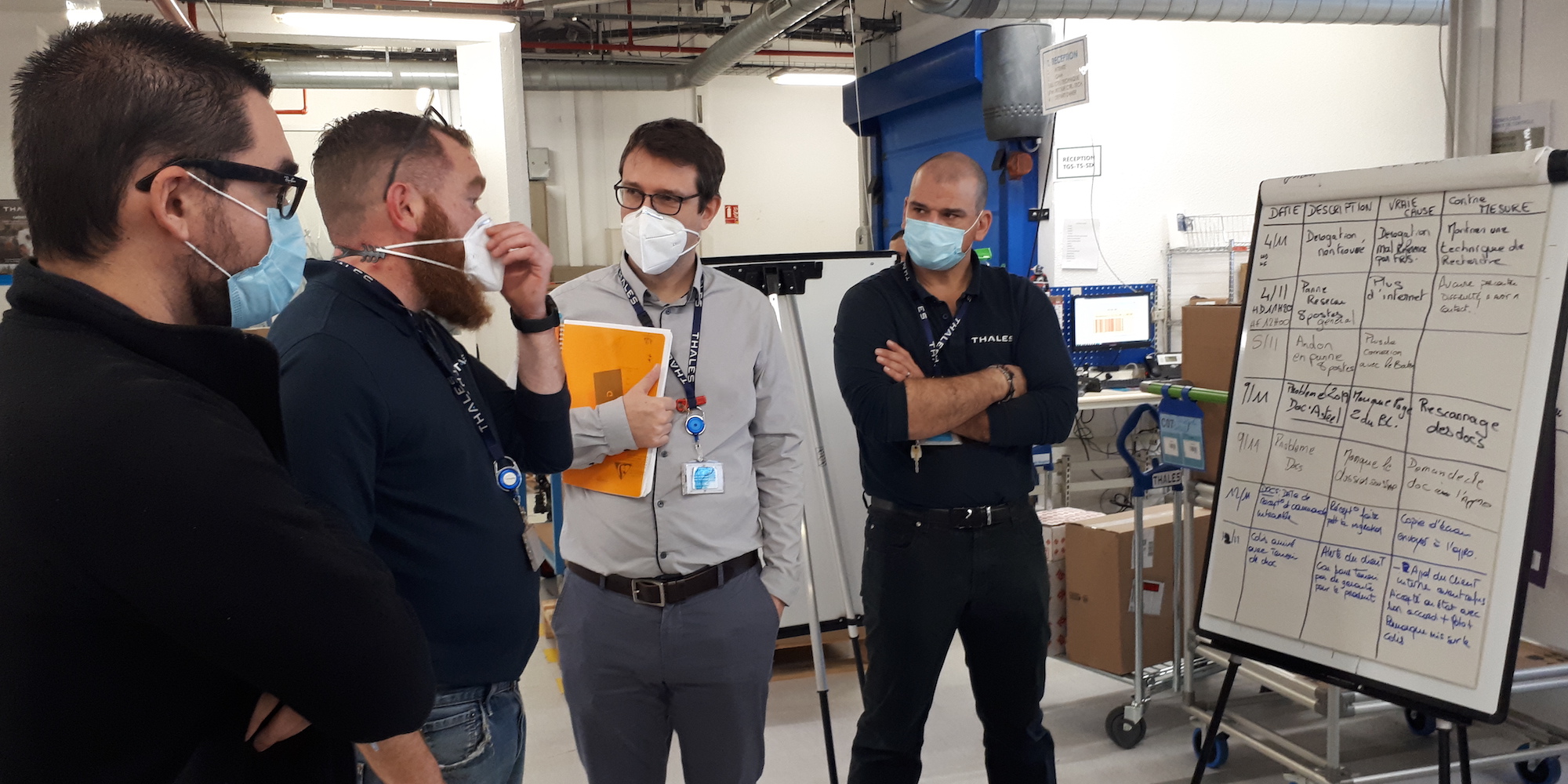
Lean logistics at Thales LAS
NOTES FROM THE GEMBA – Thanks to the effective application of Just-in-time and Jidoka, Thales LAS has managed to turn around its logistics department. Catherine Chabiron reports.
Words: Catherine Chabiron, lean author and member of Institut Lean France
I recently perused the content of my Notes from the Gemba series and realized that over the years I have observed and reported on many key applications of Lean Thinking, but never on logistics. We know how critical lean production is – it reaps major results in terms of costs, quality and delivery – and the key role that lean engineering plays in ensuring products and services are developed that customers want. But what can lean production and a lean engineering achieve if materials are missing, components are faulty, finished goods are delivered late or a key supplier goes bankrupt?
Sure, many other functions within a company are key, but my personal experience over 40 years of visiting the gemba is that supply chain management is often behind the rise or fall of business ventures, something we have been reminded of in recent month with the Covid-19 pandemic.
