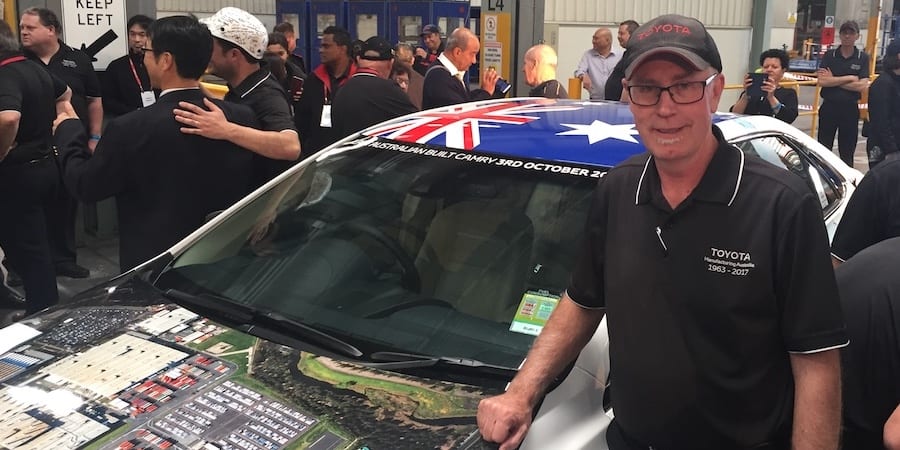
What this leader has learned in 40 years at Toyota Australia
PROFILE – What does one learn from working for Toyota over 40 years? This Australian leader has developed a unique holistic view, and a strong set of technical and social skills.
Profile on: Doug Rickarby, former Divisional Manager of Manufacturing at Toyota Australia
Words: Roberto Priolo, Managing Editor, Planet Lean
I meet Doug Rickarby on a Monday morning of mid-December at a café in Brunswick East, a few kilometers north of Melbourne CBD. It’s his first day as a non-employee of Toyota Australia in 39 years, and I am hoping to find out how that feels.
Toyota Australia shut down its Altona plant on October 3rd (Doug talks about this “lean closure” in another article for Planet Lean), a sad story with an uplifting angle thanks to the extraordinary work the company has done to help the plant’s workers to secure a future. Doug was instrumental in making the transition a success.
As we order coffee, Doug tells me he’s just come back from a weekend on Phillip Island, where he spends a fair bit of time (the fact he is a Moto GP fan is only part of it, he assures me). A weekend away is the least he could do after what must have been an incredibly emotional time.
“Because I always knew deep down that day could come, I wasn’t as shocked and surprised as most when the closure was announced. I was more ready than the average person. It certainly was very sad, but the fact that we managed so successfully in helping people prepare for the future means that I can look back with satisfaction,” he tells me.
Doug likes a challenge, and the notion of “that cannot be done” has always been a great motivator for him over the years. “Problem solving is a key driver for me, and organizational problems are something I have always liked to have a crack at,” he explains. So, it is no surprise that when the announcement of Altona’s closure came, Doug and his colleagues faced the situation head-on, determined to make the most of it.
DEVELOPING A HOLISTIC VIEW
After completing the first year of an engineering degree, Doug saw a job advertised on the paper, at Australian Motor Industries – “makers of Toyota cars”. Even though he had never heard of AMI, he applied for the job and got it.
That was a great start to Doug’s career, because he spent the first three years at AMI on the line, rotating through different jobs. This gave him a unique understanding of the work that goes into building cars (his interest in industrial engineering also helped him).
In 1982, Toyota sent Toshio Mizushima to Australia to provide TPS support to AMI, and Doug was paired up with him (the two would become very good friends). Doug recalls: “He was a very quiet guy who had worked with Ohno doing supplier development. Our job was to see how TPS might apply in a Western auto plant. Specifically, I helped Toshio navigate local culture, language, protocols, while being his voice around the organization.” In the process, Doug soaked up as much as he could. Mizushima would often ask him to take a watch, stand at the gemba, and take note of the time it took the operators to complete certain actions.
Over time, as different parts of AMI asked for help, Doug got exposed to more and more processes. “Only later could I fully grasp just how lucky I was to be in the right place at the right time. In a Toyota world with more than its share of gems, Toshio is a diamond, as a teacher, a mentor and a human being,” he continues.
