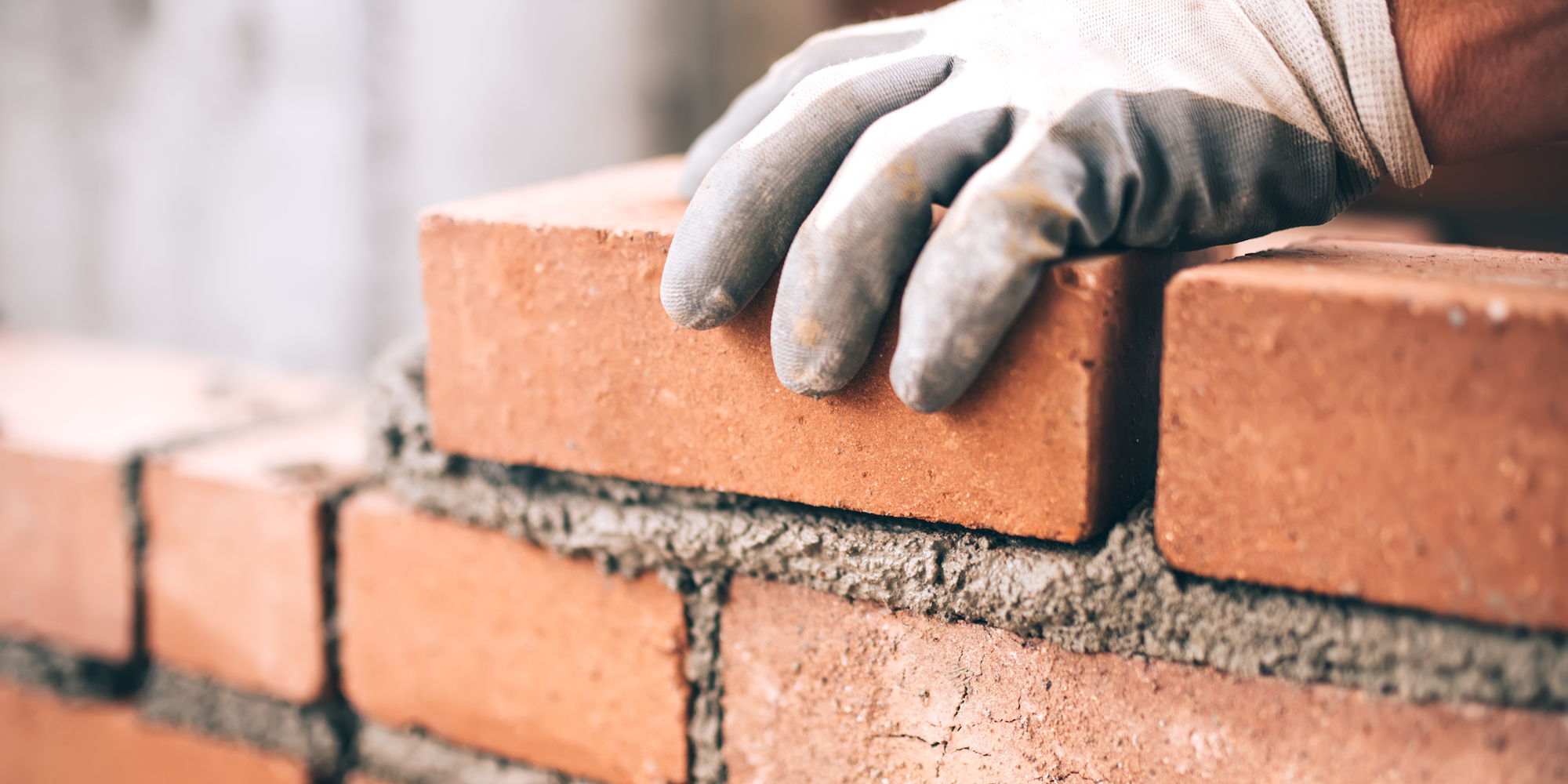
Laying the foundations of a leaner industry
INTERVIEW – The editors of Planet Lean and Lean Post recently met with a senior executive of Turner Construction in New York City. Together, they discussed leadership development, respect for people, and the future of the industry.