This is why I am so eager to start my visit to Thales Land & Air System Elancourt. In 2019, Cyril Garambois, a former Lean Officer from another branch in Thales, decided to move to an on-the-gemba managing position and took over his current role of Operations & Logistics Manager, covering S&OP, receiving, shipping, and the management of bill of materials for procurement, in an assembly plant of 500 people. As lean was hardly implemented in the plant when he started, I am a privileged witness of the early stages of development of a lean supply chain. “I saw this move as an opportunity to challenge myself to move from theory to practice,” Cyril tells me with a smile.
A quick word on the products, for context. Thales LAS assembles and delivers optronics and electronic missiles mainly for the Armed Forces and the details are pretty hush-hush. Charles, who reports to Cyril and manages the details of the lean implementation while leading the shipping team, takes me on a tour of the showroom. I see cameras for tanks, jeeps, vessels, planes, infantry, enabling vision by day, night and in smoke or fog. Charles also shows me sophisticated detection systems or laser sighting systems. He explains that, in terms of logistics, transportation or export are complex tasks as some of the products are considered top-secret defence matters. The containers themselves can reach the price of a family car.
HOW TO START LEAN IN LOGISTICS
Cyril confirms he had a few clear ideas from the start. “My mission, the way I see it, is to improve the flow management and, as soon as possible, accelerate it. That means to remove hurdles, decrease ambiguity, and reduce lead-times and stagnation,” he explains.
The question on how to build a lean supply chain cropped up only a few days prior, as Michael Ballé and I were moderating a webinar on lean and supply chains, during which we discussed common misconceptions on supply chains.
First of all, we need to give up the mass-production dream of large machines, large batches and low unit costs and work on our flexibility, both in terms of volume and product mix variations (which has much to do with small batches and SMED). This is what will help us navigate huge shifts in demand and meet new customer needs. It will also reduce the cost and time-to-market of our product launches, as the same production means can be used both for existing products and the new ones.
Secondly, we need to accelerate the flow and put the entire chain under pressure with frequent pickings, at takt time, so as to reveal where the flow doesn’t, well, flow. Sending out a truck every hour rather than a truck every day will have a drastic effect on your customer lead-time, simply because the goods will wait far less. If the next truck is scheduled to leave in half an hour, instead of the end of the day, people will be compelled to act on issues and deploy countermeasures faster. This is one of the key roles of logistics.
Third, we have to learn from any mishaps, from faulty components and badly designed products, from the supplier network, which is in fact a huge reservoir of know-how.
“Actually, flow cannot be accelerated without learning. We had to understand what created the stagnation first. Developing competence through this learning helped us find new means of accelerating the flow,” Cyril says.
LEARN TO SEE
Cyril and Charles set out to implement all the paraphernalia of lean flows, so that hiccups in the process could be spotted more easily by both operators and management.
Shipping to customers is an area where you want to monitor whether you are indeed delivering what you promised, both on time and in the right quantity and quality. The team at Thales LAS created a truck preparation area in which each outgoing truck is assigned a zone on the floor, where the goods to be loaded are stacked well ahead of the departure time. Each zone has its own post with a paper indicating the time the truck is scheduled to leave and the goods that it will carry. In addition, a board monitors whether the preparation was finished on time, as well as the truck arrival/departure times versus targets. Regular routines in front of the board help take appropriate measures to save each truck’s shipment, should a problem occur.
A heijunka box, kanban cards and a small train are used to pull the finished goods from production. Takt times range from 2 hours to 2 days – occasionally weeks for larger, more complex products. Kanban cards corresponding to products that could not be picked up at the agreed scheduled time are replaced by red markers in the time slot where the picking should have taken place, thus highlighting issues. One more time, daily discussions in front of the board help the team to make quick decisions and enable the picking of the desired product.
