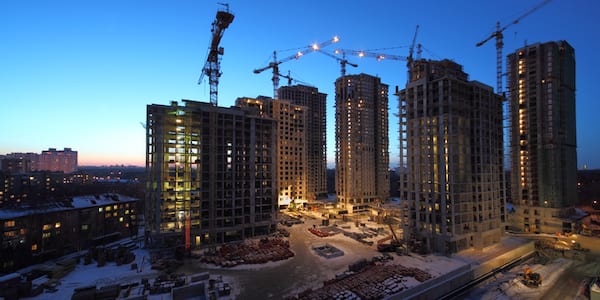
The state of lean construction
INTERVIEW – Brian Swain, Director of the Lean Construction Institute UK, has supported some of the largest construction projects in Britain, including London’s Olympic Village. Here he talks about the evolution of lean in the industry.
Interviewee: Brian Swain, Founding Director, Lean Construction Institute UK
Planet Lean: Where did the lean construction movement originate from?
Brian Swain: The application of lean in construction goes back to the early days of the methodology, as described by Dan Jones and Jim Womack. The Machine That Changed the World, which had provided us with shocking evidence on the superiority of lean production and effectively showed us that a new paradigm was coming, inspired a group of civil engineering academics from Berkeley and Stanford to see if the same approach could be applied to the construction industry. I am talking about names like Glenn Ballard, Greg Howell, and Lauri Koskela.
In the early ‘90s, Koskela wrote a seminal paper on the opportunities of lean in construction, and shortly after this movement of academics was able to raise money from a number of large construction companies that wanted research in that field to advance. At this stage, this was still a largely Californian phenomenon.
Two main things resulted from the academics’ efforts: first of all, the Lean Construction Institute was formed in the USA; secondly, the Last Planner System was introduced, a project planning system whose purpose is to bring stability to site management and to eliminate fragmentation in the supply chain by improving collaboration.
PL: When and how did these ideas spread to other parts of the world?
BS: In 1998, the UK government - to this day an advocate of lean construction in Britain - published the very influential Egan Report, Rethinking Construction (Dan Jones was one of its main authors). Sir John Egan was chief executive of BAA, which at the time was busy with massive construction projects including the rail link from Heathrow Airport to Paddington Station in London, the rebuilding of the various airport terminals, and of course the construction of Terminal 5.
With his past in automotive (at Ford first and Jaguar later) and in TQM, Sir Egan wanted the construction industry in Britain to embrace lean thinking. Following his report, the Californians went to the UK and influenced a number of organizations and projects, including BAA and the construction of St Pancras station in London.
Information started to flow in, and more and more organizations picked up the Last Planner System, which represents a whole new level of rigor applied to construction management and processes. Lean in construction helps to close the gap between an estimated project and a process-driven project and to address the lack of systemic thinking in the sector.
Lean construction is now a global movement. People are being inspired all over, institutes are being founded (we started the LCI-UK in 2006), and a drive towards lean is strengthening in large construction companies worldwide, following the example of organizations such as MACE and Skanska.
PL: Was this evolution similar to the one other sectors experienced? What’s going on today in the movement?
BS: Indeed, lean had the same evolution as in any other sector. We all started with a tool-based approach, and then we got that ah-ha moment when things became clearer. People are waking up to the idea of lean as a strategy, and the adoption of hoshin kanri principles is increasingly prevalent in the industry.
Something else lean can help us with is the developmental crisis the industry is currently experiencing. During the recession, many left construction for good, and today we simply don’t have enough people to respond to an expanding market.
In general, there are three main things happening in construction at the moment:
- The adoption of lean thinking in the industry is growing;
- Building Information Modeling (BIM – the process of creating and managing digital representations of physical spaces) and other 3D and 4D technologies are making their way into construction – more and more people are now seeing the great advantages (the main one being clash detection capabilities) that 3D and 4D software can provide us with;
- Young people are coming into the sector, and their mindset is 100% digital - a 22-your-old architect who starts working today is already well versed in 3D design, something much more uncommon to find in older generations.
