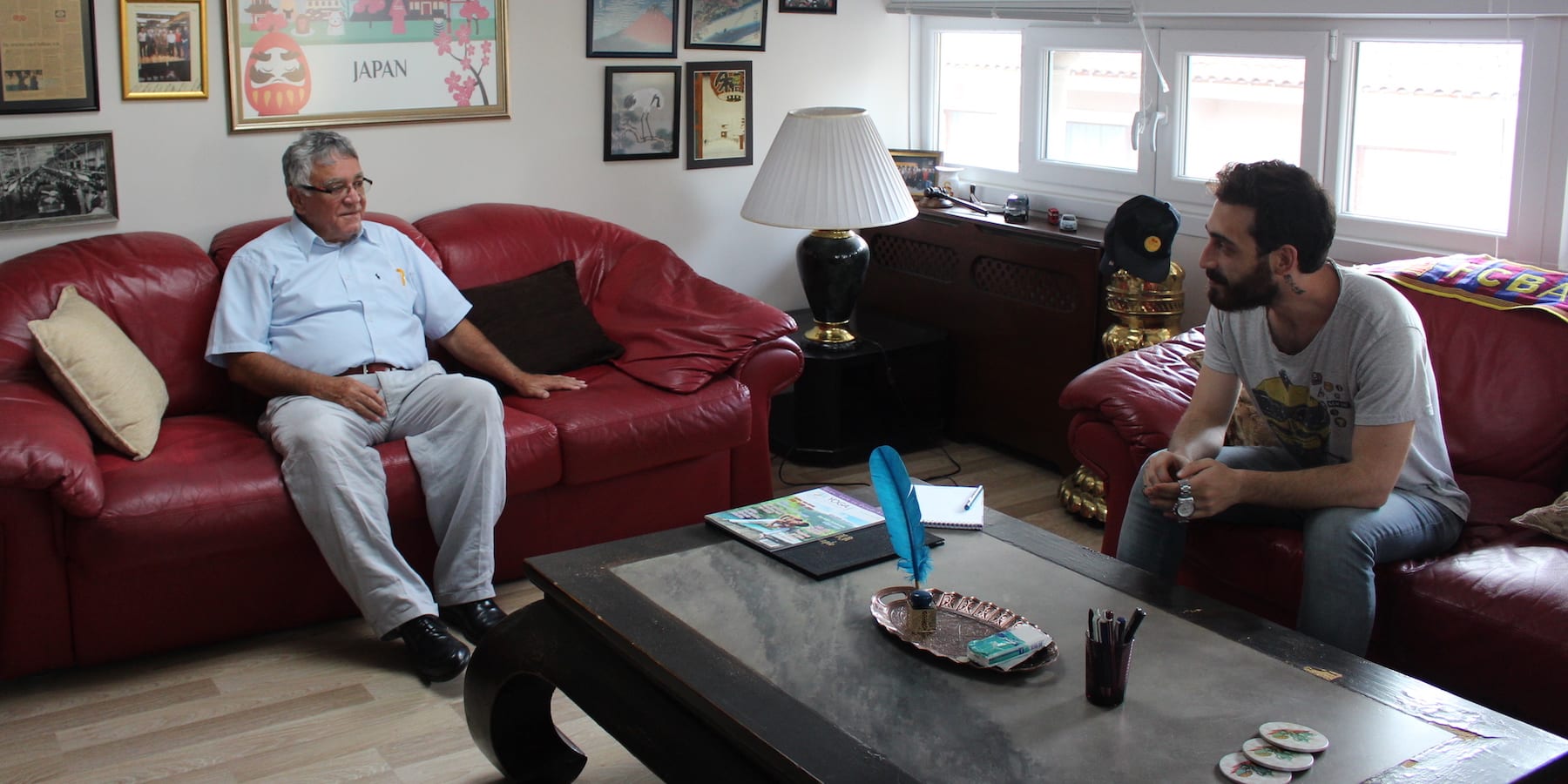
Helping Turkey to thrive with lean management
GETTING TO KNOW US – We recently visited Istanbul to learn about the work Lean Institute Turkey is doing to spread lean management in Turkey and beyond. We sat down with the institute’s President for a chat.
