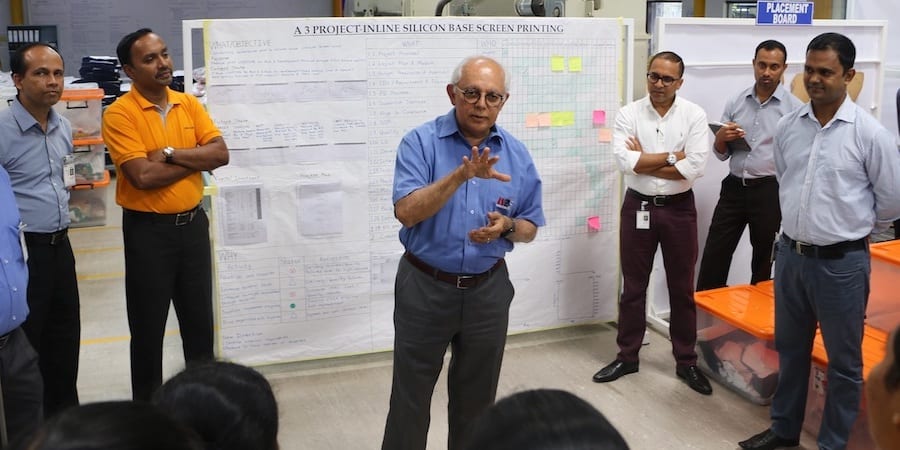
Supporting Sri Lankan society by transforming our company
INTERVIEW – Prior to his talk at this year’s Lean Transformation Summit, the CEO of a large apparel manufacturer tells us about the company’s lean journey, and its impact on Sri Lankan society.
Interviewee: Mahesh Amalean, Co-Founder and Chairman, MAS Holdings – Sri Lanka
Planet Lean: How did your lean journey begin?
Mahesh Amalean: Since our inception in 1987, we have been growing our business 20 to 30% year on year. We were a strong and successful business and, as strong and successful businesses do, over time we started to get complacent. Productivity had plateaued and waste was creeping in. Competition was growing and I began to feel uneasy.
In 2002, I visited Japan as part of a delegation led by the Prime Minster of Sri Lanka. During the trip, I visited Nissan and Toyota, as well as a number of companies in the textile/fashion industry. By the end of my week in Japan, I had realized I should have gone there 10 years before! I immediately realized that there was a lot we could have learned from the Japanese manufacturing process.
Upon my return, I shared what I had seen with my colleagues at MAS. It took me around two years to find a good sensei, who could support our journey. In the end, we went back to Japan on a week-long tour in Nagoya, during which we visited Toyota and a number of its suppliers and were taught the basic lean concepts and thinking. We weren’t sure this philosophy would apply to our industry until, on day four of the trip, we visited a plant where we saw rolls of fabric and the sewing of seat covers for the Toyota Crown and Corona. That’s when the penny dropped.
Back in Sri Lanka, we ended up selecting our best plant (which already had very high productivity) for a six-month pilot. I began to visit the facility myself every three to four weeks to understand the impact lean was having. There were some great improvements, and for the first time I realized that lean could really turn MAS around. Within a few months, that plant increased its productivity by nearly 30% and, over a period of two years, by 80%.
By bringing around these simple tools and ideas, creating an environment of learning, empowering our people, eliminating waste, and driving value added activities we were able to reduce costs and improve our throughput time. Lean revolutionized MAS, helping us to become much more competitive than before.
PL: How has your understanding of the lean methodology evolved over time, and how has your leadership style changed as a consequence?
MA: Over time, we understood that lean is more than a change in the process, but a fundamental transformation in our way of thinking and behaving – something that could change the culture of MAS. Once we got that, we took it out of the factory and brought it into HR, Finance, Legal, Logistics, and so on. We are striving to be a lean enterprise.
Along the way, my leadership style changed dramatically, too. For one thing, I became a lot more reflective when faced with a problem. I started to think through issues, trying to get to their root causes. Prior to that, I’d typically look at who was responsible, so that was a very big shift for me.
I also learned the importance of creating the right environment, one in which problems are a good thing and people are comfortable bringing them up. Today I want MAS to be a place where people are given the knowledge and tools they need to solve problems, so that in time they can become autonomous.
PL: Part of a lean transformation is also becoming a better corporate citizen and looking at the impact the organization has not only on its people and customers, but also on society as a whole. What’s the impact that MAS has had on Sri Lankan society?
