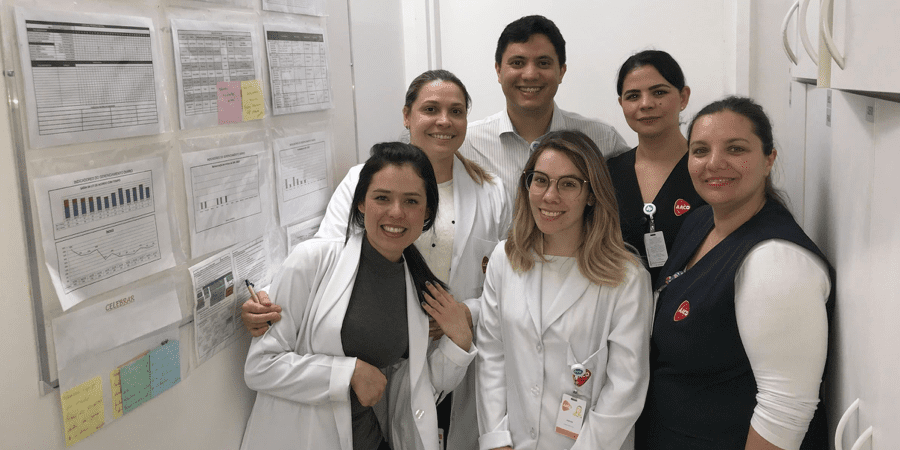
Daily management in the ICU
CASE STUDY – Effectively deploying and executing your strategy requires mastering quick follow-ups at different levels of the organization – in other words, Daily Management.
Words: Alessandra Fátima De Sousa, Andréa Matheus Basgal and Robson Gouveia
Editorial support by Tamiris Masetto Manzano
Managing and tracking every task that needs to be performed by a team is the responsibility not only of a leader (although their role is key), but also of the team members themselves participating in the process to create value for their customers… or, in the case of Brazilian hospital AACD, for their patients.
AACD is a private not-for-profit organization that serves people of all ages that come from both the Brazilian Unified Health System (SUS) and private healthcare. Its main focus is on people with disabilities, with the goal of allowing them to live to their full potential by overcoming their physical limitations. The hospital also strives to contribute to a society that welcomes diversity.
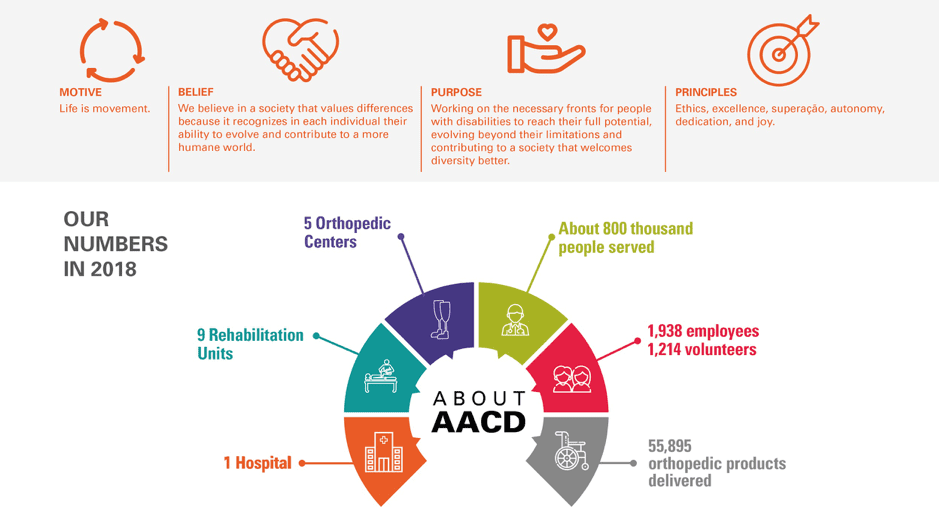
AACD is made up of one hospital, a 9-unit Rehabilitation Center (five of which are located in the state of São Paulo) and five Orthopedic Centers, all boasting a highly specialized multidisciplinary team. Every year, AACD cares for some 800,000 treatments.