By the time Mizushima finished his four-year stint down under, AMI had what was probably the first kanban system with local suppliers in Australia and ran countless lean experiments. Toyota started to buy up more and more of the company and quickly realized they had to start educating the rest of AMI in TPS if they were going to make a success of it.
To do this, Doug and his team developed training courses for groups of 20 people, coupled with real-life examples at the gemba. To support suppliers, they also piloted a Supplier Development program. When Toyota launched its partnership with GM in Australia (an initiative similar to NUMMI), Doug ran a little TPS course for the management team of the GM plant.
At this point, the direction of Doug’s career was pretty clear. In 1988, he was asked to become Human Resources Development Manager, so that he could help the company to transform the whole of the GM site. In the meantime, Toyota had decided to invest in a new facility in Altona, next to its already-existing engine plant.
Over time, it became clear that TPS was one thing, but that a big part of the success of Toyota lied in its unique management philosophy, whose elements – such as hoshin kanri – Doug gradually introduced in the skillset he wanted people to develop. He kept that training-focused HR role for around nine years, before becoming Manager of Purchasing Planning and Development in 1997.
This role gave him a lot of commercial exposure, and the opportunity to work again with Mizushima (by now he was President of Toyota UK and later became President of Toyota Europe) on observing and learning from Toyota’s Japanese suppliers like Denso or Gosai.
After that, Doug got a role as a New Model Project Manager, in which he oversaw the whole product cycle, from design to preparation to production, and beyond. This rather challenging job paid off, as it resulted in Doug being given a role in Corporate Planning to work on the development of the Toyota Australia Future Business Taskforce to redesign the company’s business model.
In 2007, he was offered to become the manager of the assembly plant at Altona, which was struggling (eight months after the launch of a model, they only had 90% efficiency). He and his team turned it around, which eventually got Doug a promotion to Divisional Manager for Manufacturing, a role he kept for a decade. “When I got to the assembly plant, the effects of the little investment in human capital that they had made up until then were painfully evident. They had constant breakdowns, and all people could do was reacting to problems rather than adopting a proactive stance. The plant was ripe for some good TPS,” he comments.
When the announcement of Altona’s closure was made, Doug had a lot of saying into how that would play out. (He and the other divisional managers were the core team.) I ask him whether the knowledge he acquired while holding so many roles in so many different departments within Toyota was useful. “Without a doubt!” he answers. “And so did the combination of my approach with that of my colleagues. My stint in HR came in handy, as I look back to those months, as did the work I did with hoshin kanri with suppliers in the Purchasing Department. What I learned about project control when I went into the assembly plant was also very useful, because once again I was being asked to turn a struggling area into something of a success.”
What’s curious is that HR was such a big part of Doug’s career, even though this was never his intention. He was, however, able to make treasure of those lessons and use them at the right time. “I feel like I have always had a pretty good understanding of people. So in that sense, I was a natural. I learned about HR experientially, which is the only way for me to learn, as I am terrible with books. I guess it’s good that Toyota’s approach to learning is based on experience at the gemba!” Doug tells me, as I urge him to drink his now-cold cappuccino.
WHAT ABOUT THE FUTURE?
Indeed, the one thing that a lean leader can't go without is an affinity with the shopfloor, and that’s certainly something Doug has. He comments: “I have always had a good relationship with people at the gemba. Whenever I went to the floor, it was great to see that people didn’t change their behavior or attitude. That was my measure of how I was perceived as a leader, because the last thing you want is for people to feel threatened by you.”
In Doug’s mind, to be a good lean leader one needs a mix of technical and social skills (“logic, good judgement and compassion,” he says): for his leadership style, these are expressed in the ability to observe and pick things up on one side and in his commitment to listening to people on the other. But as a lean thinker, he also stresses that he wants to learn to listen more and talk less – a point of “personal PDCA”.
Even though he had the option to continue with Toyota after the closure of Altona, Doug decided to go out on his own and put all of his learning to a different use, as a coach to organizations through his new company Gemba Guides. Through his years in supplier development, he enjoyed helping other companies, solving problems with them and coming up with strategies. “I have been critical of consultants all my life,” he admits, “but I intend to articulate my work differently, supporting those who were left hanging by consultants after low-hanging fruit is picked.” Doug tells me that the whole idea behind his new adventure is to get people to become independent in their ability to improve and grow their businesses sustainably – I guess you can take a man out of Toyota, but you can’t take Toyota out of a man!
