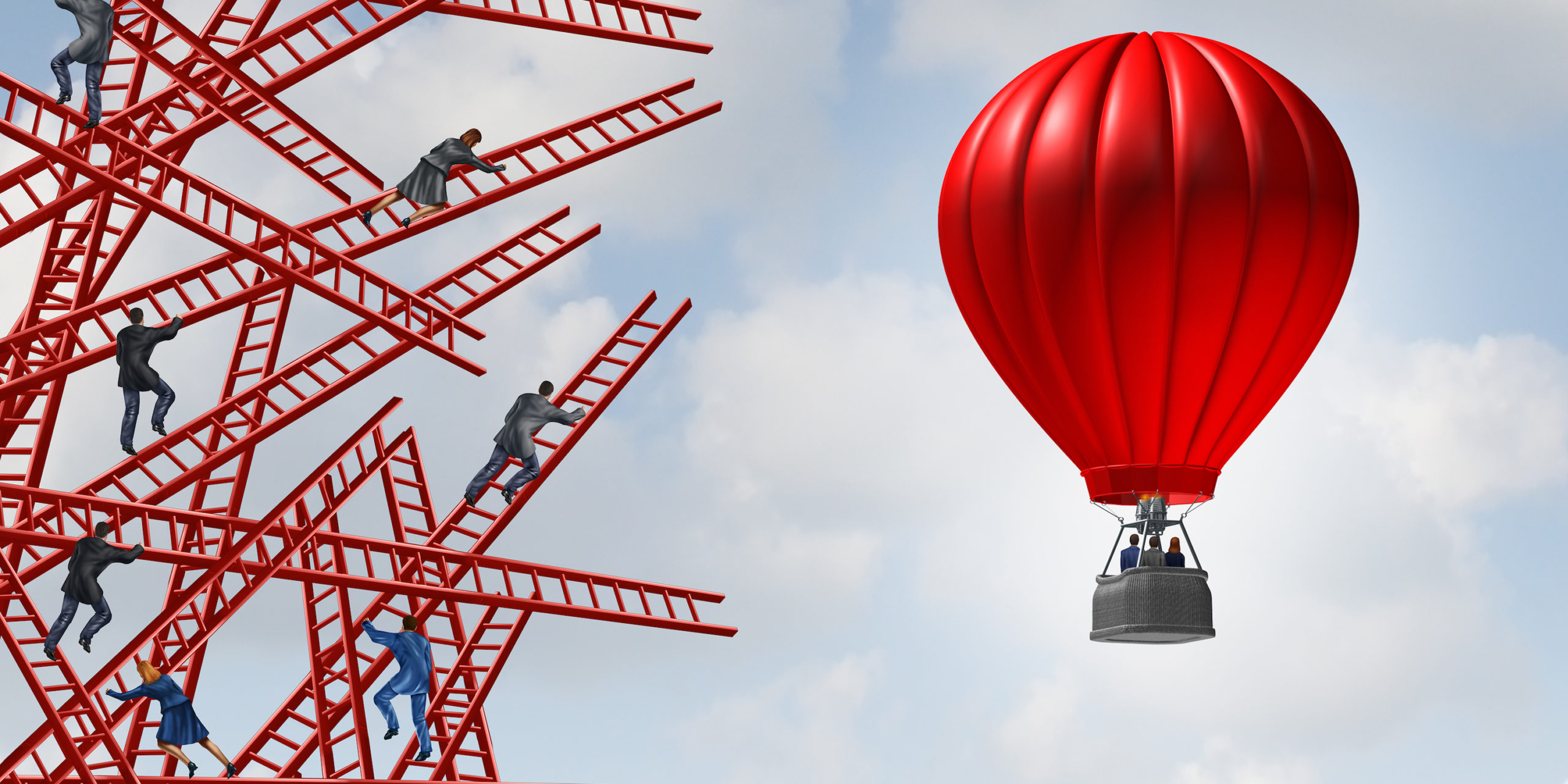
Introducing the Toyota Flow System
FEATURE – In the age of complexity and disruption, flowing value to customers as quickly as possible is critical. The new Toyota Flow System strives to address this issue.
