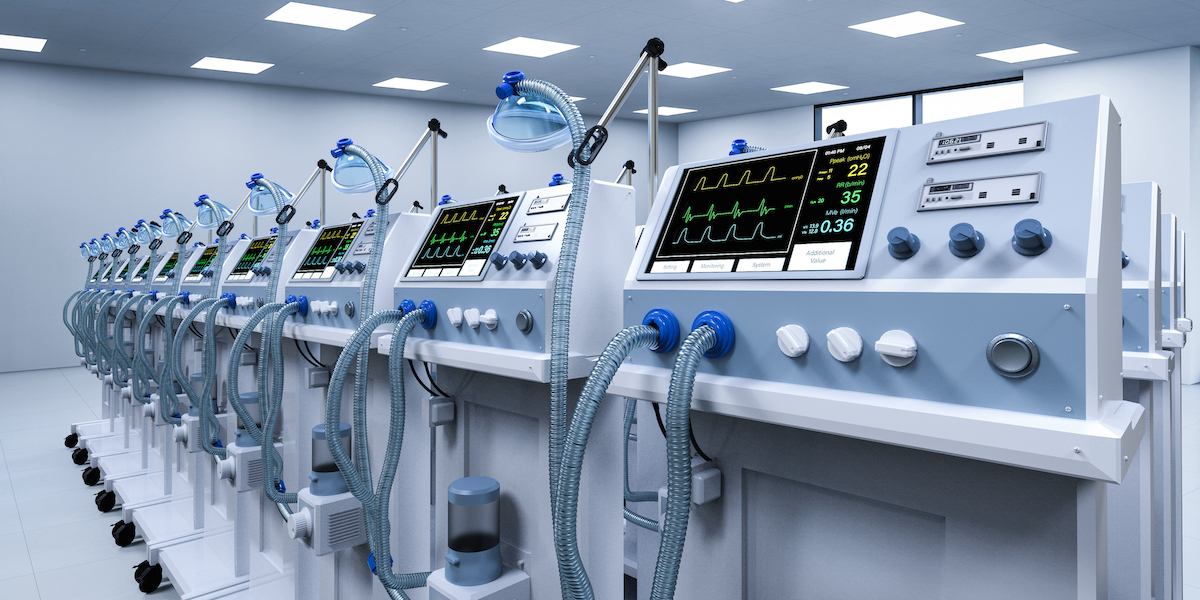
Post-pandemic hansei
FEATURE – Back on the road after two years, the author reflects on how lean organizations have performed during the pandemic and addresses age-old misunderstandings about Just-in-Time.
Words: Jim Womack, Senior Advisor, Lean Enterprise Institute
As the pandemic slowly subsides and we emerge from our hiding places, it is great to get back to the gemba and meet the Lean Community. Over the past few weeks, in conversations with practitioners and leaders as I took my first gemba walks in two years, I have often been asked for my reflections (hansei) on how Lean Thinking performed during the pandemic.
My assessment is that lean thinkers were very effective in quickly creating – and recreating – streams of value for disrupted conditions. When the pandemic first hit, a lot of activities suddenly had to be reorganized and lean methods to visualize value-creating processes proved very useful. Value stream maps in the context of A3 analysis showed everyone how the work had historically been done and how it should be rethought in the light of the new circumstances. For example, there were countless instances of lean being used to set up Covid testing sites (a process that had to be designed to make the best use of scarce resources) and helping hospitals quickly adapt to new and very urgent patient needs without giving in to panic. The lean thinkers involved in the really essential work of redesigning the world’s essential work should take a bow!
A greater challenge for lean thinkers has been to sustain the smooth flow of value from raw material to the customer as the world economy has gyrated. In fact, we have often been accused of causing the shortages experienced when the economy froze up (e.g., paper towels in 2020) and opened up again in 2022 (e.g., motor vehicles.) We constantly read this in the media, in articles by writers who have no understanding of the logic of a pull system and how it differs from traditional push systems. According to the standard narrative that most observers have embraced, the spread of Just-in-Time systems in recent years took most of the just-in-case inventory out of value streams to save money while these streams were serving stable demand. But as economies gyrated, the world became a miserable place because shortages of parts created by JIT meant that people couldn’t find every item on the shelf or get their Amazon products delivered the next day.
