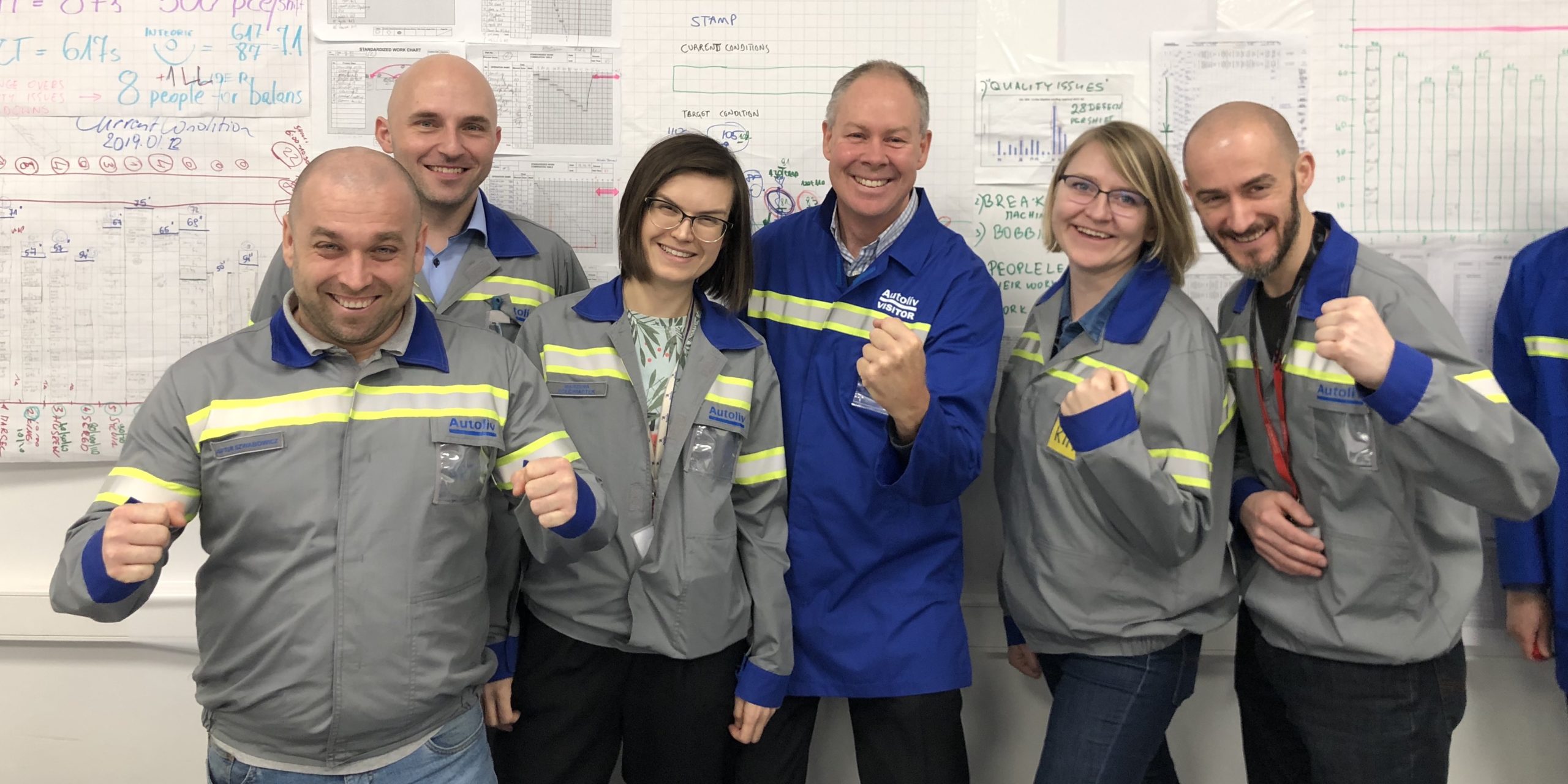
Supporting the Australian service industry
INTERVIEW – What skills do coaches need to successfully support lean transformations in the service sector? Our colleagues from Australia tells us about their experience.
