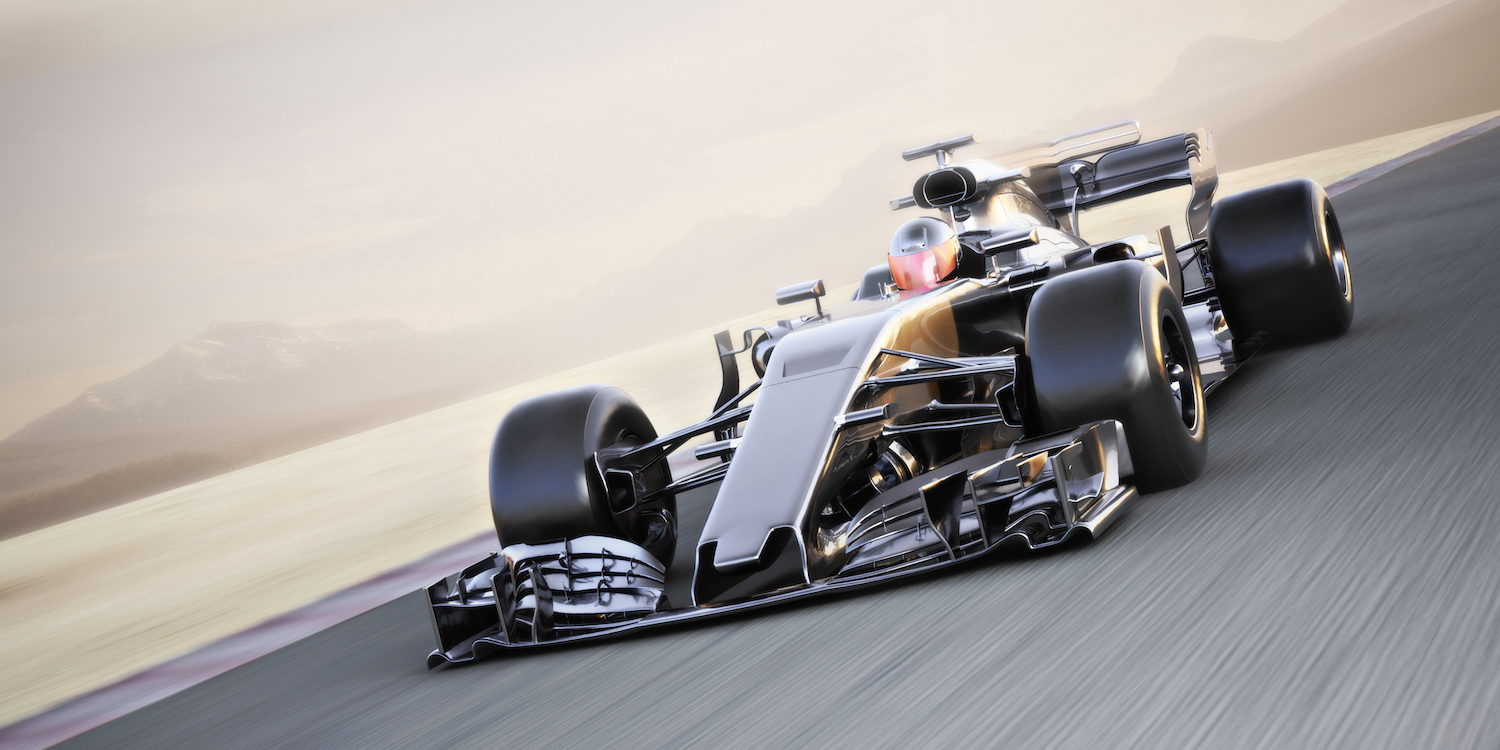
F1 cars... in the factory - Part 2
FEATURE – In part 2 of his article, the author unveils an improved process that allows this Hungarian company to replace machine parts with minimal production downtime.
Words: Dénes Demeter
Originally published by Lean Enterprise Institute Hungary here
Maintenance and repairs are some of the main causes of downtime in production processes. In our client company, which I wrote about in Part 1, machines could be down for 15 to 20 minutes during the replacement of wear parts, even though the replacement itself only took 3 to 5 minutes (depending on the size).
OBSERVATIONS
To understand what happened, we need to break down the problem into smaller, observable parts. So, let’s determine what makes up this 15- to 20-minute period.
During our observations, we found that the process could be divided into the following stages:
1. Detection – notifying the technician – technician's arrival.
2. Removing the part – obtaining the replacement part.
3. Replacing the part – installing – starting the machine.
In the first stage, we observed that the process begins when the machine reaches the maximum step count and stops. Moreover, it signals about two hours before stopping that it is approaching this point. We also learned that the policy mandates replacement at this point in time, meaning the part in question can be replaced between 30,000 and 33,000 steps. After reaching the latter, the machine stops producing.
