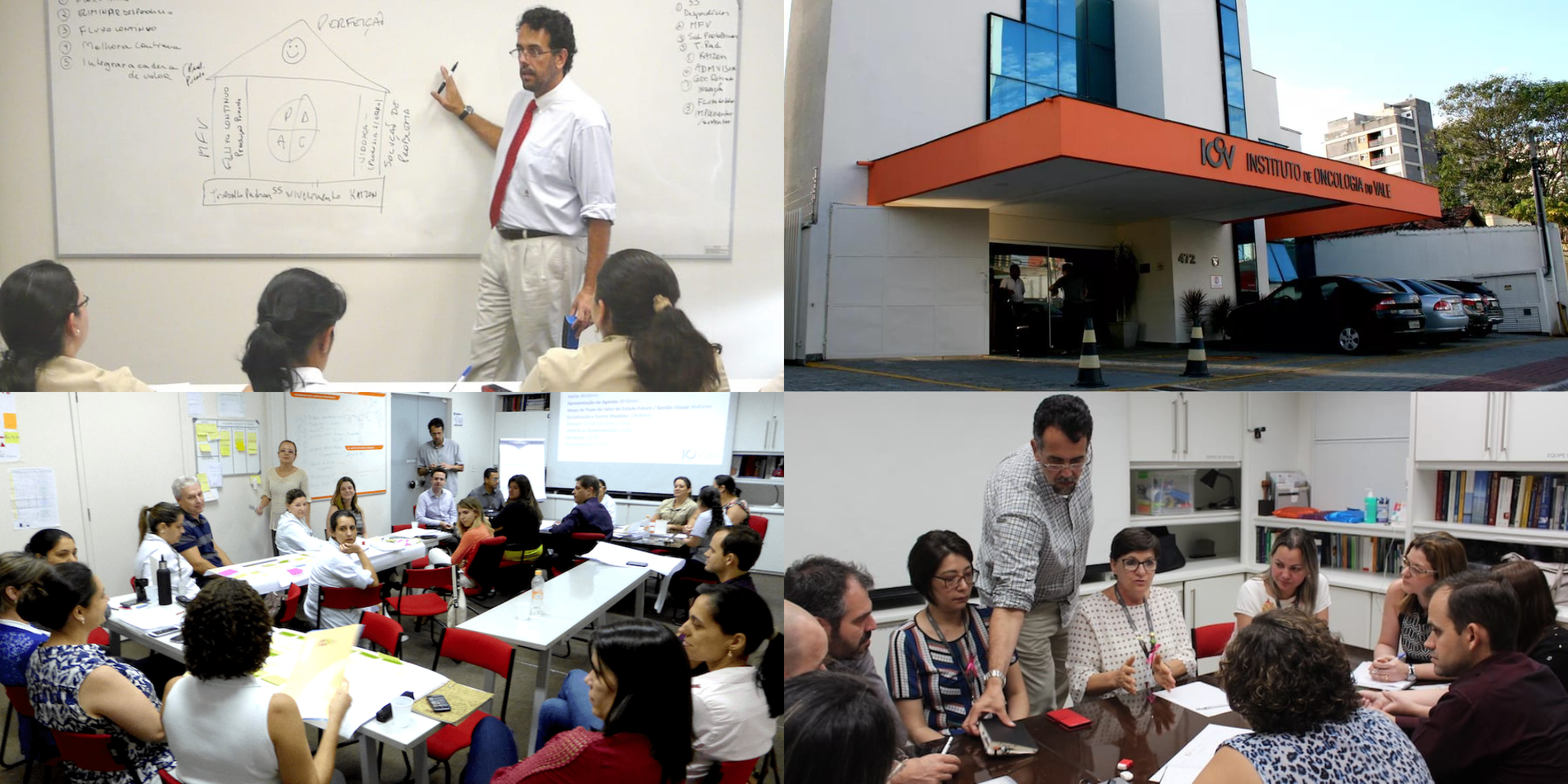
Reflecting on our 15-year journey
FEATURE – PL readers will likely be familiar with IOV, the cancer clinic in Brazil that’s become a reference for lean healthcare for countless organizations. Here, Dr Fred looks back at IOV’s 15-year journey.
