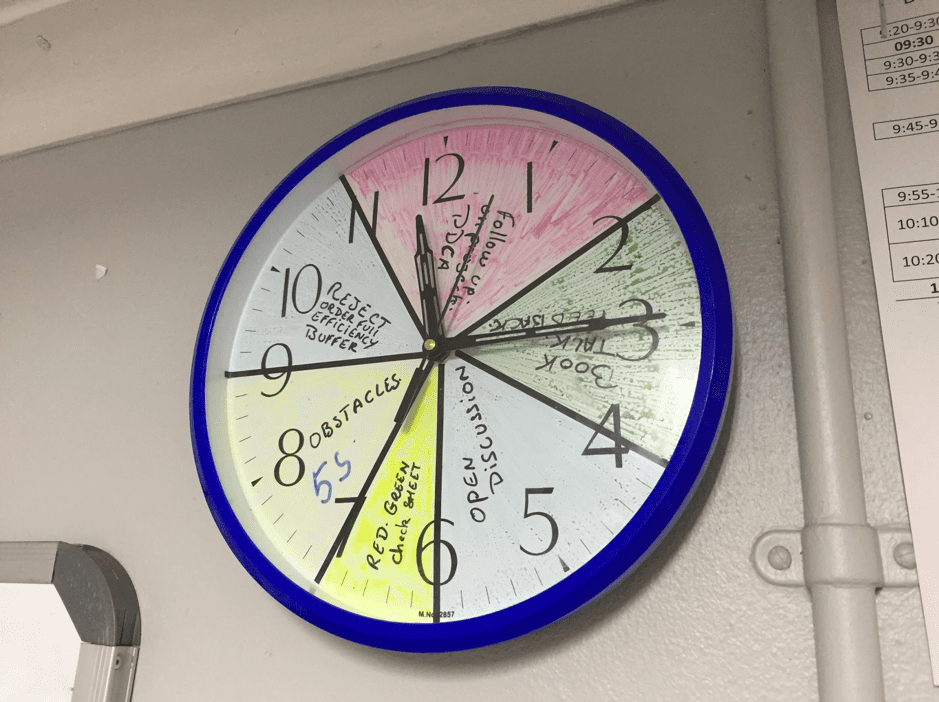
As part of my own standard work (Self-monitoring tasks), I use a check sheet with the five points I have prioritized to work on each day. The first item is ‘Read every day’.
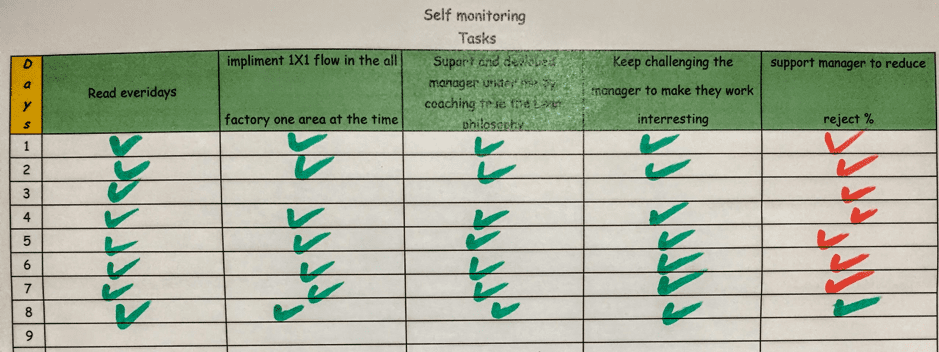
Of course, we read The Lean Bakery and were delighted with it. More significantly, as with all my reading, it has led to action. My specific focus from Bakery is the pursuit of one-piece flow: I have balanced the flow of our highest-volume line (rusks) through the scaling/weighing of ingredients, to mixing, panning, trolley loading, to the ovens, setting the cadence on the bottleneck cycle time. The photograph below of parked, empty oven trolleys is testimony to the dramatic drop in work-in-process.
