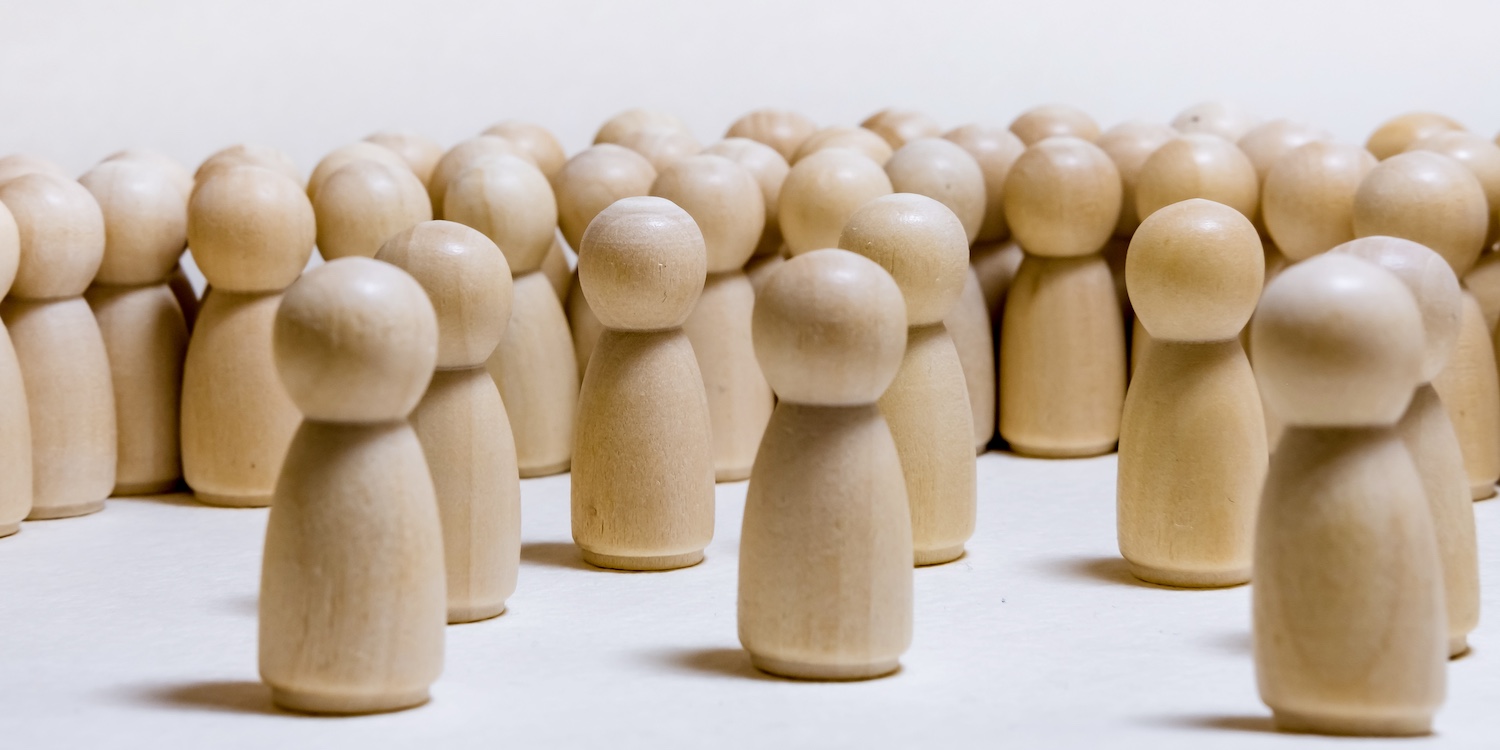
Beyond tools: lean culture and the fight against resistance
FEATURE – This student’s research confirms that lean efforts stall when culture lags. Case evidence shows fear, poor communication and top-down tools breed resistance, but participatory leadership fosters resilient lasting outcomes.
Words: Julieth Guzman
Like many logistics engineering students with real-world experience, I entered the field being already familiar with lean tools. I spent two years working as a logistics operator, followed by six months as a logistics planner—and in both roles, lean tools were all around me: visual boards, standard work, KPIs, and 5S. But something felt off. These tools were visible but disconnected from the way people actually worked – and thought. No one really explained their purpose to them, and most front-line team members, including me, weren’t sure how we were meant to use them to improve anything.
Later, during my internship as a coach redesigning a production floor, I had the chance to shape the approach myself. Instead of diving straight into layouts and tools, I proposed that we start by exploring the existing culture. Together with the team, we focused on training leaders, involving employees early, and asking real questions about behaviors, not just tools. That shift made all the difference. It was the first time I saw how starting with culture could truly shape the success of a lean initiative.