Interviewee: Yalcin Ipbüken, President, Lean Institute Turkey
Roberto Priolo: Thank you for hosting me this week, Yalcin. I have been very impressed with the work of the institute supporting lean transformations here in Turkey. It is clear to me that your main focus is on enabling lean learning within organizations, which doesn’t surprise me given your background. Can you tell us a bit about it?
Yalçin Ipbüken: You are right, knowledge sharing has always been a critical part of my work. I founded Lean Institute Turkey in 2002, but have been involved in organizational learning and improvement for much longer. Back in 1998, for example, I organized the first ever Lean Summit in Turkey, five years after first reading The Machine that Changed the World (which we translated into Turkish).
Over the course of my career, I have developed a lot of training materials and programs. For example, through the Koç University, I once developed training material in English for countries from the ex-Soviet bloc to help them to boost trade and improve land transportation in the region (a project funded by the US State Department and the World Bank, which later praised it as a First Class Example for its initiatives). Around the same time, I developed educational material for “Becoming Citizens”, a program for Turkish not-for-profit organizations. Lean management, with its strong focus on learning and personal development, was always an obvious choice for me.
RP: Your understanding of lean and business improvement first developed at the Koç Holding Group of Companies. What sort of work did you do there?
YI: I spent 30 years at Koç, during which I managed projects that aimed to improve the productivity of the group’s companies. My role was Organization and Methods Coordinator, with a specific focus on efficiency in production. Over time, my team reached all the companies in the group. I eventually got to lead the group’s internal consulting division and supported its external research for new ideas and trends.
I contributed to the development of Koç Holding’s human resources capabilities and policies. This is still a big interest for us at Lean Institute Turkey, to the point that we are organizing our first Lean HR Summit.
RP: Prior to joining the Koç Holding, you worked for Tofas, the first mass producer of cars in Turkey. What did you do there?
YI: I was at Tofas (which, in fact, is jointly owned by Koç Holding and Fiat Chrysler Automobiles) for 12 years, as the company’s first Personnel and Industrial Relations Manager. At that time of political and economic uncertainty, I learned a lot about facilitating relationships within an organization. I learned, for instance, that sports bring people together and, as president of the Tofas Sports club, I established basketball and wrestling teams.
RP: Can you tell us more about the activities of Lean Institute Turkey?
YI: Over the past 16 years, we have supported over 400 lean transformations, translated 23 lean books and organized countless events to benefit the Turkish and global lean communities. Over 1,000 people have taken our Team Leadership training program and, since 2010, we have organized 11 Study Missions in Japan, from which 262 people from over 100 companies have benefitted. We are also engaged in research (thanks to our brilliant researcher Dr Ayperi Okur from MIT).
Our 36 experienced lean coaches are active in pretty much every sector of the economy, from mining to manufacturing, the service industry to healthcare. (More from three Turkish companies we are supporting here on Planet Lean in the next few weeks.) Like our LGN colleagues, we firmly believe in learning-by-doing, which is why our approach to teaching lean is based on passing the necessary capabilities to the people who carry out the work on the field.
At present, 82% of our business is in Western Turkey, with a lot of activity (as one would expect) around Istanbul and Bursa. However, we want to be active across the country and, to do that, we need to develop relationships with local partners everywhere. There are at least 10 other cities we need to establish ourselves in! Our vision is to make the whole country lean, not just a few companies. We are going to achieve that by engaging with SMEs and by teaching lean in schools, universities and masters programs (also by placing model factories on their premises). We are hoping to get the government involved in this initiative, because we believe it can be a powerful catalyst of change. (TURQUALITY is an example of government-backed programs, which means that official backing is already a reality to a certain extent.)