Words: Nigel Thurlow, Chief of Agile, Toyota Connected; John R. Turner, Ph.D., University of North Texas; Brian Rivera, US Navy
Lean thinking, Agile, UX, Design Thinking… With so many improvement methodologies, frameworks, philosophies and techniques out there, we can’t be surprised if confusion ensues. The noise around all these different approaches – from proponents of each who often bicker with one another – can be deafening. Yet, when it comes to business transformation, we believe everybody is right and everybody is wrong.
Let us explain. There are fantastic lessons to be learned all around, from Systems Thinking to Scrum. The body of knowledge at our disposal is immense, and there are countless ways to apply it. But to truly leverage this wealth of information, we must change the narrative and realize that context is everything: different environments call for different approaches and tools, and with something as complex as a business transformation, sticking to a one-size-fits-all methodology is dangerous. Instead, we need to be able to mix and match the techniques that best suit our situation, while ensuring that key aspects of a transformation are considered.
With such flexibility in mind, over the past few years we have developed the Toyota Flow System (TFS). The TFS can be described as a system of patterns, practices and techniques to enable organizations and institutions to achieve desired outcomes in a complex world. This model uses the popular representation of a house, from the Toyota Production System model (TPS), to outline an evidence-based approach to achieving business transformation. The TFS is a system of understanding, and not a one-size-fits-all framework. (It will be released under a Creative Commons Attribution Share-Alike license.)
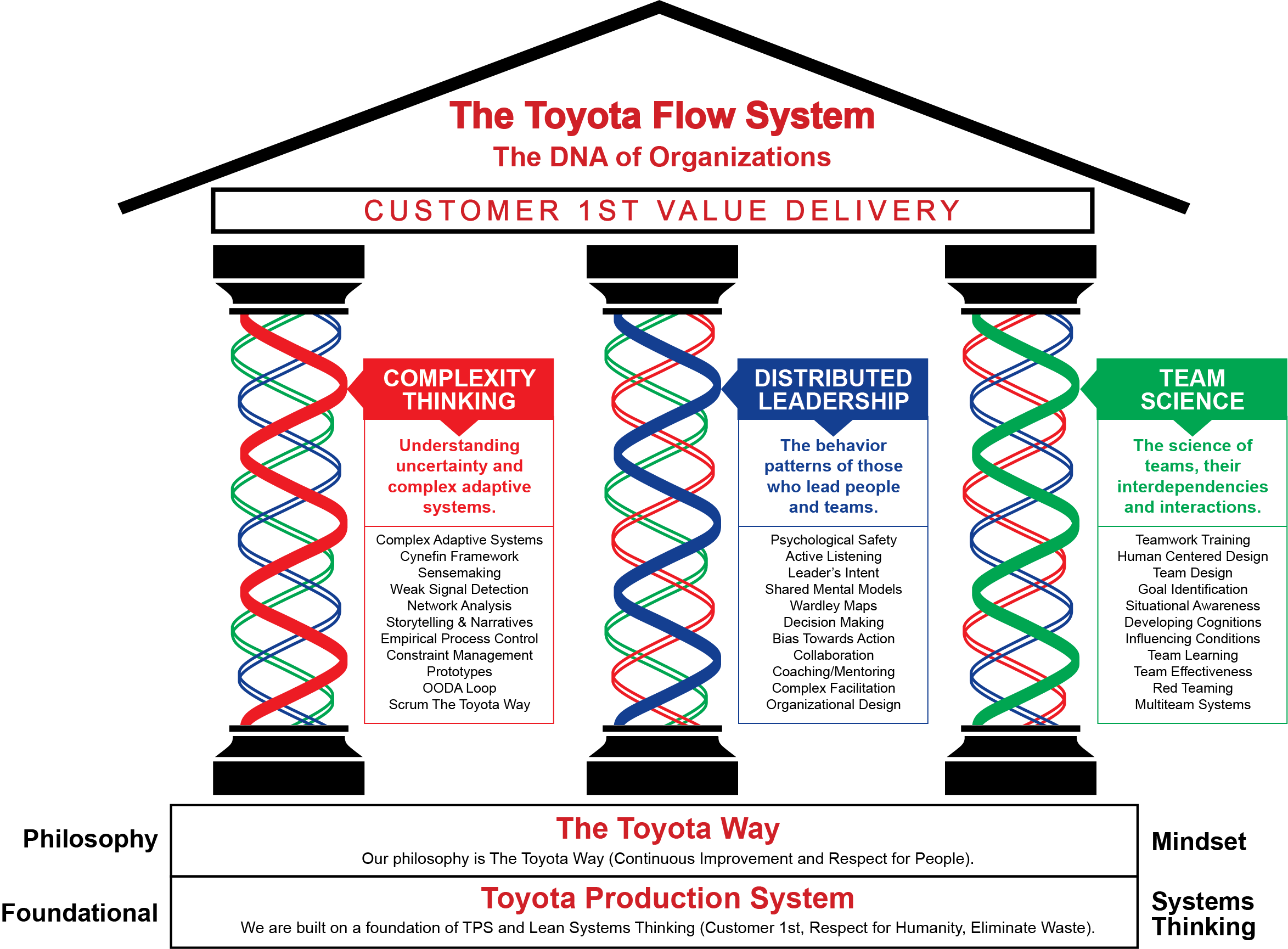
©2019 Nigel Thurlow, Professor John Turner, Brian Rivera. Offered for license under the Attribution license of Creative Commons, accessible at http://creativecommons.org/licenses/by/4.0/legalcode and also described in summary form at http://creativecommons.org/licenses/by/4.0/. By utilizing this Site and any information presented you acknowledge and agree that you have read and agree to be bound by the terms of the Attribution license of Creative Commons.
