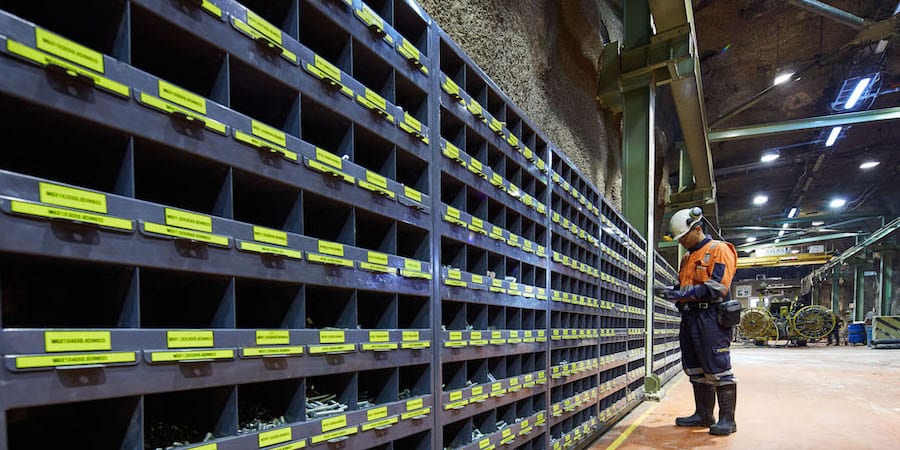
Kaizen and improved maintenance in a Turkish mine
CASE STUDY – Over the past four years, by developing its kaizen capabilities and crafting a better approach to maintenance, a Turkish gold mine has significantly reduced its extraction costs.
Words: Selçuk Turan, Process Superintendent at Tüprag’s Efemçukuru gold mine, and Hüsrev Yaman, Senior Lean Coach at Lean Institute Turkey.
In 2011, with the economic crisis still biting, the price of gold peaked at nearly $1,900 per ounce. At the time, Tüprag (the Turkish subsidiary of Eldorado Gold) was commissioning the Efemçukuru site, hoping to start production as soon as possible. The first two years of operation were rather chaotic for us, with production performance dwindling and safety risks increasing. We didn’t even have enough space to move around quickly and safely, neither underground nor on the surface workplaces. By the time 2013 came, we knew we couldn’t keep working like that.
In that same year, the price of gold dropped to around $1,280, putting a strain on mining investments and mineral exploration budgets around the world. It was around that time that we turned to Lean Institute of Turkey for help to initiate a lean transformation.
Our goal quickly became clear: because no mining company is immune to the fluctuations in the price of gold, the only way for us to achieve continuous profitability would be to deploy precise, planned and disciplined cost control. Knowing this is a matter of life or death in our business, we decided to become a more robust mining enterprise by basing our culture and processes on the idea of continuous improvement. We wanted to become a model mine that ensures the health and safety of its workers and cares for the natural environment.
The foundations for lean at Tüprag were laid with 5S and visual management, which greatly supported our initial maintenance and kaizen activities as gold prices kept dropping. (We’d have the definitive confirmation of how good an idea lean was in 2015, when the price of gold went down to $1,050.)
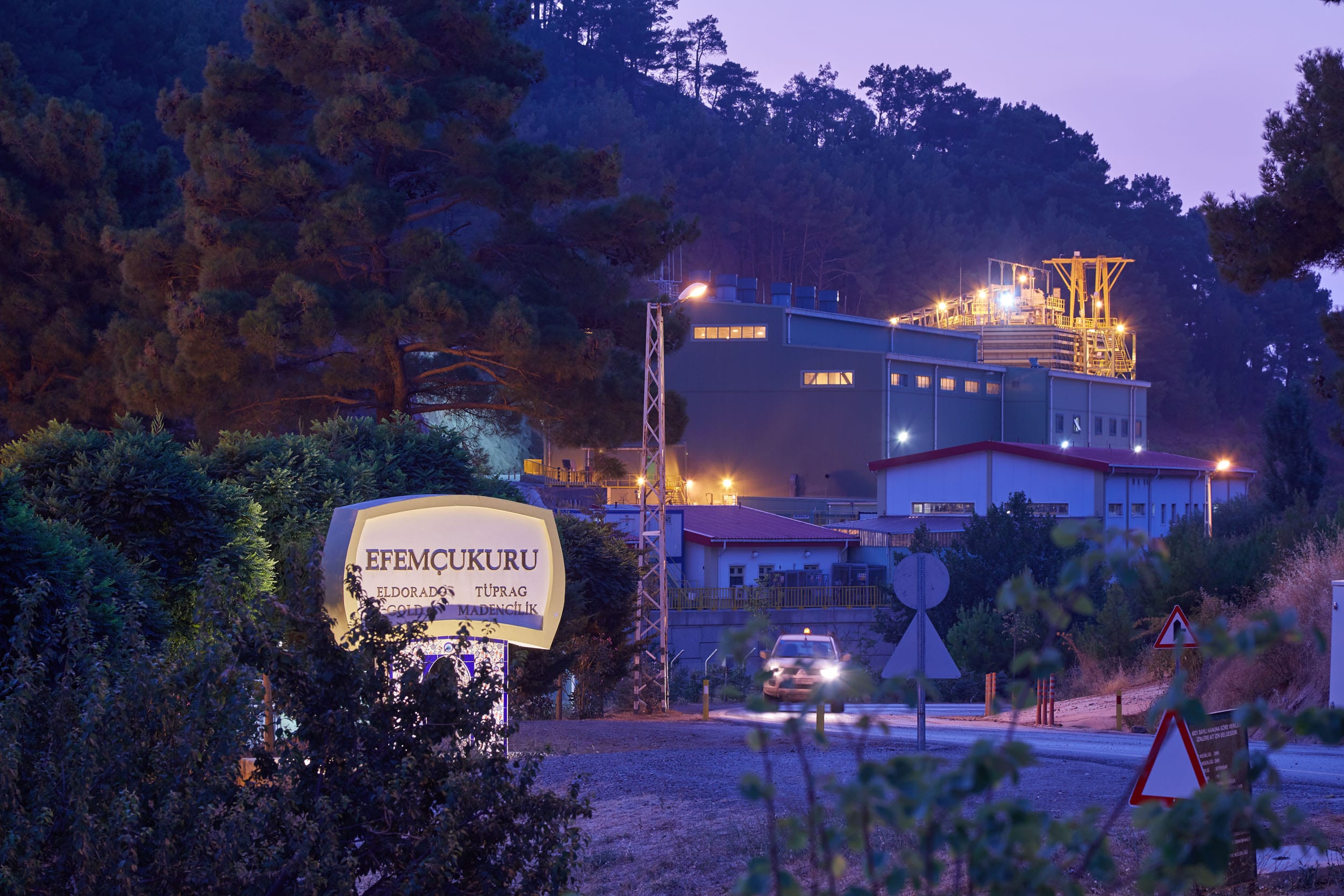
WHAT DOES LEAN HAVE TO DO WITH US?
As expected, the first Lean Awareness training sessions were met with suspicion and resistance. We got responses like: “We are Turkish miners, not Japanese carmakers”, “Mines are different, unique environments” or “You can’t apply 5S underground”.