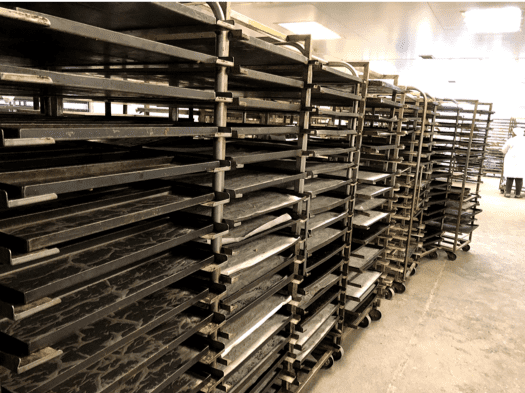
LEAN READING, LEAN THINKING
Nibbly Bits was established in 1996 by Andre Haasbroek’s father, with a small range of rusk products supplied to a national retailer of premium foods and quality clothing. I joined in 2003 when there were just 30 employees. Growth was rapid, closely tied to that of the national retailer. By late 2004, there were 150 employees and we moved to a larger, 3,000-sqm factory in a rural town about an hour’s drive north of Cape Town. Today, we have 700 employees and 150 SKUs. Andre is contemplating expanding beyond the current 5,200 square meters, but after reading The Lean Bakery I have to seriously question the need to expand the floor area!
In the picture below, I am with one of our packaging managers, Veronica Abrahams – another person who is finding that reading is changing the way she views her work and her world. Note the sketch in the top left behind us: it was done by a front-line employee after a conversation he had with Bernd Strauss (using insights from the book Humble Inquiry by Edgar Schein) about how to communicate a safety and quality message to staff. Instead of “pushing” the proposal, Bernd “pulled” the suggestion and sketch! It has proven more effective than anything tried before to make the same point.
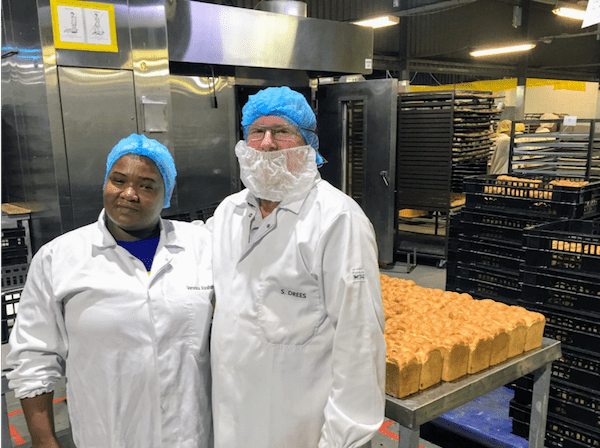
I know that for many of our folks, whose first language is either Afrikaans or Xhosa, reading or listening to audiobooks in English can be challenging, but I believe that persevering and supporting them in this effort is paying off. A few months ago, I was doing some grocery shopping in the nearby town. I was wearing a Polo shirt with the Nibbly Bits logo on it. At the checkout counter, the clerk asked me if I worked there and told them of a friend of hers who also worked at Nibbly Bits and had “read this amazing book called Mindset, which has changed her attitude to so much”. She, the checkout clerk, was now also keen to read it!
Luckily, those European military-dictator nicknames have disappeared from the Nibbly Bits vocabulary. The Lean Institute Africa workshops have resulted in shopfloor experiments and are showing improvements in yield, quality and capacity. But it is the books that are really transforming the mindsets of our people. And it is clear the effect is also reaching their homes and broader communities.
What about you? Do you read every day? What difference would reading, followed by immediate experimentation based on the books’ insights, make? To my colleagues and me, it has shown new ways to add value to the world.
