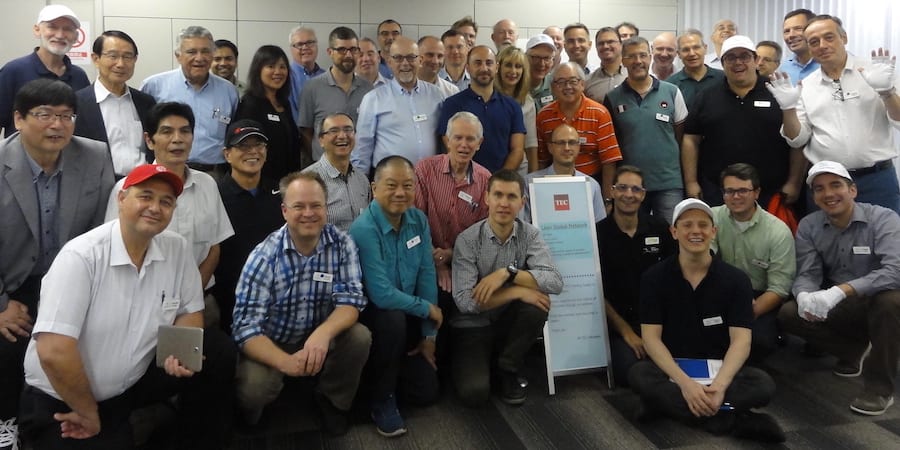
Five key takeaways from our lean week visiting Toyota
ROUND-UP – The Lean Global Network’s week in Japan in September was full of learning and inspiration. We asked five LGNers to share their biggest takeaways.
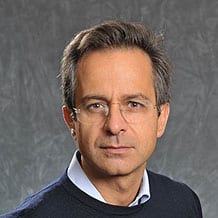
Arnaldo Camuffo, President, Istituto Lean Management (Italy)
One of the highlights of the LGN Japan Tour for me was the visit to Toyota Industries’ Shokki plant and our time with Sadao Nomura, a Toyota veteran of 35 years who led the site’s remarkable turnaround over the past decade. The change effected was clear during our gemba walk, in a variety of ways, from the focus on developing young workers’ capabilities to the state-of the-art application of lean tools on the assembly line. Interestingly, we saw no huge investment in technology, but a well-thought-out balance of robotics and human work, with the former at the service of the latter. On my flight back to Italy, while reflecting on what I learned, it occurred to me that, at least in Europe, we might be putting too much emphasis on new technologies, digital transformations and Industry 4.0. There is nothing more revolutionary than Eiji Toyoda’s motto “Good Thinking, Good Products”, a fundamental reminder that modernization doesn’t come from acquiring new machines, but from developing new thinking as a result of problem solving.
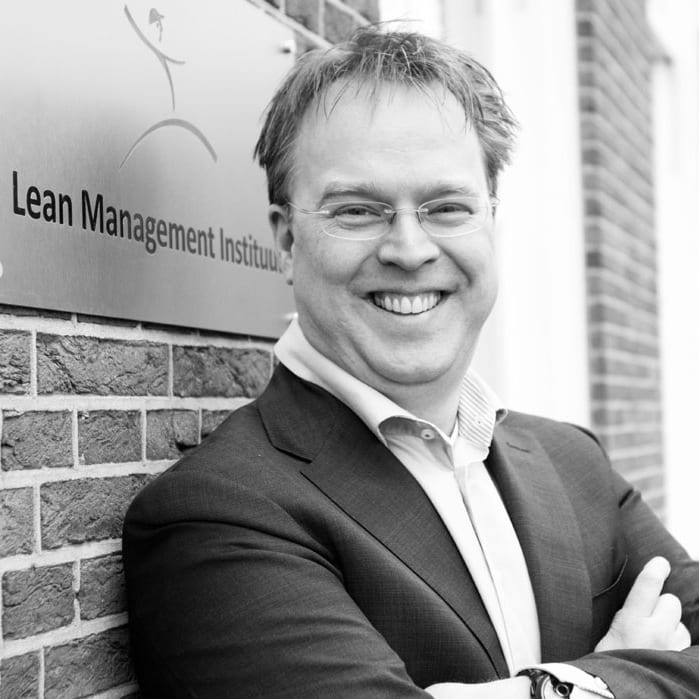
René Aernoudts, President, Lean Management Instituut (Netherlands)
Toyota keeps amazing me. I learned so many things during our week in Japan, and was really inspired by what I saw. In particular, I was struck by the following: the rigor Toyota uses in trying to minimize the use of carbon-based energy in their factories (using photolytic paint on the external walls and gravity for transporting parts in the plants); the importance of having key TPS people leading the way in factories in their role as Plant Managers; the use of paper, magnets and simple tools to run the entire process instead of IT systems; and their ability to reach 1 PPM with 80% external people in their Spare Parts Centre. All in all, a very interesting trip!
