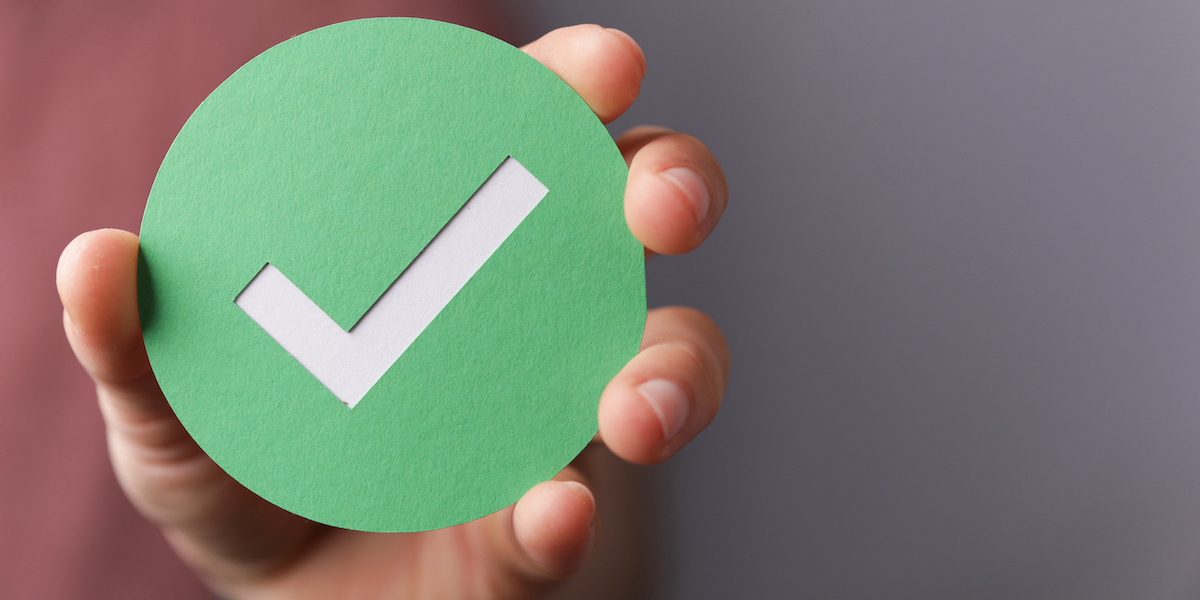
Whatever happened to quality first
FEATURE - In this article, taken from LEI's Design Brief, Jim Morgan talks about the often-overlooked topic of building quality into new products. Learn how a customer-centric approach in development can prevent costly rework and build lasting trust.
Words: Jim Morgan, Senior Advisor, Lean Enterprise Institute
This Design Brief article was previously published on The Lean Post. To subscribe to the Design Brief, click here.
This month’s Design Brief is a challenge to improve your new product and process quality. I realize that this may not be a particularly popular topic right now. Many would rather talk about breakthrough innovation or shipping minimally acceptable products. But the news is full of stories about serious quality issues in nearly every industry. Boeing, Ford, Tesla, and many other companies continually struggle with quality spills and recalls for which some even publicly blame their customers and others, predictably, revert to the “5 who’s” blame protocol. Frankly, this discussion is long overdue.
Those who are part of the lean community understand that basic quality is meeting or exceeding customer expectations and is foundational to a lean enterprise. We also know that the cost of re-work and returns can be enormous. Worse is the hit your reputation takes. Some organizations never recover.
But even the most seasoned lean practitioner can get distracted by the “new” and ephemeral. (There is a whole lot of snake oil out there.) But many of these practices lead to lazy thinking and sloppy work that can infect your entire organization. We can’t afford to lose sight of the basics of delivering actual customer value. As Akihiko Saito, executive vice president of Toyota, wrote in the foreword to Toyota Styled Mizenbushi Method (Tokyo: JUSE Press Ltd., 2002), “While our company’s method of production such as the ’Toyota Production System’ and ‘Toyota Way’ has caught the industry’s attention, I feel strongly there is a need to reform and return to the basics when we first started in the automotive business of thoroughly emphasizing that ‘quality comes first’ and ‘the customer comes first.’” A valuable reminder for us all to keep our eye on the ball.
