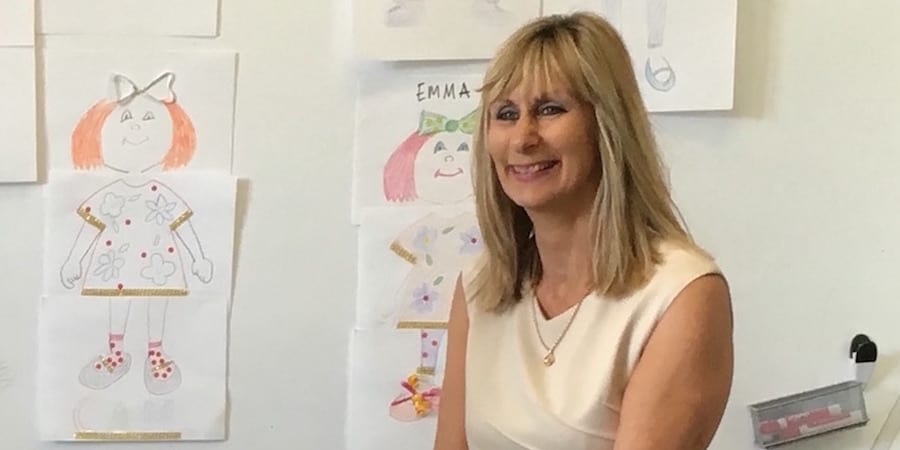
Bringing lean principles to Australian cities and healthcare
PROFILE – This month we meet another member of the lean community, a true pioneer of lean thinking, who contributed to introducing the methodology in Australian cities and healthcare organizations.
Profile on: Denise Bennett, Senior Improvement Coach, Stanford Children's Health
Words: Roberto Priolo, Editor, Planet Lean
I first met Denise Bennett in September 2013 in Beaune, France, at the annual meeting of the Lean Global Network. I had just been hired to develop and launch a publication for LGN – you guessed it, it’s Planet Lean – and I was there to meet the team, while Denise was representing Lean Enterprise Australia.
I had the chance to work in her same working group for the whole week, and I was immediately struck by her ability to get us all thinking and to trigger productive conversations. She was also very fun to be around.
Back then, I didn’t know much about Denise’s background – other than the fact that she had been working for the City of Melbourne for a few years and that they were doing truly great things there – but her enthusiasm immediately made me curious to learn more about this lean practitioner from Australia.
A few months later, after we launched Planet Lean, Denise authored a great article on the City of Melbourne, which gave me a better understanding of her experience. However, it wasn’t until very recently – in fact, just a few weeks ago – that I finally had to opportunity to really learn about her evolution as a lean thinker, when I visited her in Stanford, California, where she is currently coaching the team at Stanford Children’s Health.
Denise commenced her career as a nurse in Tasmania, Australia. She was a midwife for several years, before moving on to a part-time job in nephrology nursing after her first son was born. “Back then,” she told me in her office at Stanford, “I thought that nursing was the ideal career to support my preferred job: raising children. My mother was my role model and I wanted to follow in her footsteps. But life doesn’t always turn out as expected, and opportunities came along that had my career take a series of turns and twists that I could never have imagined or planned.”
Denise spent 12 years in nephrology, leading programs both in the public and private sector. Her interest in quality improvement first emerged during her time as Nurse Manager for the Southern Tasmanian Nephrology service.
In 1998, Denise took on the role of chief nurse for a private dialysis company in Australia, with the responsibility for establishing and operating clinics across the country. Despite her commitment to improve the life of the dialysis patients she was working with, at first she struggled to strike a balance between quality and efficiency in this high-cost clinical setting. “I just couldn’t see the waste,” she said.
At that time, Denise was studying for an MBA, and what she learned on the program really seemed to complement her passion for improvement and completely changed her perspective as a leader. She said: “I tried to combine what I learned from Peter Senge’s 5th Discipline: The Art and Practice of the Learning Organization and Kotter’s eight-step change management model to support the work of my team. While those concepts really helped me to develop an understanding of a lot of the improvement concepts and to embrace parts of the mindset, I was still lacking the tools and techniques.”
