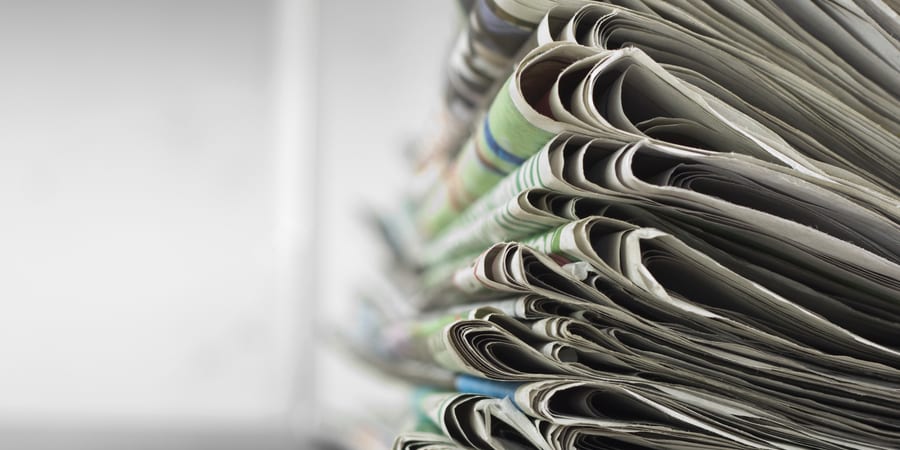
Our editor shares the May highlights from Planet Lean
EDITOR'S LETTER – If you have missed any of our May articles, we come to the rescue with this monthly round-up of Planet Lean content, to provide you with the highlights and keep you up to date with the latest in lean thinking.
Words: Roberto Priolo, Editor, Planet Lean
Among the problems we face each day as we try to drive our transformations forward, it is sometimes all too easy to forget that there is a bigger role for lean to play: that of improving our societies and our world, to give us all a better future.
Last month’s most eye-opening Planet Lean article in this sense was perhaps Marty Neese’s. Marty is the COO of a solar company based in California, SunPower. In his piece, he discussed how we must embrace a different industrial model – the circular economy – if we are to survive as a planet: the idea of “cradle-to-cradle”, it turns out, goes hand and hand with the value- and efficiency-driven principles of lean management. He wrote: “The limitations of our planet are starting to show and unless we adopt a new, leaner and more responsible approach to designing and producing what we need, our future won’t be too bright.” A powerful reminder.
Talking about the future role of lean necessarily entails analyzing the state of the industry in which the methodology was first developed. In his May column, Jim Womack made the argument that lean already changed automotive once and that it can certainly do it again. Indeed, Mobility 2.0 is a huge challenge, but also an incredible opportunity, which lean can help us to seize.
Whether an electric vehicle, a metal part or a service, to build a new product that works requires an assessment of the feasibility of our idea. In his article, Boaz Tamir discussed the risks of jumping into developing a new product (which we think groundbreaking) without having done our homework first. Can you imagine the Wright brothers flying without having fully assessed their theories?
We also had another fearure from Ian Glenday’s series on leveled production, which explained why it is not economies of scale we should pay attention to, but “economies of repetition.” Ian deemed them “crucial in developing a sustainable continuous improvement environment, delivering increased performance and making our people less stressed and more empowered.”
Speaking of improvements at the gemba, what are the main obstacles to achieving them and how easy are these obstacles to see? This is the question that Michael Balle’s latest article aimed to answer. Michael referred to hurdles as the capital sins of the gemba and analyzed each of them. An extremely useful guide for your next gemba walk.
We had a fair share of healthcare in May as well. First, we published an interesting case study on the people-driven transformation of Antwerp University Hospital (they saw the Productive Ward program in action in the UK and drew inspiration from it). Secondly, I profiled a former nurse from Tasmania who pioneered the use of lean in Australian healthcare. The profile on Denise Bennett is a must-read for anyone who is working to develop a lean culture in a healthcare or government environment.
The profile shows once again how critical it is to get leadership involved and change their way of thinking and behaving. In fact, we always say that leadership is fundamental, but we rarely stop and think of the fact actually have to concretely do something to drive lean forward. To help us answer this question, we published Torbjørn Netland’s study into the managerial tactics in corporate programs that tend to facilitate the adoption of lean thinking.
Speaking of corporate environments, we also featured the IT department at Nationwide, which as been implementing lean with great results thanks to a successful management system and leadership participation in the onboarding of new recruits.
We had another great story from the United States, all the way from the heart of the Far West! In Nevada, a Kinross gold mine has been implementing lean management principles and practices to try to make everybody on the site a problem solver and to turn around the site. An inspiring story written by passionate practitioners that, with everybody on board, lean can truly move mountains.
Finally, we introduced a new series – One Question, Five Answers – in which (the name says it all) we ask five lean practitioners to answer the same question. Capturing the variety of answers is important to paint the picture of a diverse, vibrant community that is committed to continuously learning from their mistake. In fact, the very question we asked was “What is the biggest lean mistake you have ever made?” This seems to have sparked your interest, so we will try to run it for another couple of months at least.