Interviewee: Charles F. Murphy, Senior Vice President of the New York business unit of Turner Construction Company
Interviewers: Roberto Priolo, Editor, Planet Lean and Tom Ehrenfeld, Editor, Lean Post
Roberto Priolo: Turner Construction has embarked on a leadership development program facilitated by the Lean Enterprise Institute, with a specific focus on A3 problem solving. Nine months in, what are your reflections?
Charles Murphy: By developing coaches, we are hoping to create something of a ripple effect. We want the students to become the teachers, so to speak, by sparking the curiosity of people and giving them all the mentoring and guidance they need. When we learn new things, we synthesize them to an extent; well, our hope is that our people will synthesize the lean message further and really apply to every-day work at Turner.
As I look back at the experience with our first two cohorts of general managers and department heads who have taken part in this development program, I can’t help but think of all the things it’s opened our eyes to. For instance, this initiative is enabling us to engage with our high-potential staff in a way we never could before. Across the five business units under the New York region, we are seeing the benefits of exposing people to different ways of doing things – both the coaches and coachees.
Another thing we have learned over the past few months is how much work and patience it takes to simply understand what’s going on. Take the software we use to ensure non-conforming work is corrected before project completion, for example: I needed to access the system to work on my A3 and it was so painful to go see and understand what the actual issues were and to think that our people deal with it every day! At management level, we would have never realized how urgent it was for us to improve this IT tool, had it not been for this development program. The nitty-gritty that happens at the gemba is not something we were typically exposed to. Now we have an opportunity to do so, and the fact that we are not the experts allowed us to ask lots of questions. This is a huge change.
Tom Ehrenfeld: As you look at the first two cohorts, do you think there are specific character traits that make people more or less predisposed to lean thinking?
CM: I do. In general, if you just accept things as they are and don’t question the status quo, in my mind you are not predisposed to lean. You need to be prepared to do the work it takes to know, not just assume. Most of the people in our two cohorts, after some learning, understood the difference. The cohort members who were more focused on completing tasks rather than answering the question “how do I know” weren’t as successful.
TE: Lean has brought dramatic improvement to the automotive industry. Are there specific challenges for Turner and the construction industry that you think lean can help you tackle?
CM: As an industry, we aren’t any more efficient in 2018 than we were in 1958. We just haven’t progressed very far. Masons puts a block on a block on a block, just like they did 2,000 years ago. We have seen improvements in quality and safety, of course, but even these are not where they should be.
The difficulty with improving construction is that every job is different. With each new site, you are looking at different subcontractors, different plans and specifications, and different circumstances. Part of our challenge is finding way to be more efficient in this scenario. The lean approach, to me, is an experiment, based on the feedback we get from our foremen about the improvement we introduce. Go back to the 1970s, and the relationship between workmen and management would have been very different. There are still some companies out there with very little regard for workers, their working conditions and their safety, and that to me is just bizarre. Large construction companies like Turner have a role to play, because they can demand subcontractors behave a certain way. We can try experiments with our subcontractor partners that improve production, safety and quality. As a sector, it is clear we are in search of a new model and I believe lean should be a part of that.
RP: Indeed, you are saying you’d like to transform the construction industry, not just Turner. Can you elaborate more on that?
CM: You set yourself with a lofty problem to solve and typically nothing happens. So, to change the industry, we have to start with small problems. We are going for small, incremental improvements and see where they take us. If we can get people to think differently and develop a continuous improvement mindset, the benefits would be huge for everyone in construction – no matter how long it takes to get there.
