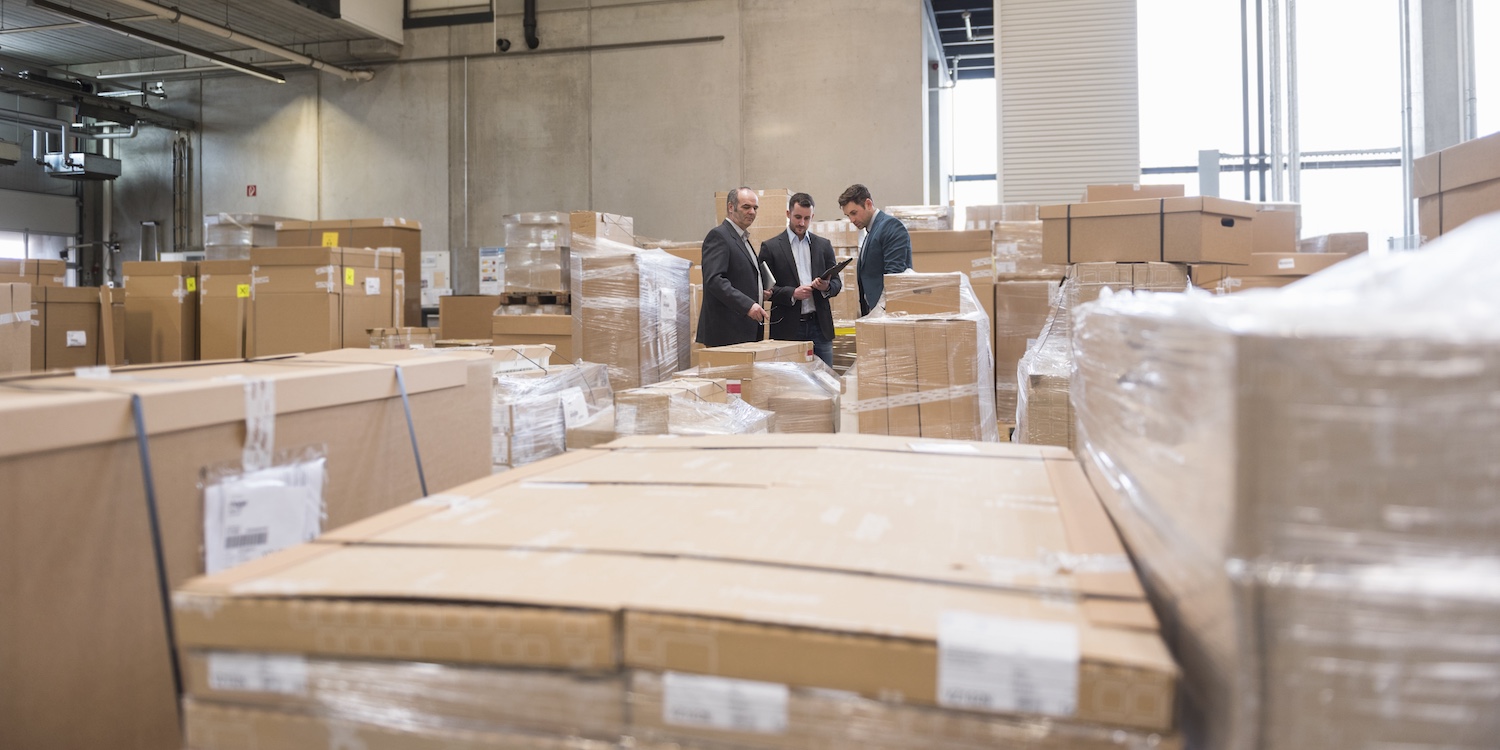
Logistic Kaizen: the devil is in the details
FEATURE – Focused experimentation and kaizen can lead to impressive results in as little as one day, as the story of this Hungarian company shows.
Words: Ágnes Antal
Originally published by Lean Enterprise Institute Hungary here.
We recently organized a one-day Kaizen workshop with the support of Cevdet Özdogan from Lean Institute Turkey, a former Toyota sensei with decades of experience.
