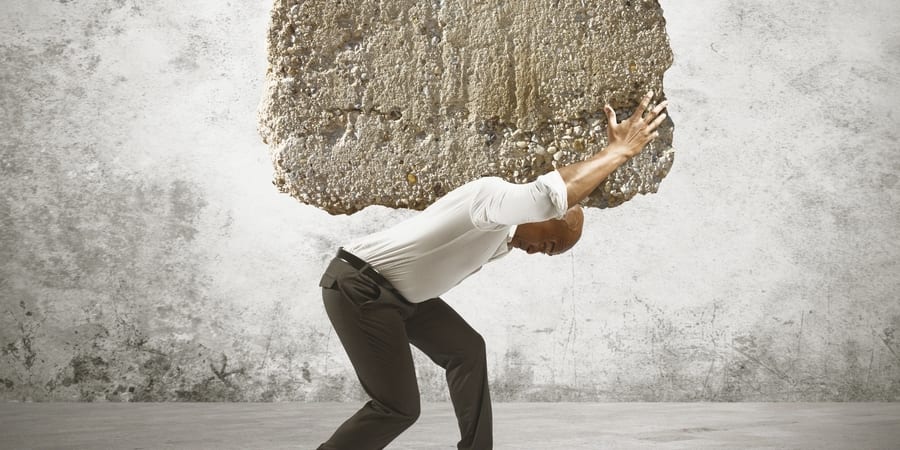
Our work has a process too, apply lean thinking to it
FEATURE - Stressed and overwhelmed by workload? Once again, lean thinking comes to the rescue, offering us a way to approach our work that helps us eliminate waste, save time, and avert breakdowns.
Words: Daniel Markovitz, consultant and author of A Factory of One
I wasn’t sleeping very well this past January.
I was six weeks into writing my new book, Building the Fit Organization, with two months till the manuscript was due. I’d wake up every night around 3am, my mind racing in a desperate attempt to keep track of all the moving parts: eight chapters, 10 long case studies, 12 smaller examples, charts, graphs, sidebars, appendices, etc. It was stressful, frustrating, and anxiety provoking. Even more stressful was the fact that when I’d sit down to write each day, I wasn’t entirely sure what I should be working on: not only did I have all the pieces of the book to write, but the chapters were all in different stages of completion. Should I work on the first draft of a chapter, or should I take on the final revision of a chapter and finish it?
This feeling of overwhelm was unusual for me. I work as an independent consultant, without the need to coordinate and cooperate with large numbers of coworkers. As a result, my life is much less complicated than that of the typical office worker. But here I was, reliving the stress of my former life working in a big company.
In my book A Factory of One, I argue that we can view ourselves as factories (small factories, but factories nonetheless)—we take some sort of raw material and turn it into something of value for our customers. We should therefore be able to apply lean thinking and lean tools to the way we work to make it easier, faster, and produce higher quality outputs.
From a lean perspective, the root cause of my (psychic) problem was that I couldn’t see the flow of my work. Sure, I had plenty of documents on my computer holding the case studies and the charts, and they were all neatly organized in folders, but it was difficult to see what I had done and what I still needed to do. So my brain was working overtime—literally—to sort out and track all the pieces of the book. Even though my brain didn’t charge me overtime wages to work through the night, it still wasn’t a particularly lean way to operate.
I took advice from A Factory of One and made my work visible. I created a personal kanban with each chapter in a swim lane, and each column representing the stage of completion for that chapter (outline, first draft, second draft, etc.). I had additional columns listing the case studies and charts that I wanted to include in each chapter. (And of course, I had a “Done” column so I could enjoy the feeling of finishing each section of the book.) When I sat down to write each day, I looked at the post-it notes on the board, determined which section I felt like writing, and then blocked out two to three hours in my calendar for work on that section—no client phone calls, no email, no interruptions. That uninterrupted block of time created flow in my work.
The difference was instantaneous. No more anxiety-filled sleep, no more waking up at 3am—instead, I was confident and sure of the progress I was making, the work that I needed to do, and my ability to meet the publisher’s deadline. Which I did. Two days early.