Six months later, however, pilot projects and kaizen had begun to bear fruit and people started to realize that the philosophy they were resisting could actually help us to solve our problems. The application of 5S and visual management, for instance, resulted in a better-organized underground work area. In the meantime, the concept of “standard work” became part of the way miners talk every day. Upon seeing the first positive results, we decided to spread 5S across the whole site and to all departments: today, 5S audits are performed in 95 locations across Efemçukuru, both underground and on the surface.
Shortly afterwards, it occurred to us that becoming a “model mine” would take some time and that the journey would prove harder than we had envisaged. We realized that if we were to sustain our results and continue to improve, we’d need a fundamental shift in culture, habits and behaviors. In turn, we learned that this could only be achieved if our people bought into this change.
Bringing order to our processes and standardizing our work were important steps at this stage of our evolution as a lean company, as was our focus on comprehensively developing our people. If our mine was to be ready for whatever the market might throw at it, our people would have to be ready, too.
IMPROVING THE VALUE STREAM OF GOLD
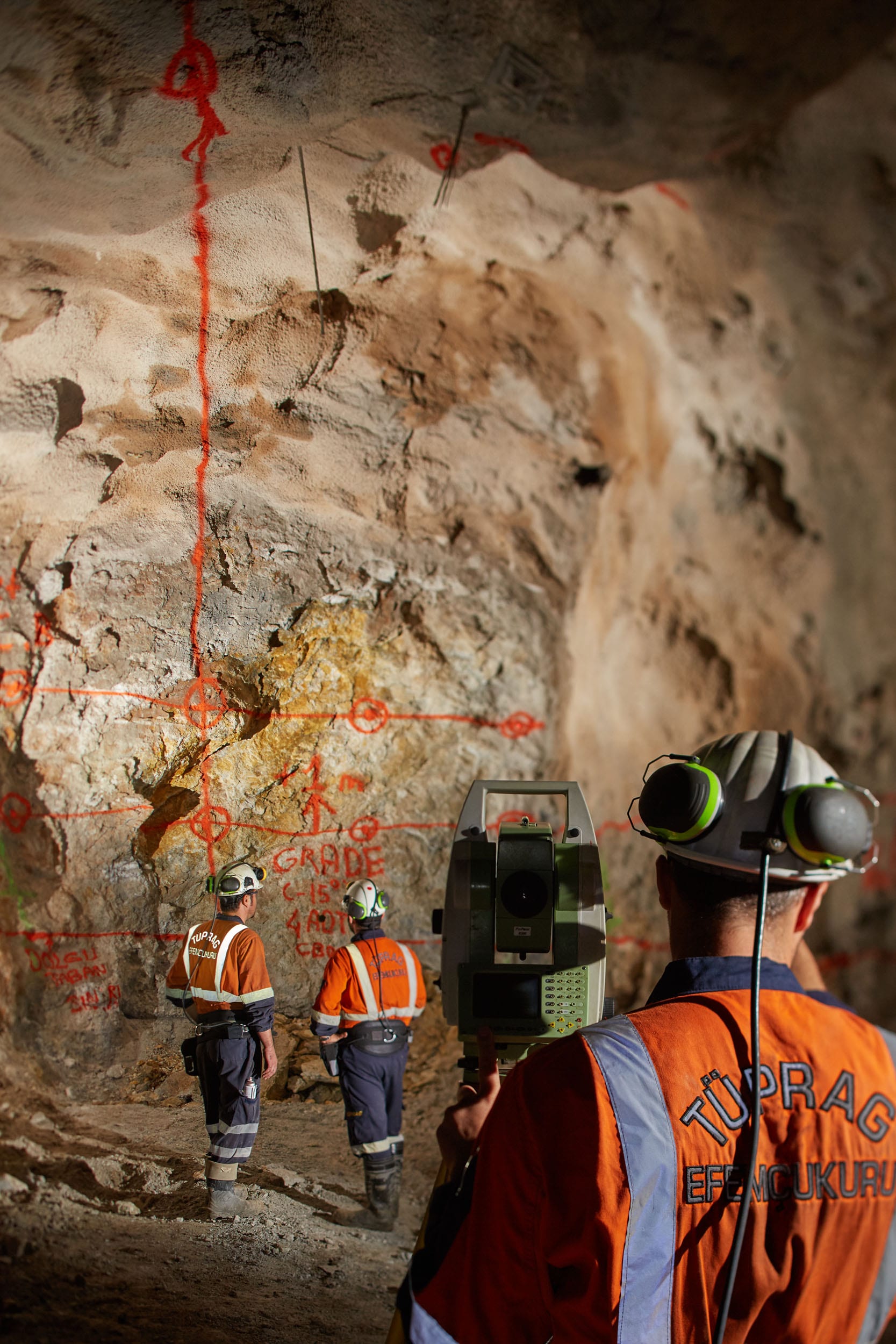
The value stream of gold can be illustrated with a circle. The process begins with drilling to detect gold ores, which are then scheduled for excavation based on the estimated “life” of the mine (in our case, the opening of galleries for each gold seam, 600 meters below the surface, were planned with precision around 10 years ago). Once the underground ore deposit is reached, the most value-adding part of the job begins, with different teams and equipment surveying, drilling, blasting, and transporting the precious metal to the surface in a cycle that continuously repeats itself. The ore extracted is then conveyed to a plant for beneficiation, a process by which its economic value is increased. Such facilities are closed-circuit plants that run 24/7 and perform crushing, grinding, classification, froth flotation, thickening and dewatering – all of this resulting in a final product called gold concentrate.
