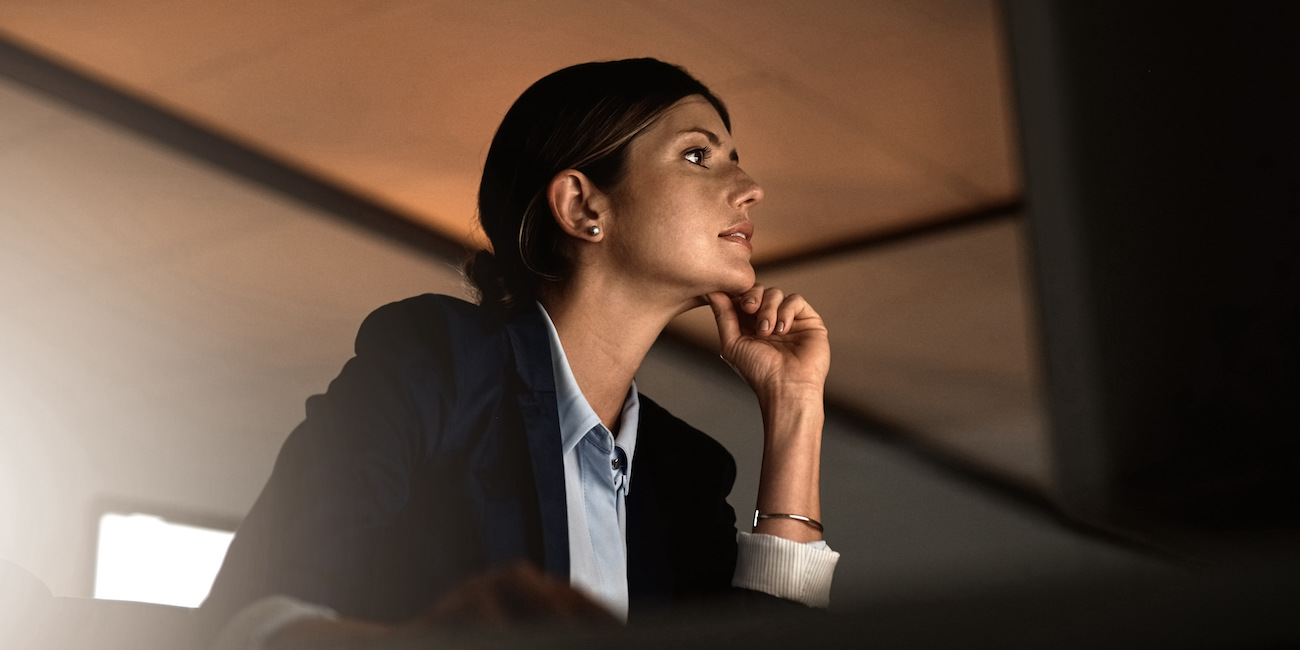
Models for thinking about Lean Thinking
FEATURE - The Basic Thinking dimension of the Lean Transformation Framework is often the most neglected and the least understood. The author tries to shed a light on the subject.
Words: Tshepo Thobejane
The phrase “All models are wrong” is a common statistical aphorism that George E. P. Box turned into the popular saying, “All models are wrong, but some are useful.” This aphorism acknowledges that models, whether conceptual or statistical, always fall short of fully capturing the complexity of reality, but can still be useful. Perhaps it was because of this that Taiichi Ohno, one of the key figures behind the development of the Toyota Production System (TPS), initially had reservations about documenting the system. It is said that he believed documenting every detail of TPS would limit its flexibility and hinder continuous improvement. Nonetheless, the business world will be forever grateful that the TPS model was captured, allowing many organizations to learn from it and use it to develop their own systems.