The TFS model aims to sustain the flow of value to the customer, who is the center of the TFS universe. As such, in the TFS diagram it is both at the foundation as the cornerstone of TPS, and at the top of the house. In today’s hyper-competitive and complex world, we must be able to serve customer needs incredibly quickly – lest we become a victim of disruption. As Peter Drucker once stated in his book The Practice of Management, “There is only one valid definition of business purpose; to create a customer.” Given the speed of business today, the iterative nature of improvement we are used to is no longer an option: there is no time for changes after a product hits the market, because it’s already time to develop the next one.
As we dig deeper into the helixes, we find the philosophies, tools and knowledge (practice and theory) behind each component. For Distributed Leadership, leadership is viewed as being bottom-up, top-down, as well as horizontal. We present it as a team construct rather than an individual construct. Complexity Thinking involves identifying the level of complexity that is present in a problem or environment and calls for viewing systems as open and complex adaptive systems (CAS). Some of the techniques utilized in complexity thinking include sensemaking and weak signal detection. Finally, Team Science utilizes empirical research to incorporate teamwork into current practices rather than operating as command-and-control groups with no teamwork present. Techniques from Team Science including proven approaches to develop psychologically safe environments that foster high-performance teams that are innovative and effective when functioning in complex environments. We believe the list of items under each component in the helixes is comprehensive, but can (and should) evolve with new understanding.
Bring these interdependent elements together, understand how they interact with one another, adapt them to your environment, and you have everything you need to truly transform your organization, address complexity and be better positioned to take on future challenges.
BUILDING ON TOYOTA’S LEGACY
Our motive to create this model was the realization of the need to change the paradigm of how organizations improve and transform themselves. We can’t keep doing things the same way and expect a different result. Toyota itself is moving away from linear project management in a bid to speed up decision-making and change. Here’s an example of how complex the problem Toyota strives to solve actually is. The company is known for top-notch quality, but what does this really mean? Does quality refer to reliability and durability, or is it also related to user experience and customer expectations? These are the types of questions we are asking ourselves in this age of disruption. Complex problems call for elaborate responses, and we believe the TFS model provides a means to formulate them.