PL: What is the impact of modern technology on the construction industry? And what is the relationship between lean and technologies such as BIM?
BS: These days technological advances allow us to do things in a way we never thought possible – think, for example, of how we build planes today.
IT has been present in construction for a long time, even though we haven’t fully understood the potential of tools like Building Information Modeling yet. In my opinion, what differentiates it is how it helps us to better understand the structure and function of a building, in a life-like environment. It tells us how a place ‘feels’ as opposed to just how it ‘looks,’ and it will give us better engineering, better planning, better procurement, and so on.
What we must avoid at all costs is making BIM “oppressive” (always the risk when machines and men interact, as Taylor and his factories’ soul deadening 20-second work cycles for employees taught us). For that, we need the enlightened understanding of work and relationships that lean gives us.
PL: Design for Manufacturing and other solutions based on pre-built parts shipped to a construction site seem to become more and more common - do you agree?
BS: I do. Pre-manufactured walls or sub-sections of buildings that can be transported to a site and assembled to an existing structure represent a quick and easy solution to many problems in the industry (possibility to correct errors early on and less stock on site being two of them). There are examples everywhere. The Chinese are building skyscrapers using this method.
But the bigger lesson here is that the increasing use of pre-built parts reflects the tendency of the construction industry to move towards more integrated supply chains in which relationships are longer and stable. Even though they don’t always work, so-called ‘framework agreements’ are becoming more common – this is how many construction companies survived the recession and are now thriving.
PL: Managing cities will be one of the world’s toughest challenges in the coming decades, and there is no doubt a smarter and more efficient construction sector delivering value-adding infrastructure could really help. Do you think lean construction can contribute to the development of a new ideal of city?
BS: Let me start with an example. Think for a minute about the value of the Victorian sewage system that London has been living on for the past 150 years. Quality infrastructure means high value use and low maintenance into the future.
Over the years, I have done a lot of work with train stations - to mention another example - many of which were poorly built. But I believe that we always have a choice to build something in a way that it will last. All we need to do is to understand the concepts of value and value retention. That’s what lean thinking is about, after all: long-term value and sustainability.
Cities are always under cost pressure. But if building a hospital or a school cost you 25% less (for example thanks to the creation of a standardized way of building) and the design is smart enough to allow for easy re-cladding or refurbishing in the future, city managers and local government bodies will have nothing to worry about. At the same time, more value will end up reaching the patient or the student.
Applying lean to construction will make our cities more beautiful and low-maintenance and will give our buildings greater functionality.
PL: The LCI-UK conference is taking place in Birmingham on October 30th – tell us about it please.
BS: Our main purpose is to host a lean networking event. There will be, however, a specific focus this year – the UK government’s 2025 program, a 10-year strategy to improve the construction industry.
Our aim with the conference (among the organizations presenting we have the Highways Agency, London Underground, and Skanska) is to bring together government and industry to come up with a set of recommendations on how to deploy the 2025 strategy. Personally, I believe that the only way to do it is through lean, and we are hoping to give a good contribution to the debate.
More information can be found here.