RP: In your mind, how can lean thinking help Turkey, especially at a crucial time like this?
YI: There is no doubt this is a difficult time for the Turkish economy, with the depreciation of the lira hurting many businesses and consumers. Nonetheless, we are seeing that export-oriented companies are doing fine, and it is encouraging to see how lean is helping them to weather the storm. In particular, we are seeing our long-time assumption confirmed over and over again: strong leadership coupled with a lean management system makes for a competitive, resilient organization. (To support this, we are studying family businesses and how they develop from generation to generation.) This is why we expect us to get more and more work in the coming months.
Today, lean thinking is present pretty much everywhere in Turkish industry, and universities are starting to include it in their curricula. But this is not enough: we also need to focus more on lean product development, because Turkey needs patents of its own rather than buying them from other countries. We also need to reduce the lead-time for new products, which is why we brought seven people from the institute to the LPPD conference in Traverse City. Thinking that lean is just related to manufacturing is not only an outdated view; it’s a dangerous belief to hold.
RP: What do you think are the next sectors of the Turkish economy that will discover lean in the coming years?
YI: As I mentioned, lean is very mature in automotive (in fact, OEMs have already started to developed their Tier-1 and Tier-2 suppliers). I also think product development will be fundamental for the defense and aviation industries – one more reason to invest in the application of lean to engineering.
After a couple of difficult years, tourism is picking up again in Turkey. I think that the hotel and restaurant industries represent big opportunities for lean. I am hoping that agriculture will also take it on (more than 35% of Turks still live in the countryside), especially after learning about the lean farm in Indiana – a very impressive example.
The Turkish government has been investing heavily in healthcare, and I expect this country to become a destination for people looking for high-quality, affordable treatments. This is another great opportunity for the lean movement, because our national healthcare system will not be sustainable forever.
RP: The Turkish institute has played a key role in the onboarding of some of the Lean Global Network’s newest institutes. What was that experience like?
YI: It was very rewarding. I have been working with people of different cultures, religions and backgrounds for a long time (ever since I worked as the Middle East representative for the Kofisa Trading Company), which I think has greatly helped me in the support we have provided to our fellow LGNers from, among other places, Russia, Bulgaria and Ukraine. We are responsible for the network’s expansion in Russia, Middle East and Central Asia, and take this role very seriously. In my mind, the next nations to engage with to try and spread lean thinking are Egypt and Saudi Arabia.
RP: What can the Lean Global Network do to have a greater impact around the world?
YI: We need to continue to reach out to lean thinkers in areas of the world and sectors where there isn’t a lot of expertise yet. For that to happen, more experienced institutes like us need to continue to provide support and guidance to newly-started institutes, because in that startup phase there are many challenges. We have new people joining LGN all the time (we have recently brought in and coached our Ukrainian colleagues), and if we help them get started we’ll be stronger as a network.
We also need to develop closer relationships with academia around the world, if we are to develop the future generation of lean thinkers. Additionally, we need to do more to support developing countries – it is part of our mission – and to do that, we need to raise money. I think we should reach out to organizations like the European Union or the United Nations.
