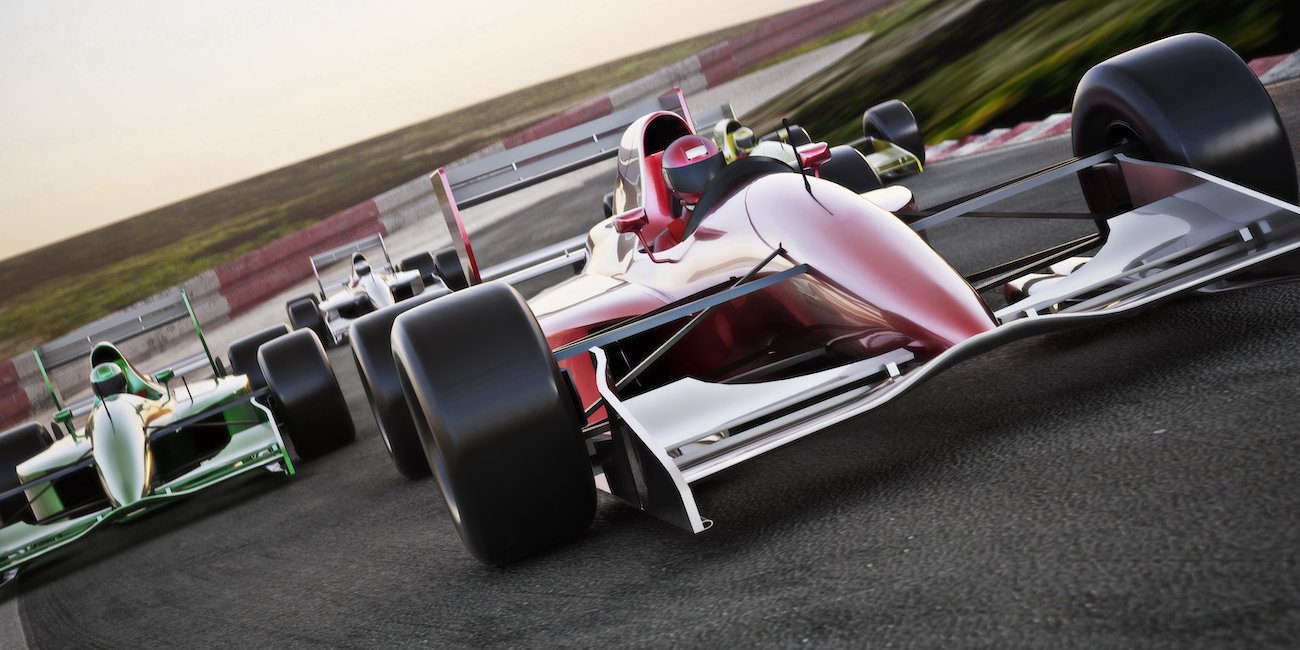
F1 cars... in the factory!
FEATURE – A situation that would be unthinkable in a sports context is an every-day occurrence in many of our organizations. Should we change our way of thinking about our machinery?
Words: Dénes Demeter
Imagine this: a Formula 1 car is pulling into the pit lane for a tire change, and nobody is there waiting. The mechanics are all busy with something else. Unthinkable, isn't it? The media would be all over this story and, undoubtedly, the team would work tirelessly to ensure something like this never happens again.
In a manufacturing environment, we can view our machines as F1 cars. It's in our best interest to "keep them competitive" with the appropriate performance level. That means maximizing value production during most of the available time while minimizing downtime and breakdowns.
Unfortunately, in several organizations, we've observed situations like the one described above persisting for years, despite the fact that with a little bit of attention and minor reorganization, significant increases in machine uptime and output could be achieved.
WHAT'S THE PROBLEM?
Let's illustrate this with a concrete example from one of our partners. In their machines, there are units in which certain components need to be replaced after a certain number of steps – much like the wheels of a racing car. Two step-values are set in the machines: reaching the lower value doesn't stop the machine but signals the need for replacement, while reaching the higher number does stop it. Thus, the system can predict imminent machine downtime.
