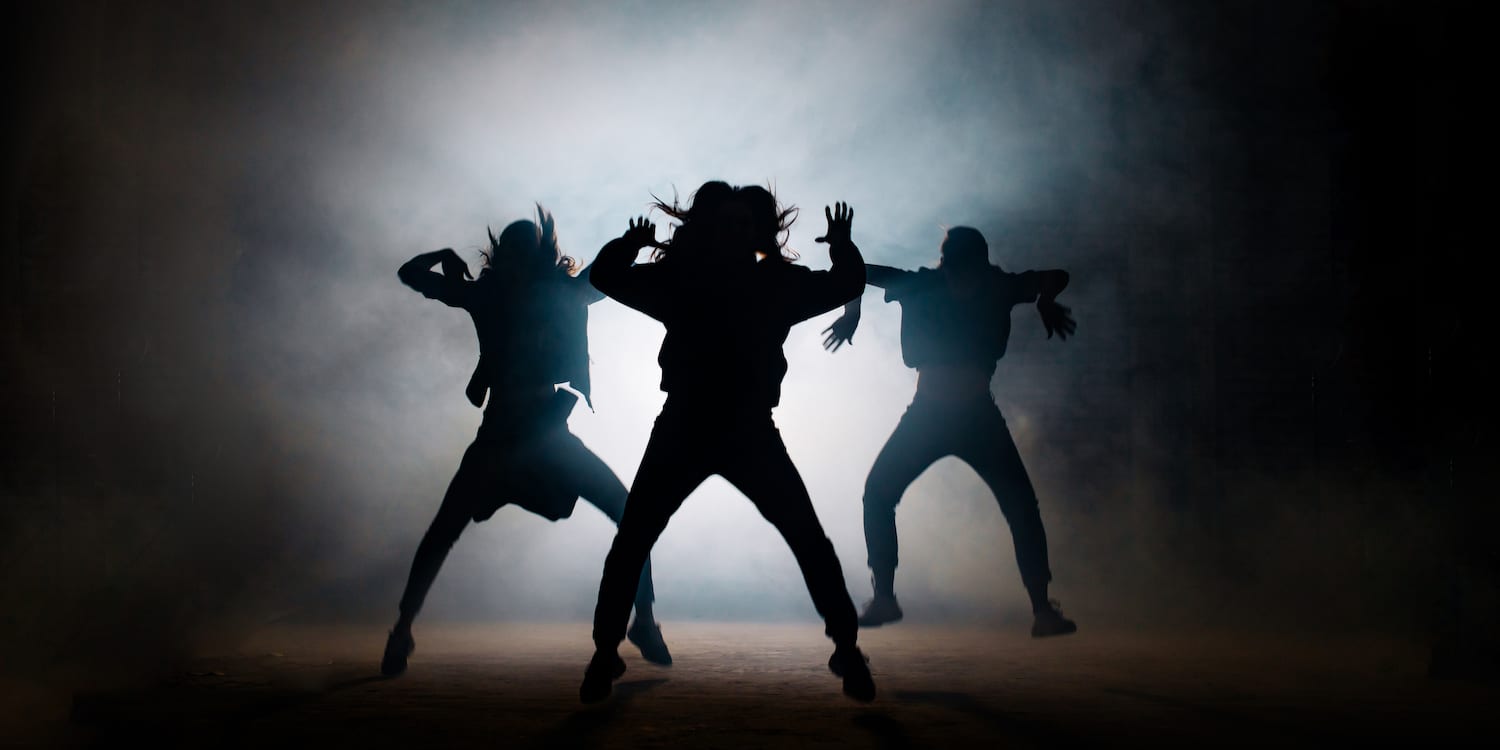
Turn the beat around
FEATURE – One year ago, the author started coaching organizations in her town of Maun, Botswana. Here she reflects on her experience and draws an interesting parallel between lean management and dancing.
Words: Sharon Visser, CEO, Lean Institute Botswana
What I love about lean is not just the way it transforms organizations but how it transforms people.
I know it is a method that revolves around using processes and solving problems to create flow and pull. However, without the people doing the work itself, lean would not exist. It only does because the workers themselves breath life into it.
In 2015, Ricardo Costin visited our dealership – Halfway Ngami – here in Botswana. He didn’t come all the way from Grupo BVL in Brazil to see the beautiful Okavango Delta (to which Maun is the gateway), but to observe the processes we had put in place at the workshop.
He told me it was like seeing an intricate ballet performance, as the vehicle, parts and paperwork travelled through the process with everyone knowing exactly the steps and responding to the melody of flow and pull.
