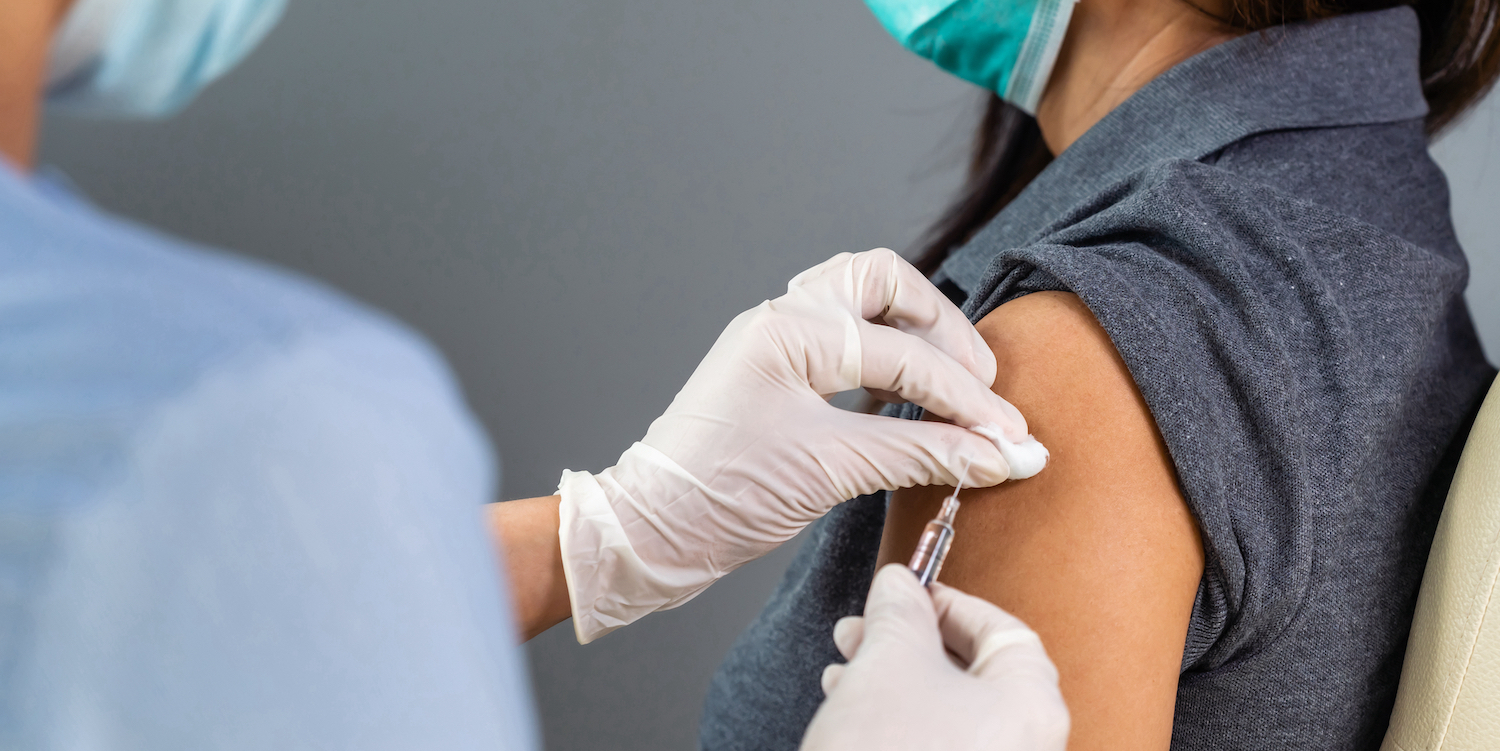
Every second counts
FEATURE – As Italy rolls out its vaccination campaign, the author reflects on what he recently observed at a vaccination hub in the Veneto region and discusses how the process could be made leaner.
Words: Roberto Ronzani, CEO, Istituto Lean Management – Italy
Countries around the world are facing the unprecedented challenge of having to vaccinate their adult population in as quick a time as possible, to protect them from Covid-19 and reopen economies.
Here in Italy, we need to vaccinate around 50 million people (nearly 100 million injections). This titanic effort needs to guarantee complete safety and an excellent “customer experience” to every single person, while limiting the time necessary to administer the jabs and using as few resources as possible to avoid any further impact on the healthcare system’s regular activities.
