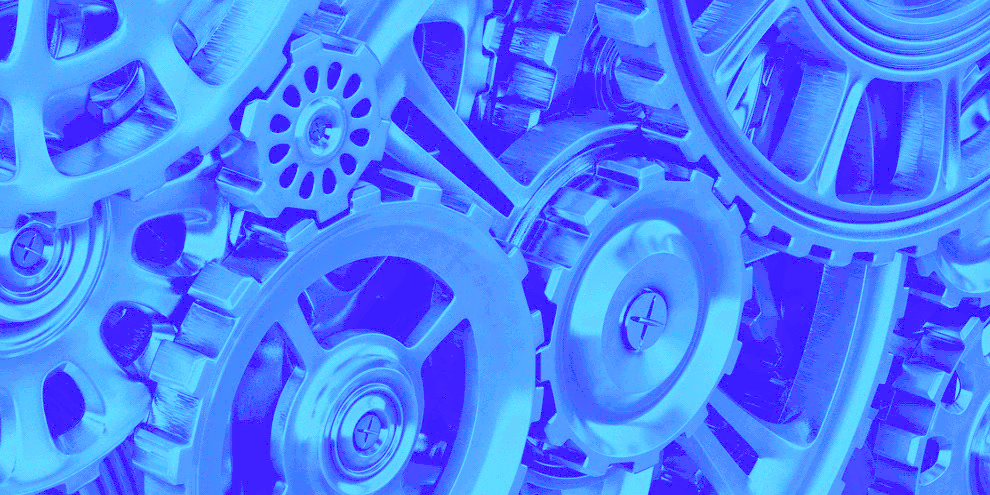
What pull systems can I combine?
FEATURE – In the last article in his series, the author discusses how you can mix and combine the different pull systems available to the lean practitioner.
Words: Christoph Roser
Until now, this series has covered the different types of pull systems and helped you identify the one that is right for you. In this last article, I’d like to explain what pull systems can be combined.
As a rule, you can combine some pull systems within the same pull loop, although there are some restrictions. Combinations of different kanban systems are very common, for example, and they often include a CONWIP system. You can also combine different pull systems for sequential loop, where for example a kanban system feeds into a CONWIP system.
WHAT PULL SYSTEMS CAN BE COMBINED IN THE SAME LOOP?
Sometimes you may need only one type of pull system. In other situations, however, you may want to combine different pull systems for different part types in the same loop to fit your needs.
Most commonly, organizations have a combination of make-to-stock products and make-to-order products. To ensure a smooth production process would typically require the use of two different pull systems here. In the (very subjective) diagram below, I represent the compatibility of the different methods within the same loop.
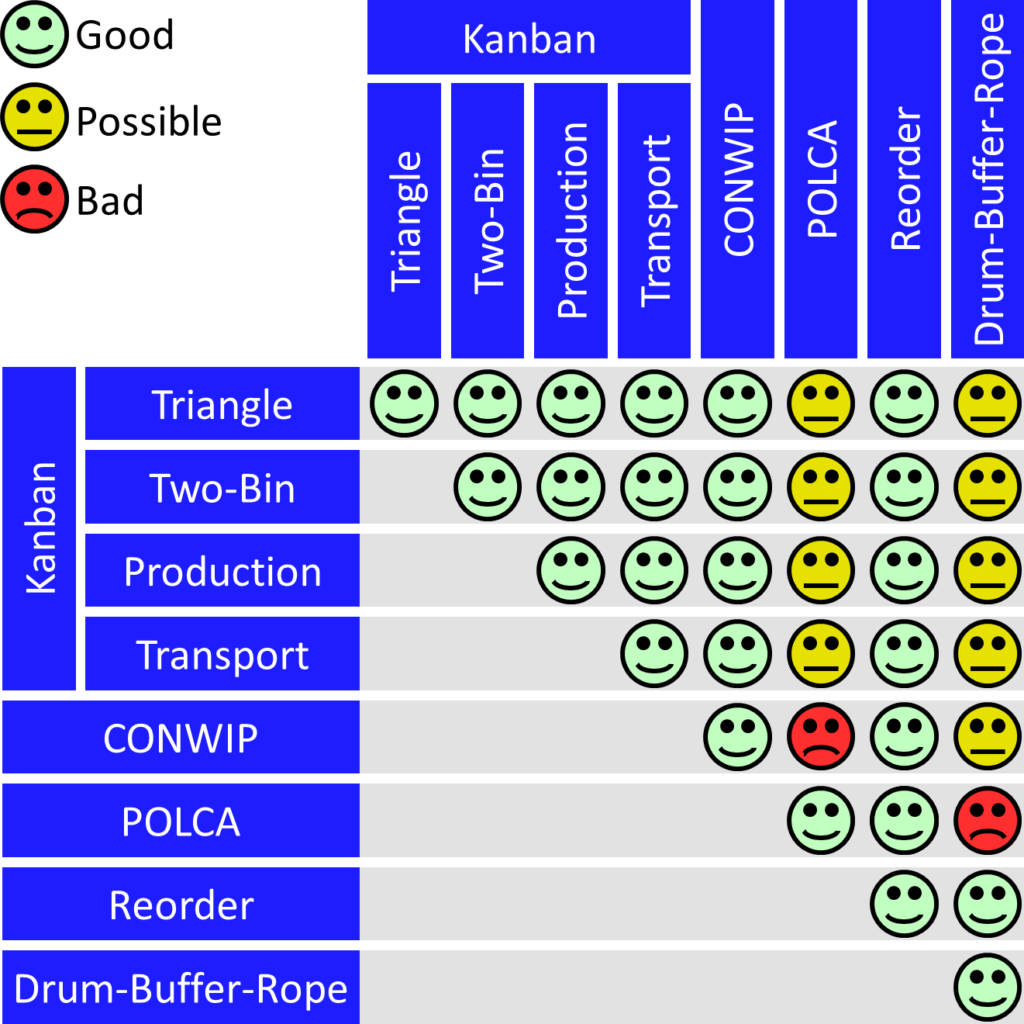
