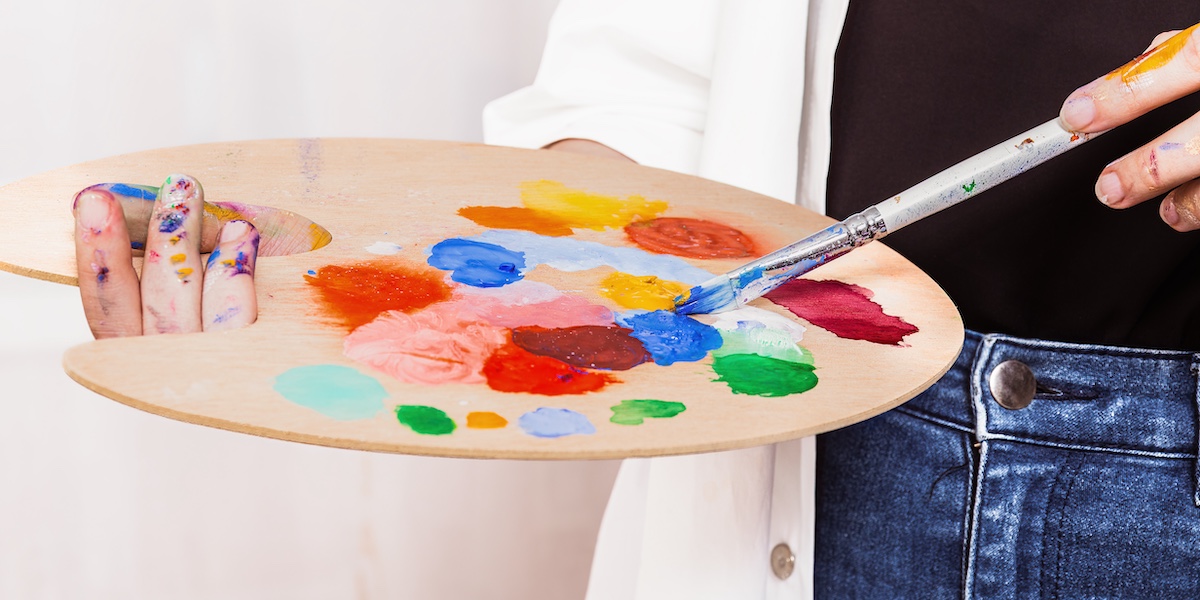
Painting change with Lean Thinking and Practice
FEATURE – Embracing lean is like painting: tools are colors, respect for people is the brush, and true change blends both with intention.
Words: Teuku Mirwan
One of the biggest lessons Lean teaches us is that problems are not obstacles, but opportunities for growth. Every inefficiency or breakdown is a chance to refine processes, elevate quality, and nurture a culture of continuous improvement. Yet, many organizations struggle to view their inefficient workflows, siloed communication, and resistance to change as canvases on which they can paint their organization anew. What’s needed are problem solvers who can recognize potential in every challenge – and who use Lean Thinking & Practices to transform those challenges into sustainable solutions.
THE PROBLEM SOLVER AS A PAINTER
Bear with me, as I delve deeper into the canvas analogy. I believe a lean practitioner can be likened to a painter – someone who crafts solutions with intentional technique, precision, and creativity. And just as a painter relies on essential tools to produce their art, problem solvers need the right elements to drive meaningful, lasting change.
A painter uses three fundamental tools:
- A color palette with a spectrum of shades and tones to bring depth and emotion to the artwork.
- A brush to bring the vision to life through thoughtful application.
- A canvas upon which the art takes form.
What if we were to look at these elements from a lean perspective?
Well, the color palette could symbolize the lean tools – PDCA, Kaizen, Value Stream Mapping, and other methodologies that shape thoughtful, effective solutions.
The brush could represent respect for people, a core lean principle for fostering collaboration, engagement, and empowerment throughout the problem-solving process.
And what would the canvas be if not the gemba, the place where the work happens, problems arise, and true solutions must be found?
THE ART OF APPLYING THE BRUSH
To make a beautiful painting we need more than just nice colors. We need to know how to use the brush to apply them. Similarly, we can’t expect to bring lean tools and techniques to an organization without showing respect to our people. Without a brush, even the most vibrant colors are useless. And without respect for people, even the most advanced lean tools lose their power.
Indeed, the success of a transformation hinges on our ability to bring together the technical and the social sides of Lean. True and lasting change is driven by people, not process improvement alone. Tools only gain their strength when applied with empathy, open communication, and active collaboration.
