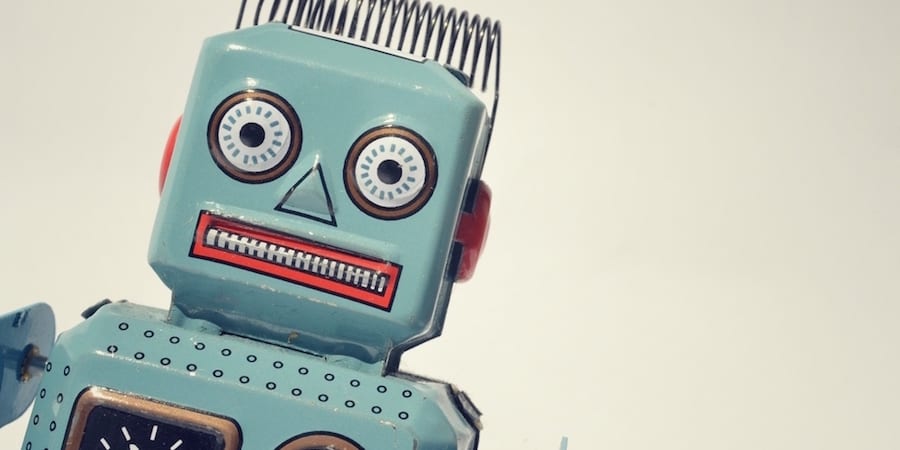
When technology hinders our ability to innovate
OPINION – In a competitive and unpredictable market, the temptation to rely on technology is always strong, but experience proves that there is no better support than people's ability to learn and adapt to new situations.
Words: Boaz Tamir, President, Israel Lean Enterprise
There was a car accident near my house recently. A driver turned left at a traffic light, while another car (which was also in a left-turn lane) went straight ahead and crashed into her. It turned out that the young man who caused the accident was using Waze, and that it was the navigation app that had told him to go straight.
There is lots to learn from this all-too-common story. Who hasn't experienced that feeling of hopelessness that prevails when the navigation system goes wild at a busy intersection? We've become so reliant on technology that we have disconnected ourselves from our own intuition and perception of space: it's as if we didn't know how to stop, look for an address, reach a familiar location or ask for directions without an automated voice guiding us.
The advantages of tools and applications are clear in relatively stable environments with a limited number of variables (like traffic, for example), but I fear the over-use of Apps, automation, and tools is actually damaging our ability to think, learn and work things out as we go.
This applies to our personal lives (and how we use our phones, for instance) as much as it does to the business world. In the lean community, we are all too familiar with the tendency to turn to consultants and expensive IT solutions rather than focus on developing people's capabilities.
We seem to forget that technology is a human creation, and even the smartest gadget and piece of software can only deal with the limited number of variables – those that the machine's creator was able to iidentify at the development stage. They can't do anything to predict and deal with the unfamiliar future: the common vision of "learning machines" and robots that repair themselves and evolve without human intervention still belongs in sci-fi movies.
It is people's creativity and ability to think that makes our endeavors succeed and innovation possible, not the use of ever-smarter technology. The mistakes we make as humans as we try to fix a problem by means of an innovative solution serve as the basis for learning and allow us to deal with the unexpected, whereas dependence on technology makes us complacent and less able to think (even though it can make a process more efficient).
In my work with product development teams, I have become fully aware of people's yearning for tools, methods, formulas, benchmarks, or at least clear and precise instructions that they hope will make things easier. This need is entirely understandable – and it happens to cater to the ego of consultants who claim to carry the solution to any problem in their toll box – and is nothing but another expression of the overdependence on technology discussed in this article (the norm in the business world). Professional integrity, however, should encourage development professionals to be wary of over-using tools: it might make them feel less helpless for a moment, but it actually provides no support to the creation of an organic learning process that makes it possible to create something new.
In Lean Product and Process Development thinking, innovation is the result of individual efforts and teamwork, achieved through the development of personal and social skills. Technology should be seen as an enabler in the research process, but it's important to understand that it is not an alternative to organized learning and human experience. Gathering information through a series of scientific experiments (PDCA) should always precede the use of technology.
Life in changing and unpredictable environments isn't simple. To cope, we have to put human beings before machines, and our internal compass before a GPS. Ignoring this basic idea will hinder the efforts to innovate of the entire organization, and take away our ability to use our brain.