Denise found herself struggling with the mindset of the company, which was too focused on increasing margins and seemed to neglect what patients really valued. It was time for her to move on.
She soon took on a Project Manager role for a national research collaborative across twenty health services. That’s when Denise met Michael Szwarcbord, the CEO of Flinders Medical Centre. Within months, he asked her to join a new team who would focus on redesigning care and improving patient flow at the 600-bed hospital.
Szwarcbord considered Denise’s skills (a combination of leadership, research, change management and project management, together with her clinical background) as a perfect match for the role.
FROM AND TO HEALTHCARE
Recalling her time at Flinders, Denise told me: “When we started redesigning patient journeys at Flinders, we took a learning-by-doing approach. At one point, a colleague from the UK came to visit and handed us a book under the table, whispering ‘Don’t tell anyone, but we are using this manufacturing approach called lean.’”
The book was Jim Womack and Dan Jones’ Lean Thinking and the team from Flinders set about following the five principles. No one else in the Australian healthcare sector was using lean, so the team – which included the CEO – attended a manufacturing-based course and worked hard to translate the principles to a healthcare setting, to improve patient safety and flow.
They learned about value and started to do some mapping. They then took out some waste and implemented a pull process. Denise said: “Wherever we had push, we started to pull. We segmented our patient flows into short and long. The results were simply spectacular.”
Flinders Medical Centre became internationally renowned as a pioneering healthcare organization, which led Denise to meet Professor Daniel T Jones and John Shook at a conference in Amsterdam. She said: “Part of why I am so passionate about this is that I have become part of this international lean family. Lean is hard work and having people to keep you motivated and on track, and have access to some of the world’s greatest mentors, is invaluable.”
As it often happens, CEOs tend to move on after a while and Michael Szwarcbord ended up leaving Flinders in 2007 He and Denise consulted together for four years, working in a lot of other healthcare systems in Australia and abroad. One of the projects she remembers most fondly was applying lean thinking principles to the design of a new facility in Queensland. Even though two-thirds into the project the leadership changed hands and plans changed with it, Denise found the experience enlightening. “It taught me a lot about how you can get patient flow right from the start, rather than spend time fixing patient and work flows later on. We found that more than 80% of the patients coming in would go home within 48 hours, so making sure they didn’t get too far into the hospital became a key focus,” she recalled.
Through her consulting work, Denise soon came across City of Melbourne (CoM). Soon afterwards, CEO Kathy Alexander (who also had a healthcare background) asked her to work internally for the organization.
The transition from healthcare to government was very interesting to Denise. “As difficult as healthcare is, you always have patients as a the main focus. Whenever it is difficult to know what to do or which improvement to support, focusing on the patient always makes things clear, for everybody. In some way, everybody’s job eventually aligns to the patient. What I immediately found at City of Melbourne is that we were constantly trying to understand what our product was and who our customers were. With over thirty very different businesses within the organization (from parks and recreation, street cleaning, arts and culture, city design, maternal child health and sustainability), it was often challenging to find the common thread that could pull us all in the same direction. I think that constantly asking ourselves these questions was the reason we were so successful,” Denise explained.
As it spread across the organization, lean gave City of Melbourne a common language where there was none. It also created alignment around Purpose, People and Process, putting people development at the core of their remit.
Speaking of her time at CoM, Denise said: “That was a very interesting six years. I had the privilege of working with a CEO who admitted that she didn’t know a lot about lean thinking or lean leadership but that she was willing to learn.”
Kathy saw the “fit” between the lean way of working and her fundamental belief in the right of people to participate in decisions which affect their work life and their home life. When reached for comment, Kathy said: “Denise taught me that respect actually meant asking questions and providing training and resources to help people identify and solve their own problems. It is actually very disrespectful to bring in outsiders to solve problems they know nothing about. It’s clear to me now that lean is about being respectful enough of staff and customers to be patient and give them the chance to win. It’s also about measuring outcomes. We had rate rises below CPI for all of the years of Denise’s guidance whilst adding six new services requiring at least 25 new staff and a population increasing at around 8-10% per year. At the same time we had increasing levels of staff and community satisfaction. Denise has certainly changed the way I think about leadership.”