The place to solve quality issues is in development
The place to start a “quality first” and “customer first” mentality is not on the shop floor – it’s in development. Development has much more leverage than any place else in the organization – not only on the efficacy of the product for the ultimate customer but for everyone along the value stream. Development can make it easy for people to execute their jobs correctly or nearly impossible. Lean Product and Process Development (LPPD) principles, practices, and tools are powerful enablers of high-quality, reliable products and processes. Improving your design practices, design reviews, quality operating system, testing, knowledge capture and reuse through LPPD methods are quite effective in improving quality. But your people will determine your ultimate success.
The heart of the matter
Consistently high-quality products come from organizations that relentlessly focus on their customer. That starts with leadership. Leaders get the culture they demonstrate and tolerate – and that is especially true for quality. And I believe that many leaders are flat out failing their organizations regarding quality.
Good leaders demonstrate quality as a priority. They provide the time, resources, quality operating infrastructure, training, and decision-making that enables their people to deliver. They lead by example and embody the customer-first mindset. They roll up their sleeves, know their stuff, and do the little things well – demonstrating the required discipline and attention to detail – every day. Poor leaders try to get away with a sincere-sounding press release and a feel-good speaker at a management off-site. It doesn’t work. Such leaders are failing their organizations and customers. Consider how millions of car customers must feel.
Don’t wait for your own quality crisis to act. Once a major spill has occurred, it can be nearly impossible to dig out from under. Just ask leadership at Boeing or Ford. Start now, and start in development, focusing on your customer to improve the quality of your products and processes. Start your own return to basics as suggested by Saito, “There is a need to reform and return to the basics when we first started in the automotive business of thoroughly emphasizing that ‘quality comes first’ and ‘the customer comes first.’” Your customers will certainly thank you, and you will be amazed at the positive changes to your organization.
In this month’s Design Brief
- Fabrice Bernhard, co-founder, and CTO of Theodo, a global lean software consultancy, contributes an essential piece on applying Toyota’s dantotsu (Japanese for “radical”) quality improvement method to software development. Fabrice reveals breakthrough improvement practices for an industry in dire need of a rethink regarding quality.
- Matthew Savas and I share a summary of our remarkable discussions with Tatsuhiko Yoshimura, PhD, former Toyota engineering and quality executive and creator of the breakthrough Toyota quality method known as mizenboushi GD3, for surfacing and fixing latent problems in designs.
- Steve Shoemaker, former vice president of engineering at Caterpillar’s Earth Moving Division, shares his experiences of how lean principles were applied within Caterpillar and, in a span of fewer than five years, quality improved by more than 50 percent while warranty dropped by $90 million. New product introductions were no longer firefighting events but methodical marches to the marketplace with few surprises.
- And finally, Matthew Savas has a conversation with my good friend and former colleague, Jeri Ford, vice president of quality at electric vehicle maker Lucid Motors, about ensuring quality through the value stream, from design to supply chain and manufacturing.
Download the latest issue of the Design Brief here.
