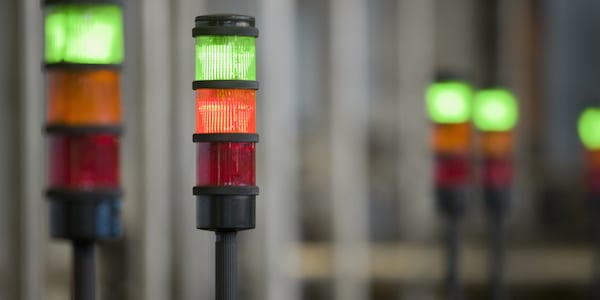
How can we help others to apply what we learn at the gemba?
WOMACK'S YOKOTEN - Given the name of this column, it only makes sense to analyze the word yokoten. So, how can we effectively help others to apply what we learn at the gemba? What makes yokoten successful?
Words: Jim Womack, Founder and Senior Advisor, Lean Enterprise Institute
Because I’ve decided to call my new monthly column Yokoten, I think I owe readers an explanation of what I mean by the term. What’s more, I need to suggest ways we can all yokoten (a brand new verb!) more successfully as a lean community.
On one level yokoten is just another of those Japanese words that some members of the lean community find so irritating; a linguistic relative of kaizen and andon and heijunka and obeya. It’s a compound of yoko, meaning horizontal, and ten, meaning expand or unfold. In sum, horizontal spread. This of course could be the spread of anything: fertilizer in a field, good ideas like TPS across an organization, or bad ideas like modern management, economic order quantities, and monument technologies across a national management culture. We hardly need to import a Japanese word into English for the simple concept of spread.
However, Toyota long ago gave yokoten a special meaning that justifies importing it into English and other languages as well: the horizontal transfer across Toyota and its suppliers of TPS thinking and successful methods. More recently, we in the lean community have given it a still broader meaning: the successful spread of lean thinking and methods across extended enterprises, different sectors of the economy, and countries. (Eventually to include the whole planet!) This grand project surely merits its own word.
Looked at another way, yokoten is a useful label for what we have been trying to do in the lean community for more than 30 years. It’s pretty much the story of my career and, I’m sure, the careers of many readers as well.
Unfortunately, yokoten hasn’t been easy. Years ago a Japanese Toyota veteran told me, “Yokoten is the really hard part.” Pioneering a new, lean practice in one place and verifying its performance gains through experiments was hard. But convincing others to embrace, deploy, and sustain proven lean ideas in the next department or across a large enterprise was much harder, even in the nurturing environment of Toyota. So it’s not surprising that the rest of us have struggled to yokoten the whole planet! Fortunately, we have also learned a great deal about the methods of yokoten, barriers to success, and the countermeasures to these barriers. Let’s begin with the methods.
I wish I could say that new ideas are best spread by books and articles. I could be a king of yokoten if this were true! But I’ve learned that while writing may play some small part, the real mechanism of yokoten is always people learning at the gemba and then applying their learning elsewhere. This means that most yokoten is the result either of employees moving from one organization where new ideas have been tried to another or consultants transferring knowledge they learned from one company in one sector in one country (often Toyota) to other companies in other sectors across the world.
The consequence of yokoten by many individuals based on many different experiences is that there tends to be a lot of noise.A lot of ideas only vaguely understood are transferred to very different situations with very mixed results. Three pervasive examples of this tendency are 5S, andon, and team leaders.
I find that 5S is the easiest yokoten there is except that it is frequently applied without any reference to whether it makes it easier for front-line value-creating employees to get their work done with less waste. A work area that is bright and shiny with yellow lines on every floor and blue squares on every desk may be good for morale but unless it eliminates waste it’s mostly interior decoration. Whoever is importing the idea of 5S needs to start with the work and the struggles of the workers and work backwards, asking what type of 5S, if any, is needed to address the struggles.
Similarly I find the entire world populated with andon lights. (I wish I had invested in whoever makes these at the time Dan Jones and I were penning Lean Thinking!) The idea is to make clear an abnormal condition at a work station so a team leader can respond to it within takt time. Yet I find andon everywhere despite the lack of team leaders or the inability of the team leader to respond within takt. So what is the purpose? Lots of electricity being burned to transmit signals that have no useful meaning!