Held at a distribution center in the Great Hungarian Plain, the workshop gave participants (both from the hosting company and from other organizations) the opportunity to develop their lean skills through practical experiments.
The areas for improvement and the business problems to be solved were identified the day before the workshop during a gemba walk with the host and Cevdet.
We focused on three areas – picking (commissioning), preparing boxes, and the inbound process – with a working group assigned to each of them.
After a brief knowledge transfer session, the task of each working group was to observe the processes and break down the problems. Following this, they defined the target state to achieve, understood the reasons behind the discrepancies, and planned experiments to be implemented in the afternoon. At the end of the day, the groups tested the improvements, measuring results and sharing learnings with others.
In part 1 of this two-part article series, we will share the observations, analysis, and learnings from the experiments conducted by each working group.
THE PROBLEM
Let’s start with the findings of the group focusing on the picking (commissioning). Their task was to improve the efficiency of this process and identify potential areas for development.
OBSERVATIONS
To understand the current state, the group was divided into smaller teams of 2-3 people, each applying different methods:
- Drawing a spaghetti diagram of the entire picking route.
- Creating smaller spaghetti diagrams to track the worker's movements between the picking cart and the items.
- Identifying different types of waste.
- Measuring cycle times for subprocesses.
The following types of waste were identified:
- Unnecessary movement: a loop occurred in the picking route where the operator revisited the same aisle.
- Overburden: In 25% of instances, items heavier than 15 kg were placed not only on the right side (as expected) but also on the left. This was problematic because, due to internal traffic rules, the operator always moved on the right side with the cart, making it harder to carry heavy items from the left. This slowed down the process and raised ergonomic concerns.
- Overprocessing: The picking process involved three separate scans plus a button press for quantity confirmation. At least one or even two of these steps duplicated checks unnecessarily.
- Inconsistency: Waste handling was not standardized. Some workers cleaned up after themselves, getting rid of empty boxes and trash, while others left them behind, causing extra work for the next operator and fluctuations in process performance.
- Waiting/unnecessary movement: The roller shelf system revealed several issues: picking was cumbersome as boxes were not open or prepared for collection; due to the improper angle, items got stuck in the middle of the shelf; these shelves stored slow-moving items; shelf capacity was underutilized, averaging around 25% fill rate.
- Unnecessary movement: Operators often walked around their cart multiple times because the label to be scanned was always on the left side.
- Unnecessary movement: Items in the box had to be rearranged to prevent heavier items from crushing lighter, fragile items picked earlier.
Given the workshop's one-day timeframe, we focused on issues with the potential for quick experimentation and immediate testing.
THE EXPERIMENTS, AND THE RESULTS
Based on our observations and the potential we identified, the following experiments were conducted. Wherever possible, we tested live; otherwise, we simulated the improved process.
- Heavy items picking: Measurements showed that picking heavy items took more time than light items. Placing heavy items on the right side, closer to the cart, therefore, reduced operator workload and saved -3.2% per order line.
- Label placement: Adding labels to both sides of the boxes could save an additional - 4.3% per line. However, this had to be weighed against the extra time and cost of preparing the boxes with double labels. While we couldn't measure this precisely, the before-and-after spaghetti diagrams clearly showed reduced distances covered by operators.
- Eliminating redundant scans: Removing one scanning step saved 1.6 seconds per scan. Although this might seem neglectable, with approximately 32,000 lines processed daily, it translated to a total of 14.2 work hours saved daily – a significant efficiency gain.
- Waste handling: The group examined how leaving empty boxes impacted subsequent workers. Carrying waste during collection took 2-3 seconds, but cleaning up after a previous worker took 8 seconds, causing at least a 5-second delay for the next operator. At this company, pay is based on lines collected, so the delay also had financial implications.
- Roller shelves: Properly opened and positioned cartons could save the company about 3 hours daily. Moreover, it would be more beneficial to store small, fast-moving items here instead of slow-moving ones. While this couldn't be tested, it represents a long-term plan.
CONCLUSION
Beyond the measurable results, this intense and incredibly educational day can be summarized with these two classic sayings: “The devil is in the details” and “Many small efforts add up.”