THE AUTHOR
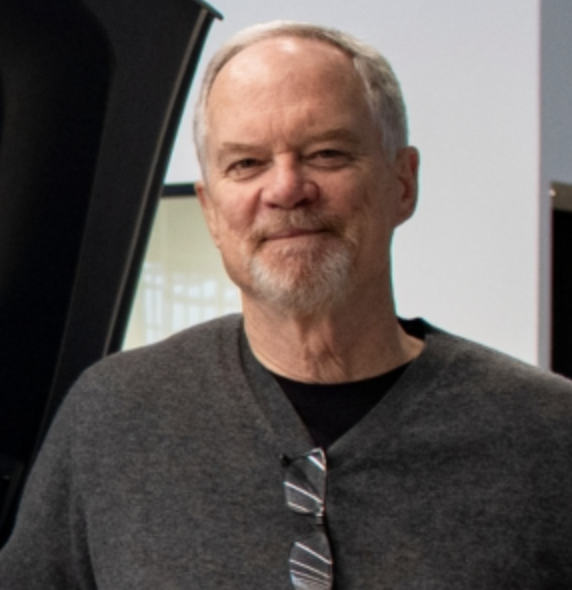
Read more
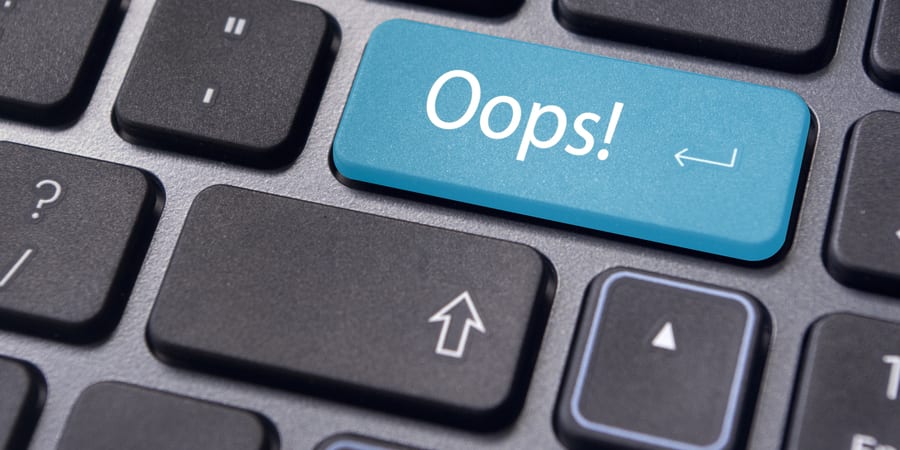
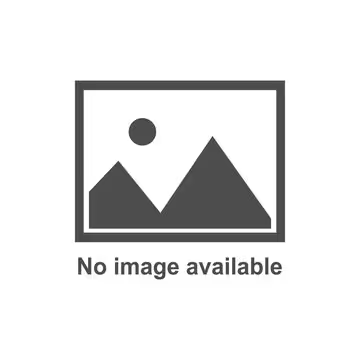
FEATURE - Traditionally seen as the mother of all evil, the IT department in our organizations has a long way to go before it fulfils its potential and becomes an actual facilitator in the delivery of excellent products and