Join Lean Institute Africa at their next Lean Summit
CAPE TOWN, October 30th - November 1st
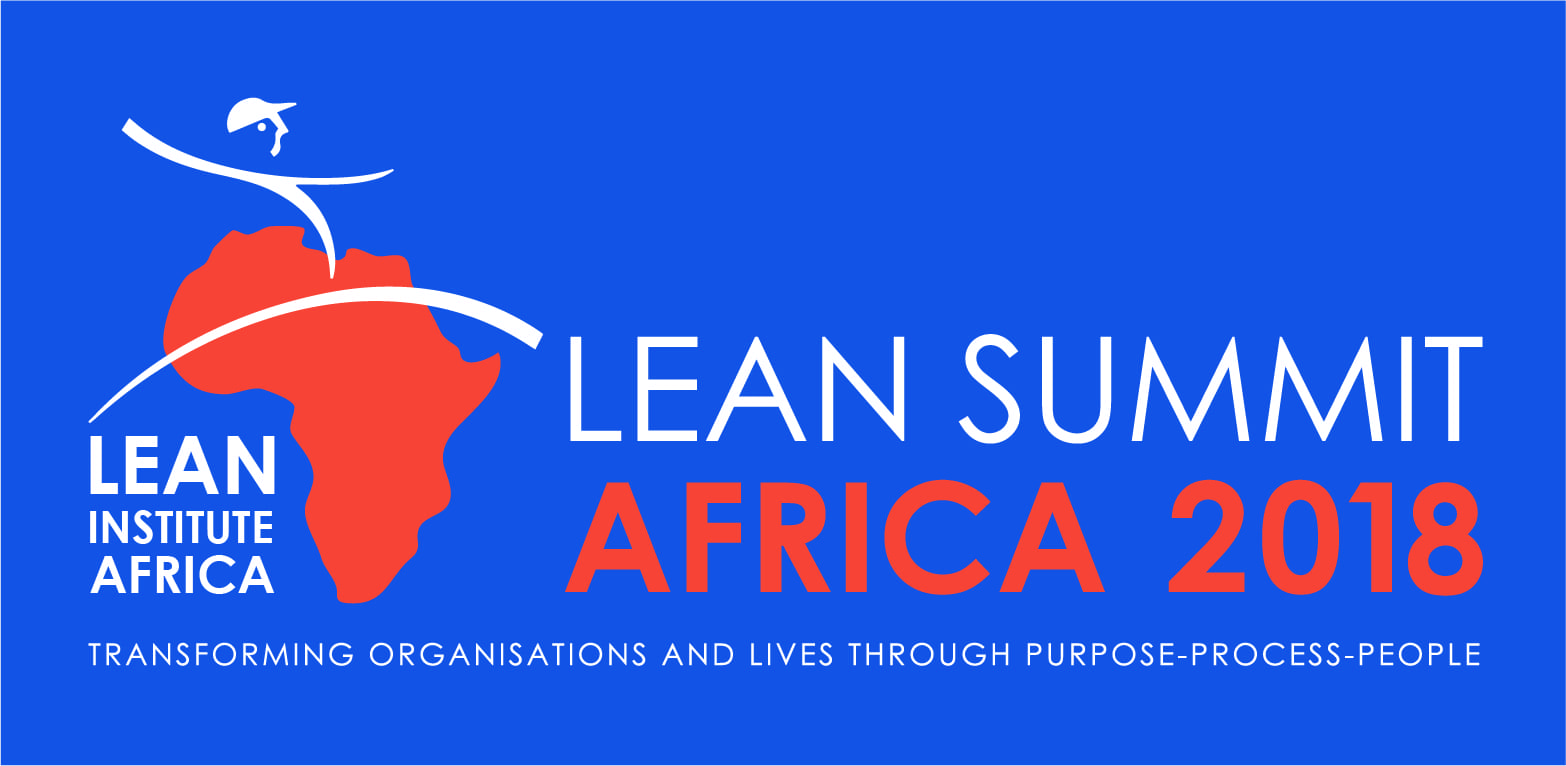
Speakers include Takeyuki Furuhashi, Kim Barnas and Dave Brunt
For more information or to register, click HERE
THE AUTHORS
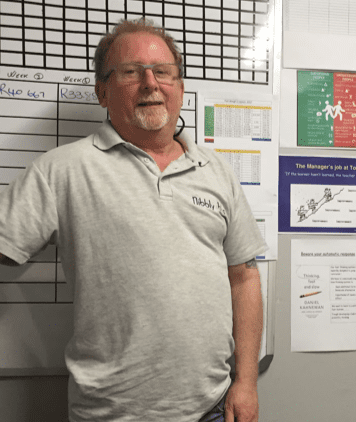
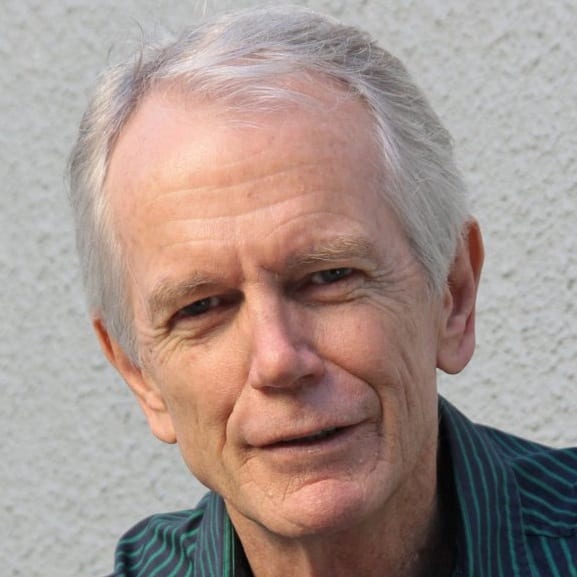
Read more
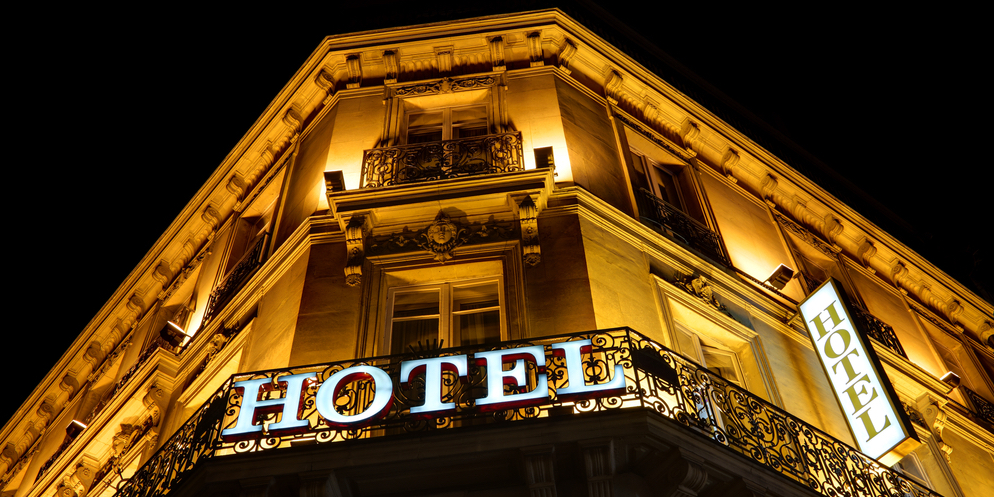
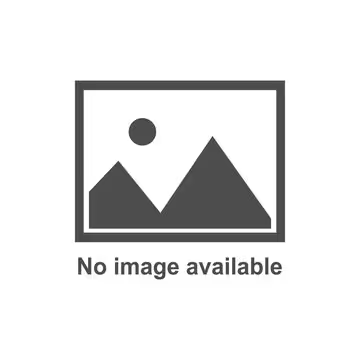
INTERVIEW – Juan Pedro Gonzalez is a pioneer of lean in hospitality, having spearheaded