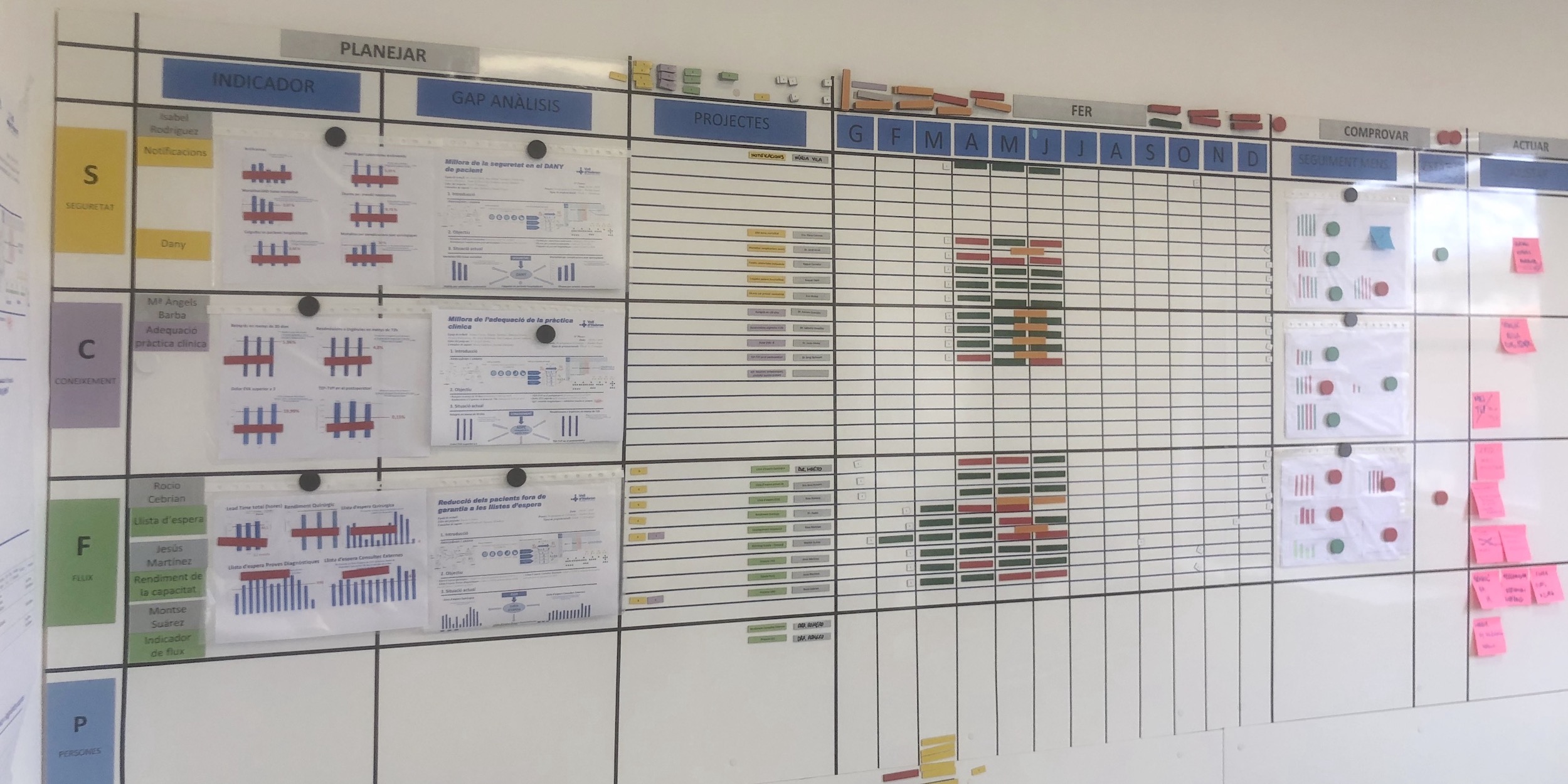
Through hardship to the stars
CASE STUDY – Catalonia’s largest hospital is undergoing a successful transformation – supported by pioneering hoshin experiments – that has already turned it into a poster child for lean healthcare in the region.
