
Discussing product development with a leading TPS expert
INTERVIEW – PL speaks to one of America's leading experts on the Toyota Production System about Toyota's unique approach to integrating product development with all other functions in the business.
Interviewee: Lesa Nichols, Toyota Production System and Leadership Coach
Planet Lean: The Lean Enterprise Institute recently started an initiative to bring together the Lean Product and Process Development community. Can you tell us about your involvement with this initiative?
Lesa Nichols: Let me start by telling you a story. Years ago, when I was working at TSSC, Jim Womack and I went on a gemba walk at a plant that we were helping with the creation of model lines. At the end of the visit, Jim came up to me and said: "It's okay, but I feel bad for the people. They have made all these improvements, and they are going to lose it all at the next product launch."
Back then I didn't know enough to understand what that really meant, but the sentence stuck with me. Over the years, as I got experience with new model introductions, I realized that it really can all disappear if your product development function stays isolated from improvements made in the rest of the organization.
Helping Toyota to launch new vehicles and components has shown me what sophisticated systems look like, and I also have a body of practical experience with LPPD that I can bring to the table to contribute to the discussion LEI initiated.
PL: One of the things this initiative aims to do is engage the communities adjacent to LPPD. What communities are we talking about?
LN: I didn't understand the value of community development until I got involved with this initiative and started to recognize potential for collaboration. For example, I have worked a bit with the Lean Construction Institute, encouraging further collaboration between them and LEI. The construction industry is still fairly new to lean, but it is an amazing treasure chest of potential to apply the methodology. I look forward to seeing what's next for them.
PL: In the past couple of years, product development has been on everybody's lips. Are people finally realizing how big an impact product development can have on their lean efforts and their performance?
LN: I don't think they have realized it yet. The majority of the companies I am working with don't see a connection between product development and lean. I think it has to do with their size – I tend to work mostly with medium-sized companies, and they are just trying to launch as well as they can.
However, attending the LEI summit in New Orleans was very encouraging. I was slightly worried that LPPD was too isolated as a group, and that the ideas we are trying to spread only appeal to large organizations, but what I saw at the summit was a lot of top managers talking about establishing a direct relationship between the customer and the employee. To me, that is the essence of lean product development.
While there is still a lot of ground to cover, the future looks bright.
PL: How does product development work at Toyota and why is it so different?
LN: At Toyota, the product development process is connected to all other functions from the very beginning in a very integrated system.
During my years at Toyota, from the moment I sat with a new model launch A3 in my hands, I was always looking at the whole picture. It is a well-oiled mechanism, where each function knows exactly where it fits in the global picture.
Toyota is great at bringing processes in at the right time. The whole focus, past the design stage, is on what the problems are. The beauty is in designing circumstances so the functions responsible for those problems cannot escape making decisions in a timely fashion. It is just amazing.
PL: You run the Lego Serious Play workshop, which is designed to facilitate communication across an organization. Can you tell us more about it?
LN: When you are interacting with people responsible for functional objectives, systems are and stay invisible. As part of my work and with the workshop, I want to end that, and help people discover and know the systems they operate in.
The Lego Serious Play workshop takes invisible things and makes them visible. By playing with what-if scenarios, it helps to bridge a gap: every time you face a very complex problem (with several functions and political boundaries involved) and you don't know how to visualize and improve it, the methodology helps you to get the team going.
It is often used in diplomatic environments so that negotiating teams can effectively work through what they anticipate. This way, it is clear where every member of the team stands before the stakes get too high.
PL: Why do some many companies fail to see the big picture and achieve an enterprise-wide transformation? Is this lean's biggest limit to date?
LN: I think it comes down to the ability to see systems in a way that makes you feel like you can do something to change them. As Deming taught us, any worker on any given day can come into work with the best intentions and still influence a mere 15% of the overall quality of a his or her output. This means that the problem is not in the people, but in the systems that we have put in place, which negatively influence the processes we design. System kaizen is definitely where most organizations get stuck.
The other thing is, it is all too common in the lean community to have little focus on establishing the right principles and creating supportive systems. I am very excited about the Lean Global Network's Lean Transformation Model, which is a great opportunity for organizations to start to see lean as an approachable system.
