
Lean in higher education: improving Macquarie University
CASE STUDY – An Australian university has been applying lean to streamline and improve its processes, discovering along the way how big a change the methodology can affect in the organization's culture.
Words: Valerie Runyan, Director, Business Process Improvement Initiative, Macquarie University – Sydney, Australia
Shortly after being appointed at Macquarie University in 2013, the Vice-Chancellor and President, Professor S Bruce Downton, conducted a consultative process across the university to establish a strategic plan. Focus groups, surveys and town halls were conducted to gather staff input.
A significant amount of feedback from these forums identified that the business processes at the university were clunky, time consuming and frustrating. Staff felt the business processes were limiting them in achieving not only their day-to-day work but also their faculties' priorities. There was a strong sentiment across the university that we needed to improve aspects of our support services in order to achieve our strategic goals. Transforming our processes was seen as an important way improve these services.
Once the plan was released, the Vice-Chancellor tasked the COO and the Deputy Vice-Chancellor for Students and Registrar to oversee the delivery of this key priority. They formed a reference group to investigate methodologies.
We wanted to create a model that developed trust, transparency, and accountability. We also wanted to entrust our people, those who carry out our processes on a daily basis, with the authority and responsibility to change their own work practices.
We looked at a number of business process improvement methodologies, but in the end we decided to turn to lean thinking because of its underpinning philosophy that people learn by doing.
Once we decided on the methodology, the Business Process Improvement Initiative was established with a staffing complement of one: me. I believed my first task was to communicate, communicate, communicate. I needed to get the message across to the university community that lean is designed to empower staff – they are the experts in the work – to drive change. This was a big task, as introducing changes in a university requires sign-off, consultation, committee approval and supervisor agreement. A long process.
Introducing lean and staying true to the philosophy would be a significant cultural change for Macquarie. Not only would we need to get buy-in from the management team to allow staff to make changes without their approval, we also needed to teach staff that they were empowered to make and implement change and that their supervisors supported them in this endeavor. This was a clear departure from the past.
I developed a six-month communication plan to ensure management and staff understood the path we would be taking, their roles in the transformation of the University, and the basic thinking behind lean.
I arranged meetings with the executives of the University – really anyone in a position of authority who would meet with me, from the Executive Deans to the Associate Deans, Directors and Managers – to explain what lean is all about, what their roles would be and what we hoped their people would contribute. I was adamant in telling management that once they gave us their nominees, those people would be empowered to make change. For lean to succeed, I knew we had to be clear – and that we needed management support and buy-in – from the start.
We also offered a university-wide session, introduced by the Vice-Chancellor and the DVC Students and Registrar, to explain the methodology and field any questions. Over 150 people attended.
LEADERSHIP AND RIEs
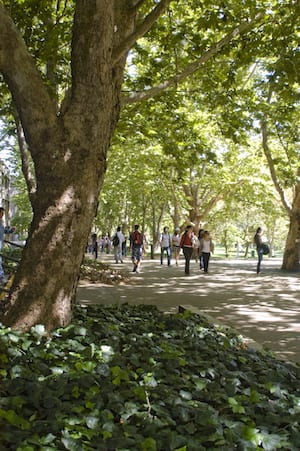
Communication paid off, creating interest in the lean methodology among staff – and a strong intention to participate in transforming processes. Suddenly, anyone could recommend a university-wide improvement that would directly impact the experience of students and the work of Macquarie staff. With each of these initiatives, we now contact the process owner and get a team of people together to define the problem. A Rapid Improvement Event (RIE) follows, attended by people from across the organization.
To avoid groupthink and to ensure management buy-in, we ask senior managers to identify delegates that will implement change on their behalf. However, we have them participate in the RIEs in person, to ask questions, give suggestions, and answer questions. They open every RIE we facilitate by thanking the participants for attending and giving up their time to improve a university-wide process, and by stressing that they have management support to implement change. This demonstrates to our people that things have changed at Macquarie and that they now have the permission (in fact, they are encouraged) to drive change autonomously. No excuses not to streamline processes!