In general, any kanban system is compatible with another other kanban system. You merely change some information on the kanban. A CONWIP system is in its nature like a customizable kanban, and is therefore very compatible with kanban, too (such a mix is recommended when you are dealing with a combination of make-to-stock and make-to-order).
Reorder systems are mostly used for purchasing, where you don’t really need to worry about compatibility. The way you order one type of goods can be completely independent from the way you order another type of goods. You should only worry about not confusing your people with too many systems.
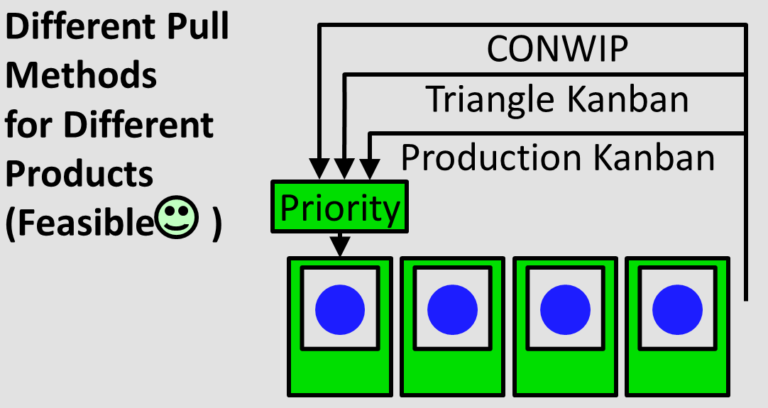
It may be possible to combine pull systems with POLCA or drum-buffer-rope. However, know that the outcome can easily range from awkward to very awkward. In general, the fewer different systems you deploy, the less confusing it will be for operators. If you use different systems, at least make sure your first process in the loop has a good standard on which signal takes priority over which signal, as shown here.
Also, please note that this table applies to the pull system for different part or product types in the same pull loop. Do not use different pull systems for the same part type in the same segment of your value stream. It also does not apply to “overarching” nested pull systems, as shown below. Even though you can find such nested systems in literature sometimes, I seriously question the benefit they are supposed to bring.
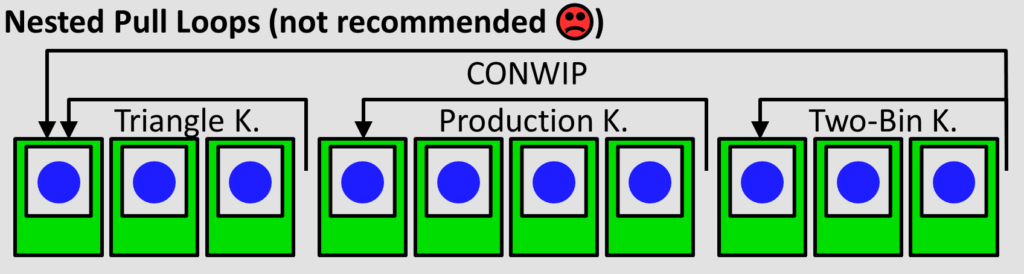
WHAT PULL SYSTEMS CAN BE COMBINED IN SEQUENTIAL LOOPS?