This doesn’t mean we are losing touch with our Toyota DNA. We still embrace the teachings of TPS and The Toyota Way. They are in the foundations of our house (it would be stupid to undo 82 years of history), but at the same time we need to find new, better ways to approach complexity.
The most recent developments in Toyota – from Toyota New Global Architecture (focused on Just-in-time to reduce cost of delivery) to the Back to Basics idea (reaffirming the company’s commitment to customers following the recall crisis) – are fundamentally about realigning the company to understand the flow of value to the customer with the best possible lead-time, highest possible quality and lowest possible cost. This was the foundation of our work. What we are saying with the Toyota Flow System is there are new tools and thinking out there that can help us in this disruptive world. The model reinforces the principles of customer first and Just-in-time delivery underpinning TNGA and Back to Basics. We believe it forges a path to continuous success, allowing Toyota to remain the leading organization it’s been for decades.
Indeed, TFS is more than just agility and innovation; it’s also about resilience and safety. This means it’s applicable to every kind of scenario – like patient safety (it has been shown that some of the main causes of death in US hospitals are related to poor teamwork and leadership). With this model, we are hoping to create a system of understanding that allows Toyota to continue to transform and take on the challenges of the future (we have already introduced it in Toyota Financial Services, but that’s a future story). We also want to help organizations around the world and contribute to solving complex social problems. The Toyota Flow System is an inclusive model that every organization in the world can find useful, from the software development firm applying Agile approaches to a hospital struggling to make teams effective.
THE RESEARCH CONTINUES
One of us, Nigel, has been looking at the challenge of transforming organizations in complex environments for a long time. Both inside and outside Toyota, he found common themes across transformational journeys: leadership at certain levels is detached, siloed, stuck in command-and-control mode and not engaged. Then came the realization that this is actually a team issue – what are leaders to do if not engage with the rest of the business to effectively run it? At the same time, the other two authors (John and Brian) were engaging in their own research into team science – John in an academic setting and Brian in the US Navy.
When the three of us connected, our combined knowledge and experiences naturally became a part of the Toyota Flow System model – the culmination of years of work, which we carried out both separately and together. The model is based on our experiences with these problems and our studying them for years. The Toyota Flow System is a model that has combined practice and theory into one comprehensive pragmatic model that has utility. To make it relevant to as many people as possible (and for our own learning), we have integrated our research with the invaluable insights brought to us by people of the likes of Deming, Ohno, Drucker and Shingo.
This is the first time someone has brought all these elements together and made sense of them, explaining how they fit within a company like Toyota. Complexity thinking is a change in mental models and management practices. The Toyota Flow System is the first to externalize it with tools and in a contextual setting. The next step will be testing it in the field in different contextual settings, to see what works and what doesn’t. It will be exciting to see how it evolves, which we are sure it will. That’s the beauty of it.
“The contents contained in this article do not represent U.S. Navy/Marine Corps’ positions or opinions.”