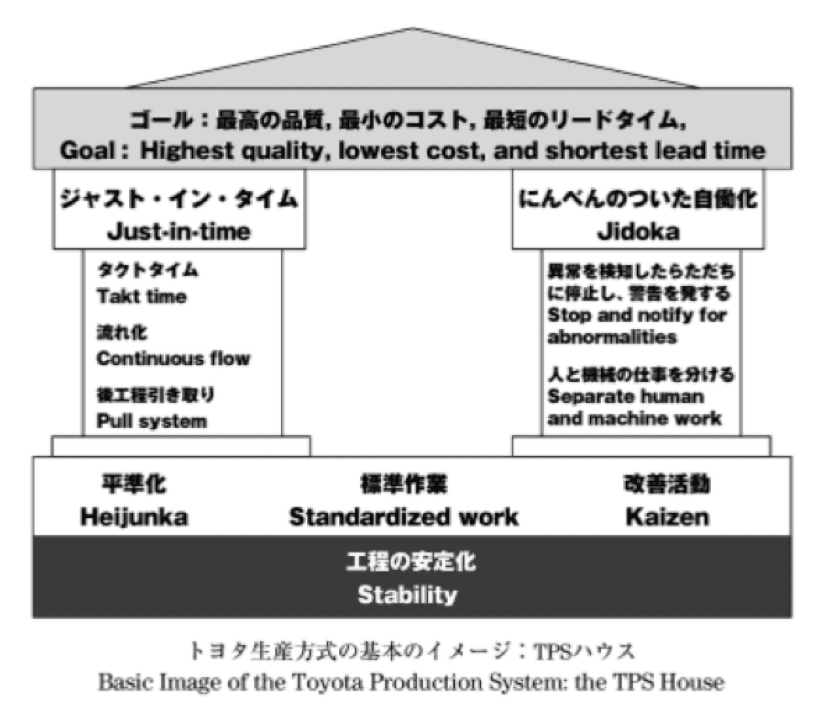
Toyota formulated this TPS House model at a time when it was trying to spread TPS thinking both within the company and to its suppliers by showing their top management how to fit into their extended just-in-time supply chain. The success rate of companies implementing TPS or Lean Thinking can vary widely depending on various factors, such as the commitment of leadership, the cultural readiness of the organization, the degree of employee involvement, and the specific implementation strategies employed. It's challenging to provide an exact percentage for the success rate of companies, but based on industry studies and experiences, here's a rough estimation:

The companies with high success experience significant improvements in productivity, quality, cost reduction, and customer satisfaction. They sustain the benefits over the long term, and often become industry leaders in operational excellence. They embed Lean Thinking into their organizational culture, processes, and management systems. They continuously strive for improvement and adapt their practices to evolving challenges. Moderate-success companies may not reach the same level as high-success companies, but they still derive tangible benefits from TPS or Lean Thinking.
Looking at the TPS House, we can see that it primarily shows the tools and practices to achieve operational excellence. However, simply copying TPS practices without understanding the underlying philosophy is the primary reason for failures and suboptimal results. This led the Lean Enterprise Institute to develop a model to guide and introduce changes in organizations that seek to undertake the lean transform journey. In addition, this model can be used to systematically resolve problems at every level of an organization, from executive-level strategy to front-line operations.