In other words, we need a brilliant process in place, one that is effective, efficient, and flexible. There is a lot that Lean Thinking can do to contribute to a speedy and safe vaccination campaign, supporting healthcare staff in their daily work. So, when the President of Veneto, Luca Zaia, expressed the need to provide organizational support to the region’s healthcare system, we at Istituto Lean Management made ourselves available.
Our initial observation and supporting activities at two large-scale vaccination hubs – the Palaexpò in Venice and the exhibition center in Vicenza – revealed several potential improvements that, once completed, could make an already strong process safer and significantly more efficient.
In true lean style, we began with the observation of the user experience from the moment they arrive to the vaccination hub to the moment they leave with the vaccine in their arm.
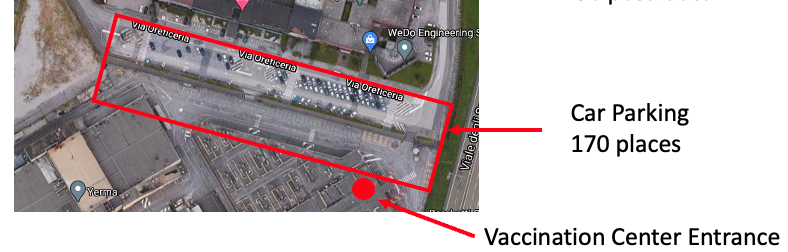
The process steps are the following:
- Arrival, parking and entering the vaccination center;
- Verification of the booking;
- Analysis of the user’s medical history;
- Injection;
- Observation;
- Vaccination certificate issuence and booking of the second dose;
- Preparation of the syringes with the vaccine (an activity that takes place separately from the actual inoculation).
This is traditional multi-step process meant to ensure “mass production”, with some variation – type of vaccine, characteristics of the user (frail, elderly, adult, etc), first or second dose, etc – that implies there are differences in process and times for certain steps.
While this means there are many possible combinations when it comes to carrying out the process, based also on the characteristics of the area being used, we found there are some common elements that, if tackled, could improve the overall process. Here they are:
1) Reducing variation in each stage of the process for the same category of user, vaccine type, and first or second dose, by defining clear working standards, providing the necessary training to ensure these can be followed, and implementing them. This leads to basic stability, which then allows us to move on the measurement of the time it takes for each stage in the process with the aim of balancing them out. The most critical (and the longest) phase is the medical history.
2) Limiting the time between a patient exiting the vaccinationroom and the following walking in. This can be achieved with a pull system, by asking the following user to wait for her turn just a few steps away from the point of use.
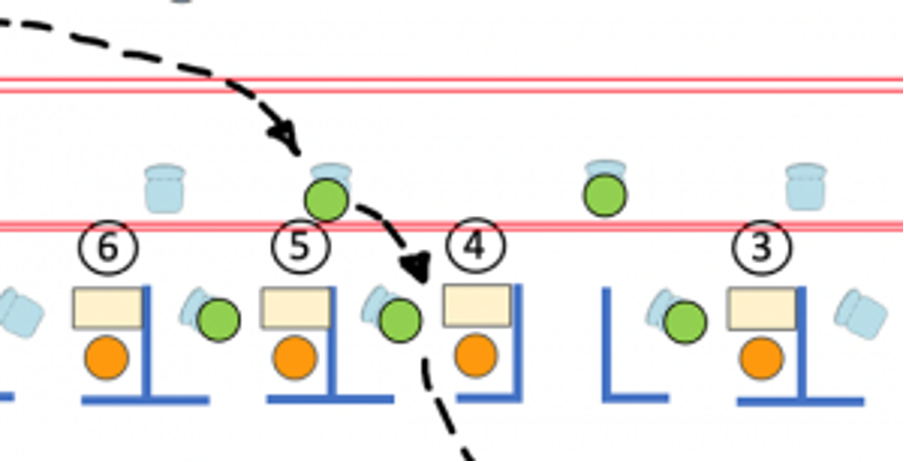
3) Reducing waiting for staff by simultaneously managing more than one user at a time, based on where in the process they find themselves: uncover their shoulder, injection or redressing.