We can, therefore, identify two main phases of the mining process: labor- and equipment-intensive underground production and process- and energy-intensive ore beneficiation. At Efemçukuru, we decided to use TPM (total predictive maintenance) and early equipment management to solve our underground problems, while in the beneficiation plant we focused on autonomous maintenance, reliability, energy efficiency and management.
Underground, our Jumbo machines drill holes in the ore face, in which we then insert and blast the explosive. The blasted ore and mine rock is then transported to designated areas, while cement is used to fill the void created by the explosion and to allow the next drilling cycle to take place. As far as this process goes, we were mainly experiencing two types of waste:
- Completing one cycle took too long. To tackle this, we created a value stream map and analyzed each of our value-creating and non-value-creating operations. We learned that our biggest loss resulted from the materials needed for production being sent to each area separately, which caused significant delays. So, for each ore face we created standardized material areas with storage bays that are refilled every hour. Doing so, we eliminated waiting and material waste, gaining one extra ore face cycle per day and a 5% cost reduction per meter excavated.
- Overbreak was high, with a 25% rate of dilution. This meant that we were transporting and feeding to the beneficiation plant a big amount of non-gold bearing rock. Every transport and processing operations represented pure waste, which resulted in capacity loss in the plant and great inefficiency. As part of a kaizen, all available ore face engineering applications were repeatedly questioned by mining engineers (given different variables) and training on each technique was given to each employee. Our mining engineers went to the gemba personally to drill the holes for explosives and find a way to standardize the new ore face pattern they had set up. The entire team worked together and was able to determine the ideal angle and explosive charge to minimize the dilution rate. Overbreak was reduced to 9% from 25%, which translated in millions of dollars in savings.