THE AUTHORS
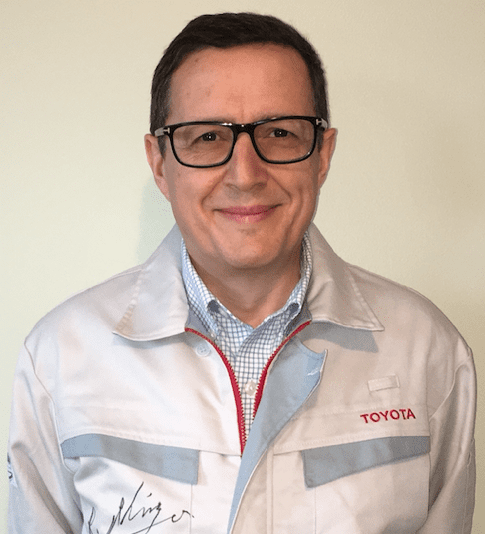
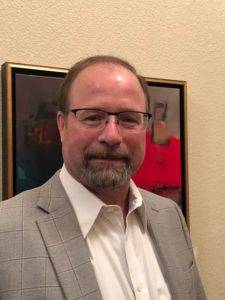
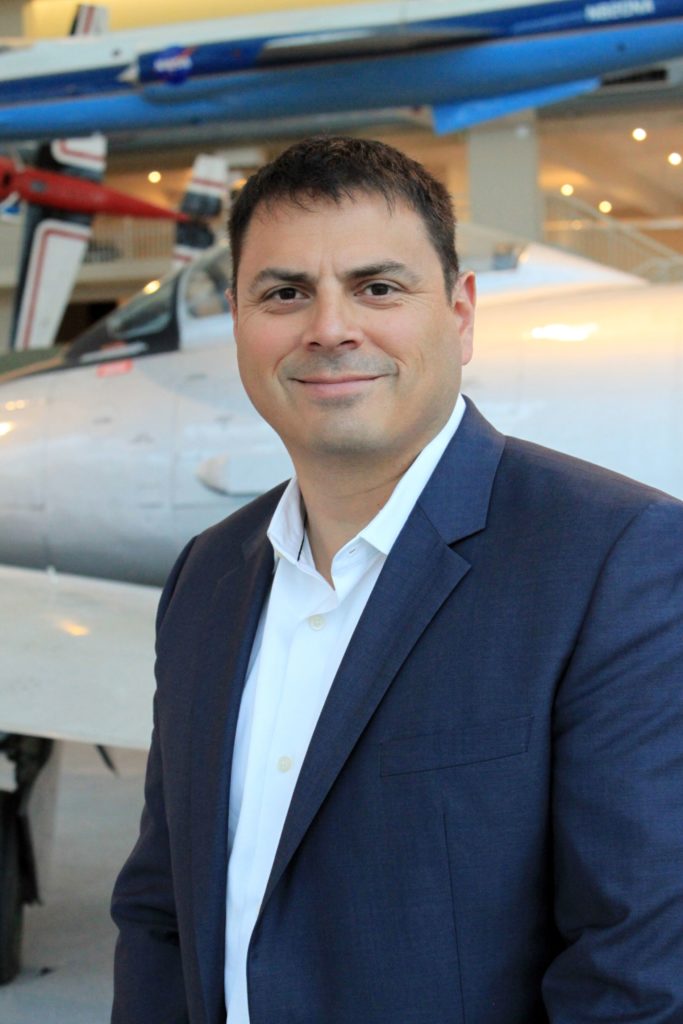
Read more
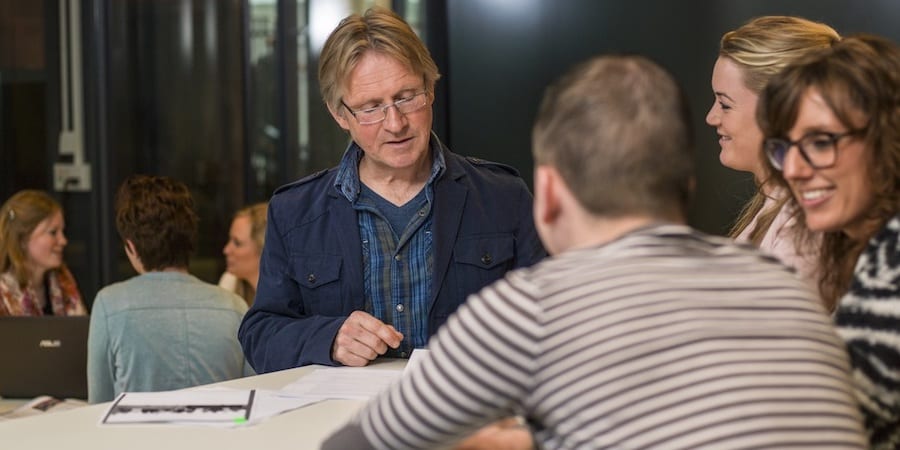
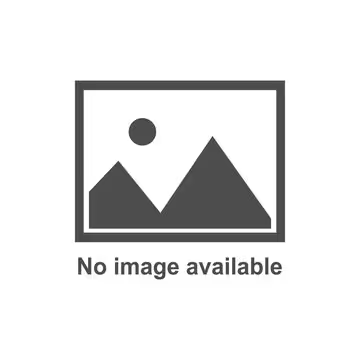
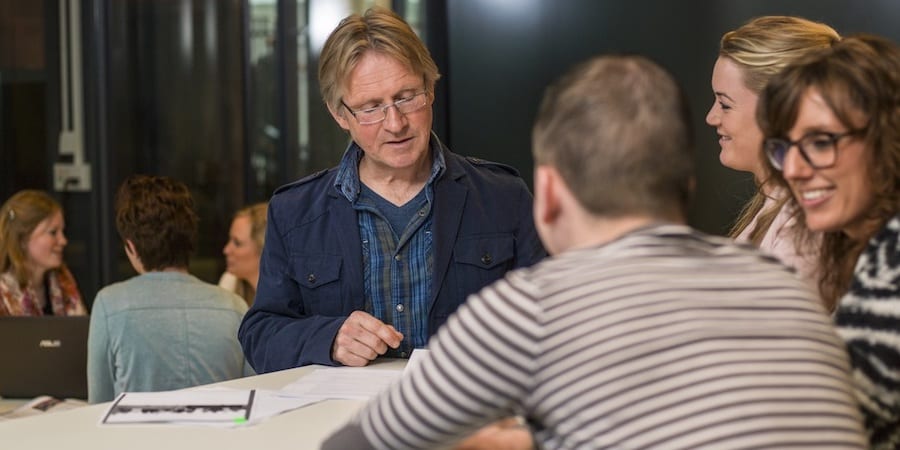
INTERVIEW – In this Dutch university, lean is not only taught in the classroom. A3s are now replacing the writing of a thesis as the final assignment students are asked to complete.
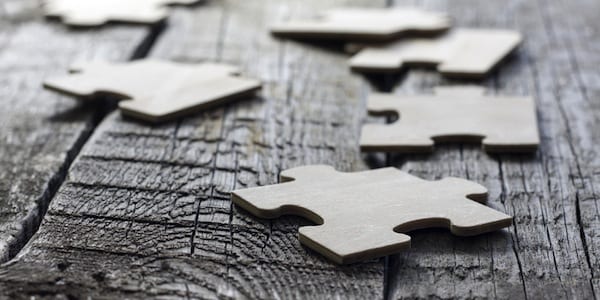