THE INTERVIEWEE
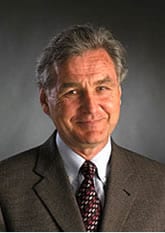
Read more
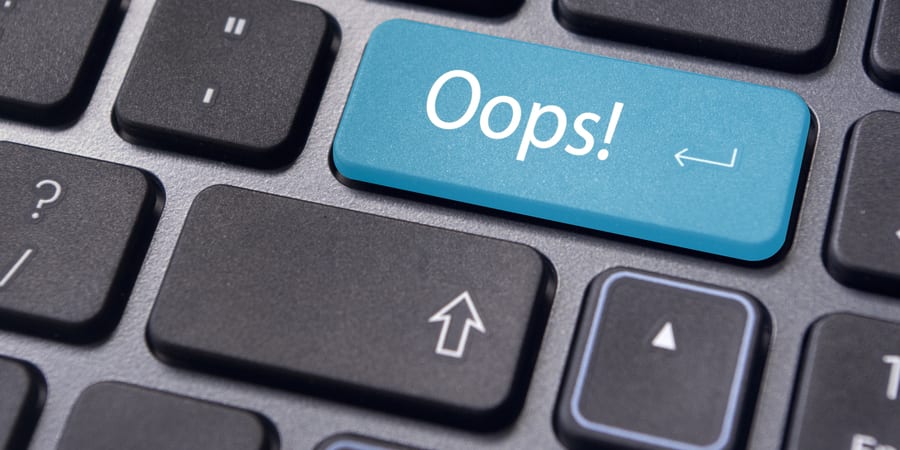
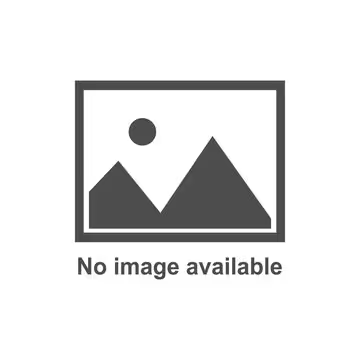
FEATURE - Traditionally seen as the mother of all evil, the IT department in our organizations has a long way to go before it fulfils its potential and becomes an actual facilitator in the delivery of excellent products and services. In the past few years, IT leaders have realized that lean management can help them to transform the function.
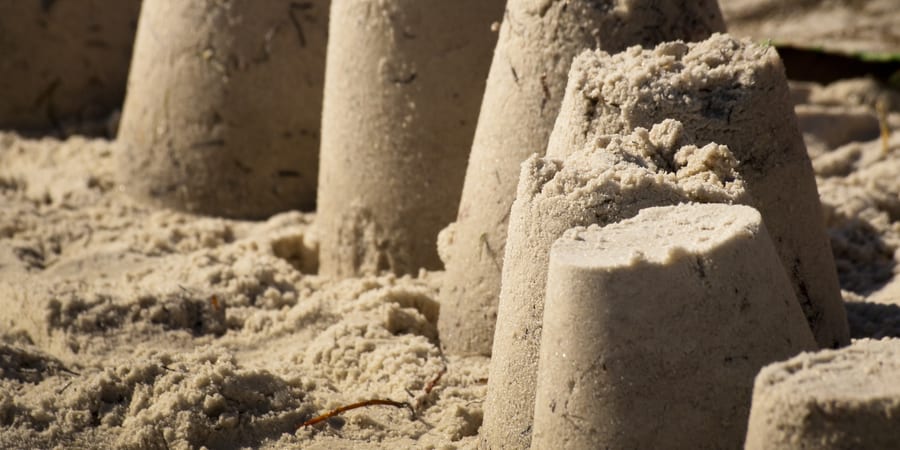
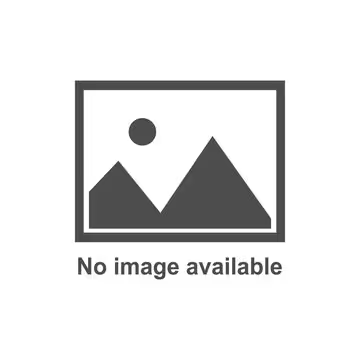
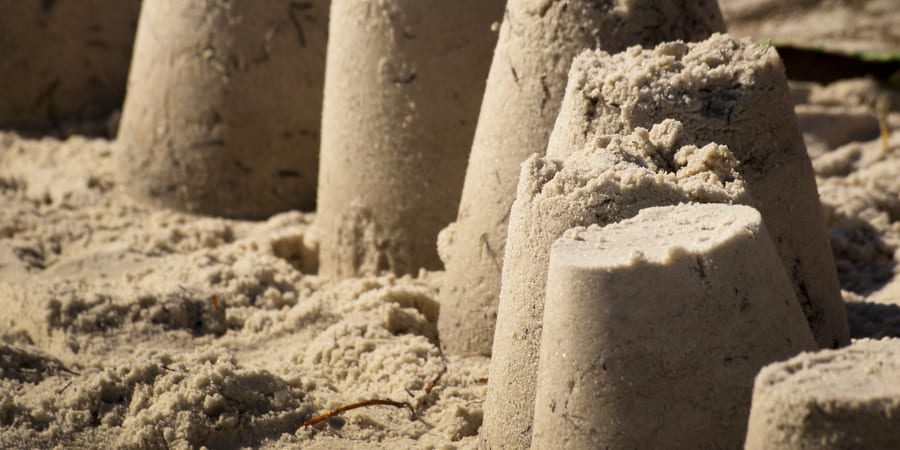
INTERVIEW – Does your company feel like a sand castle? Do you struggle to sustain lean results? At the recent Lean Transformation Summit, the CEO of Lantech told us how the firm is using daily management to prevent “deterioration”.