Words: Dr Frederico Pinto
Fifteen years ago, lean in healthcare was in its infancy. There were very few examples out there. In fact, IOV has come to be known as one of the early adopters that have opened the way for the spread of Lean Thinking in healthcare here in Brazil and South America. I am incredibly proud of what we achieved, but I also know there is still a lot more for us to do.
Still, 15 years is an anniversary that somehow invites you to reflect. So, I thought it would be a good time to look back and think about what we know today about bringing Lean Thinking to a healthcare setting that we didn’t know when our transformation began.
Lean is a learning journey, and we certainly learned a lot. Interestingly, however, what was motivating us then is the same thing that is motivating us today: optimizing the system in which we operate. What has changed is our understanding of and experience in intervening on the system, rather than working on isolated improvements. When we started, we were essentially driving blindfolded: we knew the system wasn’t working, but we couldn’t do better than trying different things until we got some results. And, truth is, we did get results. Remarkable ones. But without the awareness necessary to replicate them.
Today, whenever we are asked to help other healthcare organizations to start their own lean transformations, our first suggestion to them is to create a model line. In practice, that’s exactly what we did ourselves 15 years ago without knowing it. So, the interesting thing about this is that, if I were to start all over again, I’d probably do it pretty much the same way.
This isn’t to say that nothing has changed since then. Quite the opposite. Our understanding of lean has evolved, and this has made our lives much easier. Thanks to our and other organizations’ experiments and experience, we have a much clearer understanding of what lean is and how it works. Throughout this time, thought leaders haven’t stopped churning out new models and theories helping us to cement our understanding of this elusive management philosophy. Take John Shook’s Lean Transformation Framework, for example. It has taught us the key dimensions we need to address if we want to effect change in our organizations.
Most importantly, over the years we have learned the importance of leveraging people’s knowledge and experience and of always giving them the time and space to learn. Sadly, this is still not the case in most organizations out there, which seem to be married to a command-and-control type of management – even though its shortcomings have now become impossible to ignore.
Lean advocates for an organization where leaders become hosts for the system and strive to create an environment where people learn continuously and eventually become autonomous problem solvers. On this note, I think it’s important to mention the White Paper titled Five Guiding Principles to Transform Healthcare that my LGN colleagues and I published in 2020. The five principles provide us with a great template for designing an ecosystem for learning and teaching Lean Thinking, in other words to develop the capabilities of people. They tell us what we need to learn in order to create the environment we want. (They are about the heuristics of knowledge generation: “If I do this, I will learn that.”)
LTF and the five guiding principles are examples of how our understanding of lean – both at IOV and across the wider community – has deepened over the years. The basic information was always there – lean was always a people-centric holistic system aimed at creating more value with the same or less resources – but we have become better an unpacking its many layers and repackaging it for easier consumption by people around the world. Every day, by studying and practicing lean, we are learning to use it more cleverly.
DESIGNING AN ENVIRONMENT FOR LEARNING
There is a lot of talk in the Lean Community about the importance of leadership involvement in a transformation. While this is true, my biggest learning to date is perhaps that, when it comes to a transformation, you need more than a leader. You need someone who redesigns the system and makes it fit for continuous learning – an architect, a chief engineer.
A lot of people base their transformations on approaches that were designed for other systems and organizations. The most common example is, of course, Toyota, the company that everyone wants to emulate but that nobody fully manages to. Such pre-packaged, overly prescriptive models make little to no sense when it comes to Lean Thinking (as the LTF teaches us, every transformation is situational), because they are not a good representation of the reality they aim to change. Indeed, the reason behind a lot of failed transformations is the misconception that you can copy-and-paste an approach designed for another system.