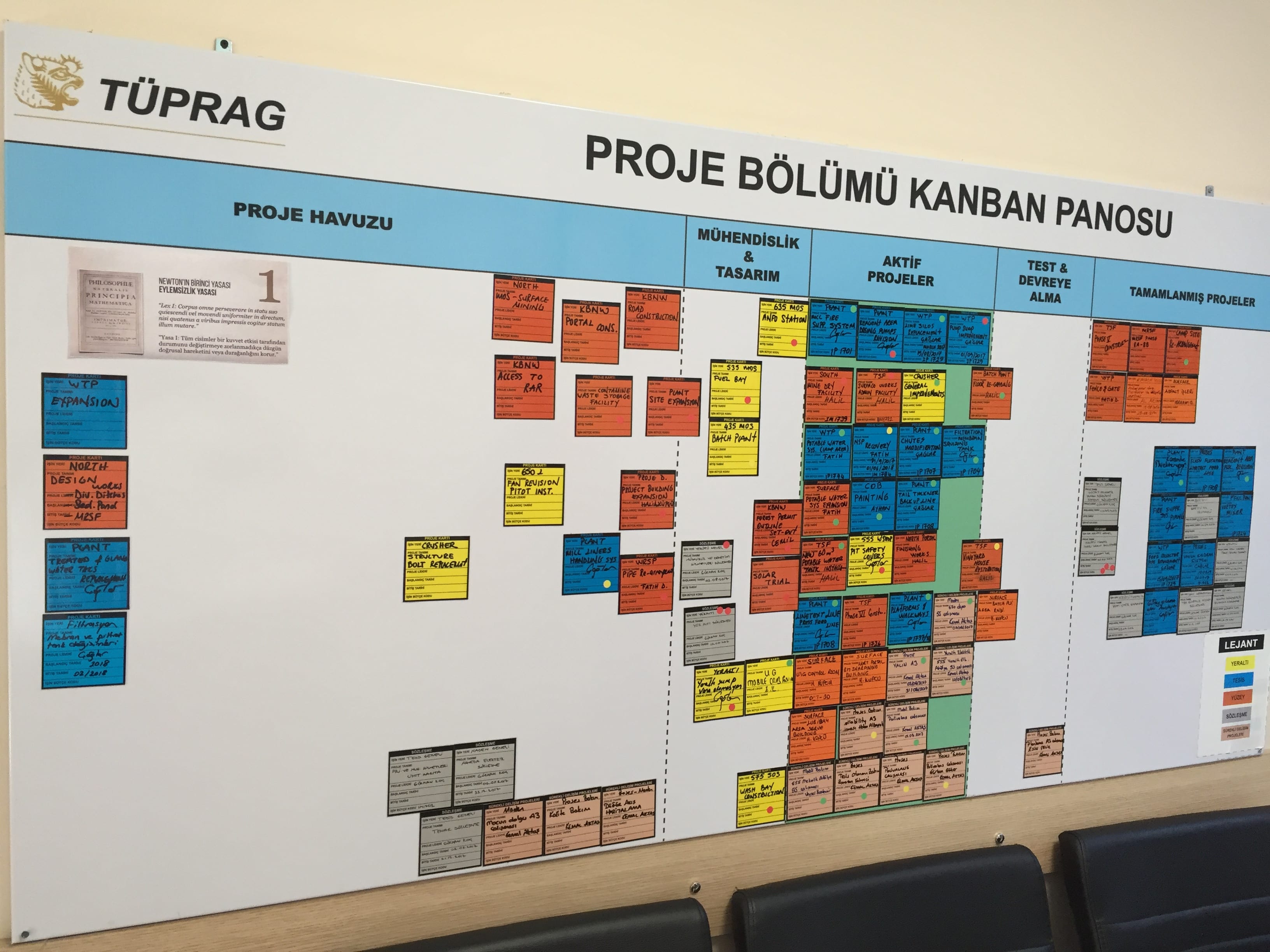
The equipment used underground tends to be at least three times as expensive as the machines deployed on the surface, with maintenance costs also much higher. However, this isn’t to say that production at the ore beneficiation plant didn’t need our attention. It is very important that all equipment in the plant is reliable and that it operates at a high OEE, but let’s just say that our initial situation wasn’t exactly like this. Up until then, our response to our maintenance problem had been to have a lot of spare parts available at all times (high inventory) and to deploy trouble-shooting crews who acted like firefighters running all over the place.
After lean was introduced, however, our approached changed dramatically:
- We first identified our critical equipment and started to monitor it continuously using online systems and manual control mechanisms. An equipment health matrix was created for each piece of equipment, which allows us to intervene before a breakdown occurs. To date, we have made around 250 different pieces of equipment reliable.
- We introduced autonomous maintenance. At a kick-off event, in which people from every part and at every level of the organization participated, each of us busy cleaning our machines and equipment. We then identified the sources of problems and hung Fuguai Tags (they are used to identify and visualize abnormalities) to the affected machines. The routine checks of the maintenance department were reviewed and a new standard for autonomous maintenance was introduced, meaning our operators could now perform checks independently and come up with improvement suggestions they will then bring into action with the help of our engineers. Ownership of the process is now apparent in the beneficiation plant. There’s more: rather than constantly fighting fires, the team is now performing root-cause analysis to eliminate faults once and for all. Over time, our planned maintenance rate began to increase and our breakdown rate dropped (we had 850 residual failure notifications – a heavy burden for us – but through our lean efforts we were able to tackle all of them in just three months). We place a lot of importance on standard work, and the number of One Point Lessons and standard procedures reached 1,213. Finally, the average gold recovery in OEE for the plant grew by 1%, reaching 94%.