Seeking to turn to a different management approach, improve the level of care and optimize the patient journey, AACD’s Orthopedic Center in Ibirapuera, São Paulo, has been experimenting with lean concepts for the past year.
The Center performs low-, medium- and high-complexity surgeries and treats patients coming from across Brazil. In particular, it is known for its expertise with complex procedures, such as scoliosis surgery.
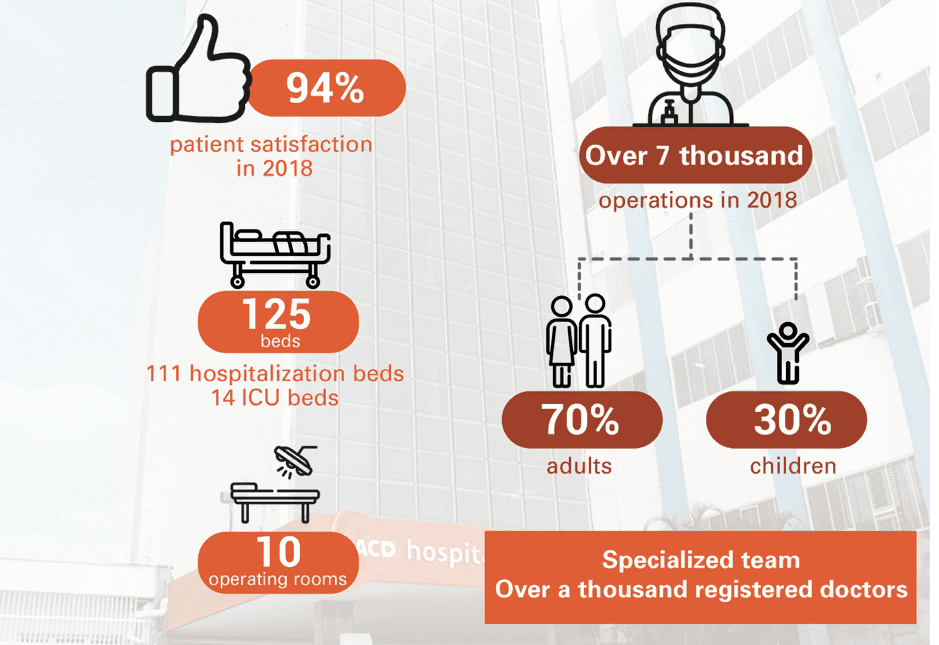
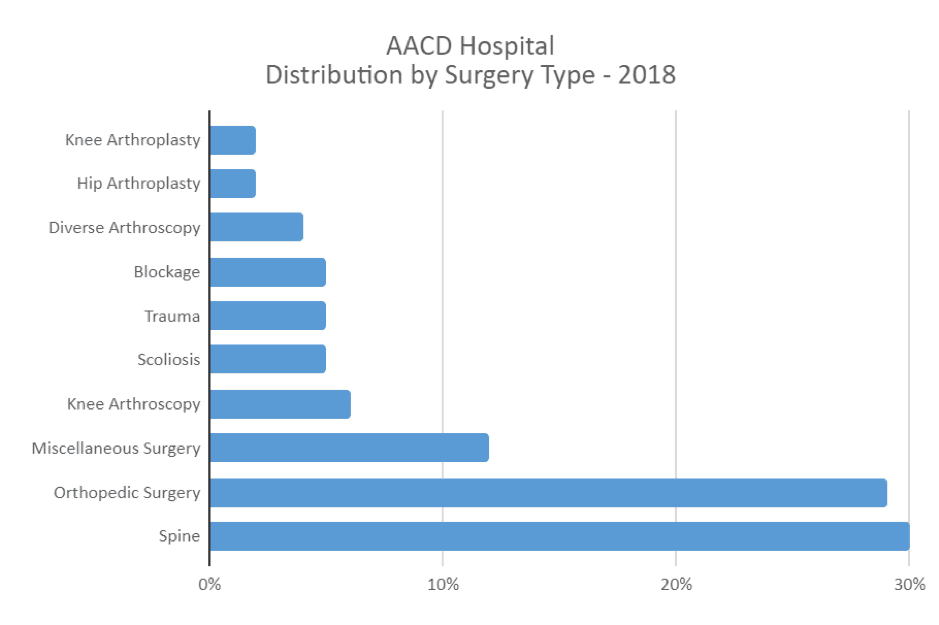
In line with the organization’s Continuous Improvement Program, the People Management team chose daily management as the strategy they’d use to develop teams and improve their real-time problem-solving capabilities. The Quality team also supported the project, participating in the training and taking on the responsibility for the expansion of the experiment to other areas.
