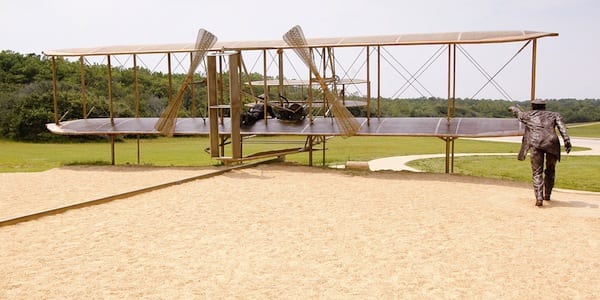
Smalley and Ballé discuss the true spirit of lean thinking - Part 1
FEATURE - We talk about “changing our mindset” all the time, but do we really understand what this means in the context of our lean transformation? This two-part article tries to understand what the spirit of lean really is.
Words: Michael Ballé and Art Smalley
“What they are doing is creating a Buddha image and forgetting to inject soul in it,” once said M. Hajime Oba, one of the celebrated Toyota Production System masters, on the subject of American companies using lean techniques simply as a way to slash inventory.
To be sure, in the past 10 years, the debate about lean has shifted from “Shall we do it?” (as opposed to six sigma, reengineering, etc.) to “How do we do it?” It is becoming painfully obvious in today’s global, hypercompetitive, industrial environment that only lean operations will survive. Astonishingly, although a great number of firms have now initiated a lean program of some sort, successes remain rarities. In other words: many try, few succeed.
Mr. Oba has been relentlessly trying to teach TPS outside of Toyota, mostly to its network of American suppliers, and he remarks that although many firms have doubled productivity in the short run, few have been able to evolve by continuing to apply the principles of TPS.
Indeed, several plants can now boast all the trappings of lean, with pull flows, kanban cards, poka-yoke and so on, and still not have a performance better than average in their industry.
Western firms have been running “kaizen events” for over 20 years, without any significant impact. In the meantime, Toyota, the inventor of lean, continues to progress spectacularly both in terms of market share, profitability and innovation – with the introduction of the Prius, one of the very few technological breakthroughs in the automotive industry in the recent decades.
The issue of “mindset” in lean implementation has been endlessly discussed. Most experts will agree that implementations fail because managers haven’t acquired the right mindset and either “resist the change”, or interpret lean tools in bizarre ways, and, as a result do not deliver expected results – what Mr. Oba describes in a more imaged way as creating a Buddha image without injecting the soul into it.
Yet, although pervasive, the issue of mindset is rarely tackled squarely. Consistently, with lean philosophy, if the standard of TPS use is Toyota, and other firms fall short, the gap in implementation defines the problem. The next step is clarifying the factors causing this gap, and mindset often comes top of the list for most experts. So, can this “mindset” issue be explored head on?
Firstly, what is a mindset?
A mindset generally refers to a set of assumptions and methods held by a person or a group, which encourages them to continue to adopt or accept certain behaviors, choices or tools. As such, the Toyota Production System clearly stems from a specific “lean” mindset which encourages Toyota employees to behave in certain ways, make specific choices, or use a number of tools such as kanban, SMED, TPM, 5S, material & information flow analysis, poka-yoke, andon, and so on. Toyota's practices, typical choices and tools have been well explicated over the past 20 years by a number of observers. The tools, in particular, have received intense scrutiny as other firms tried to adopt them, and have been published in a variety of forms, both as books for the public at large, and as numerous internal documents for the use of companies trying to “go lean.”
But here’s the catch. If used with the wrong fundamental assumptions, the tools only deliver minimal results, or worse, can backfire. Beyond the quick wins obtained through gathering the low-hanging fruit, a true “lean transformation” towards continuous improvement requires more.
Indeed, Toyota’s own lean experts have identified the issue and share the same concern. Mr. Oba interprets lean transformation difficulties primarily as a failure to apply TPS as a “system of training.” He believes that to sustain success, it is necessary to nurture the workforce and to create a culture where people internalize the knowledge of TPS.
In the same vein, one of the most respected masters of TPS, Mr. Nampachi Hayashi, who learned directly from the legendary Taichi Ohno, stresses the importance of imbuing the entire culture with a lean way of thinking. “Kaizen consciousness” must be the mindset of all employees (as explained in Toyota’s 2002 report Making Things: The Essence and Evolution of the Toyota Production System).