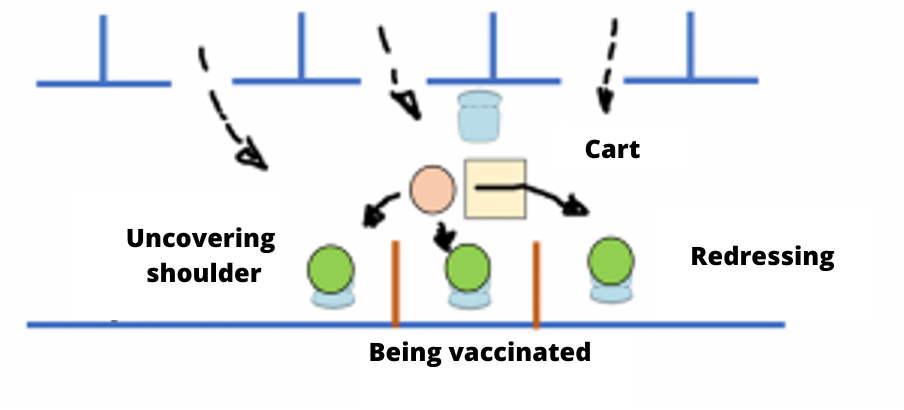
4) Separating the preparation area of thedifferent types of vaccine and positioning them (or integrating them, wherever possible) next to the vaccination area itself, to avoiding inoculating the wrong vaccine.
5) Using visual management to manage the user flow (and avoid lines between different steps in the process) as well as the vaccines (especially when they are put in syringes and places on the corresponding trays).
6) Optimizing the layout of tables where the vaccines are prepared. This is a very delicate operation that requires much concentration and an adequate organization of the space that makes it easy for staff to keep up with the pace, while making them less tired and reducing the risk of mistakes.
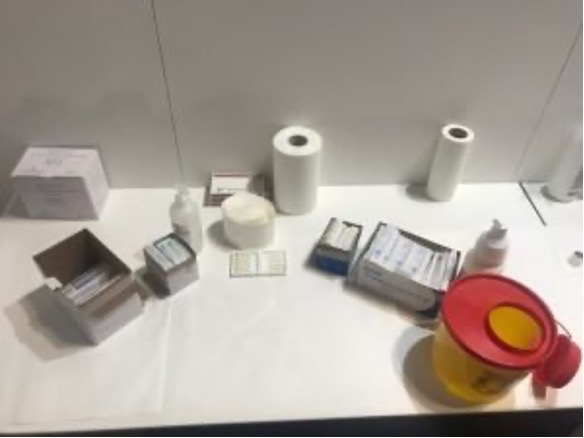
7) Ensuring the arrival of a user at the center is adequately signaled and that there are enough parking spots to welcome the number of users expected in a given time period.
We believe that addressing these elements of the work would lead to a marked increase in the number of users who can get vaccinated, without using more resources or digital tools. While a specific estimation of such increase is hard to make, we can still see how, imagining the medical history takes two minutes, certain situations can impact the system’s overall capacity.
For instance, reducing the amount of time it takes for a user to reach the vaccination chair – which currently stands at 30 seconds (longer for older people) – to 5 seconds would lead to a 17% capacity increase. Another element that can be improved is the “customization” of the vaccination process, which currently leads members of staff to occasionally take even 3 to 4 minutes to complete a vaccination. Following the standard mentioned in Point 1 above would lead to a 50% to 100% increase in capacity at each station.
Lean Thinking can help us to put Covid-19 behind us. So, let’s get vaccinated… the lean way!