MA: We gained traction with lean sometime around 2009, and in the past six years alone we have doubled the size of our business. So, what we do has a direct financial impact on the country’s GDP and economy. We employ almost 75,000 people – more than 3,000 of whom work in our two facilities in the north of the country, left in a dire state by the 30-year civil war Sri Lanka endured. In a way, we are also contributing to reconciliation efforts following the conflict.
There is more. Most of the people working with us are women, and we constantly look at ways in which we can empower them to not only improve the work they do for MAS, but also the communities in which they live. We help them to develop skills other than sewing, for instance, or teach them how to better manage money. We really strive to provide value to the people working with us.
Another thing we are keen on is ensuring that as an organization we conform to international environmental standards. Working in the fashion industry means we use a lot of power, chemicals and water. To counteract this, we strive to use the materials with the least environmental impact and we try to rely on renewable energy as much as we can.
Finally, we encourage our employees to take on a sport they like (they are currently practicing 15 different sports), because we believe that this boosts teamwork, a spirit of competition, and a sense of identity.
There is more to us than producing for Nike or Victoria’s Secret and making money doing it – it’s the impact that we have on communities and society that really defines who we are.
PL: What are the most important lessons you have learned over the course of this journey?
MA: As I reflect on what lean has meant to MAS, I realize that there is no limit to what an organization can achieve, so long as it really embraces the lean philosophy and believes in it. Lean has the power to improve processes, enable continuous improvement, revolutionize a business, transform the way people think and improve their lives.