Similarly, Mr. Teruyuki Minoura, who also worked under Taiichi Ohno, explains that the T in TPS stands for “thinking”, thus echoing Toyota’s corporate slogan of “better thinking, better products” (see special report The « Thinking» Production System : TPS as a winning strategy for developing people in the global manufacturing environment).
Coming at it from a Western perspective, Gary Convis shares a similar view: “In my experience, the most common roadblock to the successful implementation of TPS is the failure on the part of management - and particularly senior level leaders - to understand TPS as a comprehensive approach to manufacturing and management. Too often, company leaders lack the total commitment to, and understanding of, TPS, that are essential to its adoption, and are unwilling to be involved in its day-to-day implementation and application. TPS is not simply a set of concepts, techniques and methods, which can be implemented by command and control. Rather, it is a fully integrated management and manufacturing philosophy and approach, which must be practiced throughout the organization from top to bottom and consistently applied and kaizened day in and day out.”
Overall, an intriguing challenge: the issue is not just to improve every process of the company, but to change the mindset of every employee! Worse, attempting to improve operations without changing the mindset will likely lead to great efforts without much success.
Furthermore, Toyota has long been aware of this difficulty, and faces the same issue as everyone else – maintaining the TPS mindset.
For instance, an internal document from one of the Takaoka plants retraces four stages of evolution of kaizen activities in the plant – and the explicit goal of the process is “Reform of managers’ minds”:
- In the first stage, back in the 1970s, the plant worked with a push system by monthly forecast, with large lot production and suffered from frequent parts shortages and misshippings;
- In the ‘80s, at the second stage, increased sales drove the plant towards more automation and labor saving to increase capacity through individual kaizens – each area was improved but not the entire process in the plant;
- In the early ‘90s, the plant started stage three, and used kanban as a tool of kaizen, in order to clarify problems and shorten the kaizen lead-time;
- This led to, around 1995, kaizen activities through the entire process including conveyance and logistics, to make problems easy to find on the shop floor, and to take countermeasures organizationally.
In this case, kanban, the tool, is explicitly seen as way to do kaizen, and not the other way around. The aim of the “establishment of kanban as a tool of kaizen” in the plant was human development and the elimination of stagnation of material and information flow. Throughout the analysis, process issues (stagnation of parts and information), human issues and mindset issues are continuously intertwined. Contrarily, the equivalent “value stream mapping” analysis in Western firms tends to focus exclusively on the process and make no mention of either human development concerns, or mindset reform questions.
What, then, is a “mindset”? Or more precisely, how can this “mindset issue” be systematically tackled? Most of us tend to have an instinctive grasp of the notion of mindset, but would find it difficult to define it or analyze it in a cut-and-dried manner. Another, more pedantic, word for “mindset” is “paradigm”, which has been used since the 19th century and which the Webster dictionary defines as “a philosophical and theoretical framework of a scientific school or discipline within which theories, laws, and generalizations and the experiments performed in support of them are formulated; broadly: a philosophical or theoretical framework of any kind.”
Paradigms have been studied in detail the scientific world, and four main questions apply to the understanding of mindsets:
- What is to be observed and scrutinized;
- The kind of questions that are supposed to be asked and probed for answers in relation to this subject;
- How these questions are to be put;
- How the results of investigations should be interpreted.
In fact, in developing and applying TPS, Toyota’s lean masters have approached these four questions in detail and often in rather confounding ways. These four key questions provide a clear guide to understanding the “spirit” of lean, beyond the tools and techniques that are now common knowledge.
Read part 2 of this article here.