An example of one of our early RIEs was the improvement of the process for recruiting staff: we had found one of the main issues to be that new staff members were not given an email account until their first day of employment at Macquarie. This caused delays in access to a computer, systems, calendars and negatively impacted the overall productivity of the new employee for at least a week. There had always been some reluctance to give an email address to someone before their start date (even though no one knew why), until – once the lean improvement began – the group invited the COO to join the RIE and asked him if he knew of any risks the university would incur with the early provision of an email address. He said no and agreed with the project team they should implement the change as soon as possible.
This alone was a strong catalyst for the acceptance of lean at Macquarie, because the staff recruitment project team and the teams to follow realized they were really empowered to implement change.
We also introduced an escalation process to ensure that any roadblocks in trying to implement a new process would be flagged and brought to my attention (I also had the support of the Reference Group, the COO, the DVC Students and Registrar and senior management). Interestingly, however, I never needed to escalate: knowing they had an escalation process to rely on and the support of the senior management was enough for the project group to feel empowered to remove the problem on their own.
Throughout the implementation of the new process, the project group communicates with everyone involved through presentations, fortnightly updates and the development of electronic information sources, such as Wikis. Although it is the project group's responsibility to ensure the new process is implemented, by including the university community in its communication the responsibility of the implementation is shared with all stakeholders.
I believe a key to the success of lean at Macquarie is the support we give business owner, to help their suggested change succeed. We work with them to ensure they meet their deadlines to implement the new process on time, and we also agree on a post-implementation review date so we can report on the success of the new process and identify further opportunities for improvement. We do this by gathering data, conducting surveys and focus groups, and consolidating this information into a report for the senior executive meeting, all on behalf of the business owner. We see our job as working behind the scenes for our process owners; the success belongs to them, and our job is to make sure they get there. By submitting the report to the senior executives under the business process owners signature, we make sure they own the outcome and any future improvements.
DEVELOPING PEOPLE AND LOOKING AHEAD
We have been working with lean for two and a half years, facilitating its spread across the university through our small (only three of us) but very busy Lean Team. We have sent out staff into sections of the university as trained facilitators and consider them as part of our team. Although through an informal arrangement, they are invited to our meetings and asked to contribute to the team's work. In addition, we ask them to assist us in facilitating Macquarie-wide RIEs to keep up their skills level.
We have also developed a training program that we deliver through the Human Resources Professional development program for employees of Macquarie University. So far, we have had over 1,000 people (staff as well as students) participating in business process improvements for the university. We are also in the process of delivering training to staff to help them to use lean skills in their every-day work. In addition, we are strategically sending facilitators out to different faculties and departments to ensure the expertise exists in different business units rather than only centrally.
Lean has exceeded our expectations. While the primary purpose of this initiative has been to improve business processes, we have found that an additional benefit – and an exciting one – is the institutional collaboration and cultural change.
Although unquantifiable, this benefit is validated by the plethora of positive comments made by participants involved in our lean projects. They told us, for example, that for the first time they realize change is possible, that they are struck by how lean helped the teams deconstruct their jobs and build processes that work, and that they see great benefits stemming from increased collaboration with their colleagues.
We like to think that lean is becoming ingrained in the university culture, as we continue our work to make it the way we do things around here.