It is possible to combine different types of pull production (and sometimes even push, if you can’t help it) for your value stream. One or more kanban loops that feed into supermarkets can easily supply one or more CONWIP loops. The same is true for other pull methods. An example is shown below.
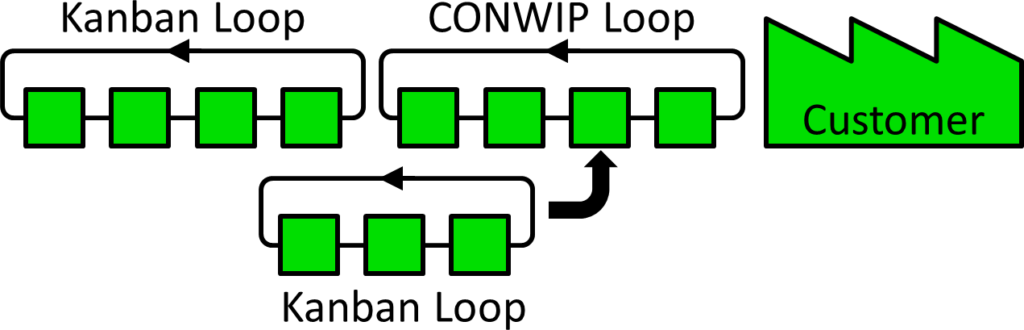
The table below gives you an overview of the possible combinations. Which type of pull system (or push) can feed into which other type of pull system (or push). As you can see, there is a lot of compatibility, with only a few restrictions.
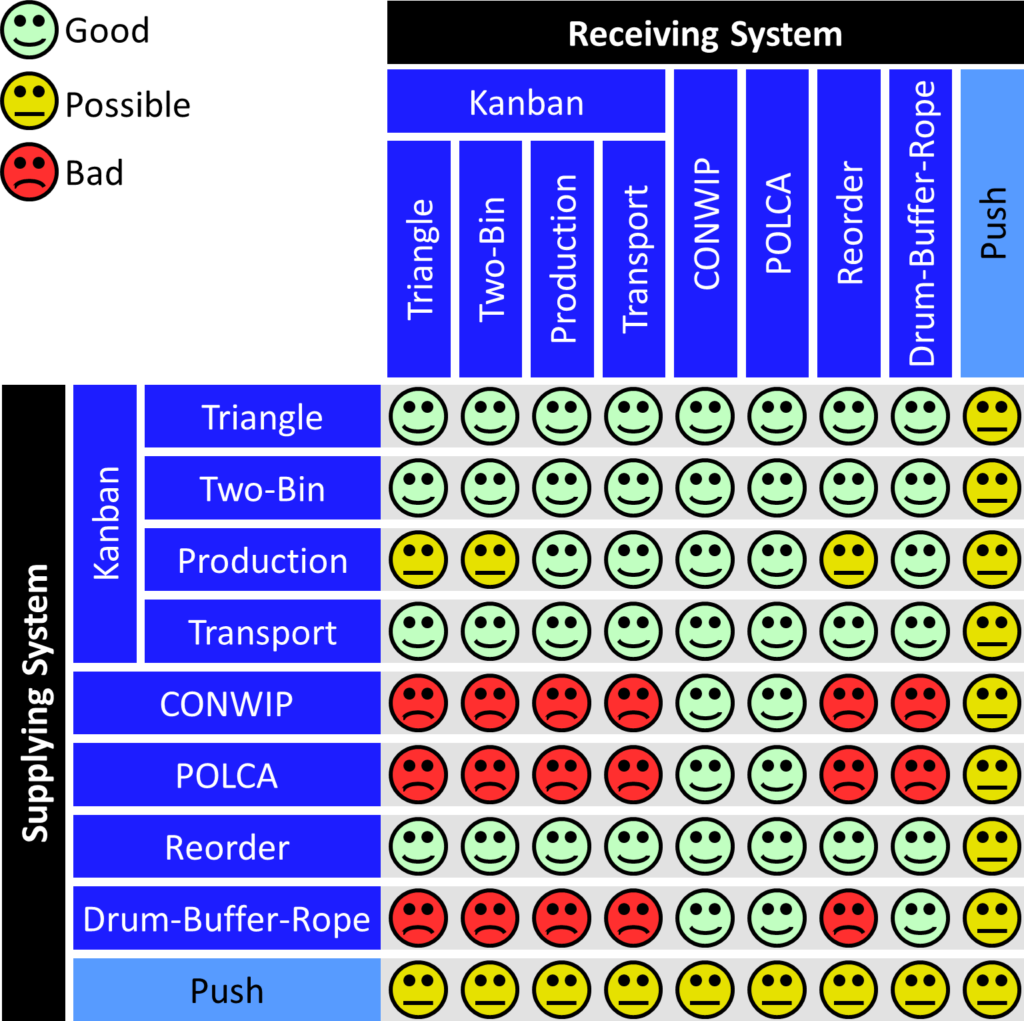
First, avoid transitions from make-to-order to make-to-stock. Systems suited for make-to-stock production – like kanban or reorder systems – can easily feed into systems suited for make-to-order production like CONWIP or POLCA. However, the same can’t be said for the other direction, make-to-order feeding into make-to-stock. If a CONWIP system supplies a kanban system, you will have custom-made parts supplying make-to-stock products. Since the make-to-order part is only produced if there is a demand, the lead-time for the entire system would be excessive. I advise against such combinations. Fortunately, it is rare to have a make-to-order system feed into a make-to-stock system, as this usually makes no sense from a technical standpoint.
A second, smaller limitation aims to avoid infrequent large orders for a preceding system that is set up for production of small quantities. In particular, reorder systems may have large orders to refill the entire stock back to the target level, but triangle kanban and two-bin kanban systems can also batch demand into larger orders. Those systems do not convey the information of their demand until they reach the minimum inventory. Once