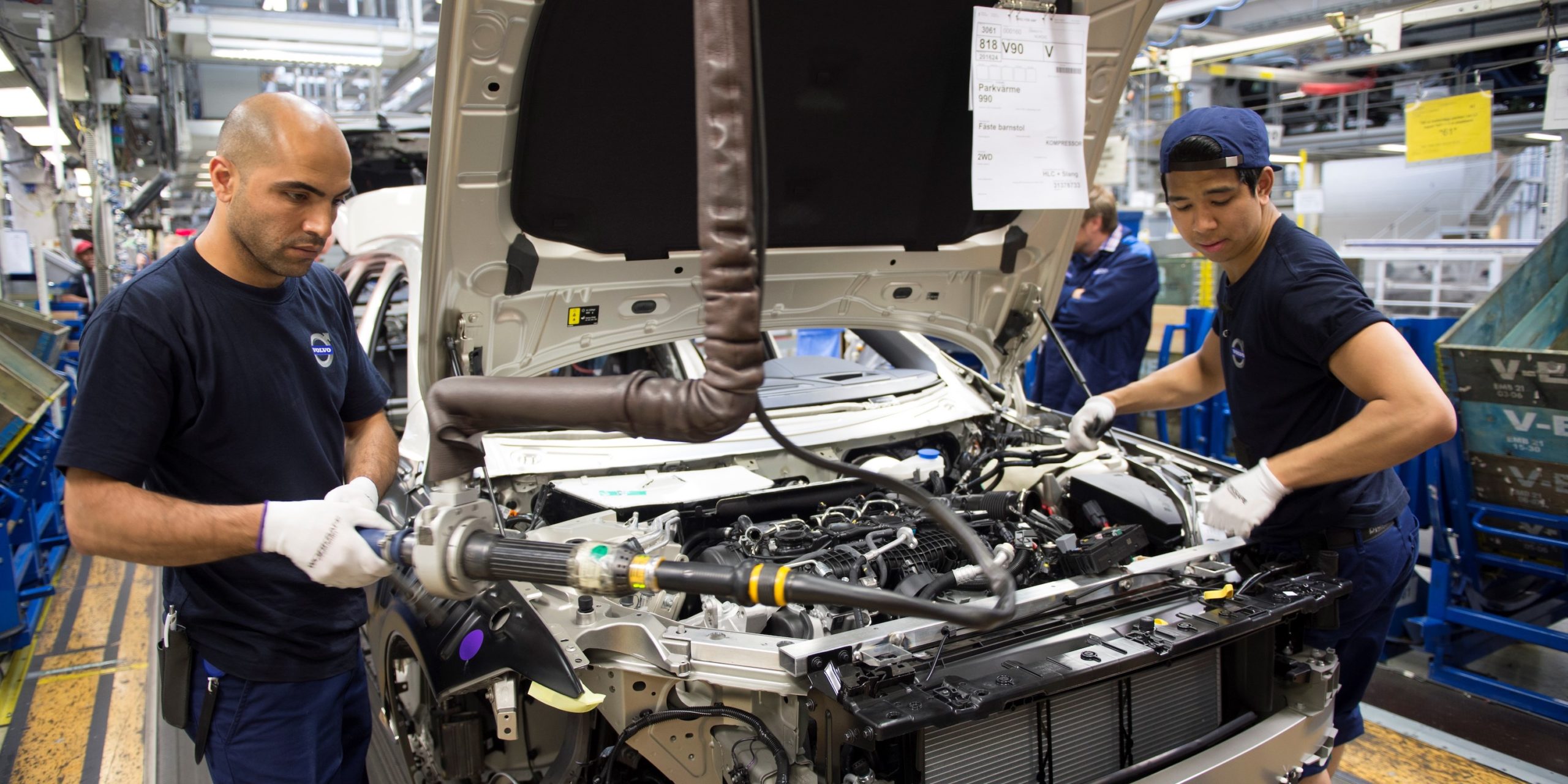
Leadership development at Volvo Cars
CASE STUDY – What is the approach to people development used at Volvo Cars? The authors explain how the organization has created a production system fully owned by operators and managers.