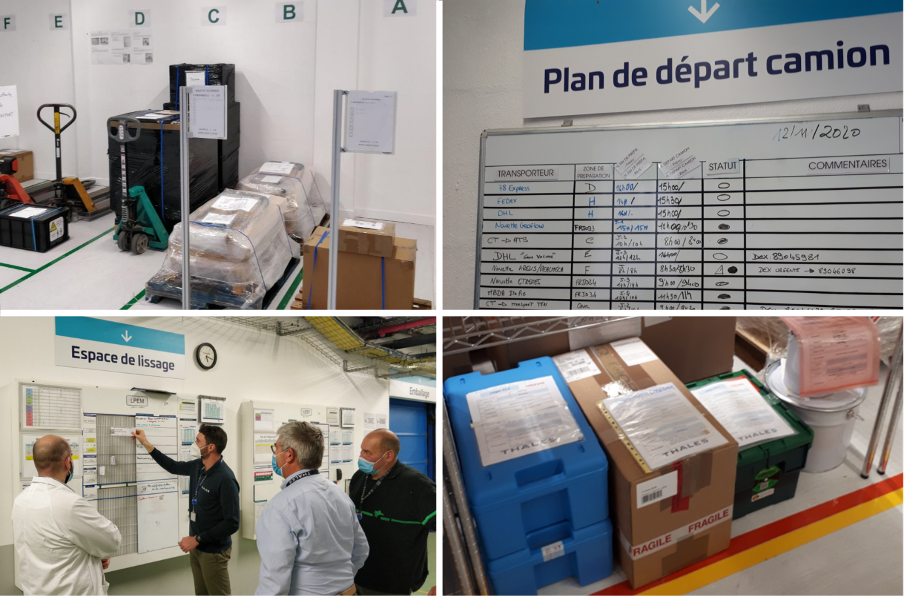
Because of their complexity and cost, most of the components received from suppliers undergo a thorough quality inspection upon receipt. The area of the received goods waiting to be quality-checked has been improved: the “red bin” section for those items that haven’t passed the quality check was moved to the centre of the receiving area, so that it can’t be overlooked or forgotten by the inspectors. Waiting NOK goods carry a label describing the issue: “We want the products to talk to us. We want them to tell us at first glance how long they have been sitting there and why,” says Cyril.
One small train runs every hour, 10 times a day, delivering components and picking finished goods. A recently introduced monitoring board helped Charles and Cyril see that the trains were far from being used at full capacity. “Each tour should take 45 minutes, but we can see on the board that the trains sometimes come back after 20 minutes! We had no idea that this was the case,” Cyril comments. Food for thought and an opportunity for further improvement.
In addition to these shopfloor visual management devices, the logistics management team also tracks a number of KPIs. Receiving, for example, monitors the stock of products that failed the quality inspection and are unavailable for production, the incoming lead-time between truck receipt and release of the product following the inspection or the lead-time and quality of goods called by production from incoming stocks.
LEARN TO ALERT
Visual monitoring devices help the team spot what goes wrong and where. The next step was for them to start doing some real Jidoka and organize the “stop and fix” – as Thales calls it. We are visiting Marc, in charge of receiving and I immediately spot an andon board above the quality inspection desks. This is a rare sight when you are away from an assembly line and I ask Marc how it works.
“If one of the inspectors has a doubt, he can press this orange button and the andon board will light up. Pierre Emmanuel, the team leader, will come and help,” Marc explains to me. Eager to demonstrate how the alert device works, he presses the button on one of the desks and the board lights up, indicating which station is experiencing a problem. We forgot to warn the team leader, who jumps up (clearly, the system works) and comes over to investigate. He then joins the conversation.
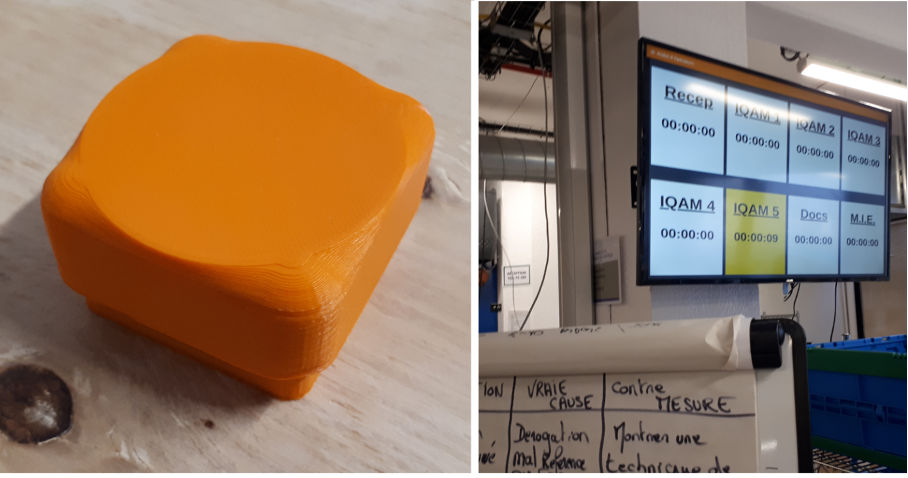
“The andon helps us solve problems on the spot when there is a doubt or difficulty. Previously, the issue would have been set aside, the product would have landed in the red bin area, and it might have been days before we got to work on it,” Pierre-Emmanuel confirms. “This system also helps me to understand who needs to be further trained on some key aspects of our job.” Marc explains how any andon call that is not solved within eight minutes escalates to him. Why eight? Because an order in the Receiving area should be quality-inspected every eight minutes. It’s their takt time.
They also have regular discussions with the team to learn from each alert and improve.