OBSERVATIONS
For a long time, component replacements were done when the machine reached the higher step count and stopped (in F1 terms, when the car pulled into the pit lane). Typically, the operator noticed this and called the technical team. After a while, a technician arrived and asked what happened. The operator explained that a component replacement was needed. The technician then went to get the necessary tools, removed the unit, and took it to the workshop. In the worst-case scenario, if the appropriate component size weren’t in stock, the technical team would have to cut one to size, replace it, and then return to reassemble the unit. Only then could the machine return to production.
The exact reasons for this won't be detailed here, but here are some examples:
• Most operators thought this was the standard procedure.
• Technicians also believed so.
• Reactive troubleshooting was the prevailing mindset ("I'll fix it when it stops").
• Performance tracking didn't reveal this loss, and a certain level of lost daily output was generally accepted.
• “This is how we have always done it.”
In an F1 context, this would look like this: the tires wear out and the car signals the need for replacement. The driver keeps going until the tires give out. When the tires are on the brink of failure, the car automatically slows down, forcing the driver into pit. They pull into the empty pit lane and signal the mechanics. One of them finishes up what they were doing, then walks over to the driver to find out what's wrong. The driver indicates that they need a tire change. The mechanic fetches the wheel nut wrench, removes the tire, takes it to the workshop to change the tire, then brings it back and mounts it on the car.
Isn't it painful to read this example in this context, as unrealistic as it may sound? Yet, this is exactly what happens in the majority of manufacturing processes out there!
RESULT
At our partner organization, the replacement process now follows principles similar to F1 tire changes. While their record isn't two seconds, they can replace components in the shortest time possible, causing the least machine downtime, given their current knowledge.
To understand what the process looks like, what steps the company went through to establish it, and what challenges maintaining the process poses, you can attend the Coloplast breakout session at the upcoming 11th International Lean Summit in Budapest.
This article is also available in Hungarian here.
THE AUTHOR
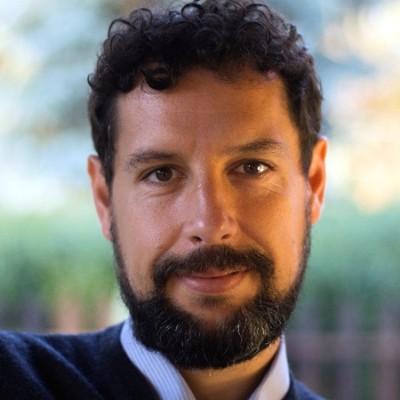
Read more
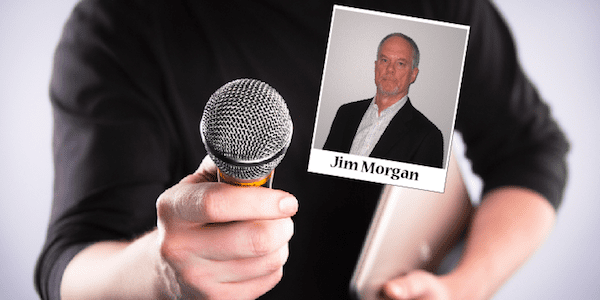
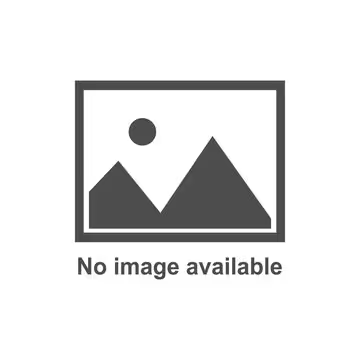
INTERVIEW - Jim Morgan looks back at his years at Ford Motor Company and talks about the challenges and opportunities of applying lean management ideas to new product development .