We often dismiss observed waste as “just a few seconds, so not worth addressing”. However, as this example shows, when they accumulate, a few seconds can quickly turn into hours.
It was also exciting to see what a small group of enthusiastic participants could achieve in a single day using the right tools. They provided valuable insights and suggestions for previously unfamiliar processes, while also learning extensively through hands-on experimentation. Instead of creating detailed but theoretical models of what the process should look like, we focused on making practical changes to the current state, one experiment at a time.
THE AUTHOR
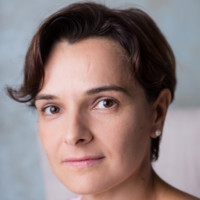
Read more
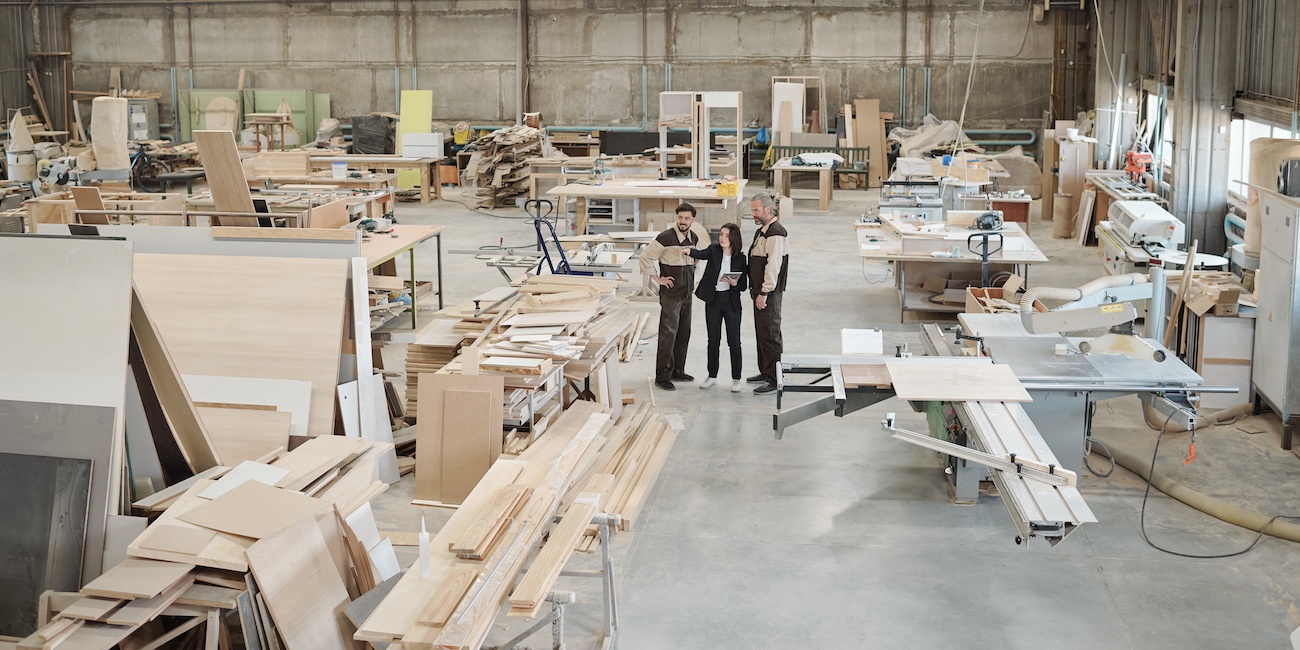
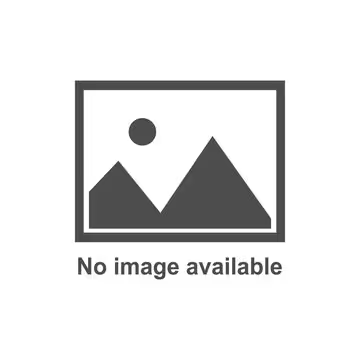
NOTES FROM THE GEMBA – What’s kaizen for? Improving quality? Generating a flow of ideas? Challenging a method? All of the above, so long as the underlying goal is to make people’s lives easier.