Ninety percent of the work we do is subcontracted, and these companies work for many of our competitors as well. I can’t imagine them behaving in one way with us and in another way with our competitors. Whether it’s safety, quality, production system, to me it just makes sense for us to contribute to the improvement of the whole industry. Because we share subcontractors and their workmen with competitors, it will be by default that the industry gets better if we get better. If we can develop a lean culture here at Turner and move from workarounds to resolving the right problems as they occur, we will become a better company and the industry will have to get better, too.
This doesn’t mean we’re not going to continue to compete in our markets. We are, but there is nothing wrong with having a collegial approach to things like safety. If we can make construction jobs safer, why wouldn’t we share that with the rest of the industry?
TE: The idea of safety goes hand in hand with the lean principle of respecting people. How are you using lea
n to build on your existing safety initiatives?
CM: We have had programs making the work safer for some time now and, whether we planned it that way or just ended up with it, that program and our lean transformation are now going hand in hand. To me, lean is overarching: if you can instill a lean culture in the business, you are going to become a safer company. It’s the beauty of lean. The benefits that lean brings you tend to compound – quality goes up, cost goes down, safety improves, and so on.
TE: During our visit to Turner, we have met very impressive people who sound passionate about the changes they make. Do you see a different way of thinking developing?
CM: I do, and it is interesting to see how the light goes on for different people, as they take the time to analyze the situation and discover the root cause of a problem. Finding out problems and figuring out how to solve them – which people will do, given the chance – is transforming the way people approach the work. Our project team for a new building at Columbia University realized that their failure to schedule timely meetings with many different stakeholders was delaying the project. After looking into the problem in depth, they decided to schedule the meeting one month ahead of time, which gave them a better chance of staying on track. They became aware of a problem they didn’t know they had and changed their approach accordingly.
RP: What’s next on your lean journey?
CM: We want to continue tapping into the potential of our people and building on the success of the first two cohorts. We need to get success stories out – like Doug Cooper’s – so that more people understand the benefits of embracing lean thinking and feel compelled to take it on.
We are starting a third cohort shortly and a fourth one in July. Sixty people will have gone through the leadership development program, and we are hoping to get at least 20 coaches out of the group. We are hoping to see everyone who took the course begin to work with their teams and share what they have learned. This will allow us to gradually build an organization that can identify the right problems to solve and implement the changes it identifies as necessary.
As far as our production system goes, we will continue to train people in the use of Last Planner System™ (30% of our people have already gone through the training). We are planning to have five classes of 20 people this year.
We are also trying to look at the value-adding work along the value stream. If we can get 60 key subcontractors to perform better, we are confident we can change the industry. To do this, the plan is to engage with the subcontractors and the unions to discuss together how to improve safety on the job.
Finally, I want our management system to improve. This occurred to me during a recent visit to furniture manufacturer Herman Miller and I was really struck by what I saw there and what the possibilities could be for our organization.
This interview is being published simultaneously on Planet Lean and its sister publication, the Lean Post.
THE INTERVIEWEE

Charles F. Murphy is Senior Vice President of the New York business unit of Turner Construction Company. With 30+ years in the industry and his whole career spent at Turner, Charles is a construction veteran. His first position in 1978 was as an engineering assistant in the firm’s Philadelphia office. In the years that followed, he was promoted positions of greater responsibility in Philadelphia and, in 1990, was transferred to the New Jersey business unit as chief estimator. In 1998, he moved to the New York unit as chief estimator. In 2002, Mr. Murphy was promoted to vice president of healthcare. He was named Vice President & General Manager in early 2005. In December 2006 he was promoted to Senior Vice President.