Jackson Pollock once said: “Painting is self-discovery. Every good artist paints what he is.” Like painting, a lean transformation reflects the mindset of the practitioner. It’s not just about applying tools – it’s about showing up for our people, whether peers or those we lead. This is, indeed, a trap those who are new to Lean often fall into: they learn as many tools and methodologies as they can, but completely neglect the human side of change.
ADAPTING TO AN EXISTING CANVAS
No transformation begins with a blank canvas. Every workplace is already painted with existing systems, historical successes, past experiences, and lingering inefficiencies. A skilled problem solver must decide whether to completely repaint the canvas or refine and enhance what already exists.
When faced with inefficiencies, organizations typically have two choices:
- Erase the canvas entirely, starting over from scratch. This full-scale overhaul may seem like the most thorough option, but requires significant time, resources, and investment. Most organizations only choose this path when inefficiencies are deeply embedded and considered “beyond repair”.
- Improve the existing painting, focusing on enhancing what’s already there by deeply understanding customer needs, identifying value-added activities, eliminating waste, developing capabilities, building daily management routines, and cultivating a culture of continuous improvement. This is the heart of the Lean Transformation Framework – systematic, progressive improvements that create lasting impact.
The most effective problem solvers understand that meaningful transformation rarely requires a full reset. Rather, it calls for a deep understanding of what’s working, what isn’t, and where targeted changes can make the biggest difference.
THE MASTERPIECE OF LEAN TRANSFORMATION
Mastering Lean Thinking & Practice isn’t just about collecting tools – it’s about knowing how and when to apply them, with precision, adaptability, and a people-first mindset. Like a painter refining their technique to create a masterpiece, the skilled problem solver blends technical expertise with emotional intelligence to drive meaningful, lasting change.
Are you ready to become the artist of transformation in your organization? Will you pick up the brush, respect the canvas, and paint a future shaped by continuous improvement?
THE AUTHOR
.jpeg)
Read more
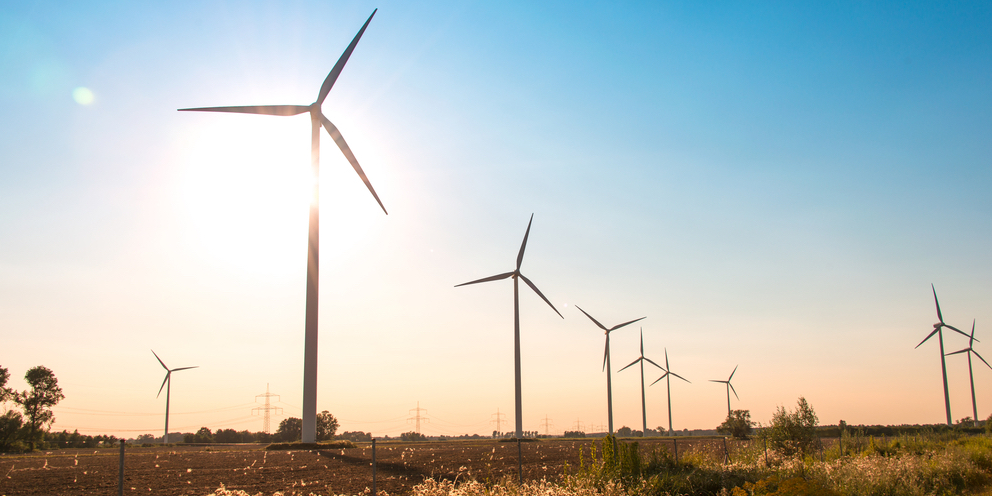
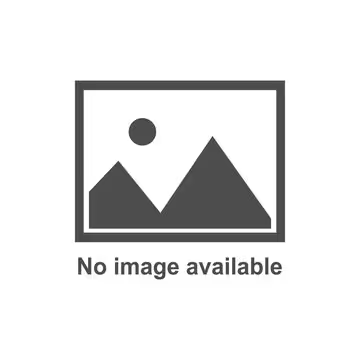
FEATURE – The planet is warming at an unsustainable rate, pollution is increasing, wildlife populations and arable land areas have plummeted, and our oceans are filling with plastic. Can Lean Thinking help?