- We examined the causes of malfunction of our underground mobile equipment such as loaders, excavators, drillers etc., whose maintenance cost is about three times the price we paid to purchase it. Interestingly, we found that most breakdowns were due to hydraulic hose damages (we often picked the wrong hose). It also turned out that the things we checked during the planned maintenance didn’t correspond to the failures we experienced during the work. Consequently, we reviewed all planned maintenance items again, creating planned maintenance teams that we asked our best mechanics to lead. Increasing the quality and speed of the maintenance work led to a decrease in the number of faults, as our machine efficiency rate went up 20%. Our main mobile equipment used to shut down for planned maintenance every 150 hours, whereas today it does every 250.
- At the same time, the transformation of our maintenance approach and the increase in equipment efficiency prevented us from having to purchase expensive extra equipment. Each year, we used to spend hundreds of thousands of dollars in mobile equipment for mine production that we often weren’t even able to properly put to use. Early equipment management was also extremely useful to us.
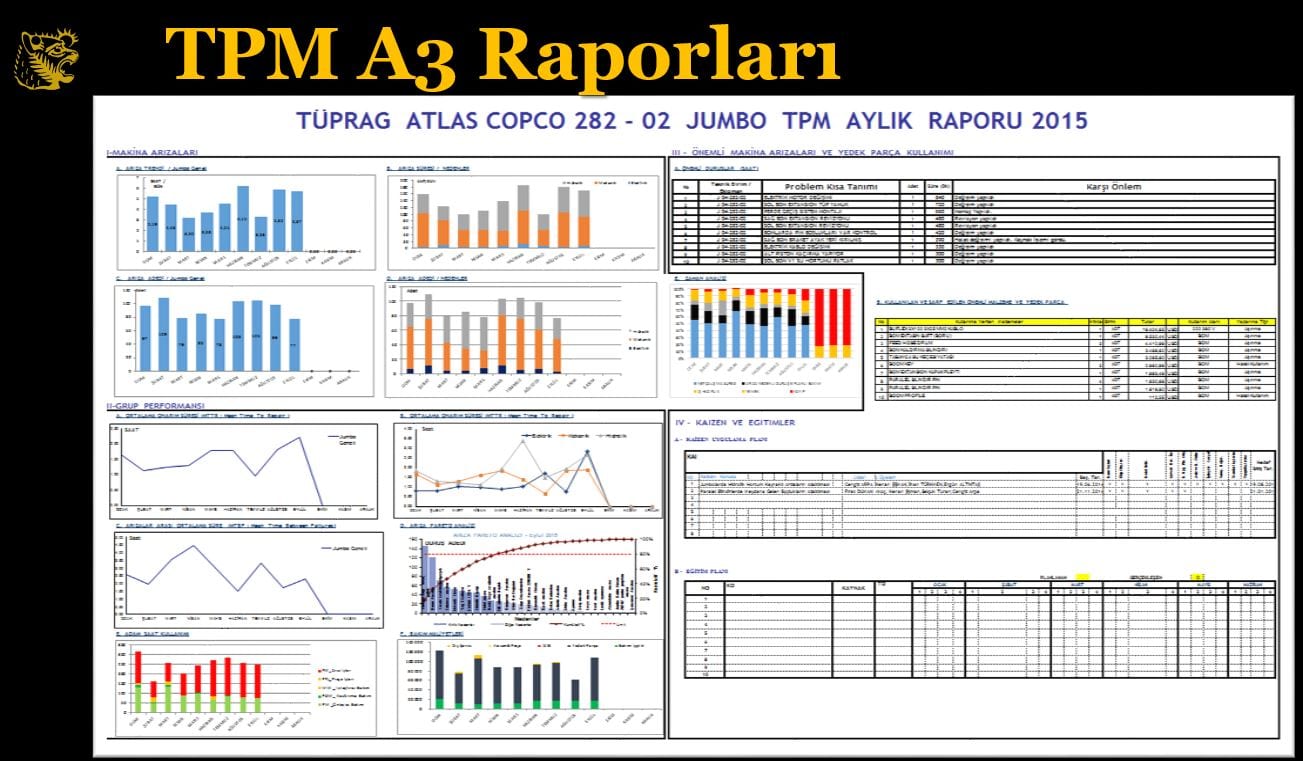
Kaizen was instrumental in tackling Tüprag’s challenges, but it’s certainly not the only element of a lean transformation we have been relying upon. To ensure the creation of teams well-versed in problem solving, we focused on the developing of lean leaders in our internal Academy. Our team leaders can now manage both normal and abnormal situations in health and safety, production, quality and cost during the daily asakai meeting. These days, A3s are routinely used at every level in the organization, while our full-time online production control and monitoring system helps us see production parameters instantaneously, detect problems and quickly adopt correcting (or preventive) measures.
The transformation that took place at Tüprag in the past four years is nothing short of a revolution. It is much more than just the sum of a few innovations, technologies and investments, however: what we have witnessed is a structured, purpose-driven effort to unleash the creativity of our people and develop their capabilities.