Words: Eivind Reke, Organisational Secretary at Los Norge, and Gert Frick, Director of Volvo Car Manufacturing System VCMS.
Main photo and picture of Duett: courtesy of Volvo.
Volvo Cars started designing and manufacturing cars in 1927 and is something of an icon in Scandinavia. Known for its classic cars, such as the Duett estate, and for the invention of the three-point safety belt (they waved the patent so that everyone could benefit, saving over 1 million lives to date). Volvo has always put people first.
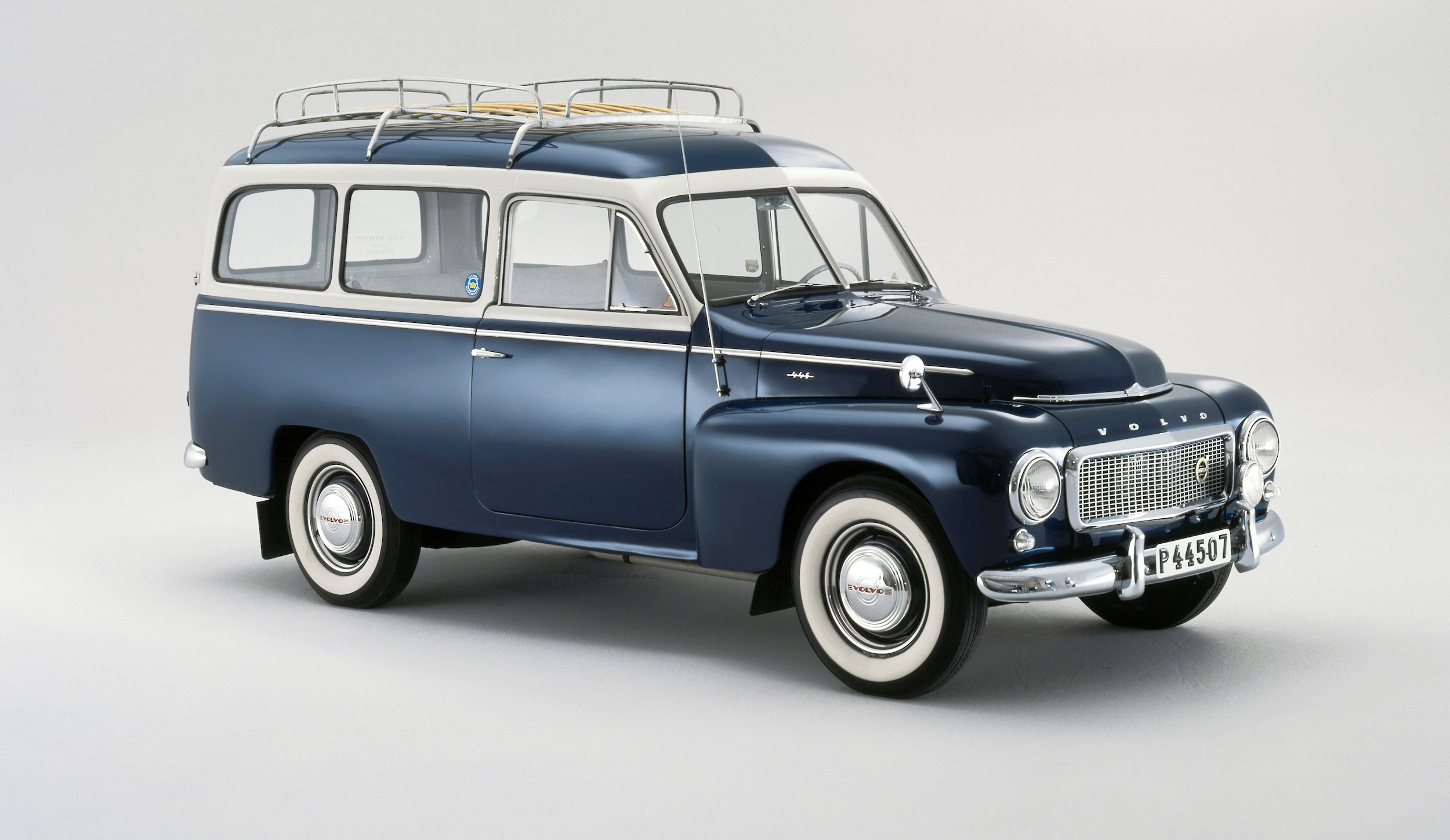
With production facilities in Sweden, Belgium, the USA and China, Volvo is now a global car company under Chinese ownership. However, it is not only customers Volvo cares about. The company also has a long history of worker empowerment.