services. In the past few years, IT leaders have realized that lean management can help them to transform the function.
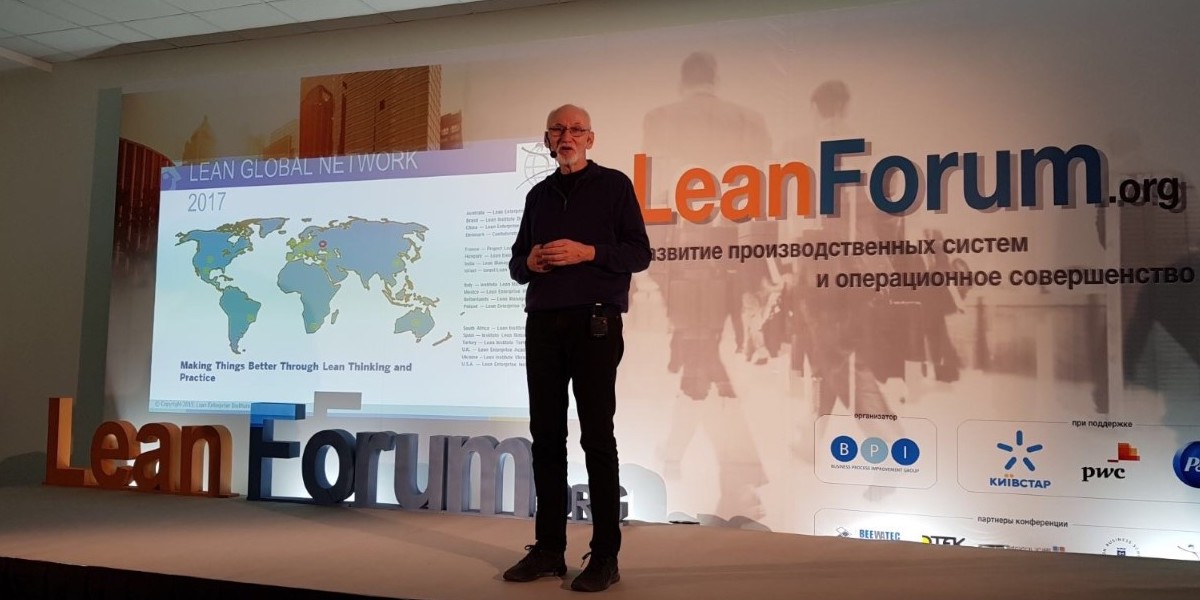
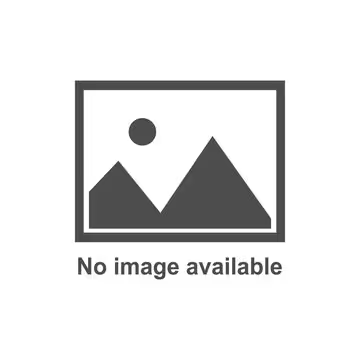
FEATURE – As the senseless war in Ukraine continues, the author looks back to his visit to the country in 2017, recalling and celebrating its vibrant lean community.