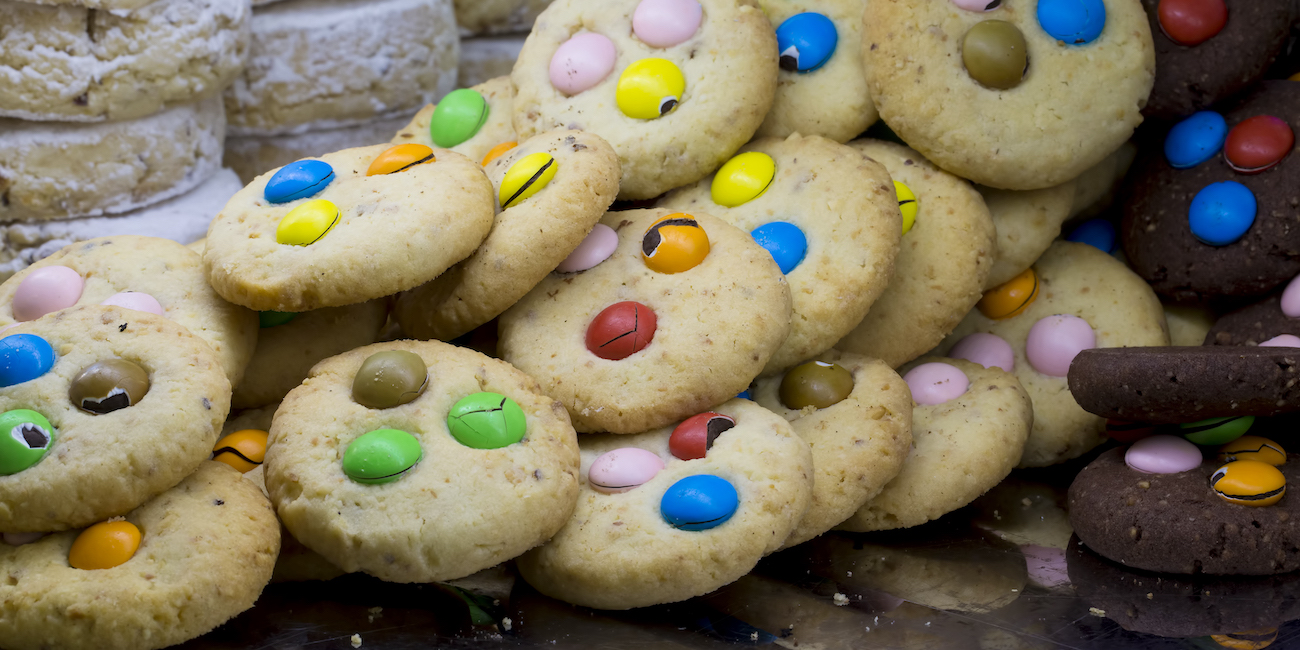
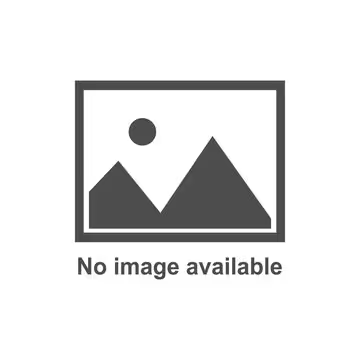
FEATURE – The successful project discussed in this article shows how Lean Thinking can bring huge benefits to small and medium enterprises and paves the way to a new way of looking at lean coaching.
