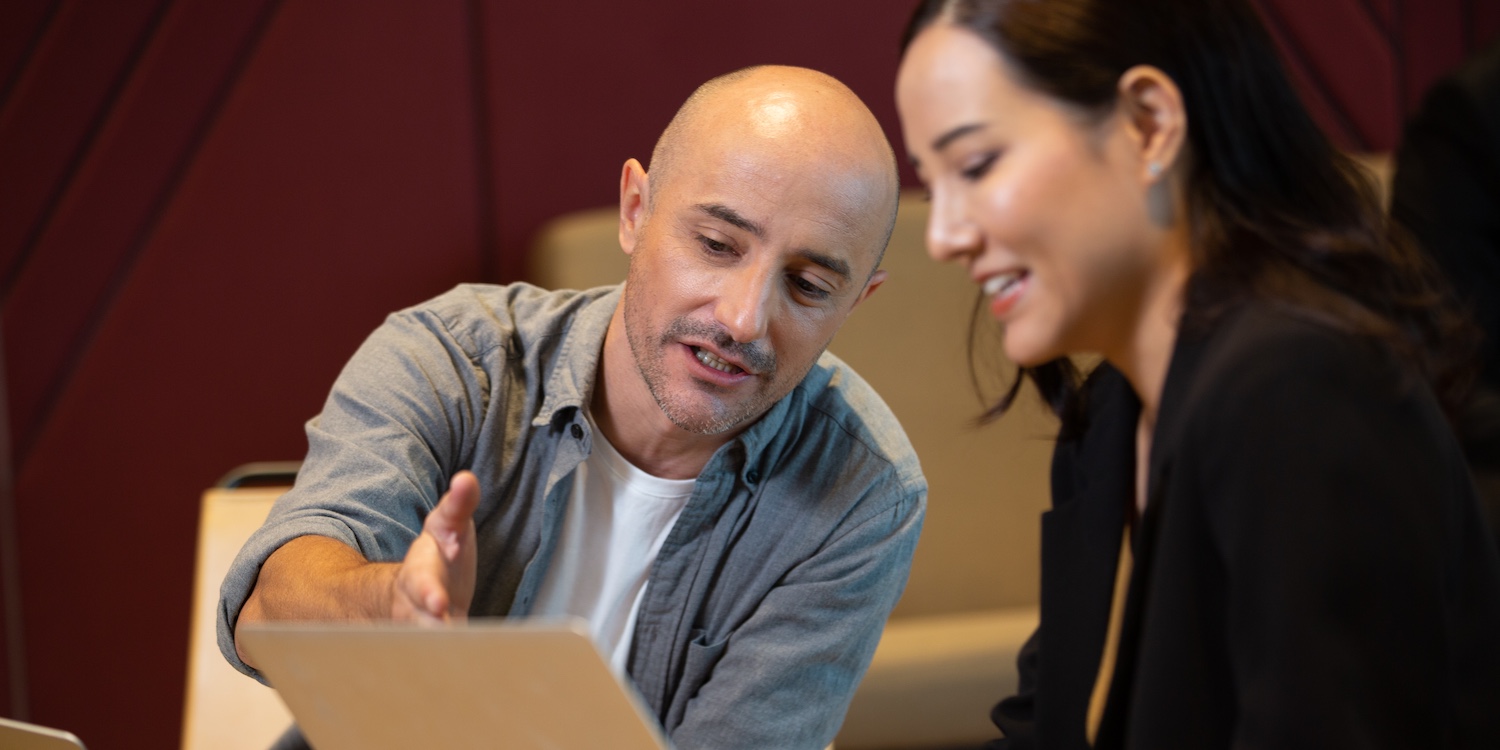
Scaling Kaizen in a tech organization
CASE STUDY – A Scaling Kaizen initiative at Veolia Water Information Systems engaged 45 teams in Lean IT practices, improving delivery, incident reduction, and fostering talent.
Words: Meriem Riadi with Cecil Dijoux
Throughout the 2010s, management conversations in IT organizations have mainly focused on agile transformations (Scrum, DevOps, SAFe, Product org., …). Over the last few years, however, we have witnessed a shift, as CIOs look for new levers to improve organizational efficiency – Lean IT being one of the most popular today. To illustrate how relevant this point is, we would like to share some insights about a Scaling Kaizen initiative, involving 45 teams in one year, using standard lean practices at Veolia Water Information Systems.
CONTEXT
VWIS delivers digital and IT solutions to over 15,000 users via 250 business applications. The company’s structure has two main parts: the first includes three departments tied to the business organization (Operations, Consumers, and Support functions), while the second is cross-disciplinary (Data, Infrastructure & Operations, Customer Relationship, and CIO Office). VWIS has nine local IT departments across the French territory and ten dedicated companies.
CHALLENGES AND OBJECTIVES
The whole Veolia Water Business Unit operates in a competitive and saturated market, challenged by climate change and a reduction in the amount of available water. To achieve the efficiency improvement objectives defined by the Board and boost customer satisfaction, the strategy is to develop people’s skills via on-the-job problem solving. In other words, Lean Thinking.
We started with lean experiments in 2021, but soon found we needed to speed up the whole transformation. The turnaround started by involving the IT executives in the Hoshin Kanri process (using a OKR approach, a standard in digital companies) and in monthly Gemba walks, and by setting up a management Obeya to openly share the challenges, the problems and the learnings.
In previous years, only three teams on average were involved in implementing Lean. Our objective is to engage many more teams, this is the reason why we decided to launch the Scaling Kaizen initiative in early 2024.
