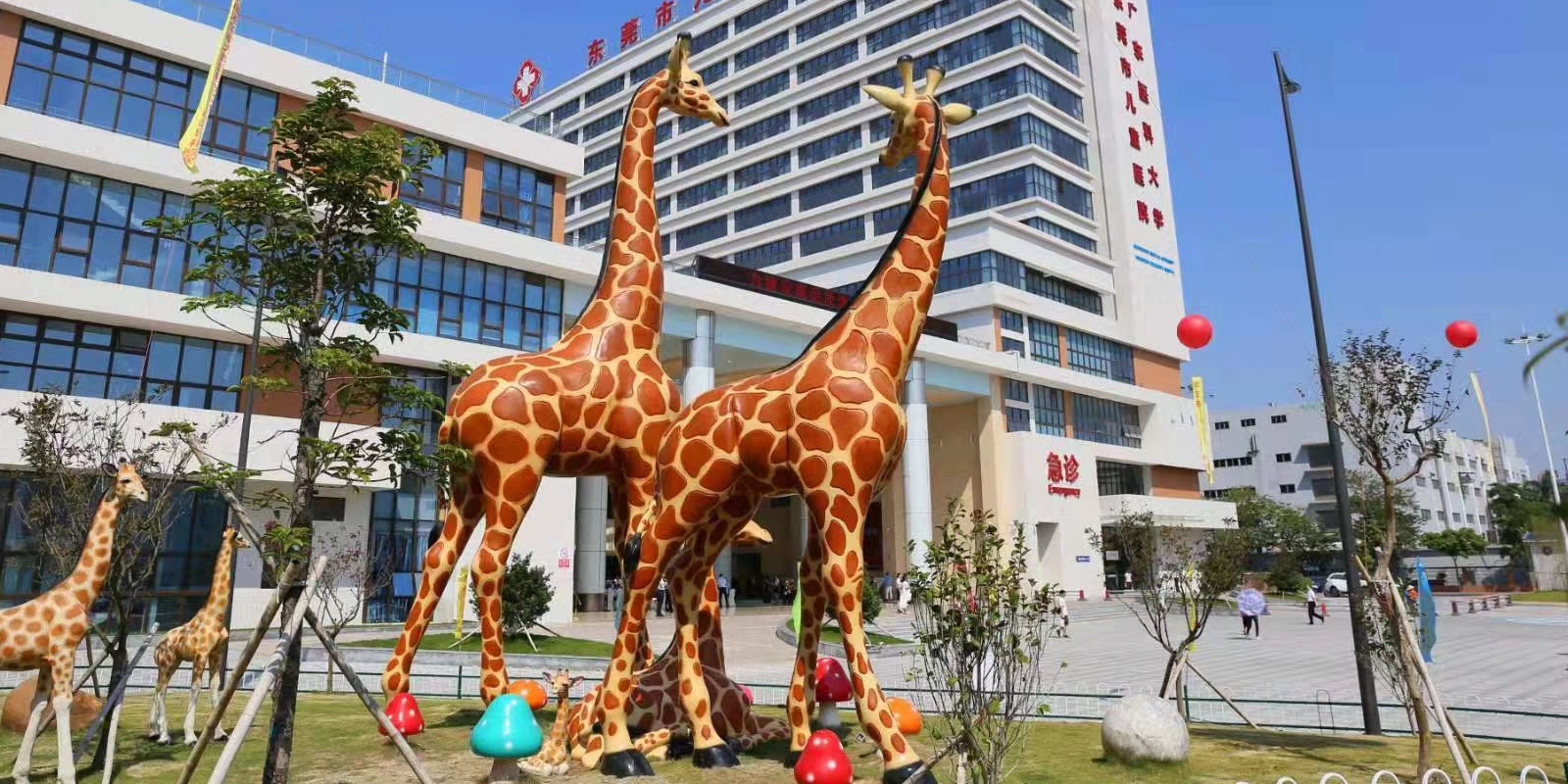
Improving children's care at a Chinese hospital
FEATURE - This story from a Chinese children's hospital reminds us that the lean healthcare improvements we make can have remarkable results on both patients and staff.