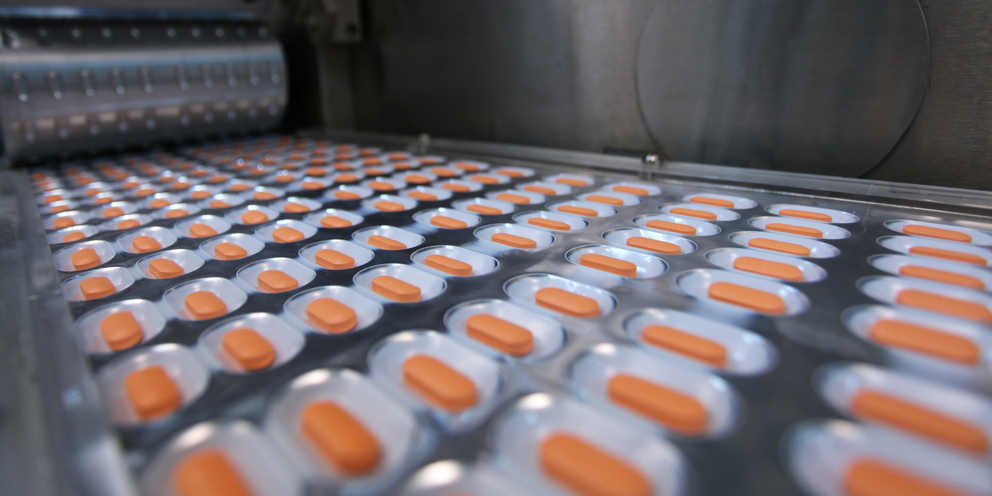
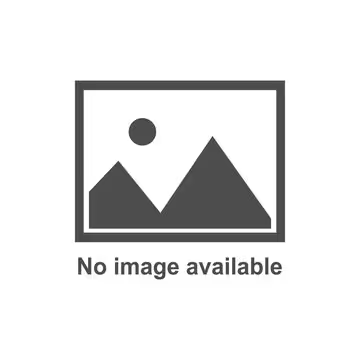
CASE STUDY – The implementation of lean in the internal logistics of a pharmaceutical company in Brazil proved key to increasing productivity and quality in the organization.
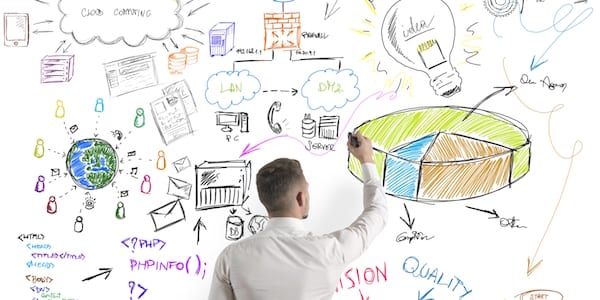
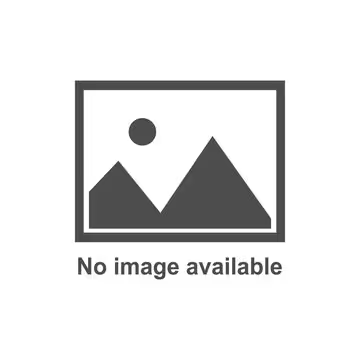
COLUMN - For her latest column, Sari Torkkola describes the initial steps that must be taken to move towards becoming a lean CIO and warn us against some of the pitfalls along the way.