You may raise an eyebrow and consider this to be overkill, since all desks are located in the same area and inspectors could just as well raise their hand to secure help. However, and this is also true on an assembly line, when they are “in the flow”, people rarely step out to get help and their immediate reaction is to set aside the issue or make a quick, potentially wrong decision on the rework to be done. To achieve a solid andon implementation requires many conditions to be met: you need an available team leader eager to develop competences, you need trust as you don’t want to be sneered at for your ignorance, you need to be under the pressure of takt time and be well aware that every minute counts.
START TO LEARN
Implementing takt time (the Just-in-Time pillar of the Toyota Production System) and the andon system (the Jidoka pillar) in Receiving supports the learning process. As we further discuss with the team leader, Pierre-Emmanuel, I start to understand the challenge in this flow of sophisticated military components: to learn even just the basics of quality inspection (documentation control, mainly) takes take up to two weeks of assisted, on-the-job training. Moving further into the specifics of mechanical control will take another month.
Capability development is the first step towards improving flexibility and agility. Marc’s team seems to have spotted the problem there: due to the complexity of the inspecting work, tasks were previously assigned to dedicated people and bottlenecks ensued. Because operators were poorly trained, goods were put in the red bin area even when a quick investigation could have solved the issue on the spot. The team has consequently worked hard on multiskilling and completely changed the way incoming orders to be checked are dispatched, while accelerating the transfer to stock after the control is completed (four times a day, instead of two).
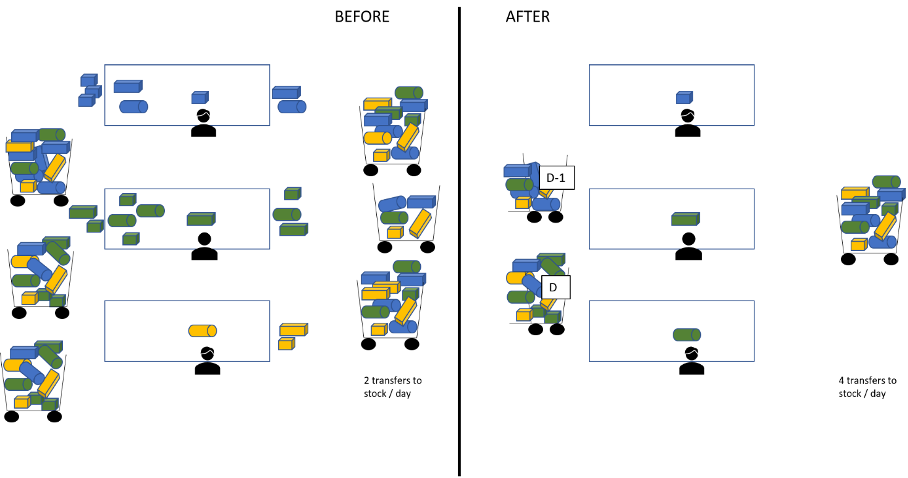
Products that need to be quality-inspected are placed in a cart showing the day they came in. Inspectors no longer cherry-pick and assign orders to their specific desk based on what they are trained for but pick up products indiscriminately from the oldest cart and work in one-piece flow. Multiskilling has greatly contributed to lead-time reduction, as shown in the following graph.
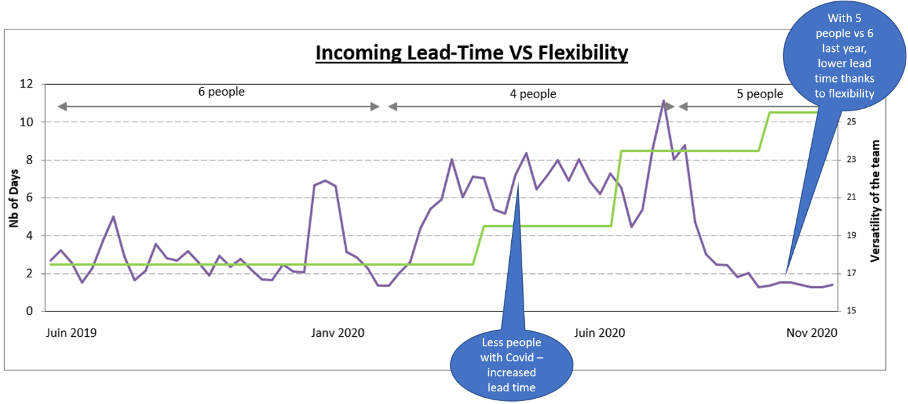
A stop-and-fix alert can also come from production and logistics is invited to help explain what went wrong in the flow. Charles shows me the latest such issue currently under investigation on the shipping customer wall – an urgent delivery that was not picked up by the small train. “We have learned to analyze what is going on in depth,” says Charles. “We try to both describe the effect of the problem, as perceived by the customer, and to unearth the real causes behind the mishap. The point is to try and find solutions that will be both sustainable over time and agreeable to production.”
