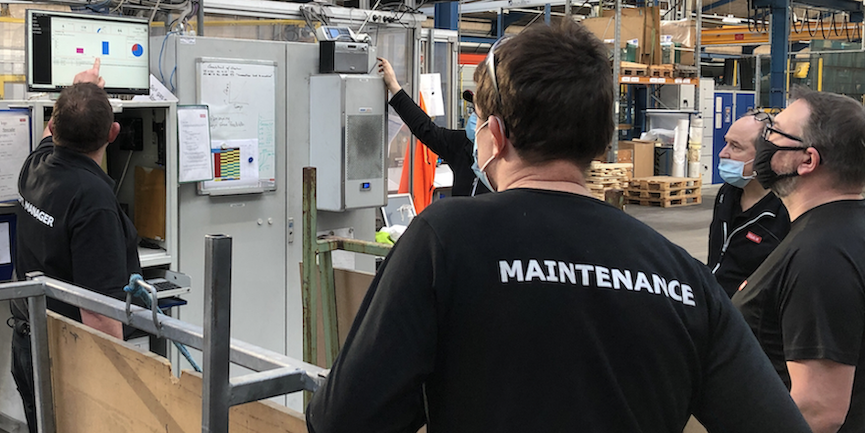
Rediscovering Lean after a failed digitalization initiative
CASE STUDY – The authors discuss how rooftop window producer VELUX harnessed Lean Thinking and Industry 4.0 to empower shop floor workers, after rediscovering the kaizen spirit following a digitalization initiative that didn’t work out.
Words: Henrik Saabye and Daryl Powell
Industry 4.0 promises transformative efficiency through the adoption of technologies like the Industrial Internet of Things (IIoT), big data analytics, and automation. IIoT, in particular, enables manufacturers to collect and analyze real-time data from interconnected systems, offering insights into production efficiency, maintenance needs, and more. Yet, despite its potential, many implementations fail to deliver the expected returns.
VELUX, a rooftop windows manufacturer in Denmark, experienced this firsthand. The company introduced IIoT systems in a key production area, equipping workers with access to data on equipment performance and downtime. The expectation was that this real-time transparency would empower workers to identify inefficiencies and take immediate action. However, six months into the initiative, there were no significant performance gains. The shop floor workers did not engage with the IIoT tools, and productivity remained stagnant.
Investigations revealed several underlying issues. Workers tended to perceive the IIoT system as a coercive tool designed for management oversight rather than a resource for their own use. Additionally, there was no structured approach to using the data for problem-solving or decision-making, and teams lacked ownership of problem identification and relied on managers and engineers to address issues.
VELUX realized that the problem was not the technology itself, but the absence of a supportive learning environment. Without empowering workers to interpret and act on the data, the potential of IIoT remained untapped. As such, the company stumbled upon an important missing link – and a priceless opportunity to revitalize its companywide lean program. This turning point led them to pivot toward a more integrated approach, combining lean and action learning with real-time data to build a culture of continuous learning and improvement.
BUILDING A BRIDGE: LEAN, ACTION LEARNING, AND REAL-TIME DATA
At the core of VELUX’s transformation was the concept of “learning to learn”. This framework emphasized the importance of equipping shop floor workers with the skills and mindset they need in order to interpret data, solve problems, and continuously improve processes. To achieve this, the company introduced a three-step approach.
Step 1: Learning to frame problems using data - From data to insights
Problem framing is often overlooked in manufacturing environments, where reactive problem solving – or “firefighting” – is the norm. VELUX’s first challenge was to shift this mindset by teaching workers how to identify and articulate problems using data.
In the initial phase, workers were introduced to IIoT dashboards displaying metrics, such as overall equipment effectiveness (OEE) and downtime patterns. While this data had previously been accessible only to managers, it was now made available at workstations. Workers were encouraged to analyze trends and ask questions like “Why does this machine experience more stoppages than others?” or “What patterns emerge in downtime over a week or month?”.
For example, in the cladding production department, IIoT data allowed workers to discover that unplanned stoppages frequently occurred during product changeovers. By investigating further, they discovered inconsistencies in setup routines, which they documented as a key problem to address.
This process fostered a sense of ownership among workers. Rather than waiting for managers or specialists to solve problems, teams began taking proactive steps to define issues and prioritize them for resolution.
Step 2: Experimentation with the scientific method - From assumptions to evidence-based problem solving
Once problems were clearly framed, workers were guided to address them using Lean’s Plan-Do-Check-Act (PDCA) cycle. This structured approach encouraged teams to test small, incremental changes, evaluate results, and iterate based on their findings.