Tools alone are not sufficient. Culture has to come first.
This realization became the foundation for my third-year research project at Breda University of Applied Sciences. I wanted to explore why lean transformations so often stall. Why do people resist? And how does the right culture – or lack thereof – shape those outcomes?
WHY I STUDIED LEAN CULTURE
To answer these questions, I conducted an exploratory, mixed-methods study. This included interviews with logistics and production managers, surveys with front-line employees, and an analysis of real-world case studies. To ground the findings in a practical context, I focused on examples documented on Planet Lean, such as Constructora Bolívar and AstraZeneca.
My goal was to examine lean success and uncover how culture, leadership, and communication influence the resistance that lean transformations often encounter.
WHAT CAUSES RESISTANCE?
Many transformations struggle not because people oppose improvement, but because of how change is managed. From surveys and interviews, I identified several recurring reasons for resistance:
- Fear of job loss or being reassigned to unfamiliar roles
- Confusion about the purpose behind the changes
- Lack of involvement or opportunity to provide input
- Fatigue from repeated top-down initiatives
Interviewees described how these patterns play out in everyday operations:
“The biggest fear is losing your job or getting moved to something unfamiliar. That’s when people start pushing back or just quietly ignoring the new system.”
(Team Leader, Netherlands)
“One thing I’ve seen is that if workers don’t know why a change is happening, they start doubting everything. Poor communication makes them distrust the process.”
(Logistics Team Leader, Netherlands)
“It’s not that people hate Lean. It’s that they don’t understand it — and no one’s really taking the time to show them why it matters to them.”
(Team Leader, WMS project)
These testimonials show that resistance is rarely about opposing change; rather, it is often about the need for transformation. Frequently, it indicates uncertainty, a lack of clarity, or a feeling of exclusion. Addressing these emotional and relational gaps is essential if Lean is to take root.
LEARNING FROM THE FIELD: REAL-WORLD LESSONS
Case studies have confirmed my observations in the field. One notable example, shared on Planet Lean, is Constructora Bolívar. During the early stages of their lean journey, they relied heavily on tools and processes, but team engagement was minimal. There was significant resistance, and improvements were not sustained. The turning point occurred when they shifted their focus to fostering a positive culture by prioritizing team huddles, open forums, and enhancing leadership visibility. That’s when real improvements began to take root.
Another example is AstraZeneca. They addressed resistance by investing in leadership development and involving front-line operators in problem-solving. By empowering employees to lead daily improvements, they cultivated trust and ownership, two essential elements of a lean culture. Both of these examples, documented on Planet Lean, helped confirm what I observed during my own research.
CRASHING VS. BUILDING: TWO PATHS TO CHANGE
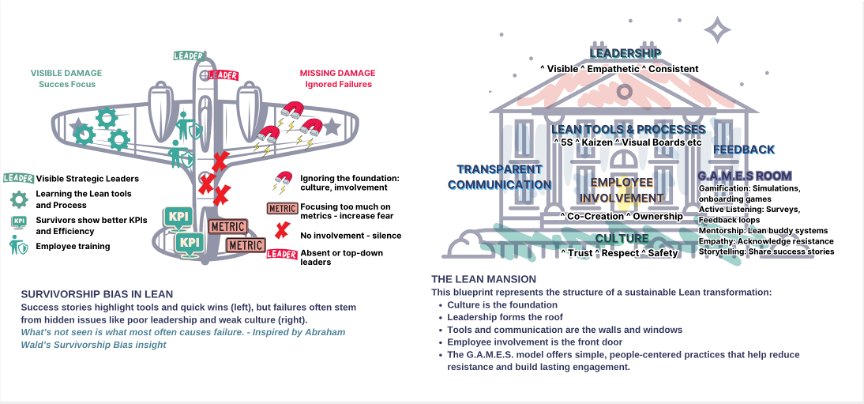
As I gathered insights from interviews and case studies, I began noticing a pattern in how organizations approach lean transformations. That inspired a metaphor I now call “crashing vs. building,” illustrated in the visual above.
On the left side of the image, you see a “lean airplane” in flight. From the outside, everything looks successful: strategic leaders, KPI dashboards, lean tools, and process training. But what we often don’t see is what’s broken or missing — much like Abraham Wald’s famous analysis of survivorship bias.
The right side reveals the hidden damage:
- The cultural foundation is weak or nonexistent
- There’s no involvement from front-line employees
- Leaders are either absent or overly top-down
- Metrics are weaponized, creating fear instead of clarity
This is what I refer to as “crashing”: when organizations rely on visible lean tools but overlook the underlying cultural and relational gaps that quietly undermine their change efforts. Even if it looks like Lean is flying, the absence of trust and clarity can easily ground it.