Words: William Luo, Lean Healthcare Director, Lean Enterprise China and Marcus Chao, President, Lean Enterprise China.
Giraffe Hospital is located in the city of Dongguan, in the coastal province of Guangdong, southern China. Its official name is Dong Guan 8th Hospital, but people like to call it Giraffe Hospital because of the towering statues of giraffes welcoming patients at the entrance of the main building.
This children’s community hospital opened in the 1970s. Due to rapid economic growth and the resulting increased in the demand for healthcare, it was turned into a large general hospital with over 1,000 beds. The giraffe statue is still there as a symbol of the hospital, to comfort children as they receive medical care. It is just one example of the hospital’s focus on patients.
This is a story of Lean Thinking applied to a healthcare setting to reduce the distance that ICU nurses and assistants need to walk every day, so that they can spend more time (and energy) providing value-added care.
It is rather common for ICU nurses and healthcare providers around the world to cover huge distances every day to care for their patients, pick up drugs, necessary equipment and materials, attend meetings or request medical consultations. In fact, all this unnecessary walking and time wasted can represent up to 25% of a typical eight-hour working day. Of course, this is an obstacle to the provision of proper care, not to mention the fact that these are not the kind of value-added activities nurses are trained to perform.
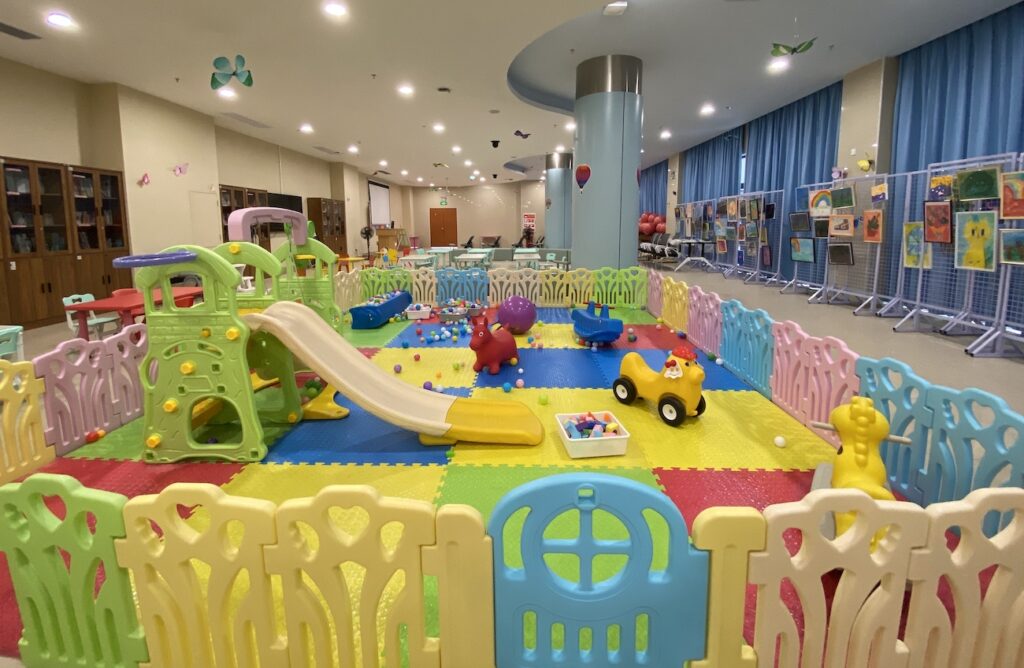
The Giraffe Hospital’s ICU Head Nurse, Ms. Song, took a lean healthcare green belt training course and decided to analyze in depth the daily work of ICU nurses to free them of the burden of non-value-added work. She shared the idea with her team and, as a target condition, she proposed a 50% reduction in the distance nurses need to cover. The project would last six months. This suggestion received overwhelming support from the nursing group, who immediately took action and formed kaizen teams to track daily walking routes for a selected group of nurses and collected data on the distance and purpose of every walk on a daily basis.
