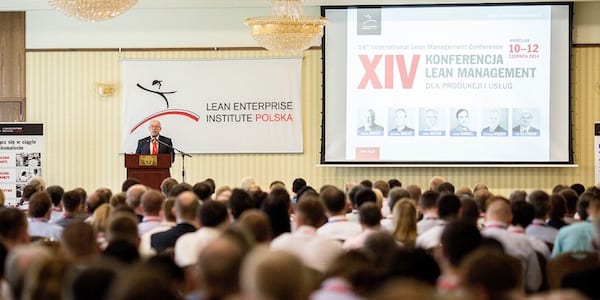
Learning lean in Wroclaw
REVIEW - Roberto Priolo reviews the 14th Lean Management Conference, held earlier this month in Poland. With great presentations and speakers, the event left him with a lot to reflect on.
Words: Roberto Priolo, Managing Editor, Planet Lean
It’s been a couple of weeks since I attended LEI Polska’s summit in Wroclaw, and many of the lessons I learned there are still swirling through my mind.
The only regret I have is not being able to attend the entire conference. I had to cut my visit to Poland short to travel to Budapest and attend another summit (for a review, click here) – however, there was so much to learn at the 14th Lean Management Conference that I can’t really say I left empty-handed. Even attending half a day would have been productive!
Running an event like this is no easy task, and it’s clear that the institute, LGN’s affiliate in Poland, has been doing this for a long time: the organization was superb, the speakers top notch, and the content very though provoking. And the customers seemed to agree with me, considering that 420 of them convened at the Haston City Hotel to attend these three days of lean learning.
We were spoiled with choice, which makes it hard for me to say what the highlight was.
On day 1, keynotes from Dan Jones and Michael Ballé made for a great start to the conference. Michael asked the audience what transformation we are seeking, and focused on the differences between Taylorism and a lean system. He then went on to say there is actually no such thing as a lean enterprise, only lean leaders. His was a powerful reminder that tools will only go so far, and that without a CEO who enthusiastically supports lean a transformation is simply not possible.
After a coffee break, there were two main streams to pick from. One was mainly intended for manufacturing organizations, the other for service ones. In the afternoon, a third one would be added: for CEOs and senior executives (it’s not a coincidence that running that session was Michael Ballé, an experienced lean executive coach.
I decided to stick to manufacturing in the morning, and I was rewarded by an insightful presentation from Mark Hamel, who flew in from the United States to share his knowledge on kaizen with the local lean community (his book Kaizen Event Fieldbook had just been translated into Polish). I particularly appreciated his analogy of the champagne glass, where the big bubbles represent value stream kaizen and the small bubbles represent point kaizen. What to prioritize is entirely dependent on the company’s needs – that was his point.
Also coming from the States was Mark Reich, from the Lean Enterprise Institute. Mark told the audience about his years working at Toyota in Japan and about the lessons he learned while there. His presentation went a long way to explain Toyota’s approach to people development and problem solving.
Right before lunch, Malgorzata Jakubik and Robert Kagan gave an entertaining and insightful talk on the national traits of the Poles and explained how these can be turned into elements that support a lean transformation as opposed to obstacles.
In the afternoon, I decided to turn to services and attend the learning session held by Stephen Parry. How great it was to be challenged so much! Stephen asked questions that initially raised a few eyebrows (including mine, I must say), but that eventually gave attendees the opportunity to grasp some of the most important issues characterizing a lean implementation in a service organization.
At the gala dinner that night (which was made even more lively by the performance of an actor – too bad my Polish is a little rusty) and in the coming days, I found myself reflecting over and over again on the things I had learned and all the interesting conversations I had had.
I guess that’s a pretty good sign the conference was a success!