they do reach it, they demand everything at the same time. It is possible to have a supply system that produces frequent small quantities for a receiving system that has infrequent but large orders. However, you need additional inventory to deal with such fluctuations. Hence, it may be better to have small orders from the receiving system. Altogether, to avoid large buffer inventories, it may be better to have another kanban system following the first kanban system instead of a reorder system. If the delta between the minimum level and the target level of the receiving reorder point system is small enough, it can work.
Finally, all combinations involving push are marked as neutral, since pull is almost always superior to push. It is possible to have a push-pull combination in both directions, if set up carefully. Push-pull boundaries can happen if a transition from push to pull has not yet transformed the entire value stream, or if some segments of your value stream are unsuitable for pull production. Still, you should go for pull whenever possible, and see push as a temporary situation until you have time to convert it into a pull system. Such combinations along serial loop types can be from push to pull as well as the other way around.
This concludes my small series on how to select and combine the different possible pull systems. More can be found in my book (like below). Now, go out, pick the right pull system for you and get organizing your work!
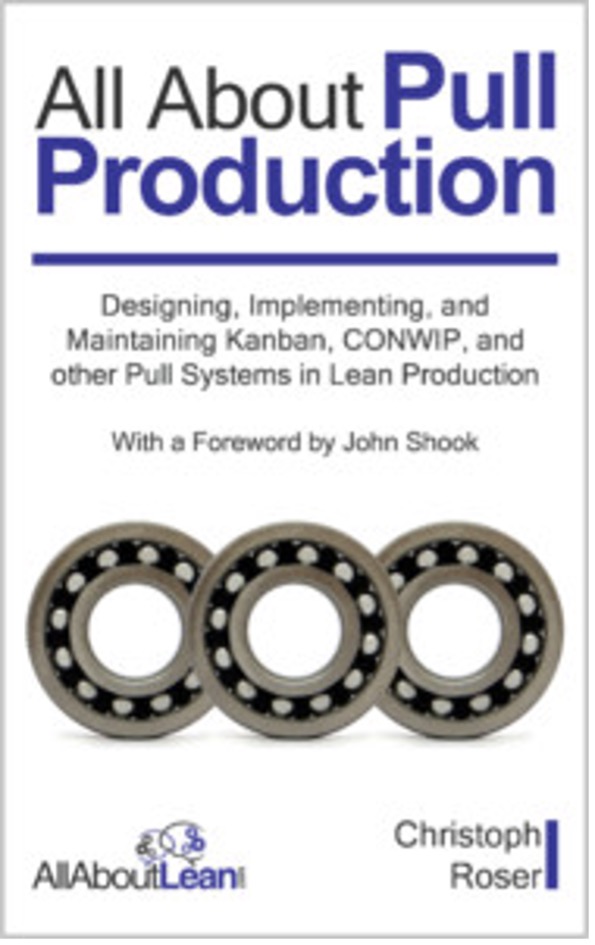
This article, originally published on All About Lean, is loosely based on Christoph’s new book All About Pull Production: Designing, Implementing, and Maintaining Kanban, CONWIP, and other Pull Systems in Lean Production, a practical guide for anyone looking to implement pull systems.