Meet Lean HE
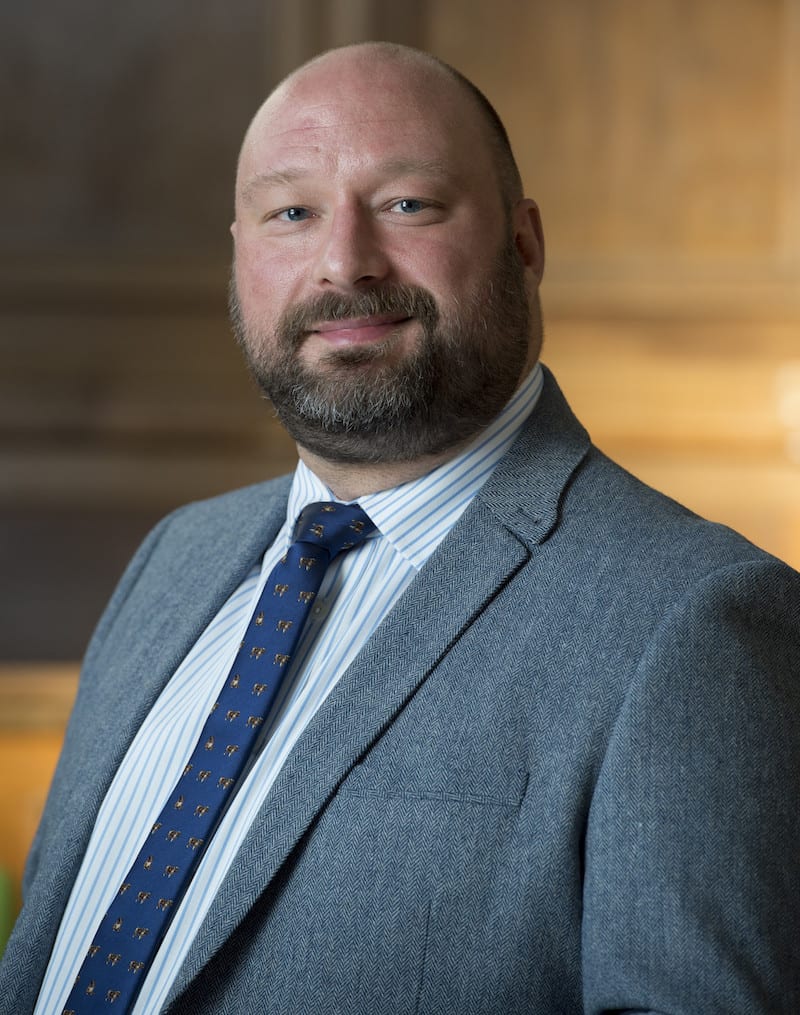
by Steve Yorkstone, Chairman of Lean HE's global steering group
Universities are crucial in answering the challenging questions our society faces – scientific developments are normally driven by university students and researchers. Yet, they are overburdened with administrative processes. The opportunities for improvement are rife, and just like current teaching methods and research processes are radically changing to be fit for the future, so there are attempts to transform the way universities operate.
Indeed, there is a growing number of passionate and enthusiastic voices advocating lean as a way to continually improve universities for the benefit of all. The work and expansion of Lean HE are testament to this.
Lean HE is a rapidly growing international community of practice for staff within universities that are applying lean. It brings together practitioners to share their knowledge and learn techniques to continually improve their work. In the four years since its founding, Lean HE has launched an established international conference series, an online network and local events around the world.
In 2006, some UK universities began to experiment with lean. To share their learnings, Cardiff University hosted a one-day event in 2008, and Scotland's University of St Andrews followed in 2010. Soon, many universities were hosting conferences every year, and their burgeoning audience of UK practitioners began to collaborate and consider how lean can be applied to higher education organizations.
By 2013, these events were drawing a handful of administrators and academics who had applied lean in higher education and believed that the content of the conferences could be further improved, to add much more value to higher education. Over a social beverage (or two), this group realized that if they wanted to release this value they had to do it themselves. That's how Lean HE began.
We are organized in a lean way, committed as we are to always remembering our purpose: supporting the transformative power of universities through their students and research (while acknowledging that many lean applications within the university context focus on reducing administrative burden).
Lean HE takes a practical approach: turn up, bring something to share, come prepared to learn and share hosting responsibilities. We like to think differently about organization and do away with budgets and formal membership lists, which do not add value but do add administration burden.
Our group quickly discovered a world-wide community of lean practitioners within higher education with whom to share, and within its first year, its organizing body had representation in different parts of the world, from the Netherlands to Canada.