THE AUTHORS
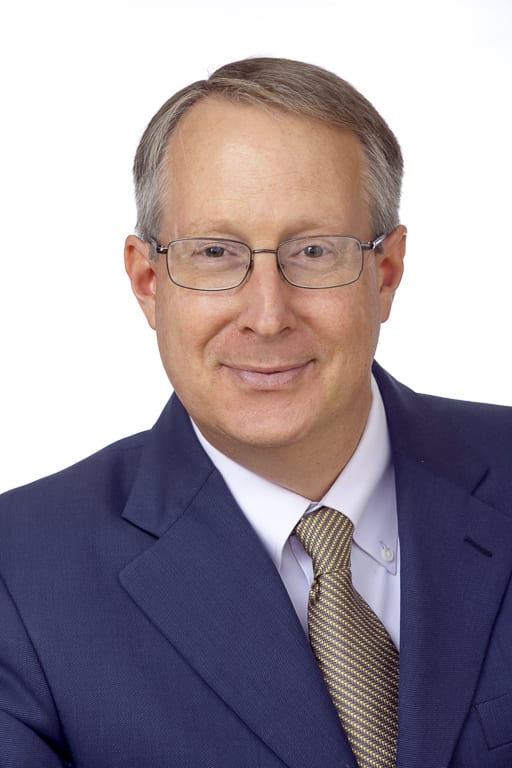
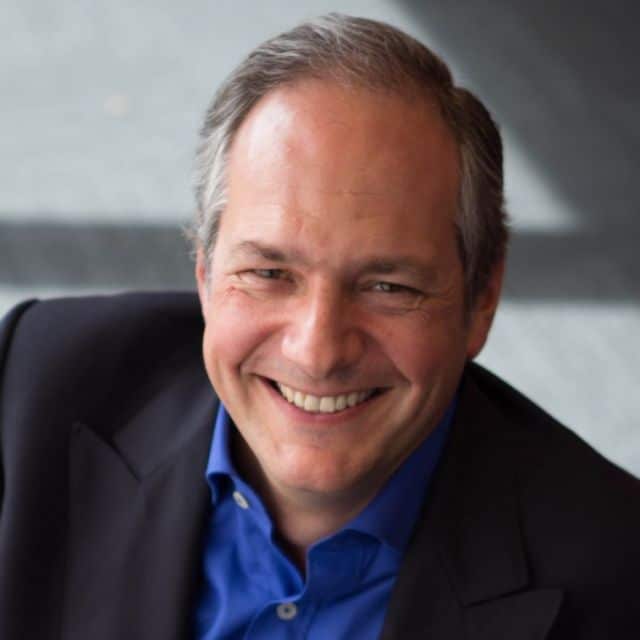
Read more
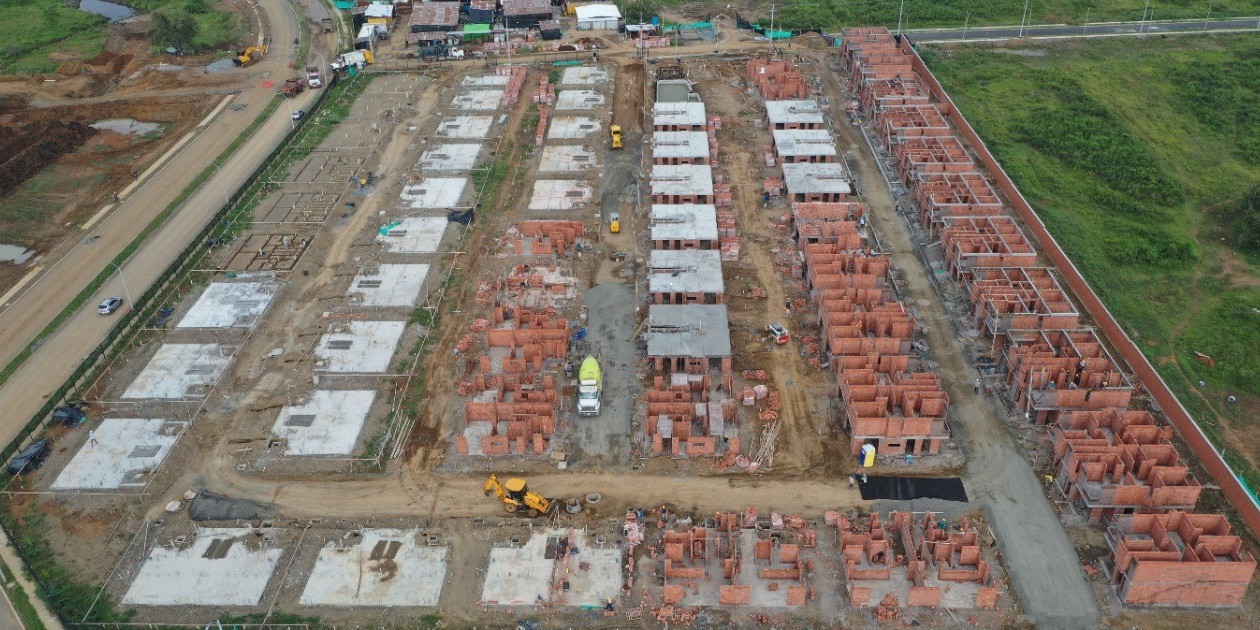
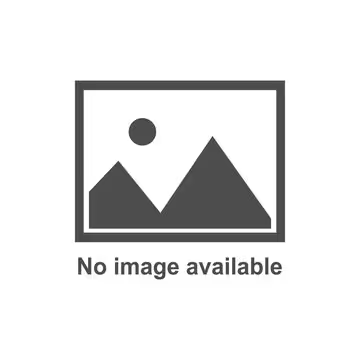
CASE STUDY – The turning point in this Colombian construction company’s transformation came when they started to embrace lean as a culture rather than just a set of tools.