With information available, the team engaged in a number of brainstorming sessions to compile a reason tree, prioritizing the issues they had identified during their observation. Based on the Pareto 80/20 principle, the kaizen teams were able to highlight four main issues:
- ICU material was stored in a central location that forced nurses to walk back and forth to pick up the items they needed;
- The inventory in the storage room was poorly categorized. This, coupled with the uncertainty on the availability of goods, caused nurses and assistants to waste many trips and spend a long time searching;
- Some functional roles and responsibilities were not clearly defined;
- Certain daily routine tasks took away hours of the nurses’ time every day – for example, meal ordering.
The team then developed action plans to address each of the concerns:
- They came up with a storage cart design that was equipped with frequently used materials, to save time and energy for nurses and assistants and spare them the need to walk back and forth. To ensure goods availability, they also established procedures to define who would need to replace what materials were being consumed and when. A similar application was applied to the medicine cart as well. The kaizen team invited other nurses and assistants, the every-day users, to jointly design different carts for IV injection, patient bathing, and general nursing purposes with suppliers to make them more efficient.
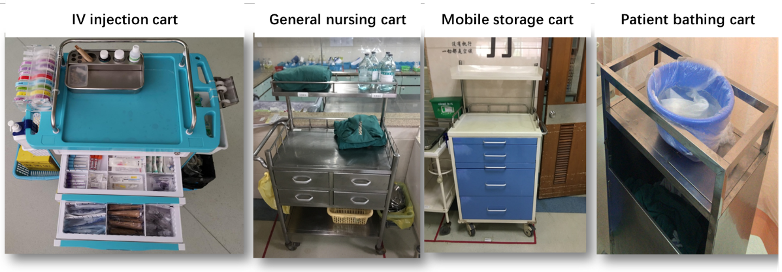
- They improved the layout of the ICU storage room and organized materials by frequency of usage. They designed a process for picking the right quantity of items and held quarterly reviews to assess the need to adjust. Another improvement entailed removing storage closet doors to make inventories visible to all users, in turn making every person responsible for reporting items that were found to be below safety inventory level. This practice boosted the ICU staff’s sense of ownership and responsibility in keeping necessary supply available.
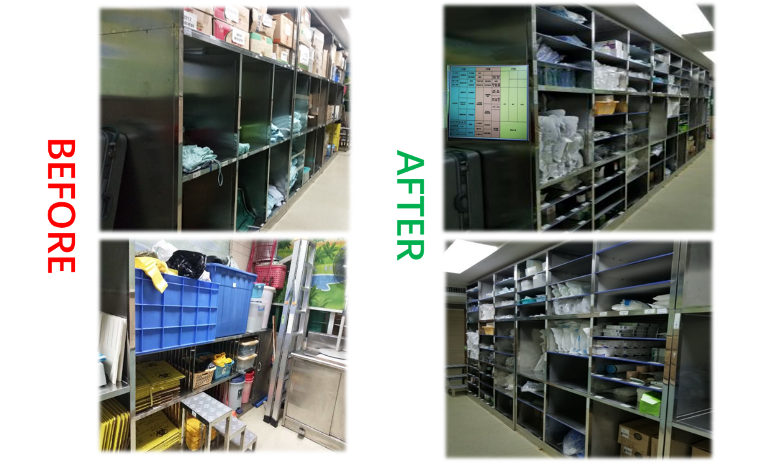
- IV preparation distribution on one hand and injection on the other were traditionally carried out by two different groups of nurses (who periodically rotate between the two tasks), but roles and responsibilities were not clearly defined. This occasionally caused customer complaints. The team discussed the issue and agreed to assign to the therapeutic group the responsibility of preparing IVs and distributing them to patients and to the nursing group that of injecting and replacing IVs. With the defined roles and responsibilities, the two groups began to collaborate more effectively and to support each other to provide seamless care to patients.
- The Kaizen team learned to apply the rule of proximity and placed all necessary equipment and materials within a short distance from the beds. They also requested the IT department to upgrade the meal ordering system to save time and energy for daily routine work.
The ICU team reviewed the project at the end of the six months and were extremely proud of the results they achieved. These included:
- The amount of walking for ICU nurses was reduced from 20,000 steps to less than 7,000 a day on average – timewise, this meant going from 126 to 36 minutes;
- The optimization of the storage room saved six cubic feet of space and resulted in a 40% reduction of ICU inventory from CNY 80K to 48K;
- Turning waste into value-added work led to an increase in the frequency of ICU patient bed service and therapy;
- ICU patient hospital days were reduced on average from 7.1 to 5.8 days and patient satisfaction reached 100%.