If you haven’t done so yet, I encourage you to subscribe to our updates by clicking the SUBSCRIBE button on the top right corner of our page. This way you will receive an email notification every time a new article is published on Planet Lean (you can select certain categories – like case studies or interviews – should you decide you don’t want to be notified for every new release). We are in the second month since our redesign, and I am still very keen to get your feedback on how find the website.
June is upon us, and you can rest assured it will be another month full of useful content for you and your colleagues.
Till next time…
THE AUTHOR
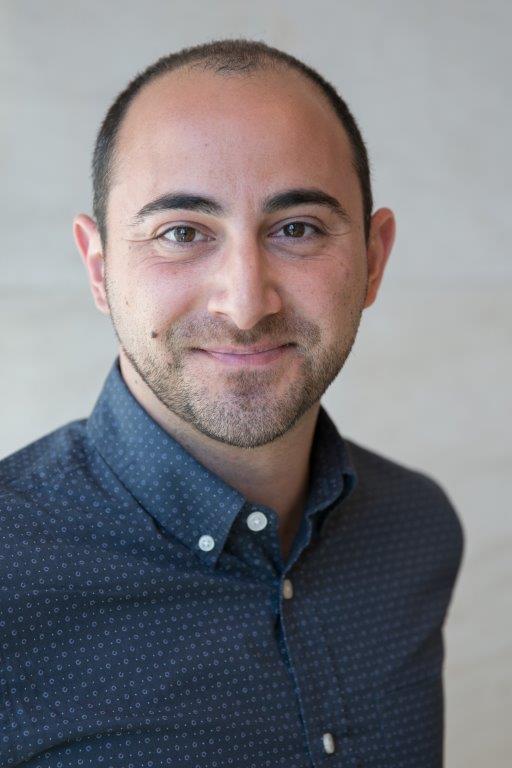
Roberto Priolo is a London-based journalist and Managing Editor of Planet Lean. Prior to joining the Lean Global Network and launching Planet Lean, Roberto was editor of Lean Management Journal and associate editor of The Manufacturer magazine. He holds a degree in Political Science from the Università Cattolica in Milan, Italy, and a postgraduate diploma in journalism from the London School of Journalism.
Read more
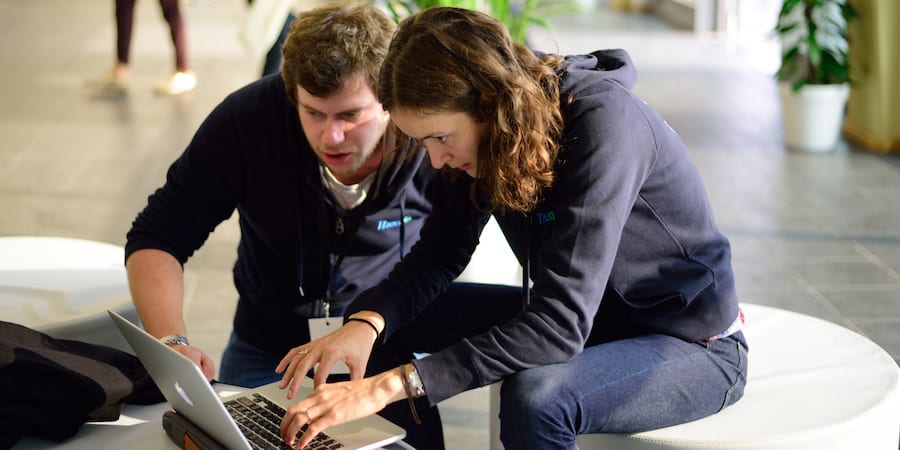
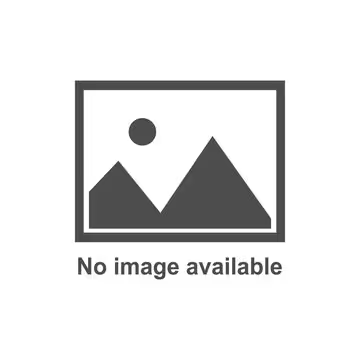
INTERVIEW – Software development company Theodo is a unique example of a digital company that has fully embraced lean and understood its potential. We caught up with their young CEO and CTO.
