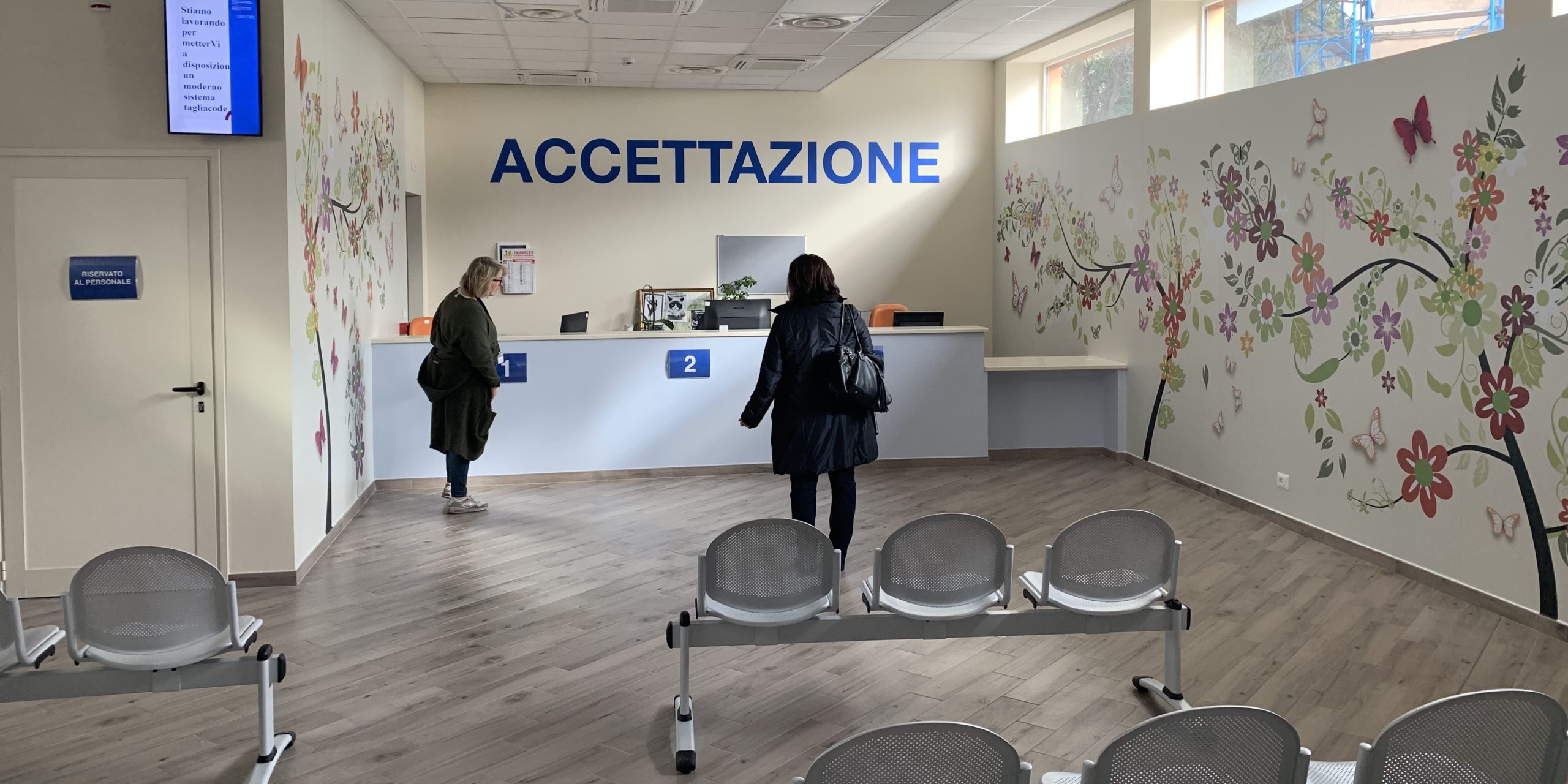
Our new, leaner Cancer Center
FEATURE – The renovation of one of its departments gave a hospital in Italy the perfect opportunity to redesign his oncology care with lean healthcare principles in mind.
Words: Jacopo Guercini, Project Manager Cancer Center, Dr Alberto Sobrero, Head of Oncology Department, and Dr Franca Martelli, Chief Medical Officer; Policlinico San Martino – Genoa, Italy
The Policlinico San Martino – a University and community Hospital in Genoa, Italy – is undergoing a dramatic transformation in the organization of oncological-hematological care. Starting in April 2018, the organization has been combining six different oncology and hematology wards into one area, a Cancer Center.