By contrast, “building” is a more thoughtful, people-centered approach. In this metaphor, instead of launching Lean into the air, we lay a strong foundation — one built on trust, psychological safety, and inclusion. Leaders are present and engaged, teams are involved early, and the change is co-created rather than imposed.
That brings us to the other part of the visual – The Lean Mansion.
Now, I realize the Lean world has no shortage of building metaphors. From the Toyota Production System house to the Lean Global Network’s Lean Transformation Framework, there are already plenty of structures out there. So, in the spirit of friendly architectural competition, I decided to add another one to the neighborhood: The Lean Mansion.
Here’s how it works:
- Culture is the foundation (trust, respect, psychological safety)
- Leadership is the roof (visible, empathetic, and consistent)
- Lean tools and communication are the walls and windows
- Employee involvement is the front door — no one gets in without it
Inside the mansion sits the G.A.M.E.S. Room — a simple, five-part playbook to reduce resistance:
- Gamification: Simulations and games that make lean learning engaging
- Active listening: Surveys, feedback loops, open forums
- Mentorship: Buddy systems and peer coaching
- Empathy: Acknowledge emotional responses to change
- Storytelling: Share internal success stories to inspire and align
This model is not meant to replace others — it’s meant to visualize the cultural and emotional architecture that needs to support lean tools. It reminds us that without strong cultural support, Lean tools crash. But with it, we can build organizations that don’t just implement change — they live it.
FROM RESEARCH TO PRACTICE: WHAT LEADERS CAN DO
Based on my findings, here are six strategies to reduce resistance and foster a lasting lean transformation:
- Start with culture: Before introducing tools, invest in building trust, psychological safety, and a shared purpose. Help people understand why change is happening and how they will be supported through it.
- Lead visibly: engage with your team by walking the floor and asking questions.
- Communicate early and often: clearly explain the reasons behind the changes.
- Involve teams: co-create change instead of imposing it.
- Prioritize psychological safety: encourage honesty and experimentation by rewarding these qualities.
- Apply the G.A.M.E.S. model: reinforce Lean through people-first practices.
Each of these actions strengthens trust and facilitates the establishment of lean principles.
CONCLUSION
This research project has reshaped my understanding of Lean Thinking, not just as a set of tools but as a mindset and a social system. Resistance should be viewed not as failure but as valuable feedback. When individuals feel excluded, unheard, or unsafe, they are more likely to resist change. However, when leaders listen, include, and coach their teams, Lean becomes a shared endeavor rather than an enforced mandate. In an era where logistics and production are rapidly evolving due to automation and digital tools, we must remember that sustainable improvement begins with trust. Culture is not just a “soft”, nice-to-have element of a transformation; it’s the engine of its resilience. By building Lean on this foundation, we do not simply change processes; we create organizations that can grow, adapt, and thrive.
THE AUTHOR
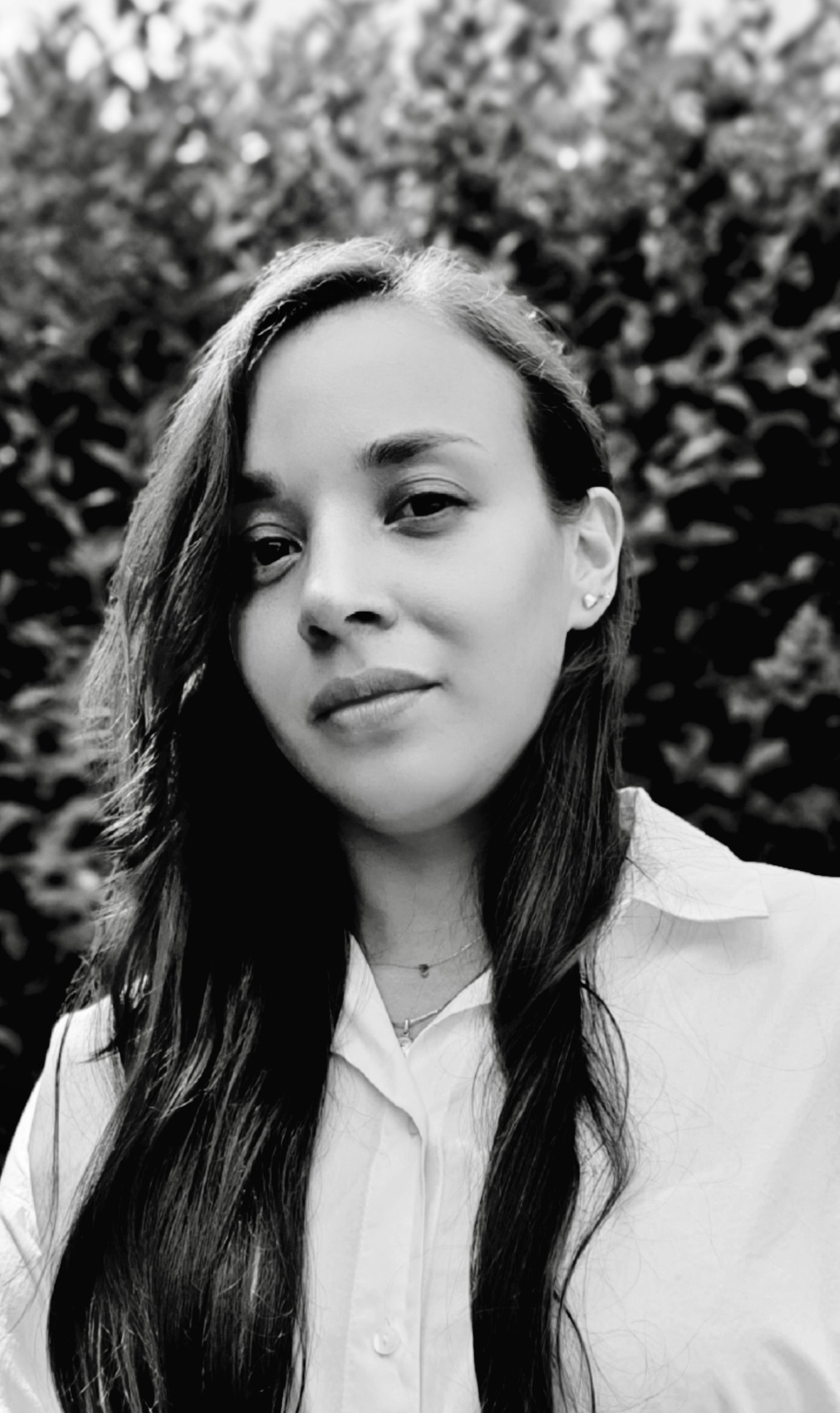
Read more
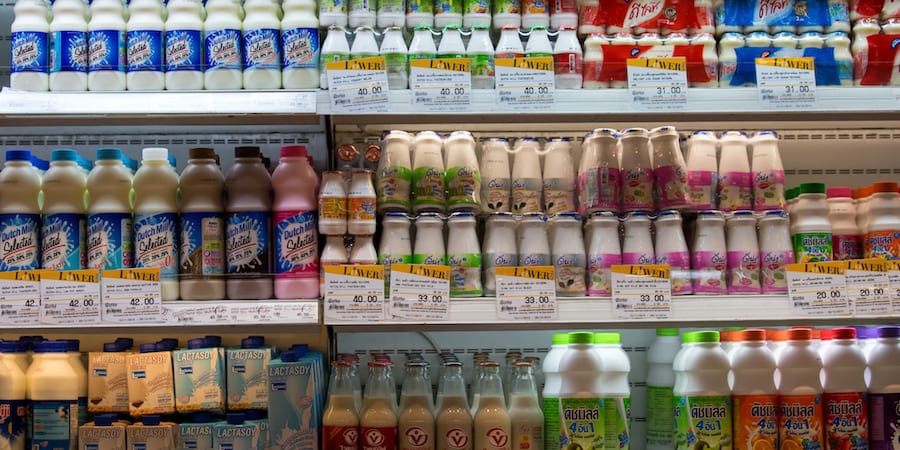
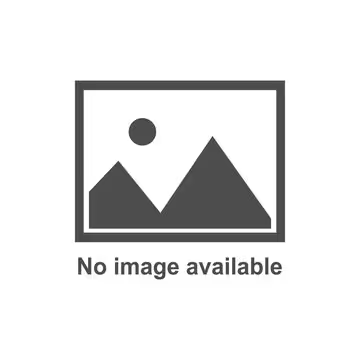
FEATURE – We often think that making every product customers might want – no matter how little they sell or how much complexity they add to our schedule – is inherently lean. As Toyota understands quite well, however, it is quite the opposite.