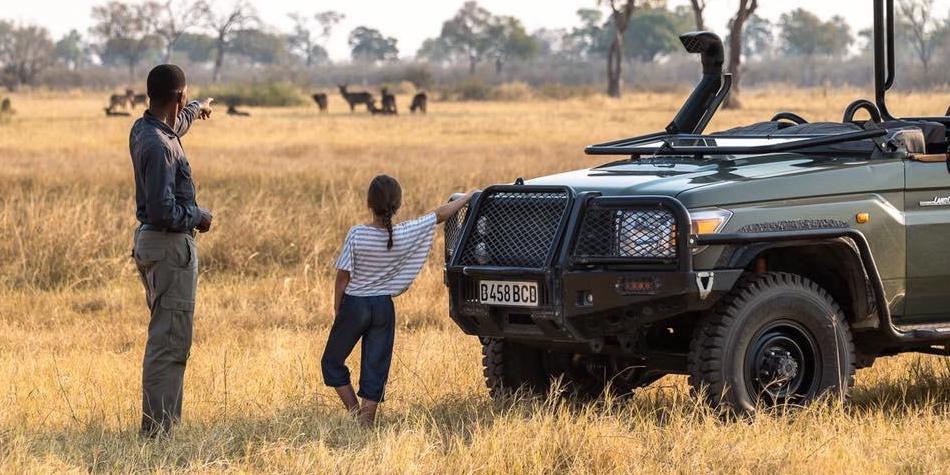
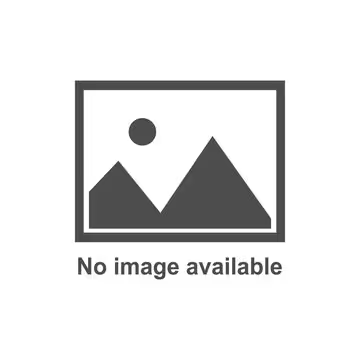
CASE STUDY – This company in Botswana has embraced lean thinking passionately to build the capacity and ability to deal with higher demand for its converted vehicles. The author tells us about their journey.
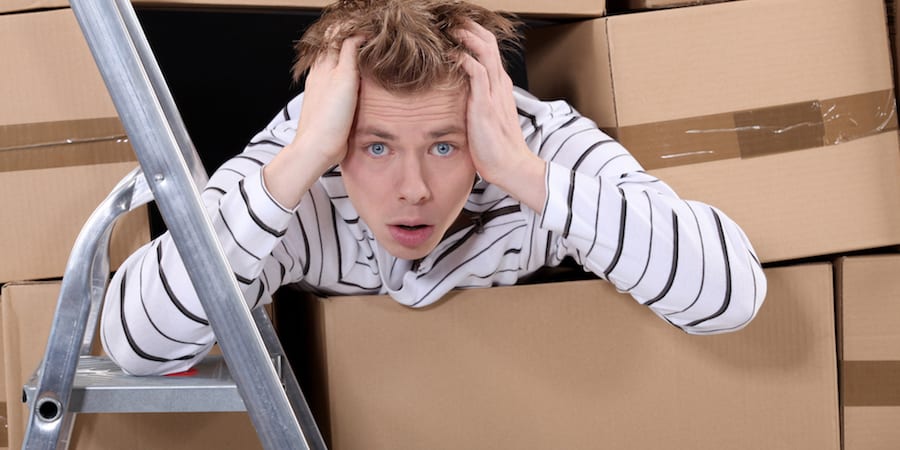
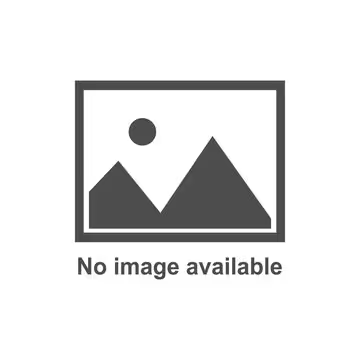
FEATURE – Inventory reduction is critical to waste elimination. Yet, many are reluctant to do it, fearing demand variability and production instability will neutralize their efforts. Grupo Sabó's story proves otherwise.
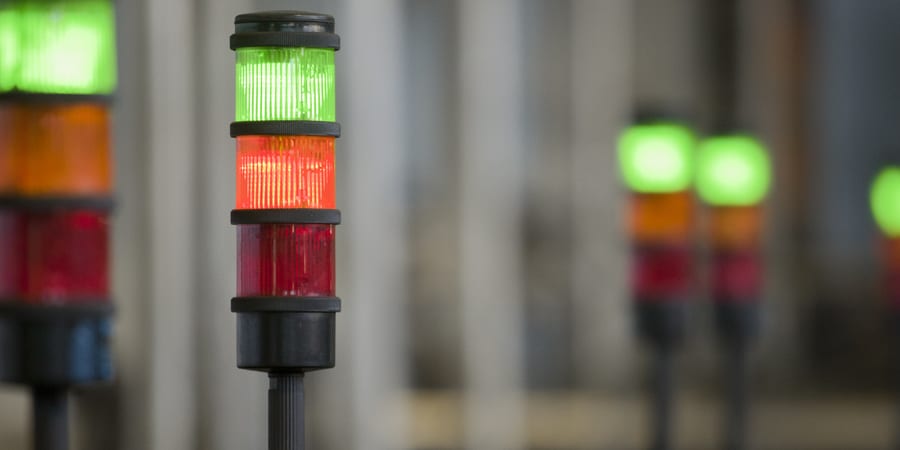
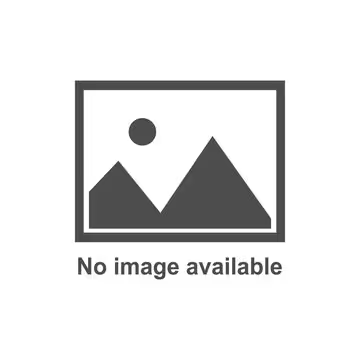
INTERVIEW – Catherine Chabiron sits down with Marc Onetto, a former executive with GE and Amazon, to discuss Jidoka and its profound effects on the way people work and think.