This is a complex project that naturally lent itself to the use of lean principles and better operations management techniques. In its first phase, which is still ongoing, outpatient activities are being consolidated – a difficult undertaking, considering the high levels of variability in the type of patients treated, their conditions and the complexity these add to the provision of care.
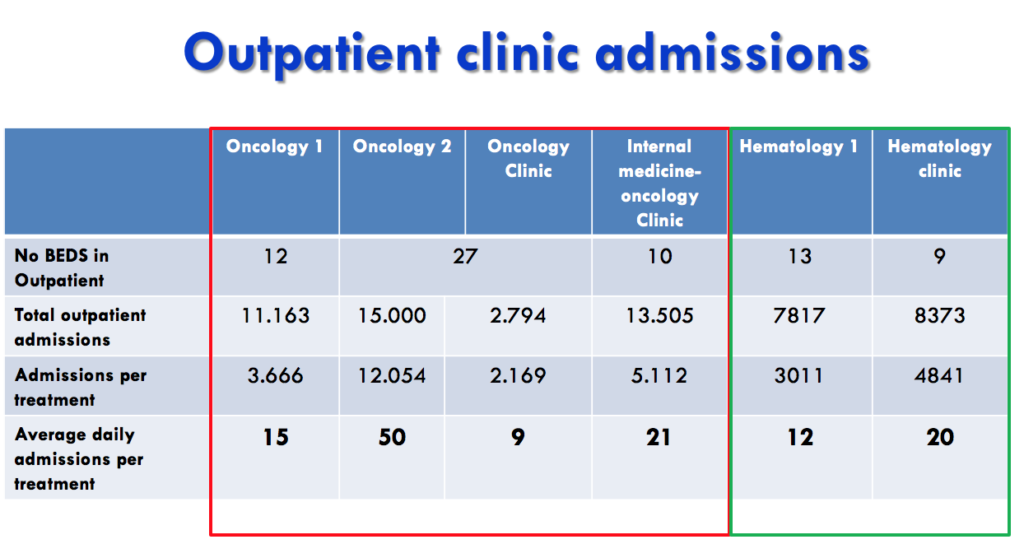
The six outpatient clinics (which Italians refer to – in English – as “Day Hospitals”) were located across five different sites, and they each have their own Director, Nursing Coordinator and internal organization. There were also big differences among different wards, whereby patients presenting the same issues could very well follow different pathways.
To try and tackle this issue and really harness the potential of lean thinking, the hospital’s management created a working team made of 13 nurses, 12 doctors and 1 pharmacist, coordinated by a management engineer (acting as project manager) and supported and coached by AMAS (Agenzia di management Sanitario, Università degli Studi di Genova). Following an initial team-building activity, a few sub-groups were created and asked to focus on different projects: reviewing protocols, planning patient flow, material logistics, wayfinding, clinical organization by illness, and primary nursing.
Between February and April 2018, the project manager worked with the staff involved to map the process in each of the sites. Several stakeholders were engaged, including Quality and Clinical Risk, Technical Office and Management Control as well as patient advocates to capture the Voice of the Customer.
The mapping exercise revealed a number of problems, including overcrowding in the early morning, a waiting time of up to four hours for patients to obtain the results of blood chemistry tests and receive medication from the oncological pharmacy. The decision to centralize oncological activities was made also because an area in the hospital was being renovated, which could house the Daily Hospital work (the Organization of European Cancer Institutes was also encouraging the Board of Policlinico San Martino to do so): the new location offered a larger and more comfortable space, and the unique opportunity to completely rethink the patient journey in the light of what had emerged from the mapping of the process. Consolidating activities in one place also allowed for the creation of a number of facilities, like a satellite lab for blood chemistry tests, a pharmacy dedicated to oral medication and a direct link with the oncological pharmacy for the administration of chemotherapies.