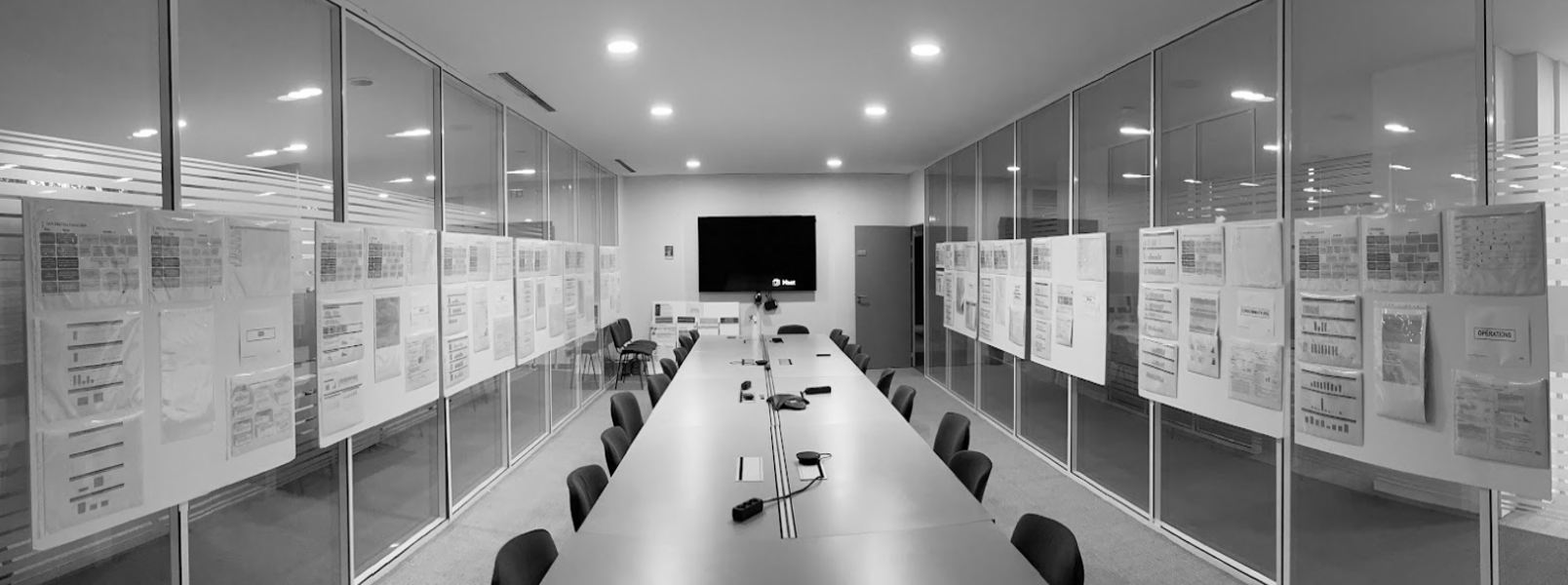
SCALING KAIZEN
Traditionally in this organization, we have been working on standard lean projects within individual teams, addressing their problems to achieve better quality, reduce delay, and improve customer satisfaction. In a view to make it possible for the organization to scale Kaizen practices, we decided to look at it from a different perspective: rather than coaching one team to tackle many issues, we decided to tackle the same issue with many teams in parallel. The problem to be solved on each occasion is chosen between one of the following three, as defined in the company’s OKRs:
- Quality: reduce incoming number of IT incidents opened by users by 20%;
- Delay: reduce the stock of incidents to be solved by 20%, in order to reduce the lead-time of their resolution;
- Operational value: improving project delivery by 20%. With Lean Thinking, we are focusing on customer value, thus using indicators that are meaningful to customers. For agile teams, we follow the number of User Stories delivered every sprint (or every week in case of teams using Kanban). [Though it is useful for teams to define their capacity, we don’t use agile standard Story Points since it has no meaning whatsoever for the customer.]
KAIZEN CIRCLE
Once the operational perspective to coach many teams was identified, we needed to find an organizational practice to make it work. For that purpose, we referred to Masaaki Imai once again with the principle of Kaizen Circle. These circles aim to bring together people from different teams to regularly work on a single business issue using lean problem-solving tools.
We decided to experiment with four two-person teams for each circle. Each pair represent a team and is supported by a dedicated coach during the first 75 minutes of the weekly session to work on the problem in the context of their team, using the A3 template. The remaining 15 minutes of the 90-minute slot are used to share the work that has been carried out in the session, in order to create the conditions for continuous Yokoten (sharing findings and learnings gathered in problem solving).
Lastly, each circle has a sponsor belonging to the Board, whose role is to support and create the conditions of engagement within each team.

THE A3 TOOL FOR PROBLEM SOLVING
The A3 is the standard used to document and carry out problem solving in Lean Thinking. Its logical, eight-section structure may seem simple at first, but it is rather demanding and requires deep thinking and investigation of gemba-based evidence. At the end of the Kaizen, the completed A3 document is presented to the management team.
THE KAIZEN SEASON TO SYNCHRONIZE THE LEARNINGS
This third and last organizational tool we used to scale our Kaizen efforts is directly inspired by the Product Increment (PI) of the Scaled Agile Framework (SAFe). The objective is that all circles start and end their improvement the same week. The duration is the same as the one we use for our standard team coaching process – 8 weeks – which makes for a gentle yet challenging pace.
At the end of the eight weeks, each two-person team has 7 minutes to present the A3 they have been working on during the Kaizen season. This allows them to practice executive summary and verbal communication in front of a large audience.
The CEO happened to be present during the presentation of Season 3. He expressed his gratitude to each team, as they worked on operational issues that were directly linked to strategic issues.
RESULTS AND LEARNINGS
A first result worth highlighting is the evolution of the number of managers and teams onboarded in lean practices. The following diagram illustrates these figures.
