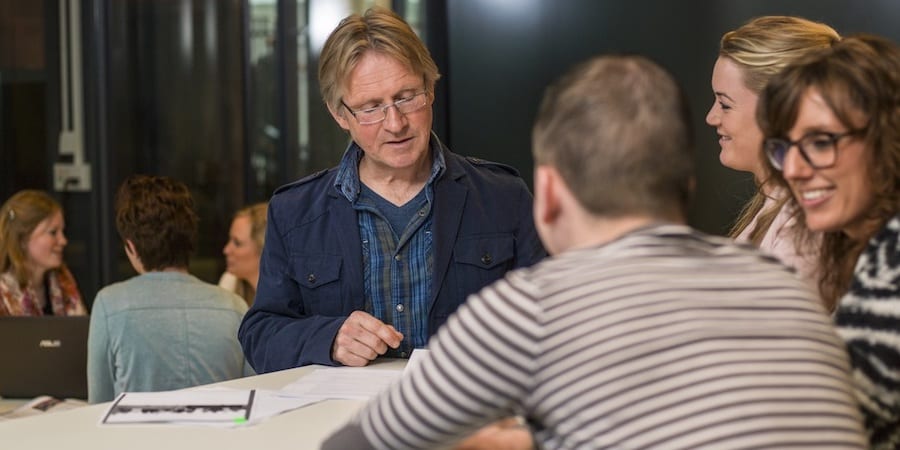
These university students are replacing theses with A3s
INTERVIEW – In this Dutch university, lean is not only taught in the classroom. A3s are now replacing the writing of a thesis as the final assignment students are asked to complete.
Interviewee: Harry van der Werk, Lecturer at Avans University of Applied Science
PL: Tell us about Avans, please.
Harry van der Werk: Avans is a university of applied sciences in the Breda area. Our students (who are between 17 and 24) stay with us for four years and do a lot of outside work, in the form of internships and projects at companies.
I am a teacher at the school of finance and management. In reality, however, I am more of a coach than a lecturer, supporting students as they complete their final projects before graduation and managing the relationship between the university and the hosting companies.
PL: What does lean have to do with this?
HVDW: Lean is built into our curriculum as one of our leading courses, lasting for the entire four years. This includes both theory and practice, like the final project at a company. We teach our students how lean thinking can lead to sustainable success for organizations. We want them to become critical thinkers, and we consider lean a great way to develop their skillsets – giving them the tools to get to the root cause of a problem and address it. Developing lean capabilities in young people is critical, because it means we won’t have to “do rework” and change their minds later on in their lives. (We all know how painful they can be, and we’d rather help them get it right first time.)
PL: What is it like for students to come to a university with such a strong focus on lean? There aren’t many covering it to such an extent.
HVDW: Arriving from very traditional schools, most of our students find the way we teach to be very engaging. Our educational strategy is based on the idea of learning that is centered around real-life projects and examples. We also encourage students to come up with their own learning strategies, based on their strengths and experiences.
PL: Can you tell us more about the final projects students must complete?
HVDW: This 20-week project is part of the last year’s workload. The company comes up with a problem (based on their needs) that the student will be asked to solve, and we at Avans gauge whether there is enough depth to the problem for it to qualify as a final project. For example, a student’s project might entail working in the business’ warehouse and solving the problem of inputting the content of boxes into the ERP system while minimizing the number of typos (thus reducing delays and rework). The companies that host our students are very different: some have a lot of experience in lean, while others are startups and haven’t started their lean journeys yet.
The standard tool we use to document the learning and map the project is, of course, the A3 methodology. Starting this year, students will no longer be required to write a thesis. The A3 will take its place.
PL: That’s very interesting. What’s the idea behind this?
HVDW: The businesses we collaborate with kept suggesting that theses and 40-page final reports are not something that students will ever best asked to produce on the job. They see them as an obsolete and time-consuming way to conclude one’s studies. To write such a long report takes at least four weeks, out of the 20 the students spend at the companies. With the thesis, students used to spend 12 weeks at the gemba and eight writing. Now they will spend 20 at the gemba! Additionally, the A3s will be reviewed every couple of weeks, which means that the final work is likely going to be much more polished (because we have several iterations and can steer students in the right direction as they progress in their projects).