THE INTERVIEWEE
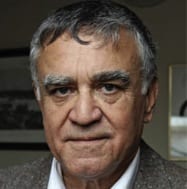
Read more
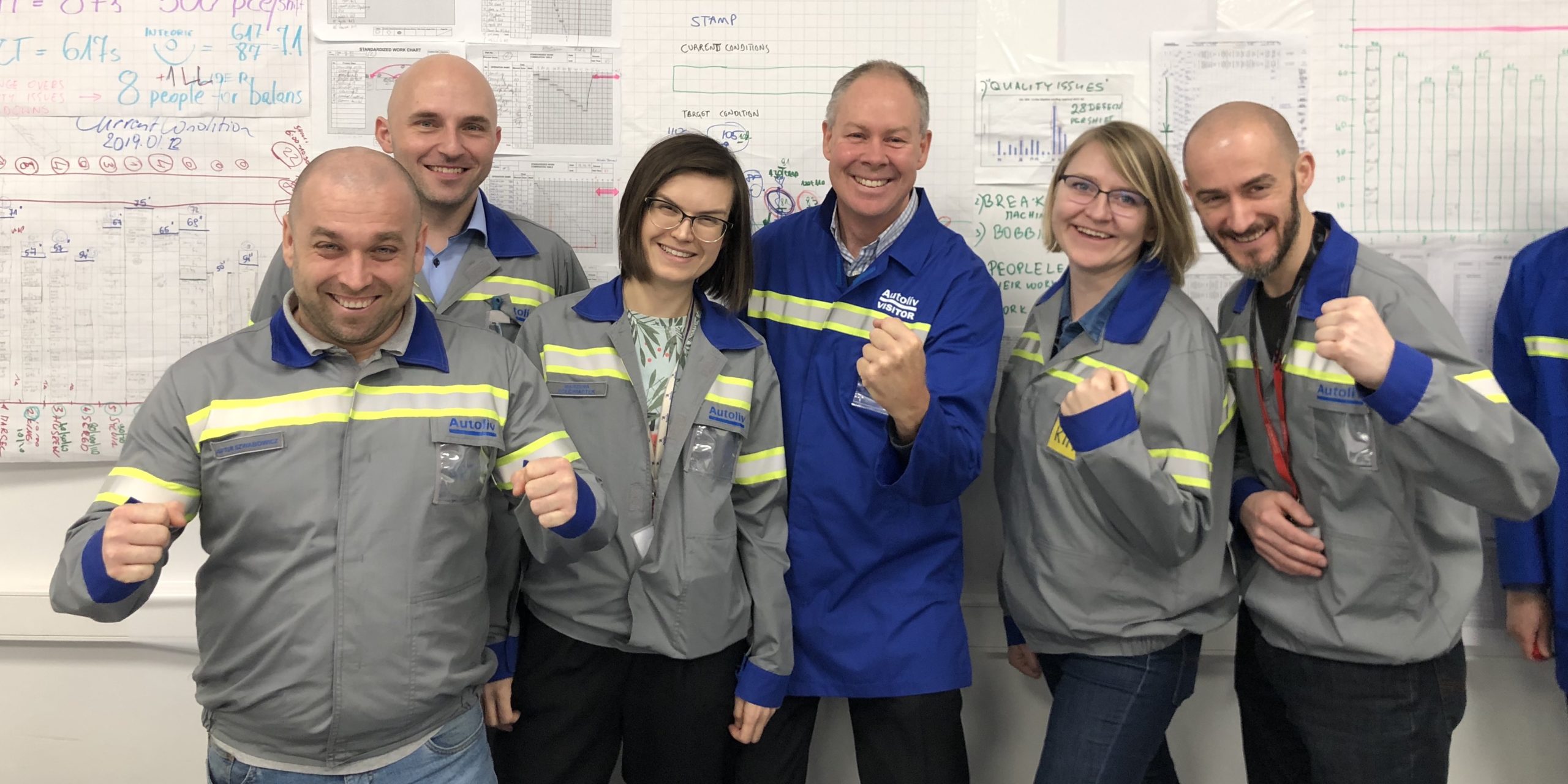
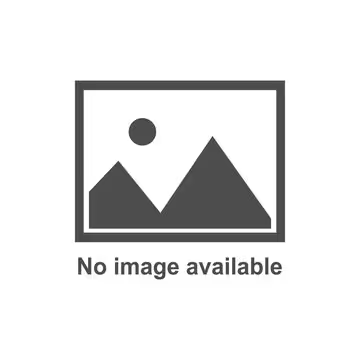
INTERVIEW – What skills do coaches need to successfully support lean transformations in the service sector? Our colleagues from Australia tells us about their experience.