After the machine stops, the operator notifies the technical team and, depending on their workload, the technician arrives to address the issue. By this time, the machine has been idle for 4-8 minutes.
It's evident that the largest loss in this stage is due to waiting, caused by the technician not being present when the machine stops. This happens because the technicians do not receive timely information.
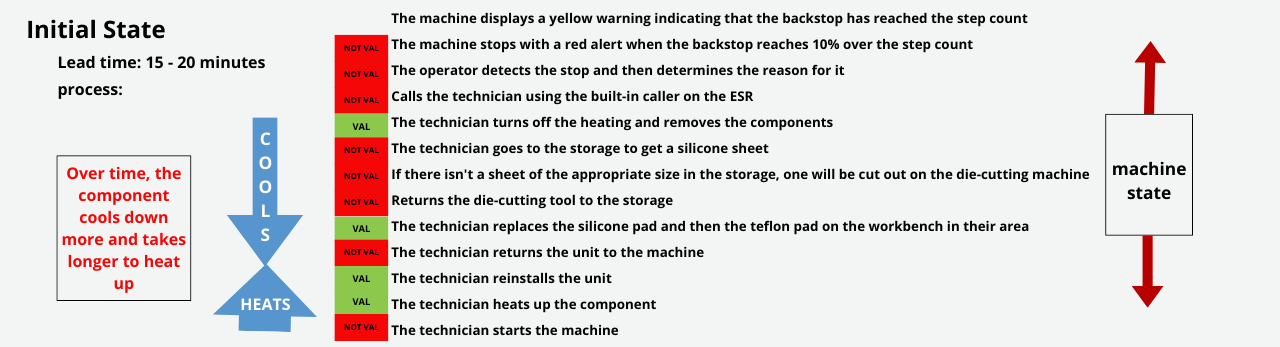
In the second stage, we observed that the technician removes the affected unit, walks to the storage area for replacement parts, where ideally, they find the precisely sized part needed. If not, they go to another station to cut the required size. Walking and searching for parts after removal takes 2 minutes, and cutting a new part takes another 5 minutes.
In this stage, the losses are due to movement and waiting. The reason for the movement was found in the third stage and, for missing parts, we saw that restocking always happened internally, meaning when the machine was already down.
In the third stage, the technician takes the obtained replacement part and the removed unit to their station, where they replace the part using a special fixture, then return it to the machine and reinstall it. The process ends with restarting the machine. Walking time in this stage is 1-2 minutes, while part replacement takes 3-5 minutes.
COUNTERMEASURES
The waiting loss observed in the first stage was eliminated in two steps.
Firstly, at the beginning of each shift, a designated technician walked around the entire machine park to collect information on which machines would require replacement during the shift and scheduled these replacements accordingly. In case of simultaneous needs, they requested assistance to perform the replacements in parallel.
The second, currently applied process is much more refined. Nowadays, all technicians have a PDA used for scheduling their tasks. The first signal, at 30,000 steps, is sent to the PDA of the technician responsible for the machine, instructing them to replace the part within 2 hours. By doing this, the time lost throughout the entire first stage is eliminated.
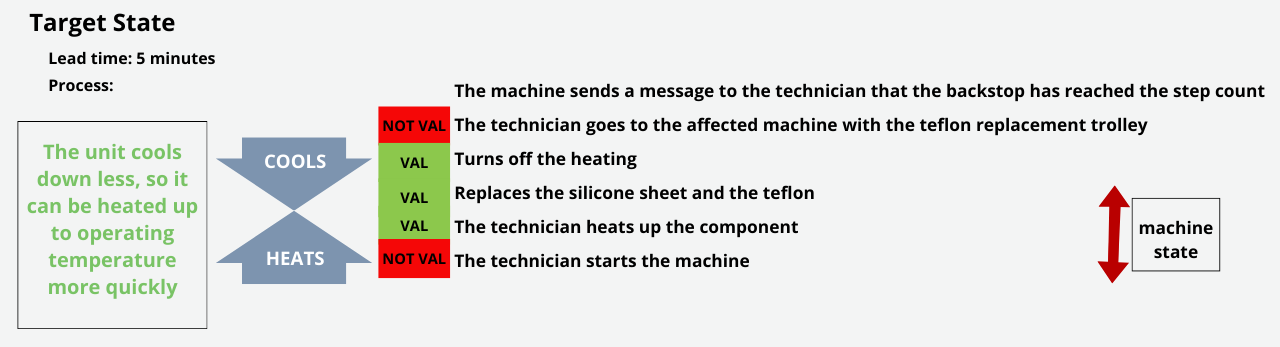
To eliminate the waiting caused by internal restocking observed in the second stage, we introduced a parts kanban system, which is replenished externally, without machine downtime.