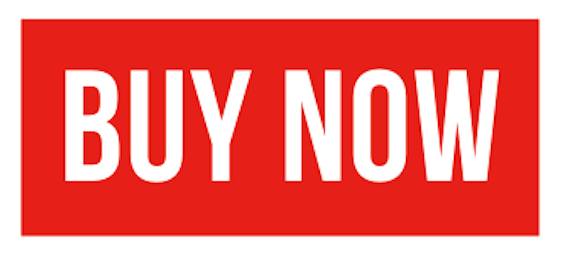
THE AUTHOR
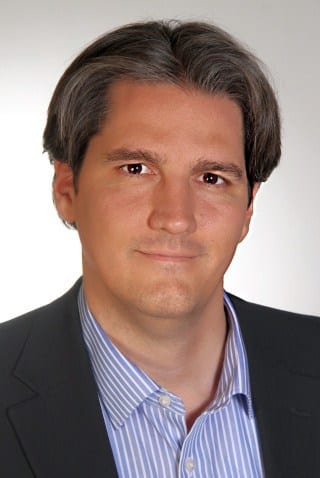
Read more
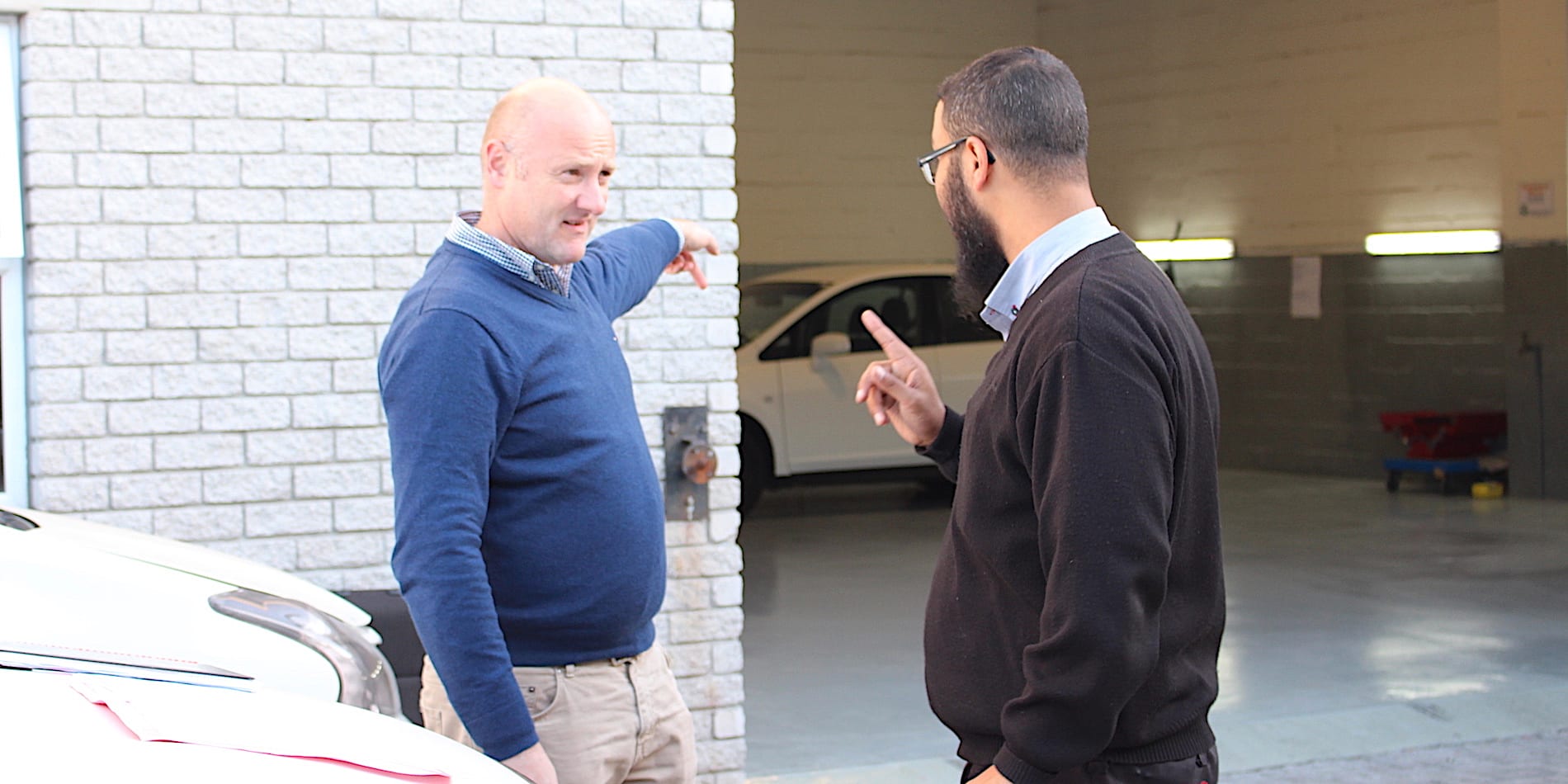
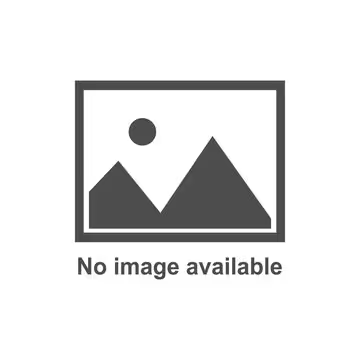
FEATURE – The role of the coach in a lean transformation is an often-debated topic. The author discusses his experience building the architecture of the Halfway turnaround.
