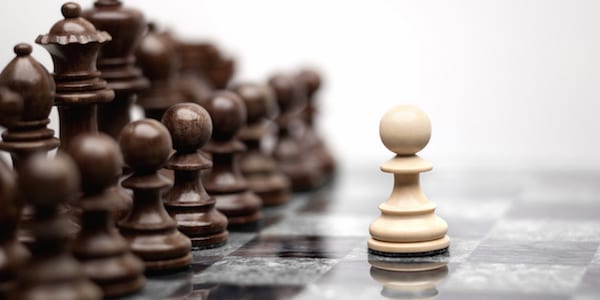
What it takes to embrace kaizen and establish a lean culture
INTERVIEW – During a chat with Planet Lean, Darril Wilburn explains why courage and humility are necessary elements to establish a culture based on continuous improvement.
Interviewee: Darril Wilburn, Lean Business Development, Honsha Associates
Planet Lean: Does improvement get harder the better we get, much like it does when we are learning a language?
Darril Wilburn: I think that is a good analogy. At the basic level, lean is simple. But if we want to create a lean culture, we must have the discipline to keep trying and even failing many times. This is where it gets difficult and where many organizations and leaders decide it is not worth it, it is too hard.
Sometimes the long-term vision can seem impossible, but if we break it down into doable pieces and the team can have short-term success then we can, step by step, over time, get closer to the vision.
That’s the power of kaizen - small incremental improvements have enormous benefits over time and we can all carry them out every day.
PL: What is your approach to teaching lean?
DW: First we must understand that the only way to learn to be lean is by doing, not just reading or talking. Having said that, I like to first work with leadership teams to help them understand the deeper lean principles of continuous improvement and respect for people. These are not just lean principles; they are principles that all organizations should be aligned with so they can develop a company that can endure for many years. If the leadership team can be honest with themselves and assess how aligned they are with these principles (as well as the “sub-principles” of courage, humility and kaizen), it can help us develop a road map for the next steps in the lean journey.
PL: Lean principles are often perceived as common sense, but so many organizations struggle to grasp them. What is it that is so elusive about them?
DW: Mark Twain’s quote comes to mind: “If common sense is so common, why is there so little of it?”
One of the big problems companies have is that they approach common sense with courage but no humility. Lean often looks so easy that they think they are already doing it, but they are not (or they are, but at a very superficial level). The key differentiator between Toyota and other organizations is the discipline to stay the course and continue to improve over time. If we ever think we are a great success and are untouchable that is the first step in our decline. If we are already great why would we need to improve?
PL: Courage and humility – how can one strike the right balance between these two?
DW: For a lot of people it is difficult. The only way to get better at it is do it and reflect on it – the essence of PDCA. We look at how we got to a decision and what process we used to get there, and reflect on how to improve our thinking, our process and our behaviors. It is a never-ending cycle.
It is also important to look at the balance between process and results. If we get results without knowing the process used to get the result, then we are lucky and some will call us courageous but maybe we just guessed correctly. If we get a result that is less than ideal but we know how we got it, we can learn, improve it and sustain it and some will call us cautious and slow. We have to decide what is most important, learning or being lucky. Learning is inextricably linked to humility; one cannot happen without the other.
PL: What trends are you able to identify in the lean community through your work with organizations?
DW: People are starting to realize that, while lean can help them to drive short-term results, the only way to sustain those results is affecting their culture and high-level processes.
For example, I am helping a government organization in the U.S. that has been working primarily on a tools basis for a few years. They then started to realize that the competencies they hire for now are different from the ones they will hire for in 10 years. They now understand they need to start building those capabilities into the people they already have, while changing the onboarding process to ensure they hire the right competencies for the future. This is a completely different way of thinking for them, the only one that can result in a changed culture.