Read more
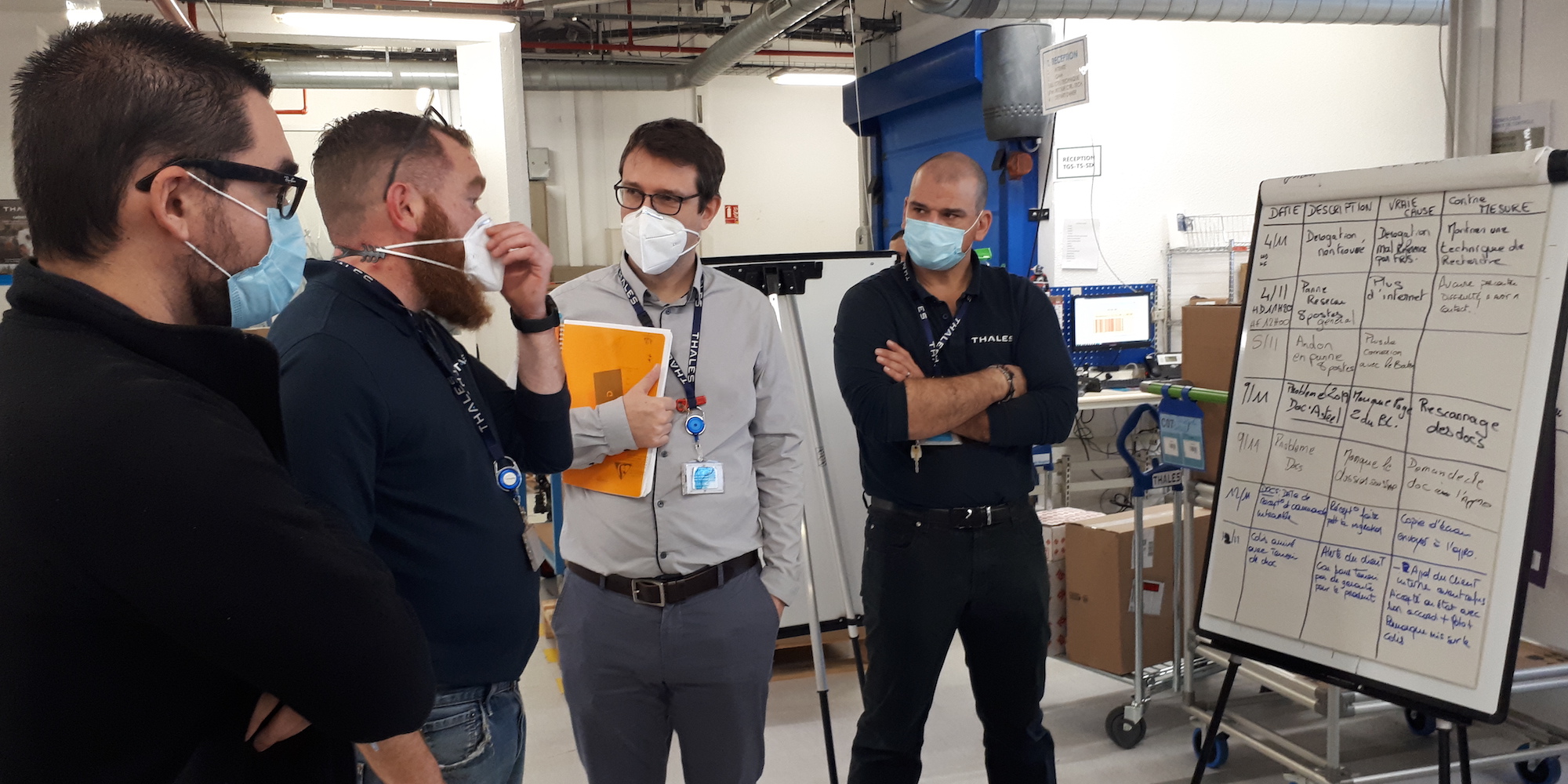
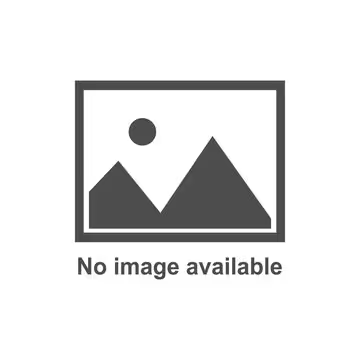
NOTES FROM THE GEMBA – Thanks to the effective application of Just-in-time and Jidoka, Thales LAS has managed to turn around its logistics department. Catherine Chabiron reports.