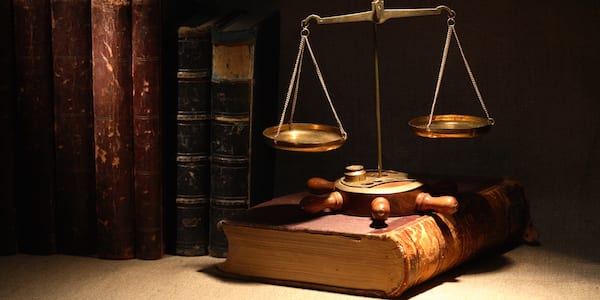
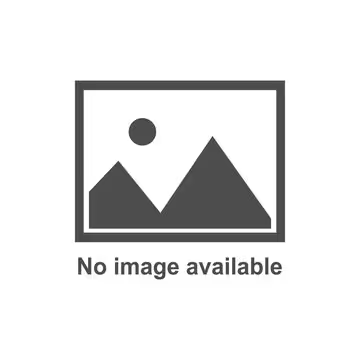
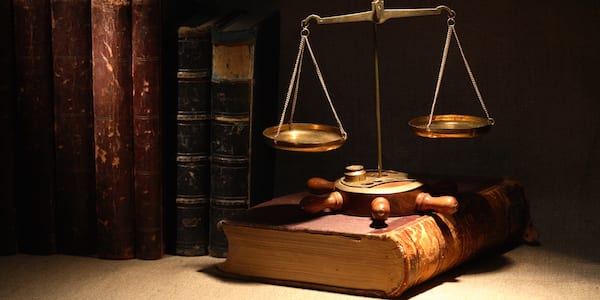
CASE STUDY - HM Courts & Tribunals Service has been using lean ways of working for over six years, learning many lessons along the way and achieving some fantastic wins.
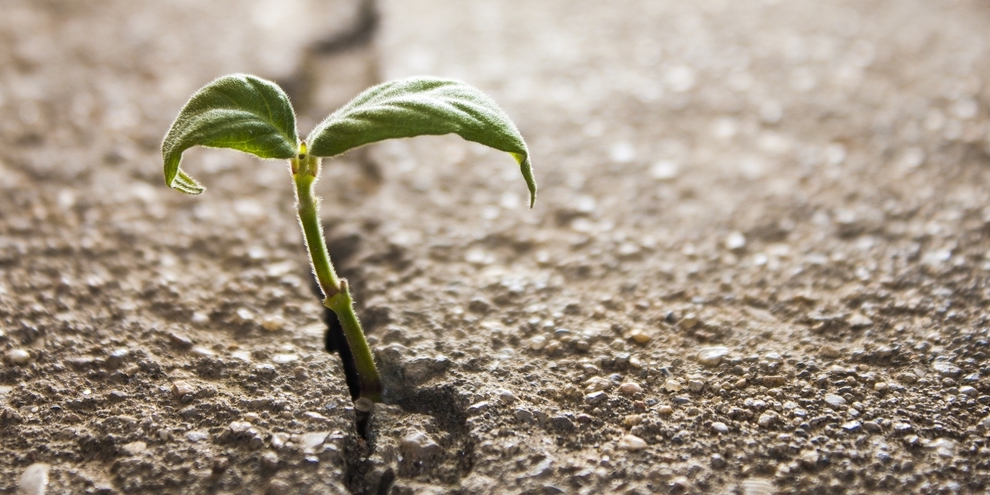
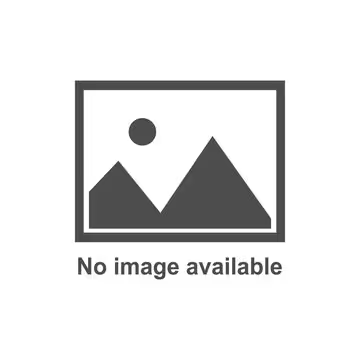
ROUNDUP – Our editor looks back at the best articles explaining how Lean Thinking can help in a crisis and bring an organization back from the brink of disaster.

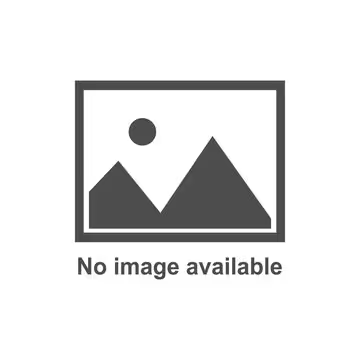
PROFILE – Persevering, letting people inspire you and committing to continuous learning. These are the things you need to do to successfully embrace lean thinking and, it turns out, learn to play the violin.