An architect is necessary to advance a lean transformation precisely because he or she provides a different perspective of the business, which managers – who are preoccupied with the daily work – don’t have. But who should this person be? It doesn’t have to be the CEO, but it should be someone (an area manager, perhaps) with a direct connection to the gemba and the ability to take a step back, see the big picture, and interact with different layers of the organization. In doing that, the architect creates the scaffolding that will support the lean transformation and enable the team to make changes, before a more “definitive” structure can be erected.
While supporting other organizations in their journeys, we learned that the scaffolding system is situational and that the system designer – the architect – is crucial in charting the course. Some systems, for instance, look so chaotic at first that no basic stability can be seen. It’s there, but it’s not visible. We ran some experiments in such settings – specifically, primary care units – using Daily Management tools even before mapping value streams. This made patterns visible and helped teams understand the hidden basic stability in their system. We are using this approach most of the time these days, with daily management acting as a scaffolding system for basic stability that will then evolve to balance workload, allow value stream management (flow), and support problem solving.
By the way, this is why good lean coaches always look for an architect in every organization they go support. Part of their intervention consists of creating an environment where experiments can take place and people can learn, but unless there is an architect accompanying the coach and building that scaffolding holding that environment up, the whole thing will fall to pieces as soon as the coaches are out of the door.
The IOV lean journey has taught me that transforming an organization requires technique, and that it is a designer’s job before it is a leader’s. I wish I had known that years ago. So, keep this in mind, as it might just allow you to achieve your own transformation faster than we did.
THE AUTHOR
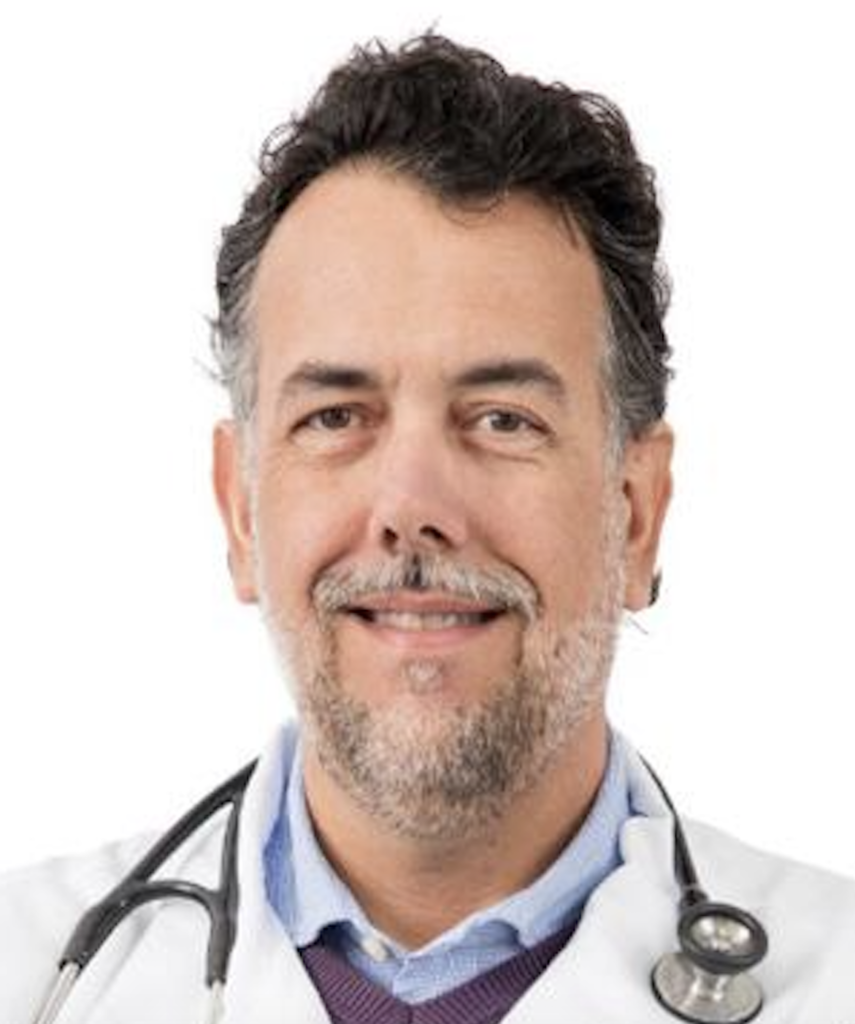
Read more
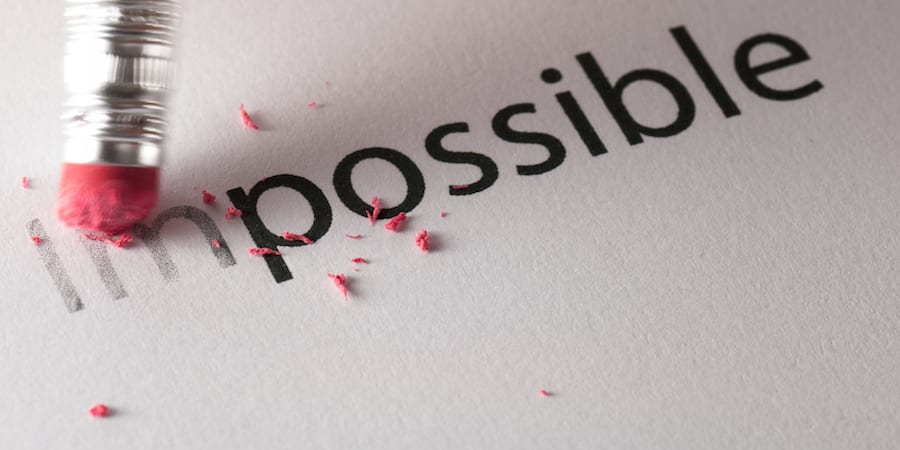
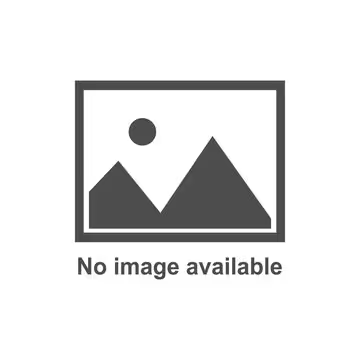
OPINION – Involvement, active listening and concern are crucial traits of lean leadership and the foundations on which respect for people is built into a learning organization, says Boaz Tamir reflecting on his evolution as a writer.

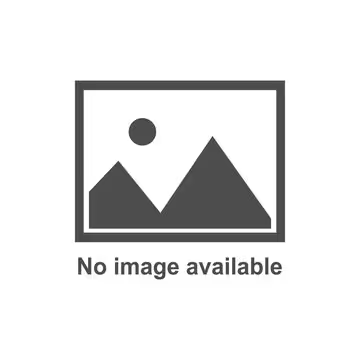
FEATURE – Sometimes you just need to get creative: as part of its flexible manufacturing model, Esquel introduced a new role on its shop floor – the “mangineer”.