The movement losses characteristic of the second and third stages were eliminated by placing the necessary fixture on a cart, allowing the part replacement to be done right beside the machine, at the point of removal.
And where are the pre-cut replacement parts? In the drawers of the cart, where the kanban is located, ensuring all necessary elements are at hand during the part replacement.
RESULT
As a result of these measures, technicians receive timely information, making the process plannable and executable before the machines stop. The cart allows replacements to occur on-site, next to the machine units, ensuring the necessary replacement part is always available. Consequently, instead of the initial 15 minutes, wear part replacement now occurs with a maximum of 5 minutes of machine downtime.
It's important to highlight that establishing the new process and the necessary technical conditions is not the end. Initially, less than half of the replacements met the new time standard. Often, for example, technicians did not arrive on time despite the signal, or they brought the unit to the cart – as they used to do to the technician's table – instead of the other way around. Therefore, involving workers, ensuring understanding, and developing skills are all fundamental actions to take. Implementing the new process and maintaining results was challenging for the leaders, but with the right goals and management routines, most replacements now meet the new lead-time.
For more content from Hungary, join us at the Lean Global Connection 2024. Register for free here
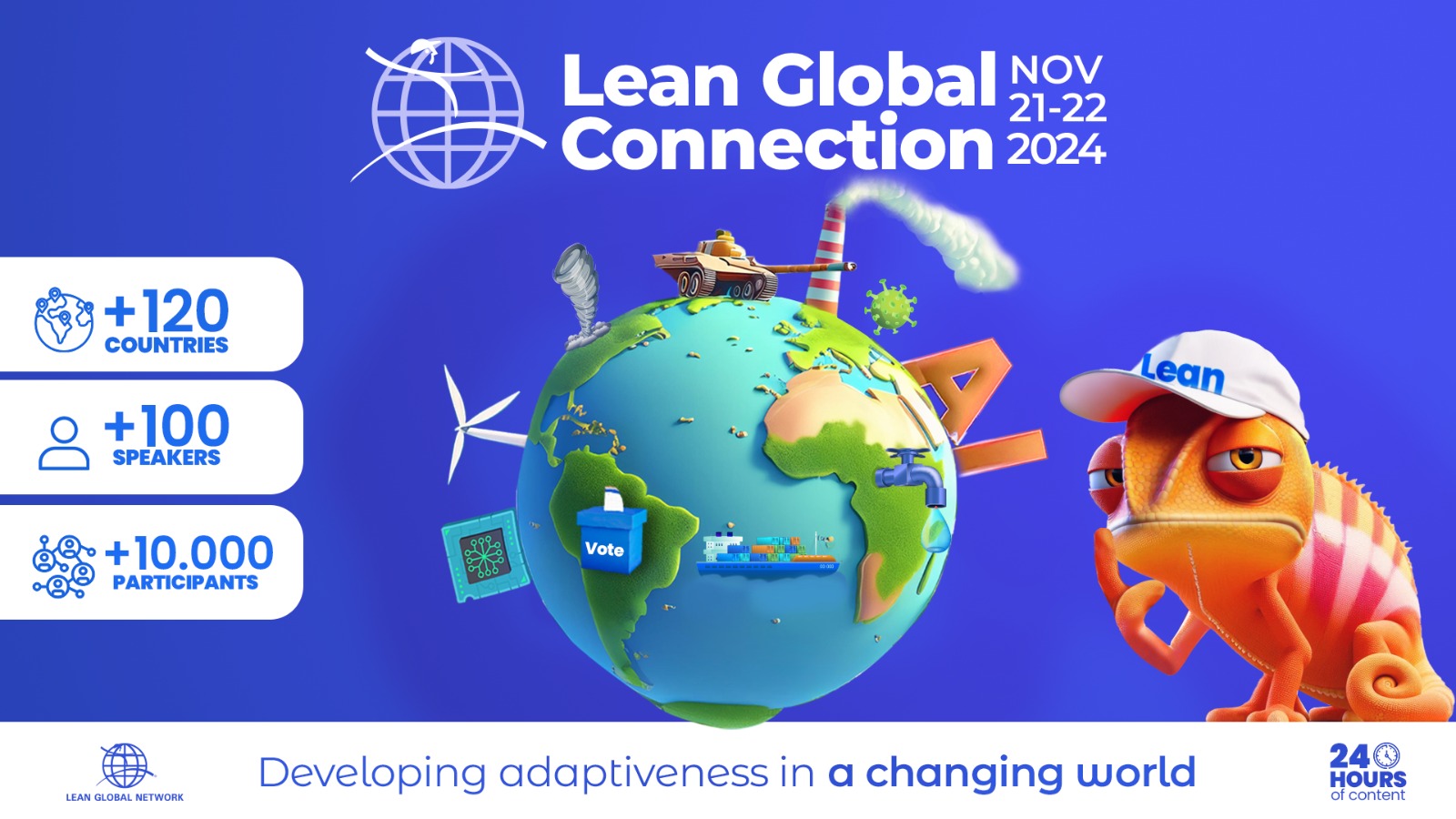
THE AUTHOR
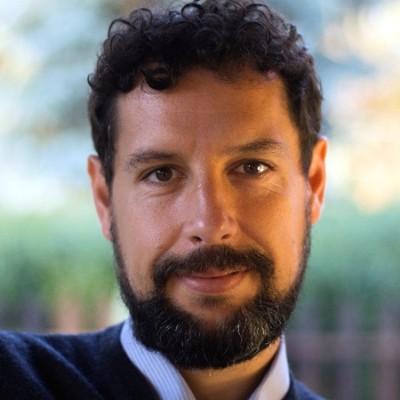
Read more