[widgetkit id=31]
Read more
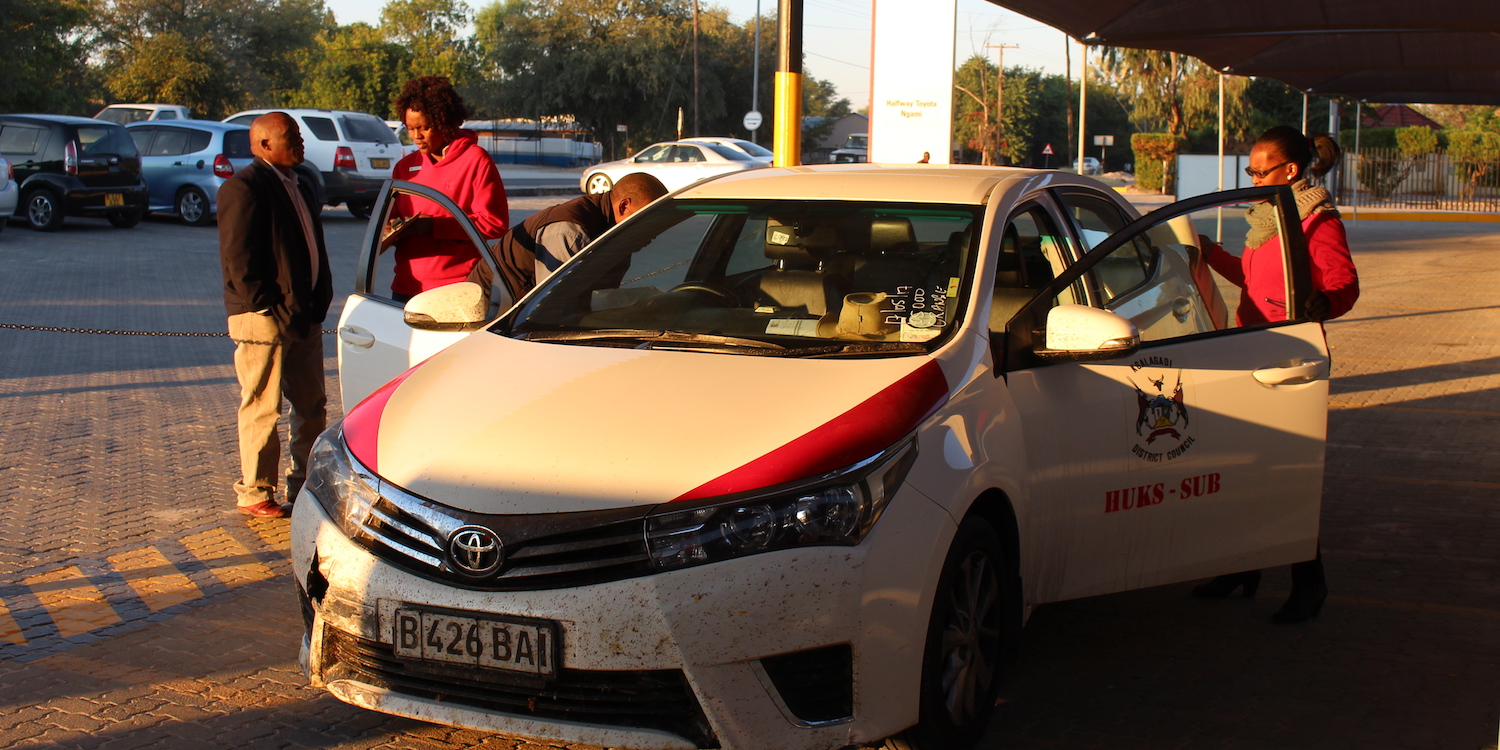
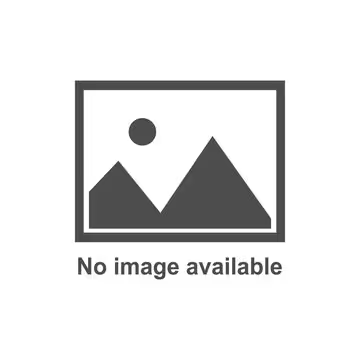
FEATURE – In this intimate, moving account, the author shares her journey of personal transformation that caused her mindset and her attitude towards employees to dramatically change.