the transformation of Spain’s Dreamplace hotels since the beginning. Here, he discusses what role lean can play in advancing the industry.
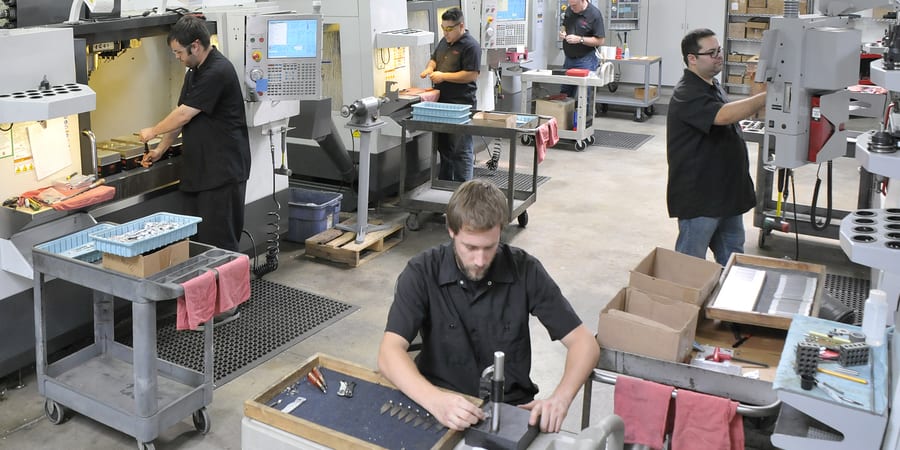
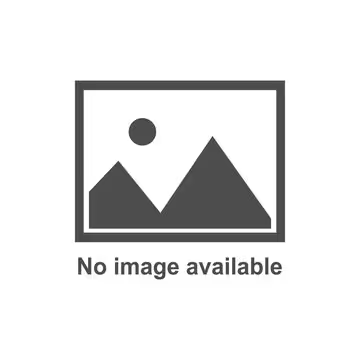
WOMACK'S YOKOTEN - If you are going to succeed at one of your resolutions for 2016, let it be that of always starting off a lean transformation with a deep analysis of the work at a single point in your organization, and then escalating your efforts to reach all the factors influencing the work.