Volvo have been on a journey of employee engagement and worker empowerment for a long time. Back in the 1980s, Volvo investigated different ways of assembling, to remove the pressure of the moving assembly line from their workers. Relying on heavy involvement of their front-line staff at their plant in Kalmar, Sweden. Volvo even tested line-free assembly – with self-organized teams assembling the entire car in a single cell. The experiment didn´t last, but the idea of putting people first is still central to Volvo’s thinking.
After implementing a company-wide lean program in the beginning of 2000s – called Volvo Cars Manufacturing System – the company is now diving into the details to discover deeper layers of problems that are preventing their operators from performing the work of car assembly in a smooth way. The driving force of their thinking is still the same as it was back in the ‘80s: How can we develop a company where people are respected, where we continuously and systematically work to relieve our employees of the pressure of the assembly line, where we show respect for people? One of the authors (Gert) has over the last few years developed a leadership training program inside Volvo, inspired by the managerial thinking of Taiichi Ohno. To support this process of discovery and improvement. In June 2019, the other author (Eivind) was lucky enough to see the results and benefits of this on-going program. So, what does it look like?
When Volvo started its lean initiative, it was mostly a staff-driven production system with lean training carried out in traditional classroom settings by dedicated lean coordinators. The content would often consist of 80% theory and 20% practical training. However, Gert and his team have now developed a training program that is centred around practical exercises out on the factory floor, studying the point of value creation closely. Over the course of the two-week training, managers – from team leaders to plant managers – spend almost 90% of their time out on the factory floor. The training course is all about improving the conditions for front-line operators, as leadership development is achieved as a result of improving the business.
The basis for the program is to go to the place where the work happens, observe it and study it, understand the conditions (eliminate Muri, reduce Mura and Muda), solve the problems you see, and establish the improved standardized work together with the team performing the operation. The first two days are spent observing and identifying opportunities for kaizen, based on the theoretical input from the trainers. The theory is based on the principles of standard work developed by Ohno and his Toyota pioneers. In other words, it´s back to basics:
- First, look at overburden (Muri), imbalance (Mura) and the seven wastes (Muda);
- Standardized work; takt-time, work sequence and standard in-process stock;
- Cycle-time and 3 types of standard work (without variation, with variation & non-cyclic);
- Just-in-time: one-piece flow and pull;
- Jidoka – zero defects, andon, visualization and separation of man and machine.
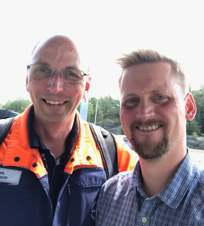
Before the course starts, facilitators like Sture Simonsson (pictured here with Eivind) will identify a process or operation that the participants will use as their training ground. Once the operation is identified, Sture will spend some time with the operators, observing the work and interviewing them, getting in-depth information on the work from the operators themselves (what challenges they normally face and so on). He will also inform the operators about what will happen and what the idea behind the training is, to make them comfortable with the situation. This does two things: once the students arrive, the operators are comfortable having them around; and, secondly, the facilitators have a head-start on their students. The first creates a relaxed environment, while the latter allows Sture to create scaffoldings for students if they see too big a gap between their current thinking and where they need to be heading.