More and more companies are also asking for what we call FMDS, Floor Management Development System. One of my favorite questions to ask floor managers is, “Are we ahead or behind right now?” If it takes several minutes to determine the correct answer, then our management system is not helping us. When we go to the gemba, whatever that is for your organization, it should teach us about the health of the system. If we have to dig too much for information, then it is failing.
PL: In a recent presentation, you called kanban an “admission of failure” – what did you mean by that?
DW: This is an extreme example, of course, and used as a teaching tool. The point is to understand the purpose of any tool we use. What is the purpose of kanban? When I ask this question the answers I get are often results of kanban; “It helps me control work in process” is a common answer. But that’s not the purpose, it is one of the results of using kanban. So what is its purpose? The purpose is to connect disconnected processes. If we know this purpose, then we always keep in mind the ideal state (that being all processes are connected physically). This perfect state of physically connected processes is not attainable in most of our companies in the near future, but we continue to pursue it step by step. So if we now have 100 kanban in the system we ask how we can make it 99, 98, 97, and so on until we eliminate it. As the Lexus marketing slogan states, it’s “the endless pursuit of perfection.”
PL: Can you explain to me the connection between courage and people development?
DW: To see potential in people and act on the potential we see is very courageous. Why is this? Because the behavior we see currently may contradict our vision of what this person can become and the easy thing to do is give up and move on to the next person. The courageous thing to do is to continue to coach and develop.
The analogy I use often is the parent/child relationship. This is not to suggest that the people we work with are children, but to make an easy-to-understand example of seeing potential in others and taking the responsibility to help them realize that potential. When a child is born, their behavior is not consistent with the potential you see in them. The newborn child only cries, eats, and eliminates waste (not the lean kind of waste). Despite this behavior we treat the child with love and respect and our behaviors towards them are based on our vision of who they can be, not just what we see currently. It is very courageous to act on vision and not just react to the current situation.
THE INTERVIEWEE
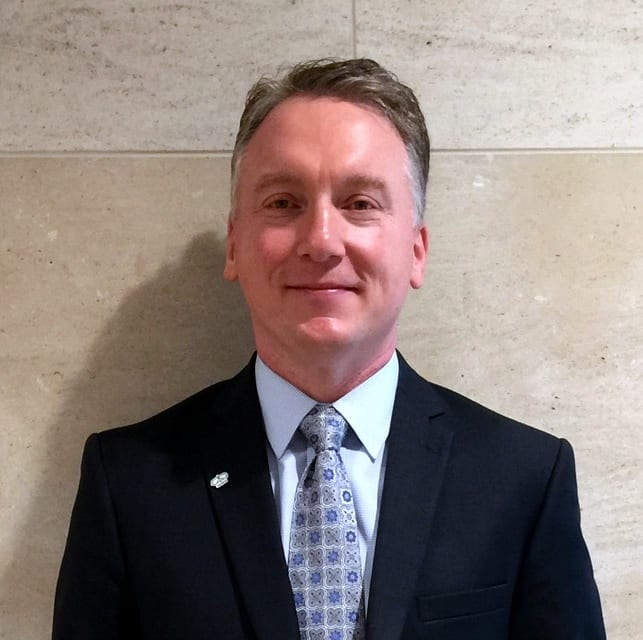
Read more
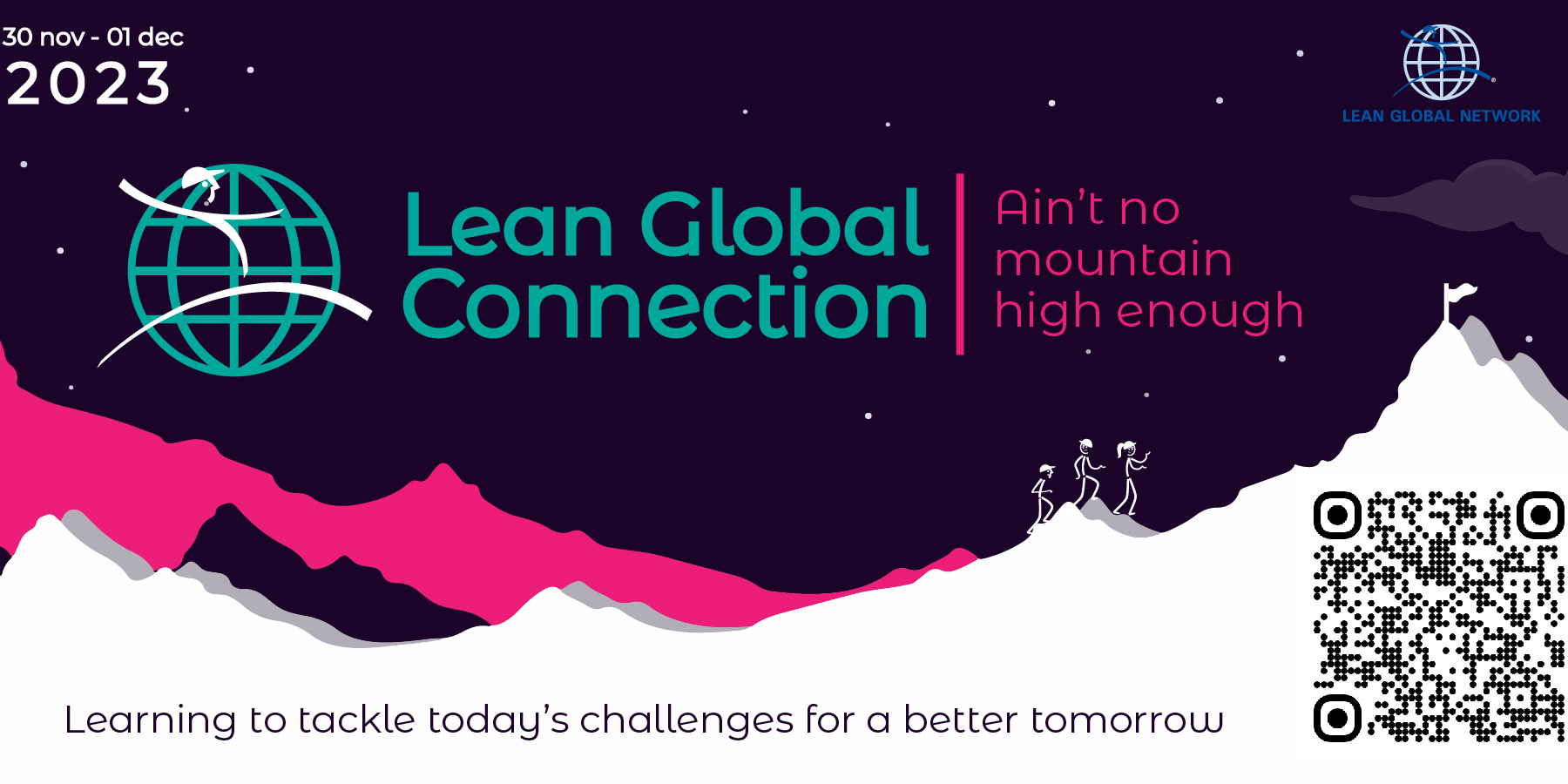
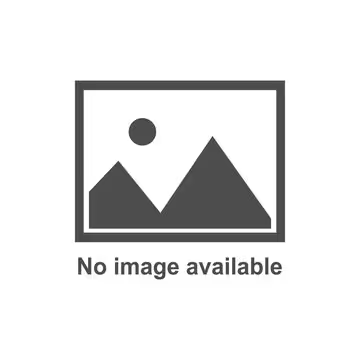
EVENT - The Lean Global Connection is around the corner! Our editor takes you through some of the key highlights you can expect and reminds us of the idea behind the largest online lean event in the world.