A case in point is a plant I recently visited after a month’s absence where I found the same andon light glowing red at the same work station. The explanation: “We always have parts shortages in this area so we leave the light on to remind the materials supply team of the problem.” In short, the plant managers had learned the words but not the tune as the company tried to yokoten a useful concept. The countermeasure in this case is to work backwards from the work to ask what type of signaling is needed to obtain a response and what type of response is needed in what time frame. Without these capabilities the useful concept of andon becomes more muda.
Yet another widely yokotened concept is team leaders. A team leader is a vital need for every front-line worker but what does the team leader need to know and to do? Most fundamentally, the team leader needs to know the details of the work, the information flow triggering the work, and the materials flow supporting the work. Yet I often see team leaders who don’t know the work (and therefore can’t jump in to help) and don’t understand material and information flow. Rather than true team leaders they are junior managers who keep track of attendance and performance (these days with pervasive production control boards) without being able to countermeasure problems within takt time or improve the work.
So how can we avoid inadequate, noisy yokoten? I have three simple rules:
- Don’t spread an idea unless you actually understand it yourself. This means observing it in use on the gemba and asking a critical question about its purpose: precisely how does it create more value with fewer resources?
- Don’t transfer it literally.Every situation demands modifications.
- Treat yokoten as an experiment. Unless performance is actually improved in a new application and more value is created with fewer resources, you may be spreading ideas that shouldn’t be spread. Bad yokoten, if you will, that actually makes things worse.
As I noted earlier, this isn’t easy. It is so much more satisfying in the short run to grab a concept, find a new opportunity, and apply it quickly. But in the long run nothing may actually be improved. True yokoten requires direct observation of a method, careful adaptation of new methods to different conditions, and a healthy dose of management by science. If we all can just do this we can create a leaner planet faster.
THE AUTHOR
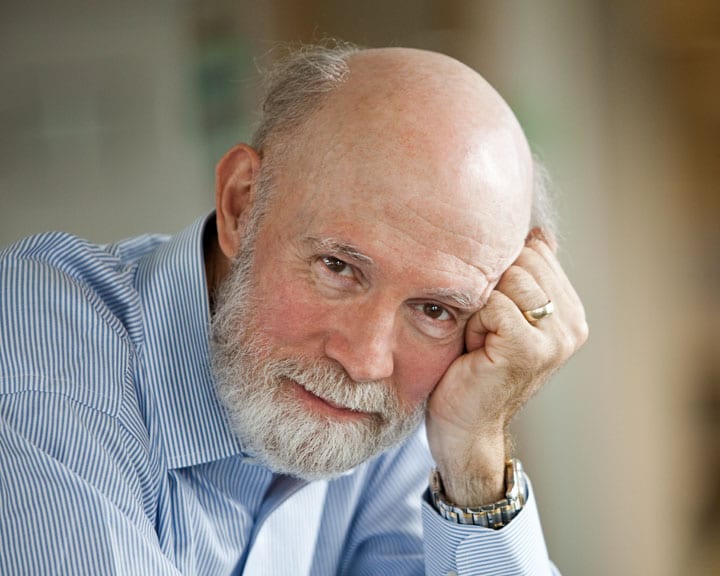
Read more
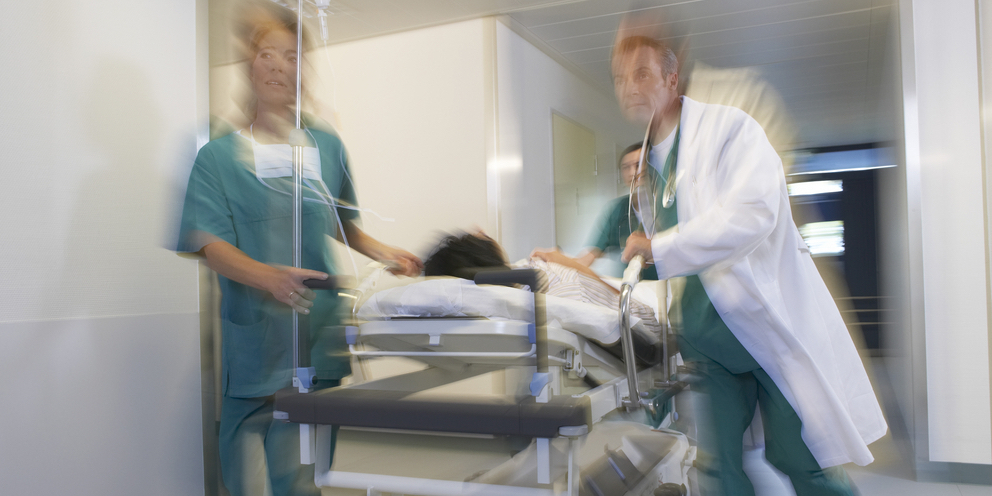
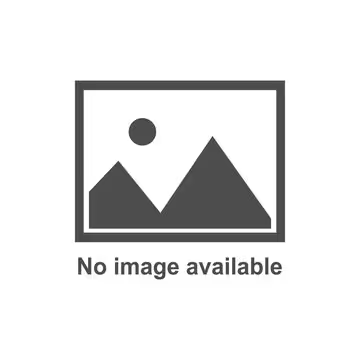
FEATURE – Our coverage of the Covid-19 emergency continues with an article discussing how lean healthcare principles can support and protect the professionals at the front line of this war.