Lean wouldn’t be lean if it didn’t benefit everyone involved, including the community around us. This is why our improvement work has not been limited to the mine. Indeed, we have been supporting good farming practices in neighboring villages, vineyards, fruit gardens and agricultural enterprises. We are also supporting cultural activities provided in schools in our area (like painting contests and excursions). Much like we extract gold from rocks, we are tapping into our people’s potential to create a better future for everyone in and around Efemçukuru.
For more information on the Tüprag lean transformation, contact Hüsrev Yaman at Lean Institute Turkey at hyaman@lean.org.tr
THE AUTHORS
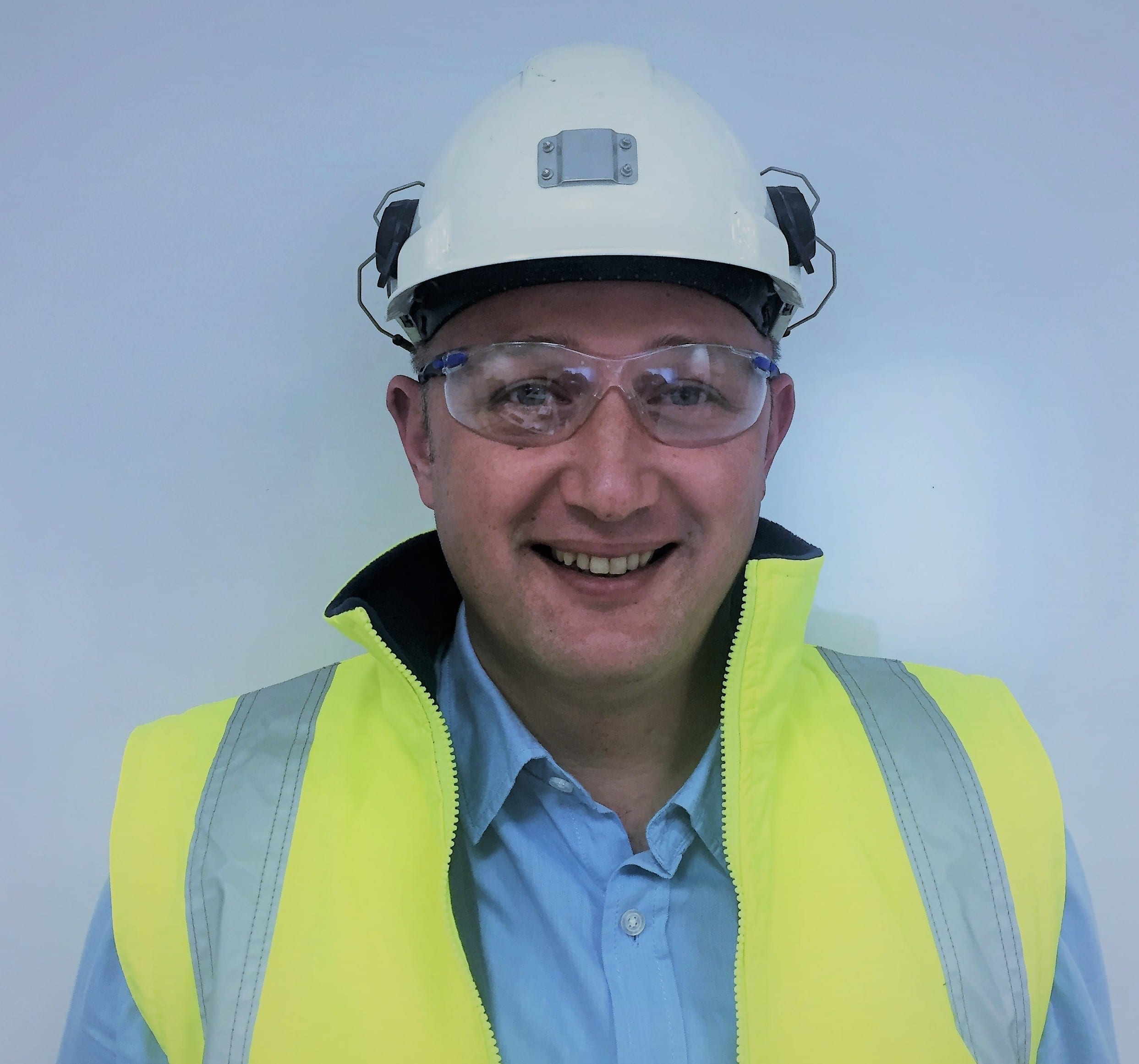
Selçuk Turan is Process Superintendent at Tüprag Efemçukuru Gold Mine (a subsidiary of Eldorado Gold), working as a Lean Management Coordinator for the past four years.
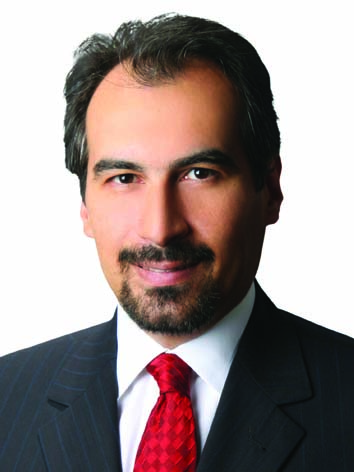
Hüsrev Yaman is a Senior Lean Coach at Lean Institute Turkey. He has supported the lean transformation at Tüprag for four years.