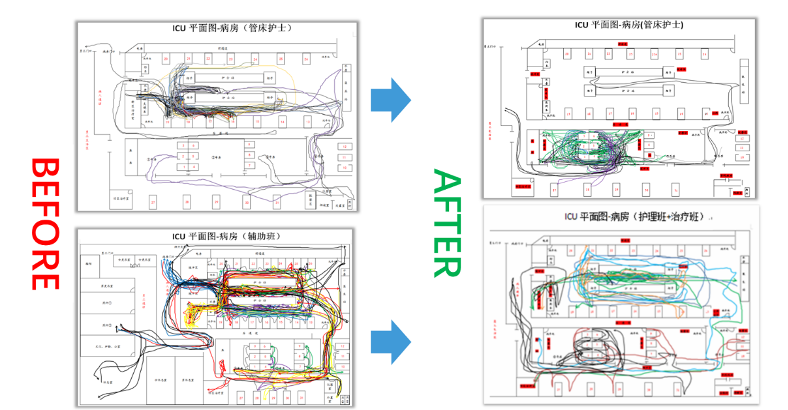
There was an added benefit of this kaizen project: with the support of the hospital’s management team, the ICU team turned an 8-square-meter storage space into a private room for patients close to the end of their lives, so they can enjoy quality time with their families. What a way to show love and care for patients!
In addition to the ICU project, the Giraffe Hospital completed another 19 kaizen projects. These included: increasing the on-time rate of the first operation of the day from 65% to 95% in just four months; reducing bed turnover time in the ORs by 40% to 50 mins and OR nurses’ overtime by 50%; increasing the OR utilization rate by 25%, from three to four operations per room per day.
On top of these improvements, the hospital management took a major step towards relieving the suffering of patients and families by relocating the Pediatric Department from 2nd floor to ground floor. The new space provides an open and pleasant surrounding full of fresh air and sunlight, and also features game facilities that help distract the children from their treatment and alleviate their fear. More importantly, the outside space reduces waiting room crowd by 30%, which minimizes the risk of spreading contagious disease.