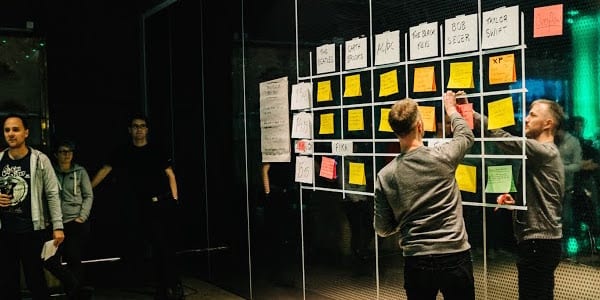
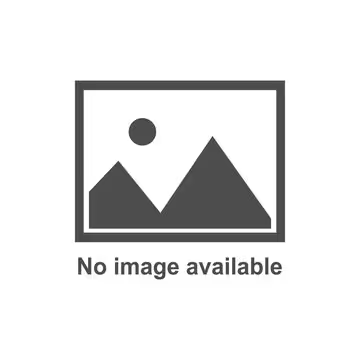
CASE STUDY - How Spotify developed an alternative management system based on servant leadership, interaction-based learning and adaptability – changing the music industry along the way.
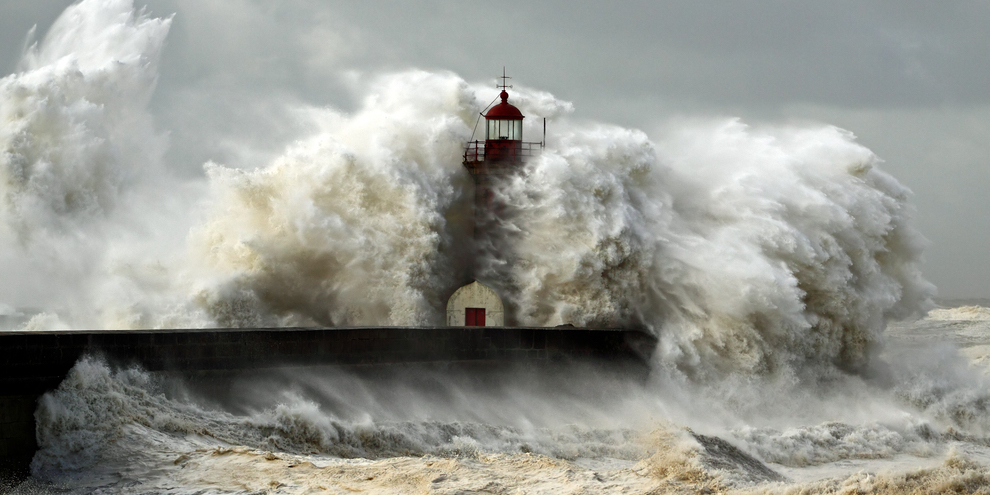
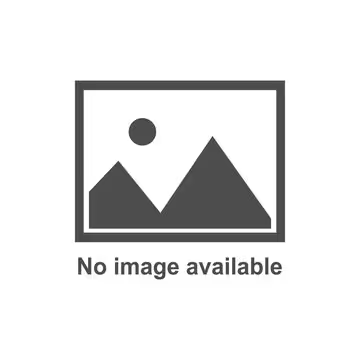
CALL TO ARMS – The current economic situation is presenting great challenges to organizations around the world, but in difficult times lean gives its best. Provided we all do our part, with conviction and determination.