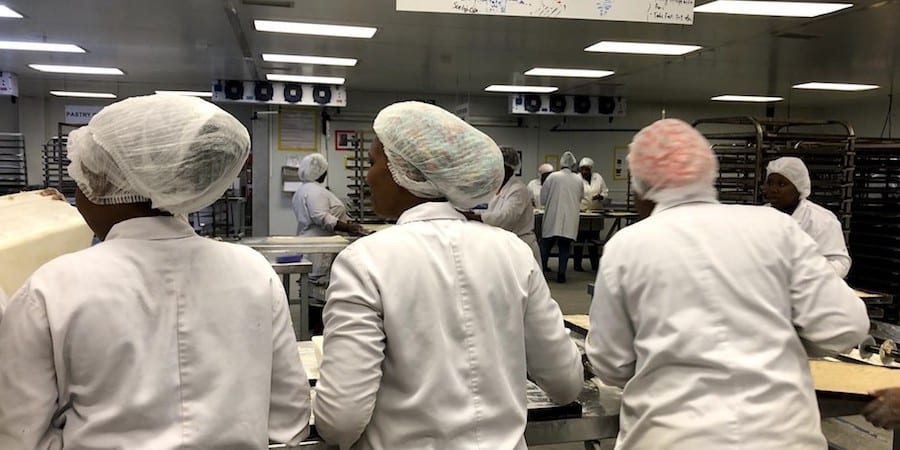
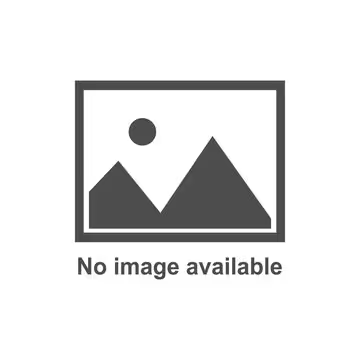
FEATURE – How reading lean books empowered people and transformed the managerial culture at an industrial bakery in the Western Cape Winelands in South Africa.
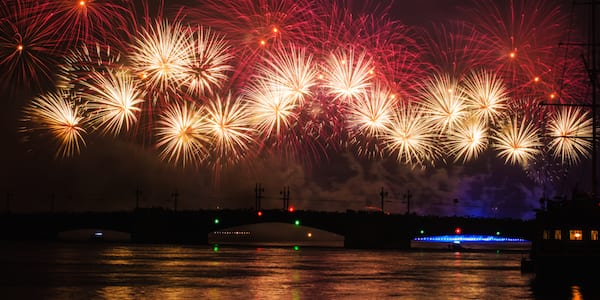
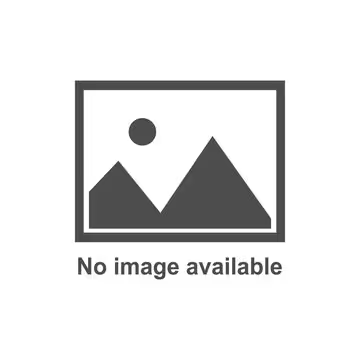
FEATURE - Planet Lean launched exactly one year ago. Editor Roberto Priolo offers some reflections and a round-up of the most popular articles we have published to date.

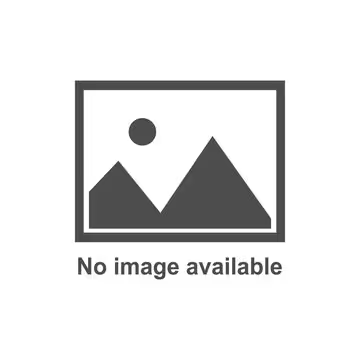
FEATURE – The conflict unfolding in Ukraine acts as a tragic reminder of the threat posed by despotic, unapproachable, and paranoid leaders, says Sharon Visser.
Read more
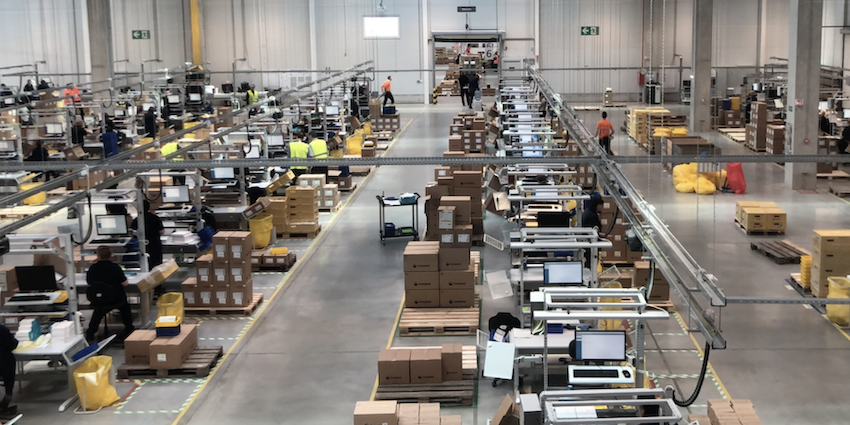
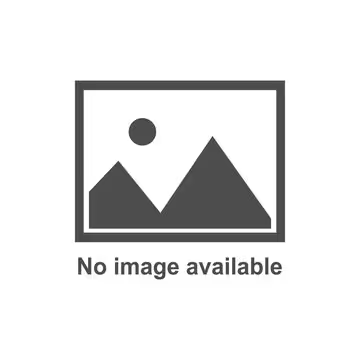
VIDEO - In February, a group of Lean Global Network coaches visited Coloplast's Parts Distribution Center in Hungary to help the local team improve the internal lead-time across the facility.