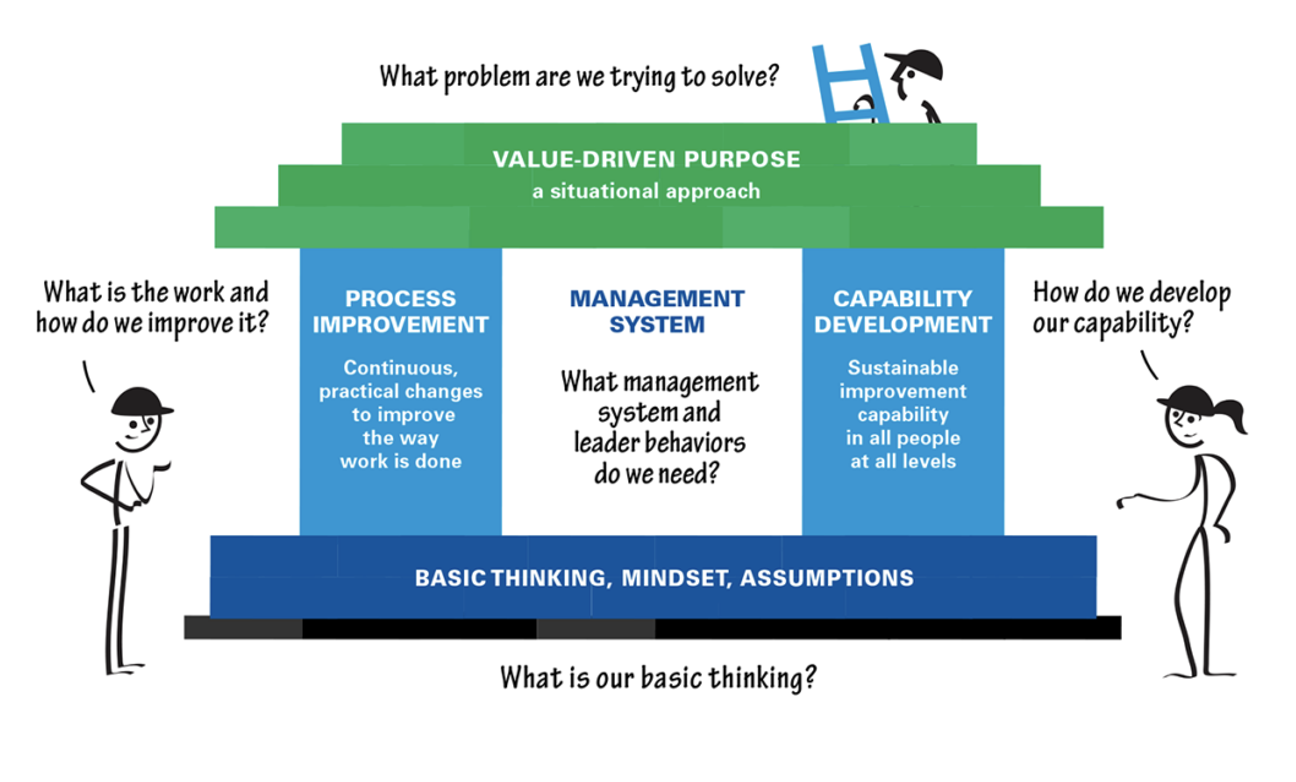
Another important aspect of this model is the recognition that every organization’s transformation journey will be situational and should start by understanding the problem(s) that the organization is trying to solve. Therefore, rather than focusing on providing answers and deploying tools, the model focuses on posing questions based on principles. The key questions or dimensions of this model are:
- What is the value-driven purpose? Or what is the problem to solve?
- What is the work to be done (to solve the problem)?
- What capabilities are required (to do the work to solve the problem)?
- What management system – operating system and leadership behaviours – is required?
- What basic thinking, including mindsets and assumptions, are required by the organization as a purpose-driven socio-technical system?
Based on common observations and discussions within the lean community, the dimension that often receives less attention compared to the others is Basic Thinking and Mindsets. The objective of this article is to add some perspective and input on this dimension. Looking at its position as a foundation on which the transformation house is built upon should highlight its importance. For this reflection, we will need another model that comes from Systems Thinking, called The Iceberg Model (Four Levels of Thinking).
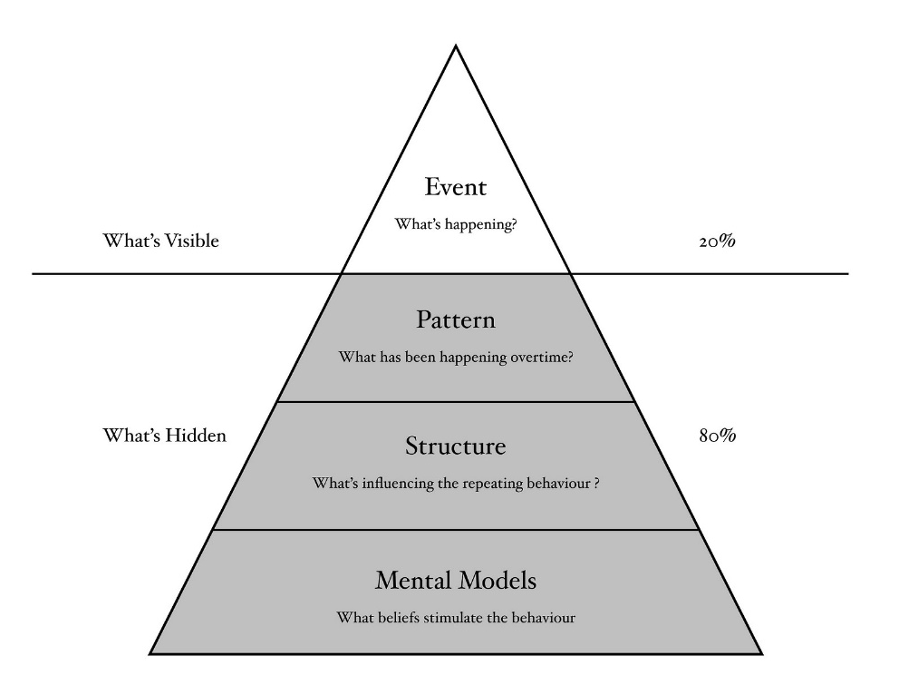
The Four Levels of Thinking model shows the depth of thinking we apply to events and helps us understand how various aspects (events, patterns, systemic structures, and mental models) influence our perception and problem solving. It’s called the “iceberg” because most of the complexity of a visible event lies beneath the surface.
