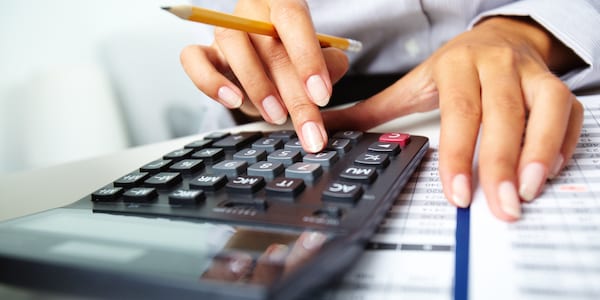
How to apply lean principles and lean tools to accounting
FEATURE - Every part of an organization can benefit from the adoption of lean principles, but what about accounting? Here are a few useful tips to efficiently close the books at the end of each month.
Words: Jean Cunningham, Principle, Jean Cunningham Consulting
Every company has an accounting department, no matter what sector they operate in, because money is the language of business and we need to record our business performance.
But on a practical level, how can we take lean principles and use them to closing the books every month? I have a few pointers for you.
If we think of some of the key lean principles, the first thing we can do is to understand who is the customer of these reports. Some of the customers will be external shareholders and owners, but predominantly we want to create reports so that our internal customers, company’s management and employees, understand and get feedback on how we are doing. It is a form of respect.
So to improve the close process, we can go out and talk to some of the people receiving our reports to understand what they need, what is missing, how precise the information needs to be. This way we can spend more time on what they are truly interested in, as opposed to what we think they are interested in and what we have previously spent time on just because “we have always done it that way.”
The second principle we can look at is the idea of small batch sizes. In manufacturing, the smaller the batch size the shorter the lead-time. What if we wanted to reduce the lead-time of a monthly close process? How can we do this? One way is to look at all the information more frequently instead of waiting until the end of the month. What shipped every single day? What materials were received every single day? What bills were paid every single day?
We can then take this information and look for insights and errors (find them earlier in the month, and they won’t perpetuate themselves through your system over time). On a daily basis you have less information to look through, and problems surface much more easily. That’s a great way to apply batch size reduction in the office. It may sound like more work to do this 20 times throughout the month rather than once at month’s end, but give it a try. Time yourself and you will find that it is not any longer, if not faster.
A third tip to close books more quickly is thinking of the items you can do before the month is over. The concept we are borrowing from the factory this time is set-up reduction.
One of the basic concepts of set-up reduction is to understand what the activities are that can happen in parallel during your last runs rather than after the machine stops. Same thing we can do with closing books – what can we do before month’s end while the work is still happening? Good candidates for such activities are things like estimates, accruals, accounts payable, inputting all your payroll entries, all the things you know before the month is over.
Here’s another tip you can use, especially for those items that are more estimate-oriented. Say you promise to ship a machine on a Friday. This means you probably have a production schedule showing the machine is ready before the promised ship date. We can do the same in accounting: we know our month ends on the 31st, but we can measure some items from the 29th to the 29th. We still have a full month’s end, but we are anticipating the end of the month. Examples? Inventory reserves, royalty payments, commissions, and other things that don’t need to tie to a perfect month but have to reflect a month’s worth of information.
The final suggestion, and I believe this is a good idea in any kind of work, is to use the data you have and measure the errors and how many times we need to rework that information. You can then use that as a basis for your problem solving. A great metric for the close is the number of manual entries for each close, for which you can create reduction targets. This way the information is naturally correct and does not require manipulation.