This narrative drives me crazy for two reasons. First, JIT is blamed while hardly any organizations outside of Toyota and its suppliers actually run a rigorous JIT system from one end of the value stream to the other. Most businesses still run push-logic material requirements planning systems (MRPs) that live inside of Enterprise Resource Planning systems (ERPs, such as SAP and Oracle). And these are only loosely connected to similar push systems at customers and suppliers. This very conventional practice is not lean at all. So how can lean thinkers be blamed for the supposed failures of JIT when the widespread switch to JIT has never happened? The second reason I reject the standard narrative around JIT is that it completely misunderstands the problem that emerges when there is a big surge in demand. The problem is not inadequate inventories at every step of the supply stream; it's the lack of emergency stocks at a few critical points.
To understand this, let’s take a look at inventories within JIT systems. The Toyota practice is to carefully specify the amount of inventory (buffer stocks) needed at the customer end of each step of every value stream in order to protect customers from shortages due to sudden changes in demand. Similarly, safety stocks need to be located at the beginning of each step to protect that it from delivery or quality failures by suppliers. Finally, shipping stocks are also needed at each step when goods can’t be sent one at a time to the next step. These are the goods being assembled in a carton, on a pallet, or in a container for the next shipment.
Note that JIT in the first instance isn’t designed to reduce inventories, but to prevent shortages. At each step in the process, managers continually review the experience with demand patterns from customers and the reliability of up-stream production processes to determine the amount of inventory needed to protect customers at current levels of demand variation and system capability. This is called “standard inventory” and lean managers must know what this amount is and whether it is being maintained at every step of a process. Then, as demand is smoothed through heijunka and capability is improved through jidoka, it is appropriate to reduce the amounts of inventory. This is good: customers are safeguarded as the amount inventory is continually reduced.
But – and this is the big “but” – how can a JIT system deal with sudden and unexpected surges in demand? Let’s take a pandemic example. During the SARS epidemic of 2003, the US government became concerned about the availability of ventilators for intensive care units in hospitals. There were only a few finished units in producer warehouses and the existing supply base could not dramatically increase production, even if parts were lying around at every step in traditional MRP environments, because the production equipment and workers with the skills needed to dramatically increase output were not available.
The demand for ventilators never materialized in 2003 as SARS fizzled. But government planners grasped a very important point: Whatever system of inventory management producers were using – JIT, just-in-case, or anything else – the only way to instantly respond to dramatic increases in demand was to establish an emergency stock of finished units at the end of the value stream. As a consequence, a massive inventory of ventilators was produced for the next pandemic – more than 14,000 – and placed in a central, government-controlled repository in Texas, ready for shipment to hospitals as needed. When the Covid-19 pandemic struck in 2020, we again heard in the media that there was a shortage of ventilators (due to a lack of parts caused by JIT!) and many manufacturers – including car makers – rushed to produce ventilators. But, in fact, the Texas stock of ventilators was never exhausted.
This was a very good thing because new ventilator production took months (to assemble the workers and equipment needed to design and make them) and the finished products weren’t at the quality levels and performance standards hospitals required. In fact, they were never used. So, the government actually did the right thing in creating and sizing the emergency stock! The sobering point, however, is that it was just dumb luck that in the end we needed less than had been stockpiled. Indeed, the problem with emergency stocks (which any system of production control – push or pull – needs in times of dramatic demand surges far outside of the normal variations) is that mere mortals cannot estimate the needed amounts to stockpile. So, what to do?
Lean thinkers don’t have an easy answer. But it is interesting to reflect on Toyota’s efforts to deal with the crisis. This is the organization that supposedly inflicted JIT on the world, but which has actually been the automaker least impacted by the post-pandemic bounce back in demand. If Toyota invented JIT and use it every day, why hasn’t it struggled more than its competitors rather than less? The simple answer is that Toyota invested in a different type of emergency stock to supplement its rigorous daily management of inventories. What separates Toyota from other players in the automotive industry today is that, in the face of a big drop in demand in 2020, the company decided to reserve production capacity at suppliers for the bounce back in demand and, if necessary, even pay suppliers and its own employees to do nothing in the meantime.
This cost Toyota a lot of money, as did the fact that it didn’t lay off any of its permanent employees anywhere in the world – not even in the first few months of the pandemic, when demand halved. This approach allowed Toyota to be ready for the surge in demand when the market came back. (The two exceptions were the lockdown in Penang, Malaysia, at the end of 2021 that stopped all of Toyota’s chip suppliers despite their availability of production capacity and the Chinese lockdowns in the past few months. These caused Toyota to lose some production, but much less than competitors.) Meanwhile, competitors cut costs by releasing suppliers and failed to notice that growing demand for personal electronics during the pandemic was absorbing all of the independent supply of computer chips. When these companies needed the capacity in the fall of 2021, there was none to spare and large shortages of new vehicles were soon apparent everywhere.