In the first week, you will also go through practical training exercises in the basic skills training center. The center doesn’t have permanent coaches. Instead, the coaching role is rotated between line managers for six to twelve months periods. The aim of the training centre is to both allow new operators to practice the required skills, so that they are better prepared for the assembly work on the line. For example, one training station focuses on the picking, inserting and fastening of screws by hand (in the picture below, Eivind is guided through the training exercise by trainers Mahmoud Masharawi and Tuna Tunca. Picking 5 screws, inserting and fastening without looking).
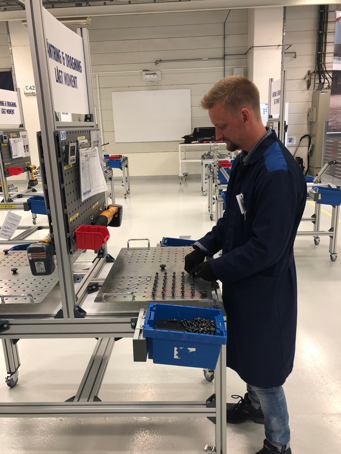
There is also a scaled assembly line in the facility that allows them to cover a lot of basic theory for the leadership training program in a controlled environment. According to Mahmoud and Tuna, there are a number of things that often occur here: for example, working faster than takt-time (thus building up inventory) or trying to fix mistakes yourselves and not pulling the andon cord (thus losing control of quality).
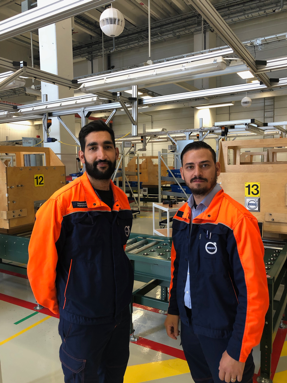
The training that managers receive, however, causes a shift in how they think. When we spoke to Patrik and Anders – Patrik is a line-manager responsible for six different operations and Anders is a team leader – it was clear that the training they had received had made a difference in the way they think. They were also working on training the line operators to think about their own work – developing deeper knowledge about the work will make everyone better at their job.
We asked Patrick to share his thoughts and he was clear that things are changing for the better. Teams are smaller and are responsible for a smaller area, which has led to a more tightly knit group and an environment that is more conducive to personal development. Even though it took time, operators are now much more involved in the improvement work. Patrick also noted that he himself is growing through problem-solving, developing a deeper understanding of the operations and how the organization works. He said: “We are no longer super-fixers looking for someone to blame, but problem-solvers looking for the root causes of our problems.”
There is a shift happening at Volvo Cars. The company is slowly moving from a staff-driven production system to a production system fully owned by operators, team leaders and their managers – one that emphasizes the development of people through practical exercises at the gemba. Now, by focusing on the personal development of each person, the organization is growing through problem-solving. Gert, Sture, Mahmoud, Anders, Patrik and Tuna are seeing a shift in leadership behaviour, too. Managers are spending more time out on the line and are committed to self-development and the development of others. Working towards an ideal where managers and operators have deep knowledge of their own work, creating a workplace where knowledge is easily attainable, where people can work in a smooth flow, and where muri, mura and muda are systematically reduced.
So, where do you start if you want to develop a leadership program like Volvo’s?
Start by looking at what problem it is you want to solve, and then ask yourself the following questions:
- How can we develop leaders with practical lean competence and experience?
- Go to the where the value adding work is carried out and study. Where is the overburden? Where are the problems?
- How can we reduce variation and the number of tasks in each cycle of work?
- How can we create a better workplace for our operators?
And remember. To learn lean, you must practice lean. Whatever your value adding work may be.