I had heard several sports metaphor about lean, but I had never heard it described as ballet dancing. I found it powerful and I could certainly see Ngami’s processes in those terms: it is true that, when the work starts to dance to the song of pull, lean takes on a life of its own and the day flows flawlessly.
Few things are more satisfying than that moment it all works and everyone is aware of the song, the movement and the beat. When this happens, all the time you invested and the heartache you endured will be worthwhile. Like all dances, however, lean is based on a precarious balance and depends on everyone making an effort to learn the steps and find the rhythm.
I remember the moment this first happened at Ngami, which is when I really understood why they call it “takt time”: I could actually feel the beat of the metronome. Everybody did, and we all went home exhilarated.
I think that so many of us who try to help people to transform organizations often encounter a bit of an obstacle in the beginning as lean’s revealing nature collides with insecurities and fear of failure. People feel embarrassed for not recognizing the song, the beat and the steps. At times, this stops people from getting on the dance floor altogether. Some say the beat is not attainable, other want control over it. Shy personalities withdraw and the guy who thinks he can dance without knowing the steps or the music disrupts the pull and flow.
Sure enough, at first there is no dance routine, no music – just potential dancers. We start by removing obstacles from the floor so no one can trip up. We teach basic routines and steps, we show people how to find the beat, we help them to find the right backdrop and song. As leaders and coaches, we become great choreographers.
The most important thing we do is stand next to the person struggling with the steps to help them develop their routine. We teach people to dance together like in a waltz or a tango until they have the confidence to become stars. Sometimes, we have to take them to the floor ourselves and dance with them.
Eventually, if we are very lucky, we get to see people who had two left feet glide across the floor like professional dancers. And we see managers become master choreographers. Eventually, that sweet moment comes when people change the dance routine themselves, and it is so much better because they did the work.
As I reflect on this year of helping new organizations who are learning how to dance the lean dance, I feel extremely lucky to be a part of the Lean Community.
I am thankful to Ricardo who first planted this thought in my head so I could share this metaphor with you.
I am thankful to Dave Brunt and Terry O Donoghue who stood next to me, showed me the first steps and coached me through all the ups and downs of getting the show on the road.