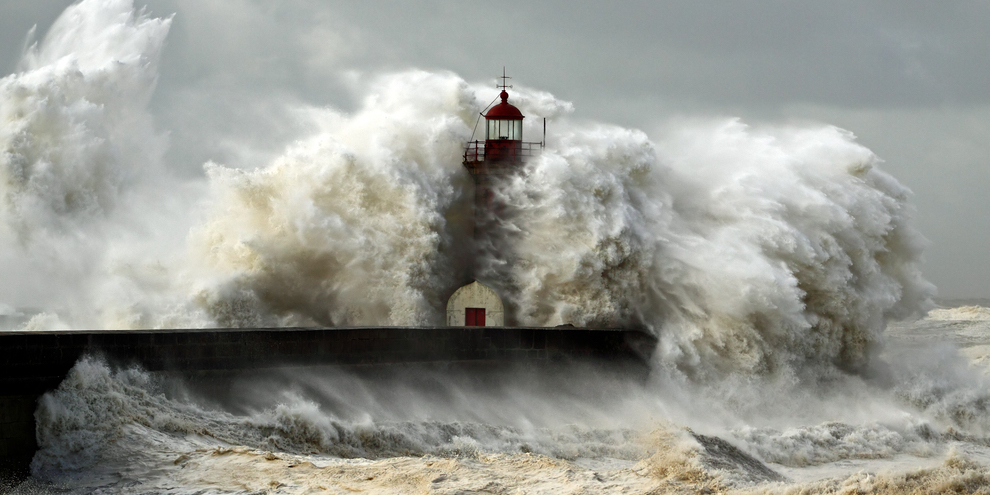
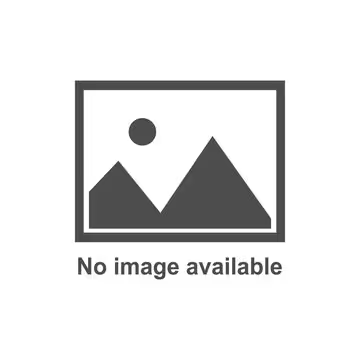
CALL TO ARMS – The current economic situation is presenting great challenges to organizations around the world, but in difficult times lean gives its best. Provided we all do our part, with conviction and determination.
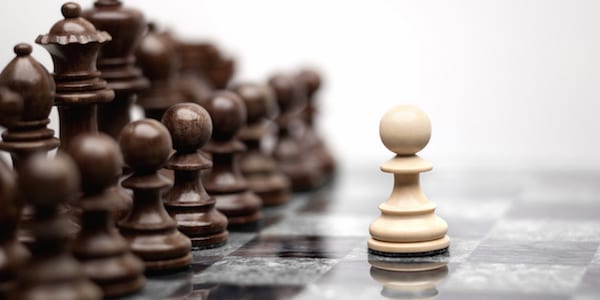
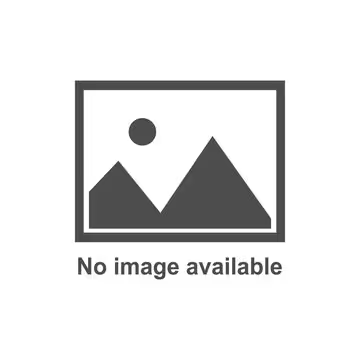
INTERVIEW – During a chat with Planet Lean, Darril Wilburn explains why courage and humility are necessary elements to establish a culture based on continuous improvement.