They started in the Clinical Engineering area in August 2018, with a focus on equipment management and technological innovation. In November 2018, they took the concept of daily management to the ICU and immediately saw some excellent results.
THE PLANNING STAGE
During the Qmentum International certification process (which they obtained last year), the AACD team realized the need to highlight the roles and responsibilities of the cross-functional team that was responsible for implementing the DM in the ICU, developing people and making everybody autonomous in solving problems.
The organization clearly saw the challenge in front of them: it was necessary to find a way to monitor every problem and task to be performed by the team in the shortest possible time to quickly act on any detected deviation – thus avoiding surprises at the end of the month. They understood that the ICU was one of the areas that would benefit most from the implementation of a daily management system as a tool for day-to-day discussions and problem solving by the staff.
For all patients to be given access to the ICU at the right time (97% of the demand is for post-operative care), it was critical to establish proper bed management in the unit to ensure that beds could be freed up in a timely manner while ensuring patient safety and humane care.
A team of physicians, physiotherapists, speech therapists, nurses, nursing technicians, pharmacists, nutritionists, and administrative assistants, with strong support from ICU coordinators, mapped the flow of discharges from the unit that were due to discussions taking longer than they should.
With an average stay of just 1.7 days and an average ICU occupancy rate of 85% in the ICU, coordinated care and synergy between the teams were essential to reach the goal of discharging patients maximum two hours after the doctor signed off on it.
Delays in discharging patients from the ICU to Inpatient Units can lead to bottlenecks. It negative impacts the experience of patients and family members and complicates things for internal customers like the Surgical Center. Between May and October 2018, the AACD ICU had a delay rate of 36% in discharges, leading to delayed admission to the operating rooms and in some circumstances to the cancellation of elective surgeries for lack of vacancy in the unit.
Under the guidance of the ICU’s medical coordinators – and with the support and engagement of everyone involved in the process – the team began to use A3 thinking, to analyze the problem, unearth its root causes and propose countermeasures, and a Daily Management board to regularly monitor targets.