Previously, workers often skipped critical steps in their problem-solving activities, jumping directly to solutions based on intuition. The new system emphasized the importance of experimentation. Workers were trained to:
- Define specific hypotheses based on data.
- Design experiments to test these hypotheses.
- Reflect on outcomes and adjust their approach accordingly.
For instance, on the panes production line, workers identified that certain machinery experienced frequent short stops. Through small experiments, they tested adjustments to feeding mechanisms and operator workflows. Over time, these iterative changes led to an 8% improvement in productivity and a noticeable reduction in operator frustration.
Managers played a pivotal role in this phase. Instead of directing solutions, they acted as coaches, asking insightful questions and encouraging reflection – a shift that not only empowered workers, but also helped managers develop stronger leadership skills.
Step 3: Teaching others to learn - Creating a ripple effect
To sustain the gains made during the initial phases, VELUX introduced a hierarchical coaching structure. Senior workers, who had demonstrated proficiency in using data and solving problems, were trained to mentor their peers.
The coaching model had several benefits:
- Senior workers acted as role models, demonstrating the value of structured problem solving.
- Peer-to-peer coaching reduced reliance on managers and accelerated knowledge transfer.
- Teams became more cohesive, with workers supporting each other’s development.
In the flashing production department, for example, senior workers conducted training sessions on how to use IIoT dashboards to monitor unplanned stops. As a result, even less experienced workers became comfortable analyzing data and proposing solutions.
This approach also reinforced a culture of accountability. Workers began holding each other responsible for follow-through on improvement initiatives, creating a self-sustaining cycle of learning and growth.
TRANSFORMATIVE RESULTS: DATA-DRIVEN EMPOWERMENT
The impact of VELUX’s initiative was felt both in the company’s operations and in its culture.
Across three action cycles, the company achieved significant gains in operational performance, including a 50% decrease in unplanned stoppages in some areas, a productivity improvement of up to 12% in key departments, and measurable reductions in lead times and downtime.
These results validated the hypothesis that combining IIoT with lean principles could unlock previously untapped potential.
Perhaps more profound was the cultural transformation that took place on the shop floor. Workers who had once viewed themselves as passive participants now embraced their roles as active problem solvers. Collaboration flourished, with teams working together to identify and address issues.
As one worker put it: “Before, we waited for instructions from our manager. Now, we analyze the data ourselves, discuss as a team, and decide on the next steps. It’s empowering.”
LESSONS FROM VELUX: A BLUEPRINT FOR SUCCESS
VELUX’s journey offers valuable insights for manufacturers seeking to integrate Lean and Industry 4.0:
1. Leadership as enablers
Managers must transition from being directive leaders to facilitators of learning. By asking questions instead of providing answers, they can create an environment where workers feel empowered to experiment and learn.
2. Structured problem-solving routines
Daily routines like problem-framing sessions and coaching cycles embed continuous improvement into workers’ daily activities, ensuring that learning becomes a habit rather than an occasional initiative.
3. Empowering workers with technology
IIoT systems should be designed to serve workers, not control them. Making data accessible and actionable is key to fostering engagement and ownership.
4. Peer-to-peer coaching
Training senior workers to mentor their peers creates a ripple effect, spreading knowledge and reinforcing a culture of collaboration.
5. Patience and long-term focus
Instituting a supportive learning environment takes time. By prioritizing long-term development over short-term efficiency, VELUX ensured that the improvements were both meaningful and sustainable.
THE ROAD AHEAD: SCALING LEAN AND INDUSTRY 4.0 INTEGRATION
VELUX’s experience demonstrates that the true power of technology lies in its ability to amplify human learning and ingenuity. By investing in people, processes, and learning, the company successfully bridged the gap between Lean and Industry 4.0, unlocking benefits that extended far beyond operational performance.
As other manufacturers embark on their digital transformation journeys, VELUX’s story serves as both a blueprint and a reminder: transformation is not about replacing people with technology but about equipping them with the tools and skills to thrive in a digital world.
By embracing this human-centered approach, manufacturers can create workplaces that are not only more efficient but also more engaging, empowering, and resilient.