As he begins a new phase in his life post-Toyota, Doug also hopes to contribute to changing the way lean thinking is perceived, filling the gap between what Jim Womack and Dan Jones intended and what’s happening. “I don’t like the fact that lean has become a bit of a dirty word after too many tried to sell it as a simplified formula. And I hate hearing companies say things like ‘we did lean last year’,” he adds. He sees his appointment as a board member of Lean Enterprise Australia (the Australian affiliate of the Lean Global Network) as another way in which he can make a difference.
As he talked about the shut-down of the Altona plant, however, it occurred to me that Doug had already made a huge difference in the lives of many people – starting with those working at Toyota Australia.
“My career has been almost entirely devoted to securing the continuation of manufacturing in Australia, and I am course disappointed to see how things have gone with Altona. I certainly regret that fact that for years we weren’t able to make enough progress at the plant,” he tells me, clearly moved. “Having said that, if I think of all the stories of people in the plant that we provided good quality employment to for so many years, I can’t help but feel satisfied and proud. We have created skills that people, communities and society as a whole can benefit from. So, it might be over, but there are important legacies.” It’s impossible to disagree.
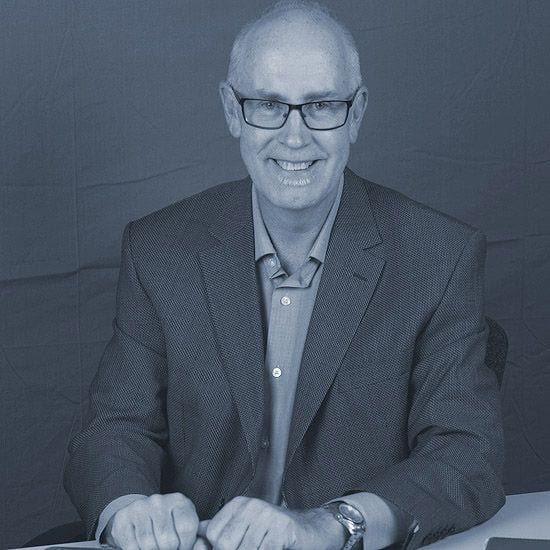
Read more
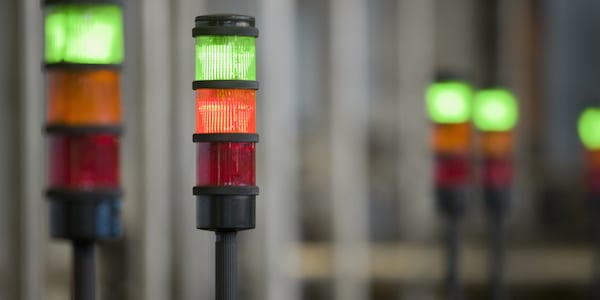
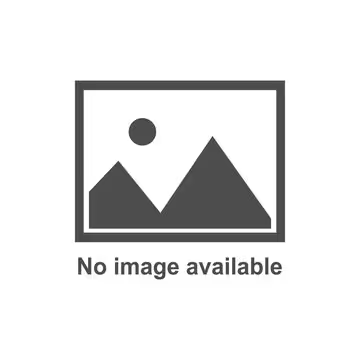
WOMACK'S YOKOTEN - Given the name of this column, it only makes sense to analyze the word yokoten. So, how can we effectively help others to apply what we learn at the gemba? What makes yokoten successful?