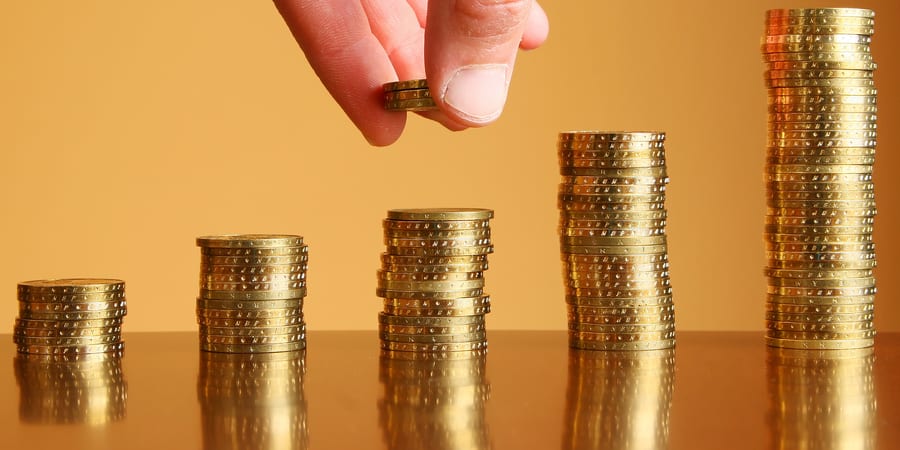
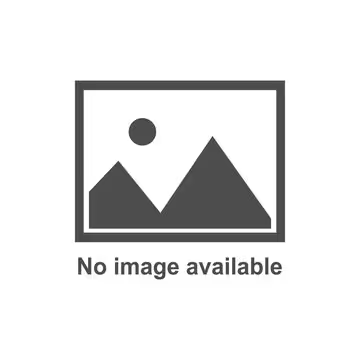
RESEARCH – What kind of financial results can a SME owner expect from a lean transformation? To find out, the author of this interesting research analyzed the performance of 100 Italian small and medium-sized companies.