Denise greatly enjoyed her time at CoM, but there is no doubt that healthcare is her turf. “There is no industry that deserves lean more than healthcare, and there is no place where lean could be more successful,” she commented.
Despite her life-long passion for improving healthcare, however, Denise had some hesitation about going back to the industry in Australia. She didn’t think twice, however, when the opportunity came along to hop across the Pacific and support the transformation of Lucile Packard Children’s Hospital in Stanford [we recently had an article on Planet Lean on the lean efforts at the hospital].
PATIENCE, THE VIRTUE OF THE LEAN PRACTITIONER
At this point in the conversation, I pointed out that Denise seems to have moved from one pioneering organization to another: to start with, Flinders, which was the first to bring lean healthcare down under; then City of Melbourne, which has done ground breaking work in the field of lean cities.
A few weeks later, when I asked Professor Dan Jones to share a thought about Denise’s contribution to lean thinking, he seemed to agree: “Denise is a real pioneer – first as an energetic member of the team at Flinders Medical Centre, and later on her own at the City of Melbourne. She never gives up and always approaches work with humour. I am so glad she is back in healthcare where there is still so much to be done.”
Now that she has made the move back to the healthcare world and, in doing so, moved to the opposite side of the planet, I asked Denise if she felt Stanford could be another place where she could take part in innovative lean work.
“This is a great learning opportunity,” she told me with a smile, “And to be able to work in a world-class children’s hospital is just extraordinary. I have learned so much already from my colleagues Drs Craig Albanese and Terry Platchek, who have led the deployment of a fine daily management system. This organization has courage and might just try some of the things others haven’t dared try: we have the opportunity to do some ground breaking flow work as we build on the foundation already laid through the management system. So yes, I feel like I have another chance to participate in something pioneering.” Stanford was supposed to be a six-month commitment, but plans have changed now that Denise has agreed to stick around to see what can be achieved.
When I asked Denise what the biggest challenge of working with lean is, she said that, more than anything, it is difficult to be patient. Senior leaders are constantly looking for the silver bullet that will bring the improvement they are seeking - fast. On the other hand, lean leaders know that there is no silver bullet and that it takes time and constancy of purpose to achieve results. It’s definitely the race of the tortoise and not the hare. Patience is a trait that Denise admits she had to learn and still frequently struggles with. As someone who rose through the ranks because of her ability to solve problems and fix things, she still finds it difficult at times to hold back and not tell people what to do.
Another challenge Denise described is leadership’s inability to stay focused on True North, bringing on new initiatives, projects and often external consultants, which tends to confuse and overload front-line leaders and staff. “One of the things I admired about Kathy Alexander at the City of Melbourne was her determination not to use external consultants to come in and solve problems for the organization. Instead, her focus was on unleashing the problem solving capabilities of the staff,” she commented. “We have so many smart people in our organizations, so why do we always think there is someone smarter out there who can do it better than us? This is a tremendous development opportunity wasted as far as I am concerned.”
People development is one of Denise’s greatest passions when it comes to lean, together with flow. It is no coincidence that, when I asked her what her biggest accomplishment as a lean practitioner is, she stops to think for a moment and eventually said: “On a personal level, the piece of work I look back to with the most satisfaction is what we did around people development at the City of Melbourne. We had people lining up to learn how to apply lean thinking to their work. Our whole approach to organizational development and leadership was focused on developing problem solvers and leaders as coaches. With the diversity of the businesses it was fascinating to see the results that individuals and teams achieved, whether that was reducing the time it took to get a parking permit or park rangers spending more time in city parks as a result of removing waste from their work. However, the most impactful work I have been involved in as a key team member is probably what we did at Flinders around nursing. We took the time the nurses spent with patients from 40% to 60%, which meant each patient benefited from an extra 25 minutes of nursing time every day. It’s the most significant because it changed the lives of so many.”
Before our meeting ended, Denise confessed another weakness of hers: “I am very impatient with people who don’t sign up, because I have done this long enough to know who is committed and who isn’t. You have got to have some fun with this, and the people you work with are a big part of that.”