THE AUTHOR
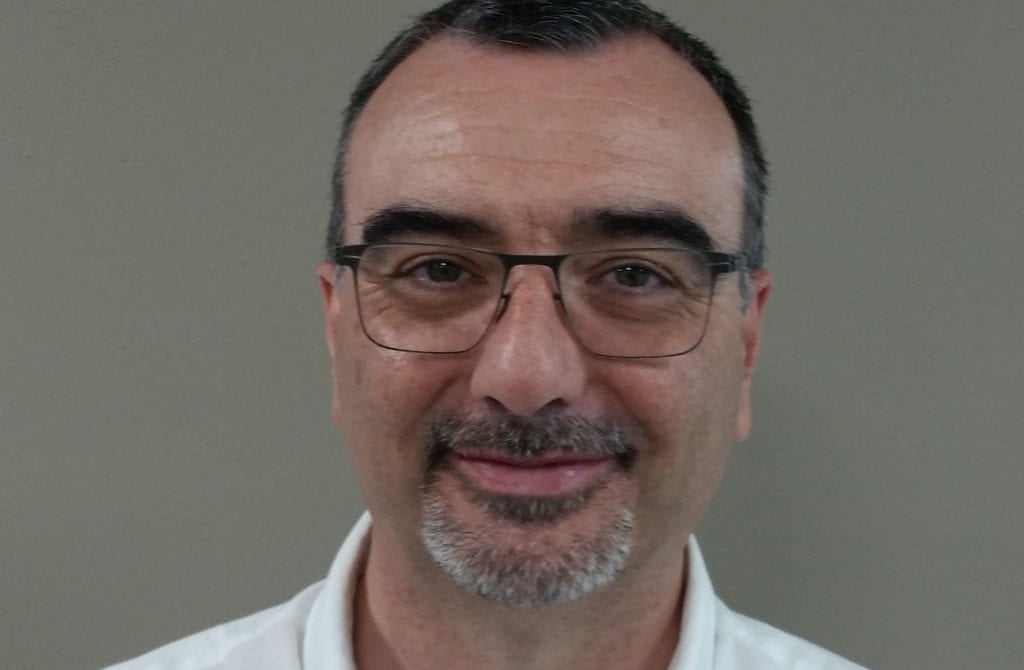
Read more
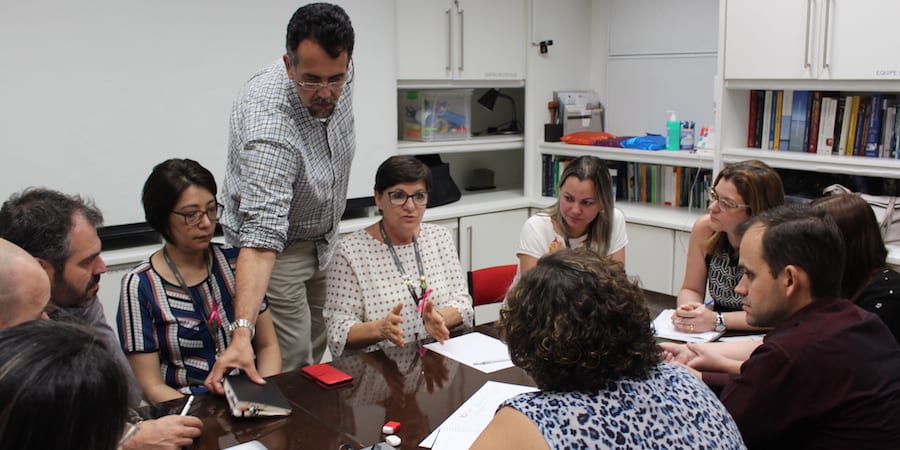
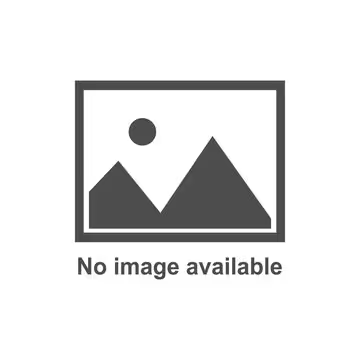
VIDEO - The CEO of a cancer center in Brazil gives us a tour of the their obeya room, taking us through their strategy deployment and explaining how it supports their mission of reducing the burden of cancer.