All of these lean improvements, which were possible thanks to the staff’s commitment and effort to build on what they had learned on the training program and to the management team’s support and engagement, are meant to provide a better-quality care and service to patients and make the job of healthcare workers easier – the only way to ensure success for the hospital.
THE AUTHORS
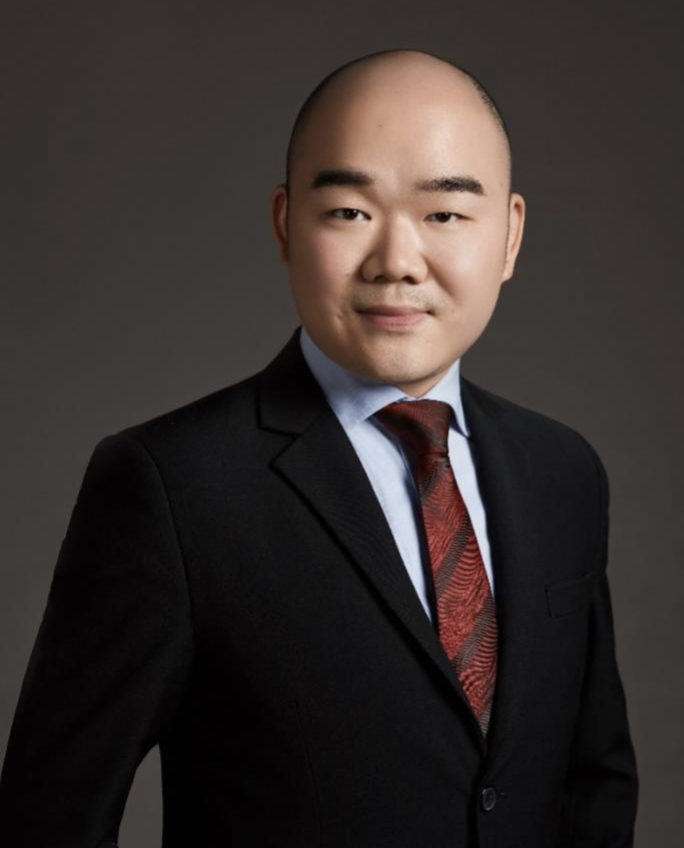
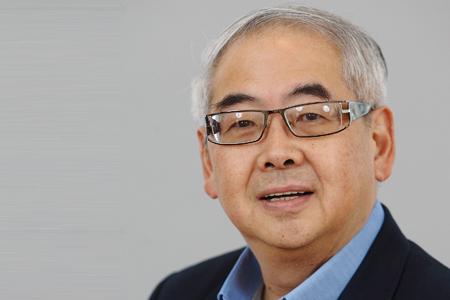
Read more

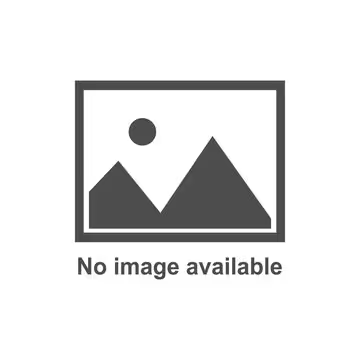
FEATURE – We tend to take the “goodness” of lean for granted, but – the author says – we should stop and think about what makes lean a good business practice. Why is it a way of thinking all businesses should adopt?
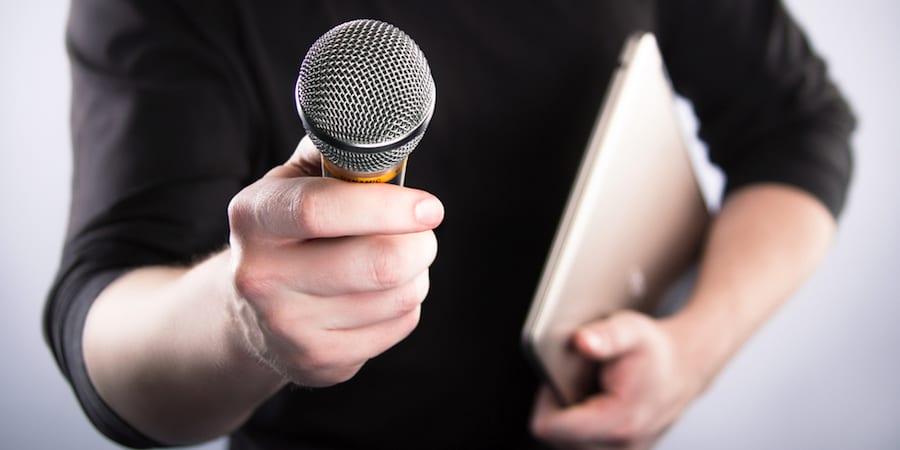
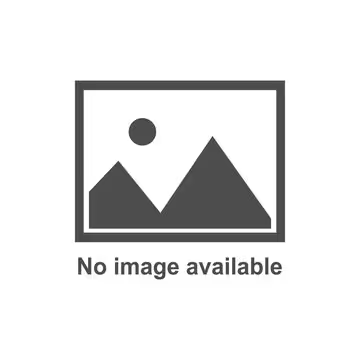
INTERVIEW – The British Broadcasting Company (BBC) has been working with a lean-inspired improvement program that is gradually transforming the culture of the business – one creative idea at a time.