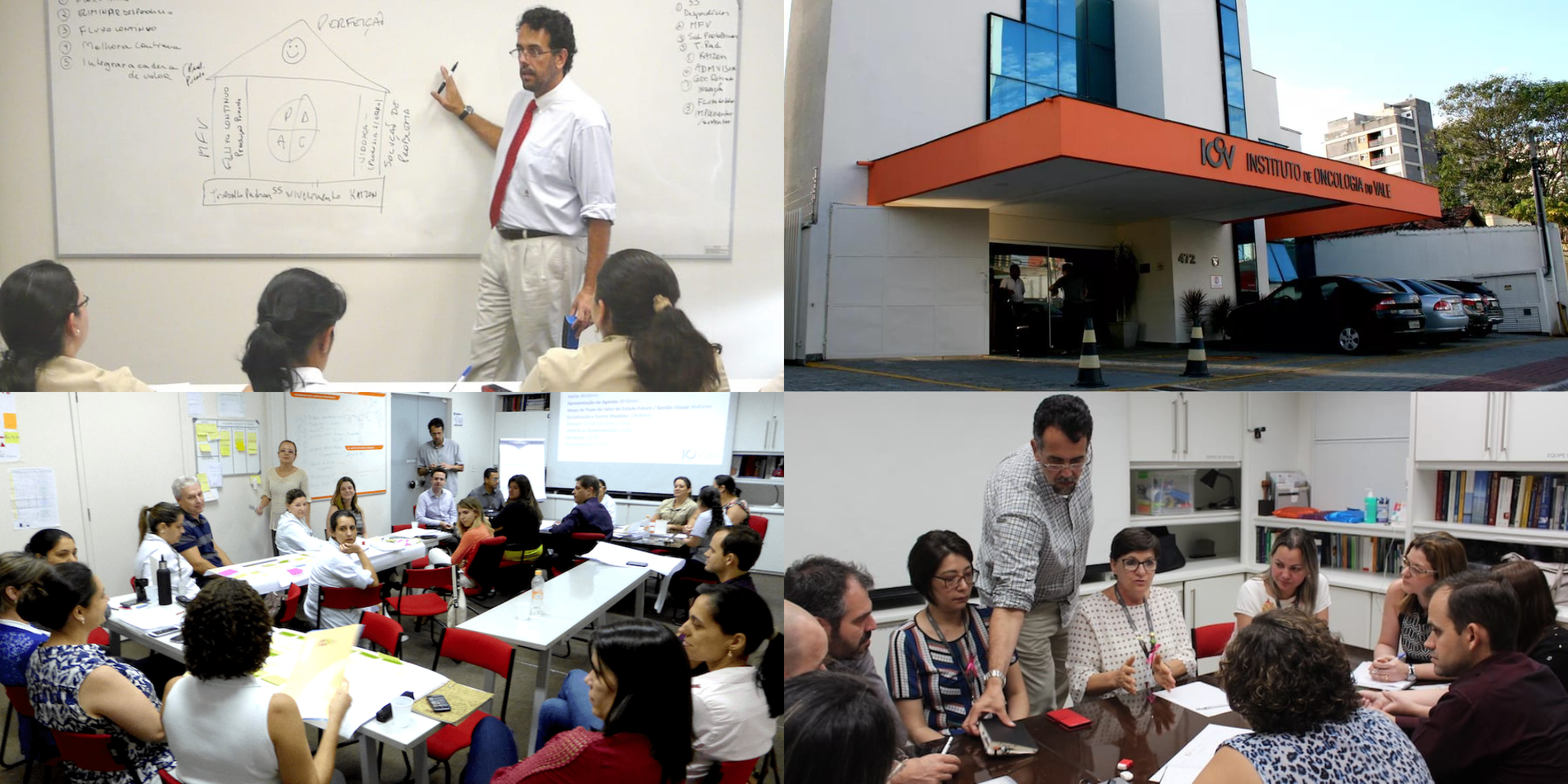
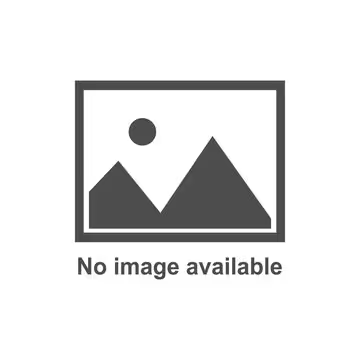
FEATURE – PL readers will likely be familiar with IOV, the cancer clinic in Brazil that’s become a reference for lean healthcare for countless organizations. Here, Dr Fred looks back at IOV’s 15-year journey.