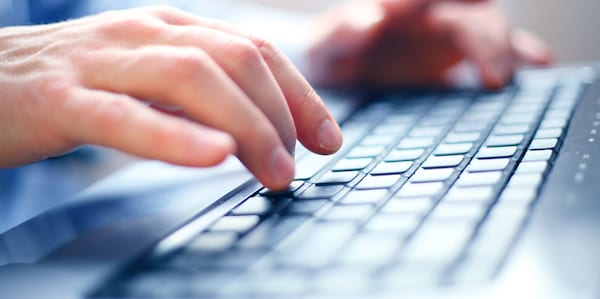
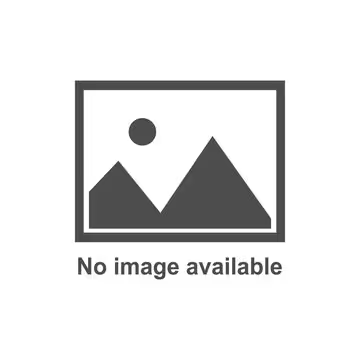
VIDEO INTERVIEW - At the Lean IT Summit, we spoke with Amazon Web Services to understand what type of flexible and scalable IT infrastructure allows organizations to be innovative without breaking the bank.
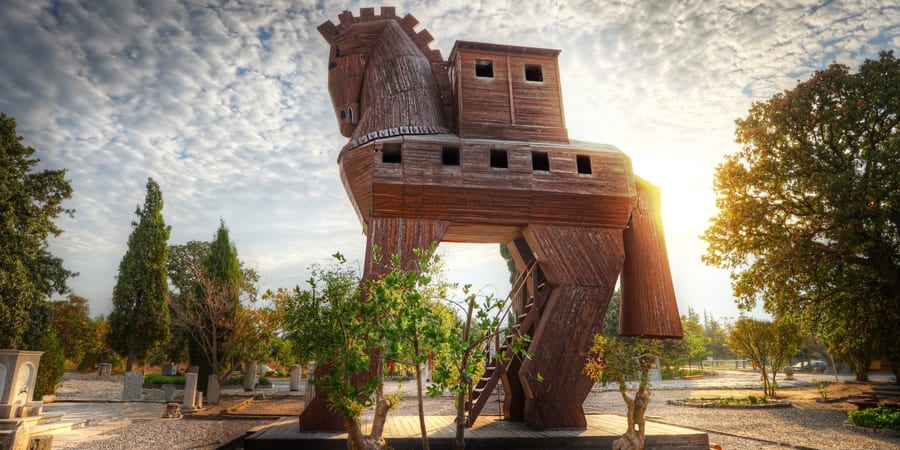
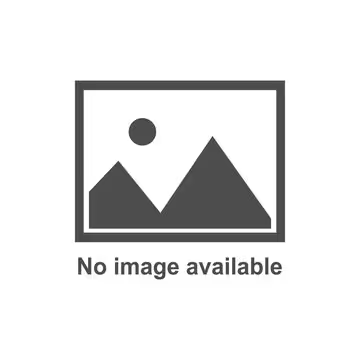
FEATURE ARTICLE - Sometimes, introducing lean thinking in an organization can make you feel lonely and hopeless. This article, which draws on the author's experience working with a chain of supermarkets in Siberia, offers some tips on what to do to start off a lean transformation.