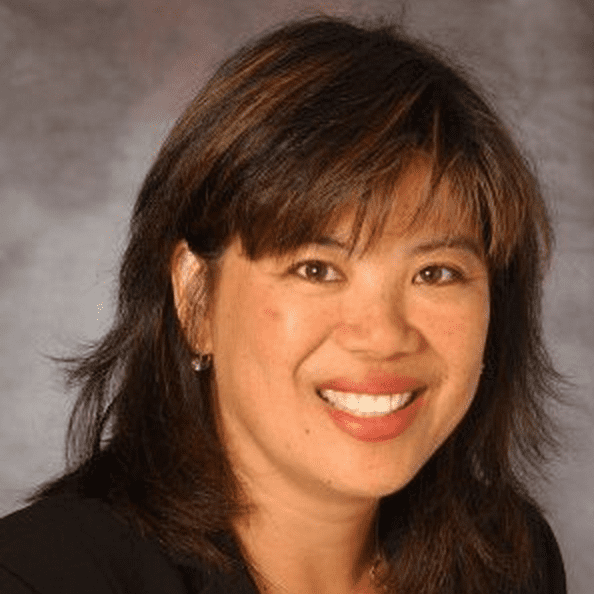
Alice Lee, Executive Director, Lean Enterprise Institute (USA)
Toyota’s focus on teaching people is key to helping them to maintain their skills. I really like that they practice what they preach. I, too, love to teach: people often prefer to work on the technical stuff and don’t enjoy the teaching, but truth is that you can’t do one without the other. I also enjoyed learning about Toyota’s Back to Basics approach. It got me thinking about the level of humility that senior leaders in the organization must have had to make that call. Recognizing you have made a big mistake and need to rectify it immediately is a very hard thing to do, especially if we consider the way senior execs normally think (profit, profit, profit). That way of thinking is incredibly rare to see.
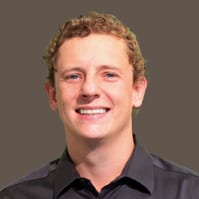
Flávio Battaglia, Director, Lean Institute Brasil
One of the main takeaways for me was how clear the purpose is in the minds of everyone working at Toyota. In every process we saw, in every area of every plant we visited, the first thing people shared with us was their purpose, the problem they are trying to solve. Another thing that struck me is how willing to teach others the senior guys are, which was really beautiful to see and is a powerful reminder for us all. It was also great to see a high-performing company that is still looking to effect major change! Everywhere we went, we were told that things were not good enough and that they were now going for system kaizen. People talked to us about “unprecedented change”, and it’s clear that Toyota has the muscles for it: at the Oguchi service parts plant, they have a seven-day inventory turnover, but that’s not enough and they want to get down to five.
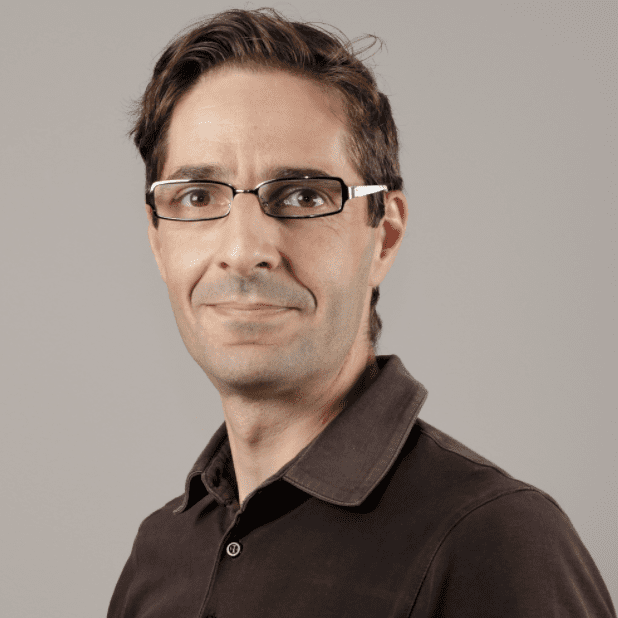
Sérgio Caldeirinha, President, Lean Academy Portugal
I arrived in Japan with a very clear expectation of what I wanted to learn. My intent was to understand how Toyota has been able to retain its mastery over many decades. In particular, I wondered how they recruit, how they build capabilities, and how they engage employees. I am happy to say I found conclusive answers to each of my questions:
- To evaluate each person’s potential, Toyota uses a formula:
Output=α x [Σi (Personality) x (Ability/Skills) x (Motivation)]
I can only conclude they use the same approach to select new hires. These come from a number of different places, like the Toyota Technological Institute (check out how the courses are structured and the learning dynamics here www.toyota-ti.ac.jp ), Nanzan University and Aichi University.