Words: Vicenç Martínez Ibañez, former CEO, and Antoni Campos Rubiño, former Process Coordinator-Strategy Deployment Director, Hospital Vall d’Hebron – Barcelona
In Hospital Vall d’Hebron in Barcelona (HUVH), we have engaged in process improvement since 2001. Over the years, we experimented with different approaches – including the EFQM Excellence Model, a traditional form of process management – and tried to get people engaged in the change we were trying to bring about, but our work was mainly focused on processes.
In 2012, the same year Vicenç became CEO of the Hospital Trueta and Hospital Santa Caterina in Girona, northeastern Catalonia, the book Transforming Health Care –telling the story of the lean transformation of Virginia Mason Medical Center – inspired us to engage with Instituto Lean Management to learn about lean thinking. We were still searching for our own way to transform the hospital.
The following year, we came across a study by the Karolinska University Hospital sharing the results of an experiment which took place in four of the hospital’s departments. Each of them had applied an improvement methodology – EFQM, lean, six sigma and another American quality approach. The study had concluded that lean thinking was the easiest approach for doctors to grasp. We were both trying to bring lean management to healthcare, and we both had a year of lean under our belts, so we decided to go to Stockholm to see what they were doing.
For the following two years, we were able to achieve tangible results in Girona. The changes positively impacted the daily life of our employees and created better outcomes for patients.
In February 2015, when Vicenç became CEO of the Hospital Vall d’Hebron in Barcelona. There, together with Dr Anna Ochoa and other members of the Board of Directors, we created a great lean team that ultimately allowed us to successfully transform our 9,000-staff hospital.
What we had learned in Girona was critical to the success of our endeavor at Vall d’Hebron. Those lessons included the fact that lean is extremely powerful in creating and managing better patient flows, that we should avoid Japanese words because they put people off immediately, and that lean cannot be brought to one area of the hospital but not another (that’s why they call it a holistic approach, I suppose).
When we introduced lean in Vall d’Hebron, therefore, we decided to transform the whole organization. We also translated the Japanese concepts into something our people would find easier to understand and digest: for example, instead of “A3s”, we talked about “posters” and instead of “hoshin kanri” we said “strategy deployment”.
The model we deployed – though based on the universal lean principles – was customized to our needs. We believe this is a fundamental step in any hospital transformation, because with lean one size never fits all. But the truth is that if we could turn around Vall d’Hebron – Catalonia’s largest and most complex hospital – there is no reason why any other hospital can’t be transformed as well.
THE PATIENT AT THE CORE
Throughout our transformation, we have never lost sight of our slogan, our Northern Star: patient first, always. To achieve a cultural transformation, you need everyone rowing at the same pace and in the same direction, for which you need a magnet orientating everyone towards the same goal – that magnet, for us, was the patient. This has been the keystone of our lean journey.
When we first started, surveys revealed that patients confided in us when it came to nurses and doctors but got lost in our processes as soon as they were left alone. We had very inefficient patient flows, both in getting to the hospital and in moving around it. It wasn’t uncommon for a patient to be admitted for a day or two because they lived far away and, upon showing up for their appointment, they found out their doctor was actually away at a conference. Achieving good patient flow became the key focus of our lean efforts.
For the service you provide to be good, you need to constantly assess and review the efficiency of each operation and constantly fight variability. Before we started, at Vall d’Hebron you’d find a bunch of different ways to perform the same procedure or organize a drawer. We worked hard to reorganize the processes across the hospital, so that people can now move from one area to another and expect the same way of doing things as in their own.
Finally, we placed a lot of emphasis on safety. We implemented a system of alerts for safety accidents, which was meant to help staff discover and fix the problem, but also highlight it and analyze the reason it occurred to ensure these wouldn’t present themselves again.
