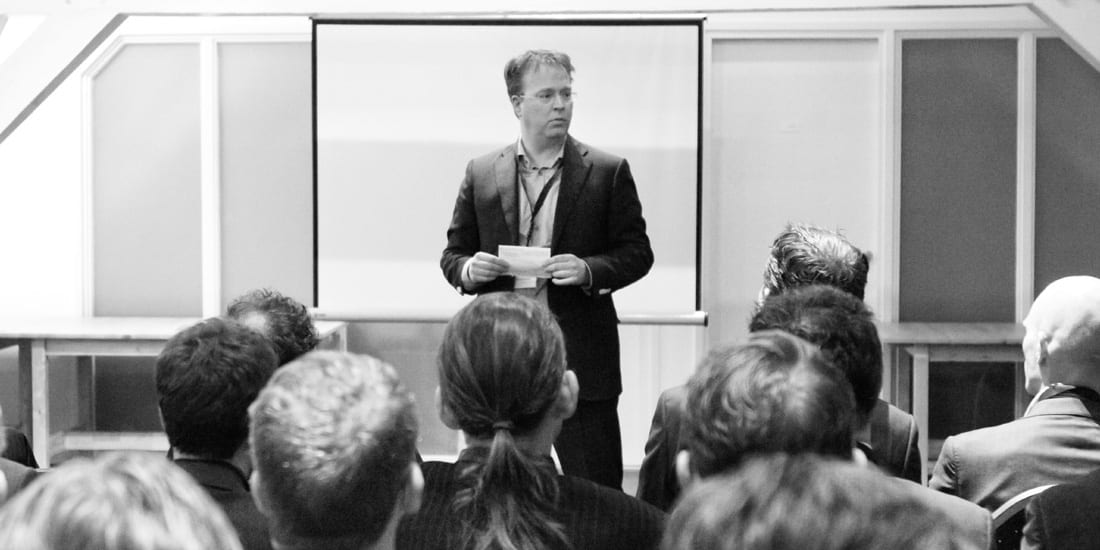
Making the Netherlands leaner and leaner
GETTING TO KNOW US – We continue our series of interviews with key Lean Global Network people with a chat with the President of Holland-based Lean Management Instituut.
Interviewee: René Aernoudts, President, Lean Management Instituut – The Netherlands
Planet Lean: What’s your background? How did you get to learn about lean thinking in the first place?
René Aernoudts: After studying business economics, I became a lecturer in business schools here in the Netherlands. After a while, I decided to make a change. I wanted to work in organizations, where the action was. I was at the Flower Auction for a while, until I started working as a junior consultant, then senior consultant, then director in a consulting firm. I did that for seven and half years.
In 1997, my boss gave me the book Lean Thinking, telling me it was something for me. That’s when I got excited about lean and ran my first ever lean project. It was a success, and I immediately decided I wanted to learn more. My career was forever changed.
In 1998, I met Dan Jones. A few years later, in 2004, I decided to leave the consulting firm and set up the Dutch institute, Lean Management Instituut (LMI). We have been working since then on the typical value streams: selling books, organizing events, delivering coaching and on-the-job training, and facilitating company transformations.
For the past three years, I have also been a director at Nyenrode Business School. I have been an Executive Committee member of Lean Global Network for the past nine years.
PL: Holland is a saturated market when it comes to lean. What can you tell us about the state of lean in the Netherlands? And what sets LMI apart?
RA: In the Netherlands, lean ideas are taught in school, in universities and in MBA programs. This means there is a relatively high level of lean adoption in the country, but it also means there is also a lot of competition for us as an institute. Nonetheless, a lot of what we see around the country is “fake lean”, which is unfortunately giving the whole movement a bad name. Too often, lean is seen as the implementation of a few tools, to grab low-hanging fruit, while real and lasting transformations are still rare.
Many people still misunderstand what lean is, thinking it is only about process improvement. I find this very frustrating, although to an extent the tendency to adopt the latest buzzword has always been there. These days, “customer journeys” seems to be on everybody’s lips, even though that’s exactly what Jim and Dan were talking about in Lean Solutions in 2005! There is a lot of ignorance about lean out there, and we need to address it if we are going to spread this revolutionary way of managing.
At LMI we try to do things differently. Where most consulting firms roll out lean in organizations, we focus on helping firms tackle real business problems using lean as a means to an end, rather than the end in itself. Our focus is on solving organizational problems as efficiently and effectively as we can, not on maximizing our profit.