Read more
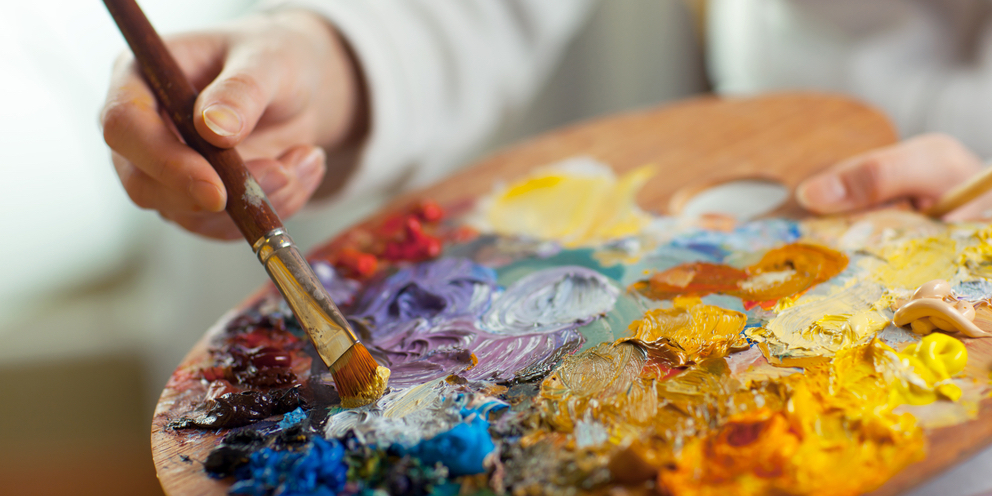
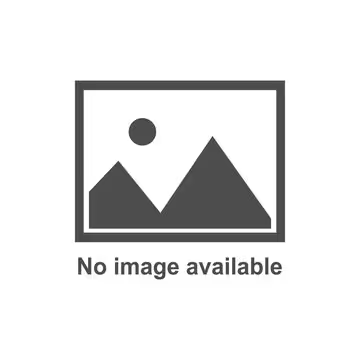
FEATURE – In this personal account, the author explains how Lean Thinking inspires her painting process, debunking the myth that the methodology stifles creativity.
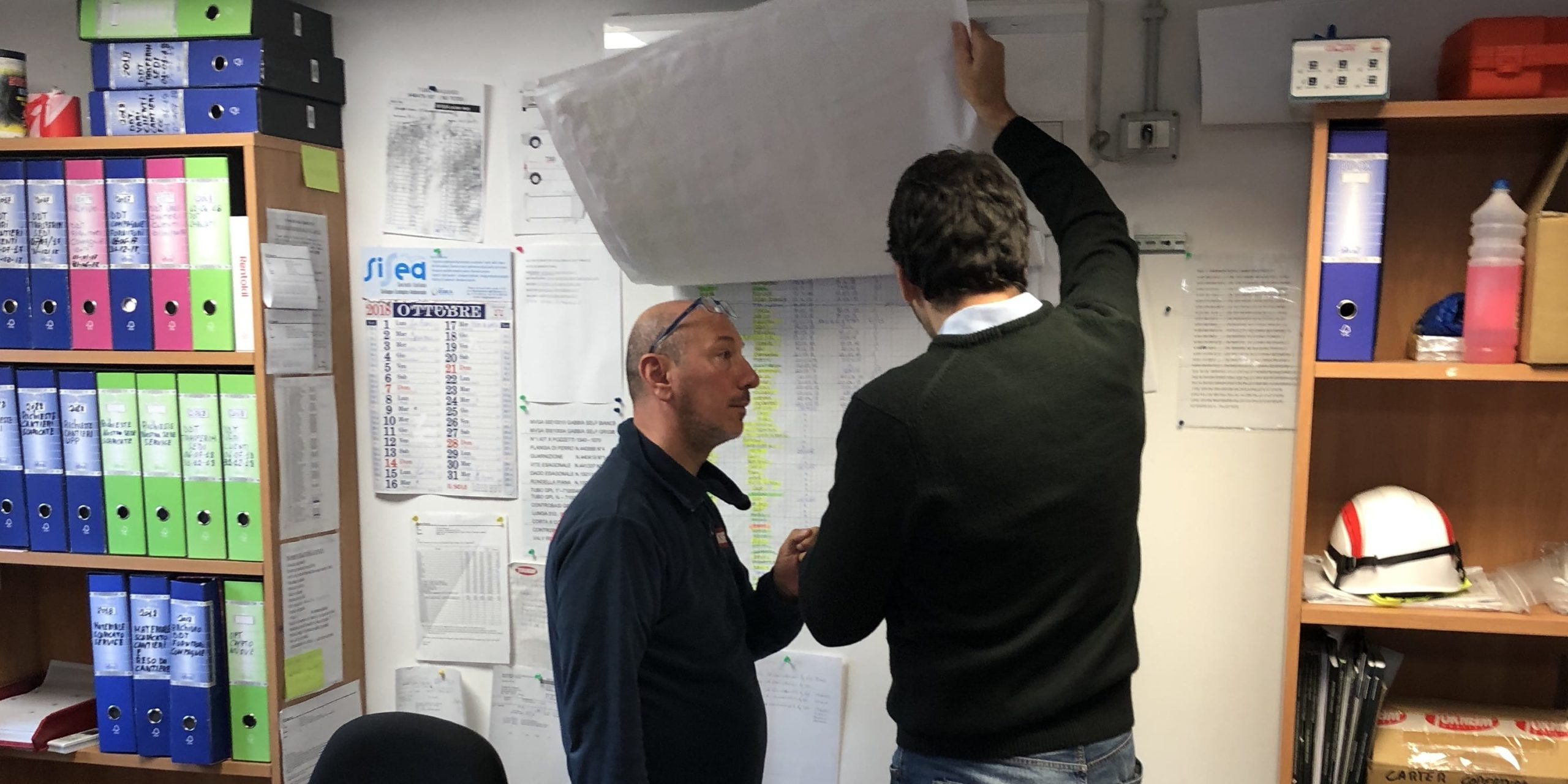
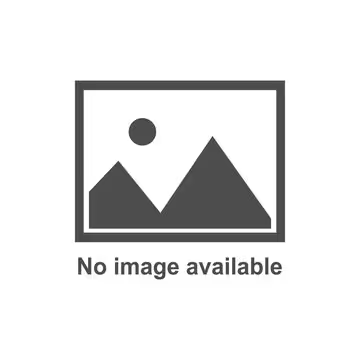