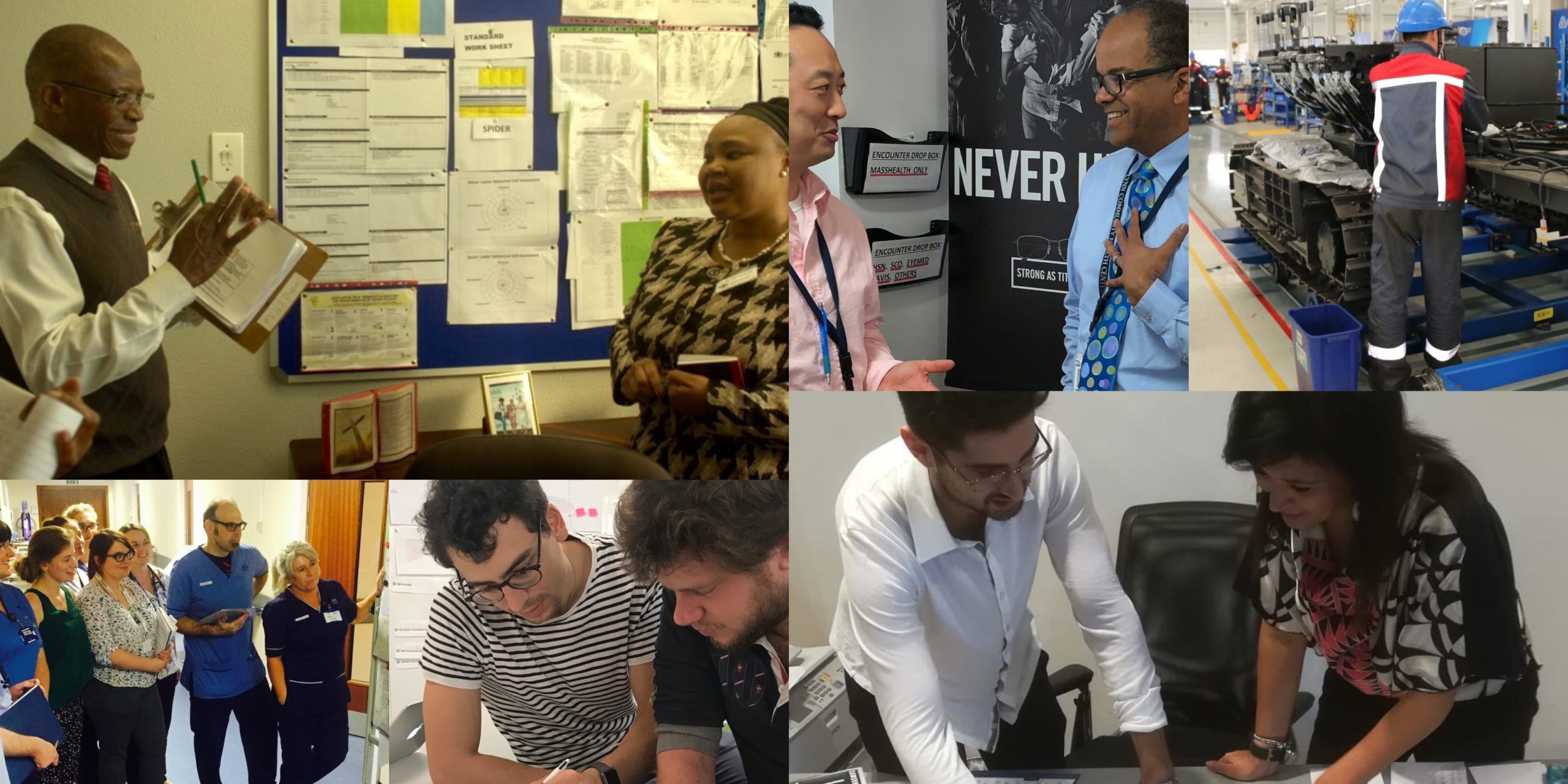
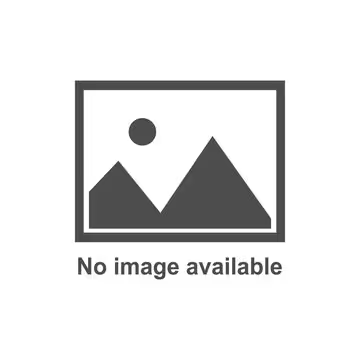
ROUND-UP – As the year ends, our editor reflects on the state of the lean movement and looks back at the best articles published by Planet Lean this year.
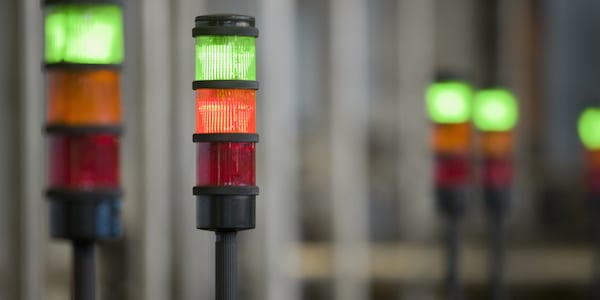
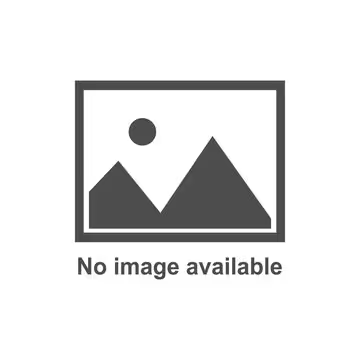
WOMACK'S YOKOTEN - Given the name of this column, it only makes sense to analyze the