I have also learned that it’s important that the transformation is led from the top. After I saw the value and the potential of lean for myself, I saw an opportunity to transform MAS. I committed to it and took the time to show it to our people, accompanying them on factory visits, even taking them to Japan, so that they, too, could develop an appreciation for what lean could accomplish. So, once again, I have to stress on how fundamentally important leadership commitment is when embarking on the lean journey.
THE INTERVIEWEE
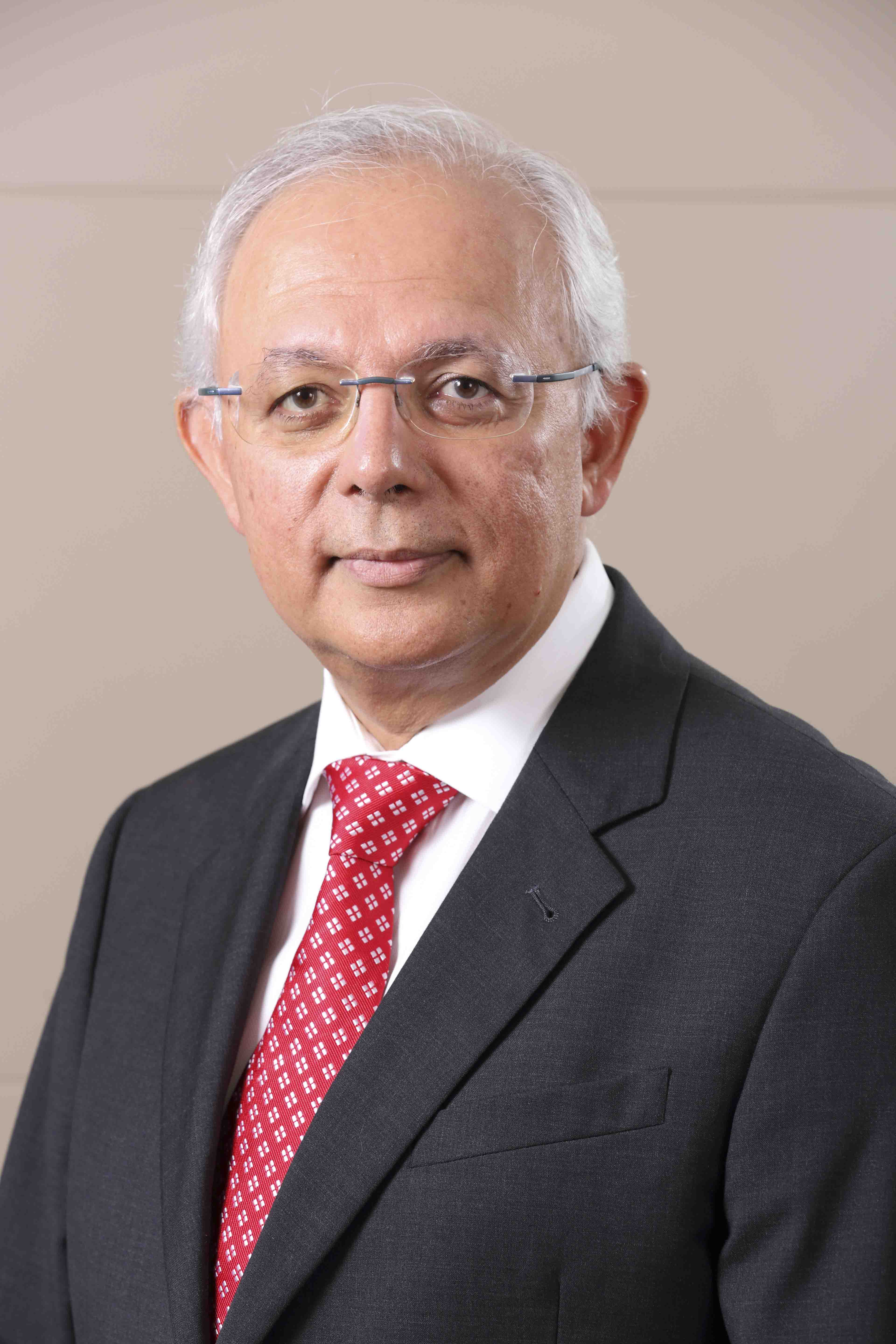
Mahesh Amalean is Co-Founder and Chairman of MAS Holdings. He believes in "doing good while you are doing well": in 2013, he was one of five global business leaders who received the United Nations inaugural Women's Empowerment Principles, Leadership Award for the company’s Women Go Beyond program. In recognition of his national service, in 2005, the president of Sri Lanka gave Mahesh the title Deshamanya or Pride of the Nation, the second highest national civil honor.
Read more
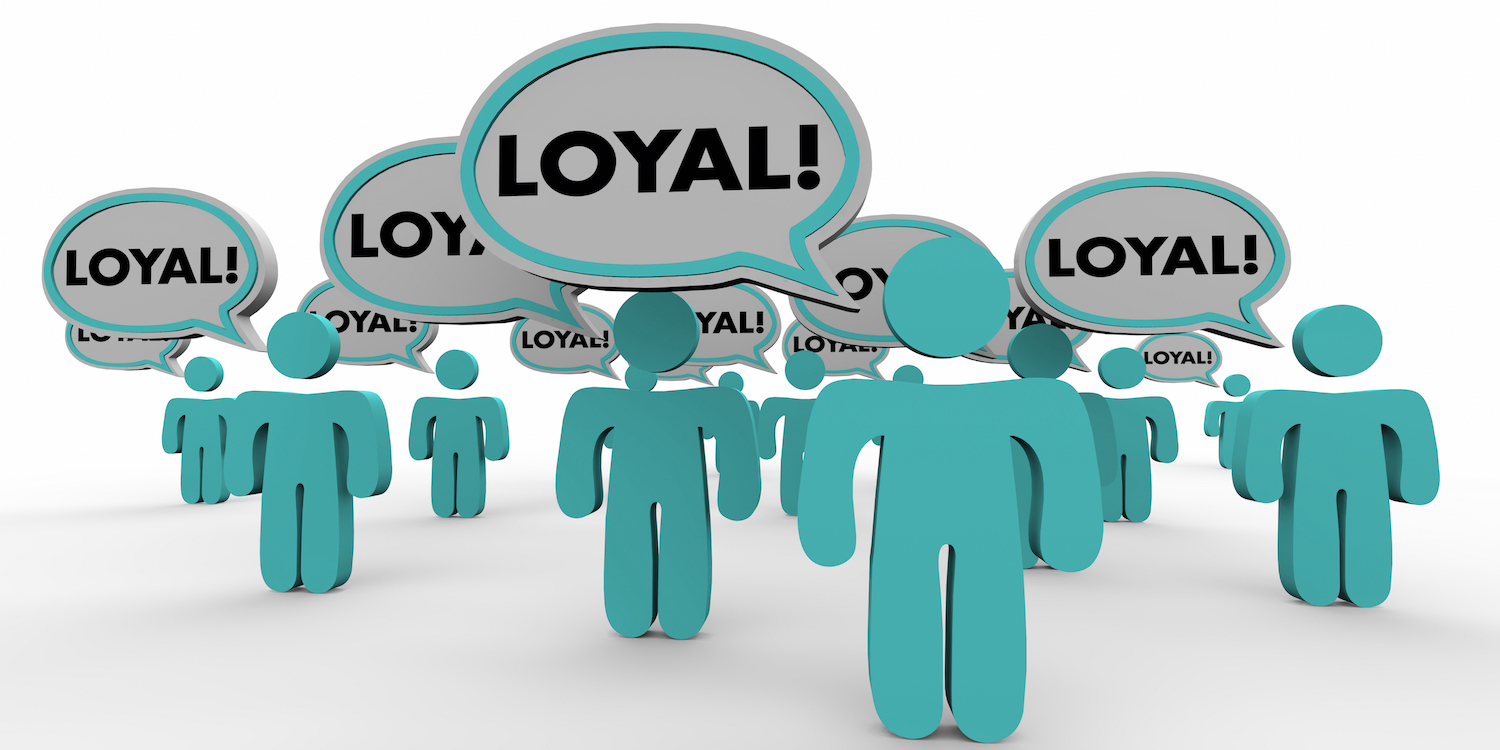