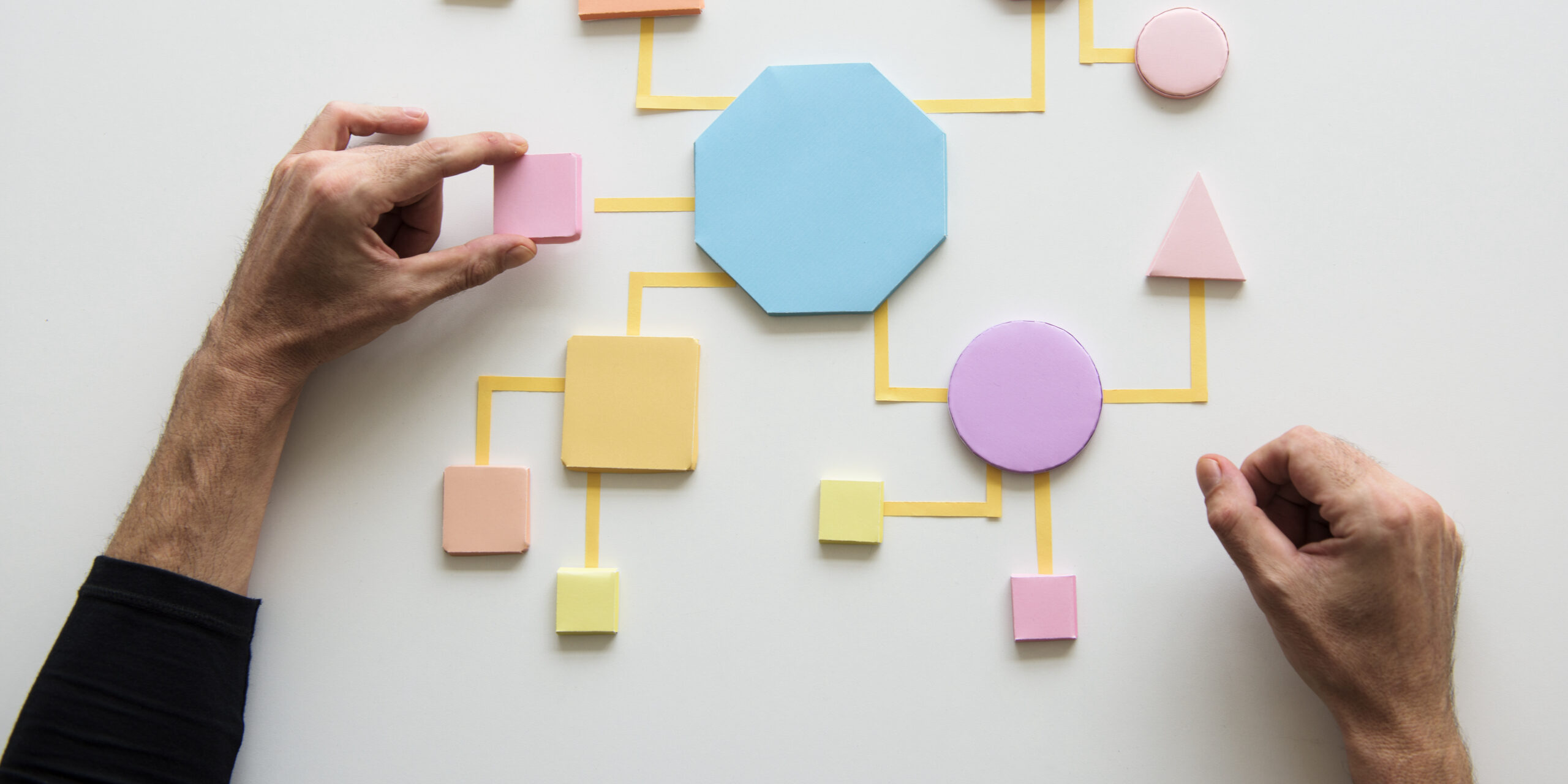
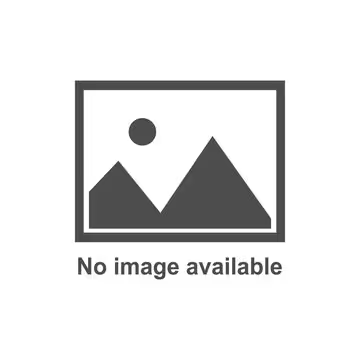
SERIES – The authors of The Power of Process open their new series by explaining why it’s critical to integrate product and process development.