Last year, Lean HE launched continental divisions in the Americas, Europe and Australasia, with each division supporting a region-specific activity program. Our LinkedIn group has almost 2,000 members and our most recent international conference in Stirling, Scotland, attracted 150 delegates from Finland, Poland, Norway, the UK, North America, Australia and the Middle East.
We know, however, that real success is measured by results: the delegates who attended the conferences have in turn formed local networks in the UK, Northern Europe, Eastern Europe and the Baltic states, which has resulted in countless improvements in many universities.
Macquarie University will host the next international Lean HE conference, Implementing, Measuring and Sustaining Change, on 1–3 November 2017 in Sydney, Australia. If you or someone you know is working to implement change within a university, we would love to see you there.
THE AUTHOR
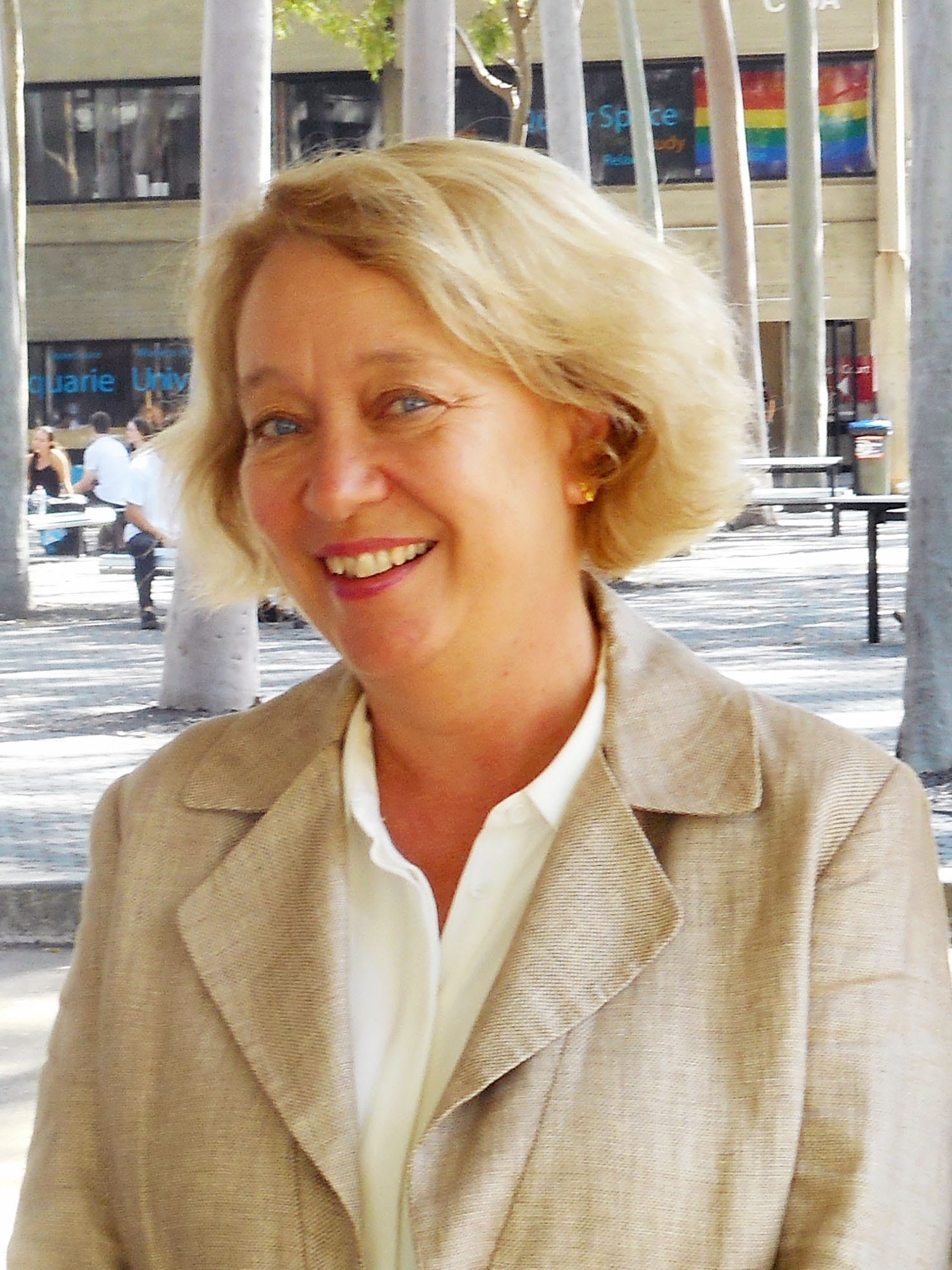
Read more
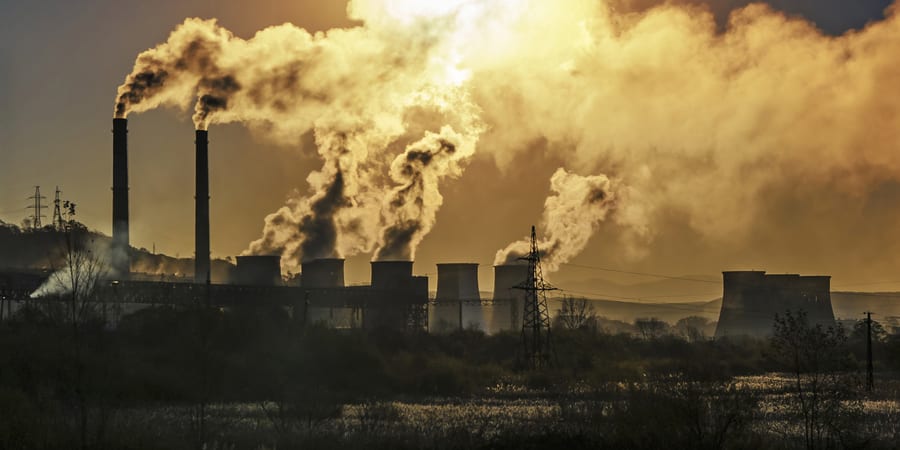
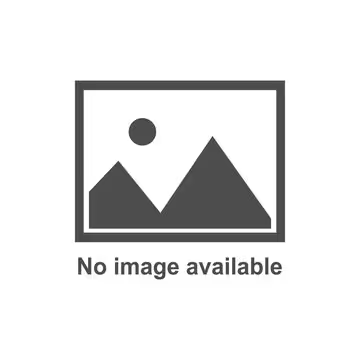
WOMACK'S YOKOTEN – Last month nations signed a greenhouse gas emissions deal – on paper, an insurance policy against climate change. But if action is to follow promises, the cost of the insurance premium, as perceived by voters and governments, must be lowered. Lean thinking can help.
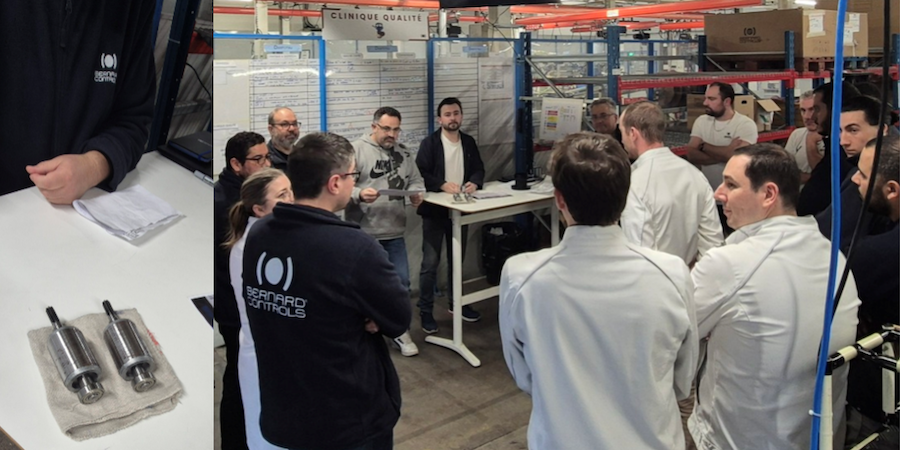
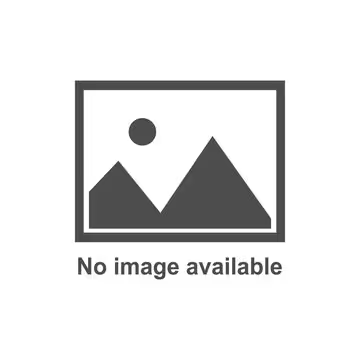
CASE STUDY – Lean Thinking helped Bernard Controls Europe improve efficiency, reduce lead times, and enhance quality, fostering resilience in the post-pandemic industrial landscape.