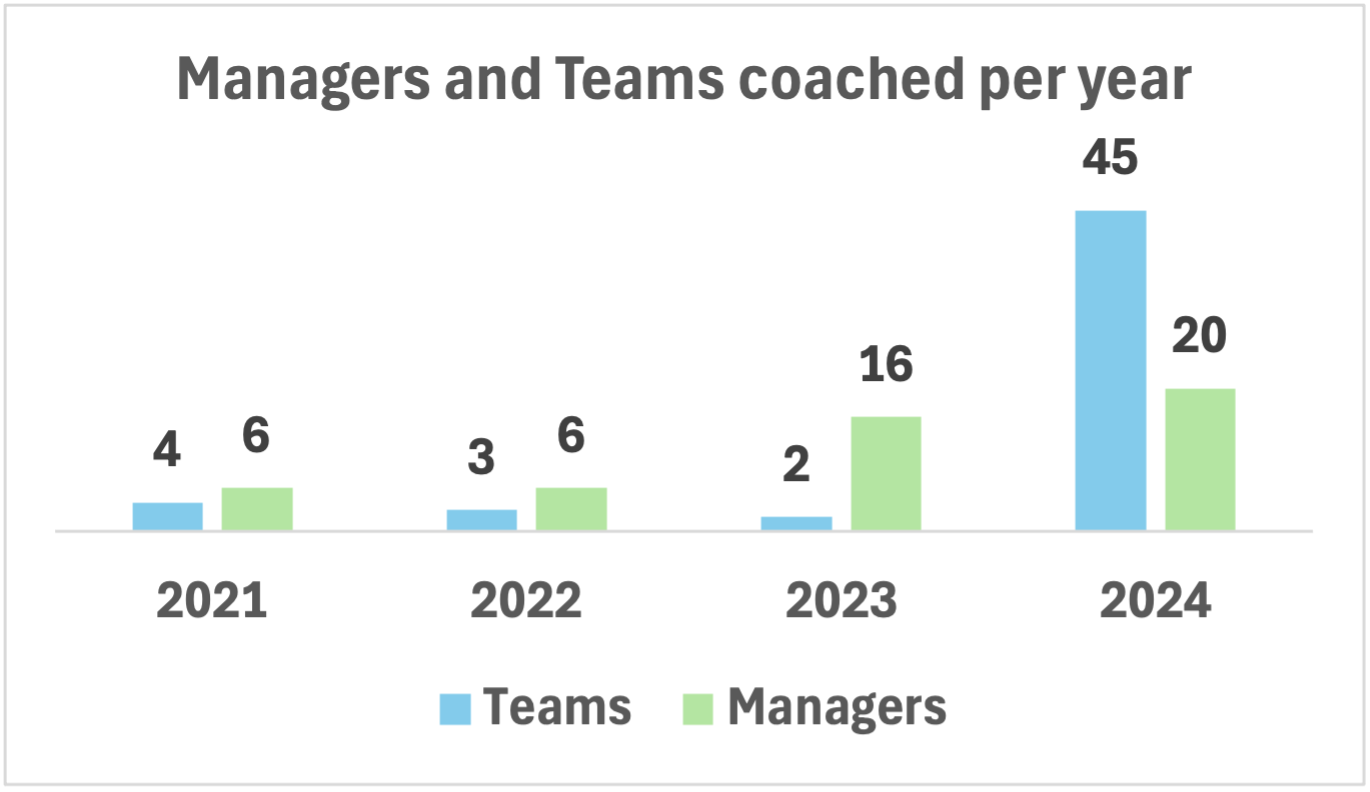
In 2023, we saw the involvement of the Board, while in 2024 we saw the results of the Scaling Kaizen experiment.
A more important result was the number of teams succeeding in reaching the Kaizen target thanks to this scaling approach (“OK” meaning “having reached the target defined in the A3”).
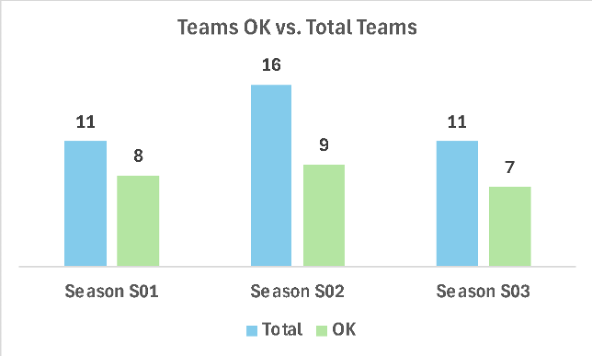
Even though not all teams reached the objective, they still carried out their problem-solving exercise and were able to generate learning from it.
The question we asked ourselves after the third season was whether the teams would be able to sustain the results of their improvement. So, we checked how season-1 teams were doing six months after completing the season and how season-2 teams were doing after three months. These were the findings:
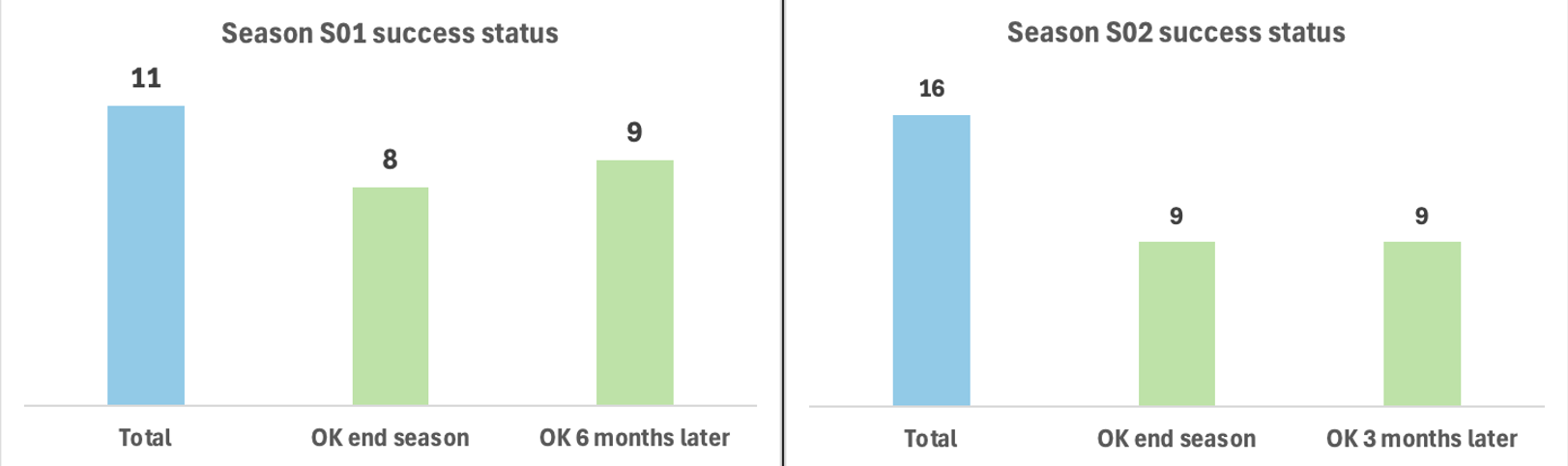
SOME EXAMPLES
Four Season 1 teams achieved significant delivery improvements following Kaizen, with average increases in User Stories (US) completed per sprint of 276%, 31%, 54%, and 10% respectively, comparing the six months before and after the initiative. Regarding incident reduction, five out of seven teams showed decreases in weekly incoming incidents by 26%, 20%, 26%, and 25% respectively, over the same period.