THE INTERVIEWEE
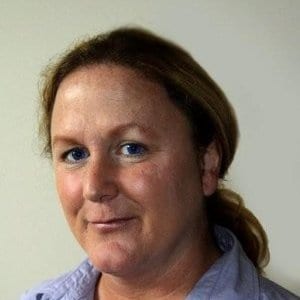
Read more
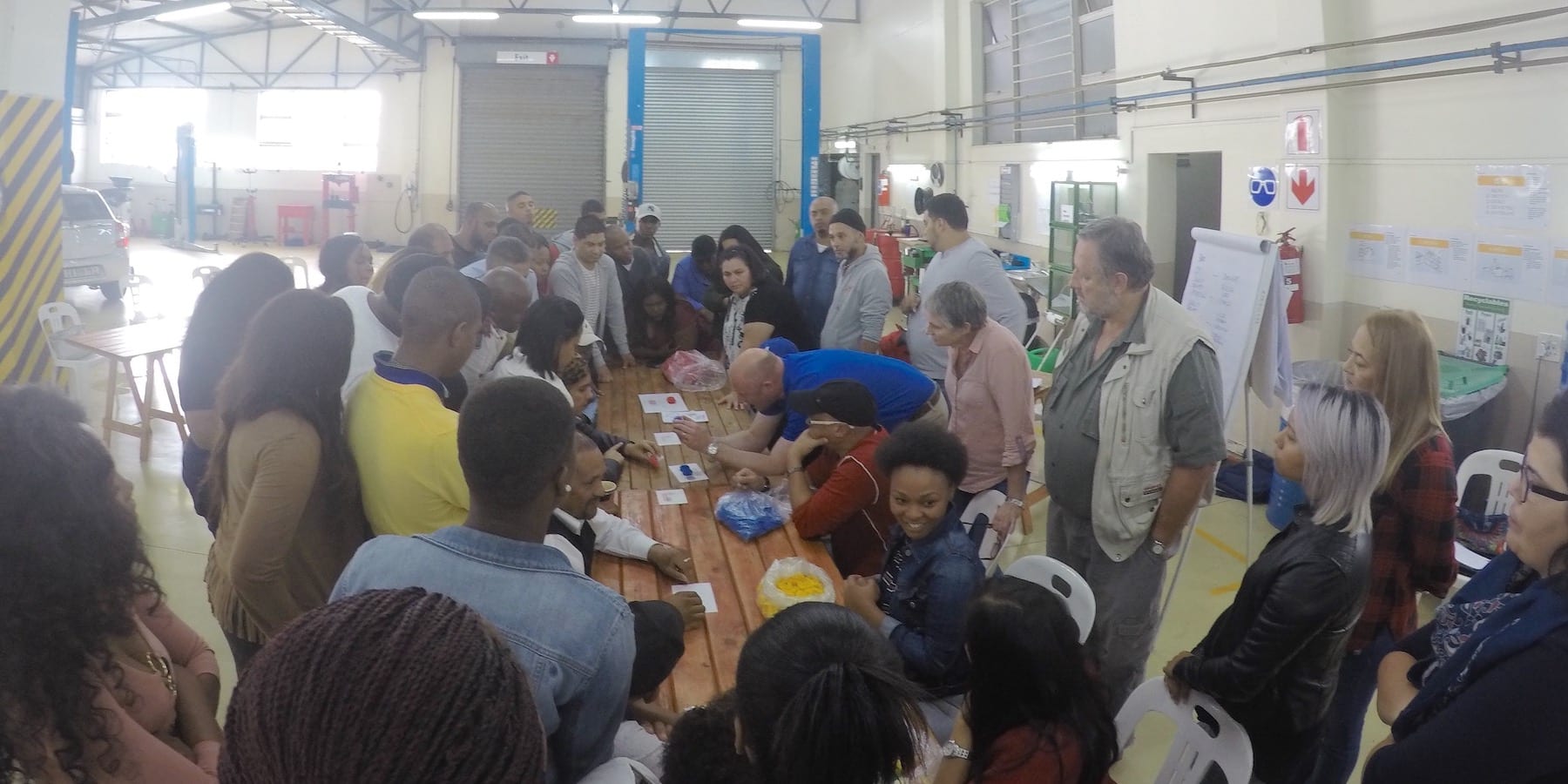
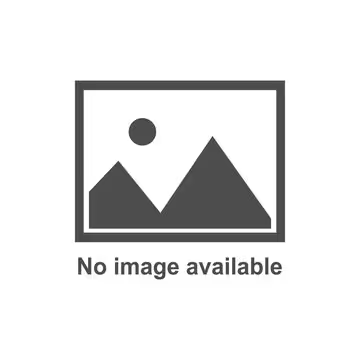
FEATURE – The principal of the Halfway Ottery dealership explains how their lean culture based on respect and improvement is not only changing the business, but transforming the lives of people in the townships.