At least for now, Denise seems to be enjoying her California adventure helping Lucile Packard with its lean transformation. “Sorry, I need to run… Our daily fluddle [a stand-up meeting for flow] is starting and I don’t want to be late for that. People are doing great and I want to show my support,” she said, before running off.
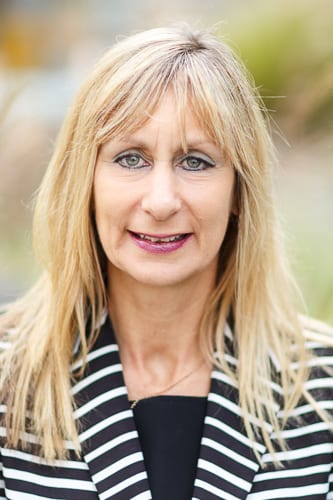
Read more
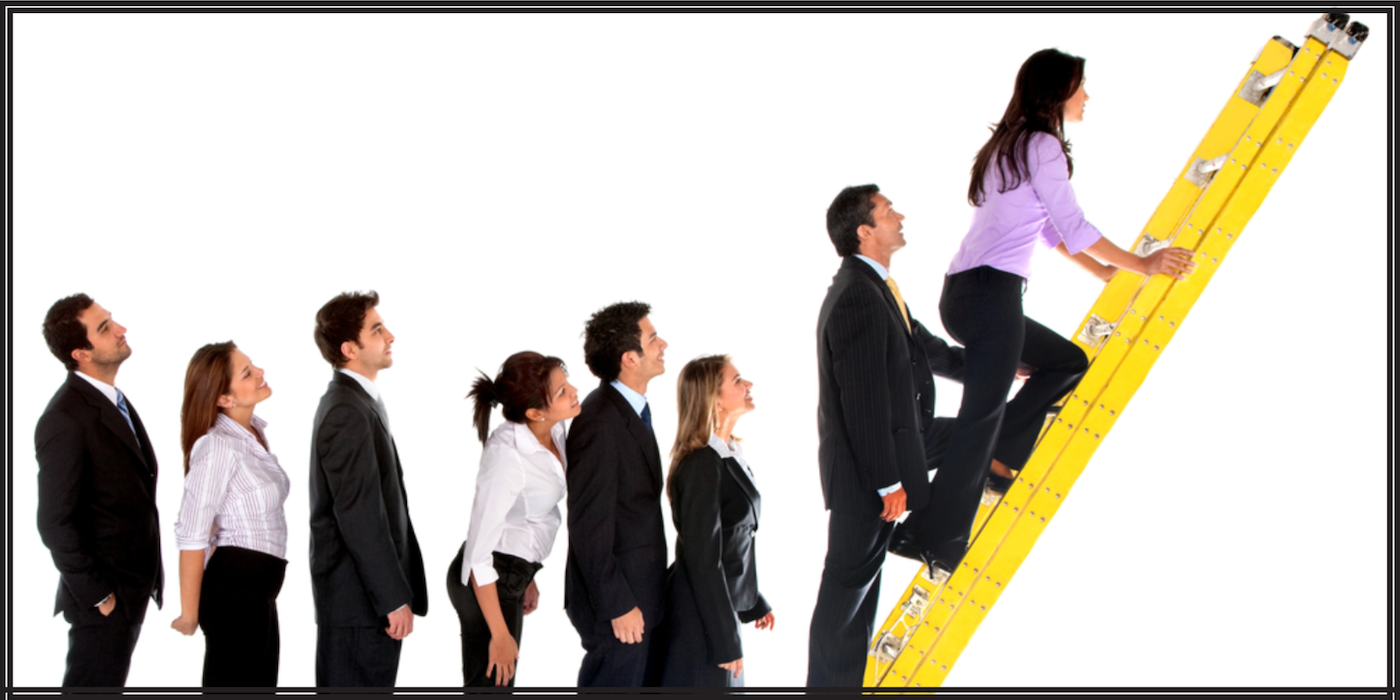
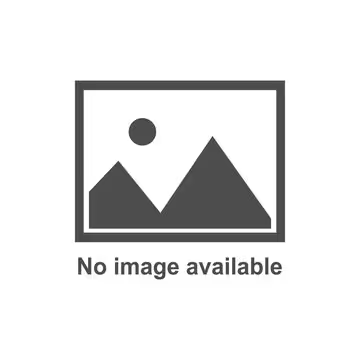
FEATURE – If you think one is born a leader, think again. Leadership can be learned and, in this article, the author provides a four-step guide to developing it.