Read more
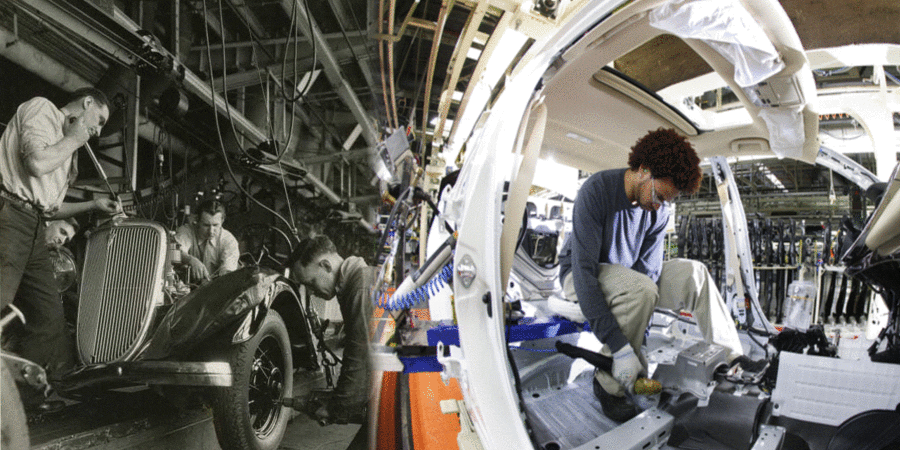
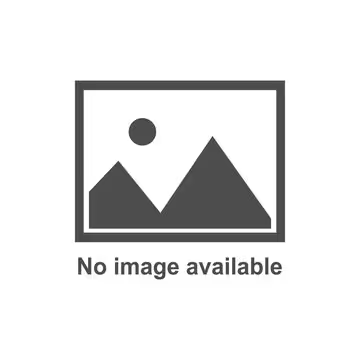
FEATURE – The author offers an overview of the ingredients that made lean thinking what it is, of the 30 years of incubation it underwent at Toyota, and of its diffusion from 1980 onwards.
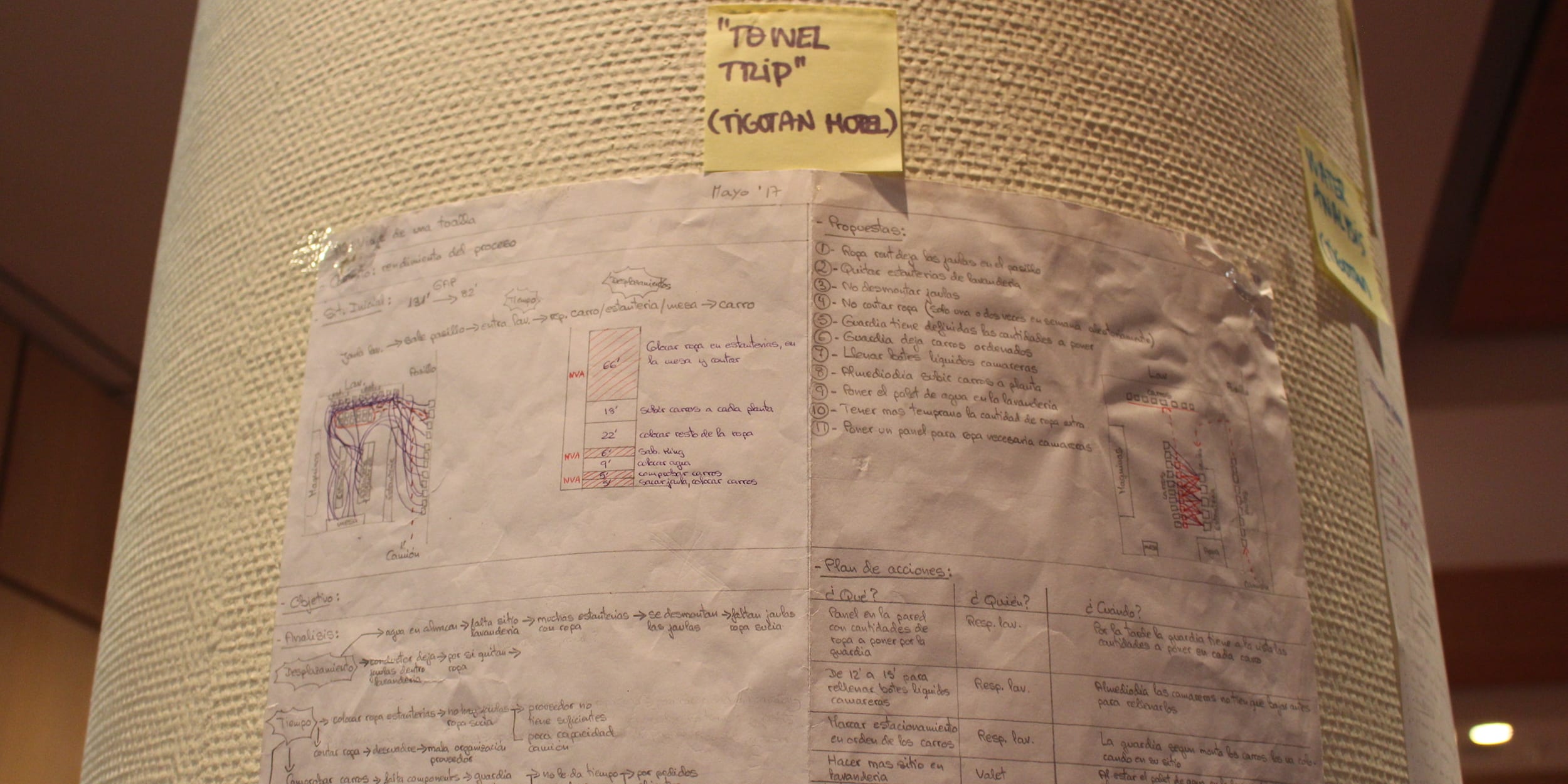
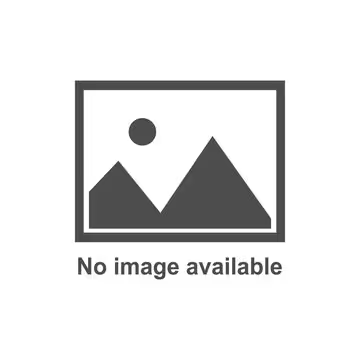
VIDEO – The director of a hotel in Tenerife explains the first steps the team is taking to develop a lean daily management system, and how this connects to the organization's hoshin.
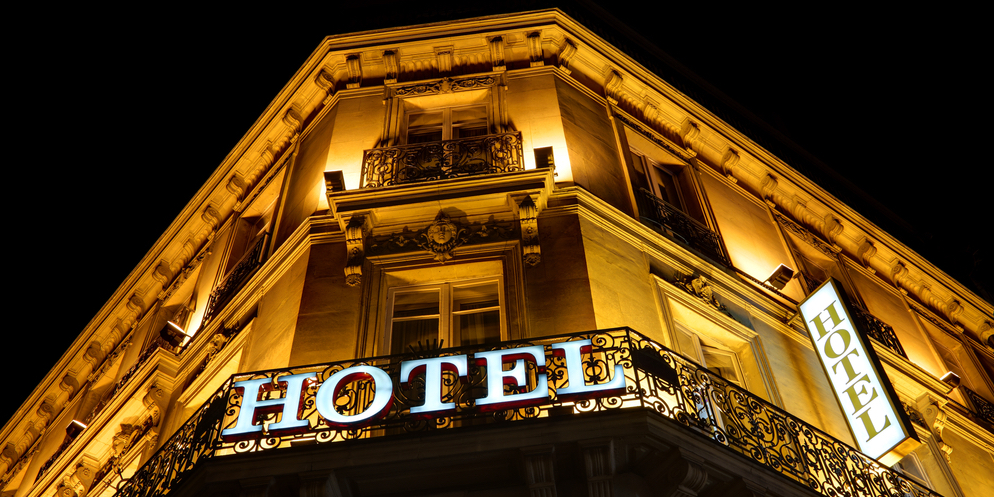