Based on volume history, a simulation was carried out on the usage of the new assets (for each therapy, the team considered the infusion time of different medications and the corresponding pre-medication and washout times). In particular, we calculated the average occupancy rate of the 51 stations available in the Cancer Center considering the average day in outpatients with its 150 chemotherapies and 10 transfusions. The simulation revealed that planning outpatient therapies between 8am and 4pm is possible to serve patients from all six locations while minimizing their waiting time. We then decided to plan the therapies assigning each patient a time slot. This plan, if respected, guarantees a short waiting time. This planning includes the following processes:
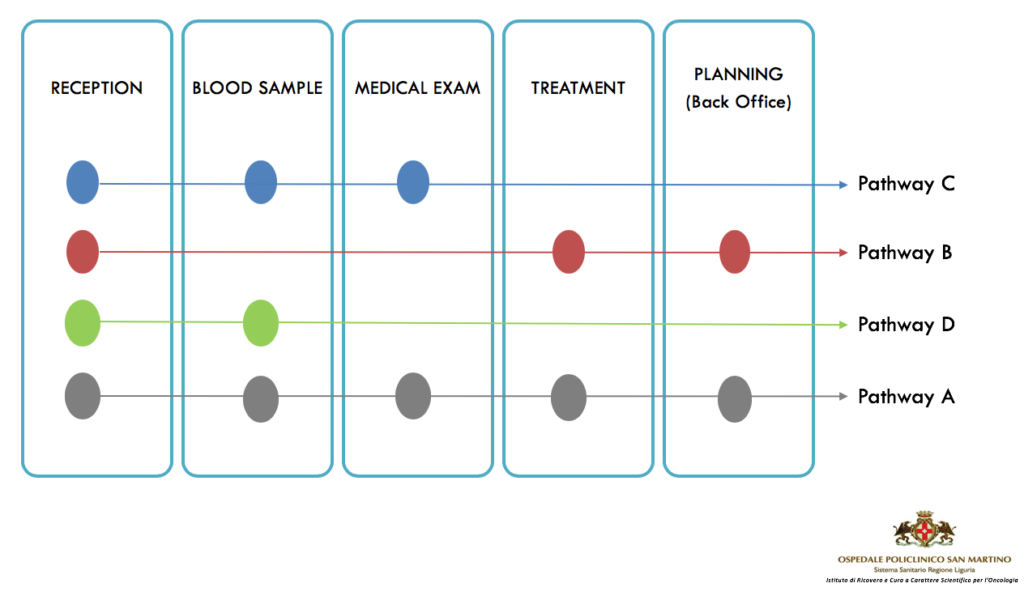
For instance, Pathway A represents the patient going through all activities on the same day: considering the average time required to complete each activity and the time required to technically review blood chemistry tests, the time patients are called is calculated based on the availability of the stations.
Using a spaghetti chart, these pathways have been optimized from a logistical standpoint. Here’s the spaghetti chart for Pathway A:
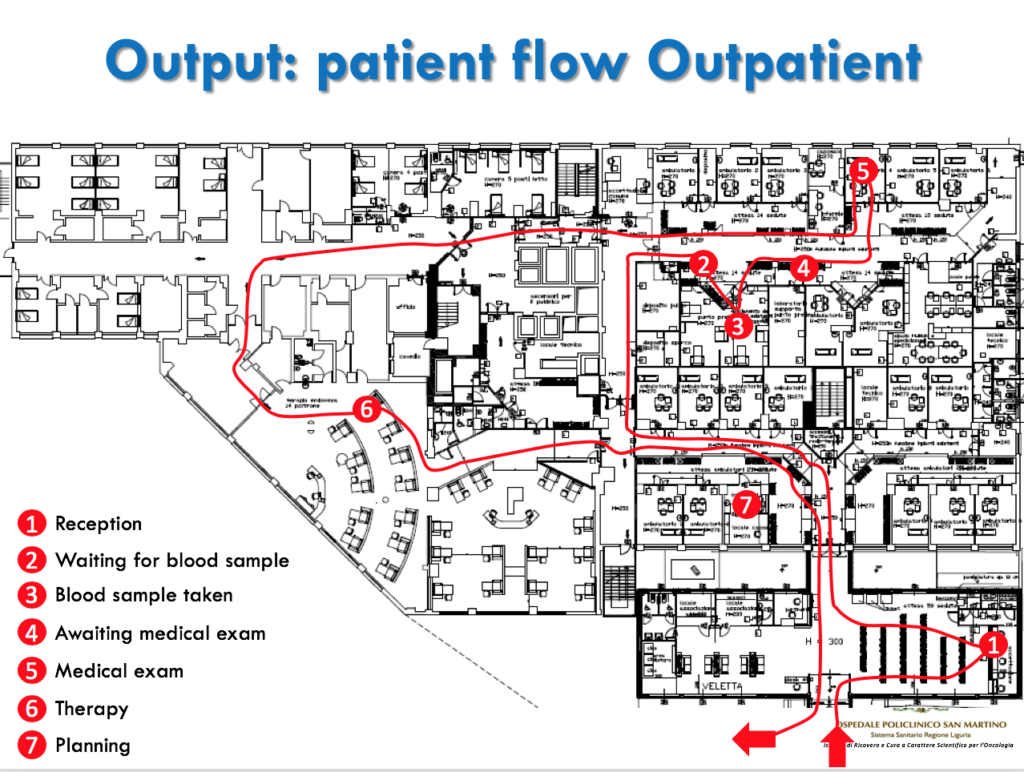
The first transfer was carried out on November 26 last year, with four inpatient clinics (two oncological and two hematological) being moved to the new facility. We noticed a few problems – including overcrowding early in the morning, some difficulty in understanding the logistics of the new location, and the coexistence of very different organizations within the same processes. In June, we will move another oncological inpatient clinic. We will complete the transition in September.