THE AUTHOR
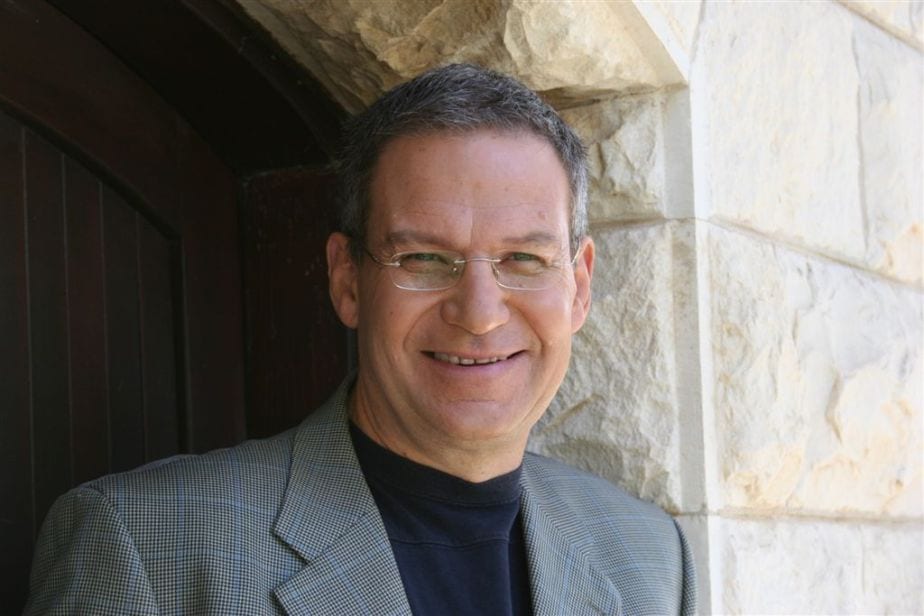
Read more
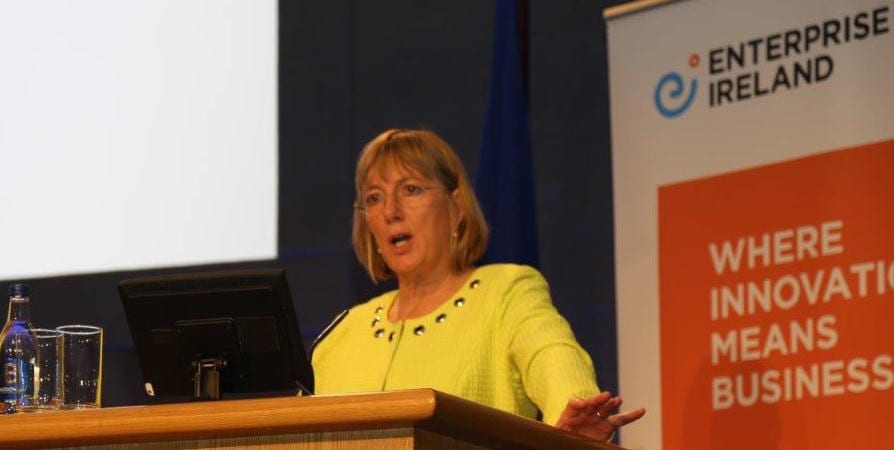
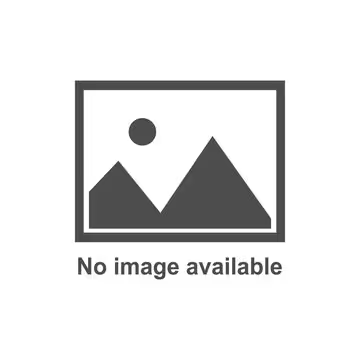
RESEARCH – This insightful paper explains how the Irish government is encouraging organizations to adopt lean thinking to improve their competitiveness with the Lean Business Offer.
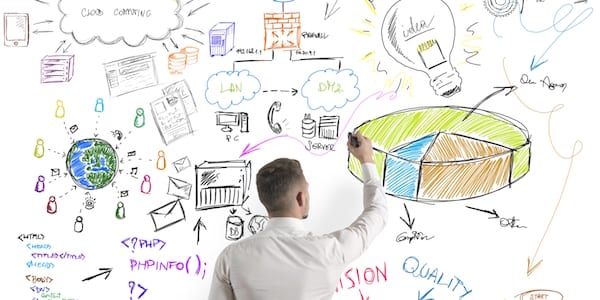
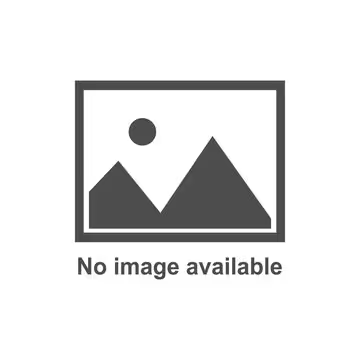
COLUMN - For her latest column, Sari Torkkola describes the initial steps that must be taken to move towards becoming a lean CIO and warn us against some of the pitfalls along the way.