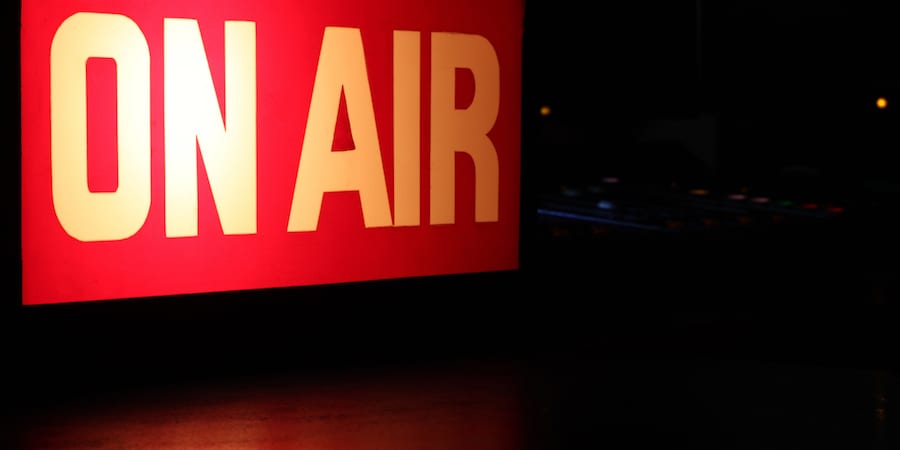
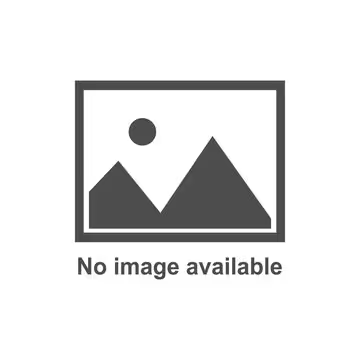
CASE STUDY – The Finnish Broadcasting Company has been leveraging lean thinking to scale up its agile work. In the process, it has developed a greater understanding of customer value.
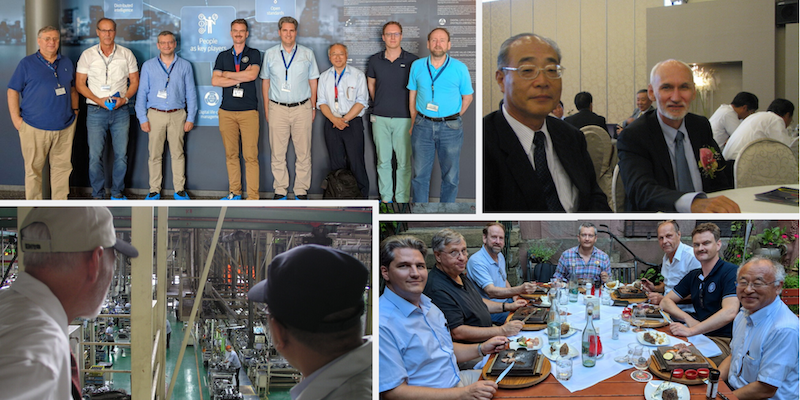
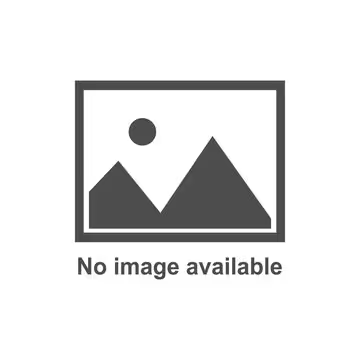
FEATURE – 2019 was another momentous year for the Lean Community. John Shook reflects on what we lost and what we gained in the last year of the decade.