THE AUTHOR
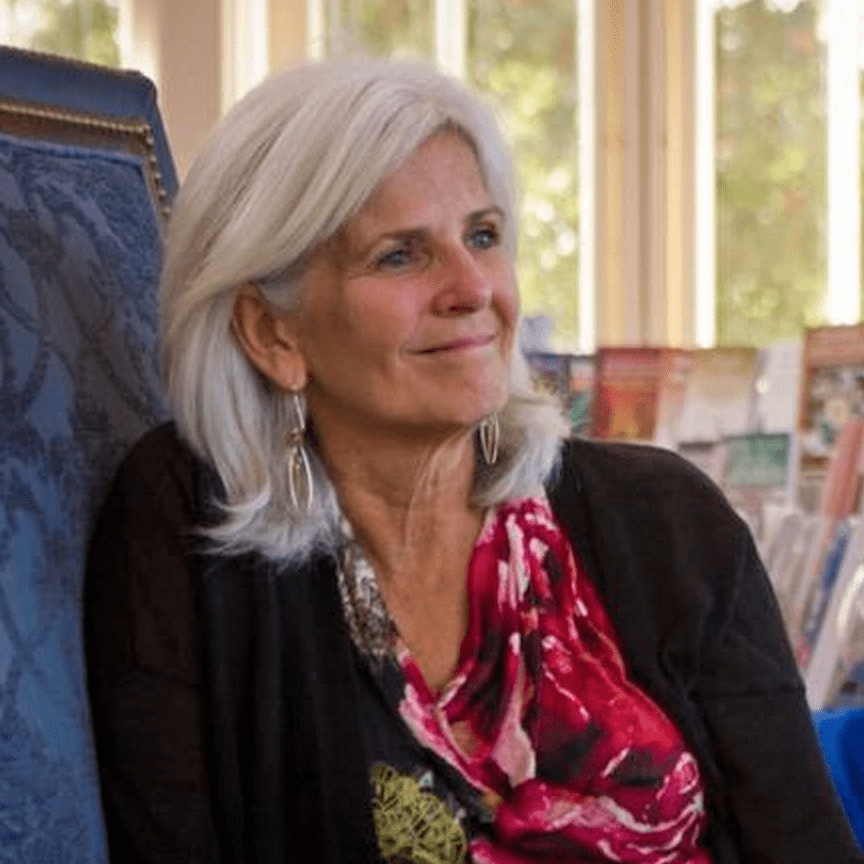
Read more
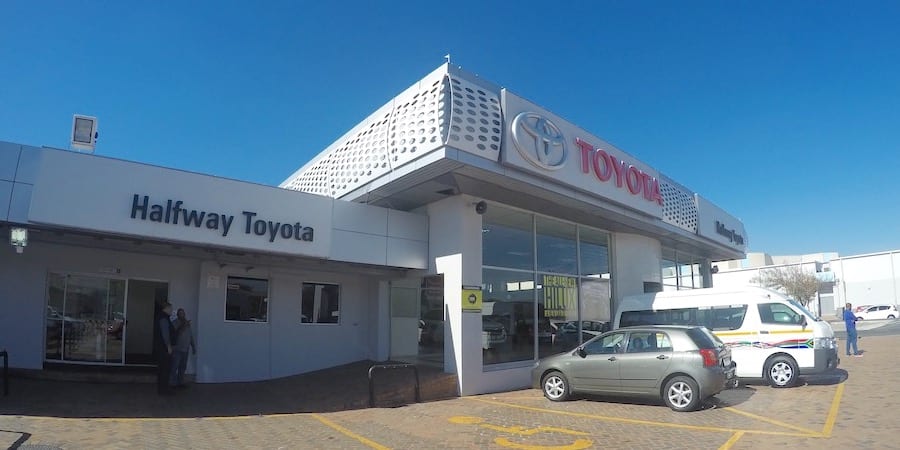
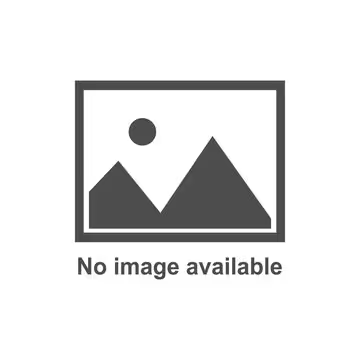
FEATURE – For the first article in our series on the Halfway transformation, we asked the Sales team to tell us about how they apply lean to selling cars in a challenging social context.