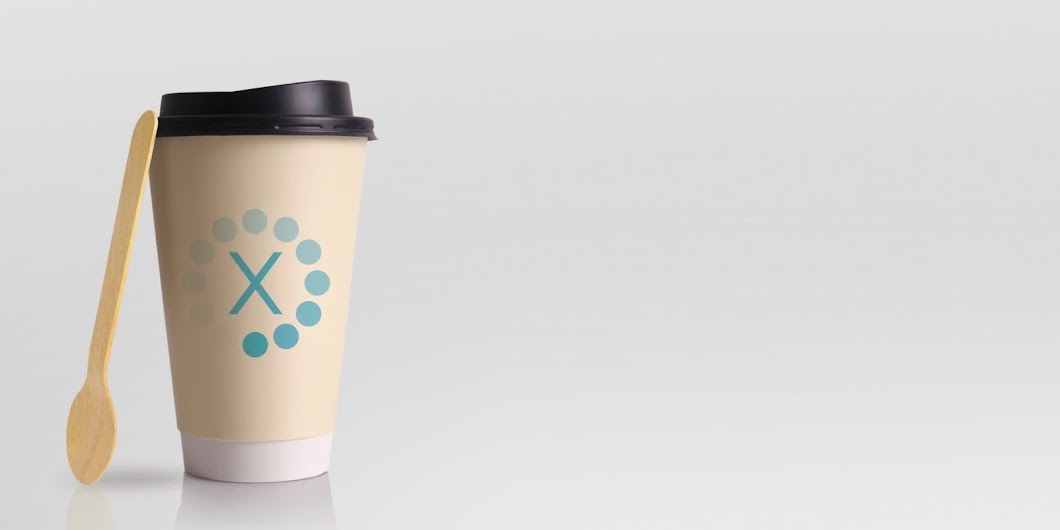
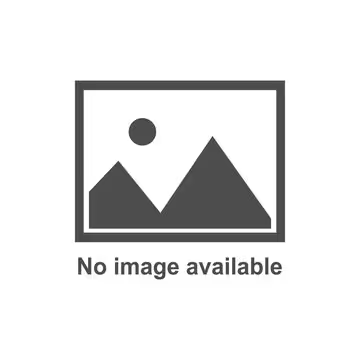
CASE STUDY – This digital organization has embarked on a cultural transformation that is allowing them to become more agile while keeping people and stimulating interactions at the heart of their work.
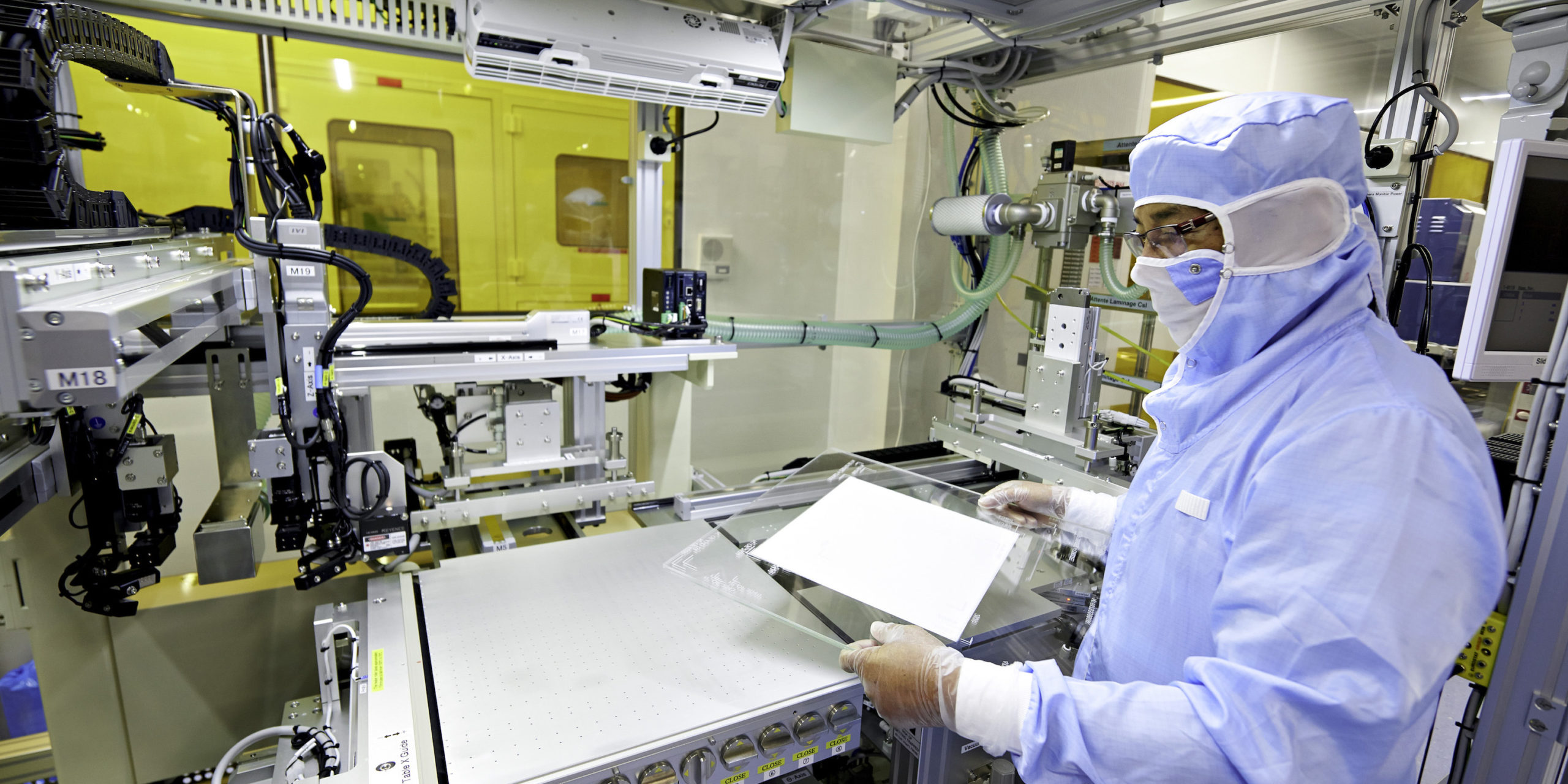
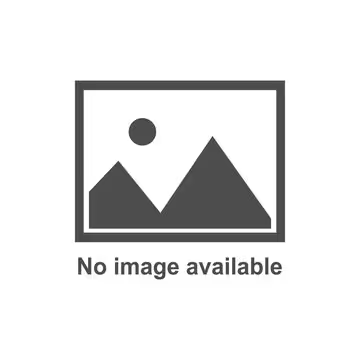
NOTES FROM THE GEMBA – A culture in which problems are tackled as soon