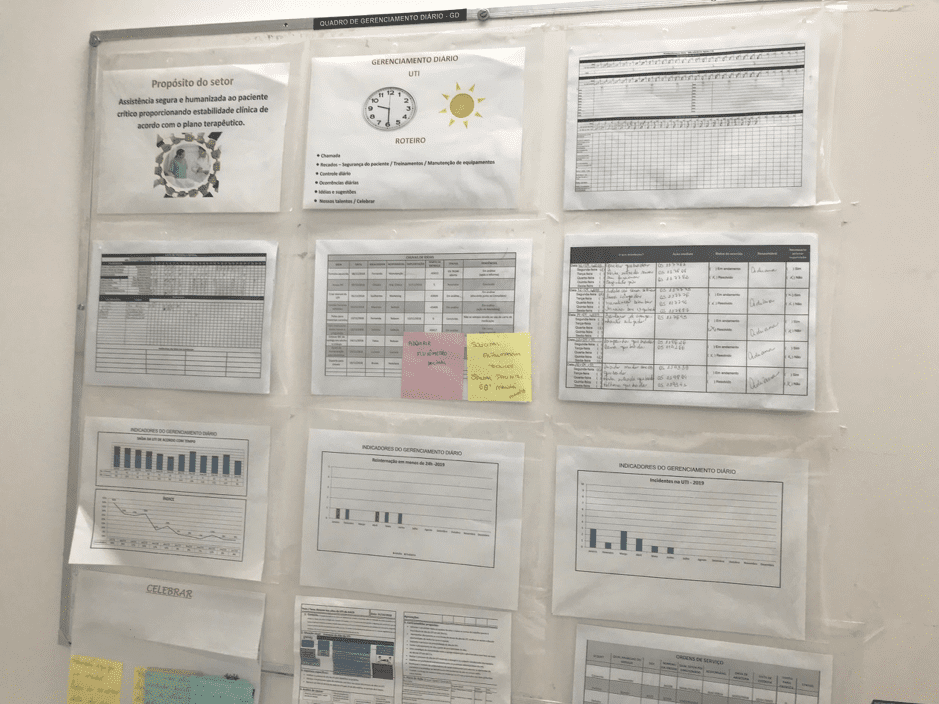
THE EXECUTION
Every day at 9:30 AM, the ICU’s crossfunctional team meets in front of the Daily Management board to reflect and discuss – the real purpose of Daily Management. Focusing on their True North – which is to provide critical patient care in a safe and humane way – the team seeks to understand how needs will be met according to the goals set for the area.
The daily meetings also allow them to analyze adverse events, such as readmissions after less than 24 hours, and to monitor the unit's equipment management. The team has the opportunity to express their concerns and to make suggestions, which are recorded in the Brainstorming field. There is also some time reserved for praising people for their achievements and making general comments.
The meeting is attended by an administrative assistant, who has the important role of ensure the meeting proceeds in a timely fashion and that everyone gets involved. The Daily Management meeting happens every day, no exceptions (even when the leader cannot attend).
Initially, the clinical team was very concerned about leaving their work to attend the meeting, as this could impact the execution of planned activities. Over time, however, results started to appear and their behavior changed. These days, they do everything they can to be available for the meeting.
THE RESULTS ACHIEVED
Daily Management has become an important communication tool in the ICU, giving autonomy to team members and providing a way to anticipate and solve problems.
Six months after the implementation started, the ICU reduced the number of delayed discharges from 36% to 8%. The average delay dropped from 92 minutes to 50 minutes – a 53% reduction. The team also experienced an improvement in bed management in the ICU, in the use of the intensive care specialists’ time, in the collaboration among professionals, and in waiting time in the operating rooms.
The next challenge for AACD is to monitor the system that cools down the environment, which is critical for patient and staff safety. The Quality sector is determined to continue supporting the areas where Daily Management has already been introduced as well as those that are interested in using it.
Here are some of the most important lessons we have learned over the course of the past year:
- Really understand Daily Management and how you will use it;
- Visit organizations that are already using it, to get inspiration;
- Take the time to explain the idea and purpose of DM to area managers;
- Do it with the support of leadership. All of this needs to make sense to the leader;
- Make the results visible and publicize them as a way to recognize the efforts of the team (and perhaps even inspire other areas).
ACKNOWLEDGEMENTS
To Dr. Leôncio Batista Neto (Medical Coordinator of Adult ICU), Dr. Fabiola Toffoli (Medical Coordinator of Pediatric ICU), Robson Carvalho de Santana (Nursing Coordinator of ICU), and the Multiprofessional Team (auxiliary and administrative staff).
Read this article to learn how to effectively use daily management.