Toyota has created a second type of emergency stocks over the years to deal with a sudden loss in production capacity when the asteroid hits the plant, the tsunami floods it, the earthquake breaks it in two, the fire destroys the equipment, or (and most troubling) there is a terror attack or a war. When these happen it can marshal excess resources within the Toyota Group of supplier companies to find equipment, staff and expertise (often from its internal lean team) to quickly recreate production processes as needed. This was most spectacularly demonstrated in 1997 when a fire at the Aisin brake valve plant in Toyota City destroyed its entire world production capacity. Yet, Toyota created new production capacity in a very short time – in fact, within four days – and its small emergency stock of brake valves could largely sustain production.
If the only answer to demand and production shocks is some type of emergency stock, how much finished inventory beyond standard inventory or production capacity beyond current needs are you willing or able to put aside? Without the help of society more broadly – as in the case of the US government’s stockpiling of ventilators – the answer in most cases is “not much”. So, as hard as it might be to hear, we need to realize that a rising tide lifts all boats, but a large enough tsunami – a global pandemic, for example – sinks all ships. Some disruptions are simply beyond our control as managers. Rather than trying to guess the right amount of emergency stock we might need to maintain normal production over an extended period of chaos – a largely futile exercise – we should follow Toyota’s example: always maintain standard inventory to eliminate short-term shocks for customers. And do what’s possible to create different types of emergency stocks at modest cost. (Oh, and don’t waste time blaming JIT when shortages emerge.)
After my recent gemba walks, my sum up on the performance of the global “Lean Team” in the pandemic is that we deserve a lot of credit for quickly reconfiguring value streams and that we don’t deserve any blame for the shortages we have been experiencing. That’s not the perfect result we would all like, but the best that’s realistically feasible.
THE AUTHOR
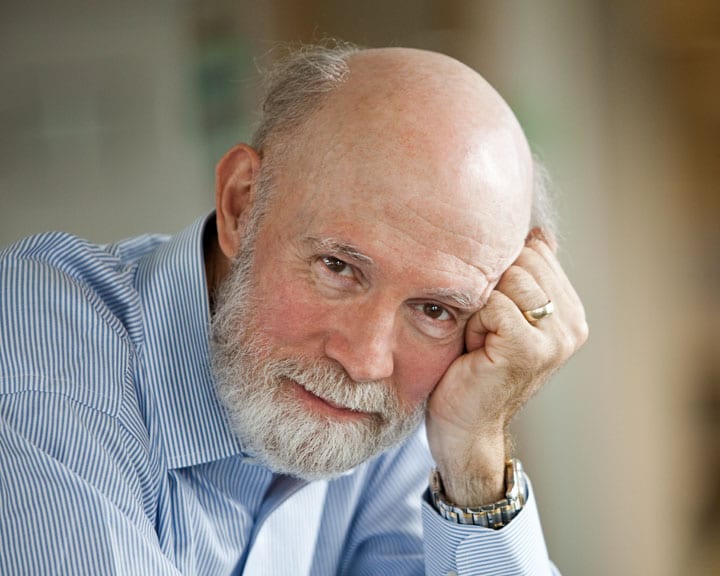
Read more
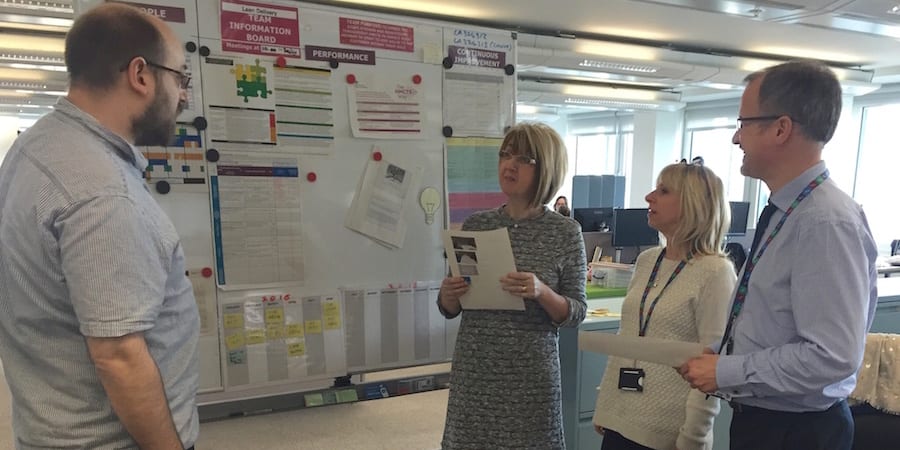
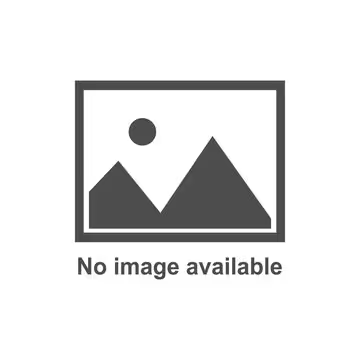
PROFILE – Lean leaders are often tempted to jump in and fix the problems they see. Julie McGrory is successfully transforming the culture of a large and traditional government organization by learning to take a step back and letting people take the lead.