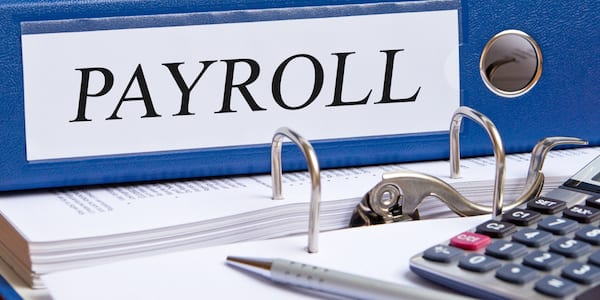
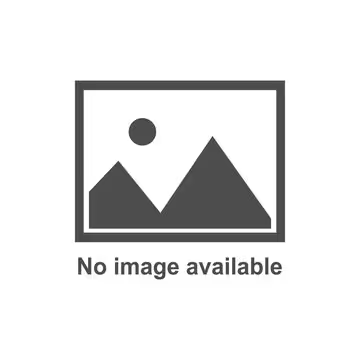
COLUMN – Finance is a critical function within a firm. Yet, lean thinking seems to struggle to make progress in this field. Following a workshop with Nick Katko, the author of this article sees an opportunity.
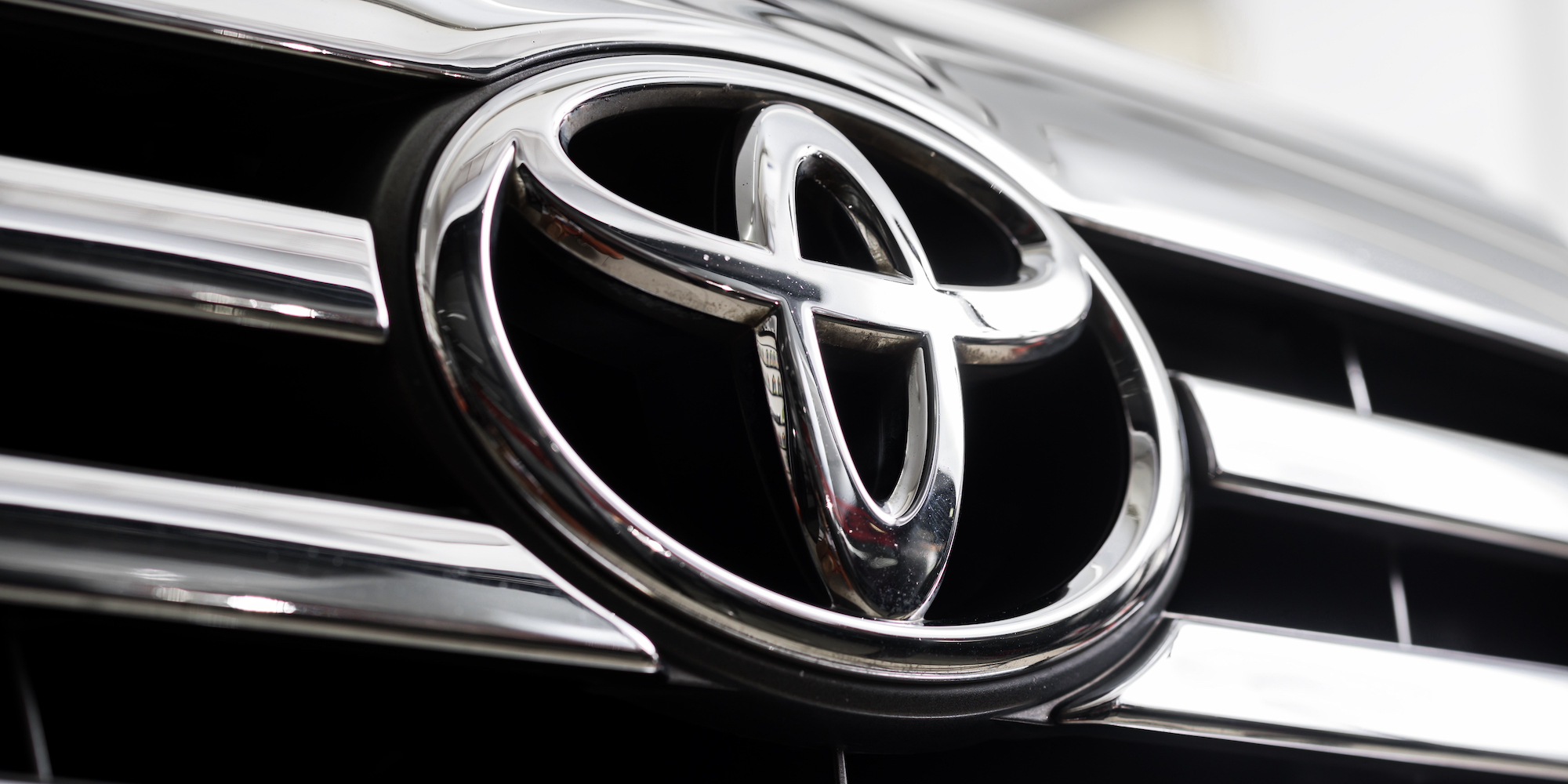
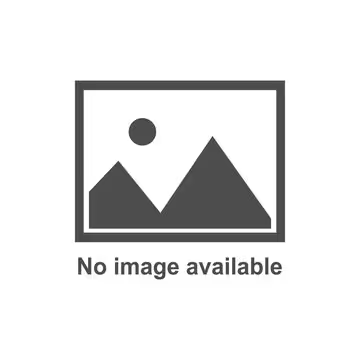
ROUND-UP – Our editor looks back at the most insightful articles Planet Lean has published on the most talked-about company in the lean world. Here are eight key lessons from Toyota, straight from our archives.
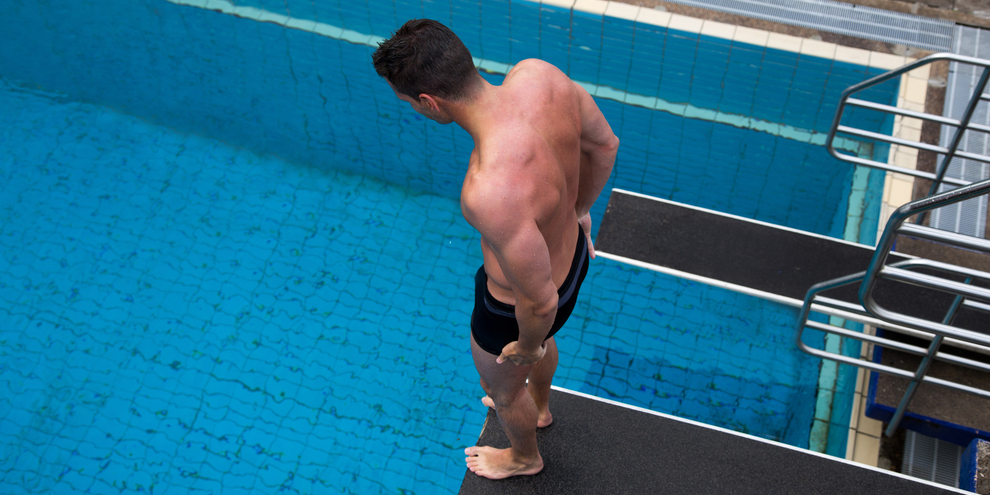
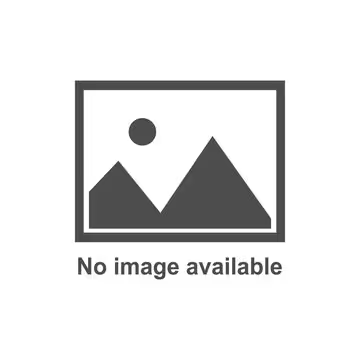
FEATURE – To wholeheartedly embrace lean means to accept changes in our hearts and minds. Understanding this means to finally grasp the reason why lean is only truly taken up by few.