As far as A3’s result is concerned, as an example, an agile team of 10 people succeeded in improving its sprint “engagement” (i.e. the number of User Stories delivered vs. number of User Stories planned in the sprint) from 56% to 95%, and the average delivery from 14 US delivered per sprint to 18.3 (hence 31% improvement).
Key practices that were developed by the team throughout the process included:
- Clarifying User Story expectations by defining acceptance criteria to help developers deliver right-first time.
- Having the Product Owner ensure that business rules are explicitly defined in US, as less experienced developers may not be able to understand their underlying assumptions.
- Defining daily objectives of US to be delivered and ask for help from the right expert (with precise questions) whenever a daily objective cannot be achieved.
- In retrospectives, investigating each US that was not delivered as expected using PDCA, in order to find the root cause of the problem, and accordingly update the team’s Definition of Ready and/or Definition of Done (team’s agile standards).
WHAT WE LEARNED
This experiment showed us how scaling Lean in an IT organization really entails scaling A3 Thinking, as Steve Bell (co-author of the seminal book Lean IT – Enabling and Sustaining your Lean Transformation) explained in his Lean Digital Summit talk in Paris in 2015.
At the end of the first year and its four seasons, 45 teams were coached. Our objective to increase the number of involved teams tenfold was exceeded, with about 2/3 of the teams achieving their objectives, too.
A second learning was that Lean often challenges middle management’s beliefs. Some managers may see Kaizen as a trivial approach of little value compared to larger scale improvement projects, an issue identified in Western management by Masaaki Imai. This preconception needs to be addressed using Gemba evidence and challenges by the executives who want to implement this strategy. Each person learns at their own pace, and it may take some time to engage middle managers in the focused and deep thinking required to manage daily performance and problem solving. It’s worth persevering.
A third learning was that Kaizen allows the IT board to identify problem solvers and talent that may have not emerged in a non-lean management system. Lean allows a business to develop learning, autonomy and leadership, and we are now able to identify the organization’s leaders of tomorrow. They will help us to solve critical business and customer issues.
THE AUTHORS
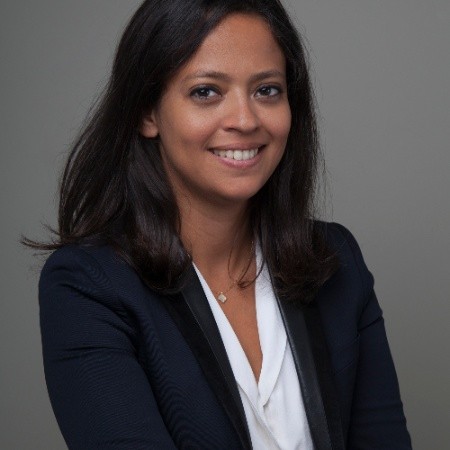
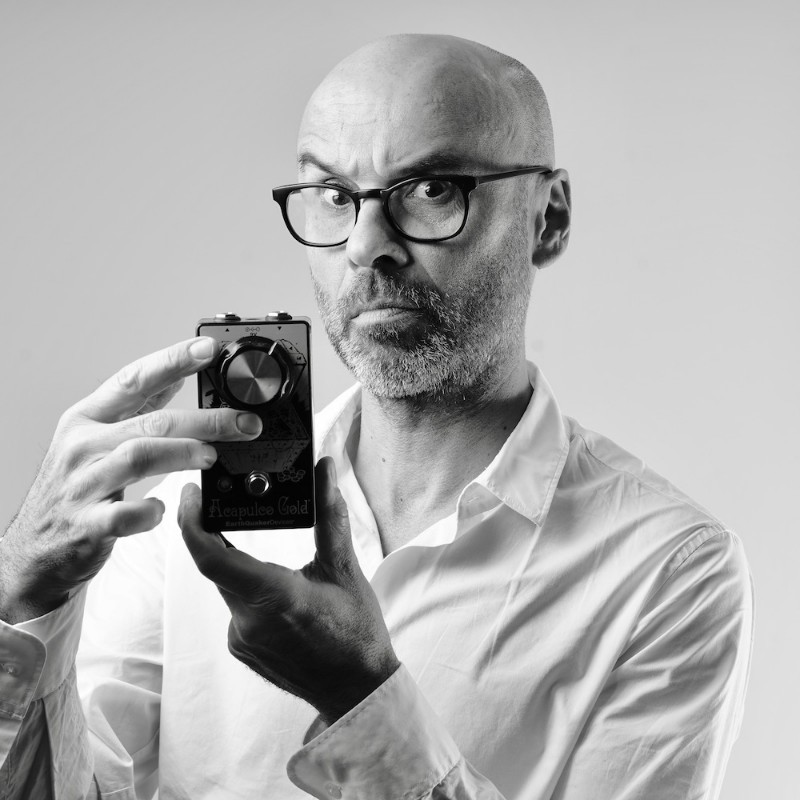
Read more
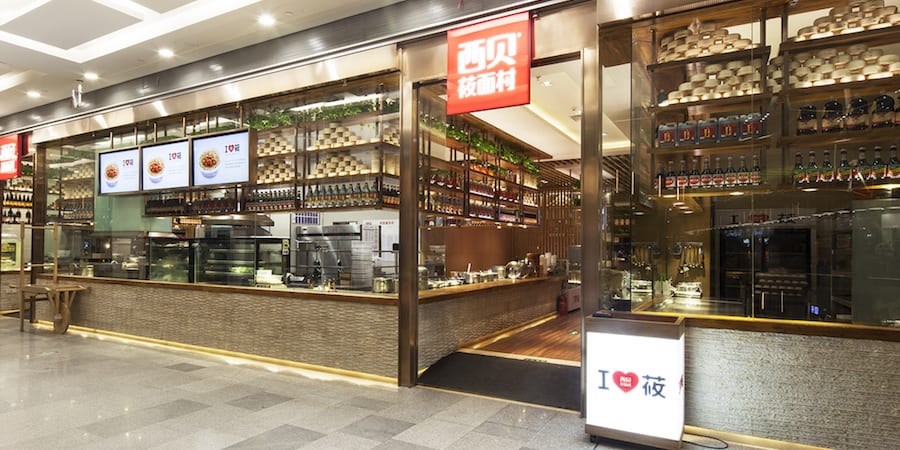
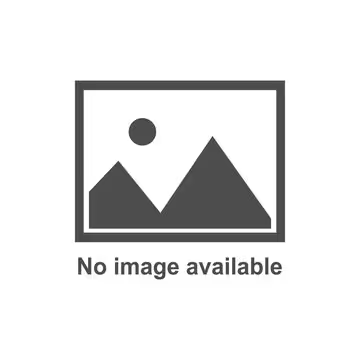
CASE STUDY – An entire restaurant chain going lean is not something you see every day. Coming all the way from China, Xibei's story of cultural change will inspire you to never forget the fundamentals of lean, from standardization to quality.