THE AUTHORS
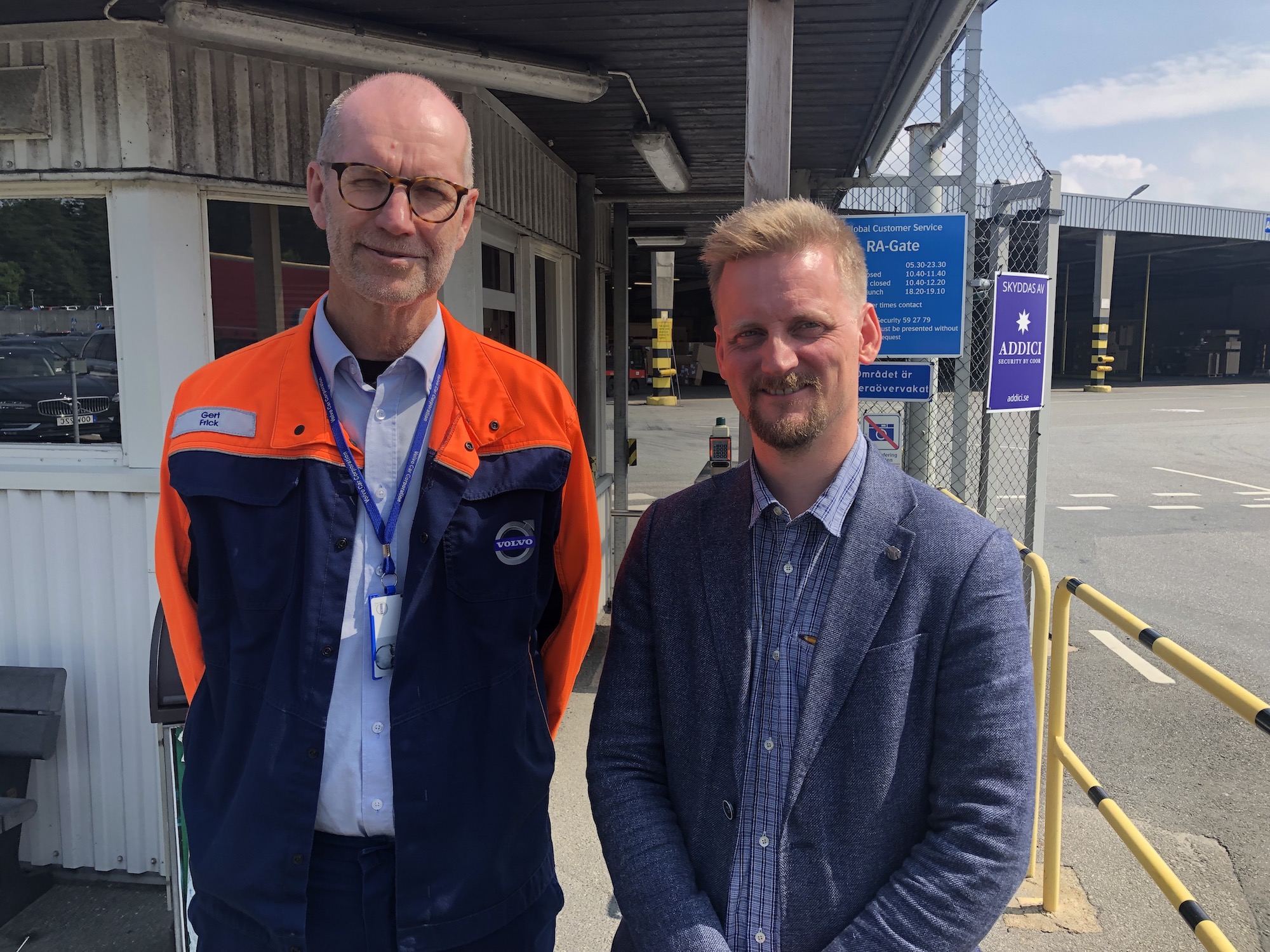
Read more
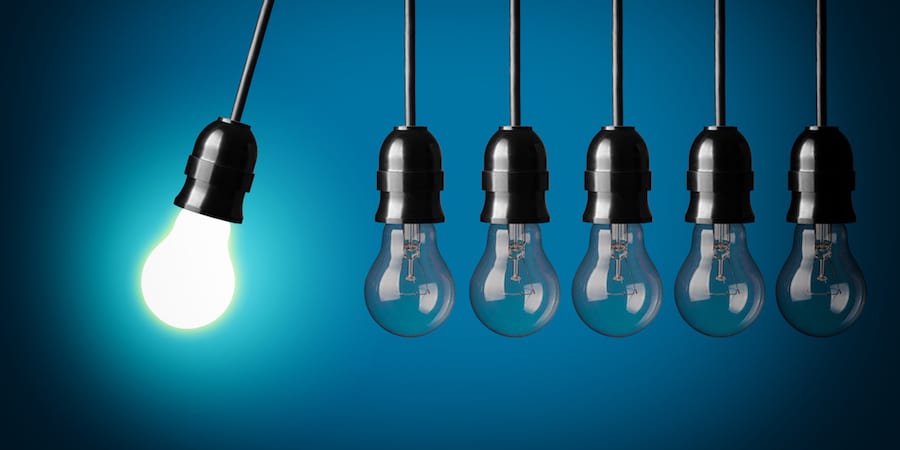
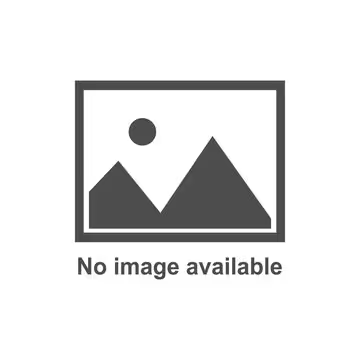
FEATURE – For this new monthly article, we will be asking five lean practitioners the same question and share their answers with you. We started by asking them about their biggest lean mistake.