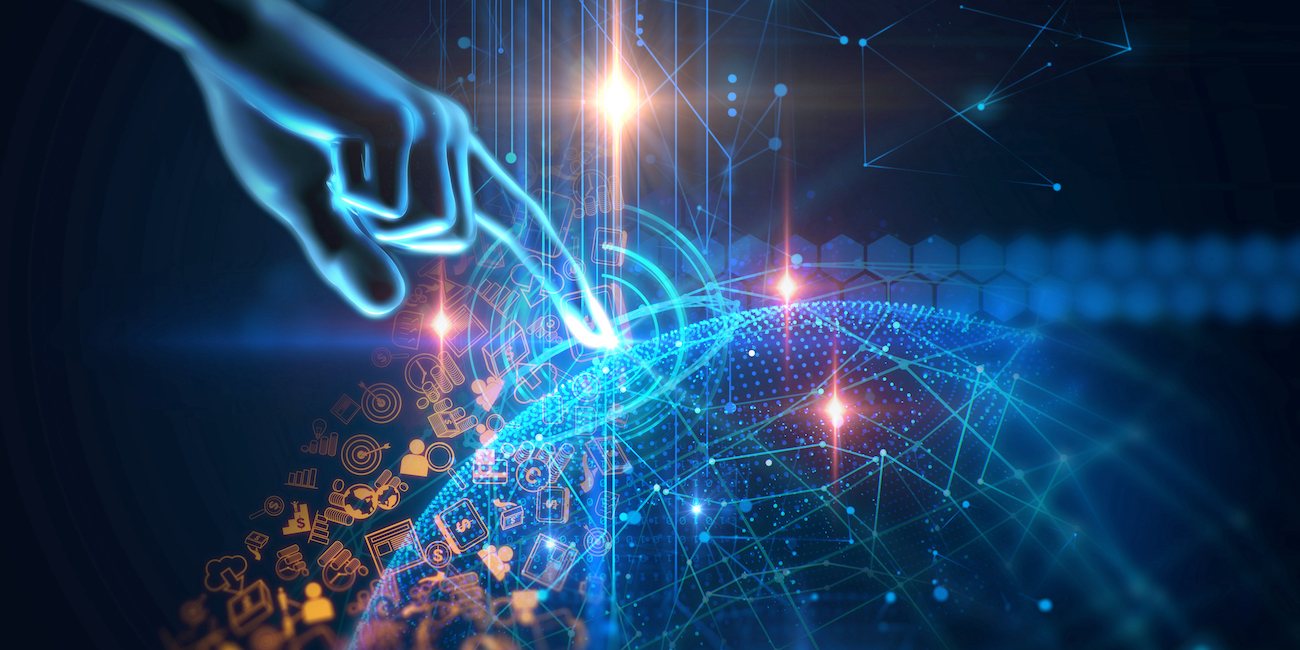
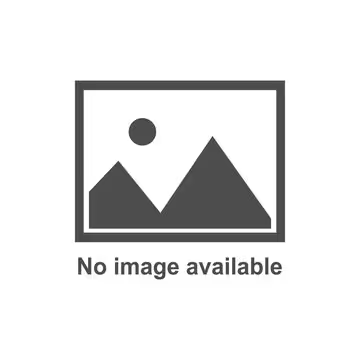
FEATURE – The author shares a few lessons learned on his company’s journey to Industry/Quality 4.0, the foundation to 5.0 Artificial Intelligence.
Read more
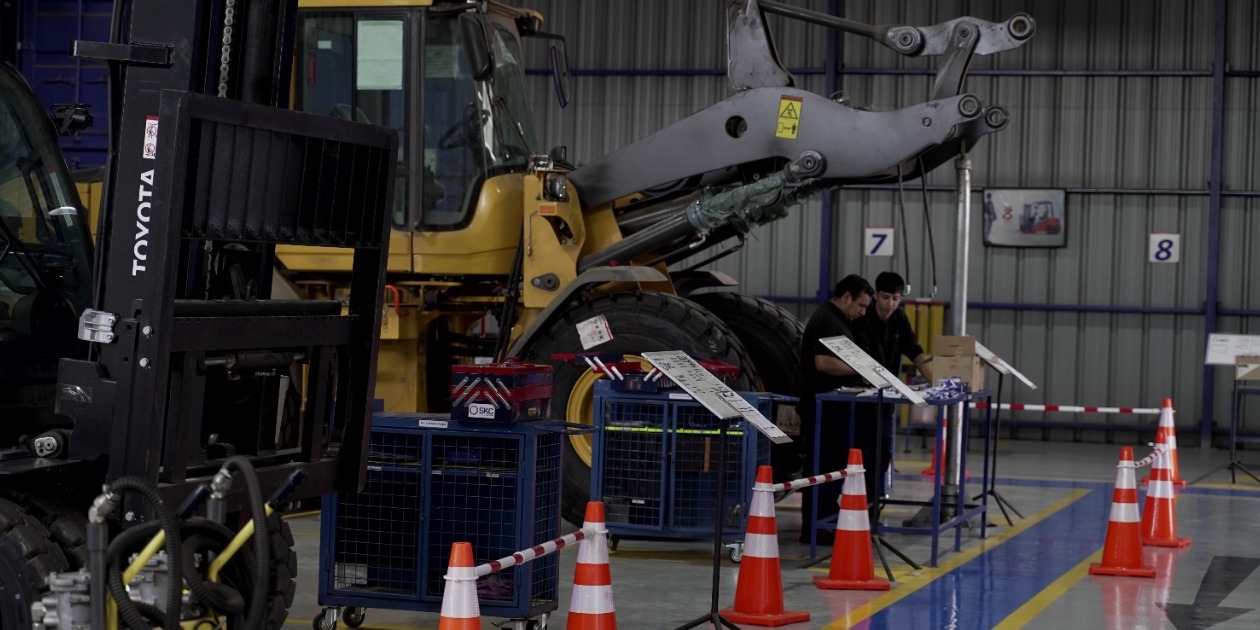
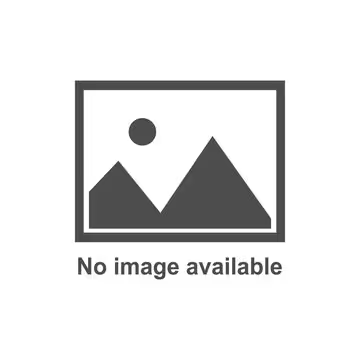
CASE STUDY – A Chilean company selling and servicing vehicles and equipment for a variety of industries has made of humility the leading trait of its cultural transformation, with great results.