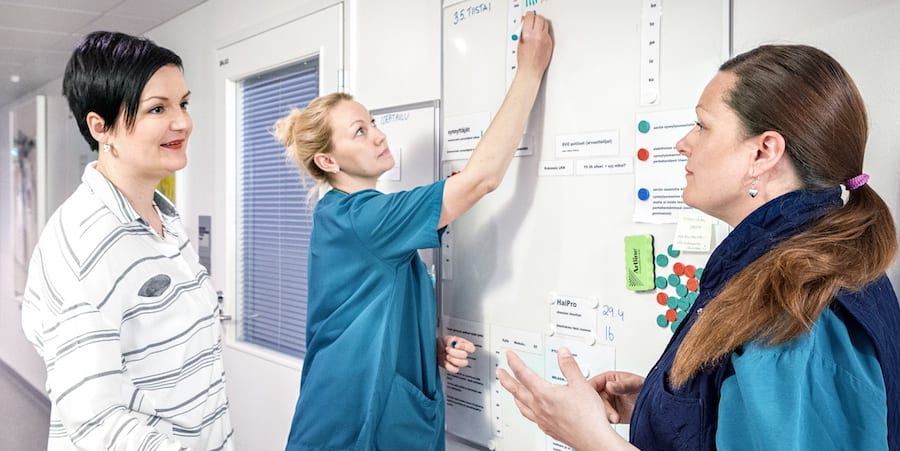
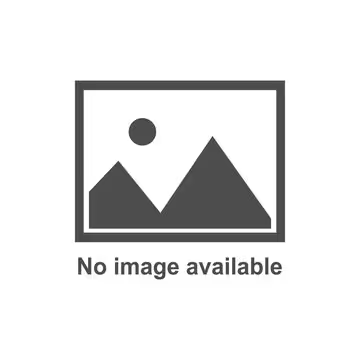
CASE STUDY – The whole of Helsinki’s hospital district is leaning out, with incredible results. It isn’t every day that we come across – let alone have the opportunity to observe – a lean transformation in such a large healthcare organization.
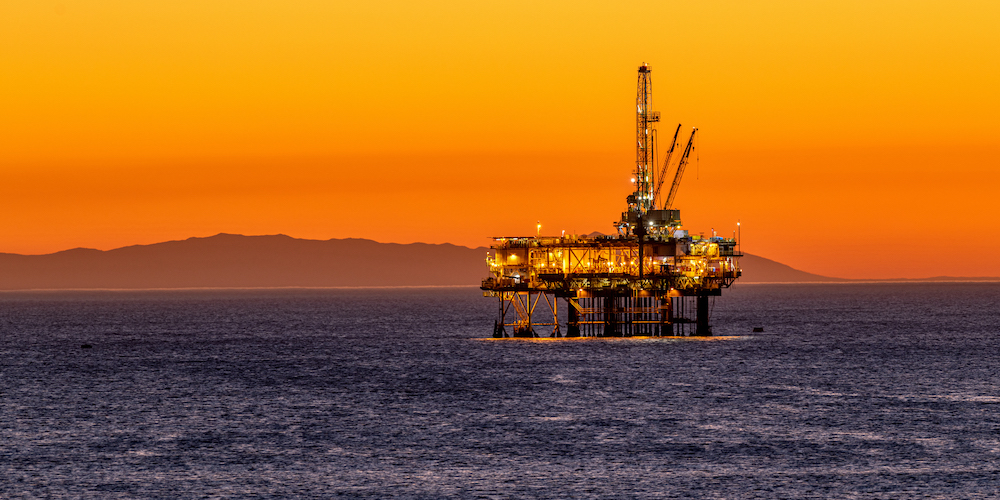
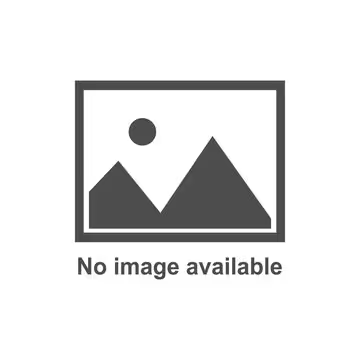
INTERVIEW – In this Q&A, the Chief of Transformation of oil and gas company TechnipFMC tells us about their experience implementing Lean Product and Process Development.