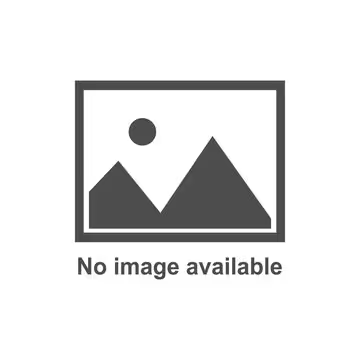
FEATURE - This set of guidelines will help you to understand how to properly structure your lean transformation, keeping into account the entire organization as it tries to embrace and manage change.
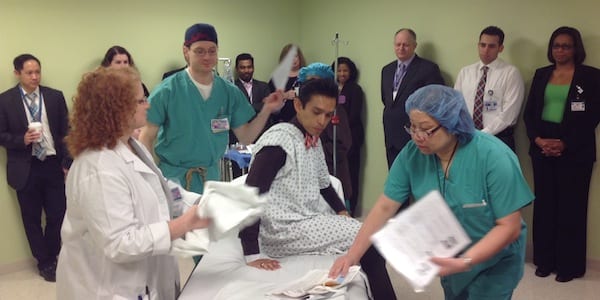
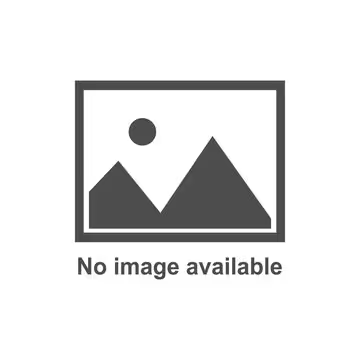
INTERVIEW - New York City's public hospitals system leveraged lean principles and techniques to improve the quality of care and boost organizational performance.