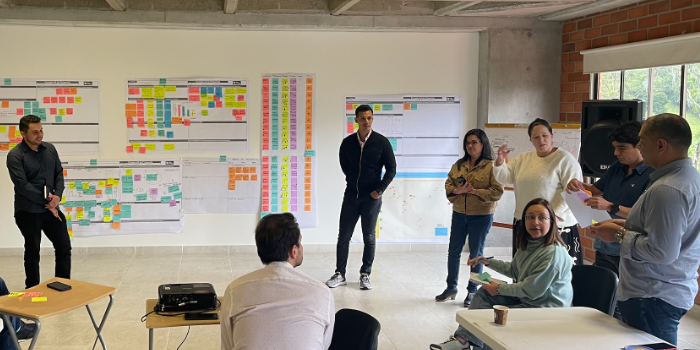
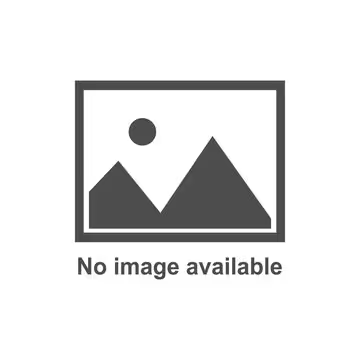
CASE STUDY – Following a positive experience in manufacturing, this Colombian company brought lean to the rest of the organization. Its goal? To become a reliable partner for its clients in the national and international markets.
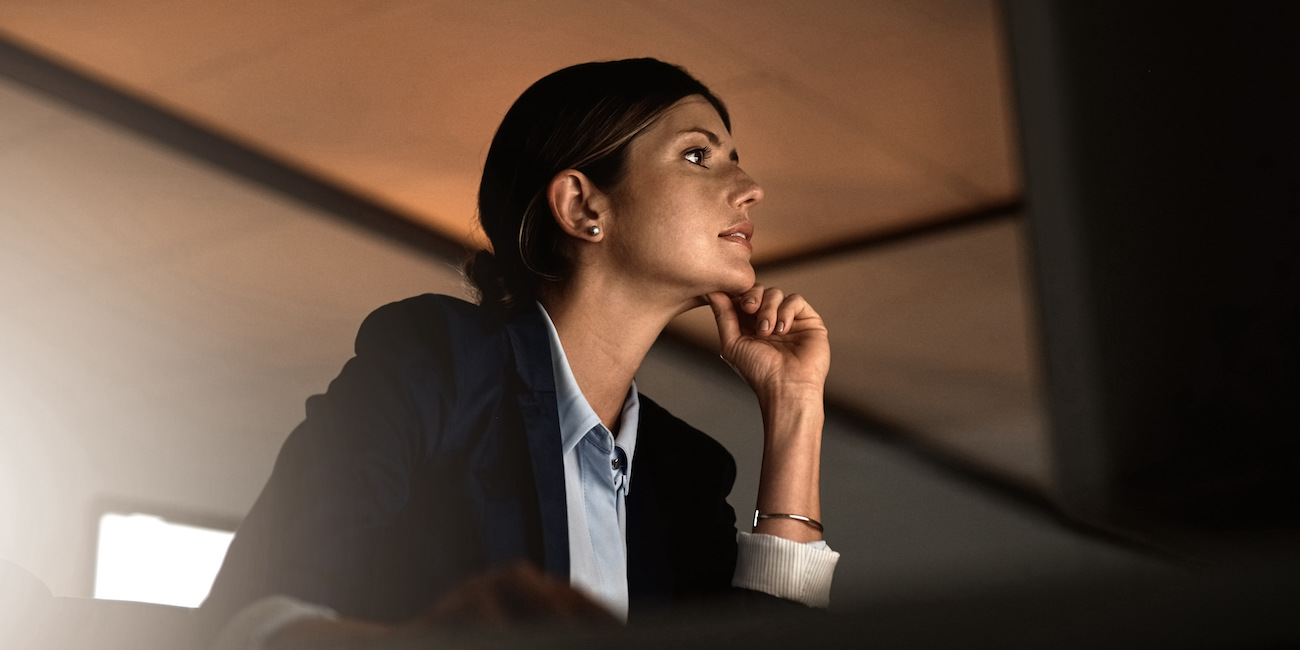
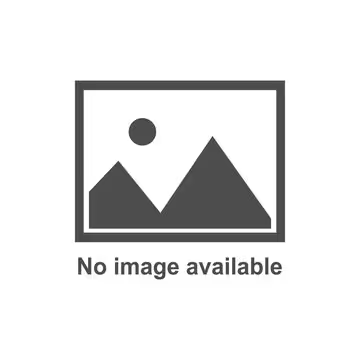
FEATURE - The Basic Thinking dimension of the Lean Transformation Framework is often the most neglected and the least understood. The author tries to shed a light on the subject.