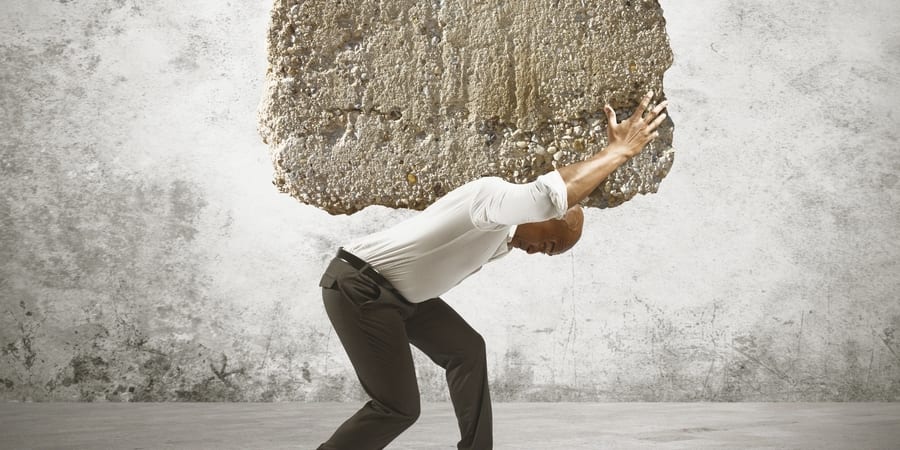
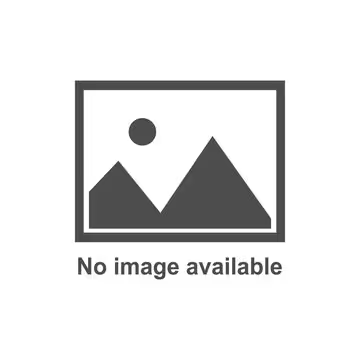
FEATURE - Stressed and overwhelmed by workload? Once again, lean thinking comes to the rescue, offering us a way to approach our work that helps us eliminate waste, save time, and avert breakdowns.
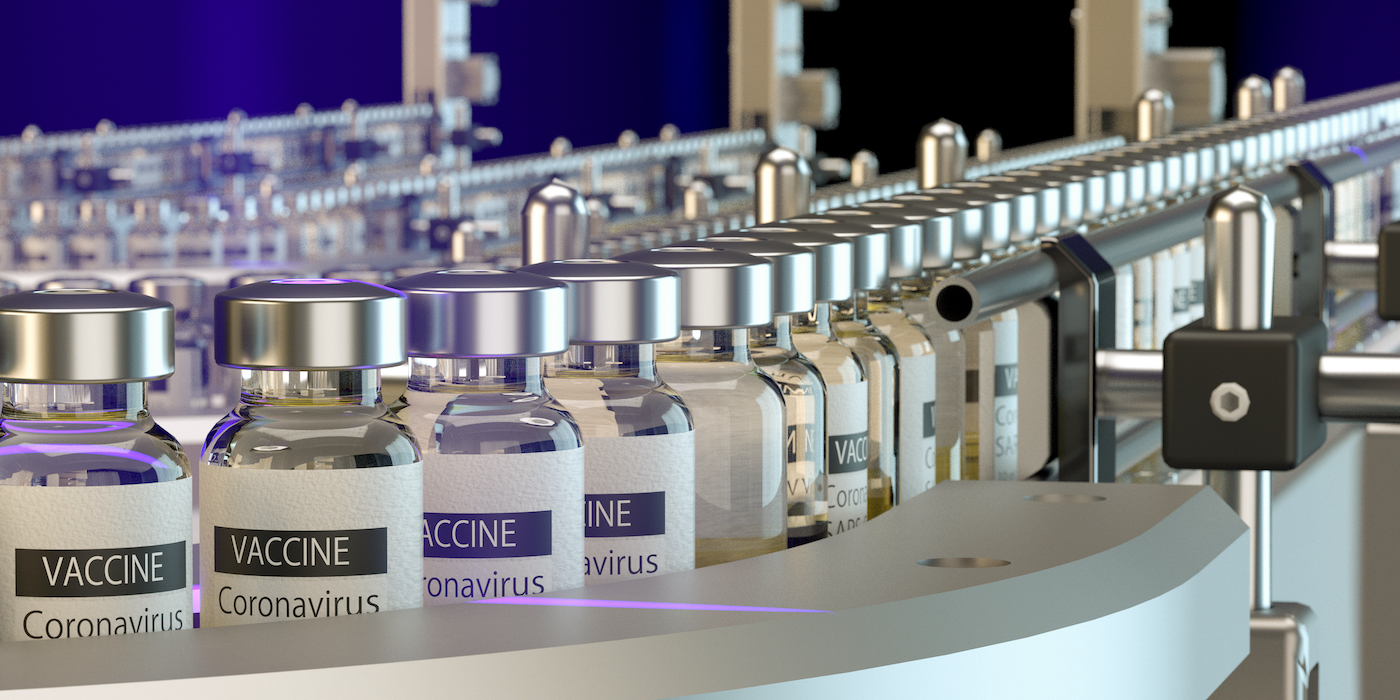
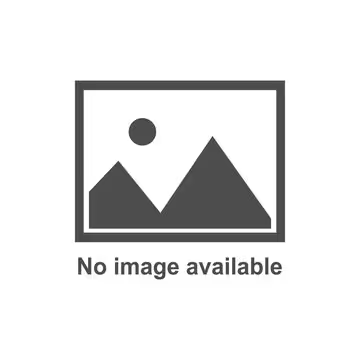