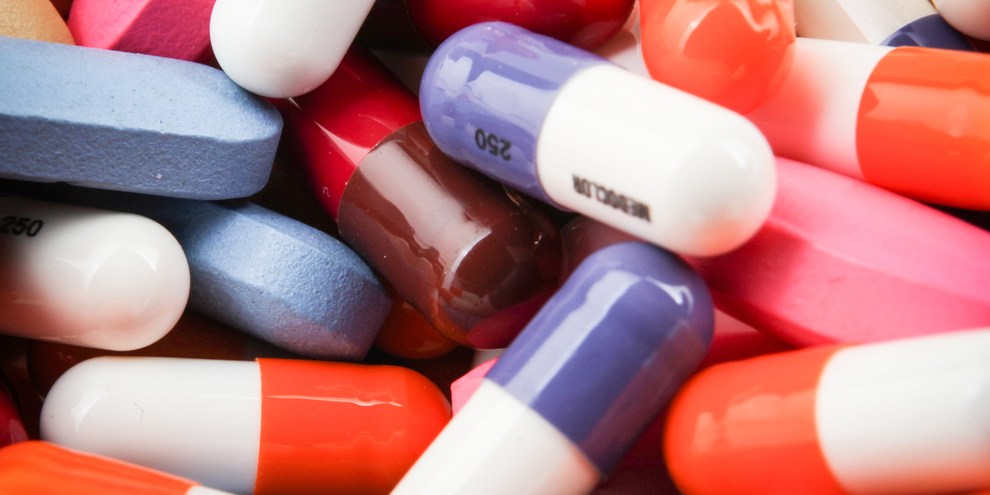
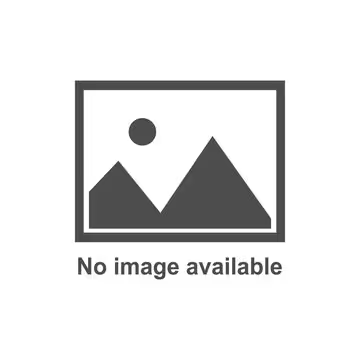
CASE STUDY – Clinical trials are known for their rigorous analysis and approval process. The experience of Roche Brasil teaches us what lean and agile thinking can do to speed it up.

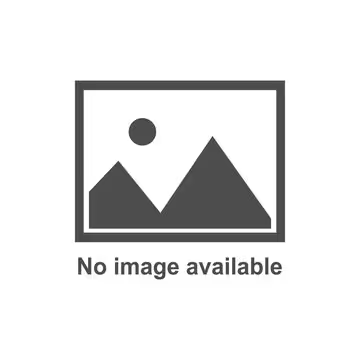
FEATURE – Lean thinking is increasingly applied end to end, reaching virtually every area and function of the enterprise, and yet in many companies IT is still left out of the lean transformation. Isn't this dangerous in a world that is going more and more digital?

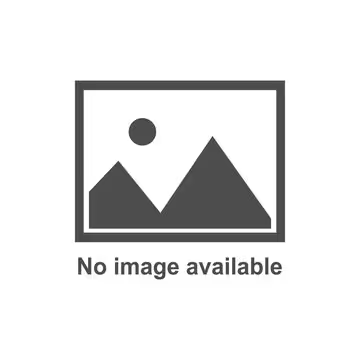
INTERVIEW – In this Q&A, we learn how the Technical & Production (T&P) area of Nestlé Colombia Ecuador is using lean and Art Smalley’s four types of problems framework to bring leadership closer to the gemba.