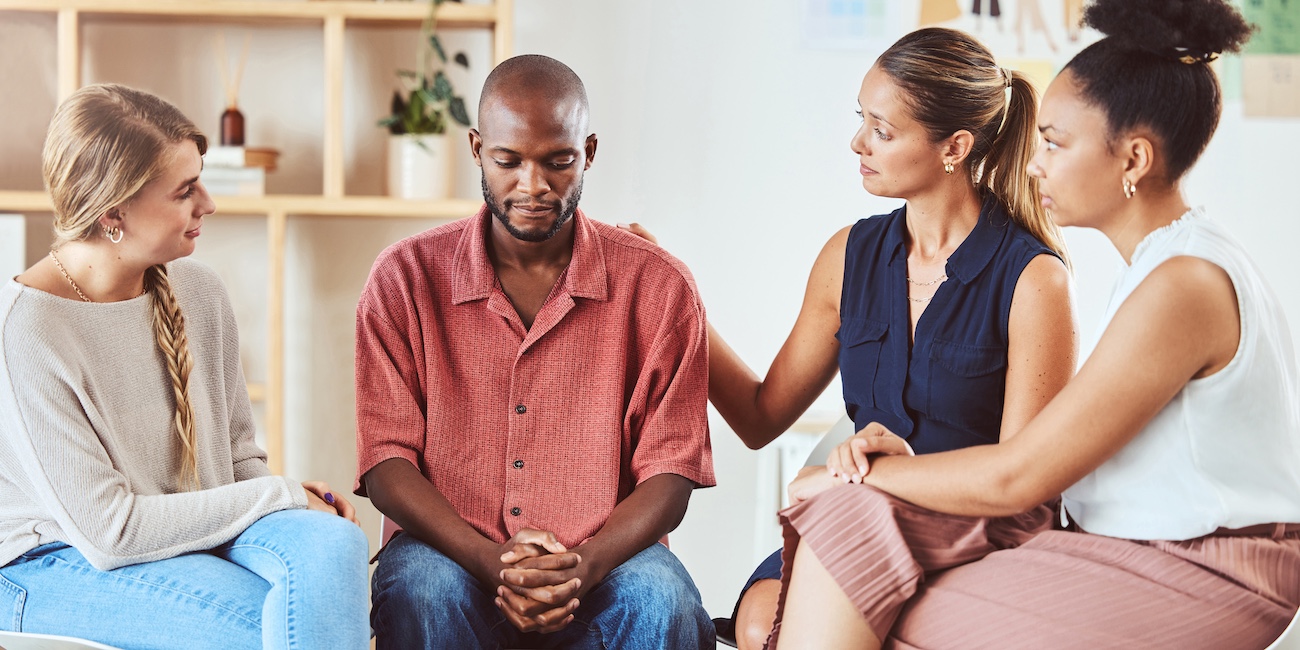
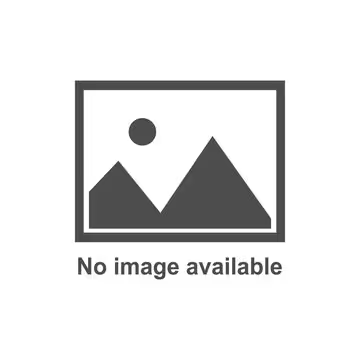
FEATURE – What is psychological safety? What is it not? This article explores its advantages and foundational elements, and how organizations need to transform their leadership to achieve this evolution in management.