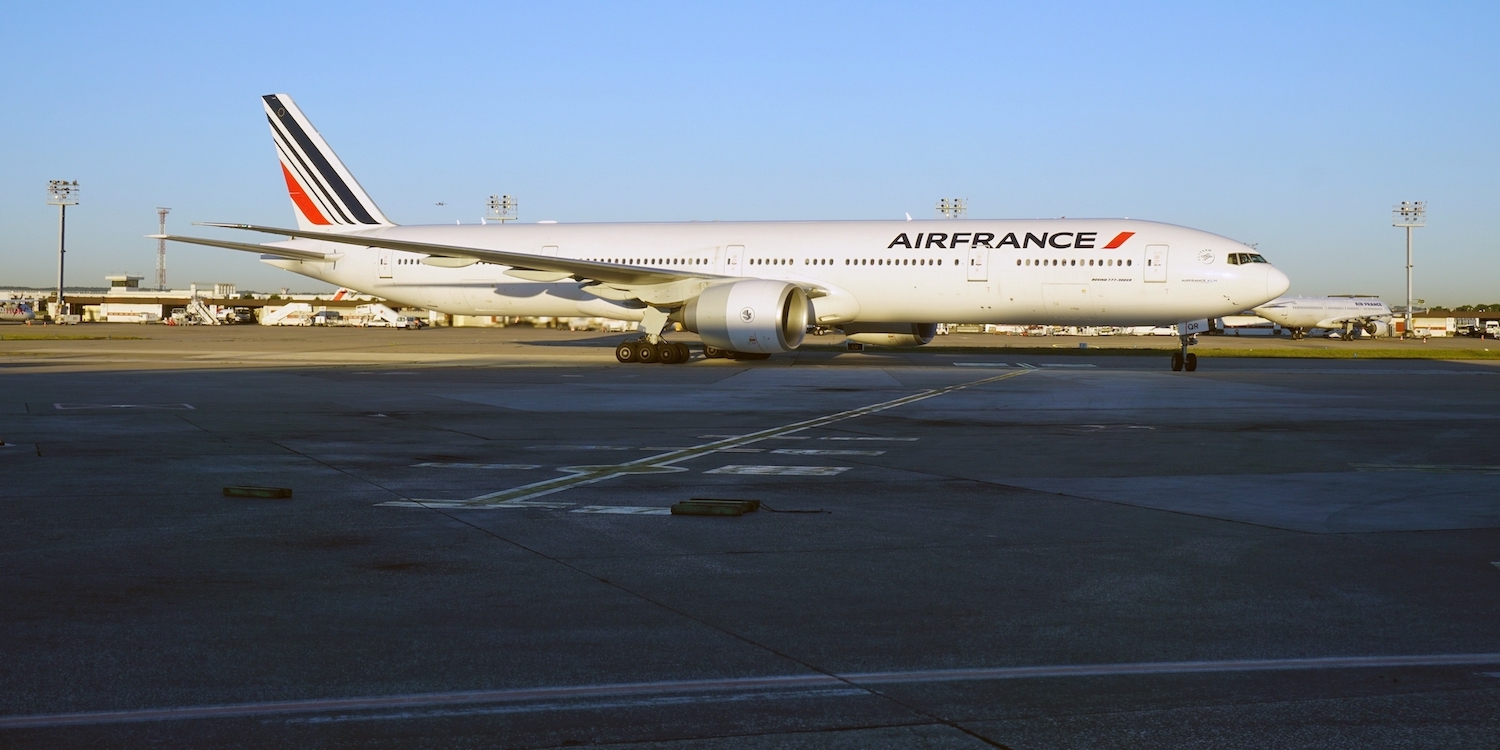
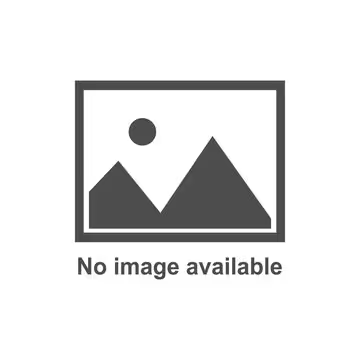
NOTES FROM THE GEMBA – The author visits the Parisian airport of Orly to learn about a pilot project (pun intended) that aims to tackle the late departure of flights using lean thinking.