word yokoten. So, how can we effectively help others to apply what we learn at the gemba? What makes yokoten successful?
Read more
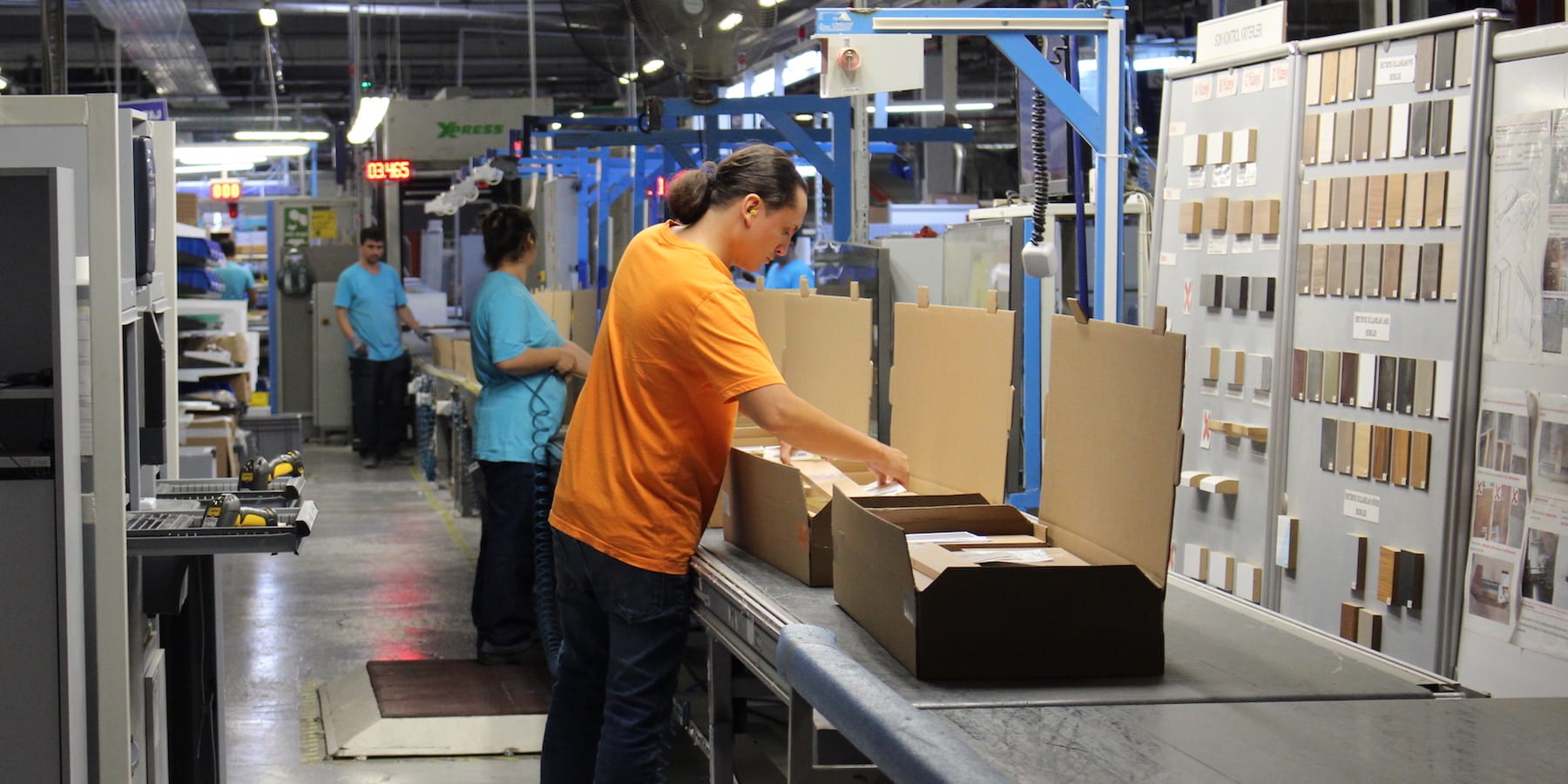
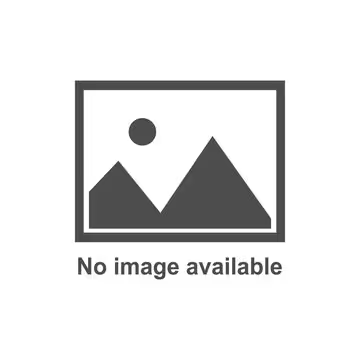
CASE STUDY – This Turkish producer of sanitaryware has boosted its quality so dramatically it’s now a player in the German market. It did so by bringing drastic change to its production system.