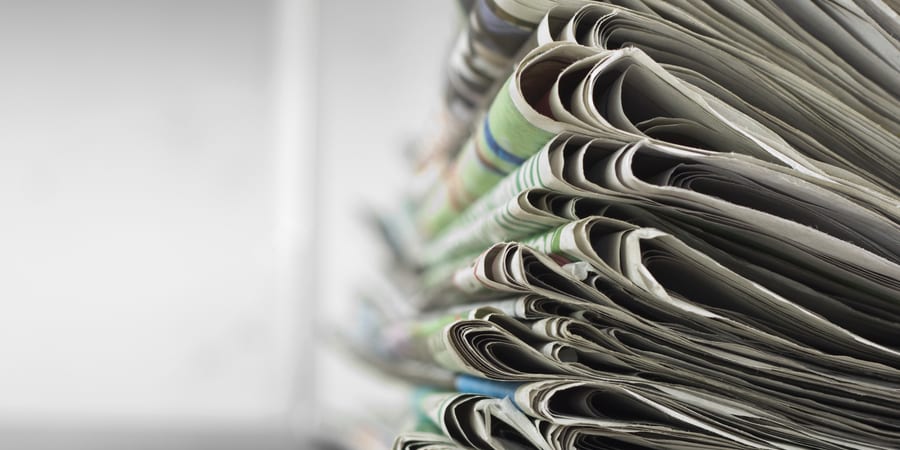
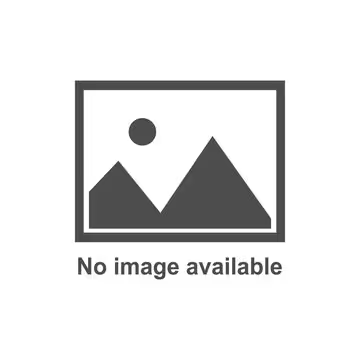
EDITOR'S LETTER – If you have missed any of our May articles, we come to the rescue with this monthly round-up of Planet Lean content, to provide you with the highlights and keep you up to date with the latest in lean thinking.