Interviewee: Alister Lee, President, Lean Enterprise Australia
Roberto Priolo: What is the current situation with lean thinking down under?
Alister Lee: Lean thinking and practice has spread into most sectors in the Australian economy. The original stronghold of manufacturing has been declining in employment over many years and that’s culminated in the automotive industry leaving. Toyota was the last carmaker to cease production, in October 2017, and that was a big hit for the lean movement – many people gained insights through visits and interacting with Toyota people. The upside is that we now have ex Toyota employees who are taking their knowledge and spreading it to new businesses and sectors.
RP: What is Lean Enterprise Australia working on at the moment?
AL: Inevitably, our work has reflected the transition from manufacturing into the service industries – banks, insurance companies and, with Denise Bennett’s expertise, healthcare and local government. For example, we are coaching senior and middle-level executives in problem solving at Knox City Council, in Melbourne. Other sectors we work in are food & beverage production and mining.
We have just started a collaboration with digital company REA Group. We took part in the latest of their hack days (events that aim to generate creative ideas that can benefit society), which was themed “muda”. The company has been a pioneer in Agile practices and we will coach their teams to develop their problem solving and process improvement capabilities. This is an exciting project for us!
Another interesting trend is more SMEs are taking on lean thinking and practice. In our experience, they can make good progress particularly when they are supported by strong leadership. Working with small businesses is quite enjoyable: they are more flexible, free from the constraints of bureaucracy and politics, and people tend to be engaged. With many of them going through their startup phase, I find them to be very open to taking on new ideas.
RP: What are the differences between manufacturing and services when it comes to introducing lean thinking?
AL: It is a joy to prove over and over again that lean principles work just as well in services as they do in manufacturing. In fact, some of them work better: for instance, seeing the work flow is quite hard in the service industry, which typically makes visualizing the work and mapping the processes very impactful.
Another thing to have clear in mind is the concept of customer value, which in a service environment is slightly different. We know that value is in the eye of the customer and that every customer values different things. Hence, it is critical to spend a bit more time understanding the customer and making improvements that have a positive impact on them: after all, in services, we are not only designing own internal processes, but also the process that the customer experiences. I feel there are great opportunities to advance lean thinking and practice in this sector.
RP: What’s your background? Tell us about your career, please.
AL: For most of my career, I worked in the automotive industry. My first exposure to lean was reading The Machine that Changed the World on a plane and I remember being intrigued but skeptical. I was doubtful that the improvement and management methods developed by Toyota in Japan would work in Australia, where employees are often willing to challenge management initiatives. Surely, I believed, this would make it harder for lean to take root. I now stand corrected: challenging things is a key element of lean!
The manufacturing company I worked for had Toyota as a customer. We were doing OK on quality and delivery, but they wanted us to lower our costs. We eventually let them help us (somewhat reluctantly at first, I must say) and, from the very first kaizen event they ran with us, I was convinced. They worked with one of our best-performing teams and many small step improvements done in a short space of time had a significant impact on their quality and output. That, to me, was the first real taste of lean thinking. It’s when I realized how impactful it is to get people together, find ways to simplify the process, and empower the team to continue improving.
In 1998, I was transferred to the US, tasked with spreading lean principles and techniques across different plants. Working with teams all around the country and sharing our stuggles and successes was a fantastic learning experience for us. After a couple of years, I took on an operational role in a plant in North Carolina. This proved to be an initiation by fire as we had a major quality issue shortly after I joined, which threatened to stop our customers production line. With corporate breathing down our necks and in firefighting mode, my team focused on finding the root cause of the issue. Some intense problem solving averted the crisis but it was nearly a career-ending event that taught me to never jump to conclusions, no matter how urgent the situation is. During my time in the US I was fortunate to have a number of great mentors who taught me the importance of people development, an understanding that guided me as I went back to Australia as CEO of the company.