The aim of this project is to introduce a patient-centered model for the improvement of the quality of care and the organizational efficiency of the clinics involved. To date, here are the main results we have achieved:
- Waiting time between reception and therapy (measured before the consolidation and after the first phase of the move)
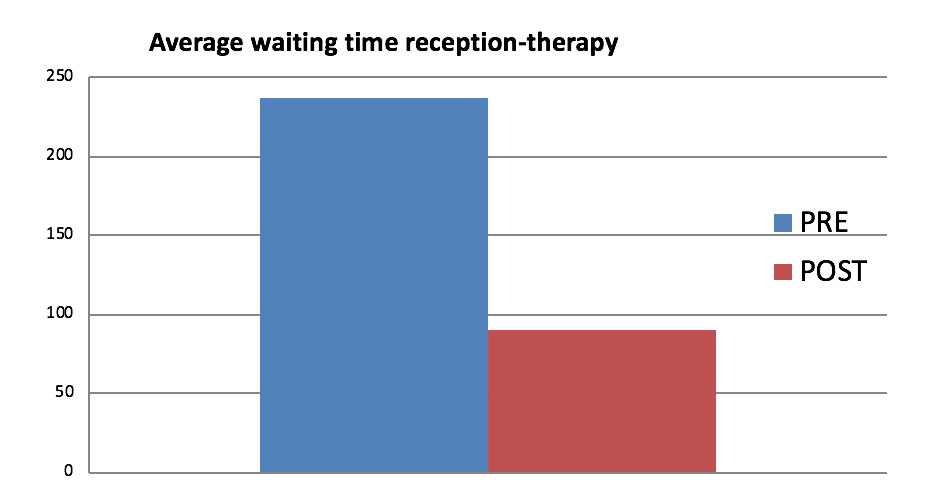
It is worth noting that, starting in January 2019, the average time between the planned reception time and the moment therapy begins is 90 minutes (with a 60-minute standard deviation). This is extremely positive – a sign of well-performing processes.
- Chemotherapy preparation times (January-March 2019)
We have gotten to a point where 82% of the preparations are requested the day before, and 95% of those are completed on the same day. Only 5% is completed on the day of the therapy.
For the preparations requested on the day of the therapy (representing 18%), the times are the following:
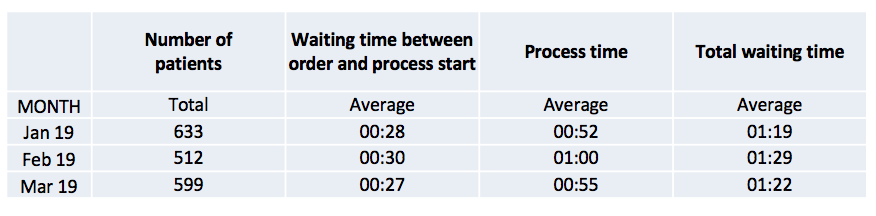
- Customer satisfaction
At the end of January, we interviewed 43 patients. Another 47 were polled in early March. What emerged from the questions we asked them is that they particularly appreciate the new internal logistics, the way they are welcomed, and the shorter waiting times. External logistics appeared to be an area where we can still improve a lot.