THE AUTHORS
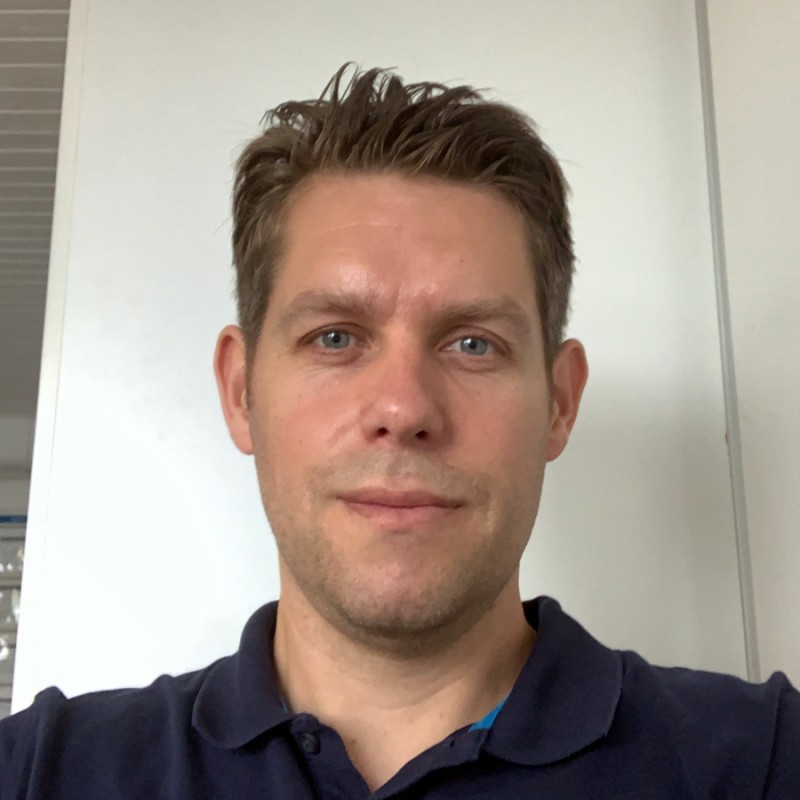
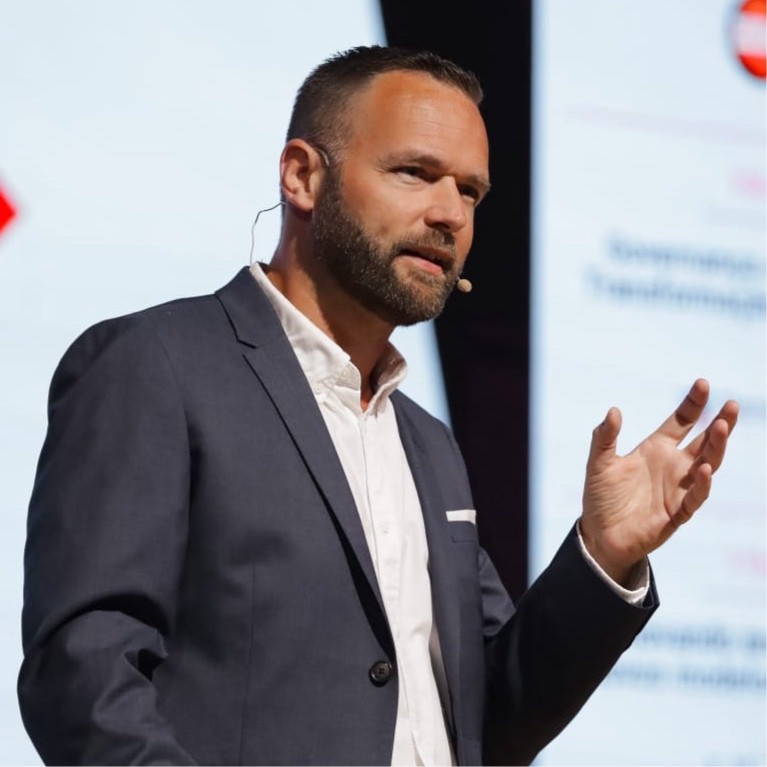
Read more
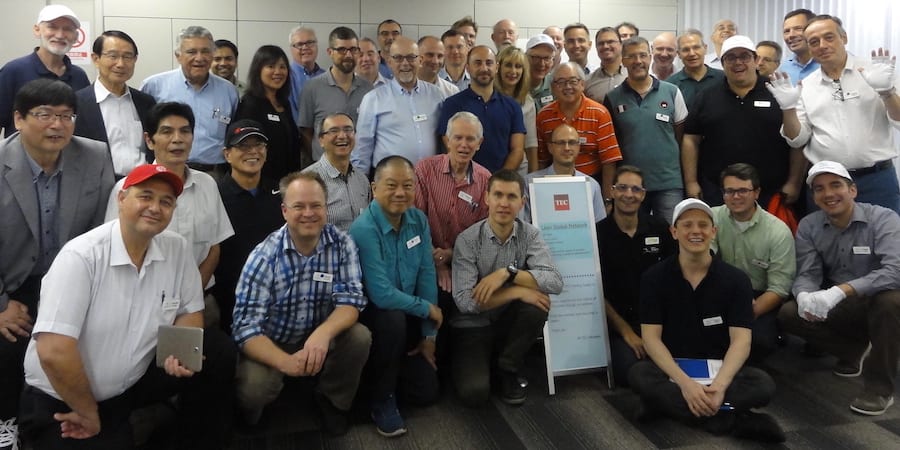
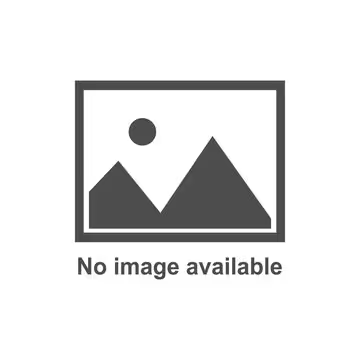
ROUND-UP – The Lean Global Network’s week in Japan in September was full of learning and inspiration. We asked five LGNers to share their biggest takeaways.