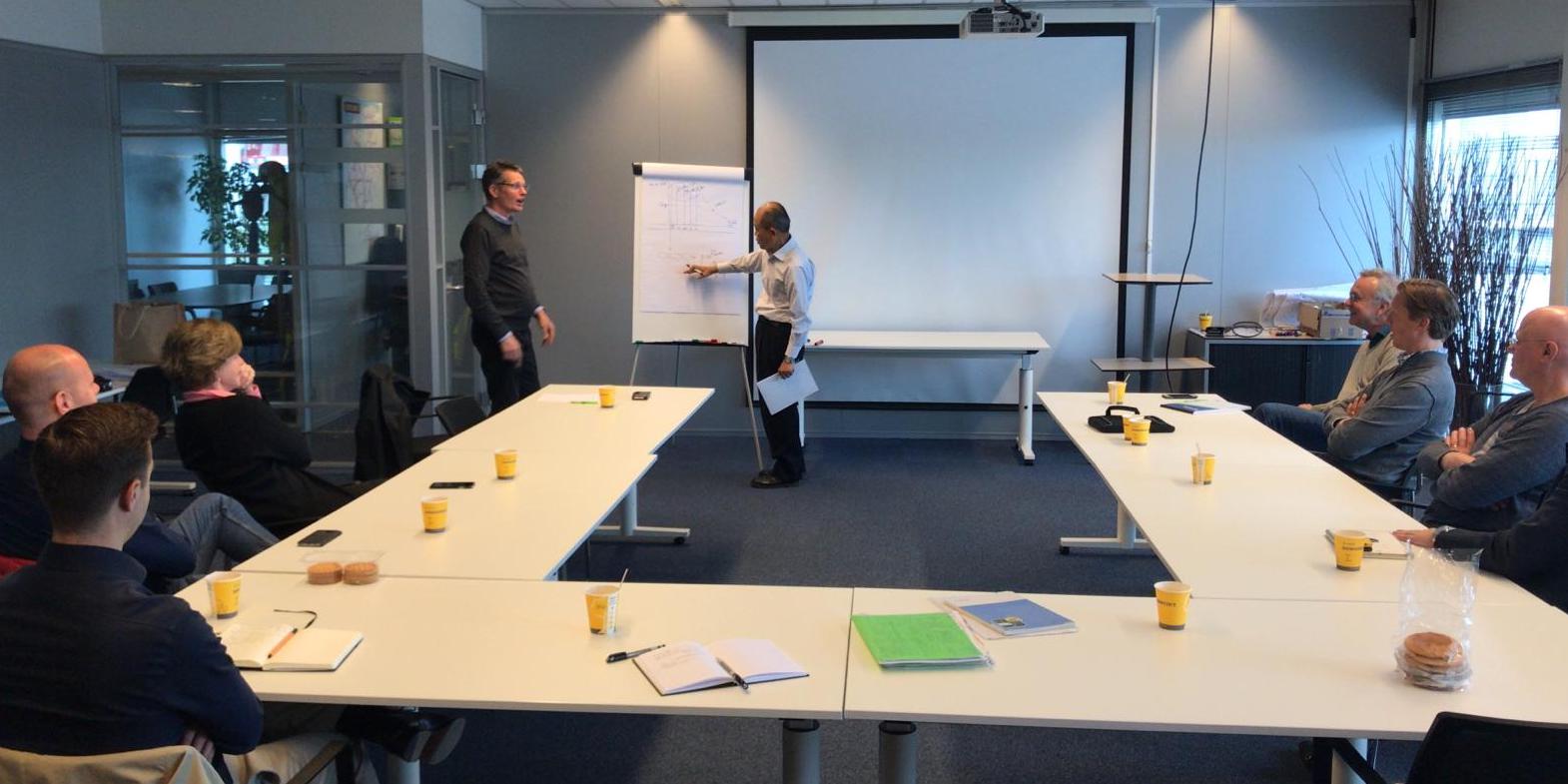
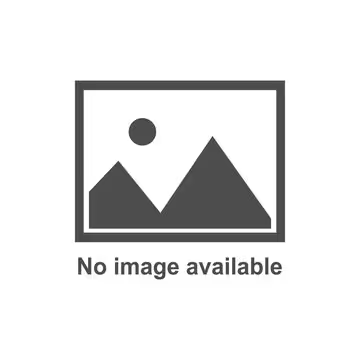
INTERVIEW – A couple of weeks ago, our editor caught up with Toyota veteran Sadao Nomura. In this Q&A, he discusses quality improvement and leadership engagement.