It took a lot of these alerts to become proficient in this exercise, but the major advantage of the system – as Charles, who is in charge of shipping, and Marc, who is in charge of receiving, confirm – is that it fostered collaboration and trust. Both Production and Logistics collaborate with the same tools on issues, while swift and relevant analysis and countermeasures help build trust between the hitherto separated management silos.
Charles is also leading quality circles with the 6-point Kaizen approach (define the performance to be improved, analyze the current method, generate new ideas, define the implementation plan, execute the plan, evaluate the new method). Interestingly, the learning never stops. A recent kaizen on containers led the team to use metal boxes coated with foam to secure the transport of chemical products.
However, this led to a near accident when the small train operator started to use them. He nearly ripped his hand open on the sharp edges of the box while handling it. This led to an andon pull and to an immediate improvement of the box’s edges with tape.
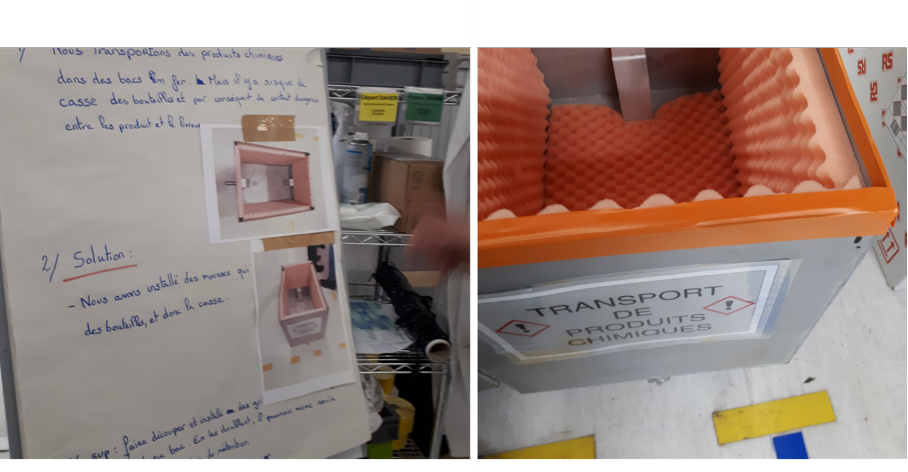
Kaizen with the shipping team is also leading them to work on the documentation flow, experimenting with new layouts or devices showing the stock in each bin.
Charles learned the hard way that a kaizen can unveil many side problems, and the decision to address them as they pop up will be made at the risk of losing sight of the initial issue. He also learned that a solution designed and tested by the team who will use it stands a much better chance of surviving the test of time than an idea promoted by the boss.
“The difficulty is to hand over the pen,” Charles admits. Those kaizen discussions are opportunities to develop skills in both the team’s work and in teamwork coordination. The next step is therefore to let team leaders or even team members learn this kaizen coordination. We have an interesting discussion on how Toyota firmly believes in developing kaizen capabilities at all levels, everywhere, all the time.
Cyril continues: “One of the areas where I have most changed my mind is the importance of the team leader in this teamwork and kaizen activity. The team leader’s role is of course to ensure products are delivered on time, but also to understand where team members get stuck and help them develop their competence. The improvements we have made in Receiving are a demonstration that it works.”
GIVE TIME TO SAVE TIME
Cyril admits to me that in its early stages the lean implementation was mostly led by him, with a top-down approach. “I was implementing tools, but not giving people the time to change their minds and understand the why. I wanted Logistics to change and, at an early stage, I wanted to move fast, in order to demonstrate the benefits of lean. Gemba walks with fellow lean officers or sensei helped me to see I had to change my approach. What’s on top of my mind at the moment is whether the changes I am encouraging my team to make will be understood, agreed on, and sustainable.”
Despite Covid-19 and the increasing number of problems being unveiled (a normal and indeed welcome occurrence when visual flow management and andon are deployed), the acceleration of flow is slowly becoming a reality in the logistics department at Thales LAS, as can be seen on the shipping lead time.