My time as CEO was a wonderful but intense experience. It was a great opportunity to drive engagement and improvement from the top. When I left the automotive industry in 2006, I took a year off and travelled with my family around Australia, living under the stars. While in the Outback, I had a lot of time to reflect and I realized that I wanted to be a lean coach and develop others as my mentors had developed me. And that’s what I have done for the past 12 years. At first, I went out on my own. I called my company “Lean Experience” (my wife often joked that it was called “Lean” because there was very little money coming in). During my time working in automotive, I had developed a relationship with Peter Walsh at Lean Enterprise Australia and we started working more together. Today, I co-run the institute with Denise Bennett, a true pioneer in taking lean to new environments. (Read Planet Lean’s profile on her, here).
RP: What’s the biggest challenge for LEA at the moment?
AL: The challenge for us in Australia is to support and strengthen the lean community as we expand in service. Lean applies to knowledge work and we need to become more relevant in the digital space, and to be more aware of the strength we can add to approaches like Agile. There are many improvement methodologies that share similar principles and practices, and we are trying to forge alliances with people using them (a case in point being our work with Nigel Dalton at REA Group). I think that, as a lean movement, we need to be more open to others and learn how they work. Whenever we do, we immediately see the underlying lean ideas guiding them!
RP: What are the benefits of belonging to the Lean Global Network?
AL: For me, it’s the ability to learn from others around the world who worked in all sorts of different environments. We are only just starting to tap into that potential, with group activities like a Jishuken week we just had in Poland.
For our institute, there is great benefit in being part of a large not-for-profit organization. The LGN’s mission to share knowledge and co-learn with lean organizations around the world really resonates with our customers.
THE INTERVIEWEE
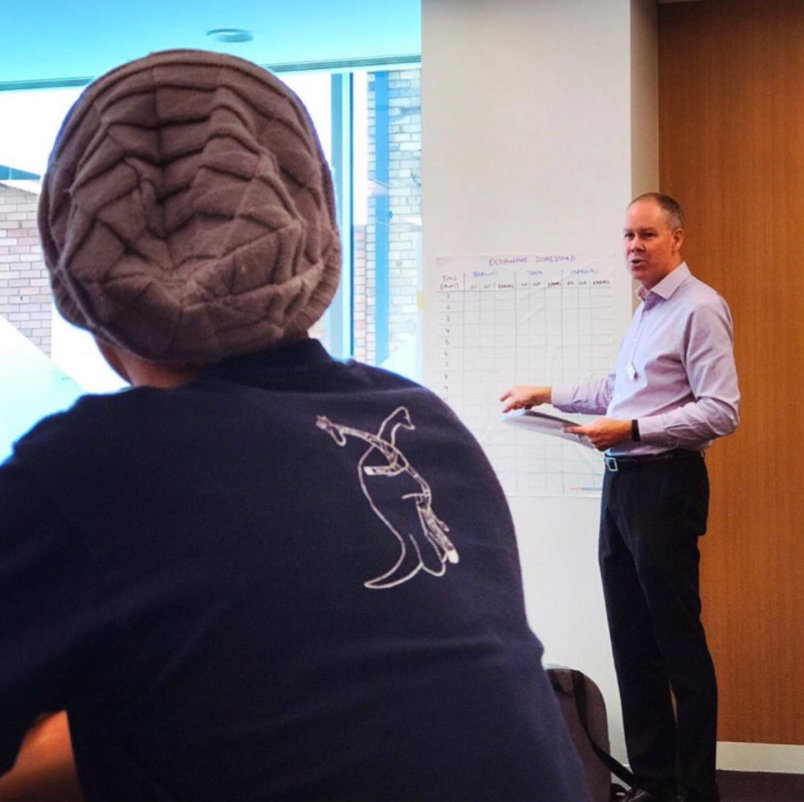
Read more
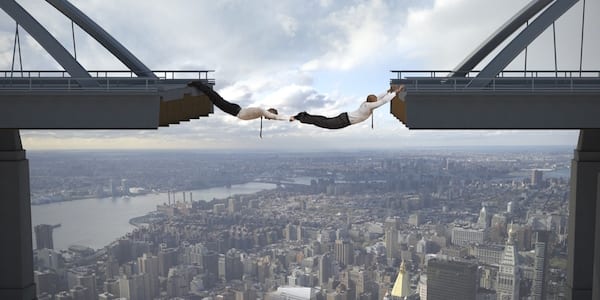
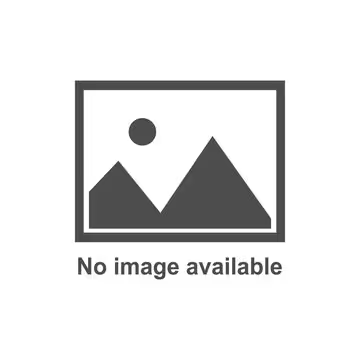
INTERVIEW - Like many other improvement methodologies, LeanUX shares a lot of principles with traditional lean. Yet, the two communities don’t know a lot about each other. We ask an expert to bridge the gap.
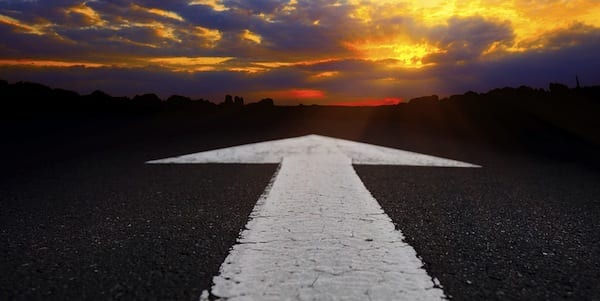
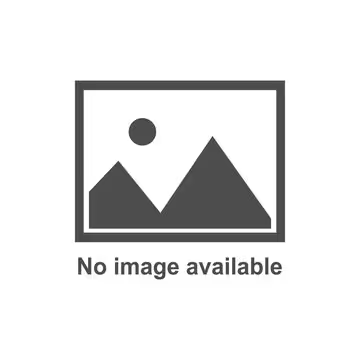
FEATURE - The author looks back at his many years with Toyota and shares some of the key lessons he learned along the way. What a unique company!
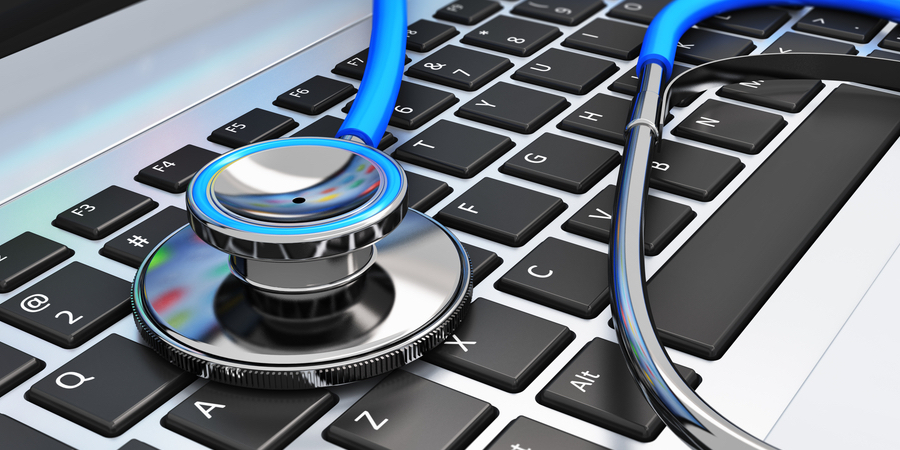
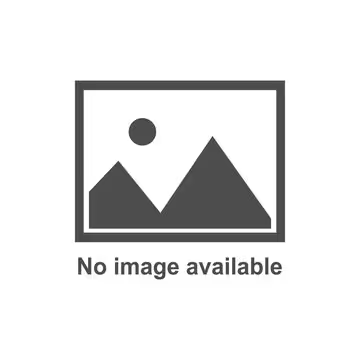
OPINION – The team at Instituto Lean Management in Barcelona comments on recent news from the Catalan healthcare sector and reflects on lean sustainability.