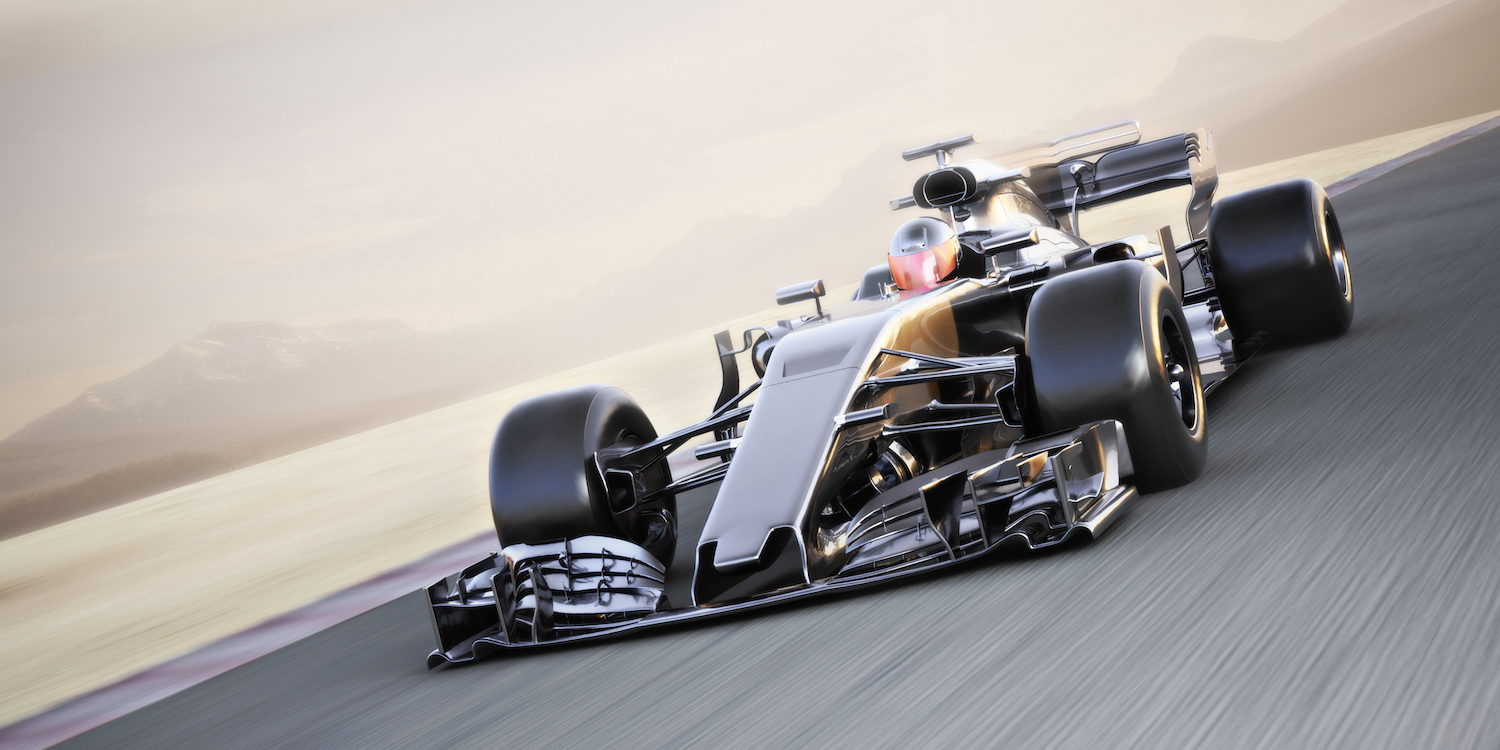
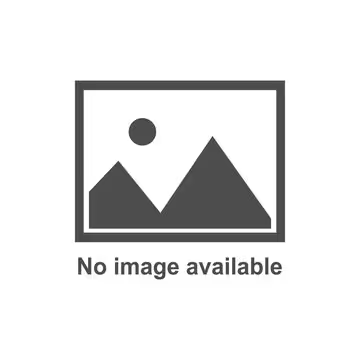
FEATURE – In part 2 of his article, the author unveils an improved process that allows this Hungarian company to replace machine parts with minimal production downtime.