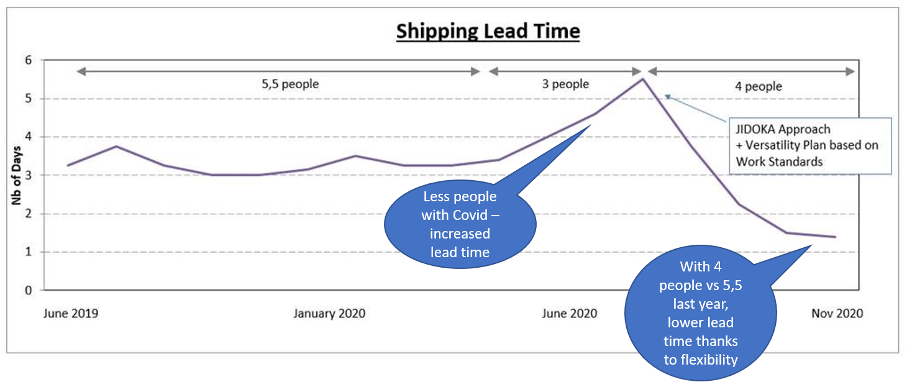
THE AUTHOR
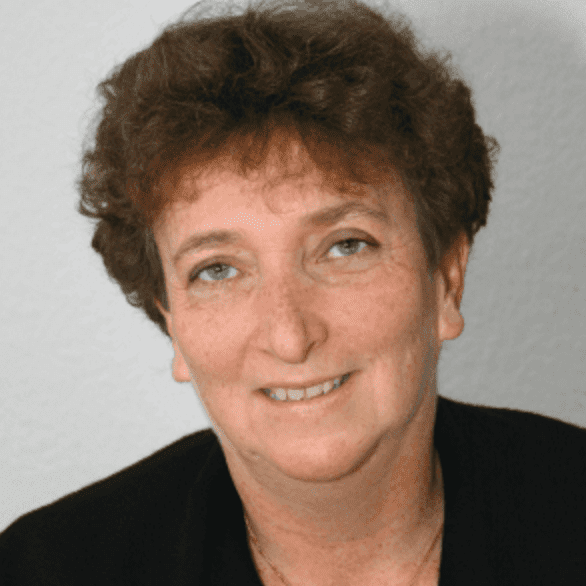
Read more
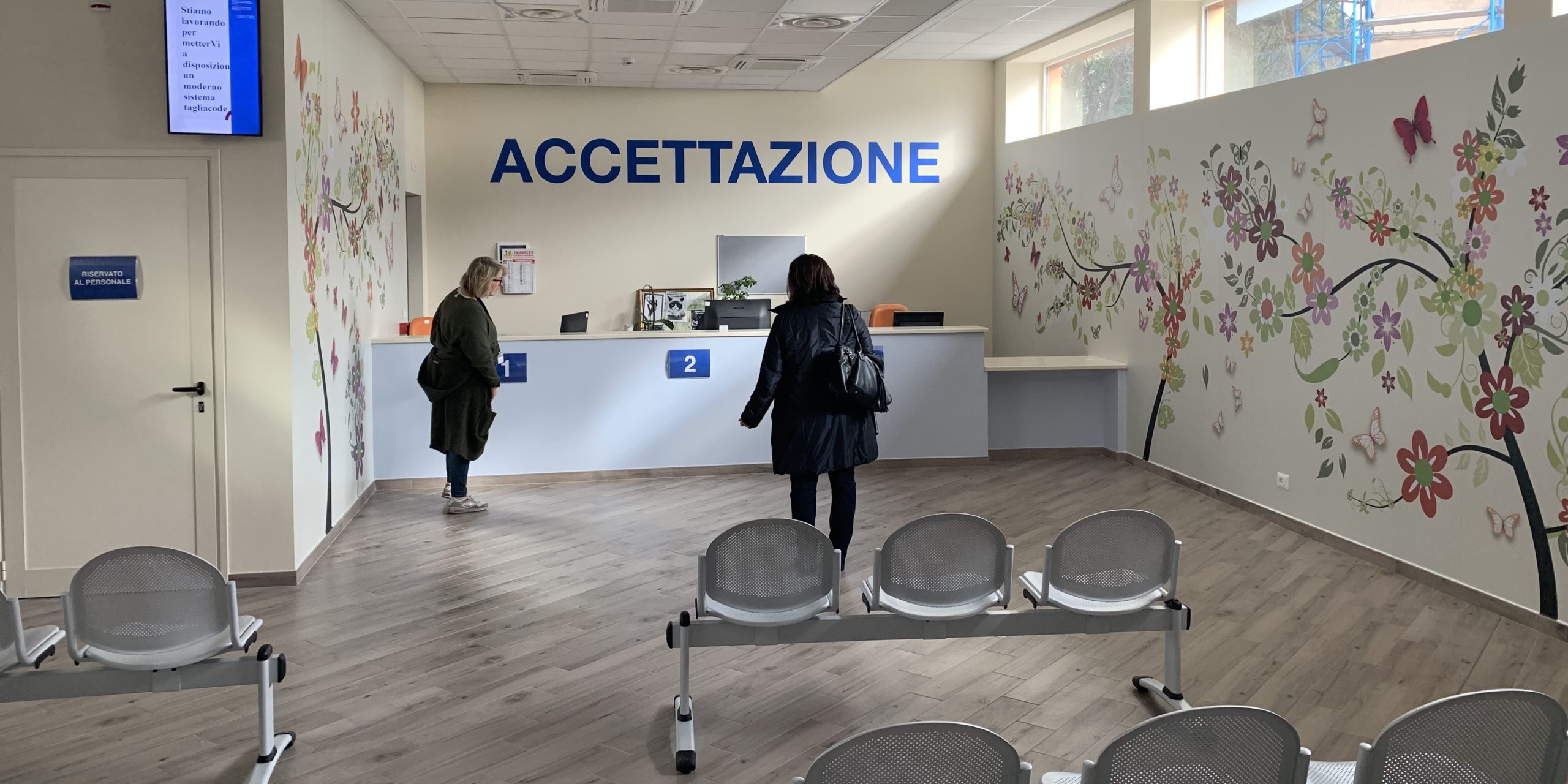
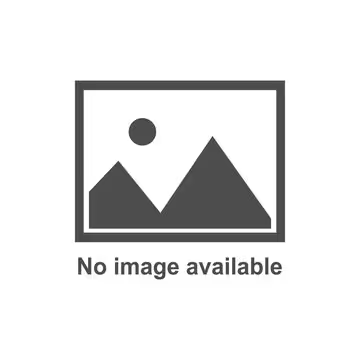
FEATURE – The renovation of one of its departments gave a hospital in Italy the perfect opportunity to redesign his oncology care with lean healthcare principles in mind.