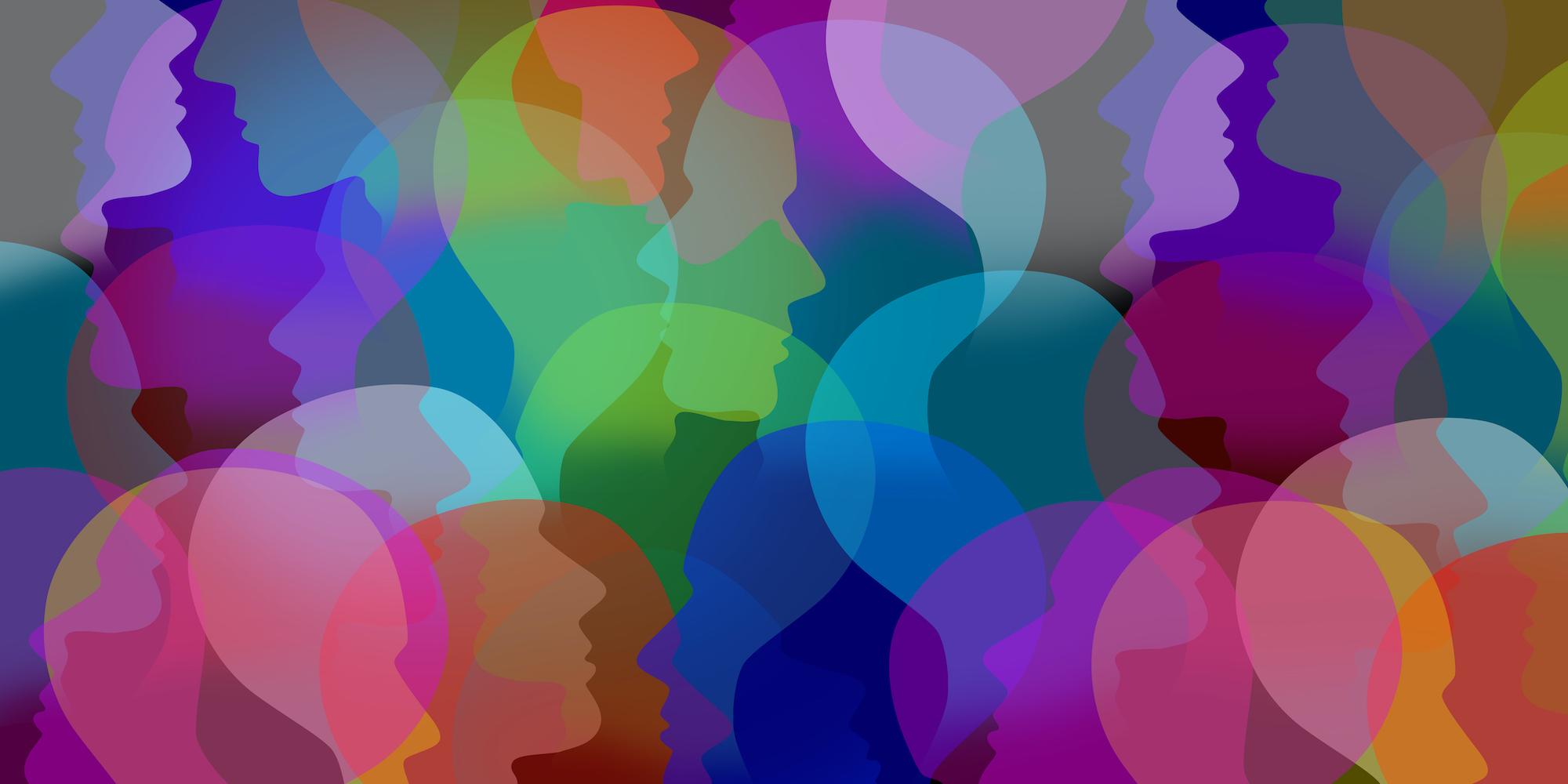
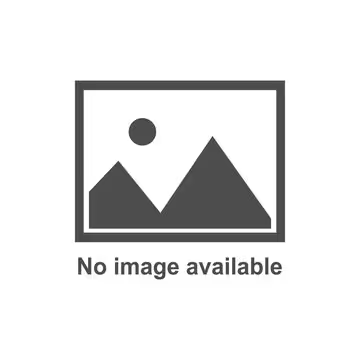
FEATURE – This compelling article explores how our brain constantly looks for emotional resonance with the environment around us. Is this System-3 type thinking the key to enabling joint problem solving?