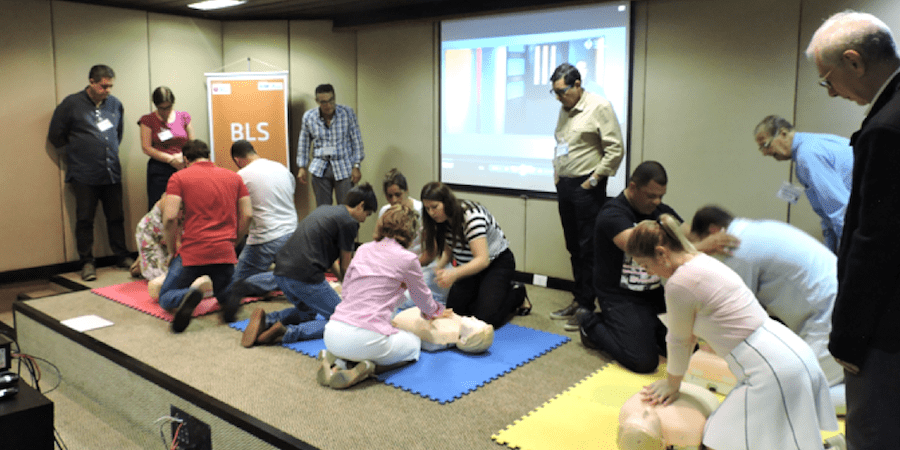
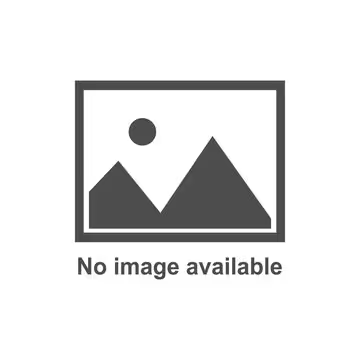
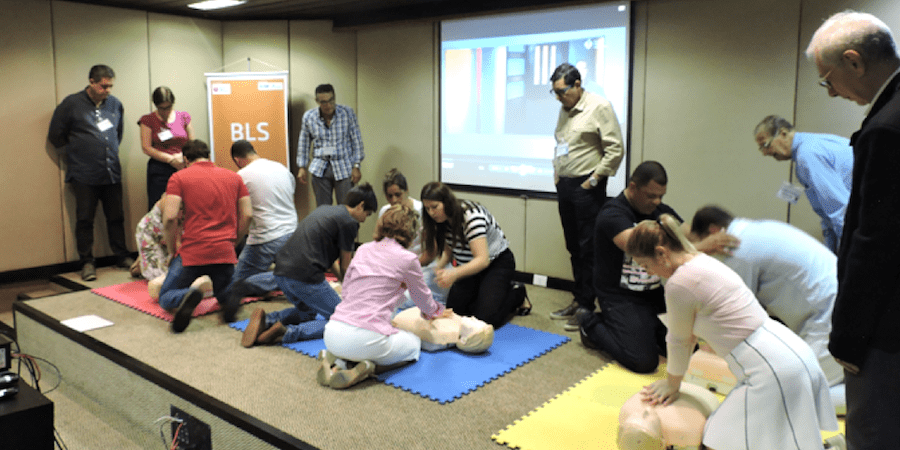
INTERVIEW – A cardiologist from a hospital in Salvador de Bahia explains how his department was completely transformed following the introduction of a dedicated pathway for heart patients.