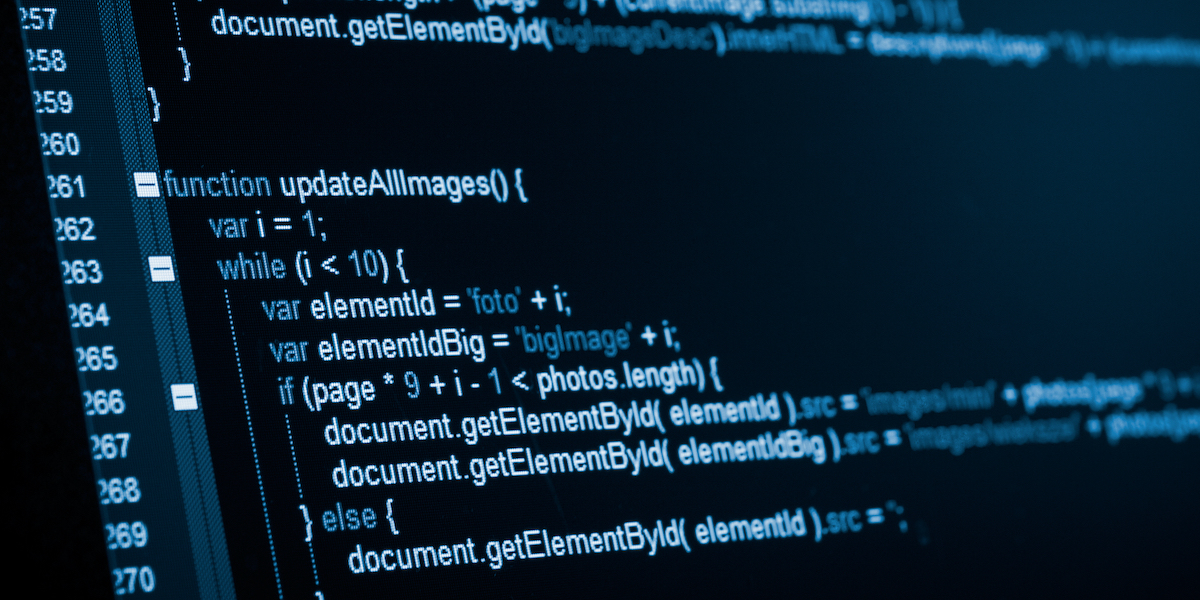
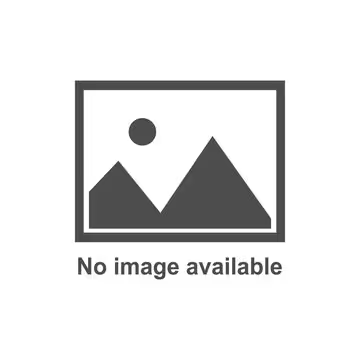
FEATURE - The author explains how a recent book on radical quality improvement in manufacturing inspired him to initiate similar experiments in his software development firm.
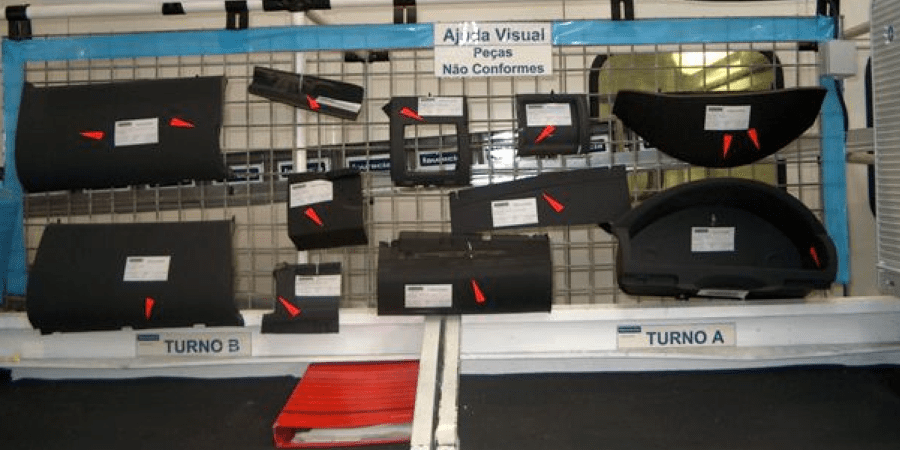
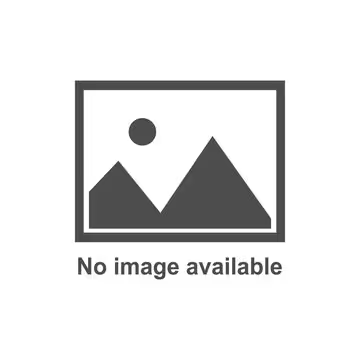
THE TOOLS CORNER – This month, the author discusses how we can ensure quality problems are identified early, tackled swiftly and prevented from reoccurring.