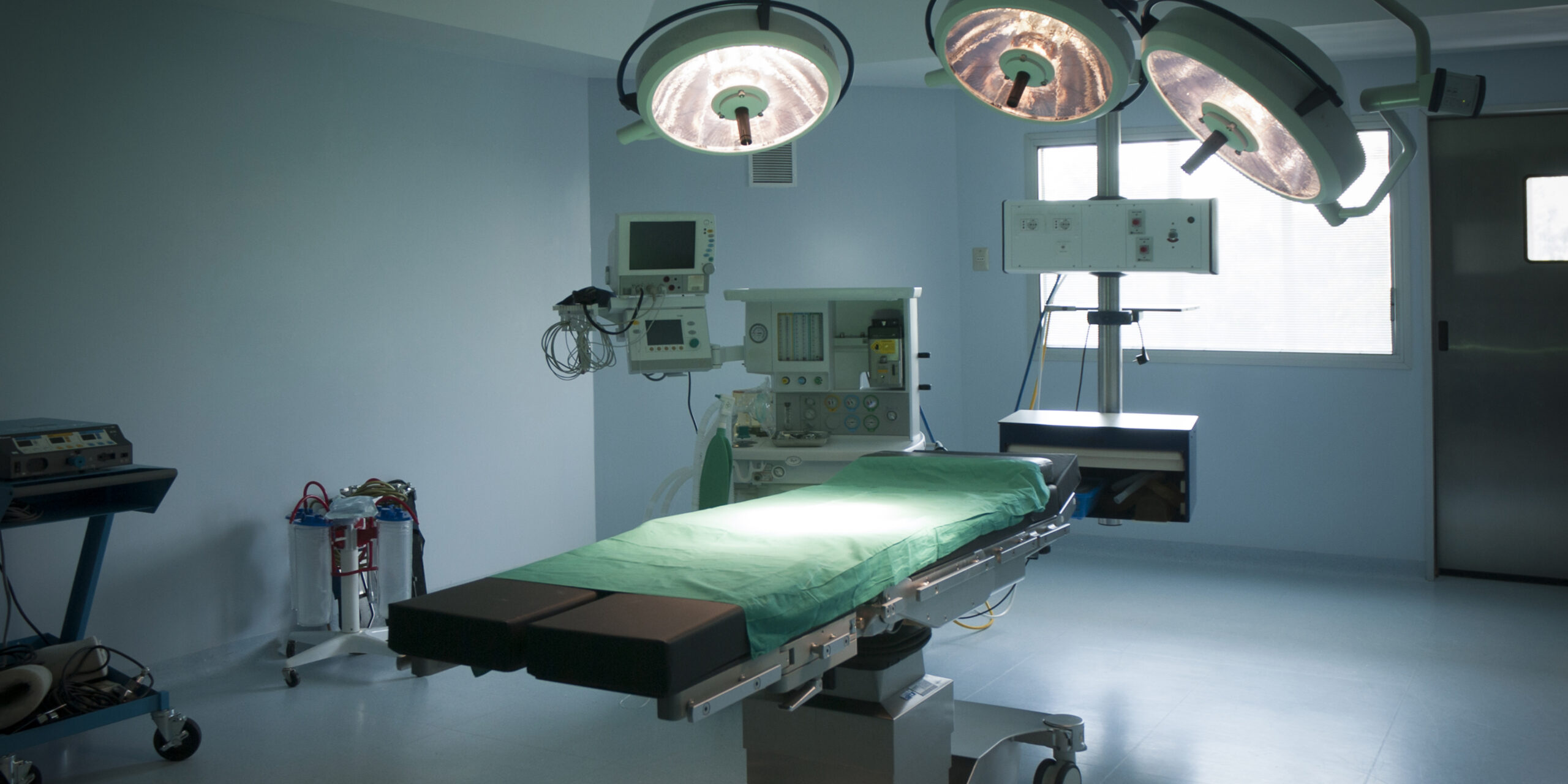
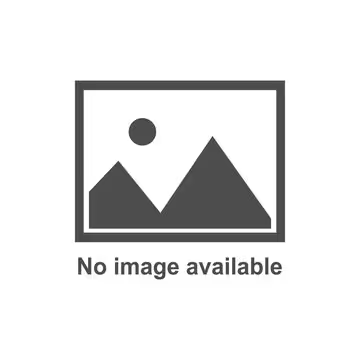
FEATURE – Lean healthcare is new to China. The authors share some examples of improvements projects taking place in Chinese hospitals, which they hope will inspire more organizations to take lean on.