as they appear and the production and product development teams work closely together is helping this French healthcare technology company to thrive.
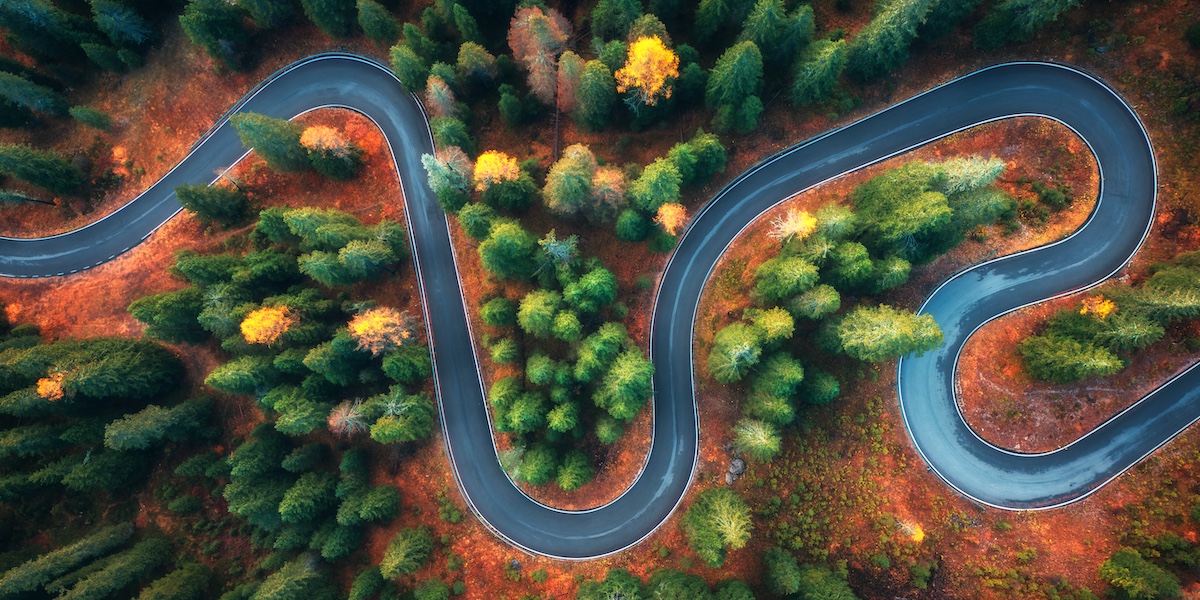
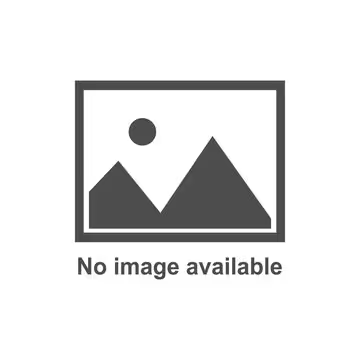
FEATURE - Projects or programs? The authors discuss why Lean Thinking should go beyond piecemeal operational improvements, as a transformative strategy that balances today’s demands with future adaptiveness.