There are also benefits for us teachers. The number of students at Avans is growing and last year, we had about 100 theses to read before the summer holidays, with 15 teachers available. Considering the evaluation is done by two teachers, you can imagine how much work we had to complete, in a batch, at the end of the year. The A3 will change all of that, making our job easier while helping the organizations with practical advice they can immediately use to improve their processes. There is no doubt an A3 has a more direct impact than a booklet. To me, this is a win-win: the companies get help, and we teachers get a smaller workload. We have moved away from batching and this has made things better for all of us. We were so used to writing theses that we couldn’t explain why any more.
PL: What do you think students can get out of this A3-based system?
HVDW: It’s more compatible with what happens in the workplace, for starters. It’s also a much easier way to get feedback. It’s more motivating for them as they learn to put what they learn to good use.
PL: What makes it possible to do this in your school and not in others?
HVDW: We have the guts to do it, for starters. It’s also the fact that we work closely with businesses and they are asking us to do it. This is really about listening to the voice of the customer: the companies, the students, and more or less directly the community (the improvements our students make in the organizations can be really impactful, especially if they happen to run a project at the municipality of Breda or at a local hospital).
PL: You are training both students and teachers with the help of Lean Management Instituut. What book are you using?
HVDW: John Shook’s Managing to Learn, of course. What else?!
THE INTERVIEWEE
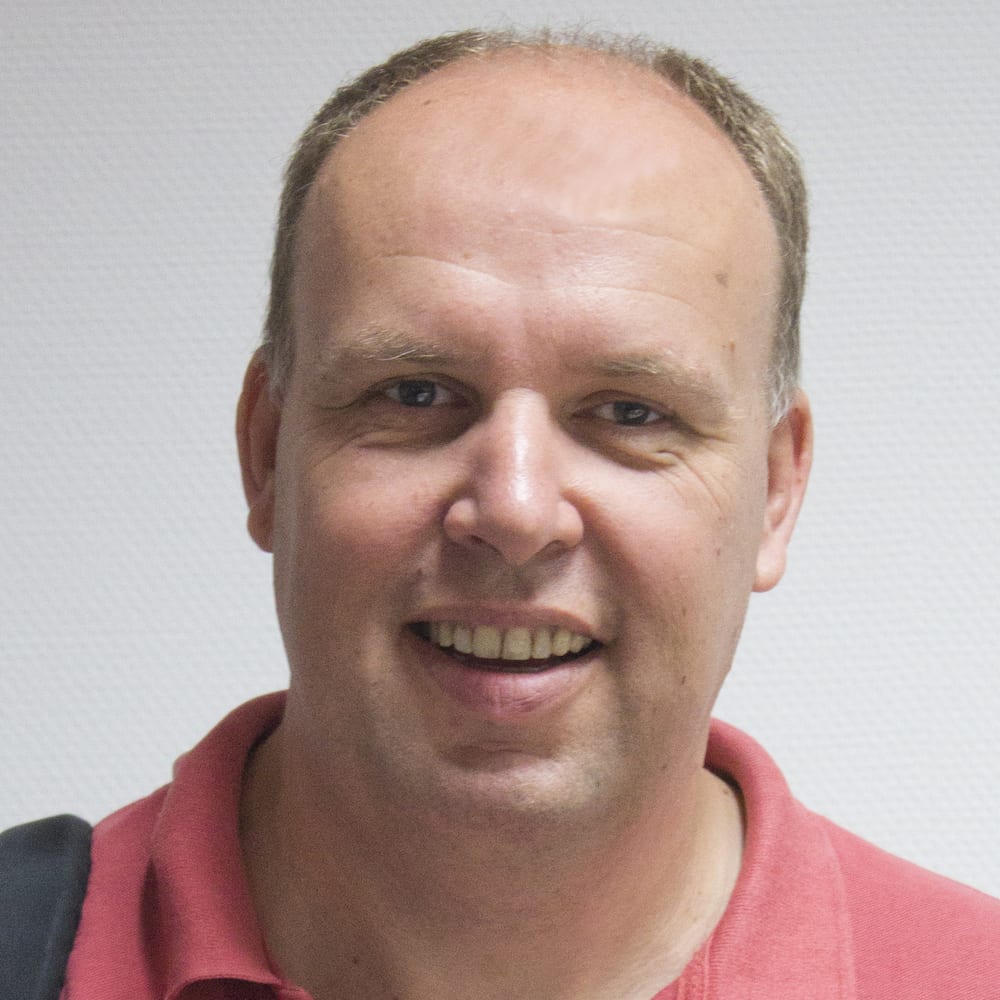
Read more
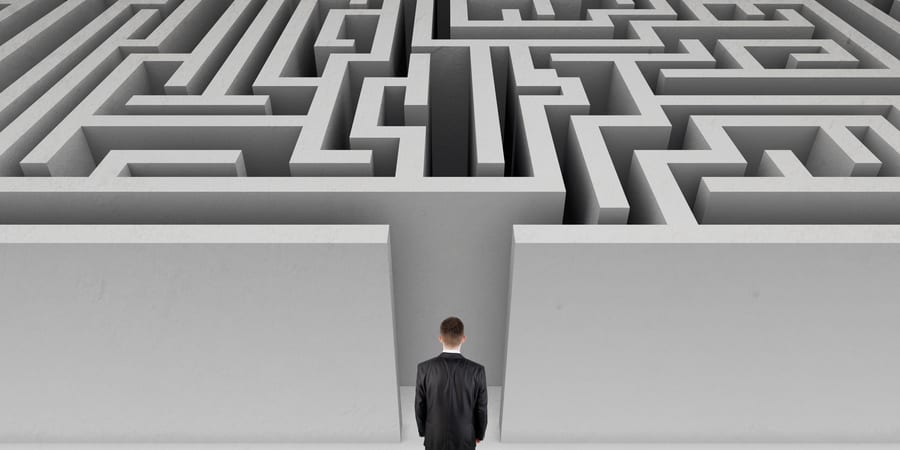