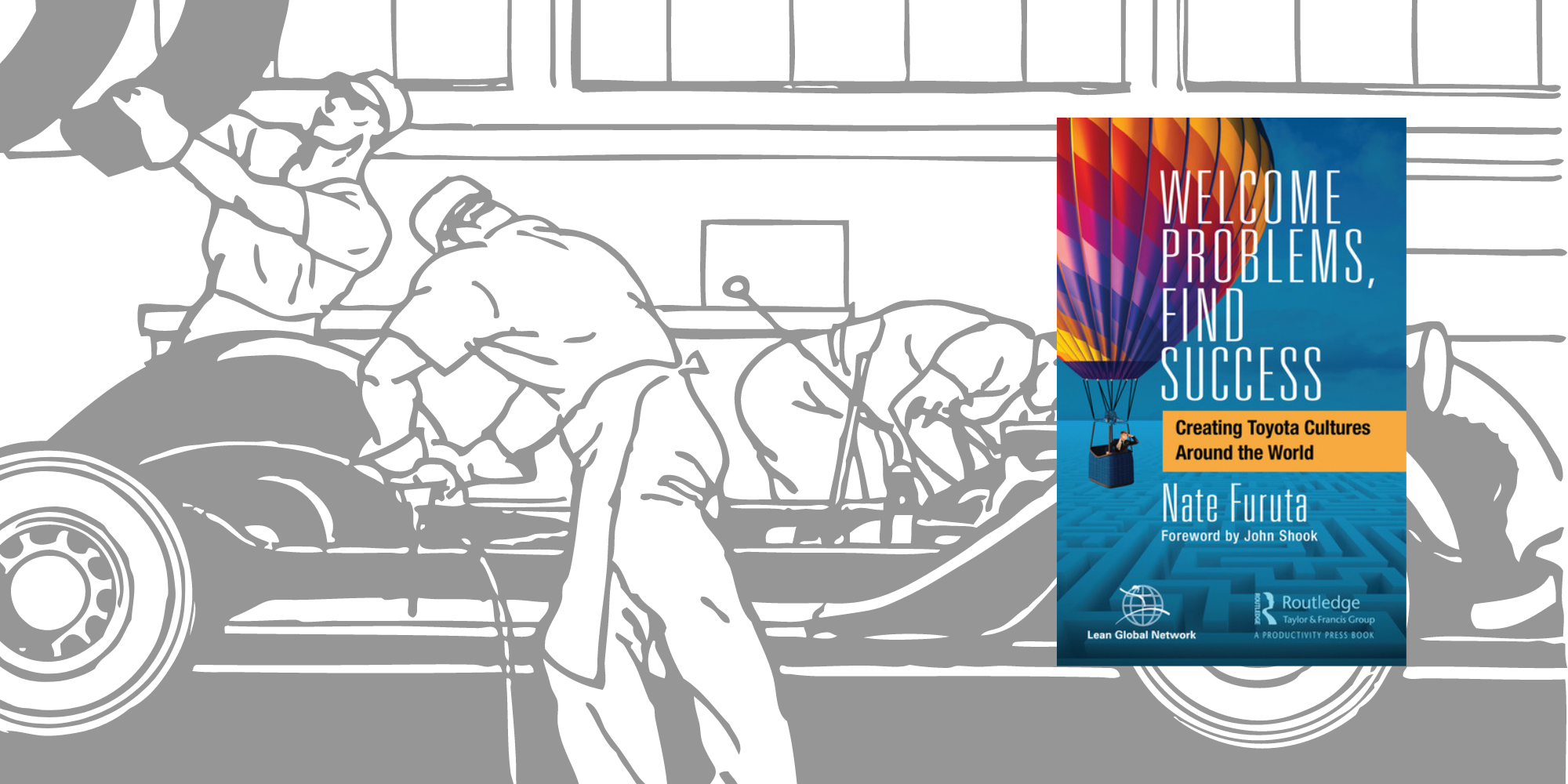
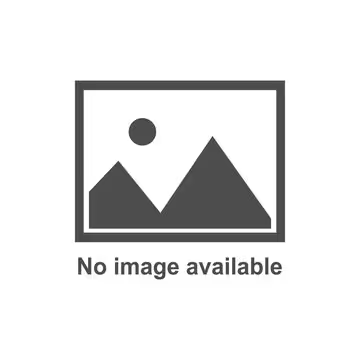
FEATURE – The Lean Global Network just published a new book by Kiyoshi “Nate” Furuta sharing compelling examples of how Toyota principles and culture can be effectively spread to new environments.