Read more
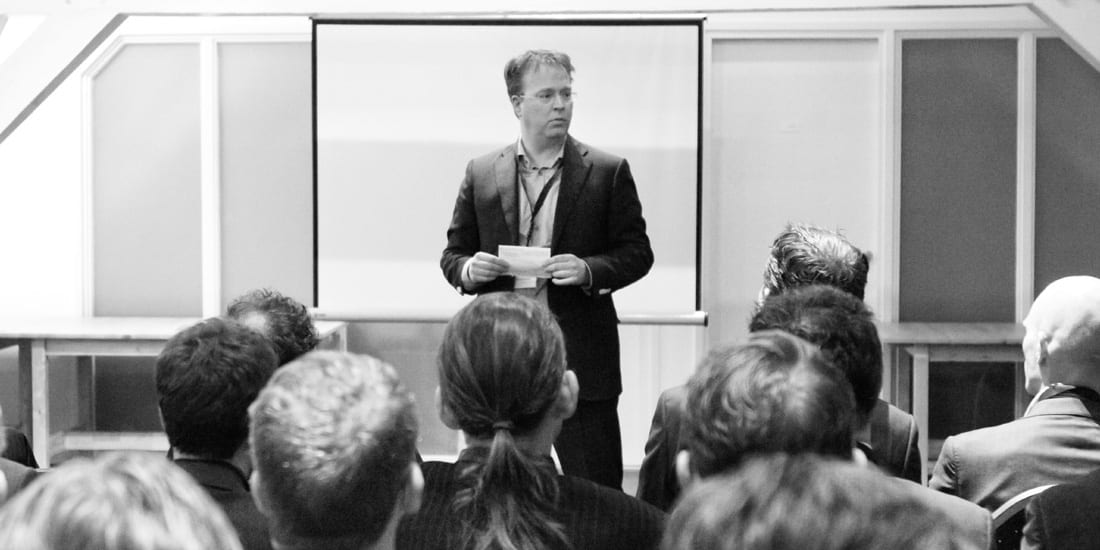
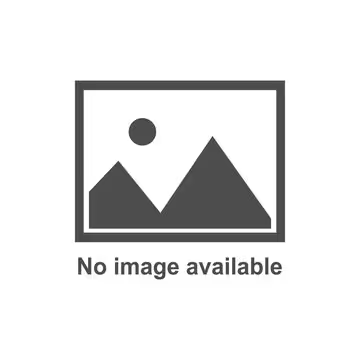
GETTING TO KNOW US – We continue our series of interviews with key Lean Global Network people with a chat with the President of Holland-based Lean Management Instituut.
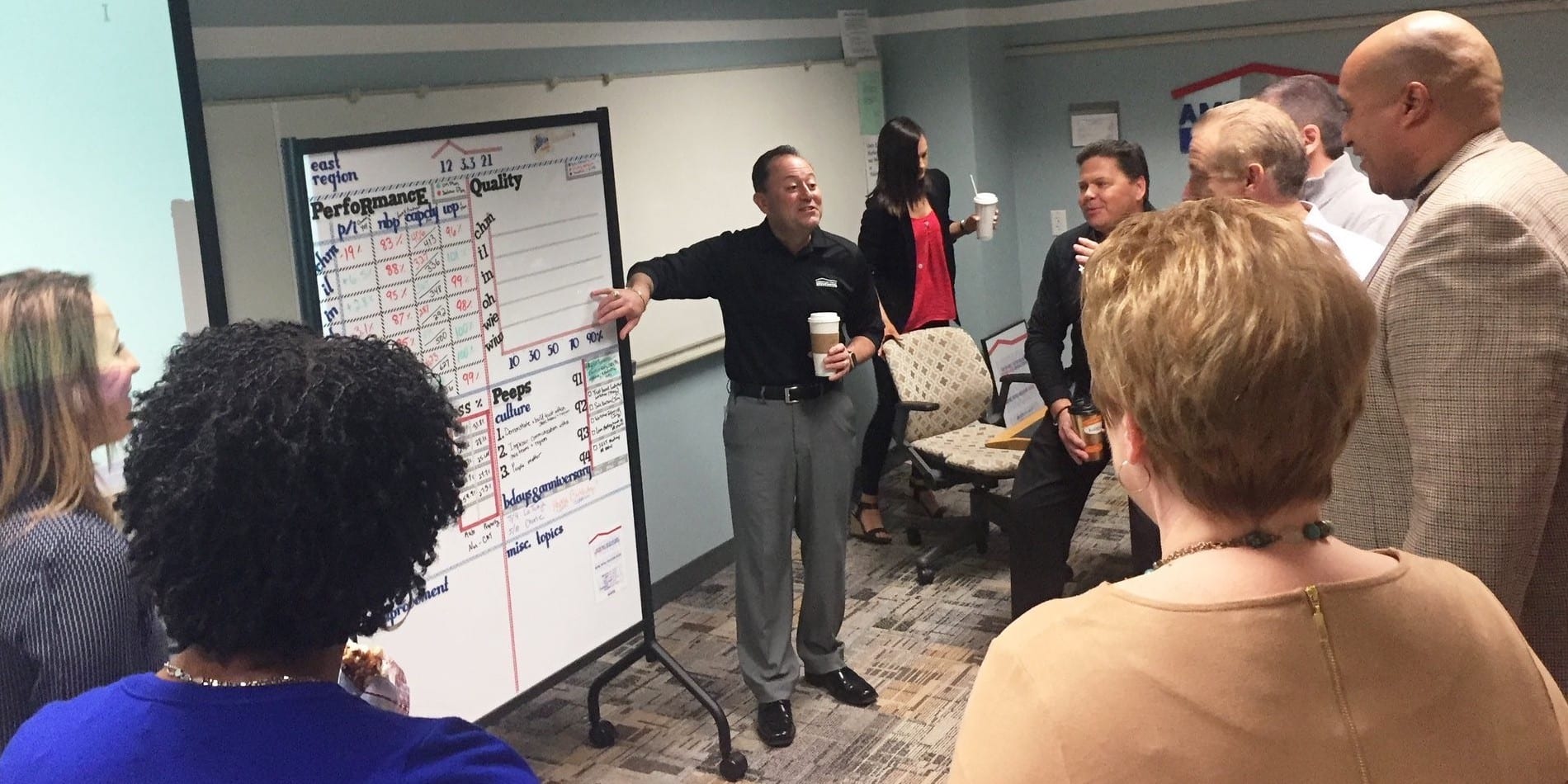
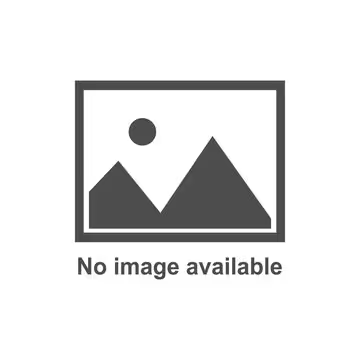
INTERVIEW – With a long history of improvement efforts and a commitment to giving divisions the time to really grasp lean thinking, American Family Insurance is laying the foundation for real and lasting change.

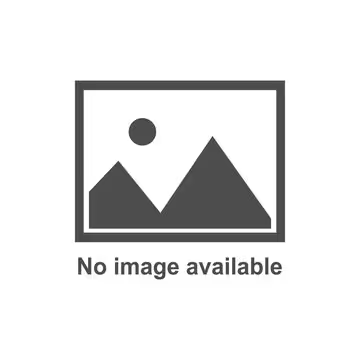
FEATURE – Philips has embarked in an ambitious development program for lean executives, which is helping the organization make substantial progress in their transformation.

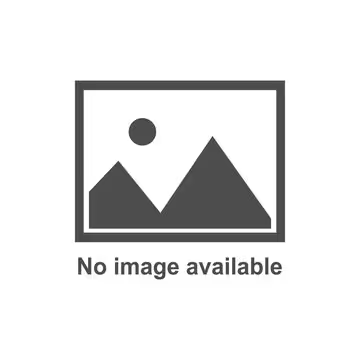
FEATURE – To develop a lean culture means to develop each lean thinker and help them reach their full potential. Here’s how Aramis Group does it.