When we talk about lean, we generally talk about how it applies to external systems and processes. We forget that all the work we do contains processes as well, from organizing a meeting, to preparing a budget, to developing a marketing campaign, to designing a new running shoe. And those processes can be improved through the application of lean thinking. We can’t measure the benefits in the same way that we measure improvement on an organizational level, but they’re just as real. Lower stress levels. Less feeling of overwhelm. Greater emotional capacity to connect with colleagues. Fewer careless errors in your work.
Most of all, applying lean to your own work—or more precisely, to the way you work—means that it will consume less time. If lean is about creating more value with fewer resources, then using time more wisely and more efficiently is of utmost importance, because time is the only truly non-renewable resource we have. If everyone “worked lean,” overall lead-times in your organization would get shorter, and you’d have more time to spend with your husband, your wife, your partner, or your dog. And that sounds pretty good to me.
THE AUTHOR
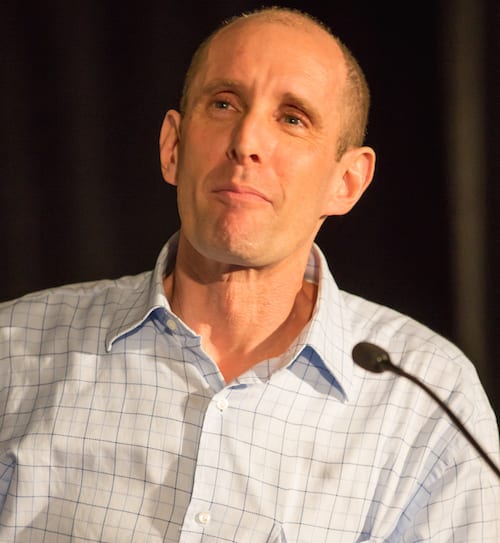
Read more
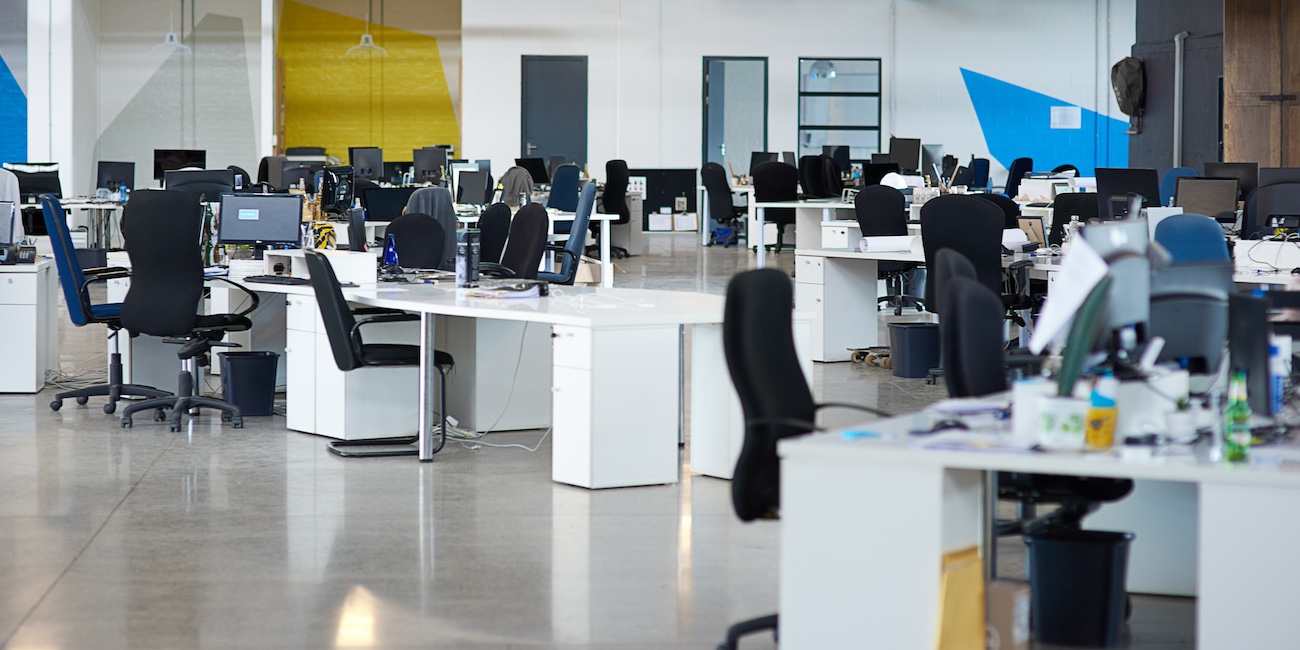
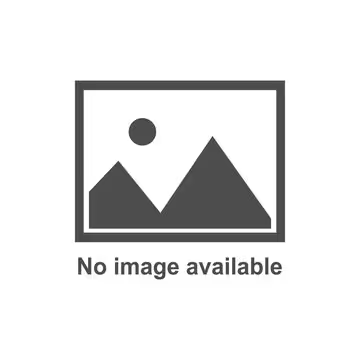
FEATURE – Attracting, developing and retaining talent has become a pressing issue in the corporate world, as new generations show skepticism towards traditional management. Lean is the answer, say the authors.
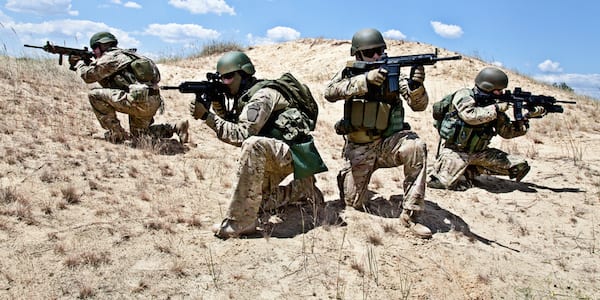
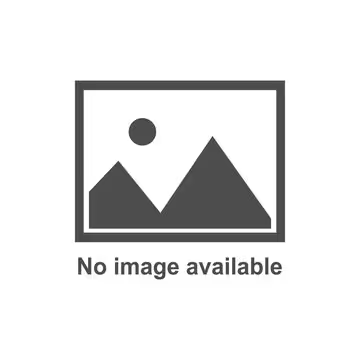