PL: What is the institute currently working on and where do you see it go in the next few years?
RA: We don’t have much mass production in the Netherlands, but we do have a lot of service organizations, construction company, and of course government. Around half of LMI’s work is with not-for-profit organizations (from housing associations to government). Over the years, we have seen we can have a major impact on government organizations, which we typically help with strategy deployment to reduce lead-times in providing services to citizens. I want to continue down that path.
We also have systemic challenges in healthcare, and I think we can contribute to tackling them. Doing good for society is why I got into lean in the first place, so that only makes sense to me.
PL: As an Executive Board member of the Lean Global Network, what do you think are LGN’s strengths?
RA: What makes the Lean Global Network unique is the high level of knowledge and the quality of our people. We are united in our belief that what Jim Womack and Dan Jones started is quite remarkable, and we strive to stay true to that lean spirit. This means we try to stick to the original lean promise of making the world a better place. We have this great method, vision, philosophy, and we see how it can help leaders and organizations create more value. We are interested in helping people make a difference.
Another unique factor is the fact that at LGN we have knowledge and experiences from all around the world, something that enriches us greatly. We have dozens of people of all ages, backgrounds, nationalities who are working together towards a common goal – spreading lean thinking and practice around the world – and that makes me really proud. We work across borders, religious and cultural differences. We accept that we are different, but we are also respectful of diversity and find great value in it. We try to practice what we preach, engaging in continuous PDCA. I don’t know of any other organization where there is so much openness to working together. We share a passion, and that’s unbeatable.
PL: There are many improvement methodologies out there, and some of them are getting more attention than lean. What can we do to fill that gap?
RA: I like the fact that there is no copyright on lean, which is essentially a gift that developed through the centuries (check out John Shook’s article to learn about the roots of lean thinking) until it came to us in the form we know it today. I am glad Jim and Dan didn’t make a business of this, even though this often means that the lean message gets diluted over time. It’s a trade-off we are familiar with. We must be aware of this situation, and focus on marketing our ideas better. That’s why I think initiatives like Planet Lean are so important.
THE INTERVIEWEE

Read more
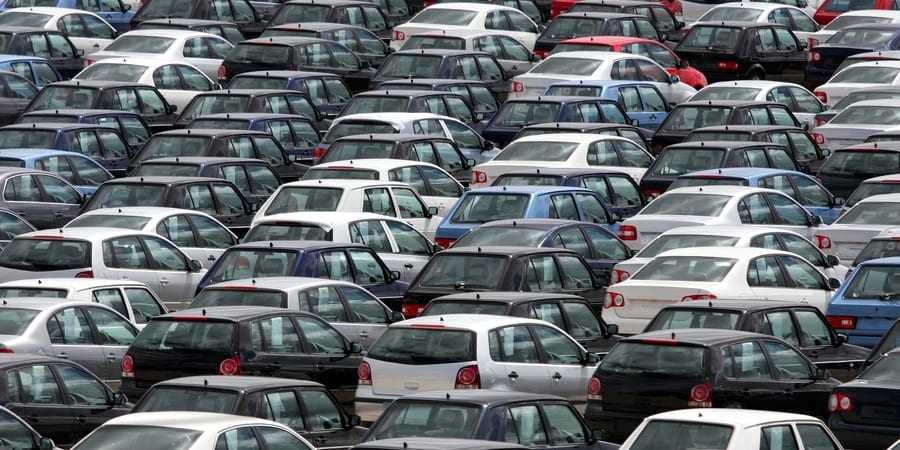
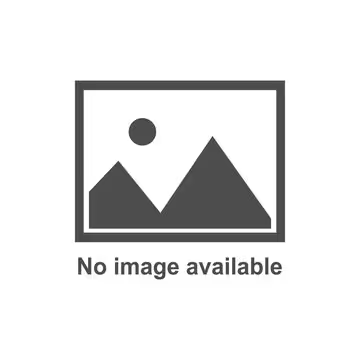
WOMACK’S YOKOTEN – The sharing economy came with a very “lean” promise – underutilized resources made available to those who need them for a reasonable fee – but not all that glitters is gold.