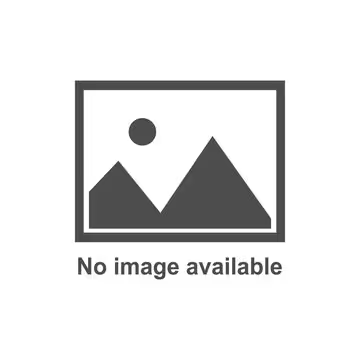
INTERVIEW – Juan Pedro Gonzalez is a pioneer of lean in hospitality, having spearheaded the transformation of Spain’s Dreamplace hotels since the beginning. Here, he discusses what role lean can play in advancing the industry.
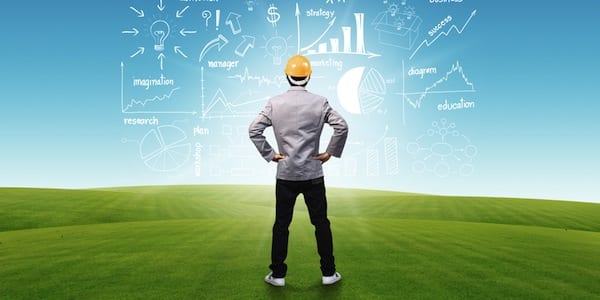
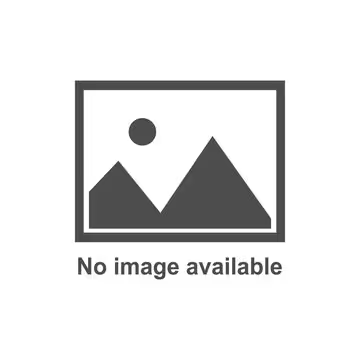
FEATURE - In this essay, first appeared in his book Gemba Walks, Jim P. Womack describes the benefits of launching lean in a greenfield environment drawing from his experience volunteering in Central America.