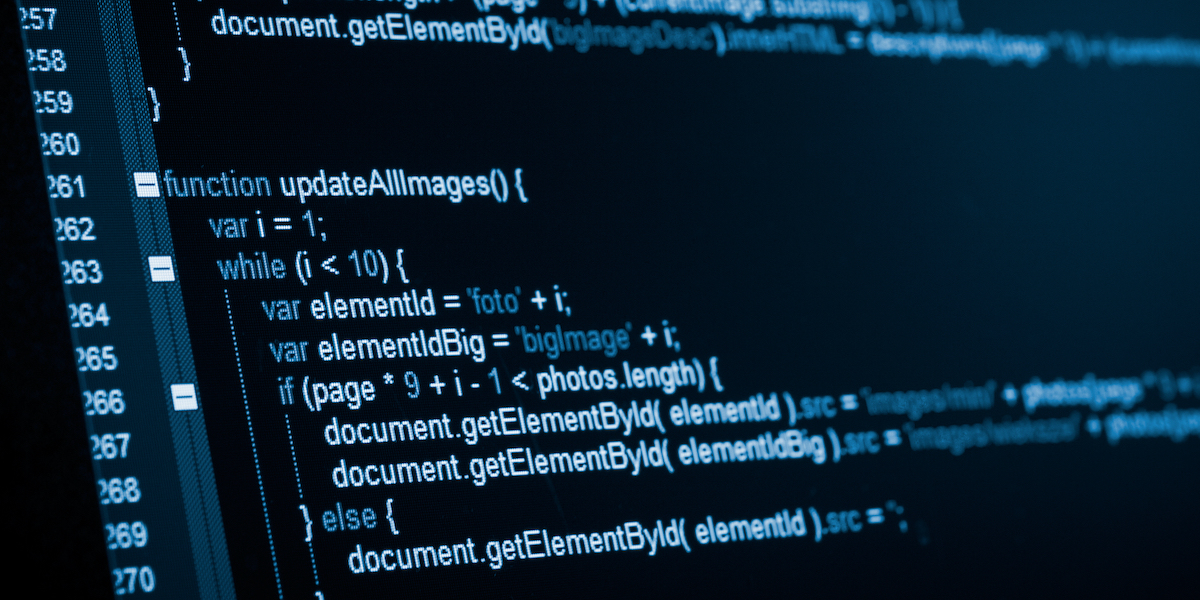
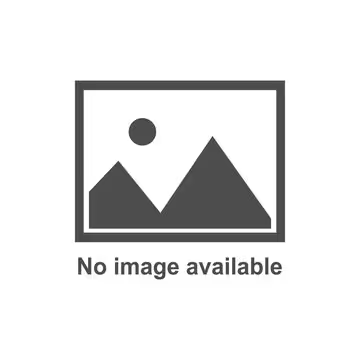
FEATURE - The author explains how a recent book on radical quality improvement in manufacturing inspired him to initiate similar experiments in his software development firm.