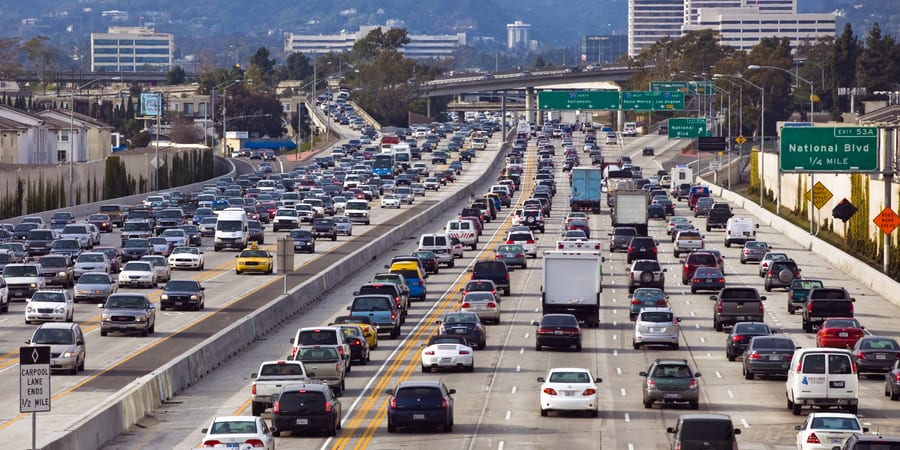
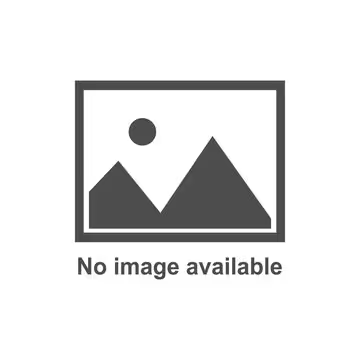
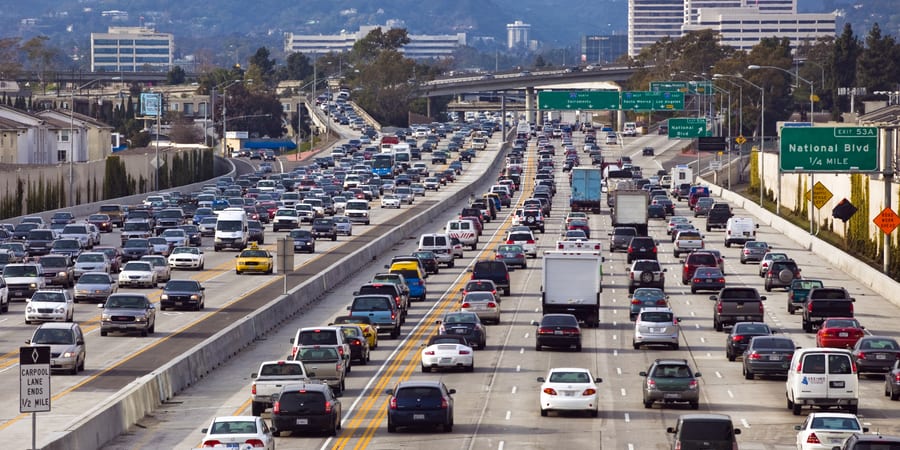
WOMACK’S YOKOTEN – In this month’s column, Jim shares an insightful analysis of the trends and dynamics of today’s automotive industry and looks at the opportunity that lean has to facilitate its next transformation.
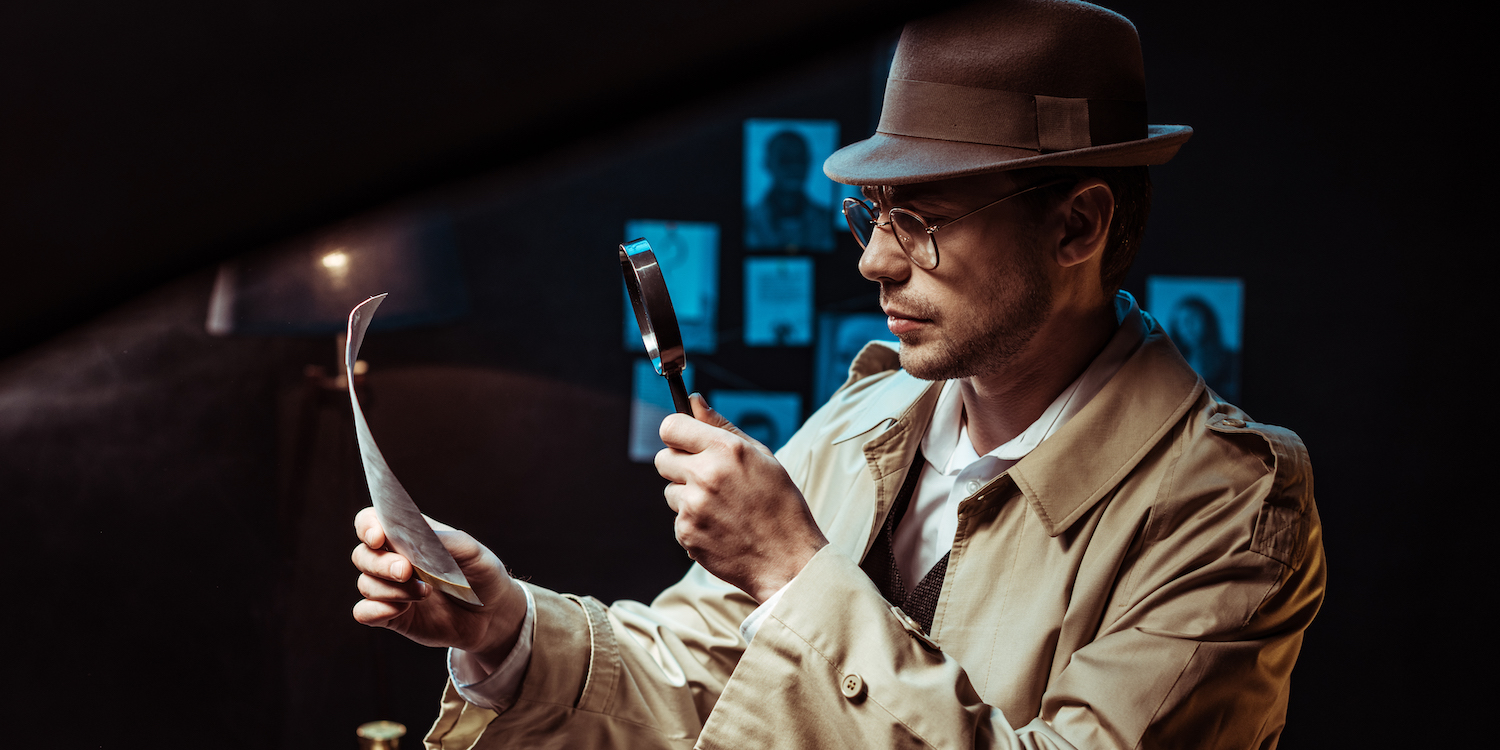
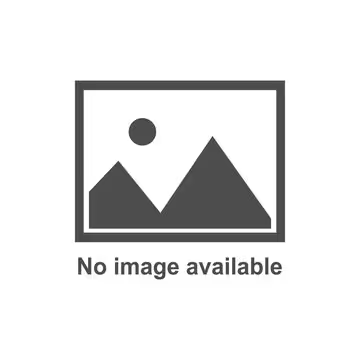
FEATURE – This insightful piece explores the true meaning of problem solving, looking at the common mistakes leaders make when they adopt some of its key practices.