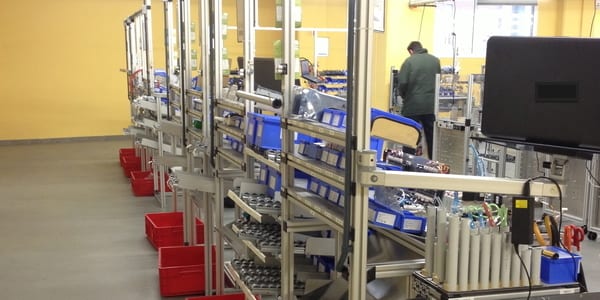
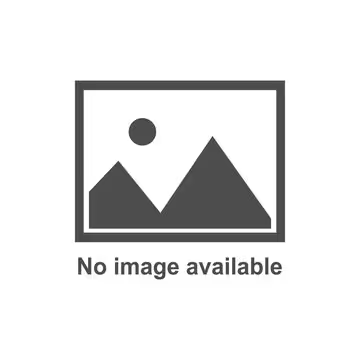
FEATURE - It took a Spanish clinical diagnostics instruments manufacturer the introduction of a new product to realize how an old-fashioned system and management style were preventing the company from thriving.
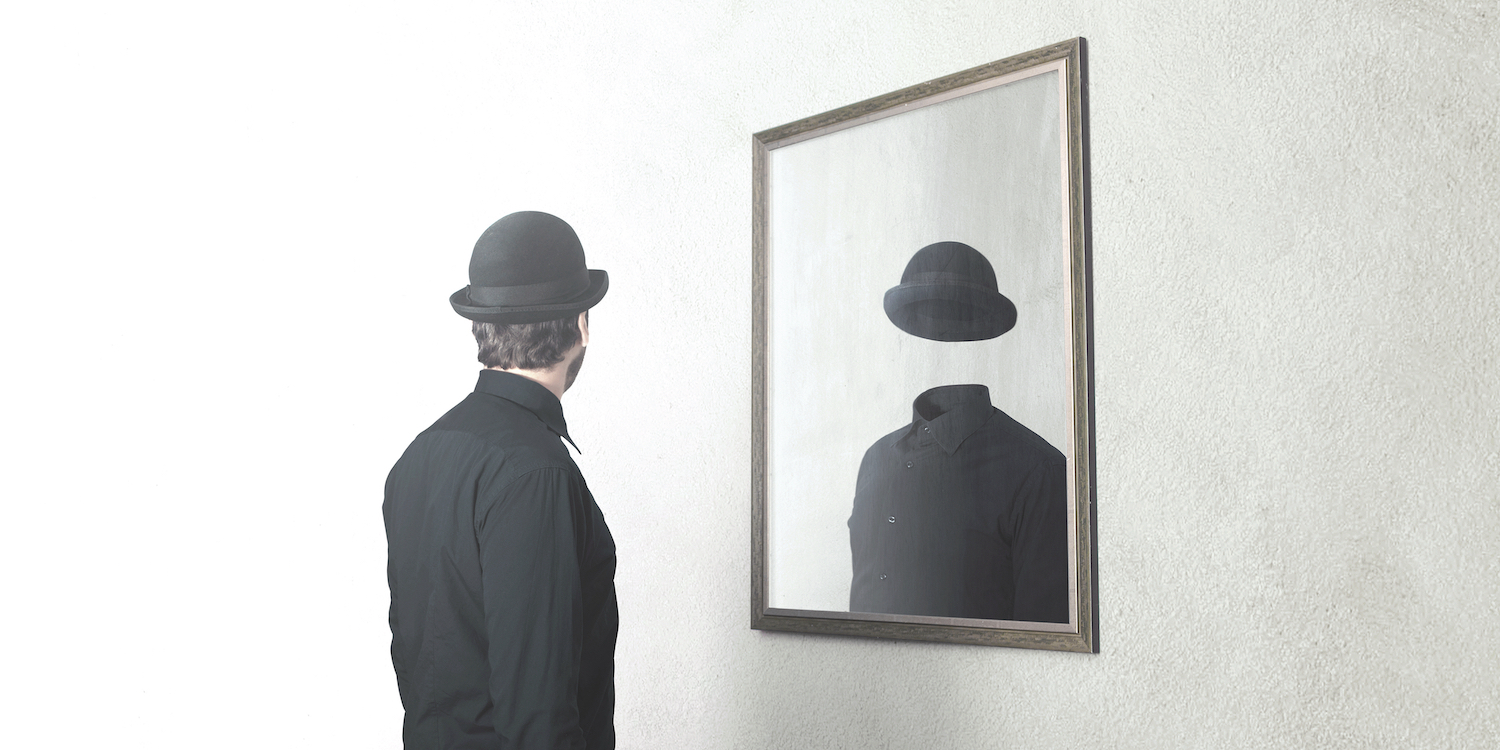
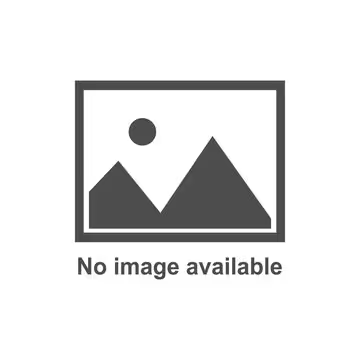