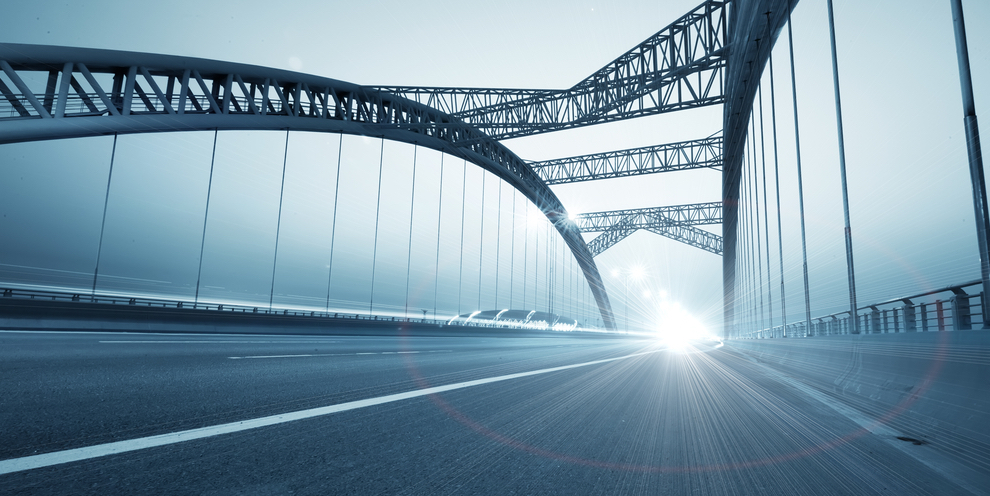
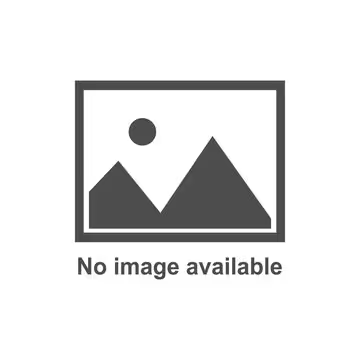
INTERVIEW – This metalworking company based in Poland has leveraged the cultural change brought by Lean Thinking to significantly improve its processes. Ahead of his presentation at the LGC, their lean manager tells us how they did it.
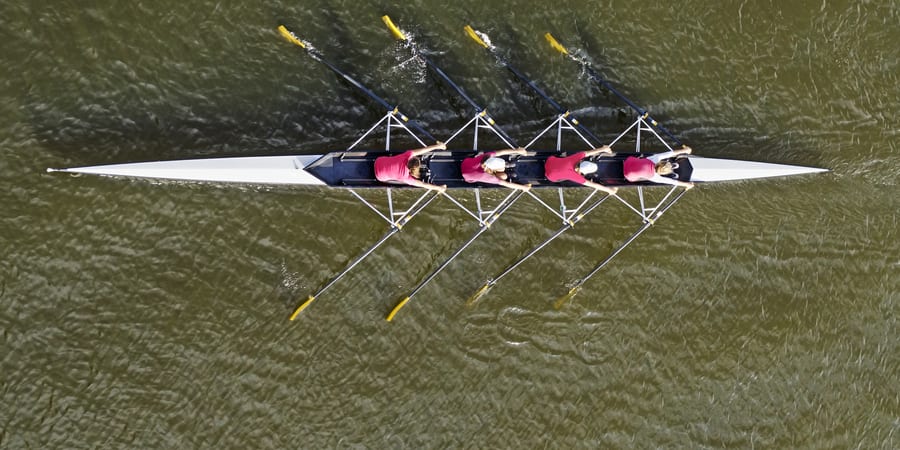
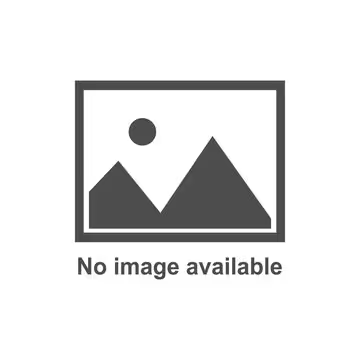
FEATURE – We all want to create a lean culture in our organizations, but what makes cultural change possible? And, more importantly, what are the leadership behaviors that enable a new culture to take root?