THE AUTHORS
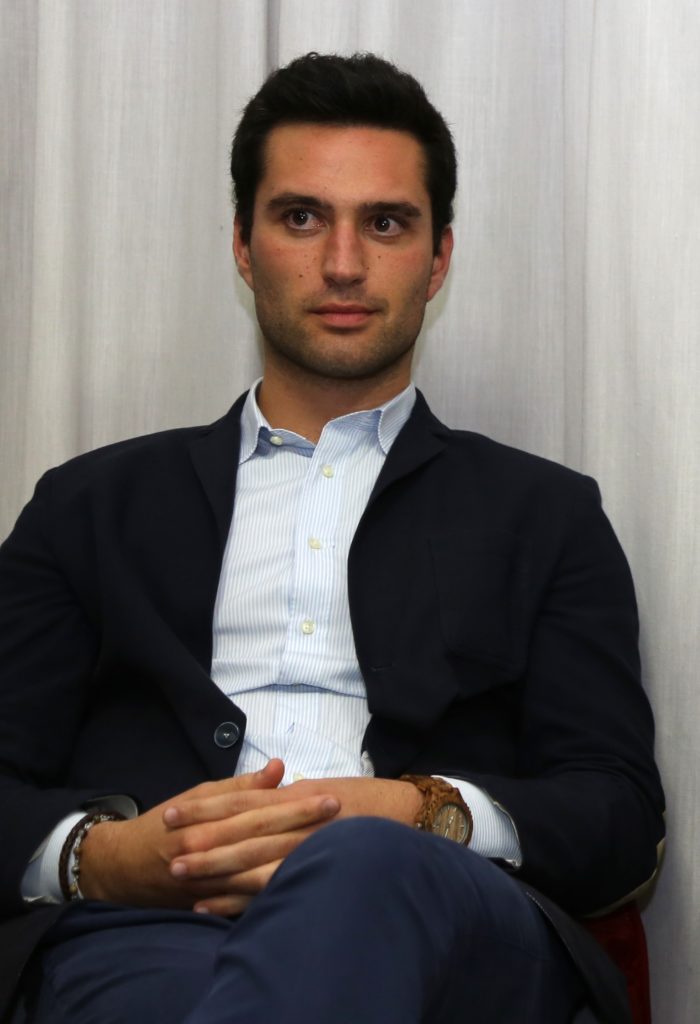
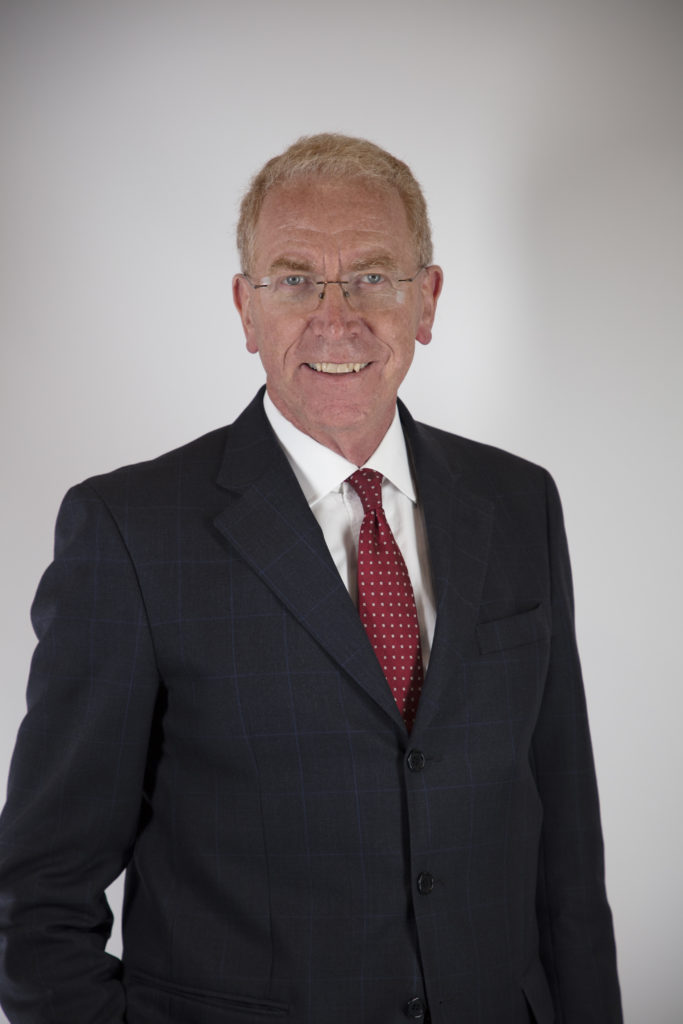
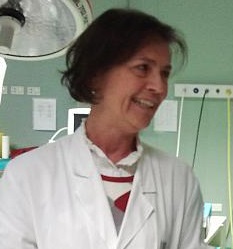
Read more
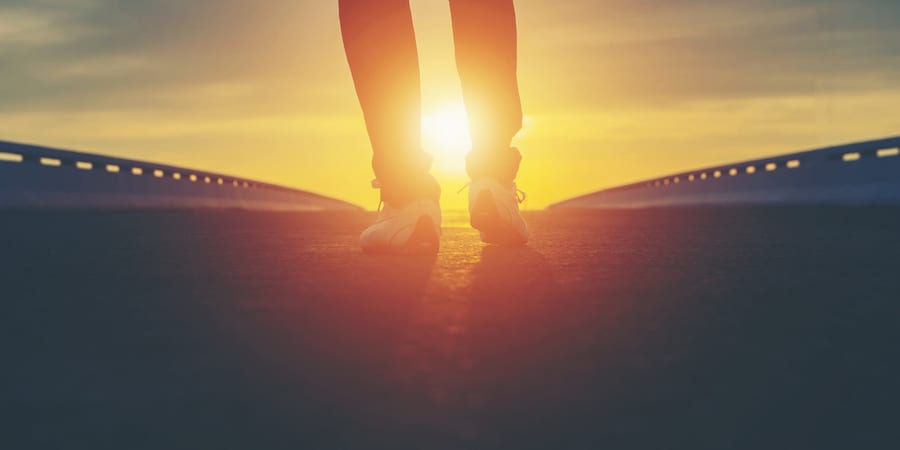
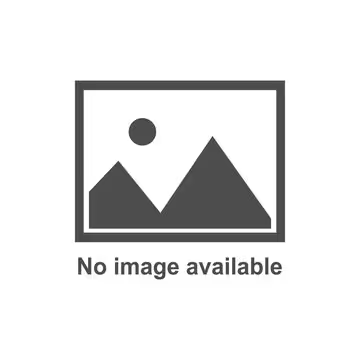
FEATURE – Lean is a people-centric system for learning that acts as an alternative to traditional