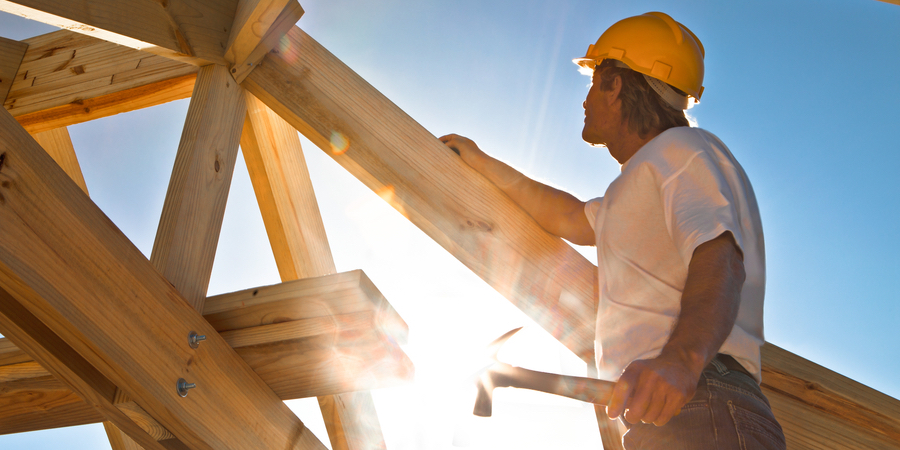
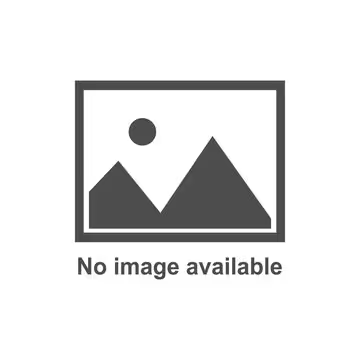
CASE STUDY – We hear from a construction company in Chile that embarked on a lean journey in 2018 to transform its culture and improve the work on its many sites.
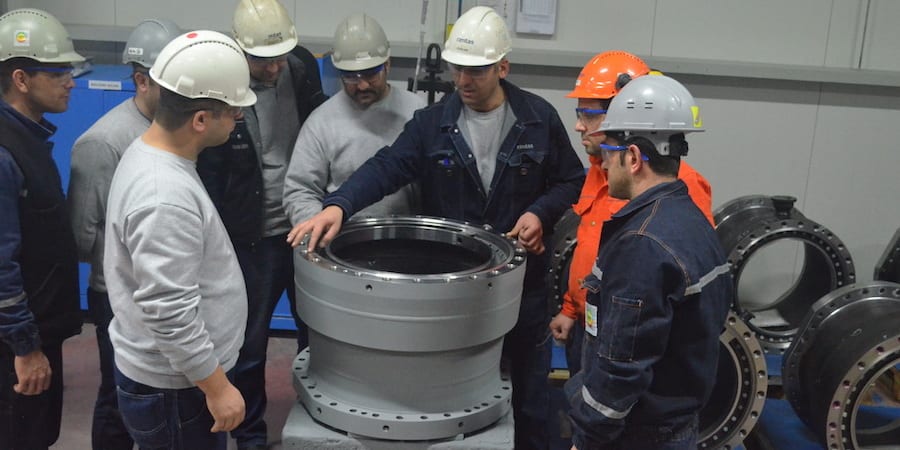
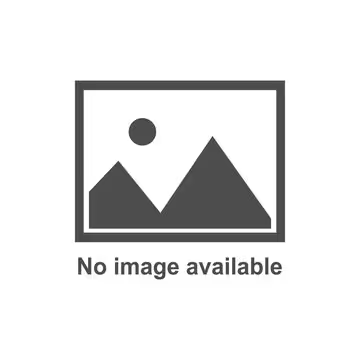
CASE STUDY – With plans to double capacity year on year in its new precision machining business, a Turkish company found in lean a way to control growth by stabilizing old processes while new ones are introduced.