Read more
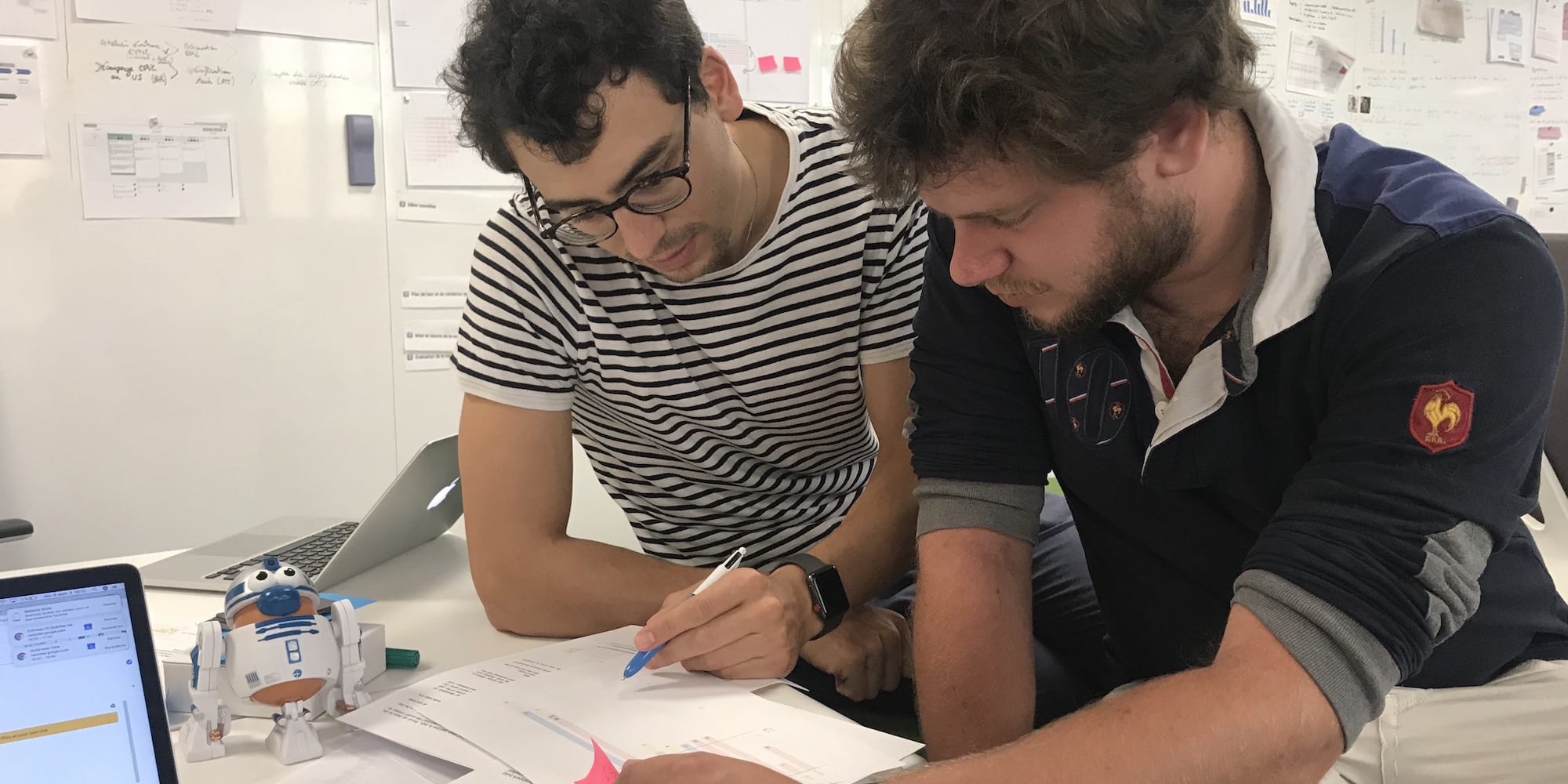
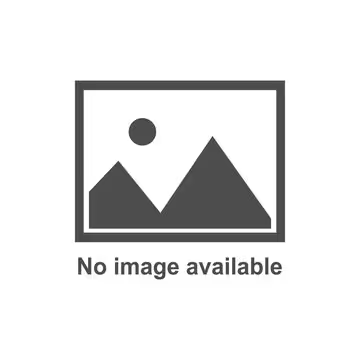
BUILDING BRIDGES – In another article for their series, lean digital company Theodo tells us about their efforts to measure and reduce its lead-time to deliver product features.