THE AUTHORS
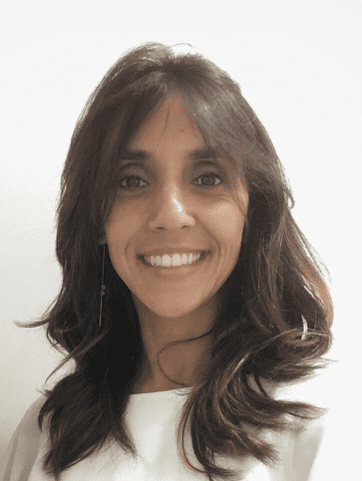
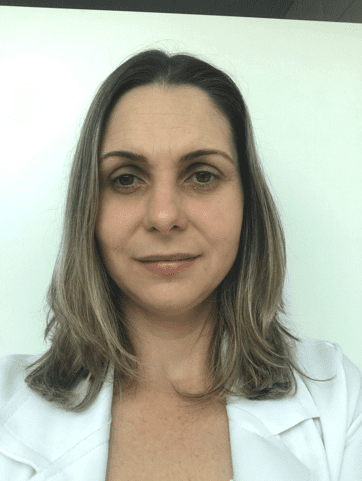
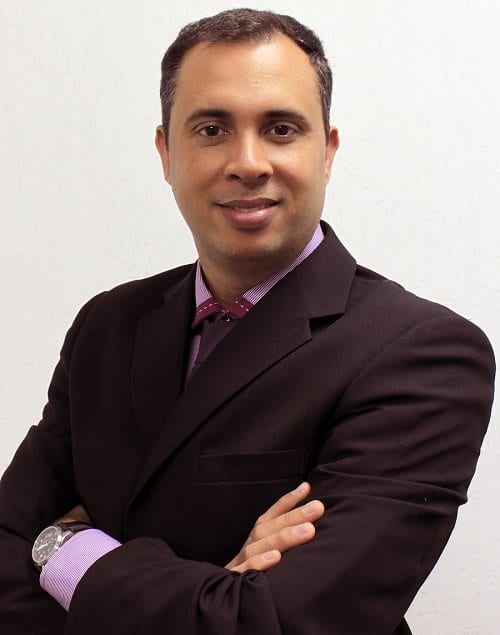
Read more
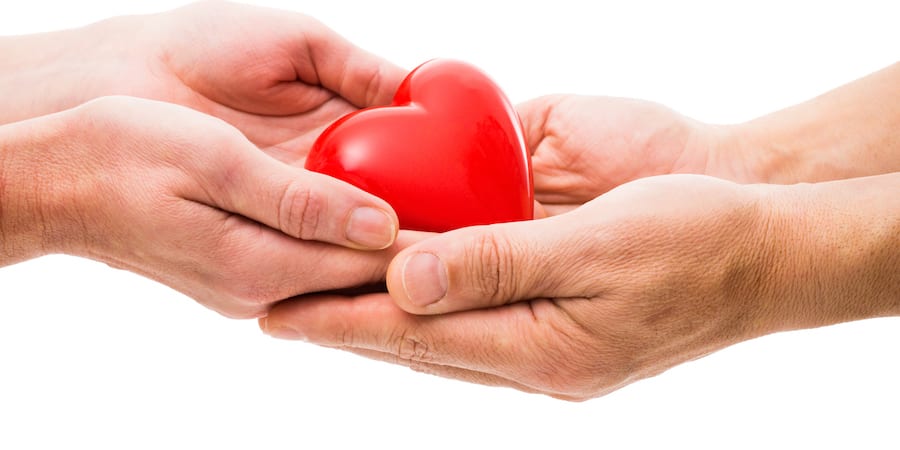
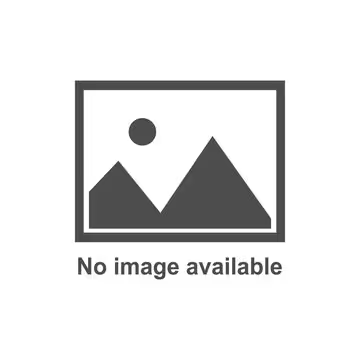
FEATURE – A Michigan NGO that facilitates organ and tissue donation shares its experience with value stream mapping, reflecting on people coming together to understand the gap between current and future state.