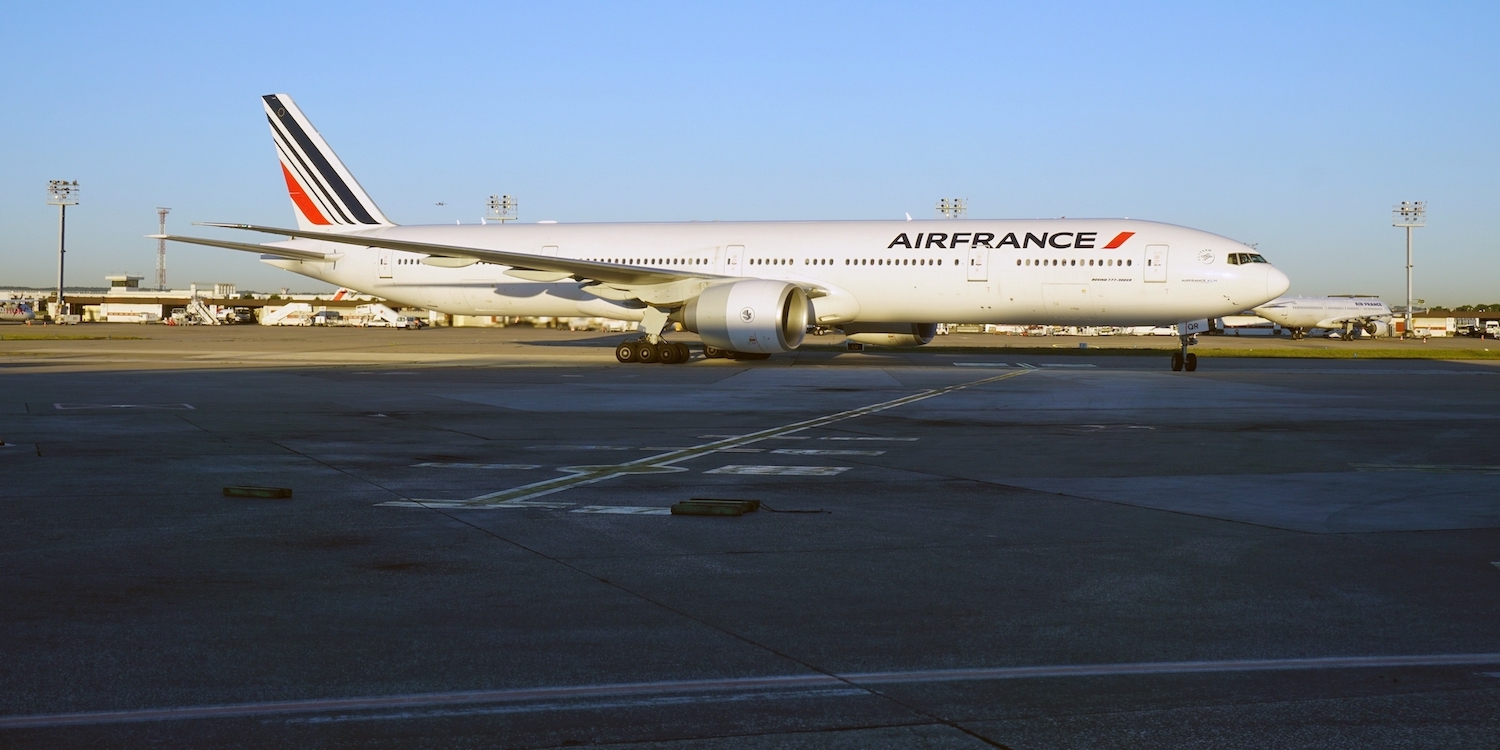
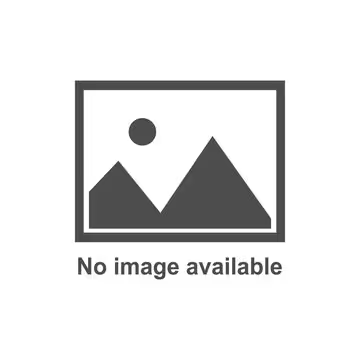
NOTES FROM THE GEMBA – The author visits the Parisian airport of Orly to learn about a pilot project (pun intended) that aims to tackle the late departure of flights using lean thinking.