I am thankful to the organizations I help for being brave enough to take to the dance floor.
I am thankful to everyone who shares on Planet Lean, as everyday they plant new seeds in willing soil to change the work and the world.
THE AUTHOR
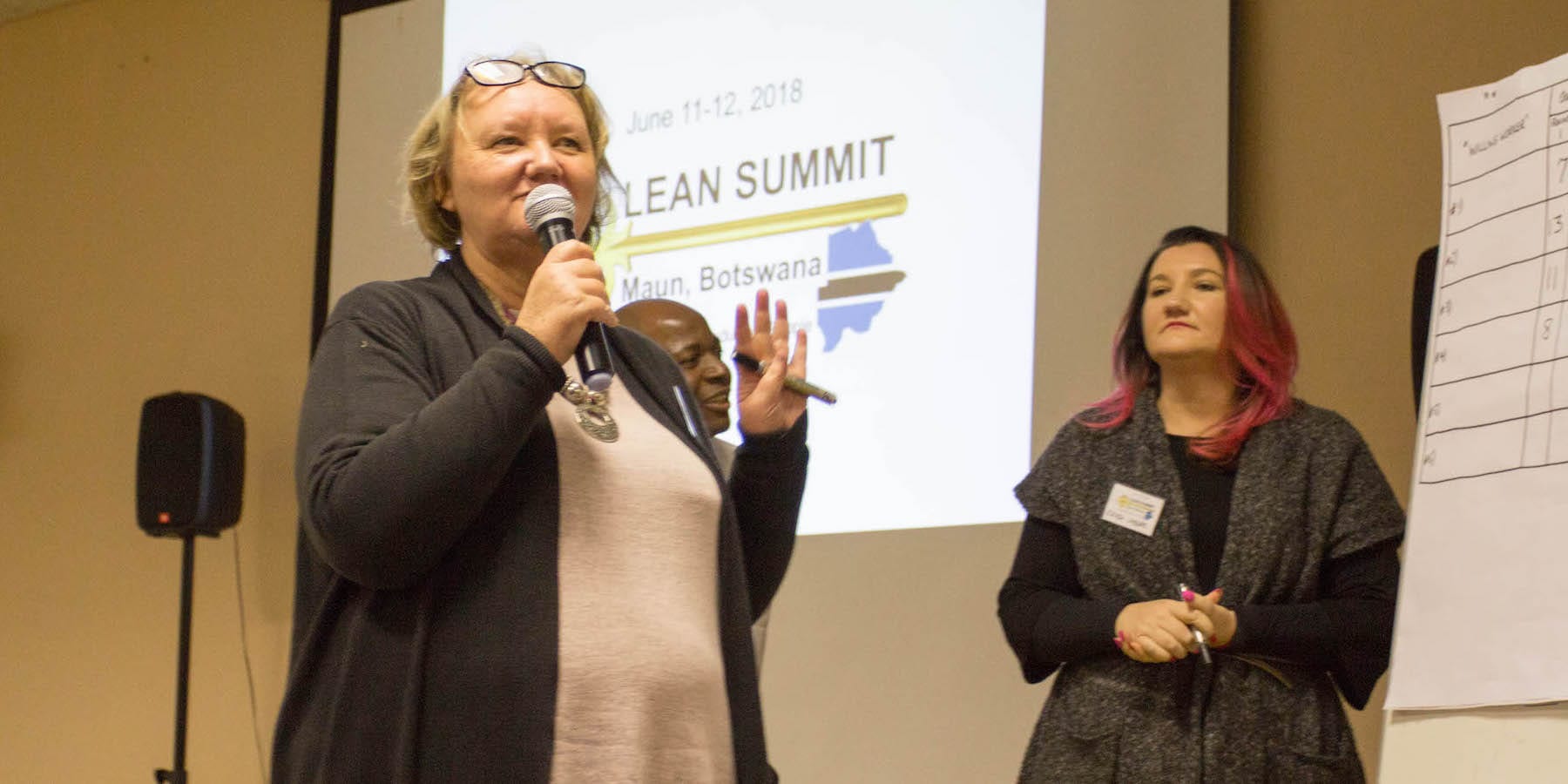
Read more
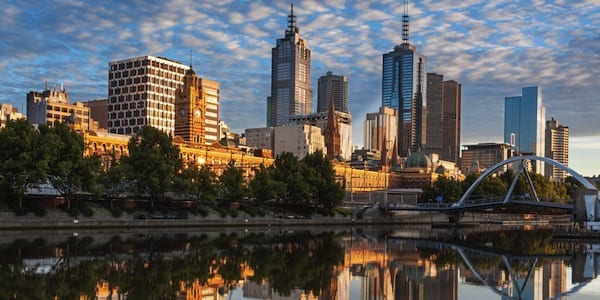
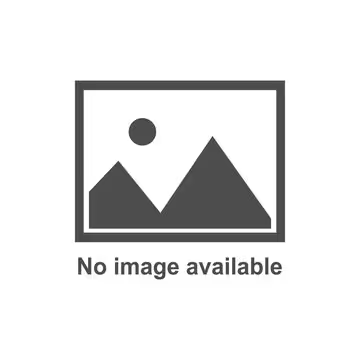
CASE STUDY - How does lean contribute to making Melbourne one of the world’s most liveable cities year after year? Denise Bennett explains the approach followed.
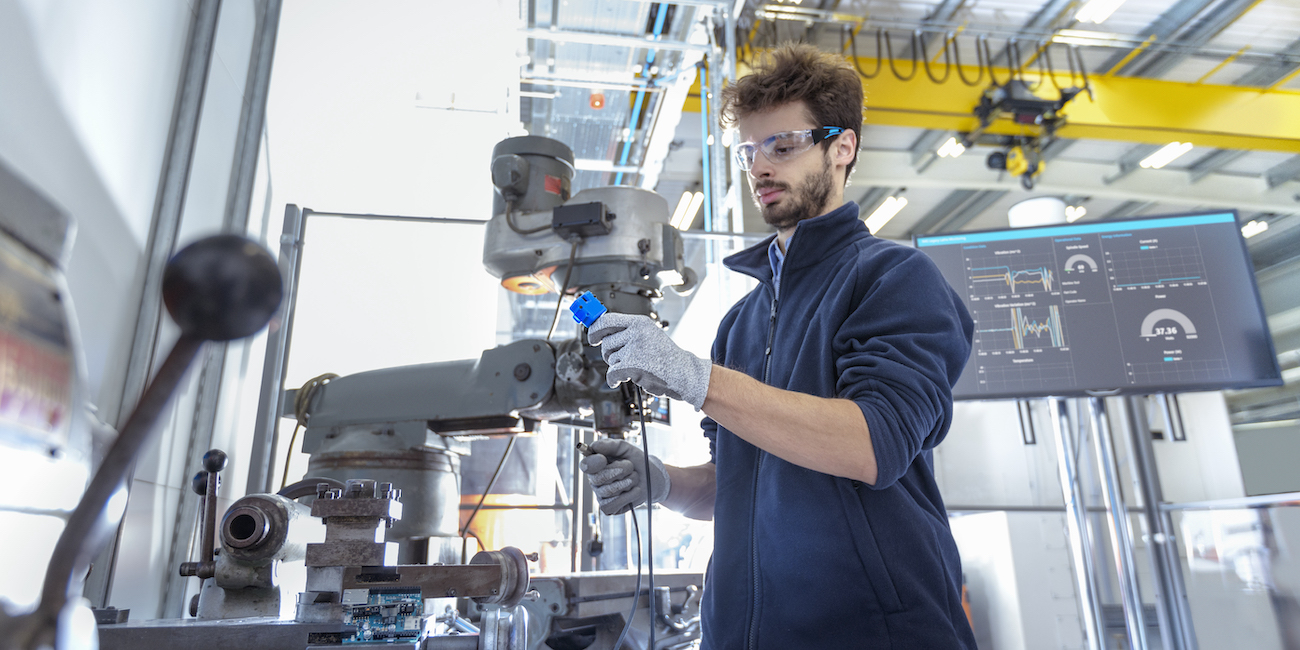
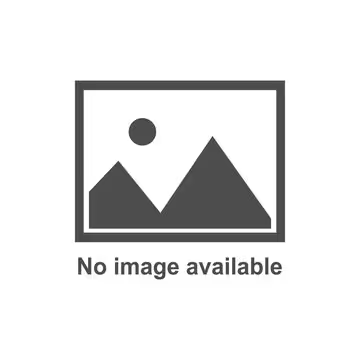
FEATURE – Through kaizen, people can directly participate in the improvement work. But without a manager’s clear responsibility and follow-up, they will left alone with the consequences of the introduced changes.
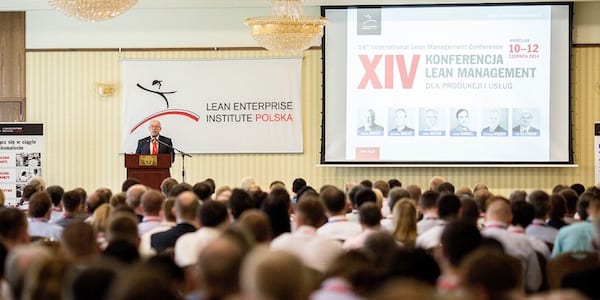
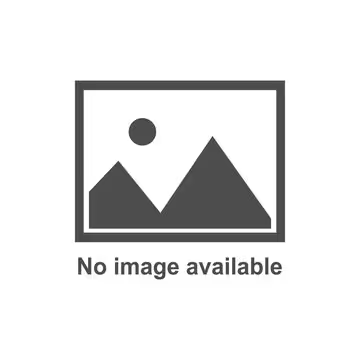
REVIEW - Roberto Priolo reviews the 14th Lean Management Conference, held earlier this month in Poland. With great presentations and speakers, the event left him with a lot to reflect on.
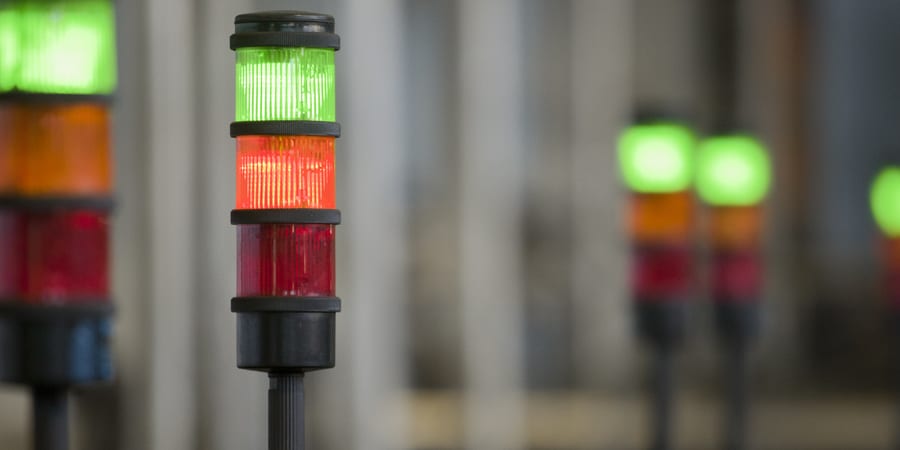
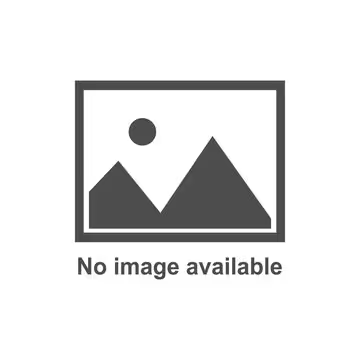
INTERVIEW – Catherine Chabiron sits down with Marc Onetto, a former executive with GE and Amazon, to discuss Jidoka and its profound effects on the way people work and think.