In organizations without Lean Thinking, most managers will most likely prefer to address issues at the events level because they are visible. However, the level of events thinking is the shallowest and actions based on events thinking are reactive and can only temporarily address symptoms. The absence of deep thinking in an organization suggests that if an employee makes a mistake, the first response will be to blame them. The recurrence of such events implies that there is likely to be minimal trust between management and employees. If trust is weak, things like investing in people development will not happen, which reinforces reliance on top-down approaches... which further reinforces the mental models of no trust.
A lean organization recognizes the need to develop deep levels of thinking in its people. Both management and staff are trained and equipped to perform root-cause analysis and to identify the structures responsible for the undesirable cause-and-effect. In addition, building trust and investment in people development are ingrained in the mindset of a lean organization. Therefore, the key considerations for the Basic Thinking dimension of the Lean Transformation Framework is to reflect on our recognition of the importance to develop systemic and scientific thinking in people and to build trust between employees and management. Without this mindset, it will be difficult to hold up the other elements of the Lean Transformation Framework.
If you have used the LTF, we would like to hear from you. How has it helped you and what are some of the challenges you are facing in your transformation journey? How have you approached and worked with the Basic Thinking dimension? By the way, is it a coincidence that the proposed Basic Thinking considerations align with the pillars of the Toyota Way (a set of principles defining the organizational culture of Toyota Motor Corporation, formalized in 2001 after decades of academic research into the Toyota Production System)?
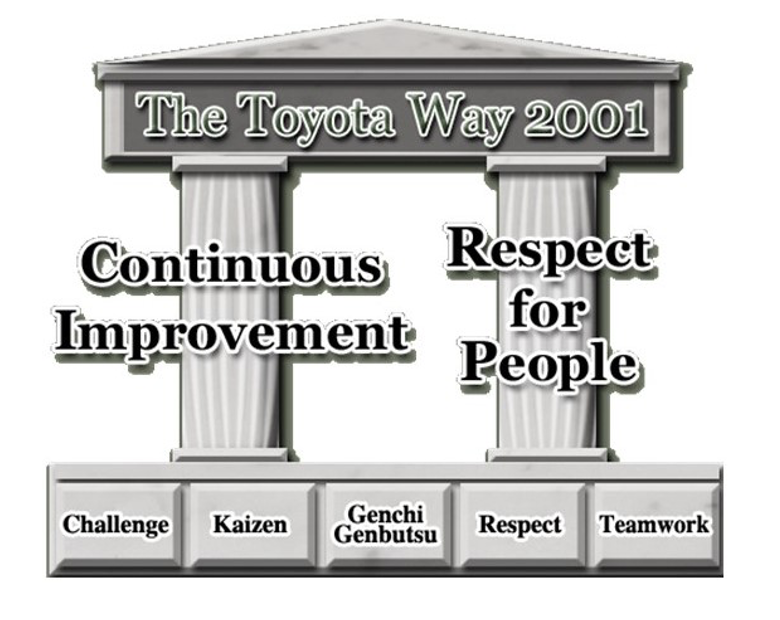
THE AUTHOR
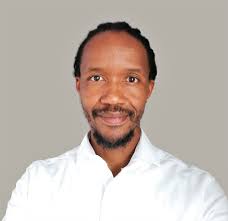
Read more
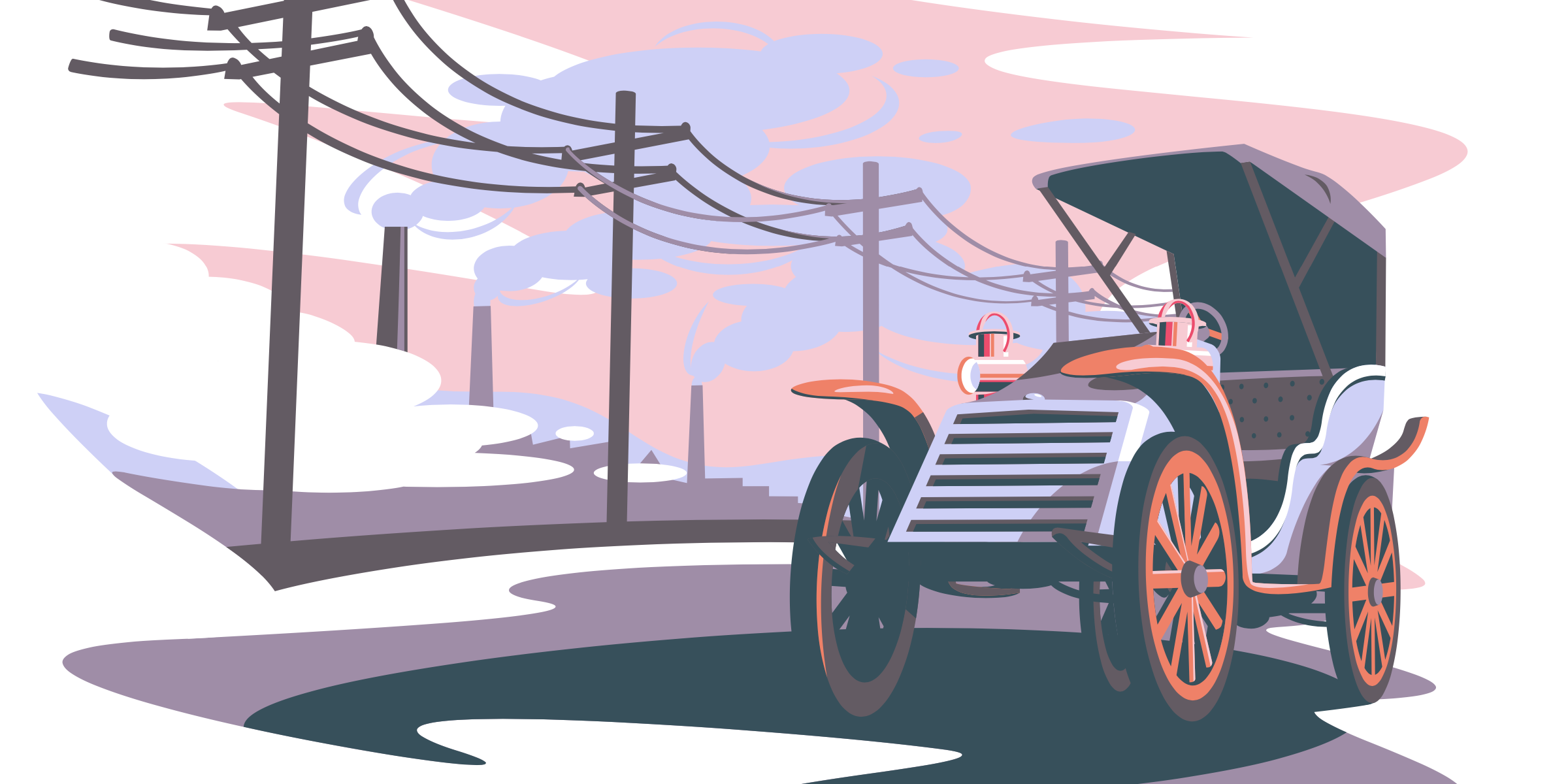
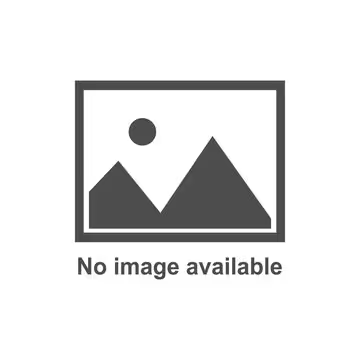
FEATURE – Every lean generation has faced challenges, and it’s critical we understand the context around us if we are to continue to grow our Community, says Jim Womack.