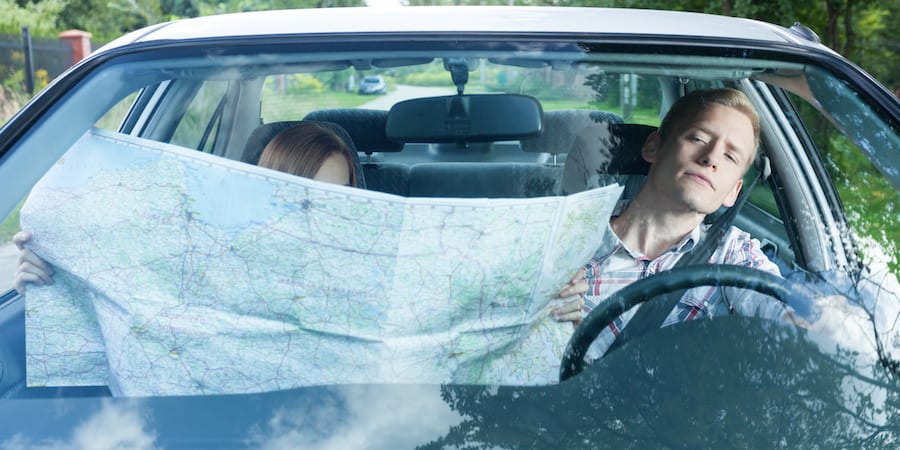
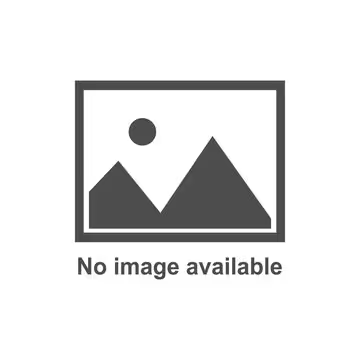
COLUMN – With many of us about to leave for our summer vacations, the importance of planning (a holiday just like a business venture) could not be clearer. But objectives and potential problems should be identified before setting off.
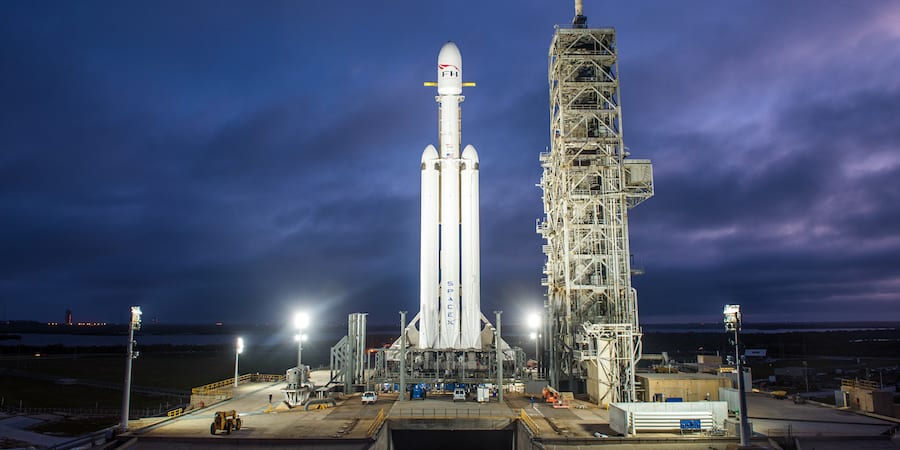
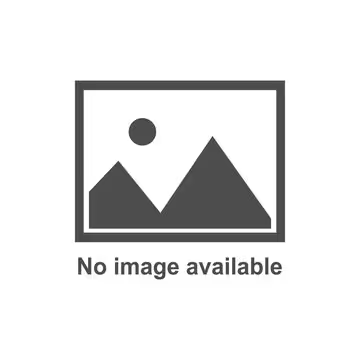
WOMACK’S YOKOTEN – In his first column of 2018, the author looks at one of the most talked about companies in the world, Tesla, from a lean point of view.