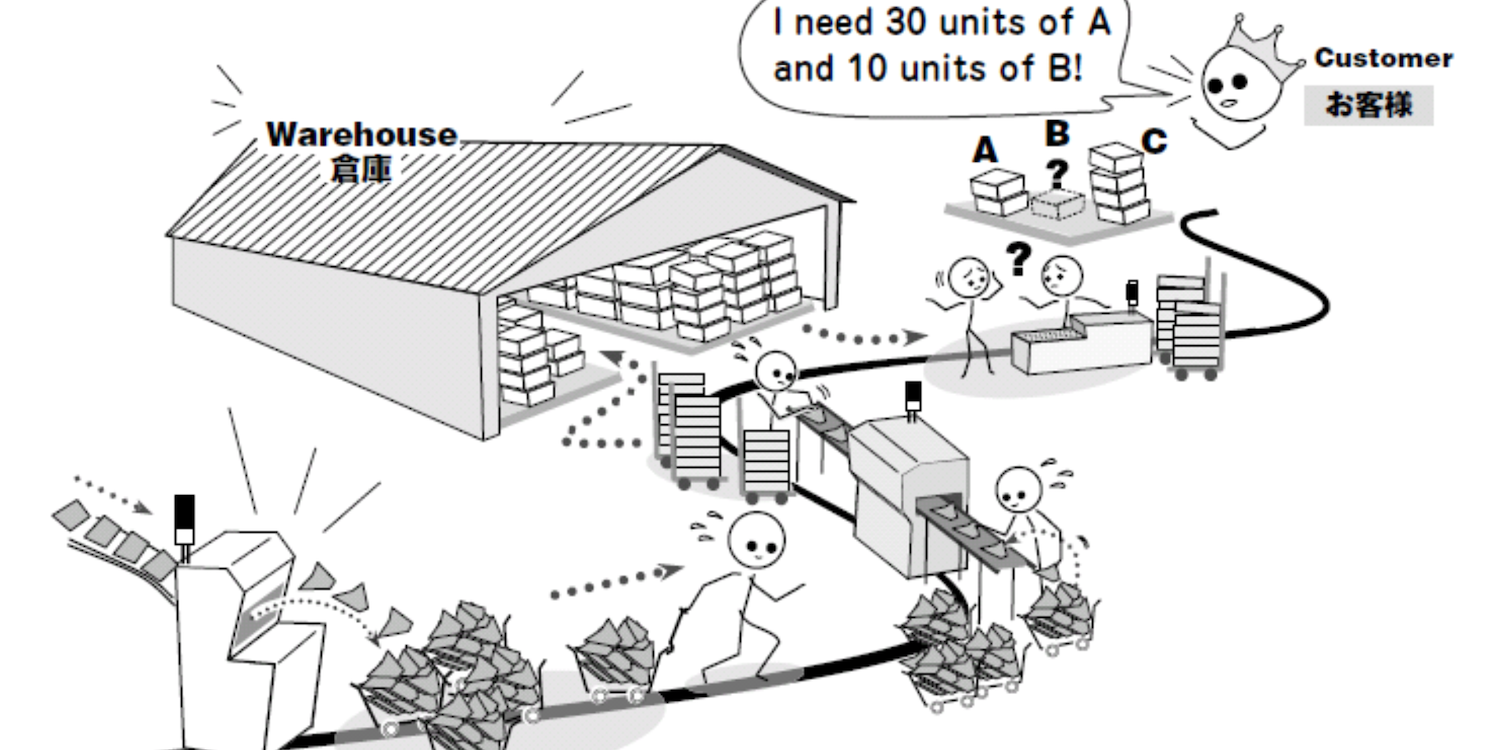
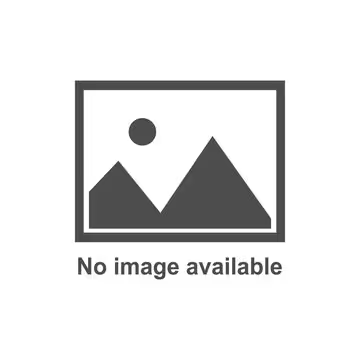
FEATURE – The release of Christoph Roser’s new book All About Pull inspires John Shook to discuss the origins and true meaning of “pull” and why it is incorrect to blame JIT for the shortcomings of global supply chains.

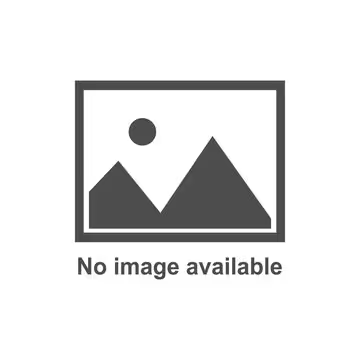
FEATURE – A school board in Holland is discovering the potential of lean thinking and improving its processes to tackle the overburdening of teachers.