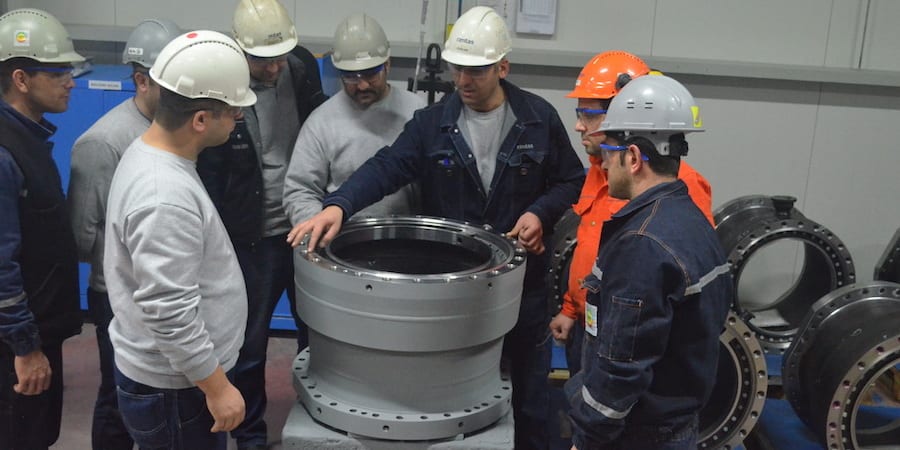
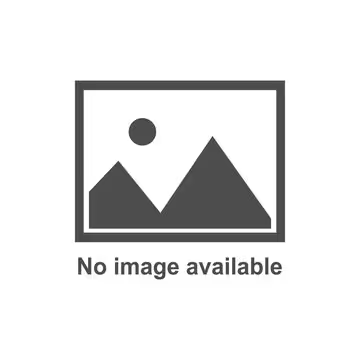
CASE STUDY – With plans to double capacity year on year in its new precision machining business, a Turkish company found in lean a way to control growth by stabilizing old processes while new ones are introduced.
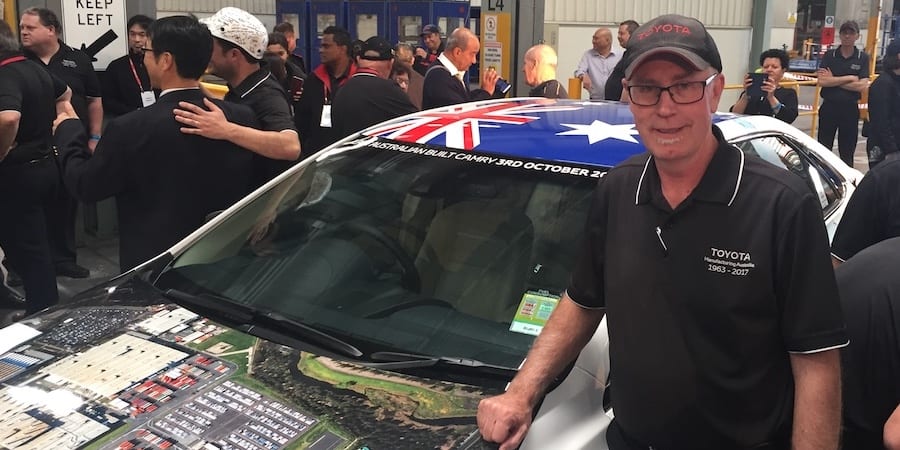
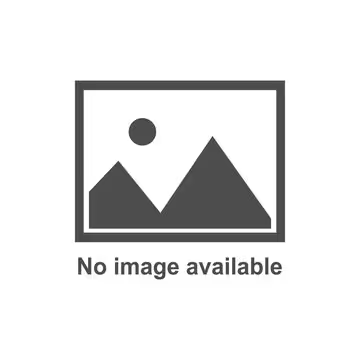
PROFILE – What does one learn from working for Toyota over 40 years? This Australian leader has developed a unique holistic view, and a strong set of technical and social skills.