FEATURE – What does it take to meet the historic challenge of rapidly increasing the annual global vaccine capacity from 5 billion to 19 billion doses? And how could Lean Thinking help?
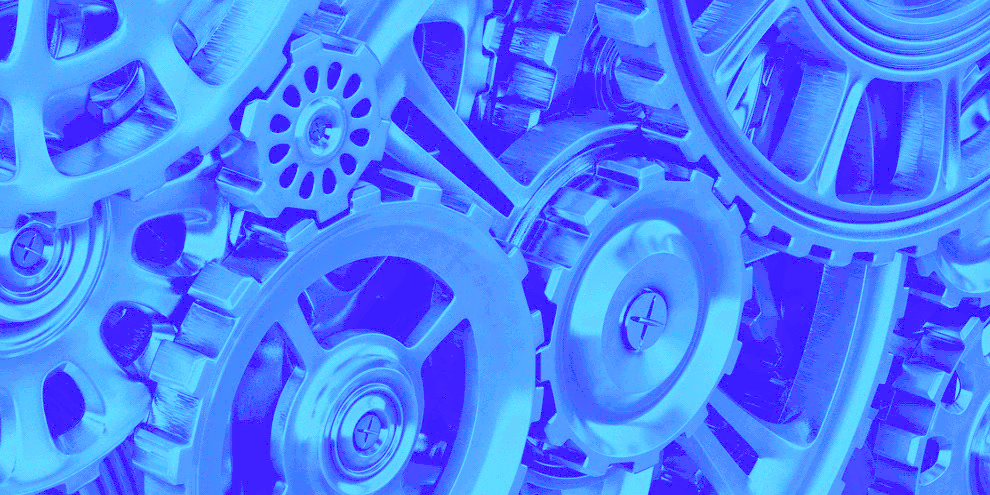
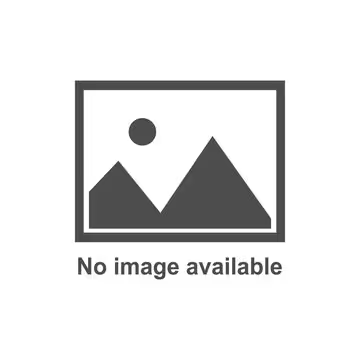
FEATURE – In the last article in his series, the author discusses how you can mix and combine the different pull systems available to the lean practitioner.