- To develop people’s skills, I saw a very advanced use of dojos (a place of learning and training in a plant, where the work experience is mimicked). New hires train here for a whole month, with practical and theoretical evaluation throughout the process.
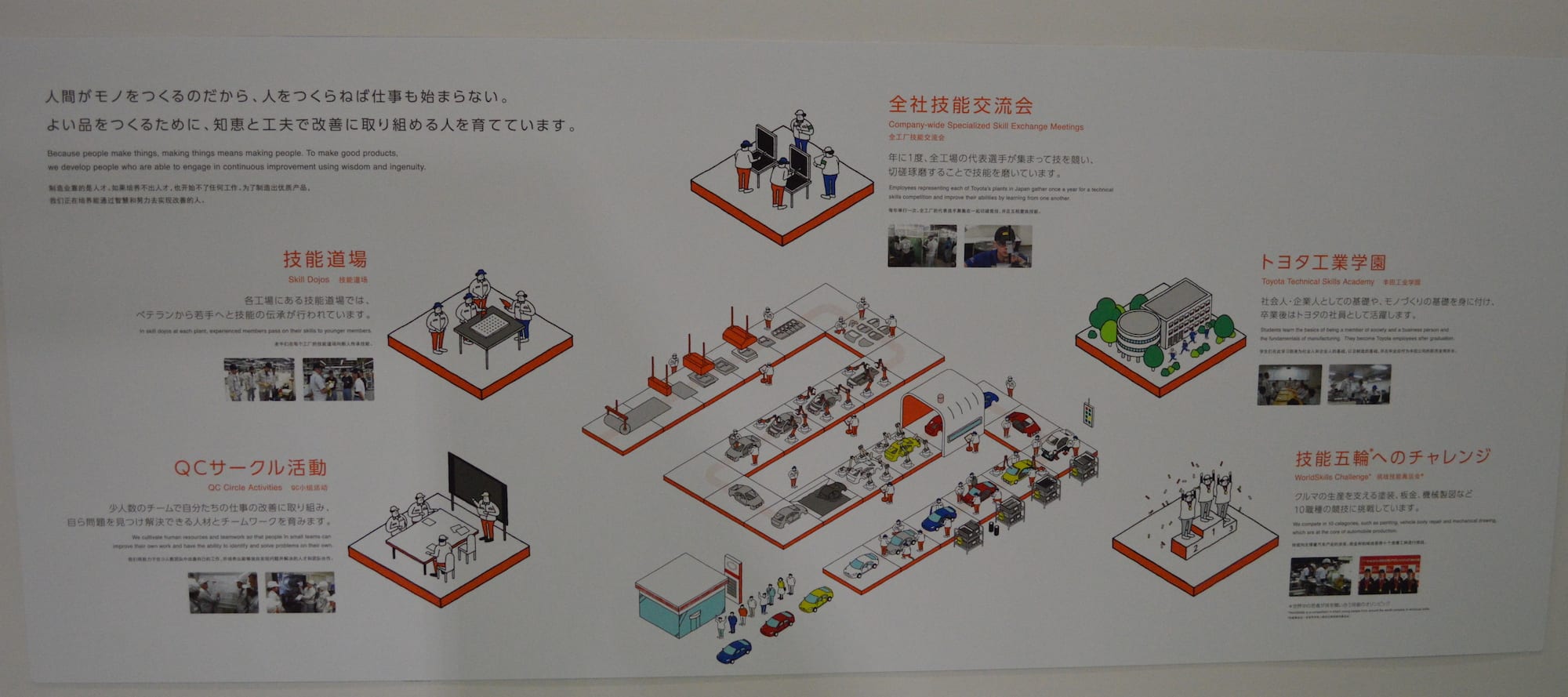
- At Toyota, engaging workers means letting them do the work, providing them with feedback, giving them exposure so they are pleased and develop the will to start a new cycle of improvement. This is amazing in its simplicity.