It’s important to mention that our transformational model isn’t only based on lean thinking. We incorporate other elements, tools and approaches – from clinical knowledge (to capture best practice in the provision of care) to kata and Design Thinking (to craft the best possible relationships among different professionals and better professionals and patients). Whatever tool or method we decide to deploy needs to have two characteristics: it needs to be effective and it needs to be simple. To transform a culture, you need simple principles and practices and repetition; complexity is an impediment to both.
That’s why, as we mentioned, we don’t use the lean jargon (“pace” instead of “takt time”; “process map” instead of “value stream map”). For us it was important that our people realized the transformation was for them to have an easier life at work so that they could provide better care to our patients. With this in mind, you can’t expect clinical staff to adapt to engineering lingo; it should be the other way around.
Another important element in the hospital’s transformation is the multi-disciplinary nature of the lean work. For one, the Kaizen Office is made up of nurses and doctors, who have joined forces with engineers. This reflects an attempt to follow the horizontal orientation of processes (which move across silos and departments) by bringing together people from different areas who are involved in the care of a specific type of patient, whom we strive to follow from the moment she steps into our hospital all the way to discharge. And we have also added the patient to the mix, engaging them in the creation of an initial improvement suggestion (an approach we borrowed from Design Thinking) – their input and feedback are fundamental – which is then given to the improvement team, who will work on the actual kaizen.
An important contribution to the creation of this collaborative culture was given by what we call “cross-functional empathetic observation” (which combines elements of lean and Design Thinking): we ask professionals to observe colleagues who are working in different areas or roles (like a doctor to observe a nurse or a nurse to observe an assistant doctor) to really understand the work they do. This has done wonders to strengthen our teamwork ethos.
PIONEERING HOSHIN KANRI IN HEALTHCARE
A year and a half into the transformation of Vall d’Hebron, we had increased the number of surgeries in the hospital by 10%. This, of course, meant we now needed more beds, which put pressure on the hospitalization process and led to delays in Emergency. That’s when we realized that you need to synchronize the lean work among departments and find a better way to link organizational goals with every-day operations. This meant one thing: hoshin kanri, of which Vall d’Hebron was one of the first examples in healthcare that we know of.
Hoshin brings together routine and innovation, and it consolidates teamwork. It’s where strategic planning and daily operations come together. The KPIs you track with it are used to evaluate the effectiveness of the plans you are deploying and to ensure that weekly, monthly and yearly we are working as we should.
Hoshin reflects a fundamental change that took place in the organizational culture. These days, it is organizational objectives that come down from hospital management – not directions. At lower level of the organization, people know exactly what they have to do to meet the targets that will collectively contribute to the achievement of those hospital-wide goals.
To meet their targets, people solve problems in the daily work and improve it continuously. In Girona, we used to send the experts in (from the Kaizen Office), but learned that this way people didn’t own the problems; today, at Vall d’Hebron people at the front line are encouraged to take on the responsibility of solving problems and are given the tools to do so.
Until now, problems were highlighted and solved by using value stream mapping and standardization. More recently, the hospital’s development efforts have focused on giving people more structured problem-solving capabilities through the introduction of A3 thinking.
As we reflect back on our work with hoshin, we realize how big a change it meant for Vall d’Hebron. In the past, it was experience and intuition that guided us in our decisions on what projects to open, whereas now strategy deployment gives us hard data that informs our decisions on next steps. These days, the only projects that are allowed to start are those connected to the strategic objectives we are working towards.
When it comes to hoshin, the most critical lesson we have learned is that you can’t do it without creating stability in your processes and orienting everyone towards the same goal. If we had explained it at the beginning, we wouldn’t have succeeded. With all things lean, you almost have to wait for people to ask for the next advancement in the journey – when they have improved to a point that they are stuck and need to move to the next level. So, hoshin can’t be done without having gone through waste elimination or without interiorizing PDCA.
We could have started off with hoshin, leaving the hospital the way we found it – inefficiencies and all – but we wouldn’t have gone far. Sure, we would have improved a bit (starting from chaos, every improvement seems huge) but we would have never become a truly lean organization. It is through the mistakes we made along the way that we learned all the thing we need to know to make hoshin work for us. Our struggles and the solutions we found the problems we encountered is what led us to where we are today. It’s the beauty of lean… you can only learn it by doing it!