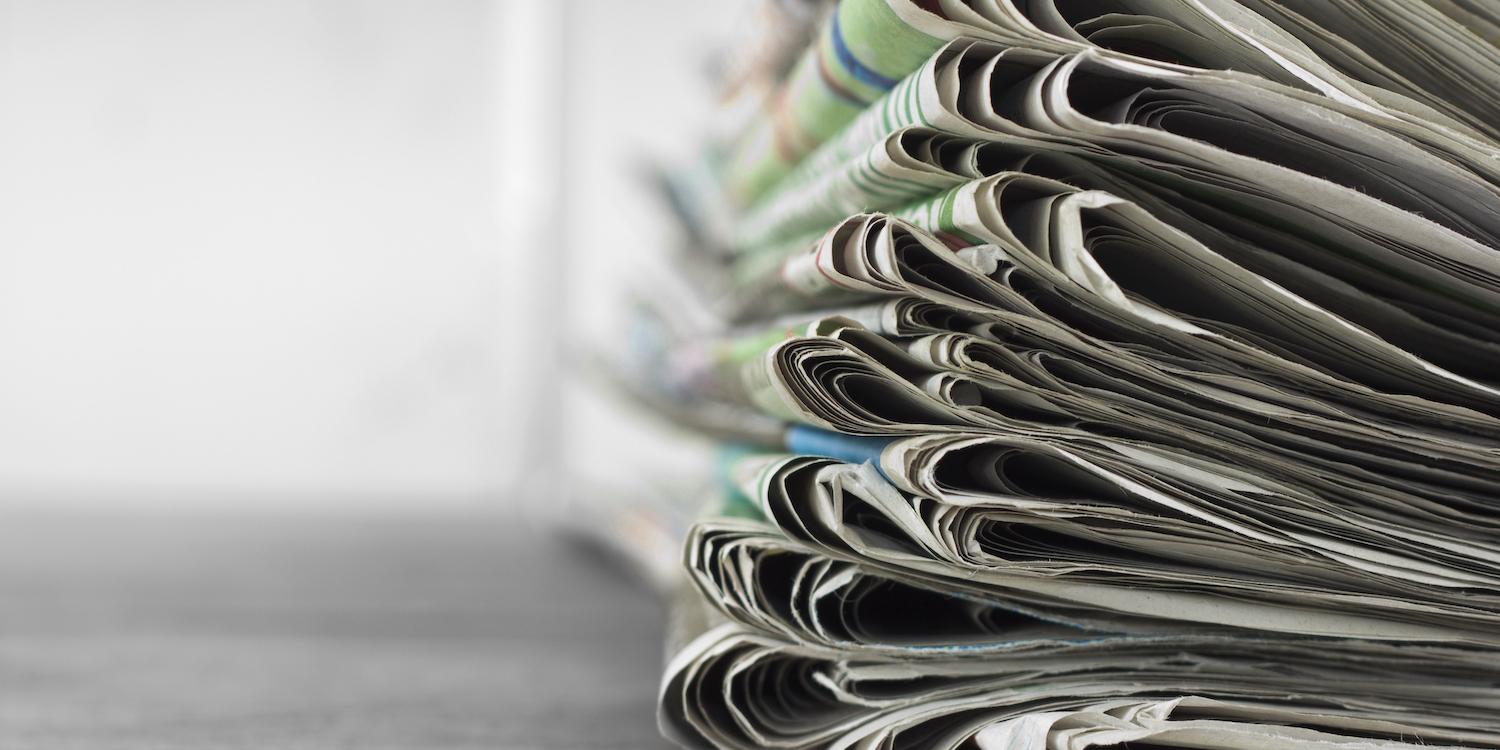
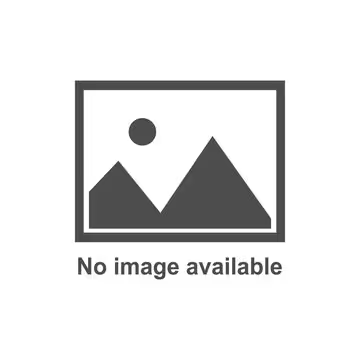
ROUND-UP – In his annual review of the best content we published, our editor looks back at 2022 and what this year was like for the Lean Community.