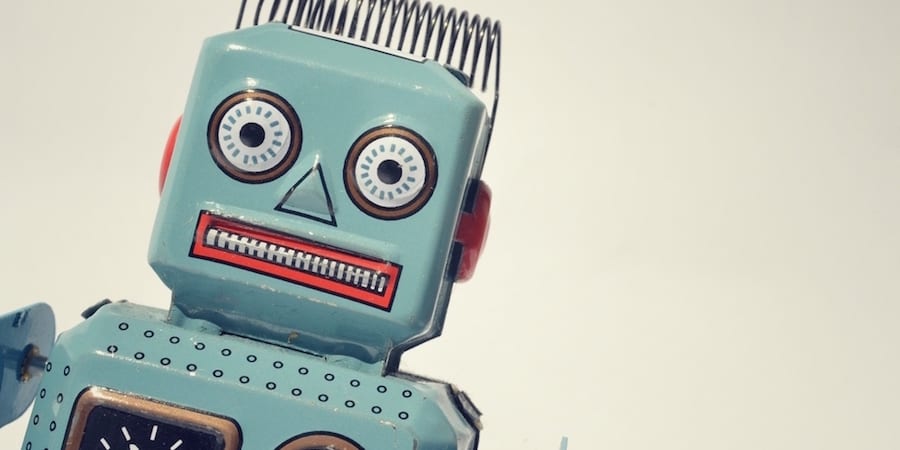
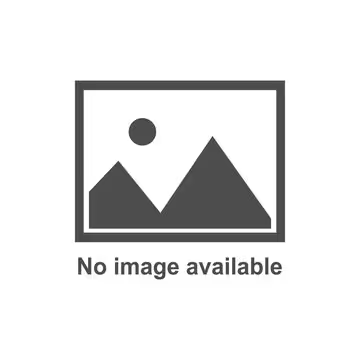
OPINION – In a competitive and unpredictable market, the temptation to rely on technology is always strong, but experience proves that there is no better support than people's ability to learn and adapt to new situations.
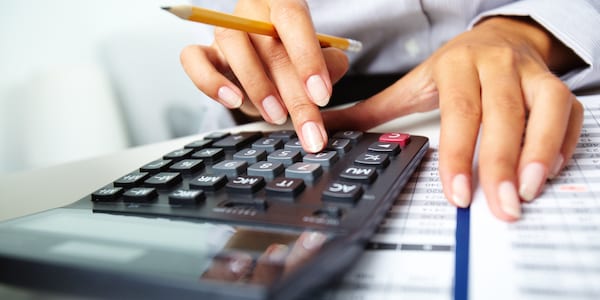
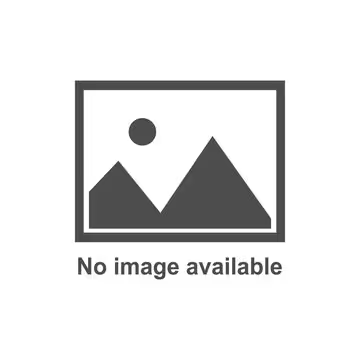
FEATURE - Every part of an organization can benefit from the adoption of lean principles, but what about accounting? Here are a few useful tips to efficiently close the books at the end of each month.
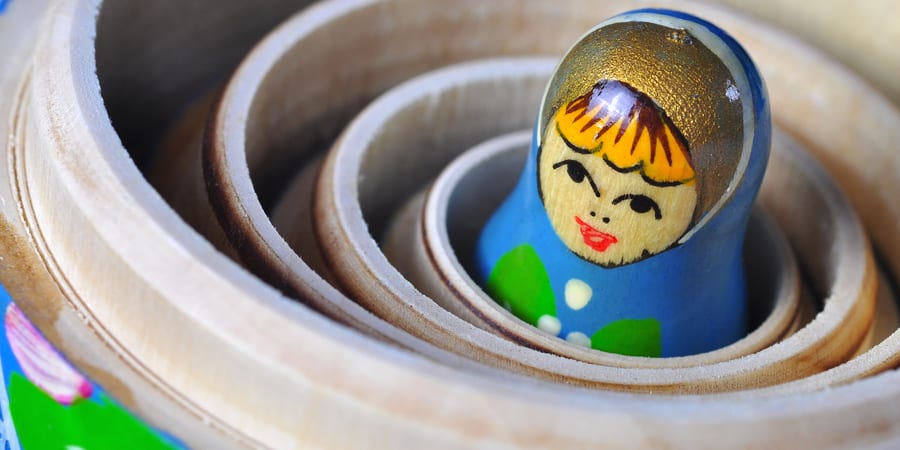
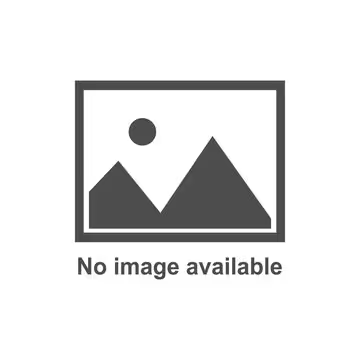
FEATURE ARTICLE - It is always fascinating to learn about the evolution of lean in other countries. This piece gives us the lowdown on the state of lean in Russia, a late adopter where interest is now growing fast in all sectors, from government to agriculture.