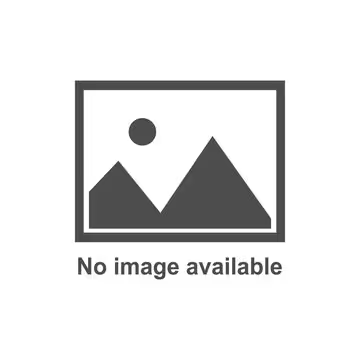
FEATURE – We start the new year with a reminder to put customers first, always. It is they who make our business and keep our lean initiatives true, says the author.
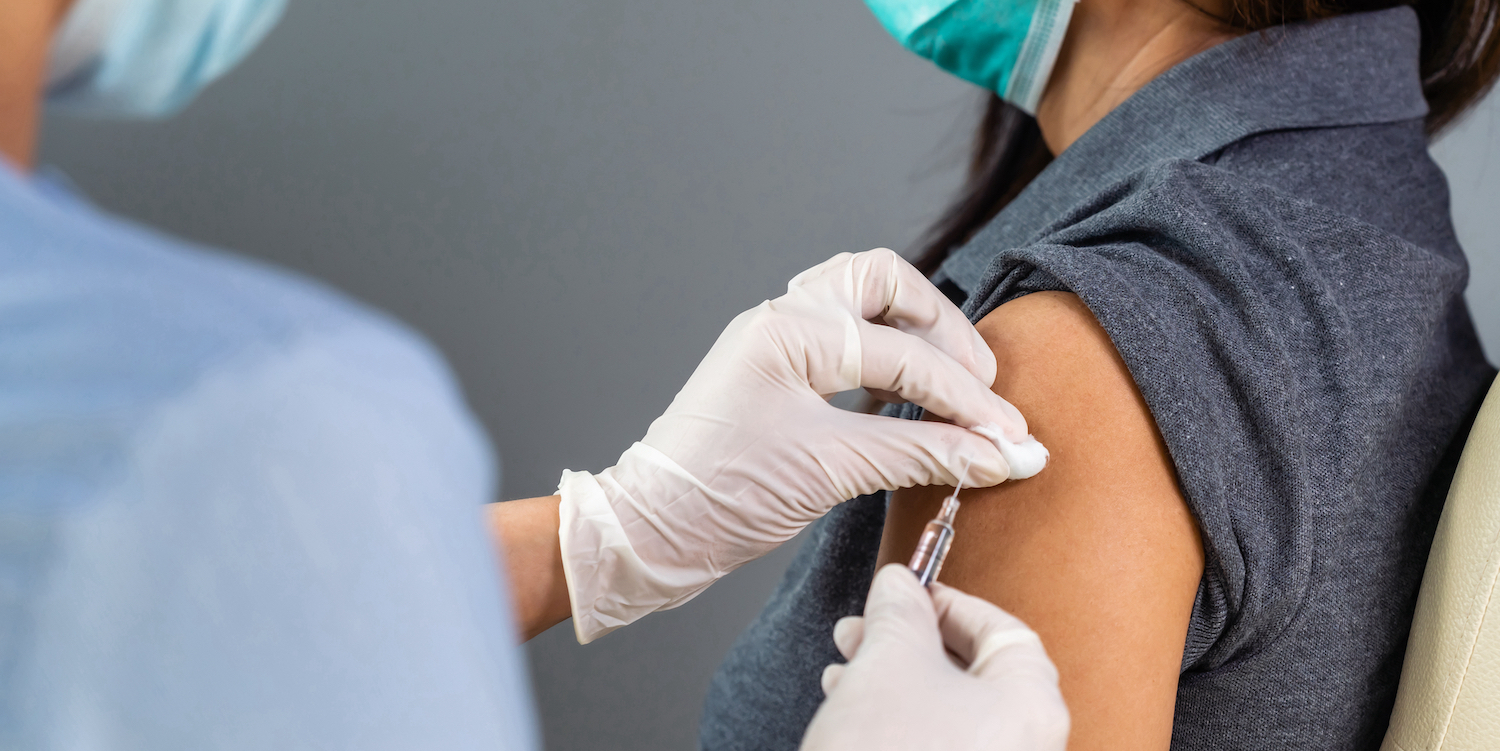
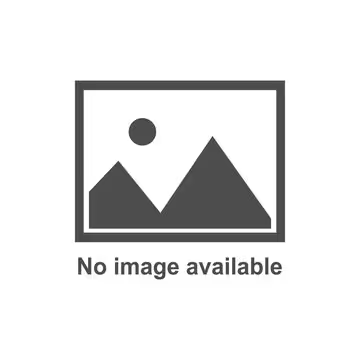
FEATURE – As Italy rolls out its vaccination campaign, the author reflects on what he recently observed at a vaccination hub in the Veneto region and discusses how the process could be made leaner.
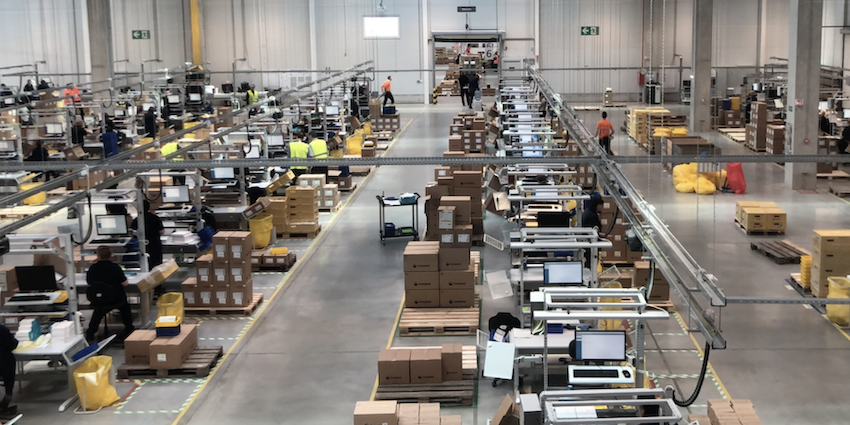
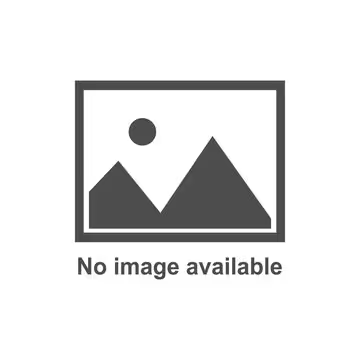
VIDEO - In February, a group of Lean Global Network coaches visited Coloplast's Parts Distribution Center in Hungary to help the local team improve the internal lead-time across the facility.
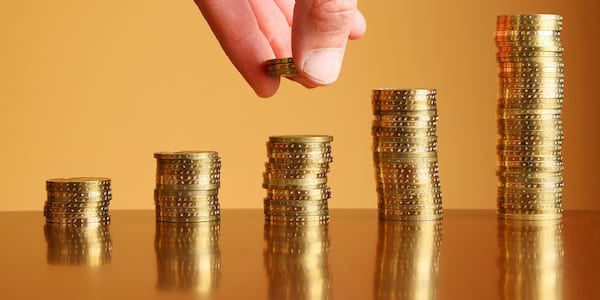
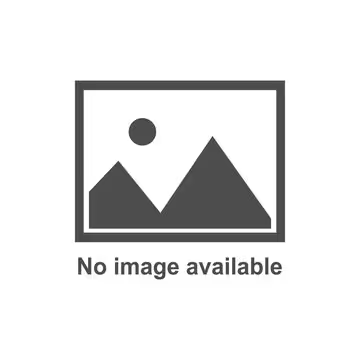
INTERVIEW – How many times have you been asked, “What is the ROI of lean?” Jean Cunningham provides her insight to help you measure the financial impact of your lean improvements.