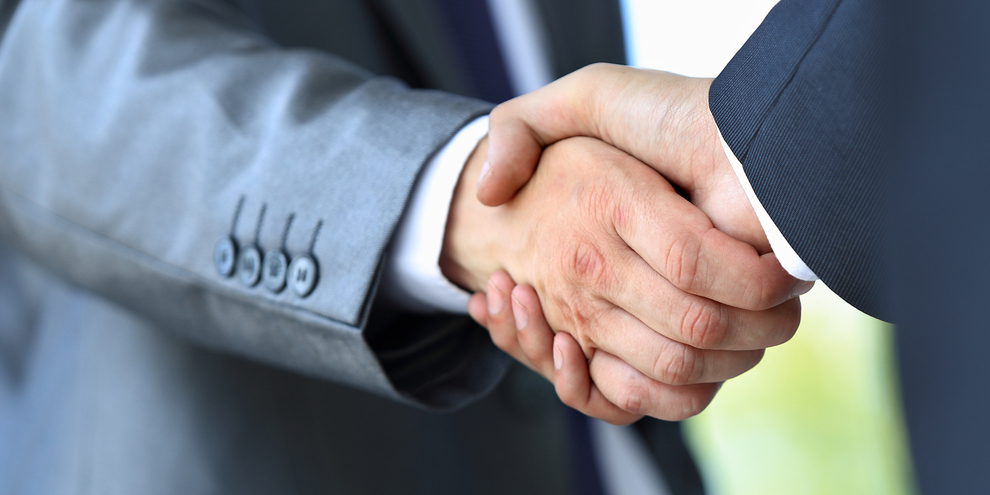
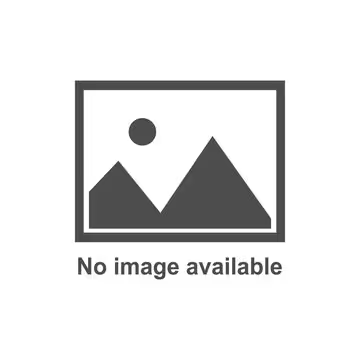
FEATURE – We are used to approaching strategic thinking as if our organization was in a position of stability and dominance. What if we started to look at it as creating better deals with all parties involved?
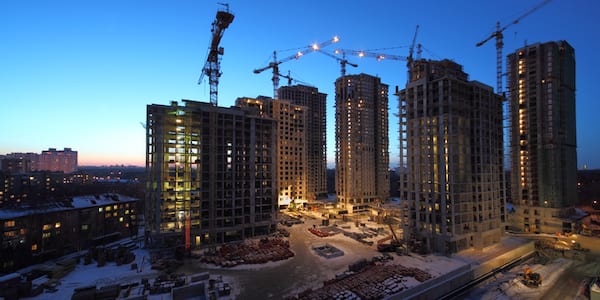
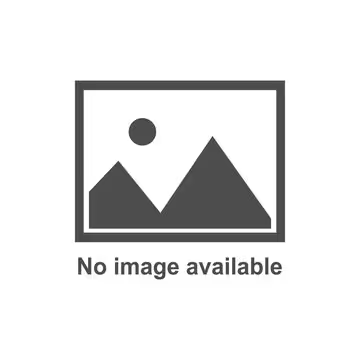
INTERVIEW – Brian Swain, Director of the Lean Construction Institute UK, has supported some of the largest construction projects in Britain, including London’s Olympic Village. Here he talks about the evolution of lean in the industry.