Read more
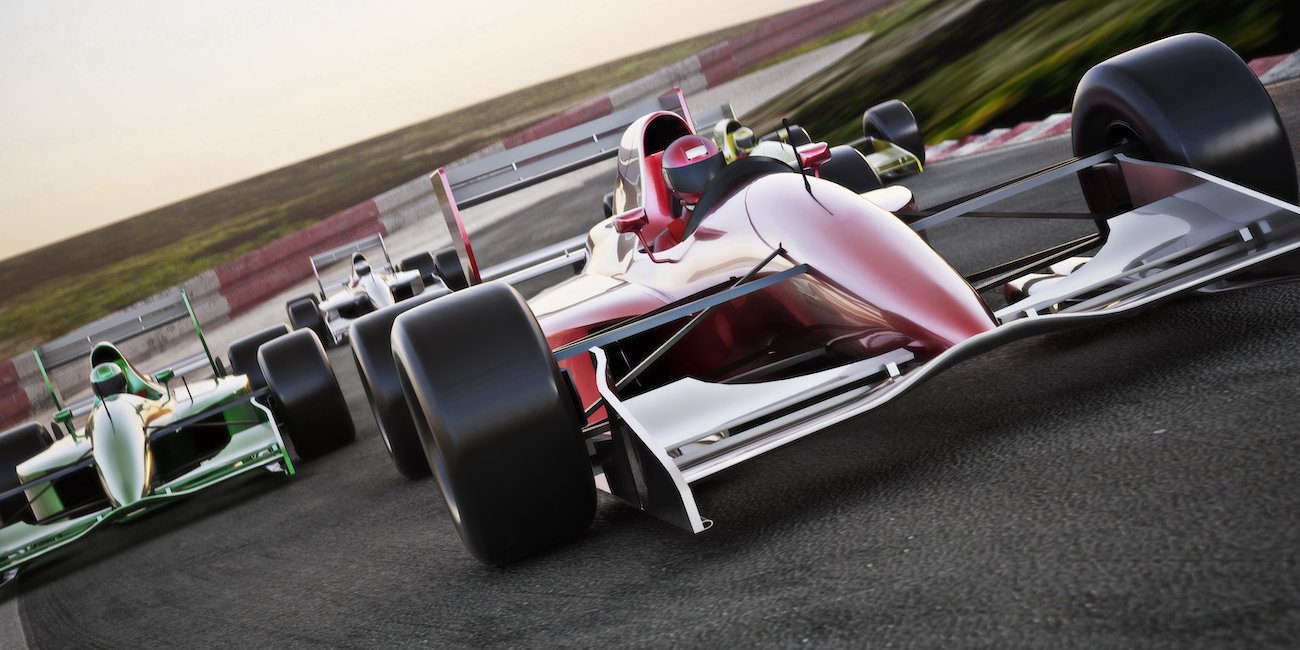
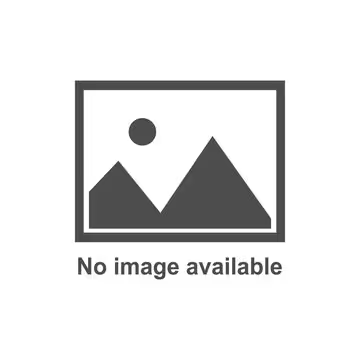
FEATURE – A situation that would be unthinkable in a sports context is an every-day occurrence in many of our organizations. Should we change our way of thinking about our machinery?
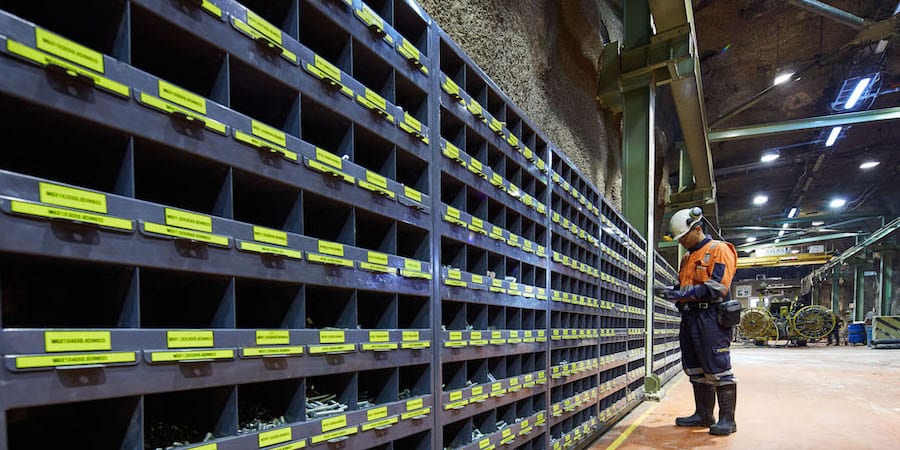
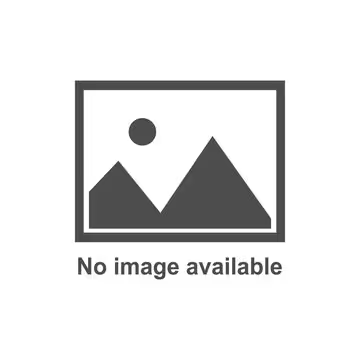
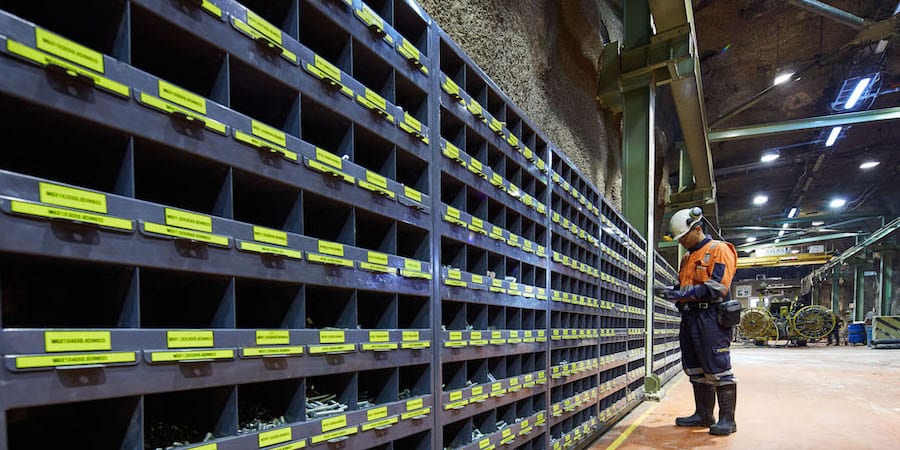
CASE STUDY – Over the past four years, by developing its kaizen capabilities and crafting a better approach to maintenance, a Turkish gold mine has significantly reduced its extraction costs.