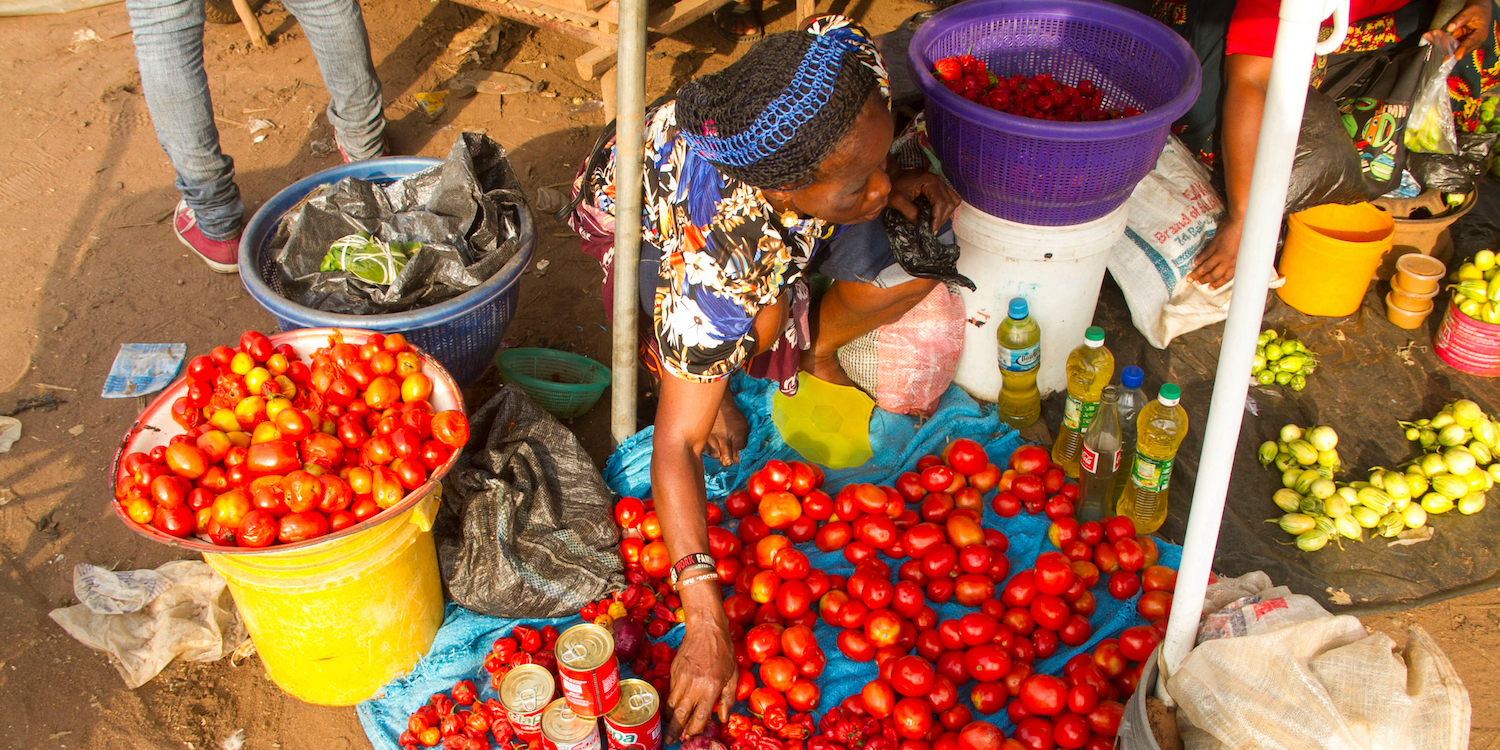
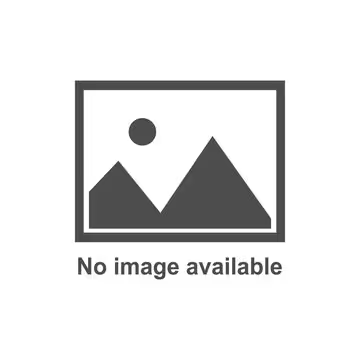
CASE STUDY – Lean Thinking travels far and wide. Here’s how the experience and insights of an Indiana-based farmer have supported a USAID project to improve outcomes for farmers across Nigeria.