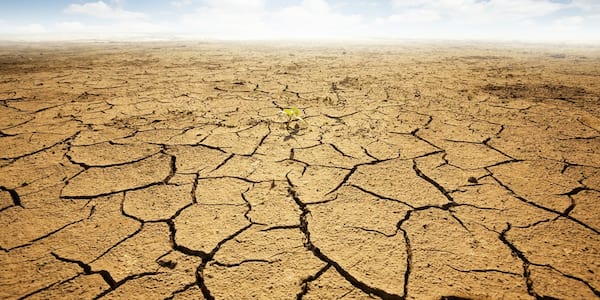
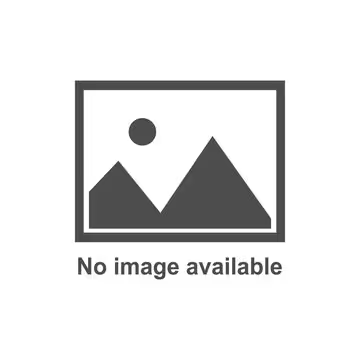
FEATURE – A kaizen suggestion scheme has the ability to unlock the potential of lean change in our organizations, but too often our mistakes kill it before it even has a chance to take off and gain momentum.
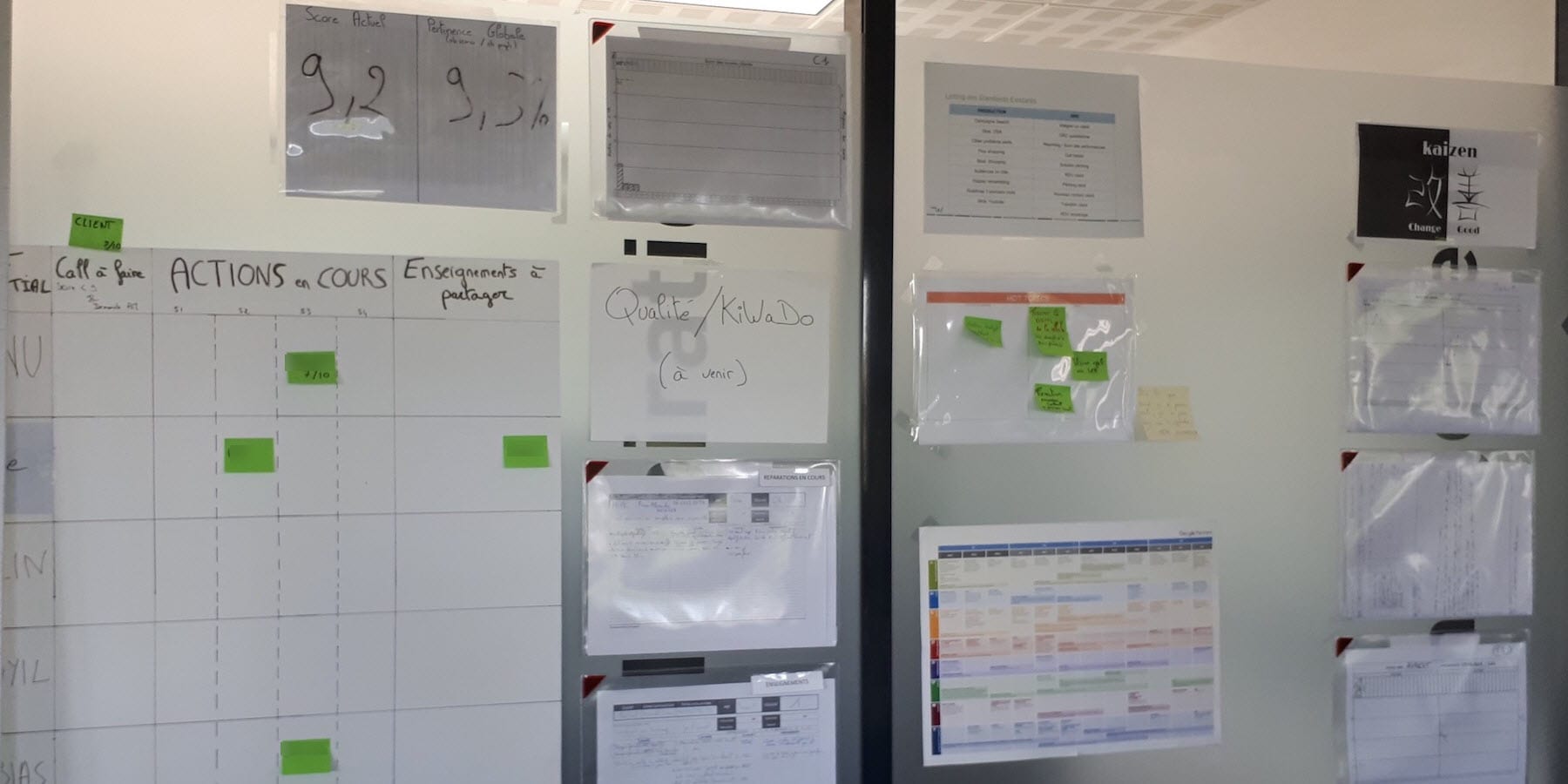
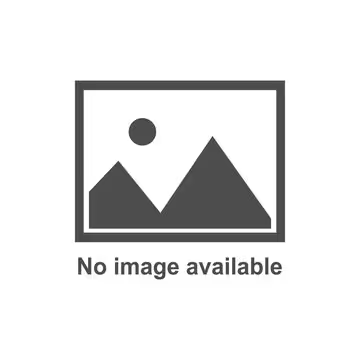