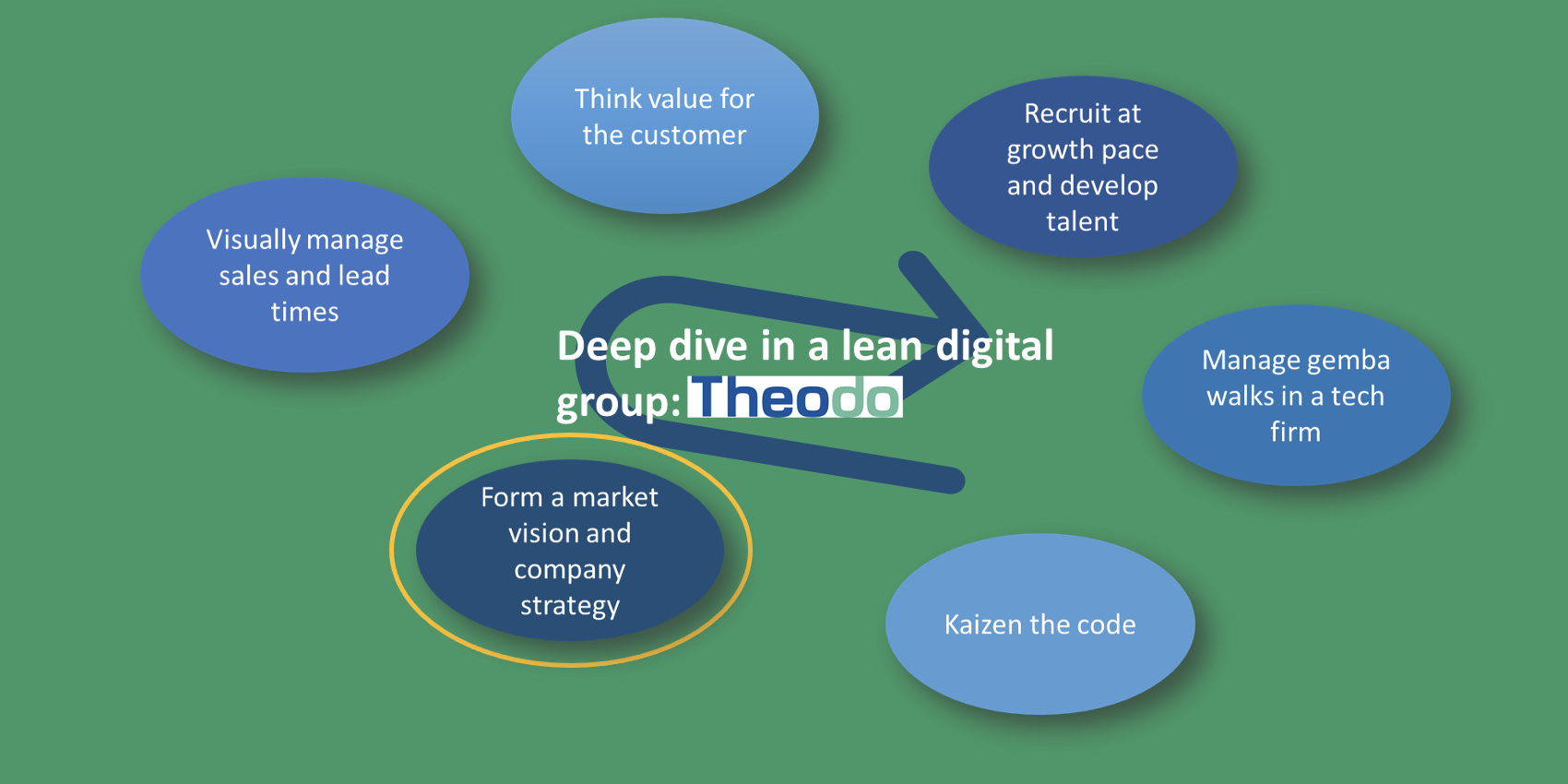
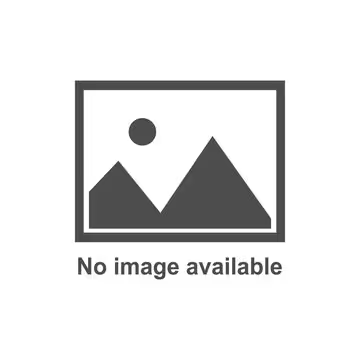
FEATURE – In the final article of her series, the author spends a day with Theodo’s CEO and co-founder to learn how lean informs its strategy and vision.
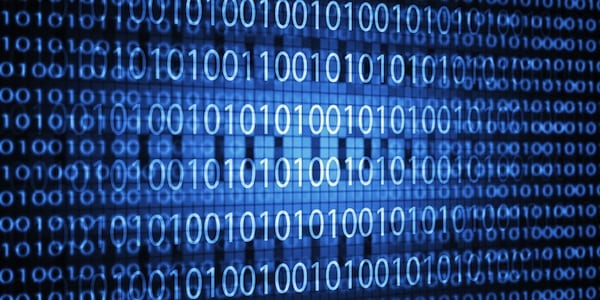
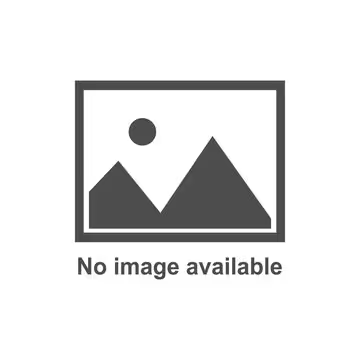
FEATURE - Professor Dan Jones looks at the unique challenges the digital age presents the business community with, and explains how lean thinking can help us to effectively address them.
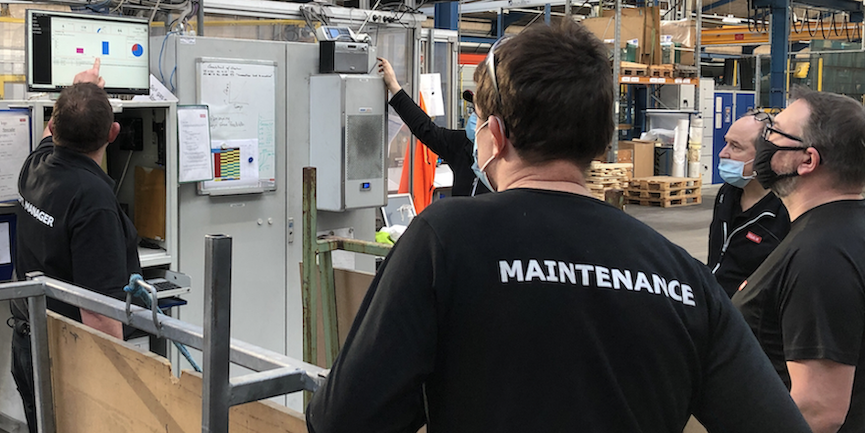
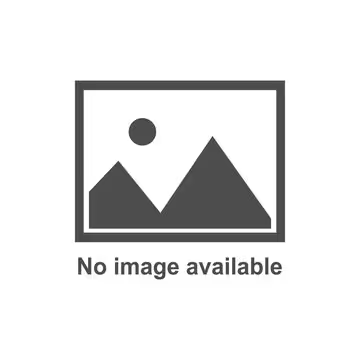
CASE STUDY – The authors discuss how rooftop window producer VELUX harnessed Lean Thinking and Industry 4.0 to empower shop floor workers, after rediscovering the kaizen spirit following a digitalization initiative that didn’t work out.