INTERVIEW - What do the United States Army’s Special Forces unit and Toyota have in common? To find out, we spoke to the Green Berets’ former Director of Training at the LEI summit in New Orleans.
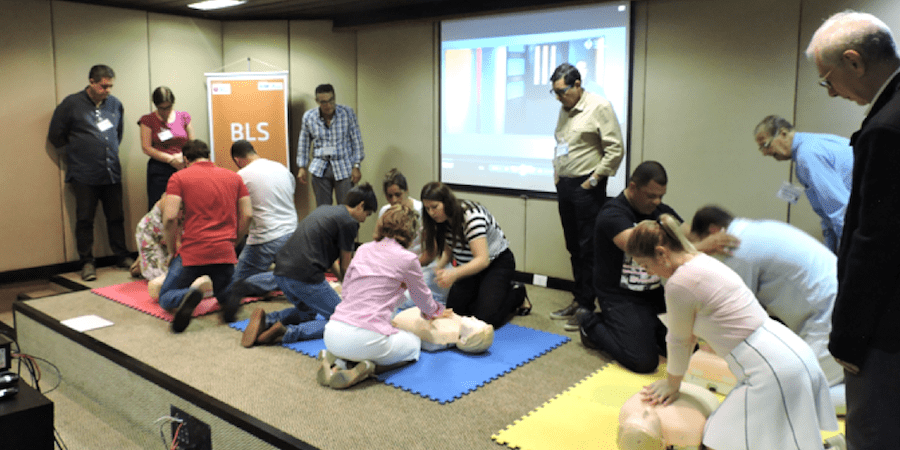
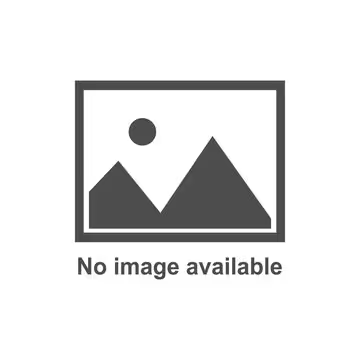
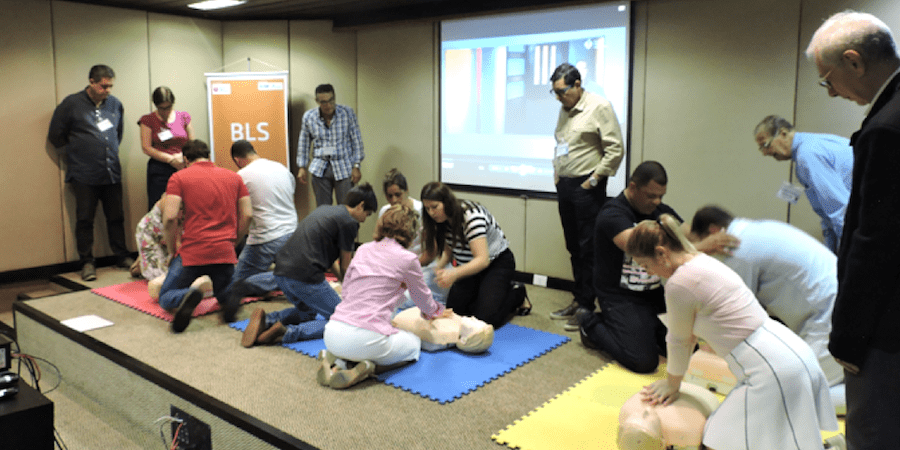
INTERVIEW – A cardiologist from a hospital in Salvador de Bahia explains how his department was completely transformed following the introduction of a dedicated pathway for heart patients.
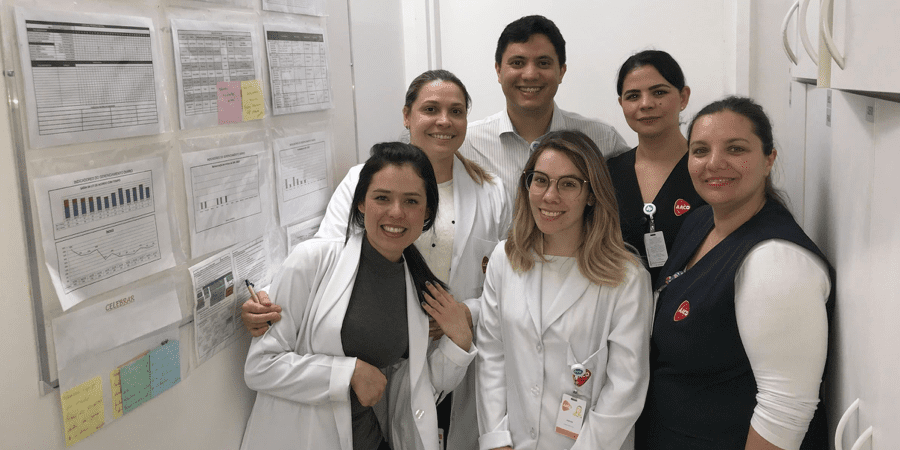
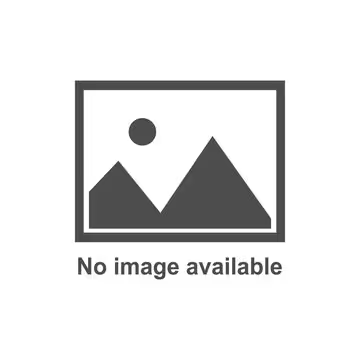
CASE STUDY – Effectively deploying and executing your strategy requires mastering quick follow-ups at different levels of the organization – in other words, Daily Management.