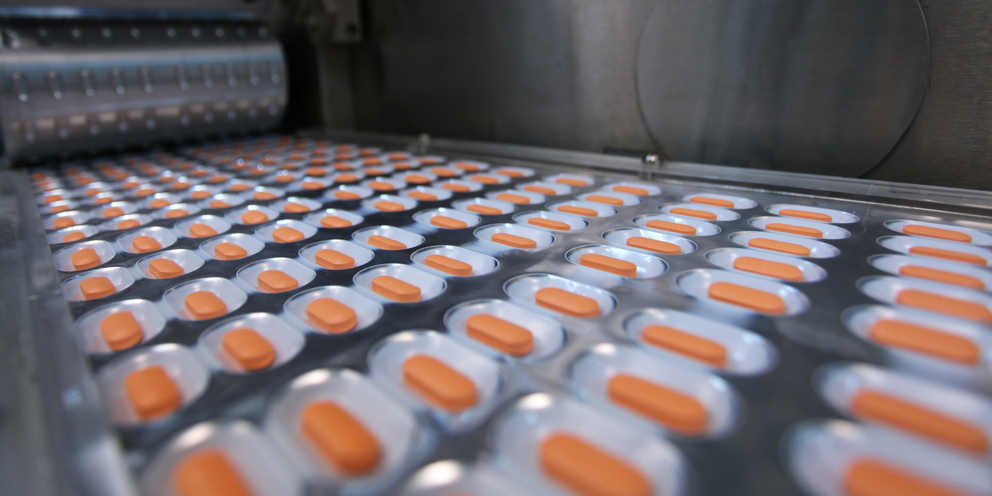
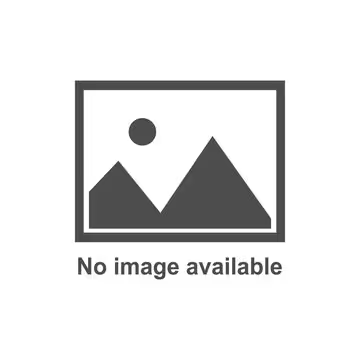
CASE STUDY – The implementation of lean in the internal logistics of a pharmaceutical company in Brazil proved key to increasing productivity and quality in the organization.
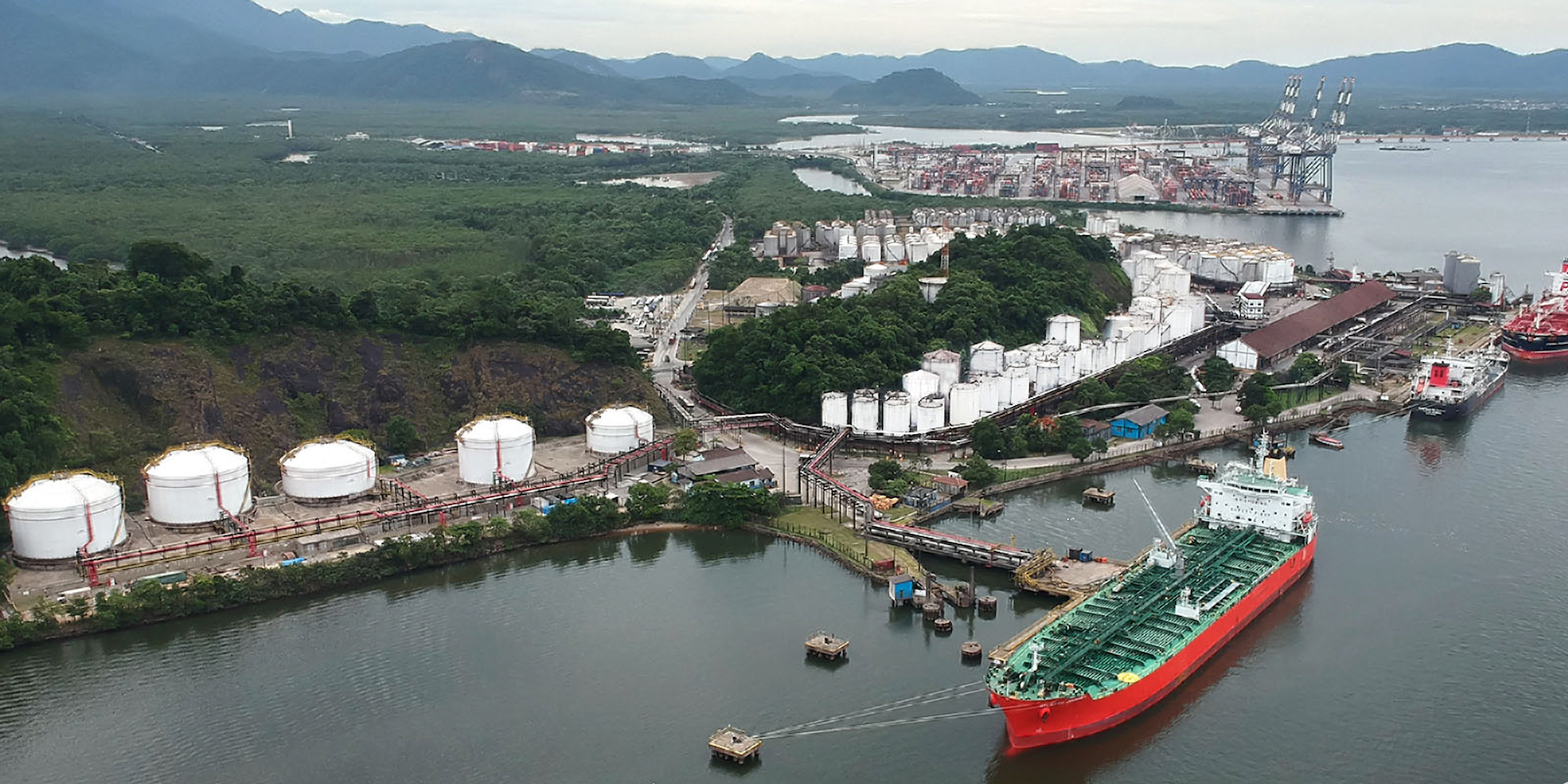
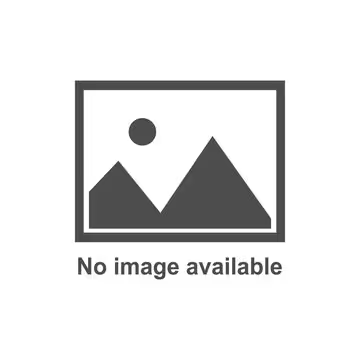
CASE STUDY – Logistics can be the key to achieving success and creating a