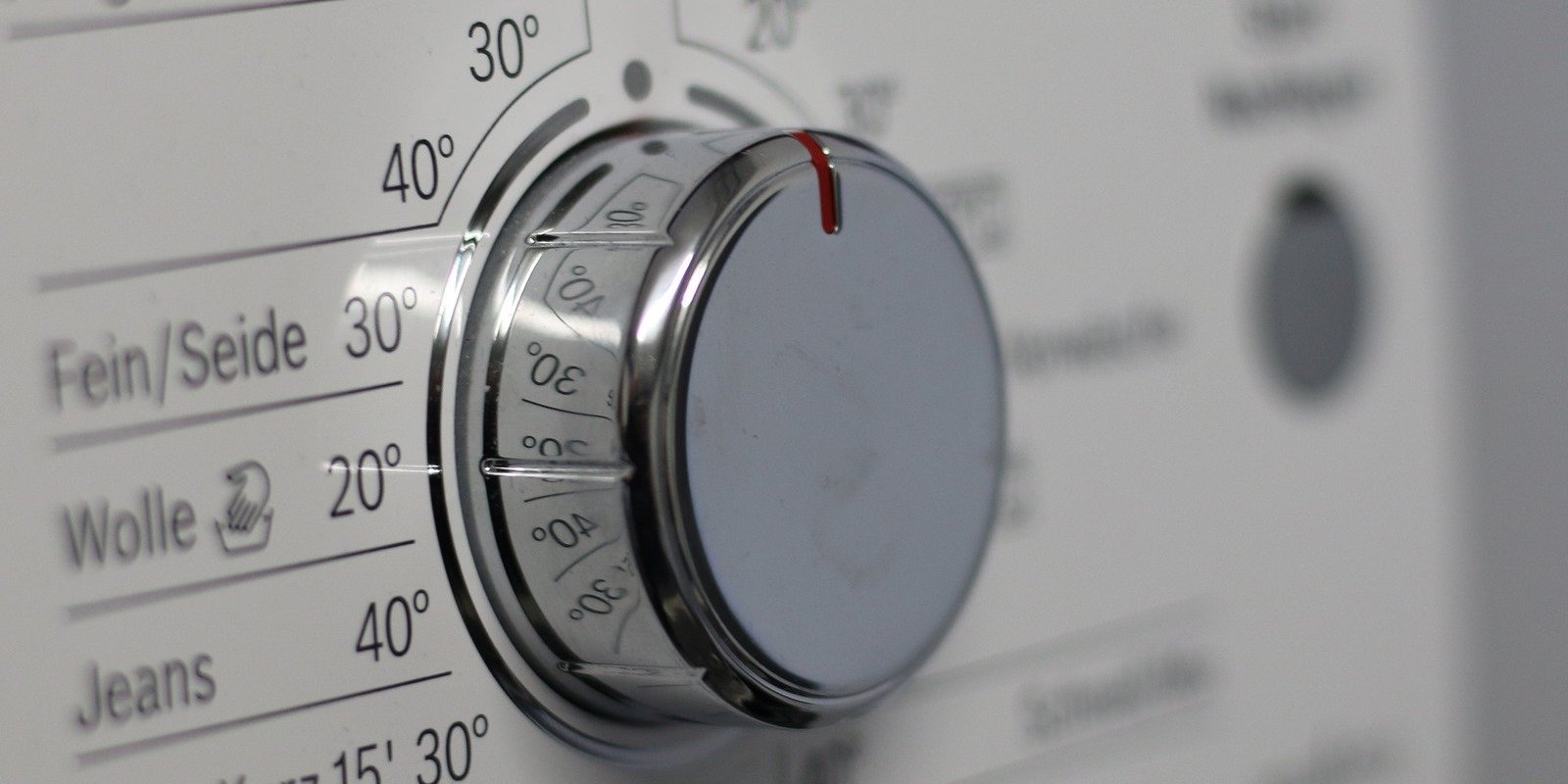
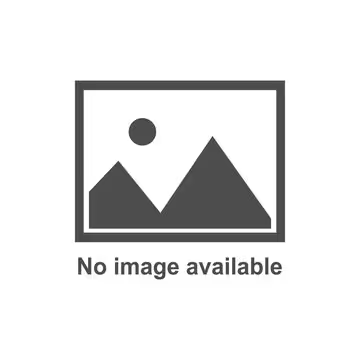
FEATURE – In this compelling read, the author explains how “centerlining” tools and settings can reduce variation in a process and avoid having to constantly seek adjustments à la McGyver.