FEATURE – Innovation is a process and lean thinking allows that process to take place, by empowering everyone in the company to think creatively about solving customer problems.
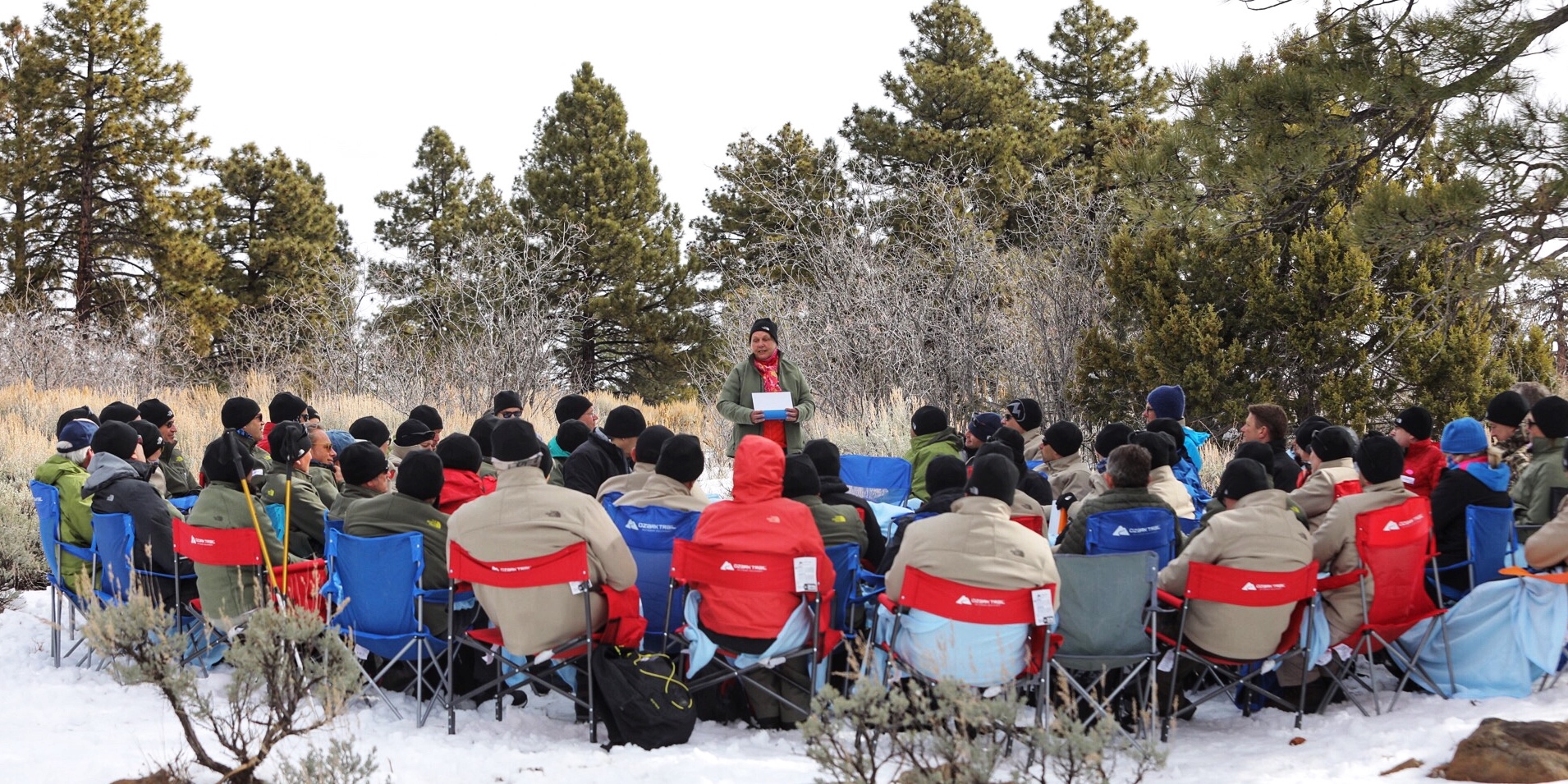
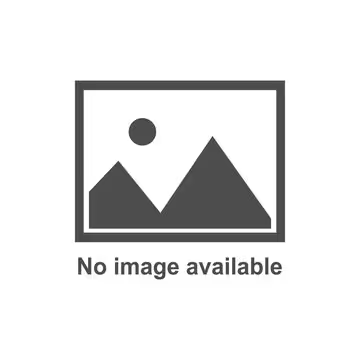
FEATURE – A few weeks ago, we learned how Philips is leading their lean transformation. In