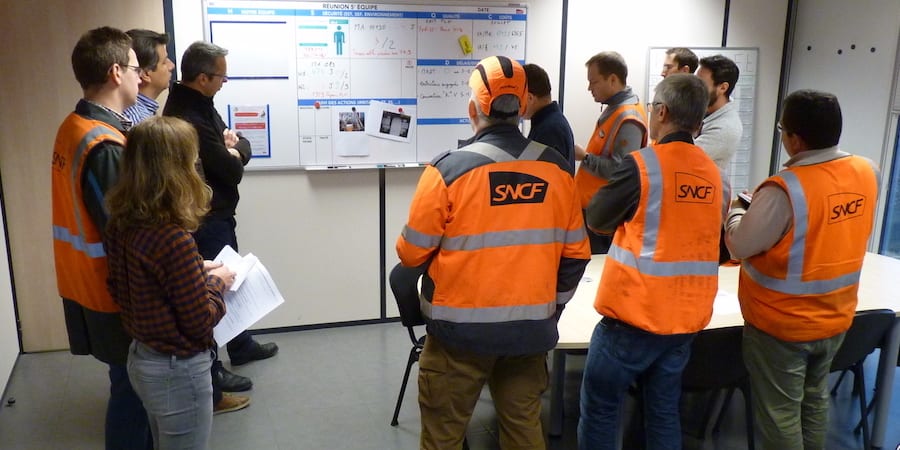
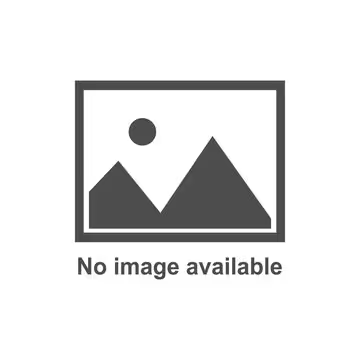
NOTES FROM THE GEMBA - We follow the author on a visit to a train maintenance center in France. Through practical examples and pictures from the gemba, she explains how the center is transforming itself.

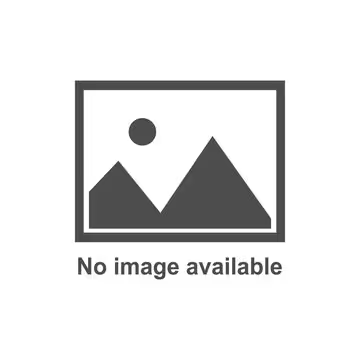
FEATURE – The problems agricultural businesses encounter every day can be solved using simple concepts of lean maintenance, resulting in considerable gains.