management and financial capitalism. It represents the best strategy a company can adopt to meet the needs of the future.
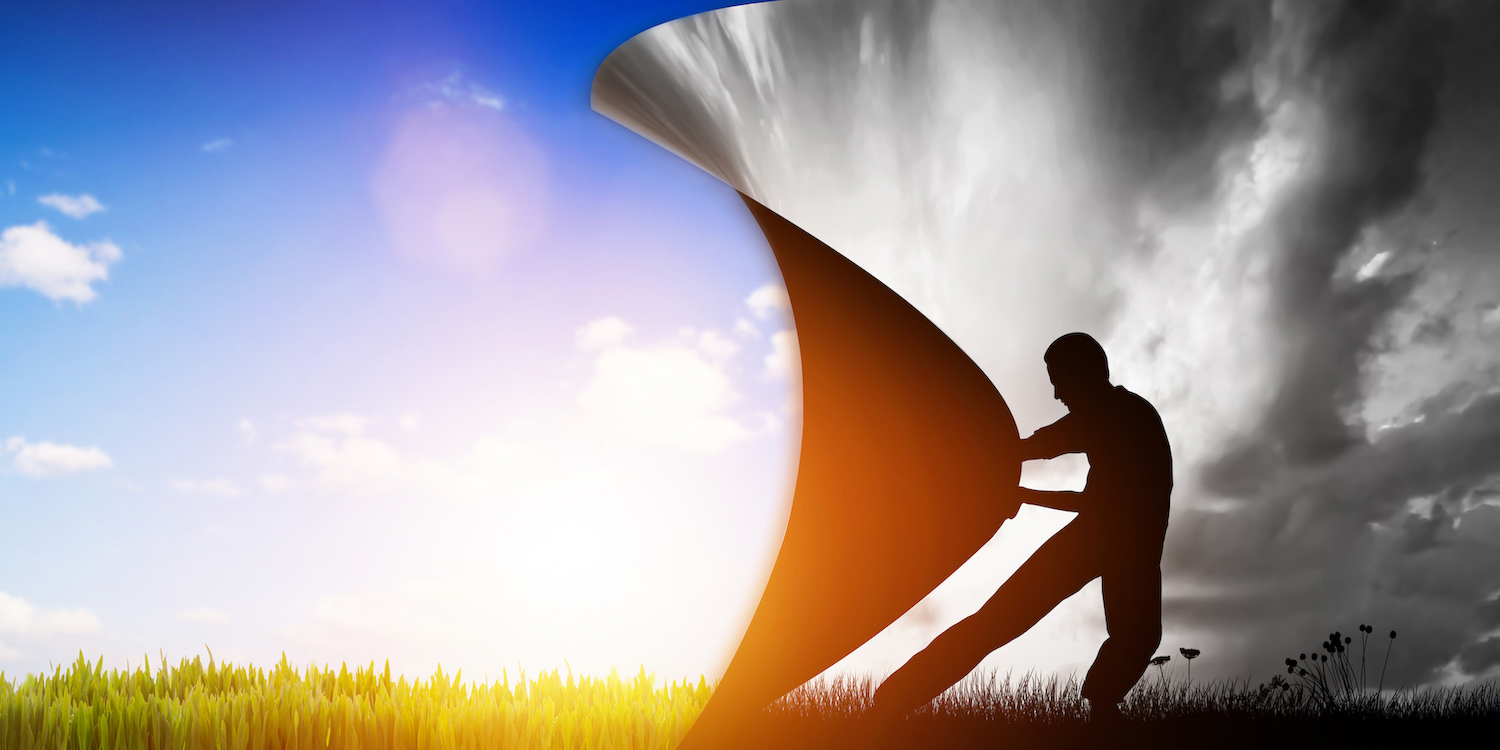
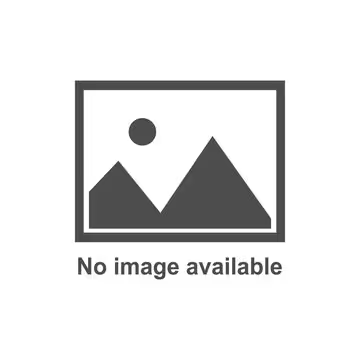
FEATURE – The author discusses how the daily practice of lean thinking develops perseverance and the grit a leader needs to improve an organization.