this follow-up article, the authors provide some great tips based on the company’s experience.
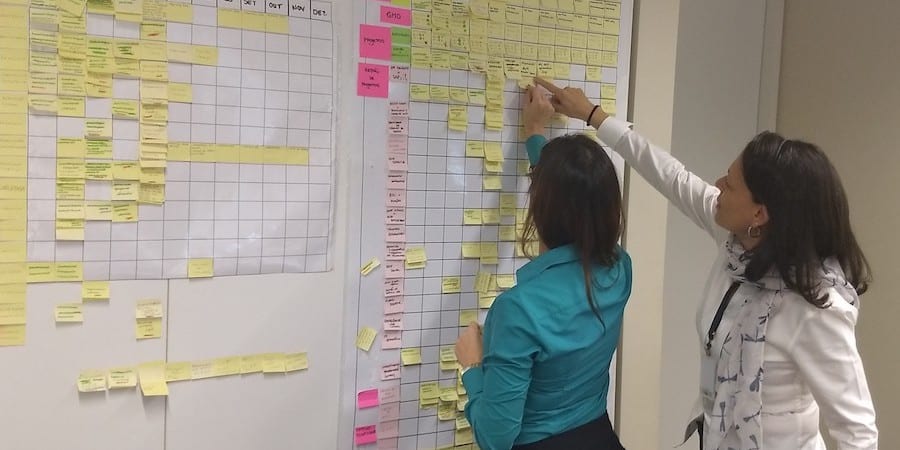
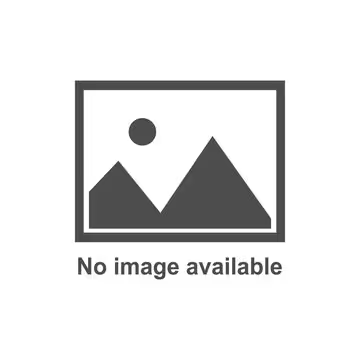
INTERVIEW – In this follow-up conversation with the Hospital Moinhos de Vento in Brazil, we learn about the elements that are helping them to make lean stick.