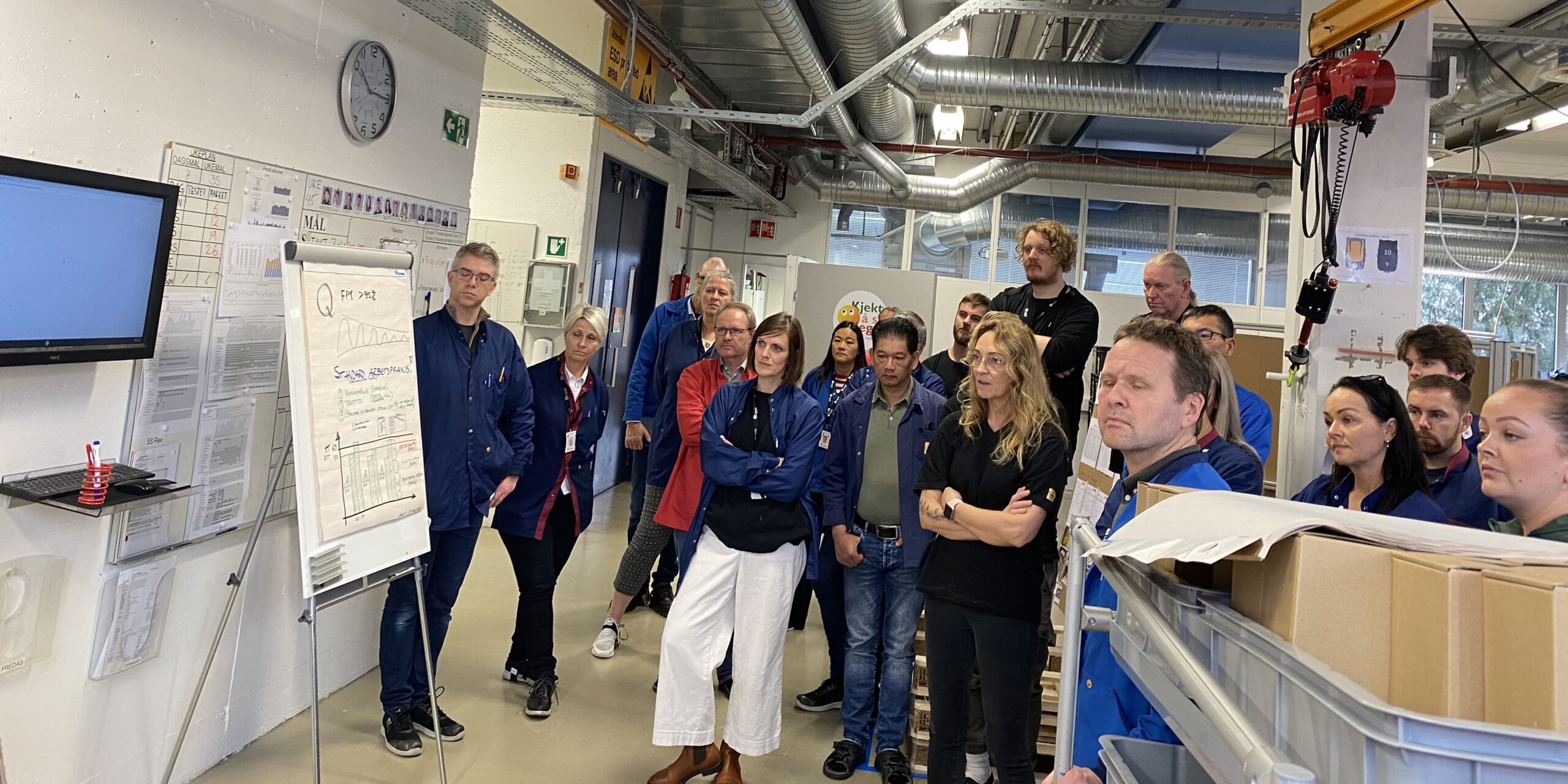
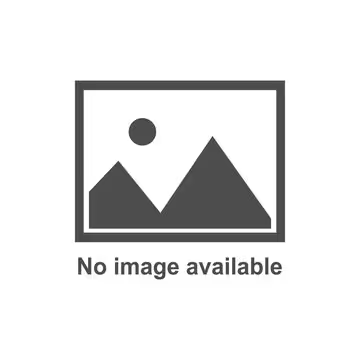
FEATURE – How Lærdal Medical was able to enthusiastically restart its lean journey with help of a good old-fashioned Kaizen Week.