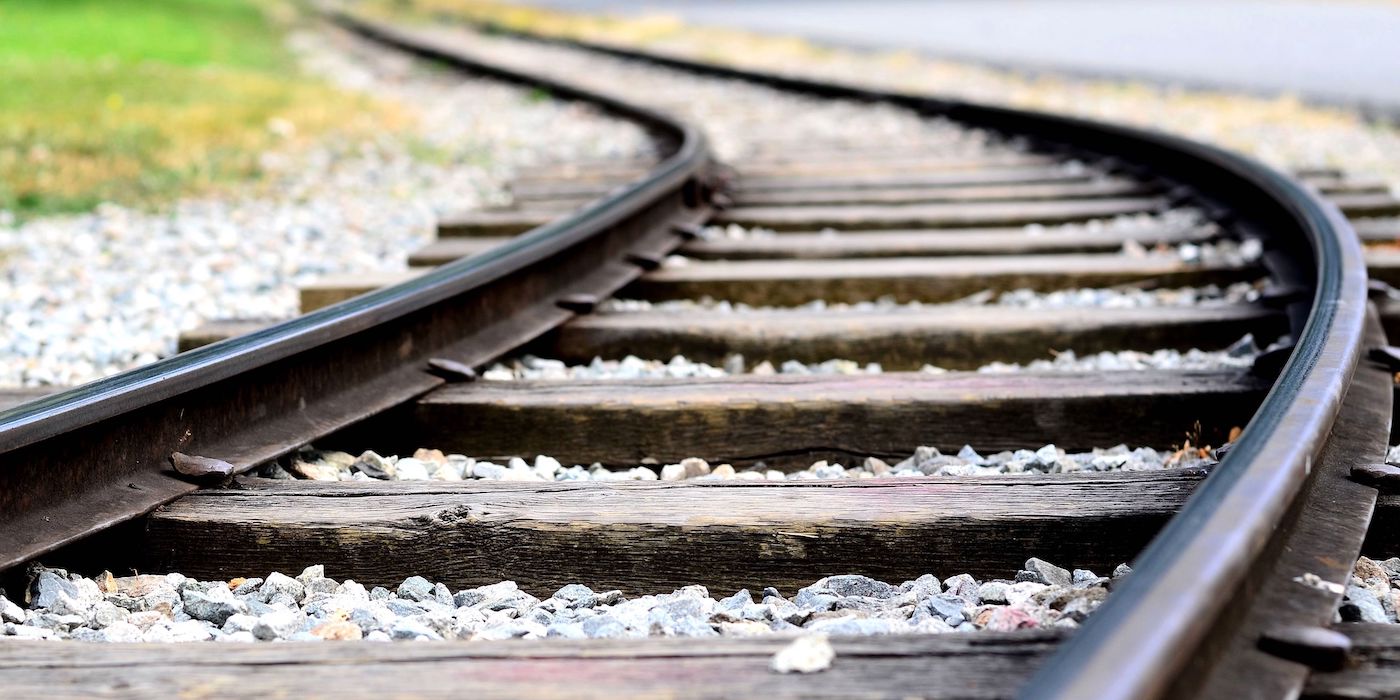
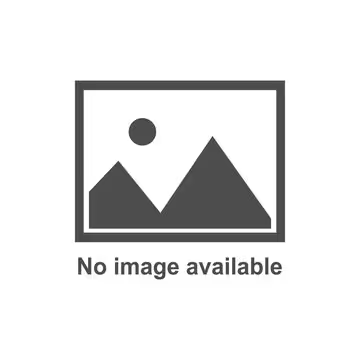
NOTES FROM THE GEMBA – The author goes back to a train maintenance center she visited two years ago and finds an organization striving to learn continuously.