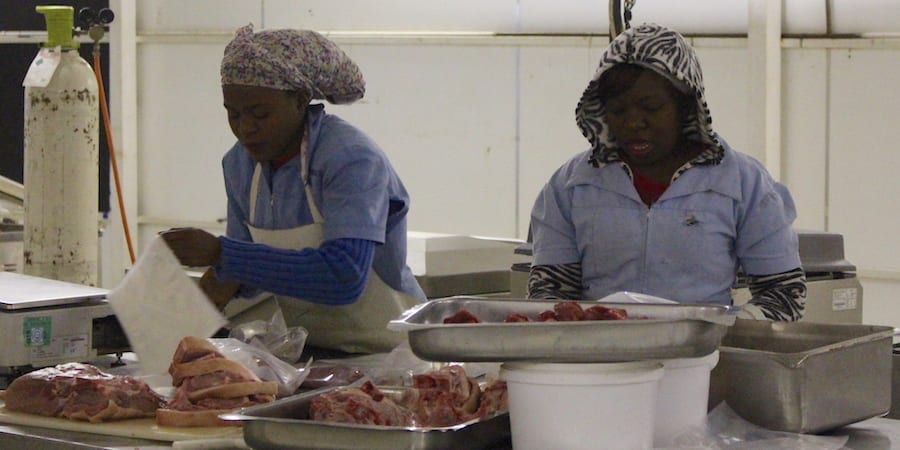
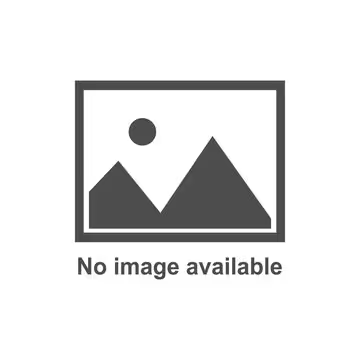
CASE STUDY – Faced with complex logistics and customer complaints, a small deli and butchery in Botswana saw in lean a way to bring the business back from the brink. The philosophy didn’t fail them.