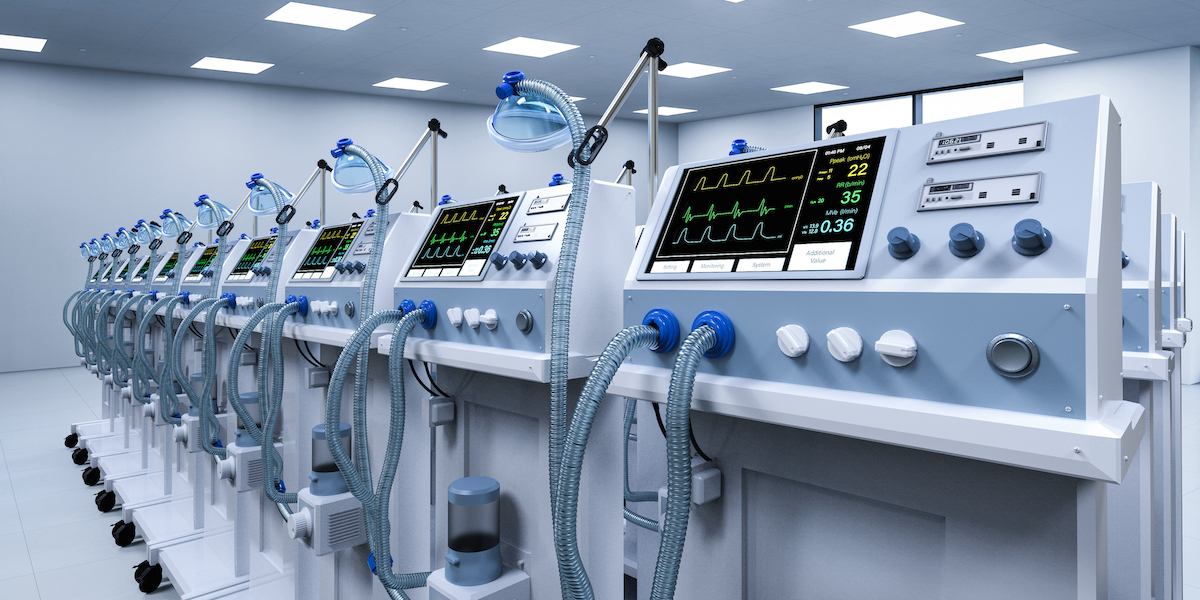
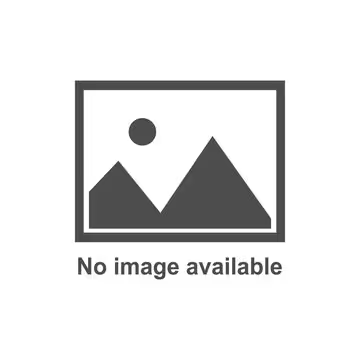
FEATURE – Back on the road after two years, the author reflects on how lean organizations have performed during the pandemic and addresses age-old misunderstandings about Just-in-Time.