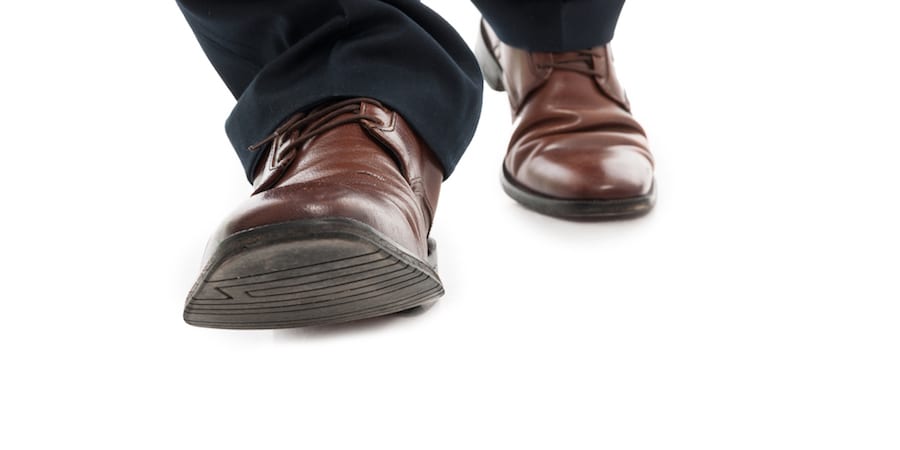
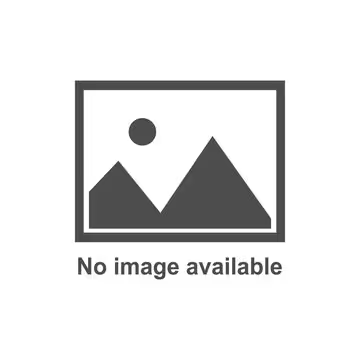
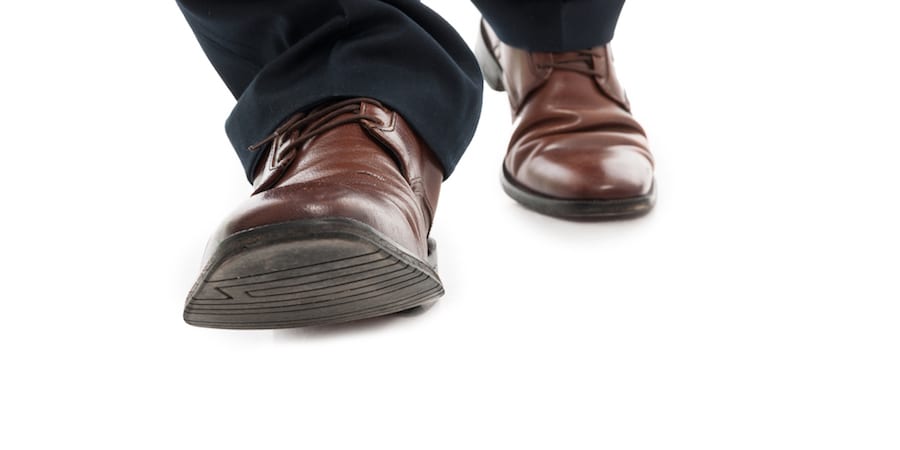
FEATURE – Lean encourages us to go to the gemba as much as we can, but what should we actually do when walking the workspace? It turns out it’s not so much about doing as it is about thinking.
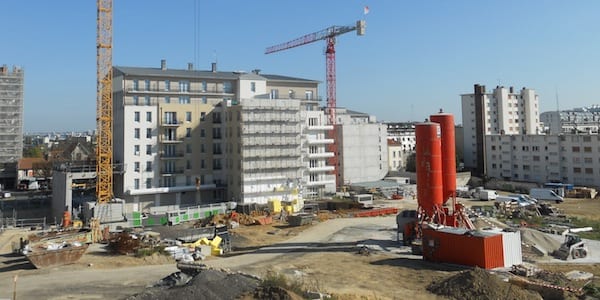
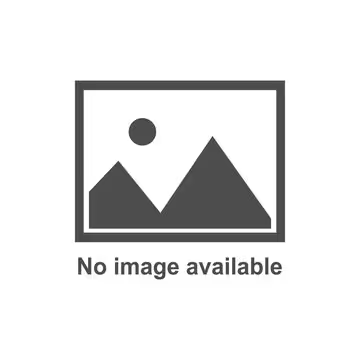
COLUMN - In the first of a series of columns written by CEOs, John Bouthillon of PO Construction explains how lean has kept his company afloat through the recession.