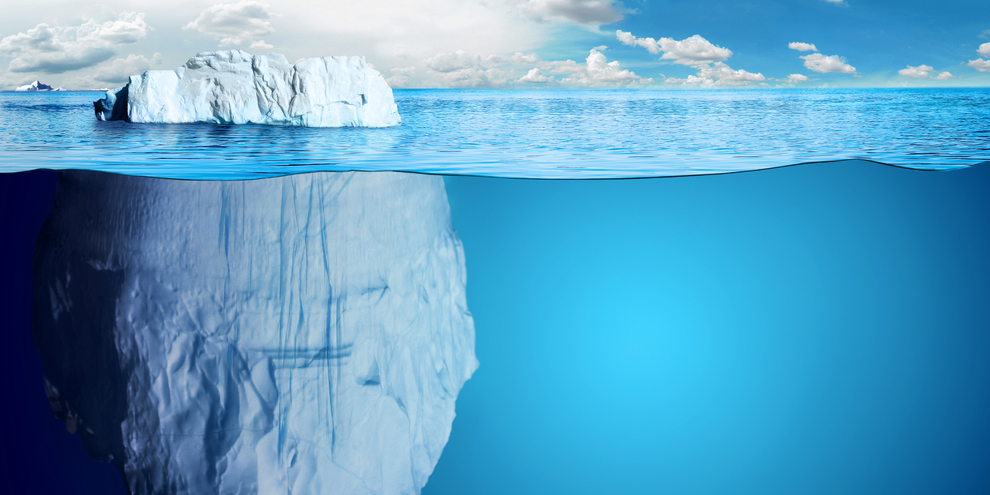
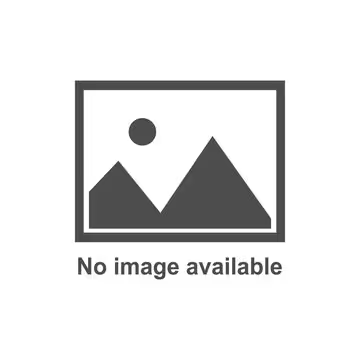
FEATURE – A real understanding of Lean Thinking can only stem from an exploration of its tacit aspects, not just its most explicit, easy-to-grasp elements.
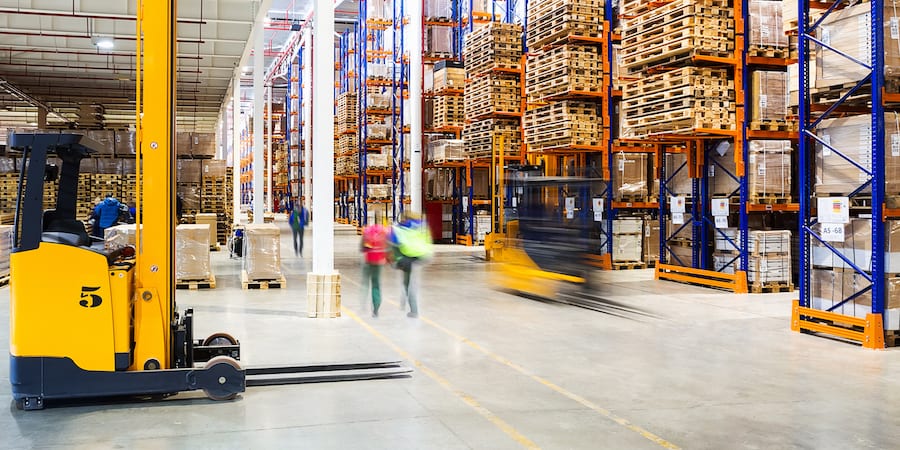
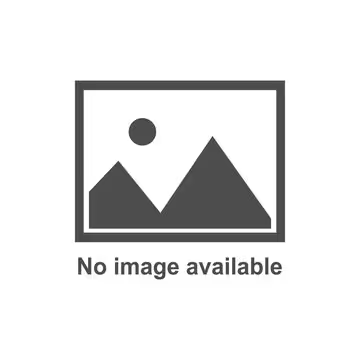
COLUMN – Want to grasp the current situation? Then you must go to the gemba, but it would be a mistake to think that alone is enough to change your business… you also have to ask why and show respect.
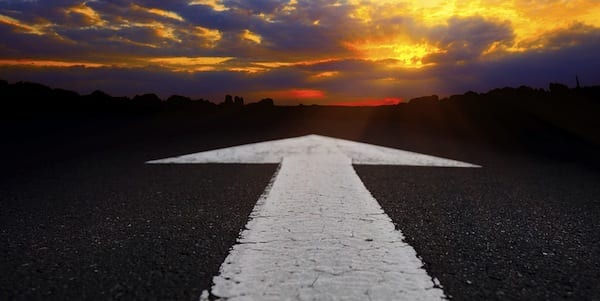
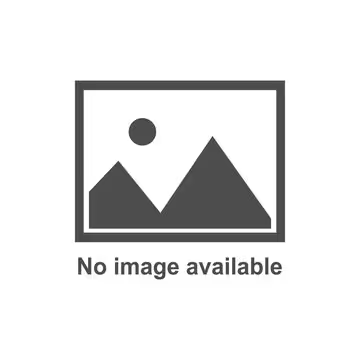
FEATURE - The author looks back at his many years with Toyota and shares some of the key lessons he learned along the way. What a unique company!