competitive advantage in a company. This case study tells the story of a port terminal in Brazil that has used lean to achieve significant gains in managing its road flow.
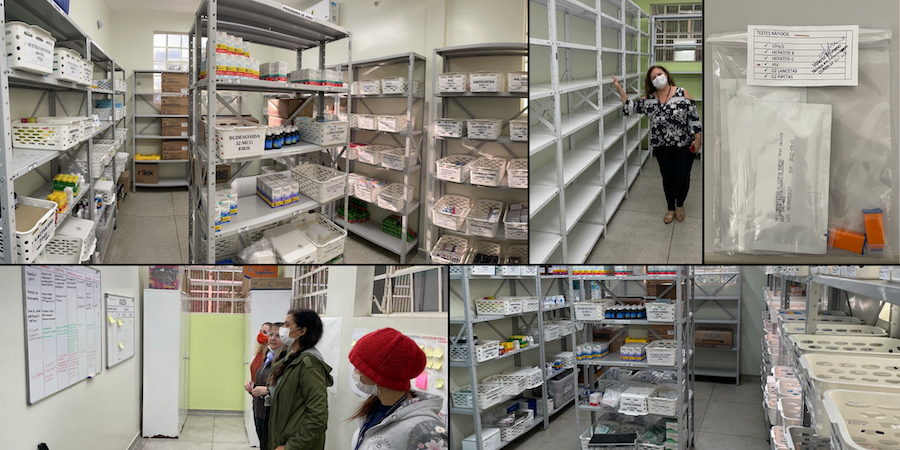
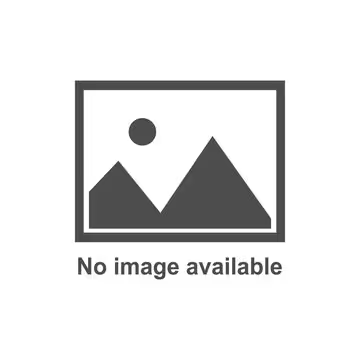
FEATURE – In this article, we hear about how the lean successes of one hospital inspired an entire healthcare authority to introduce changes to their processes.