THE COACH COMMENTS
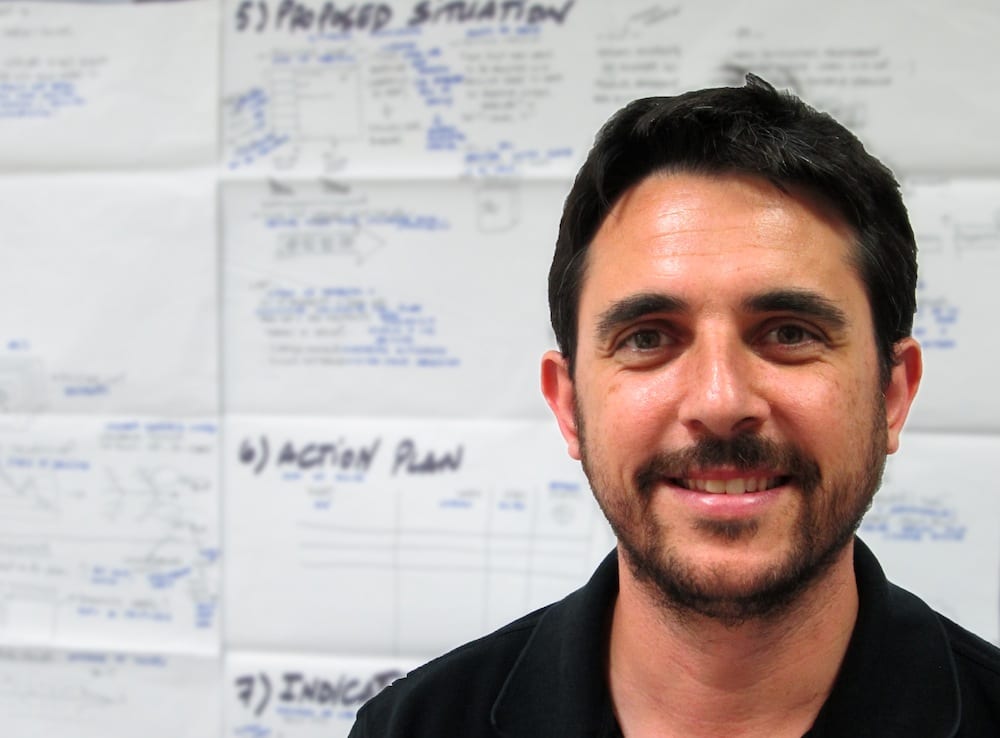
I had the opportunity to support the team at Hospital de la Vall d’Hebron as they designed and implemented their Hoshin Kanri. On the first day I got together with Vicenç and his team, it was immediately clear that the challenge was to apply a management system tied to the organizational strategy (as they said, “just like the best automotive companies do”). I was surprised by the clarity of their requirement and the determination of the team to push forward with this undertaking. My experience was in businesses of a different nature – predominantly in industry, occasionally in the service sector – but never in healthcare. It was a big challenge.
First, we had to find a framework comparable to the classic SQVCP (Safety, Quality, Volume/Service, Cost, and development and involvement of People) that would apply to healthcare. Following a number of working sessions, we came up with a framework carrying Safety (of patients and employees), Knowledge (tied to the adaptation of clinical practices and how these could be improved by applying the knowledge) and Flow of patients within the clinical processes. Later on, we would add cost management against Budget, teaching and investigation (so important in healthcare) and, finally, the development and involvement of people in managing the system. This way, the resulting framework would become SCFCDP.
The healthcare sector has a deeply-rooted culture of managing by KPI, which makes information readily available. The challenge for the team was to focus on just a few and manage the organization using them. Defining the granularity and bottom-up structure of the KPIs was also part of the work to be done, to ensure an alignment between the high-level goals of the hospital and the combined improvements taking place at department/process level. It was exhilarating to be able to work with doctors, nurses and engineers to figure this out and adapt and apply Hoshin Kanri to the healthcare sector. A few more working sessions led to the creation of a board that would be used to manage around 20 high-level indicators, establish the priorities for the current year, and spell out the main projects to open in the organization (these were managed with “posters” – that’s what A3s are known for at Vall d’Hebron).