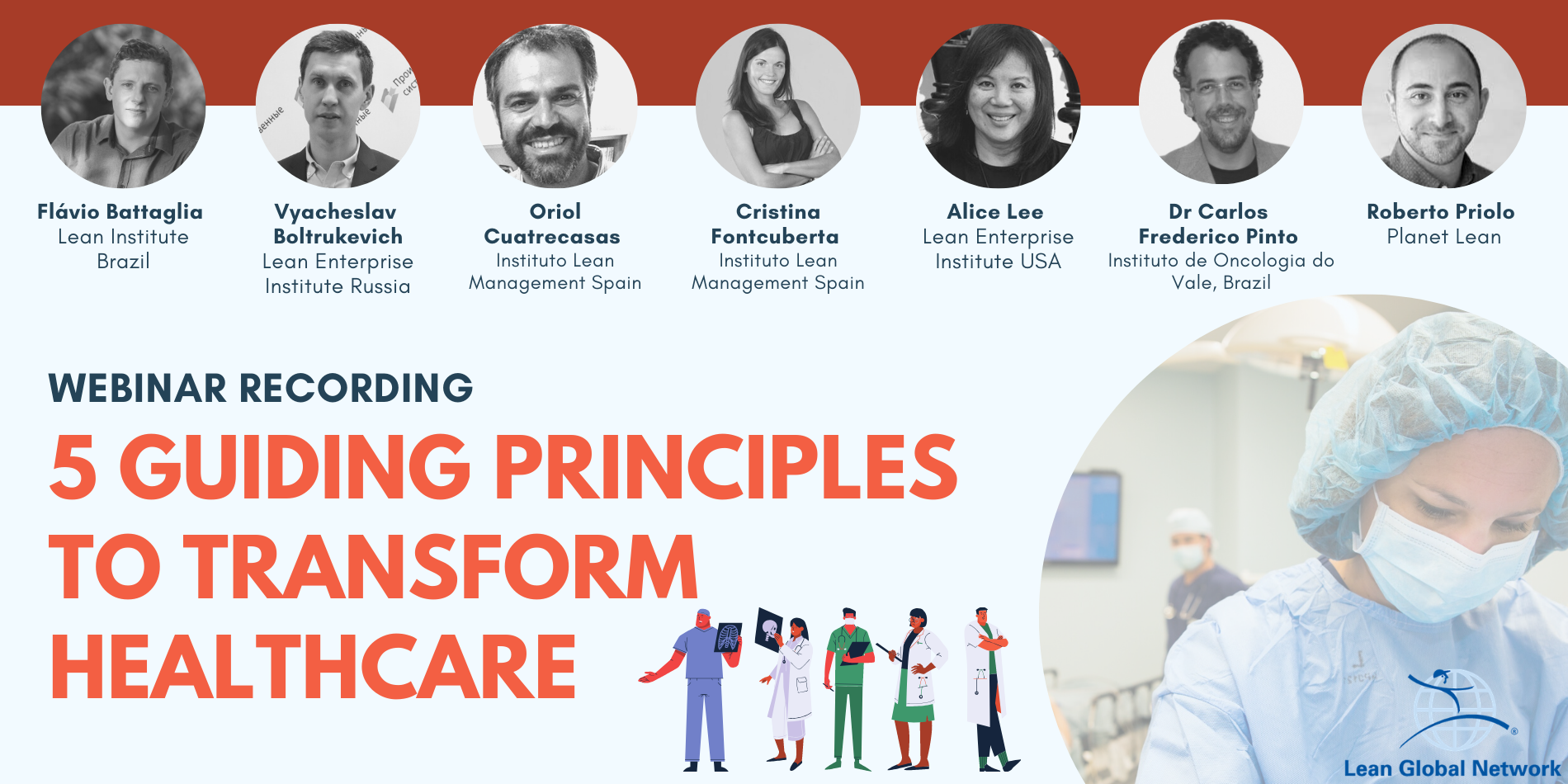
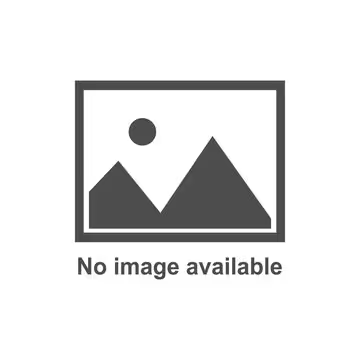
WEBINAR - The Lean Healthcare Initiative teams presents the results of their research and provide five guidelines to successfully transform healthcare organizations.