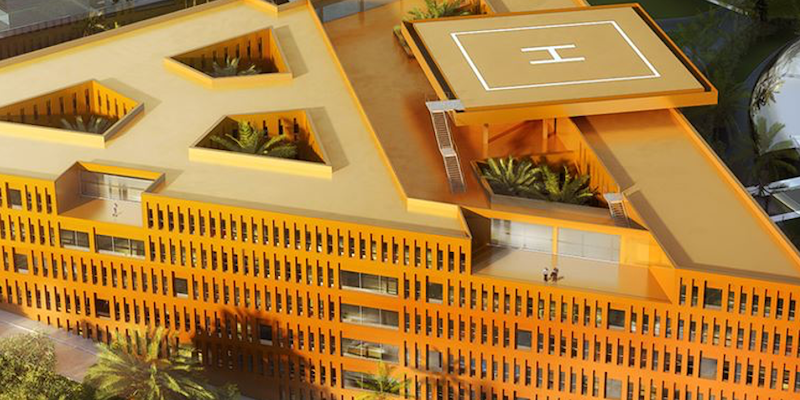
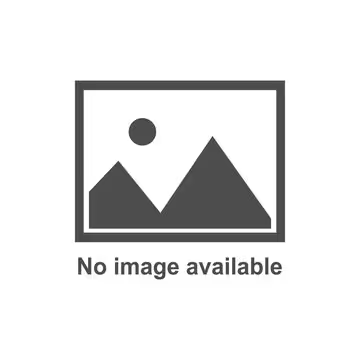
NOTES FROM THE (VIRTUAL) GEMBA – In the last of her series of virtual gemba walks, the author learns how a hospital in the Caribbean island of Martinique relied on Lean Thinking in its fight against the Coronavirus.
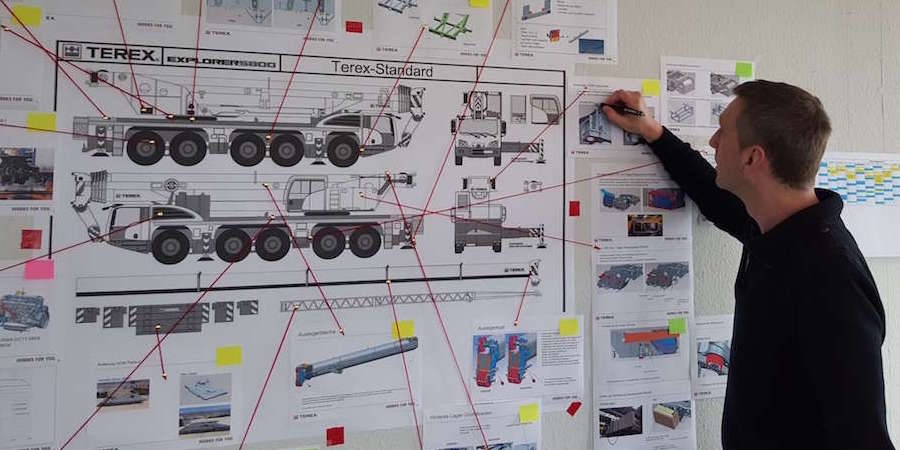
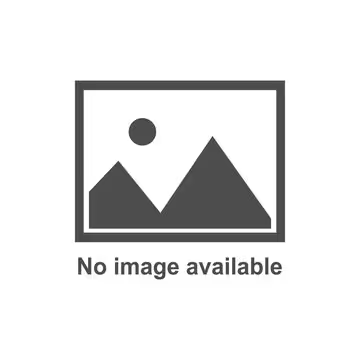
NOTES FROM THE GEMBA – In the past 15 months Terex Cranes has successfully initiated a lean transformation. Follow Catherine Chabiron on her gemba walk to see what this large company is doing to put learning at the heart of its activities.