In an unforgettable inaugural session organized for those who would run the system, Vicenç was clear: “Everything starts with policy deployment” (without mentioning the Japanese word hoshin, to ensure everybody would understand the concept). Thanks to the board and the management system related to it, it became easy to understand what projects were being prioritized, what their status was and how the respective KPIs were doing.
The application of the methodology, like the management of the associated systems, was the same as the previous experiences in other sectors. The hospital had to adapt them to the “new” system of indicators SCFCDP, but there was no other change aside from that. I had the chance to bring together people from the hospital deployment and people from industrial or service projects and they understand each other perfectly, thanks to the similarities of their strategic management.
I would like to thank Vicenç and his team for the opportunity to learn so much during the design and execution of the Project, and encourage the Vall d’Hebron hospital to continue improving day after day using its powerful management systems.
Néstor Gavilán, Instituto Lean Management
THE AUTHORS
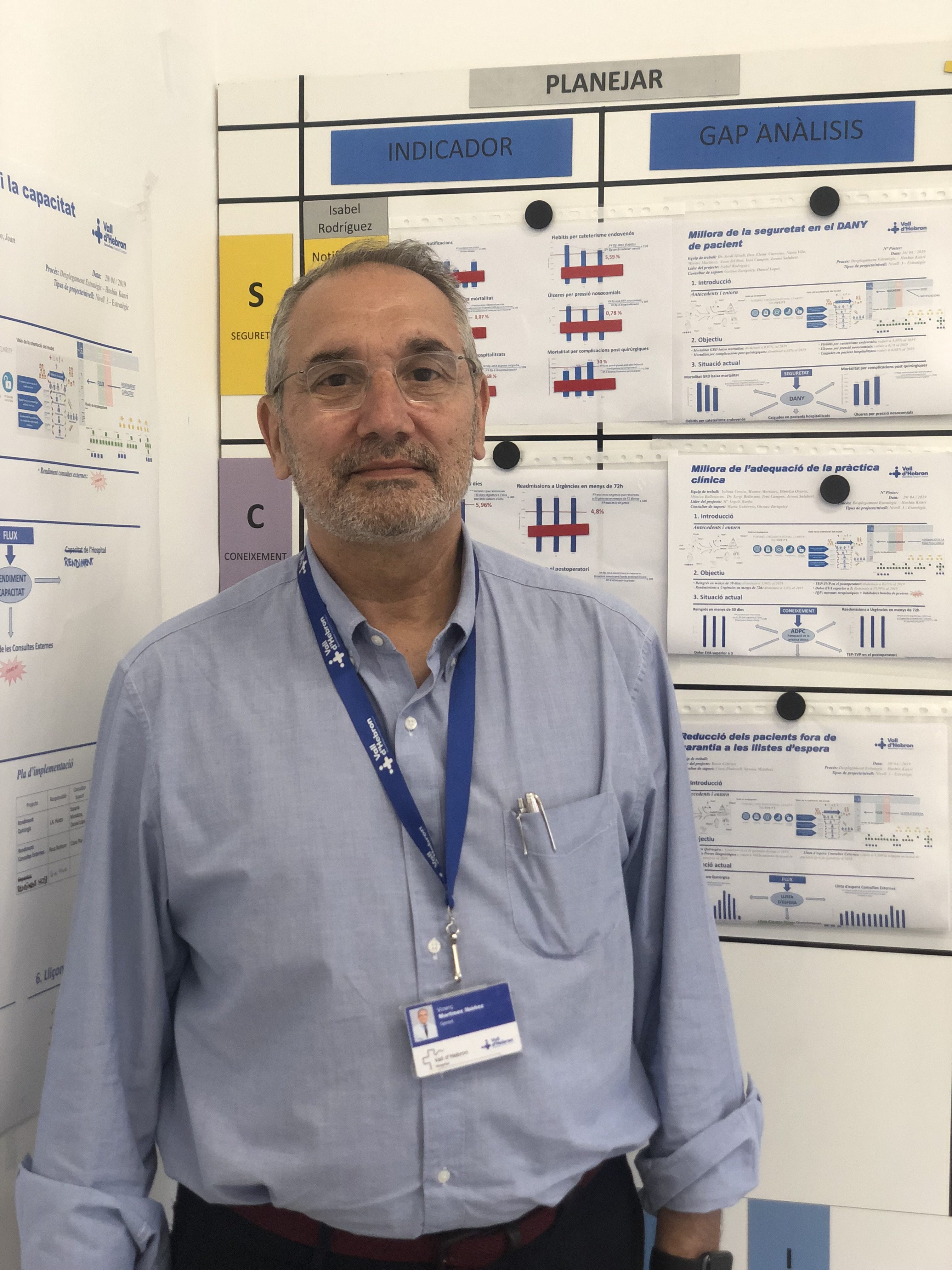
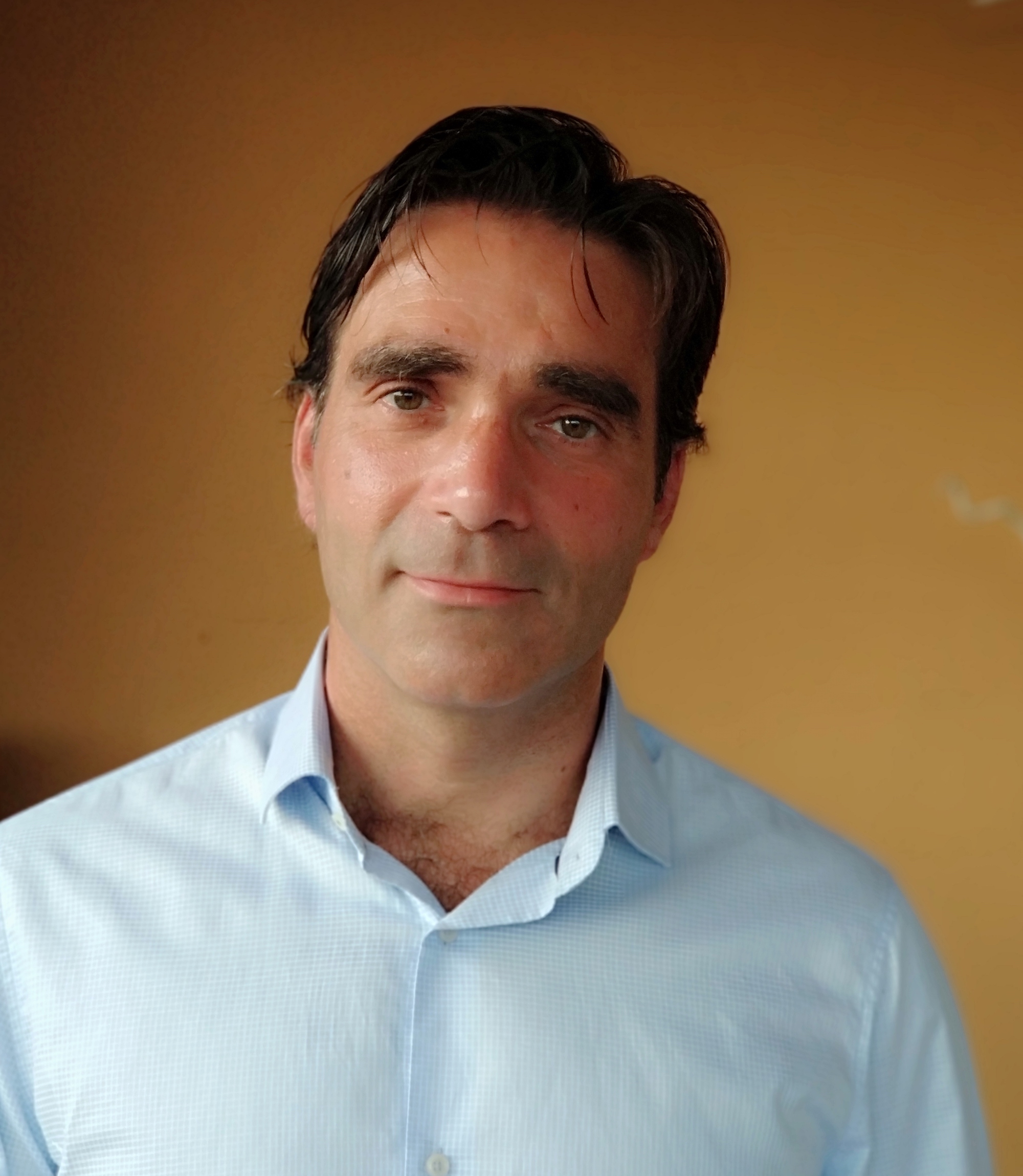
Read more
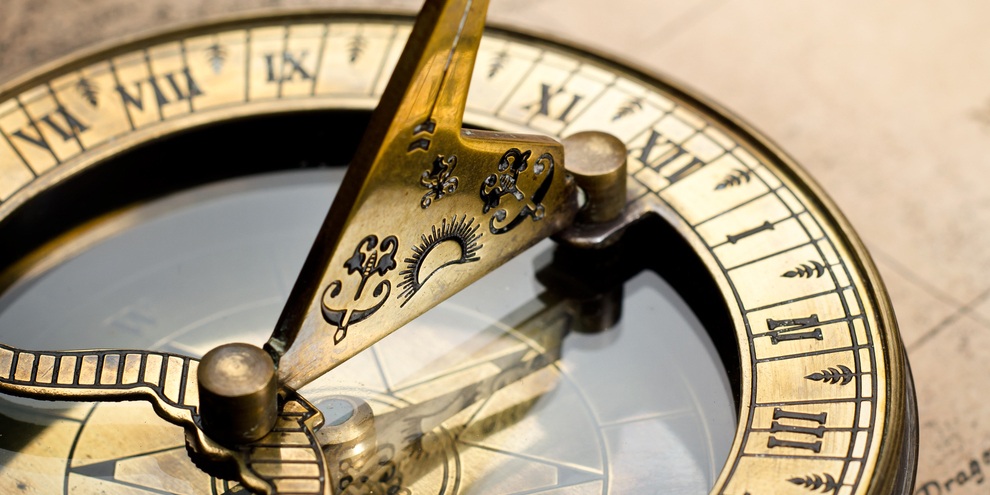
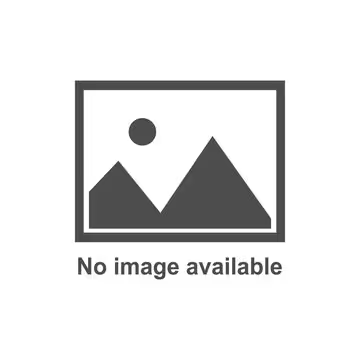
INTERVIEW – The extraordinary events of the past year have encouraged lean organizations around the world to ask deeper questions about purpose and value creation, says Josh Howell.

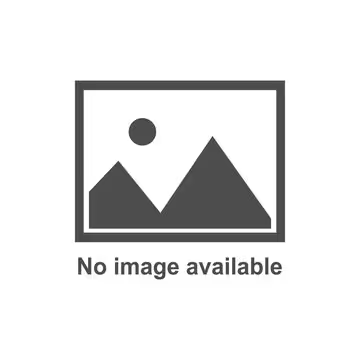
INTERVIEW – PL speaks to one of America's leading experts on the Toyota Production System about Toyota's unique approach to integrating product development with all other functions in the business.