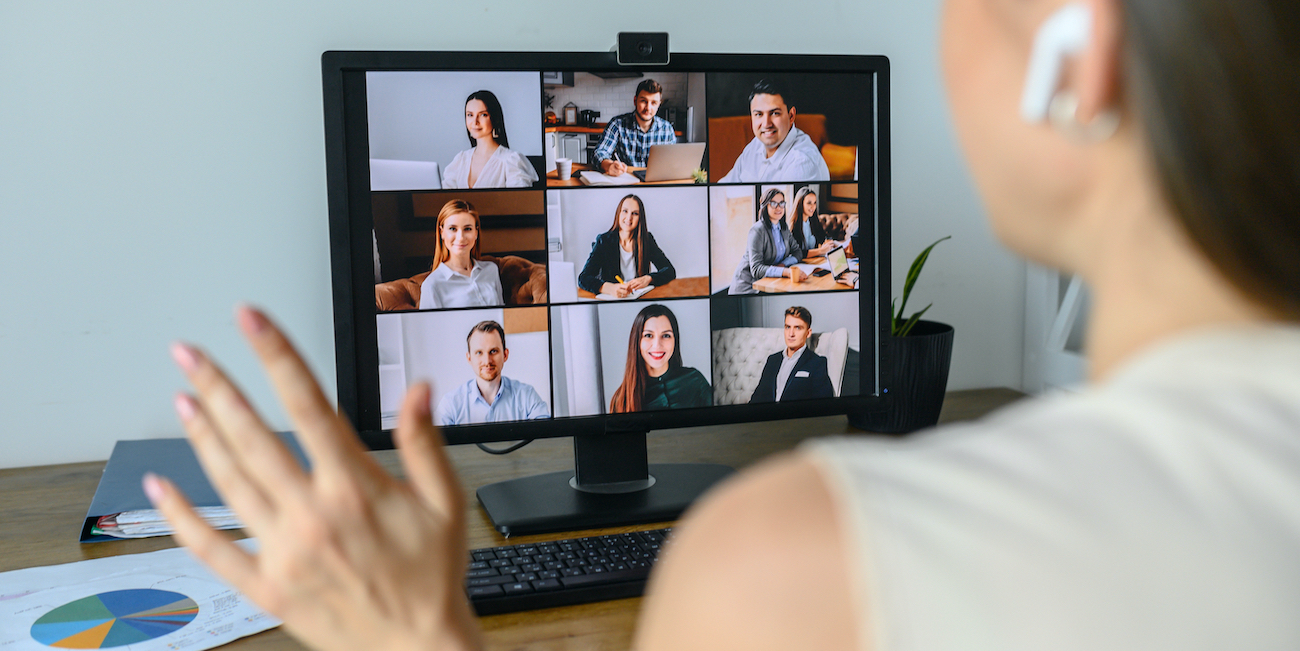
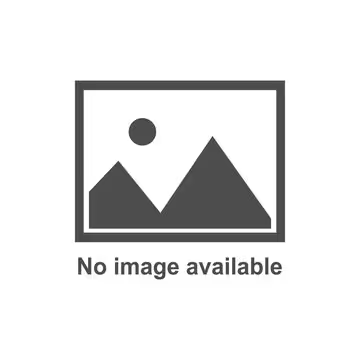
FEATURE – The Covid-19 pandemic has reminded us all that the nature of the work has changed forever. The author discusses remote work and how Lean Thinking can help you make the most of it.
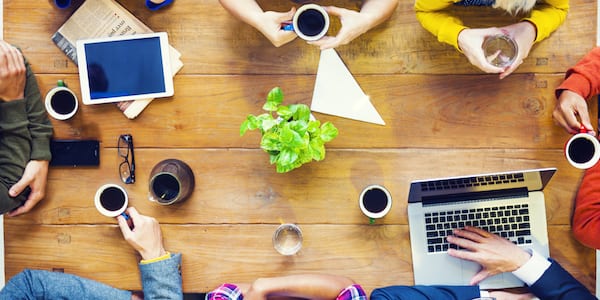
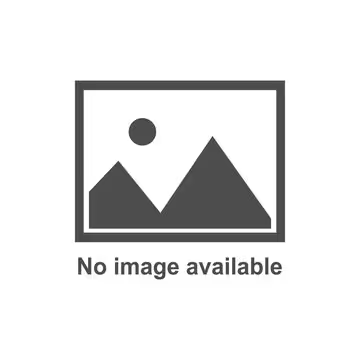
FEATURE - An initial look into the impact of lean management principles on the growth of young organizations hopes to encourage further analysis into why and how lean startups succeed.