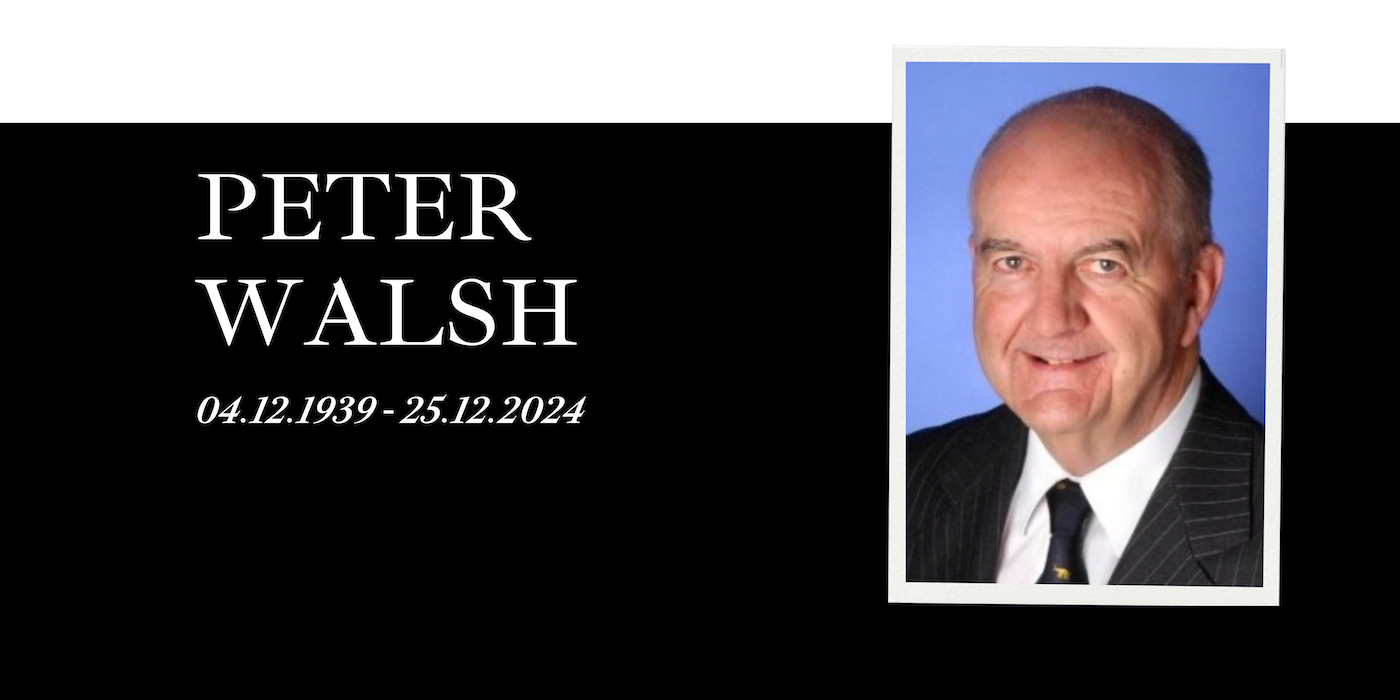
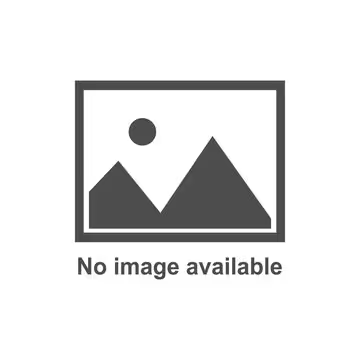
FEATURE - With heavy hearts, we share the news of the passing of Peter Walsh, a pioneer of the Lean Community. Peter's work was instrumental in allowing Lean Thinking to take root in Australia, as some of those who knew him tell us here.