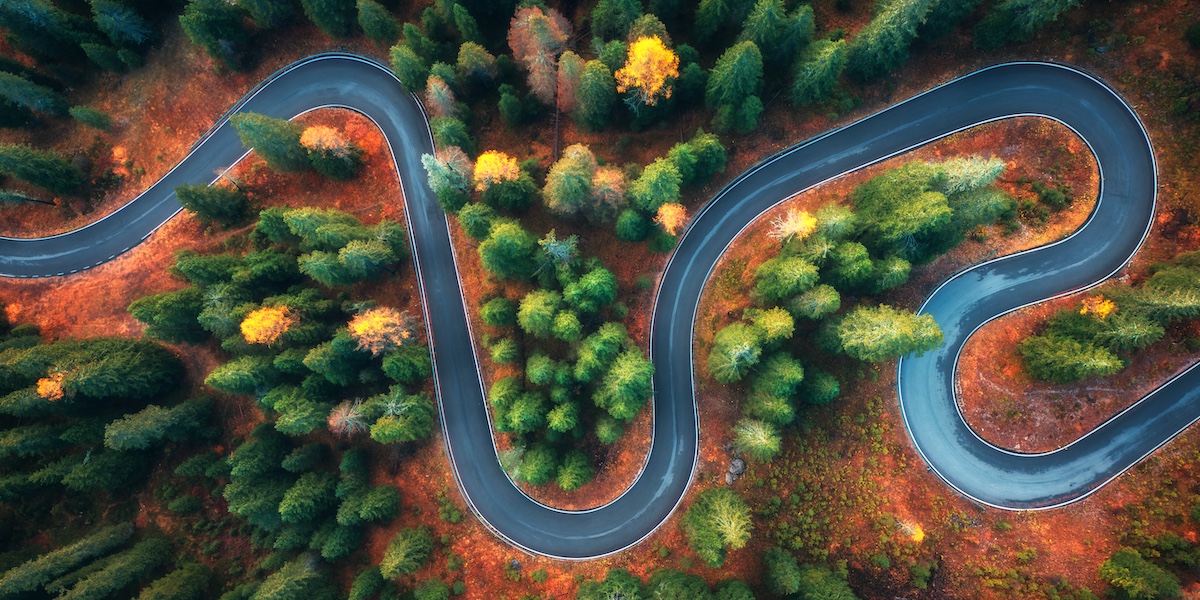
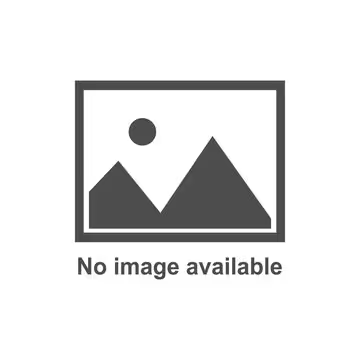
FEATURE - Projects or programs? The authors discuss why Lean Thinking should go beyond piecemeal operational improvements, as a transformative strategy that balances today’s demands with future adaptiveness.
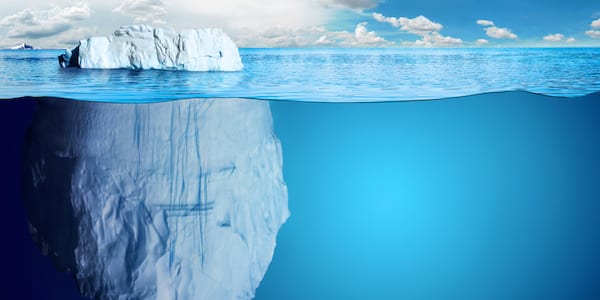
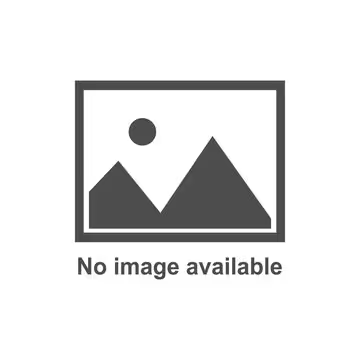
ARTICLE - What is lean? We all like to think that we know. This personal story reminds us all of how elusive the methodology can be, and how determined a practitioner has to be to fully grasp it.