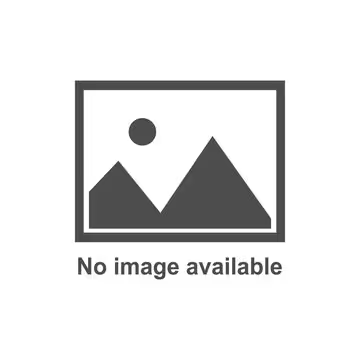
RESEARCH – The author explores the effectiveness of five common managerial practices in driving a corporate lean initiative forward, analyzing the data gathered while visiting 36 factories of a large corporation.
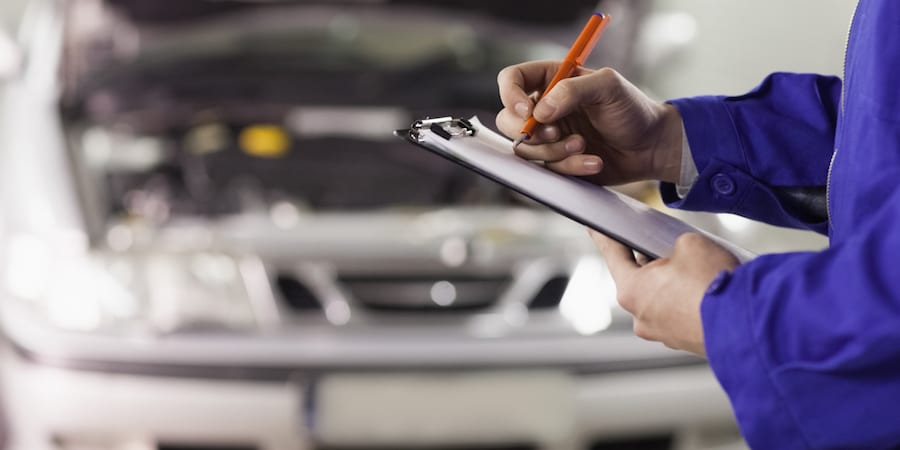
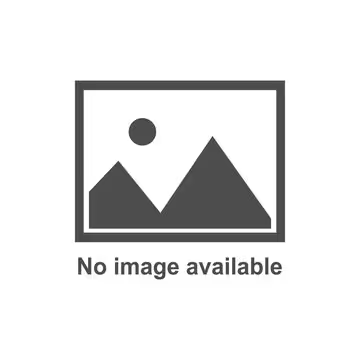
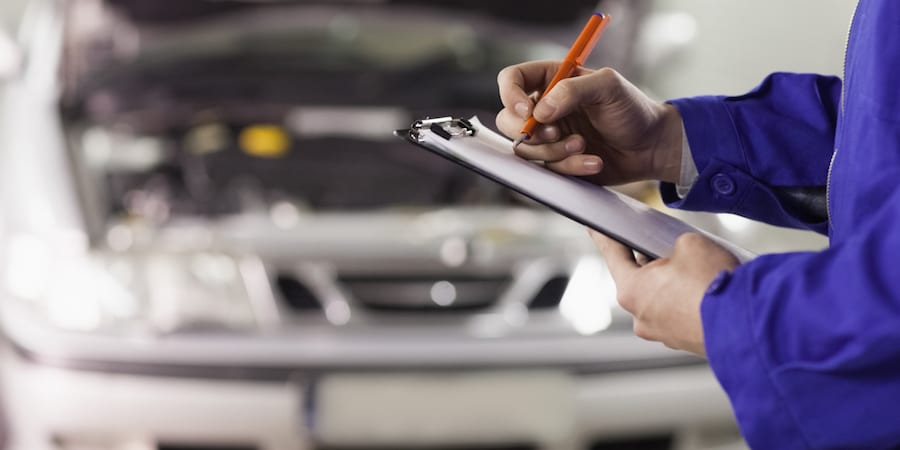
WOMACK'S YOKOTEN – In our lean journeys we spend so much time on improvement (kaizen) and innovation (kaikaku) that we often forget to address the issue of how to maintain our gains. Do you know iji? Perhaps you should.
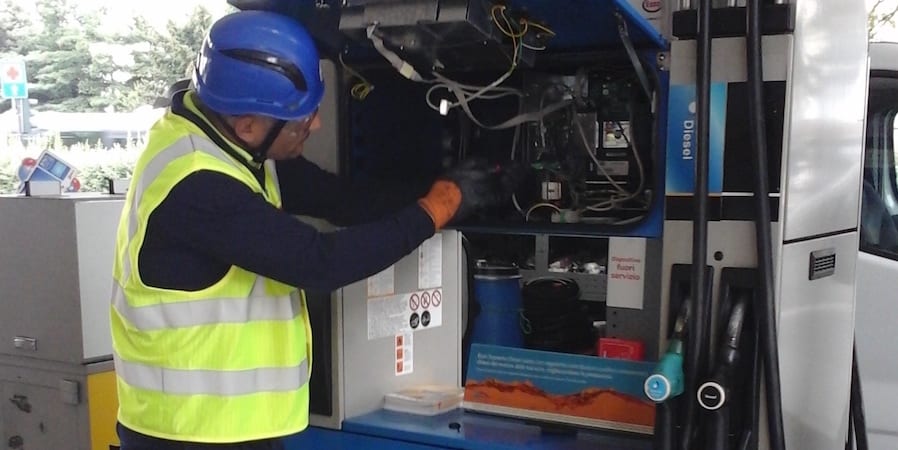
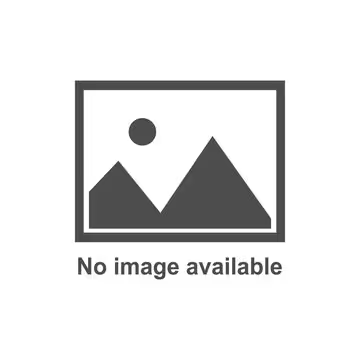
FEATURE – When market changes caused operational problems in their firm, two top managers decided to stick to lean thinking (and a set of specific practices) – learning to focus on what truly matters and letting their people embrace problem-solving.