NOTES FROM THE GEMBA – In the web marketing world, a competitive advantage is a matter of life and death for businesses. The author meets a firm that has been leveraging lean to gain one.
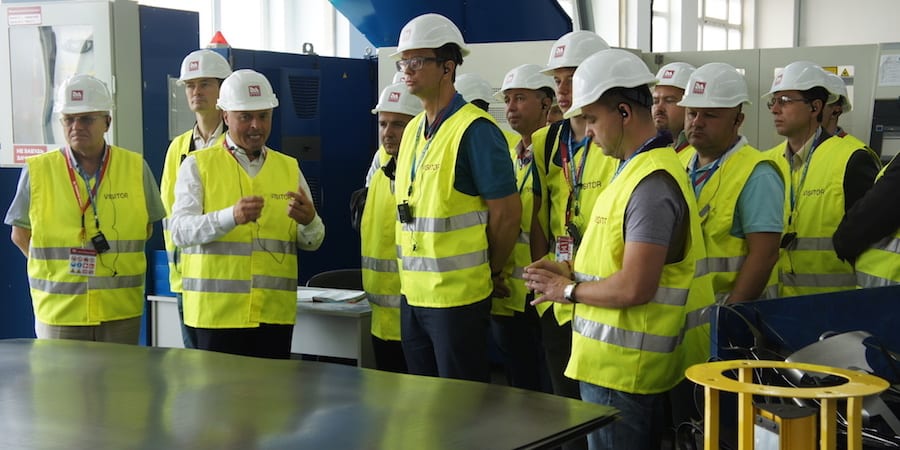
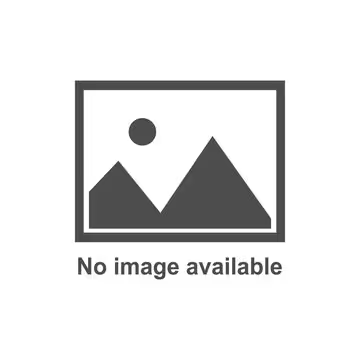
INTERVIEW – In this Q&A, the CEO of a Ukrainian provider of equipment for stores shares how lean thinking has helped his company modernize its processes and engage its people.