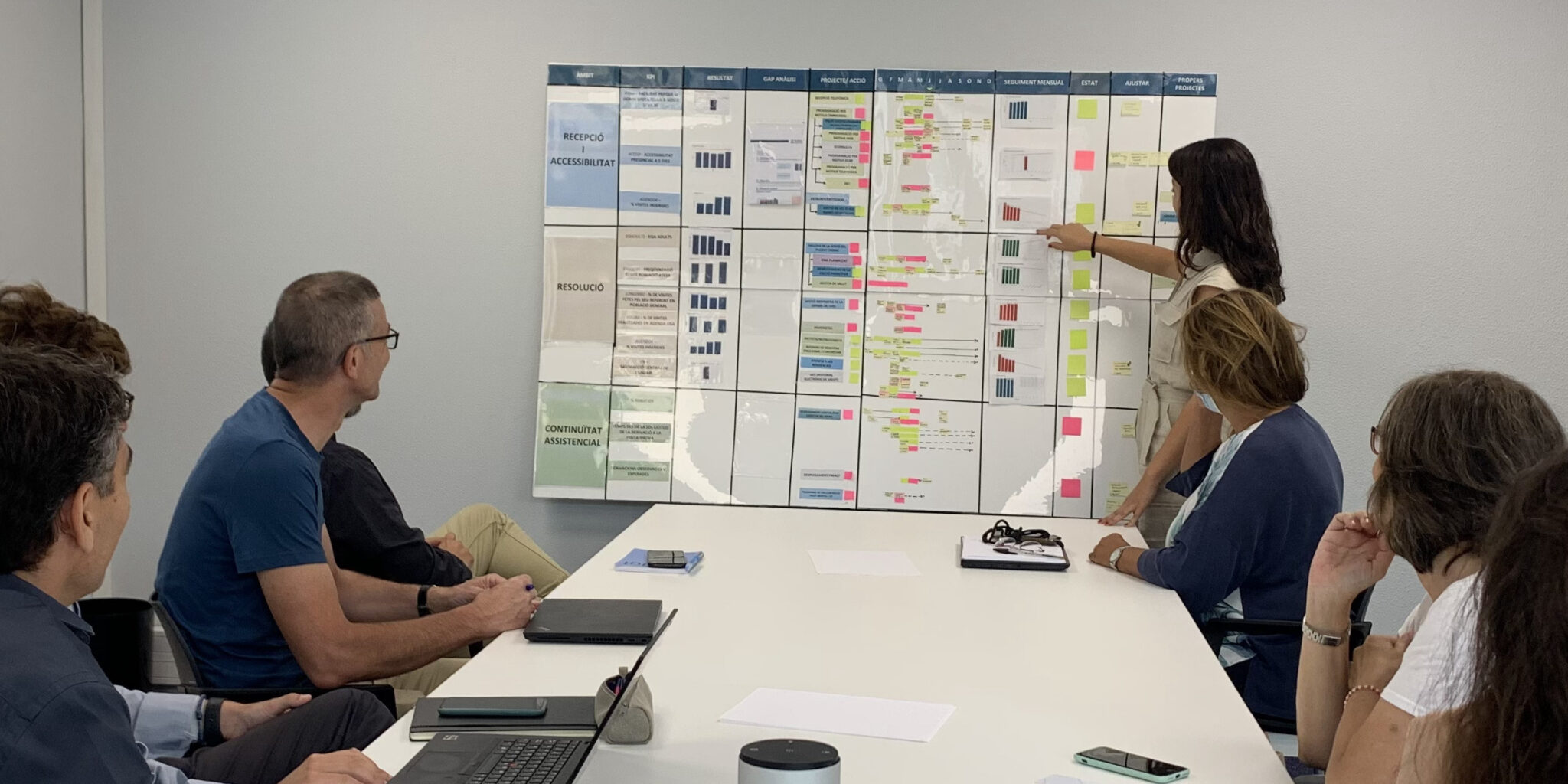
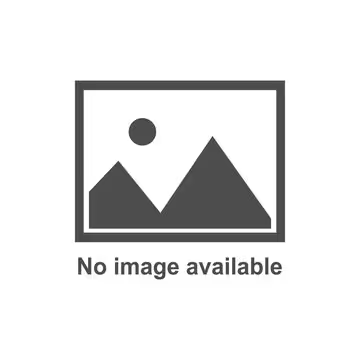
CASE STUDY – How do you give hundreds of primary care units the tools and knowledge they need to make improvements? The Catalan Health Service found the solution in hoshin kanri.