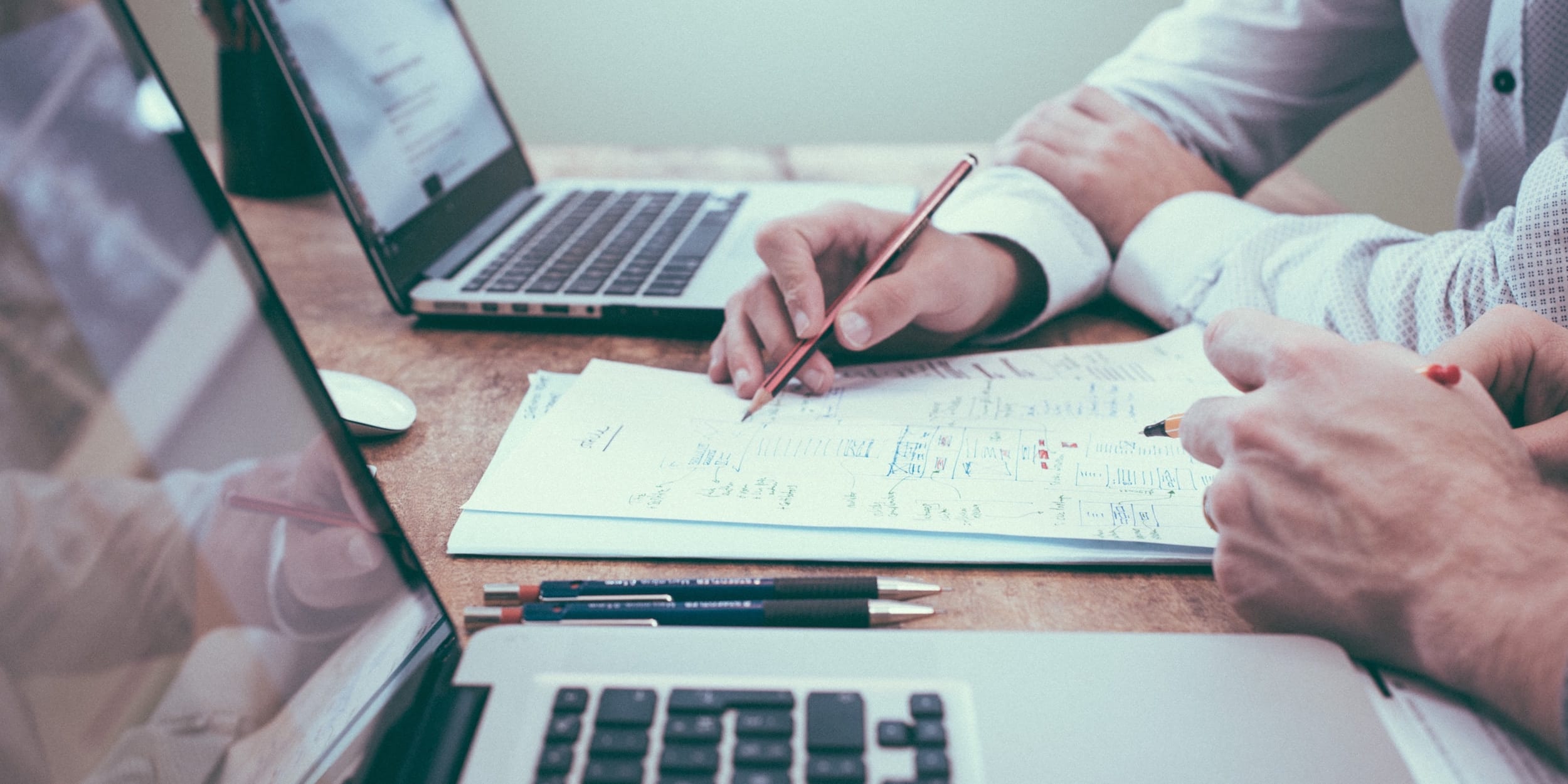
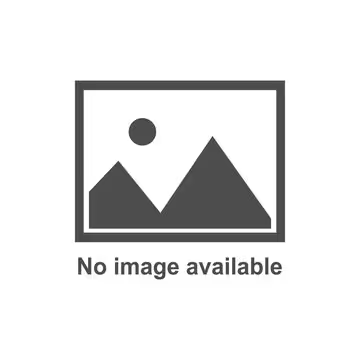
BUILDING BRIDGES – A member of the Theodo team tells us about their attempts to improve the performance of their Web apps using lean principles.