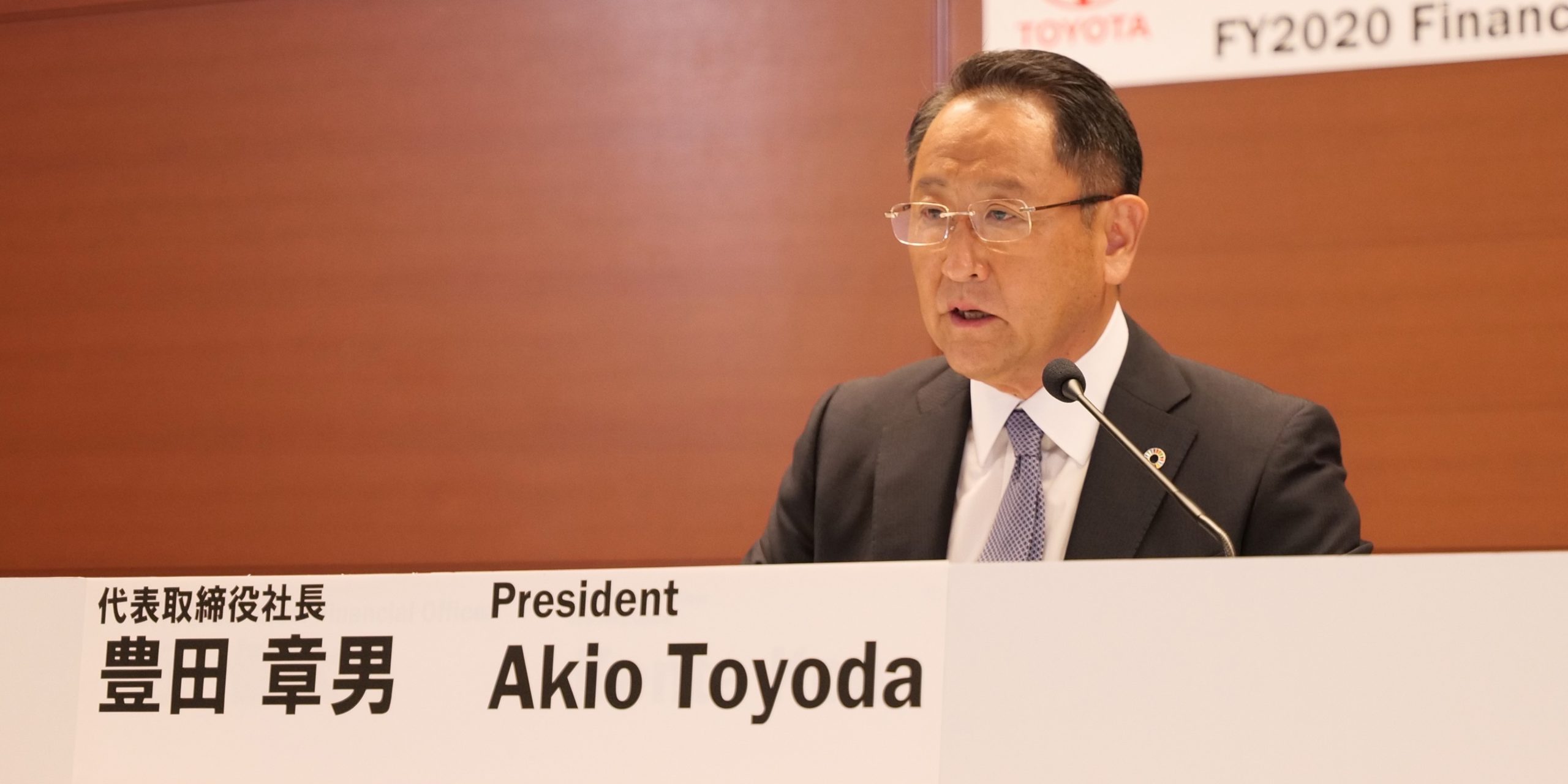
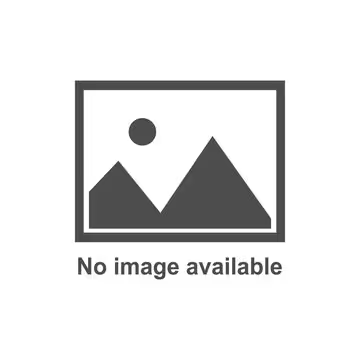
FEATURE – Akio Toyoda’s May 12th press conference to present Toyota’s financial results offers great insights into how the company is reacting to the pandemic, say Jeff Liker and John Shook.