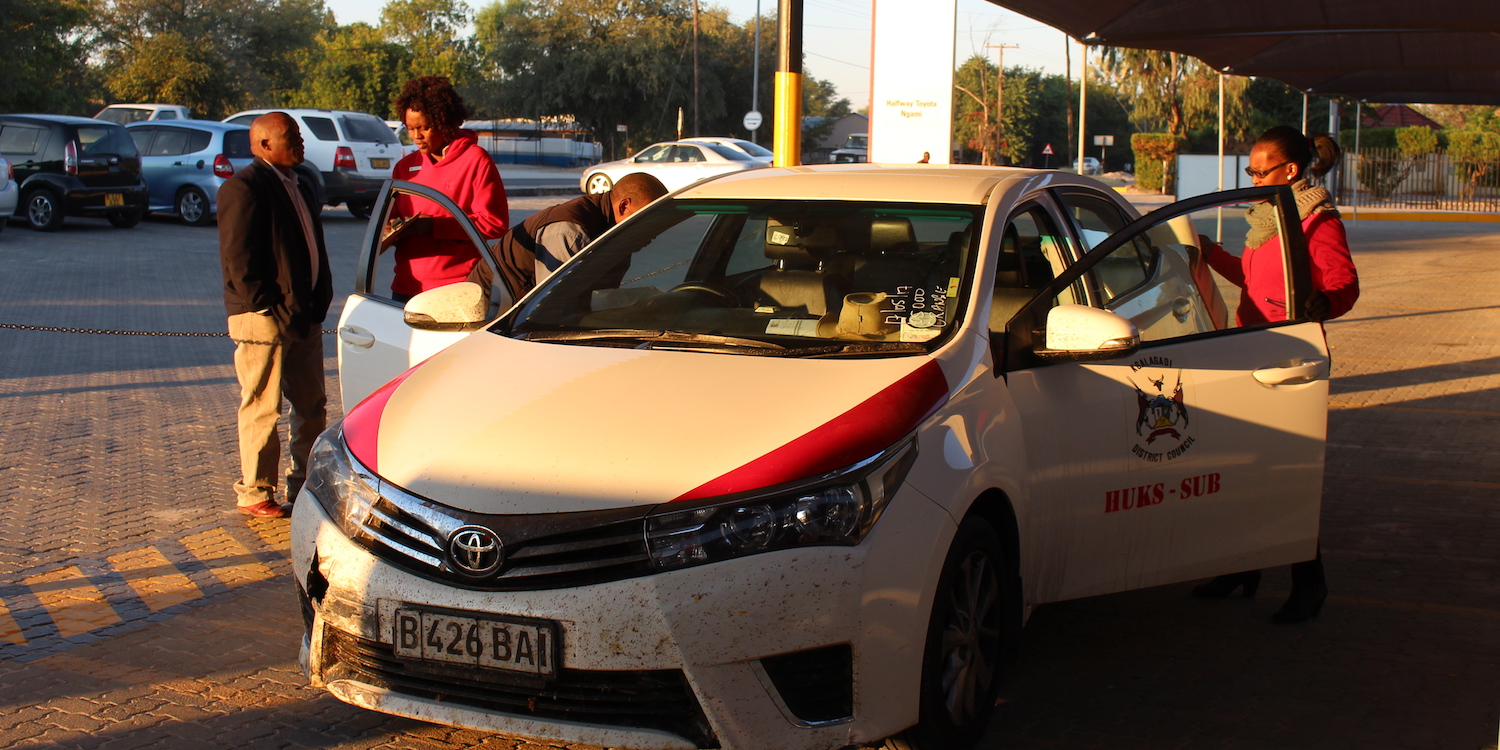
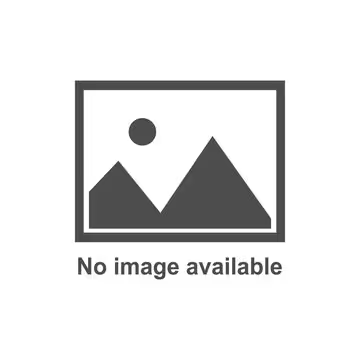
FEATURE – In this intimate, moving account, the author shares her journey of personal transformation that caused her mindset and her attitude towards employees to dramatically change.