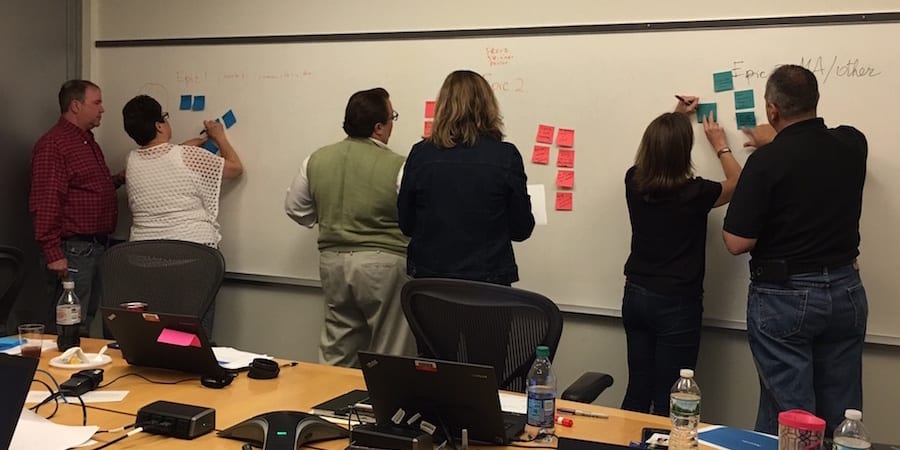
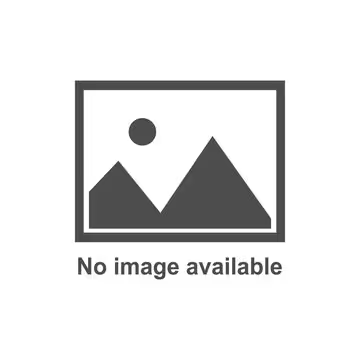
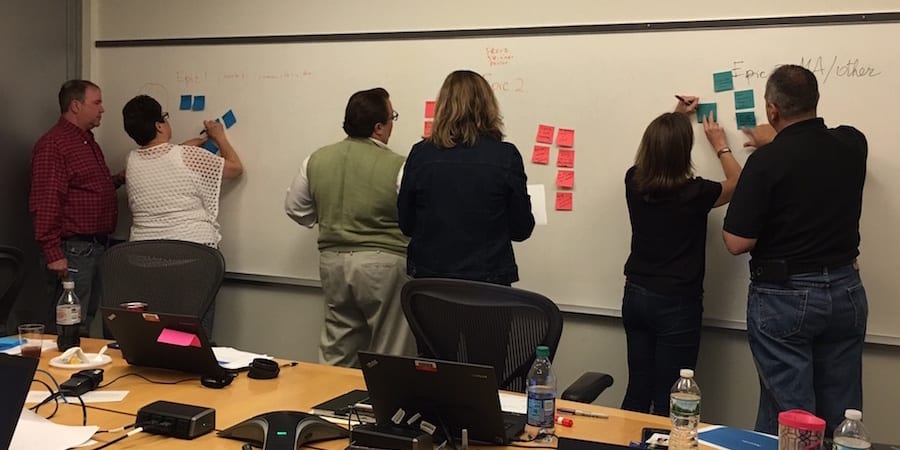
INTERVIEW – Business services company Dun & Bradstreet learned that the best way to tackle organizational challenges is using a combination of agile, lean startup and more traditional lean principles.