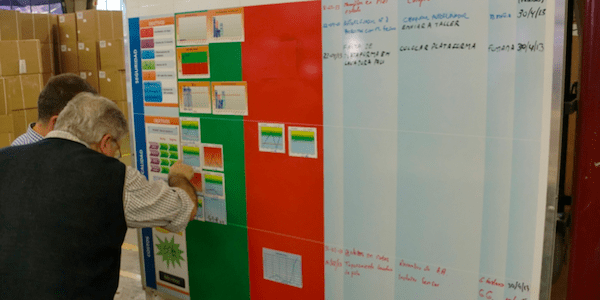
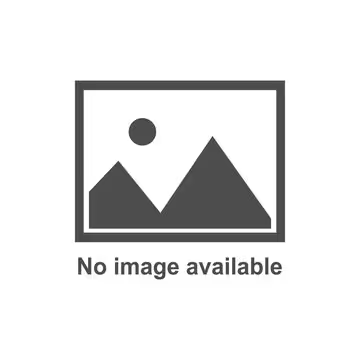
FEATURE - Strategy deployment is fundamental to a lean transformation, but managers often struggle to understand its importance amid the day-to-day firefighting. This article will tell you how to make hoshin happen.
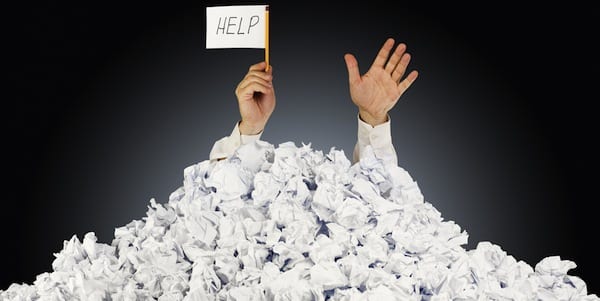
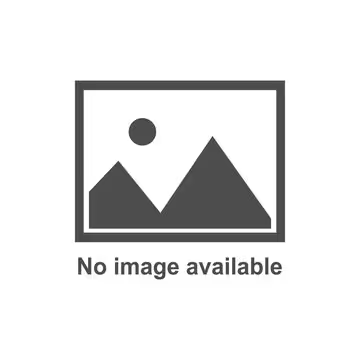
FEATURE - Develop your people if you want to develop a better (lean management) system in your business. This is the key message of this article, which looks at the role of management in an organization and in society.
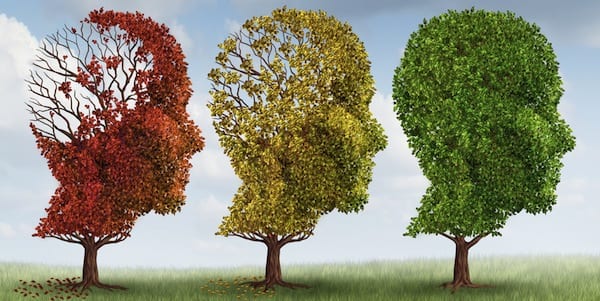
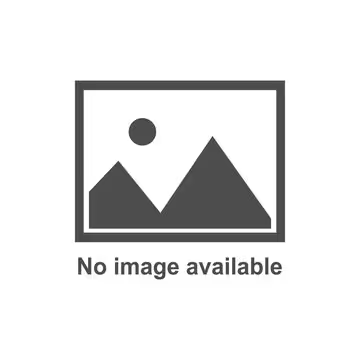
OPINION – How many times, in the early stages of kaizen events, have you thought about giving up? Hang in there. As frustrating as they can be, they will also teach you a lot, says our Danish colleague.