FEATURE – The gemba tells us more than we think. The authors discuss what we need to look at during our walks to understand the impact of non-manufacturing functions on the overall process.
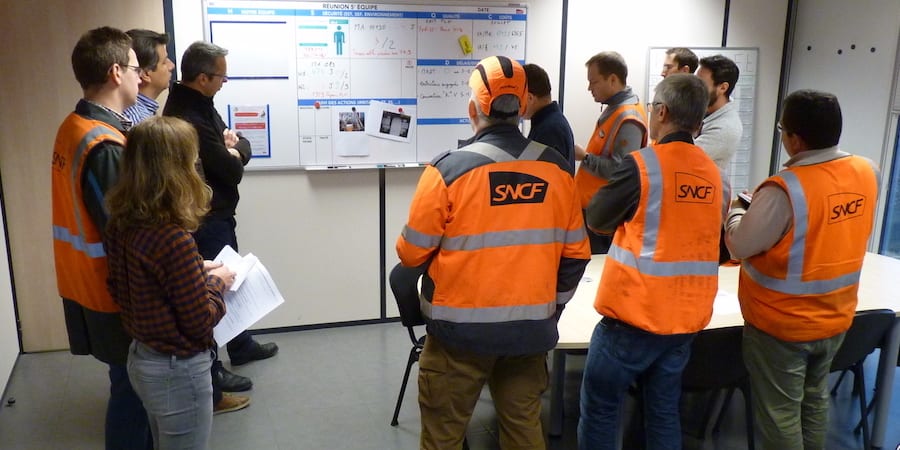
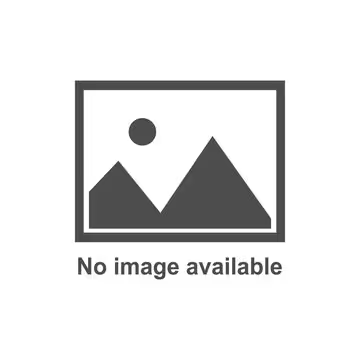
NOTES FROM THE GEMBA - We follow the author on a visit to a train maintenance center in France. Through practical examples and pictures from the gemba, she explains how the center is transforming itself.