To conclude, I think it’s clear that people are Toyota’s biggest asset. They represent a straight path to sustainable continuous improvement.
To read more about our trip to Japan, don't miss these articles by Jim Womack and John Shook.
Read more
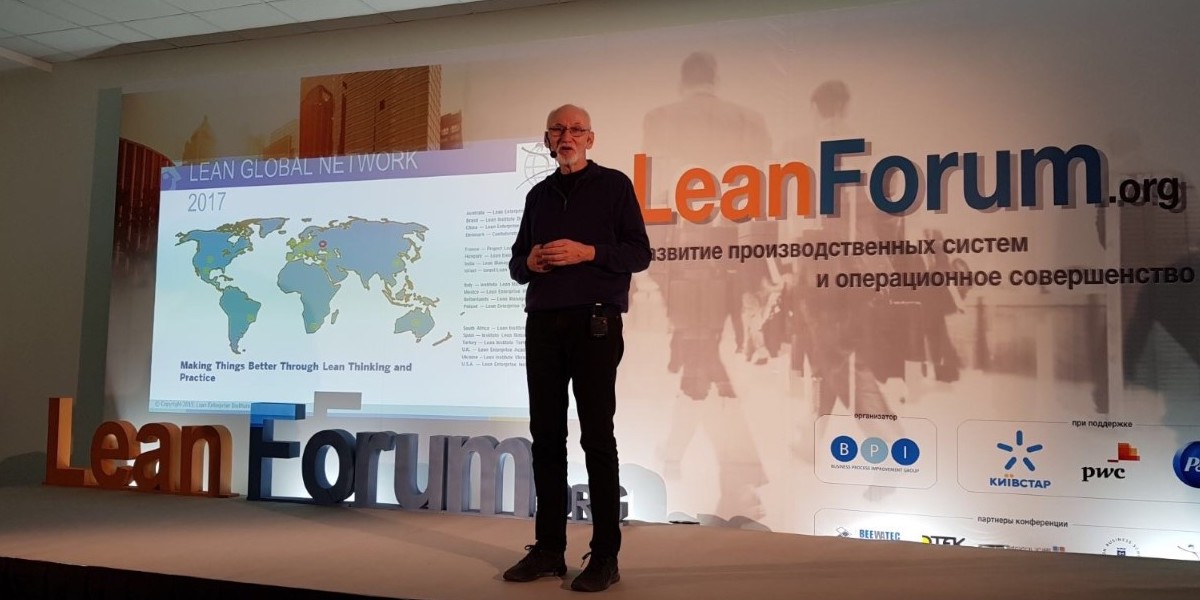
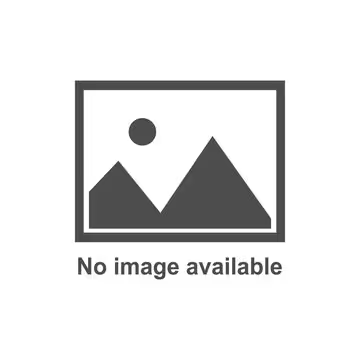
FEATURE – As the senseless war in Ukraine continues, the author looks back to his visit to the country in 2017, recalling and celebrating its vibrant lean community.
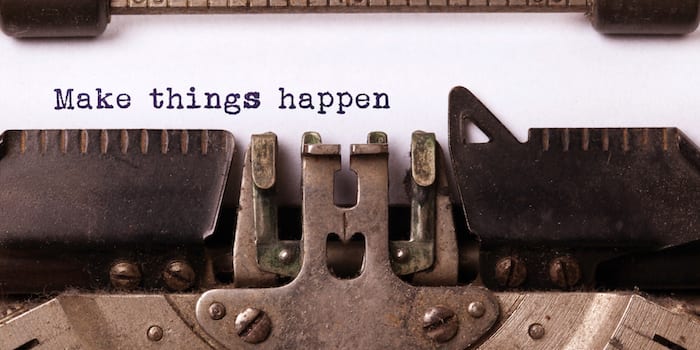
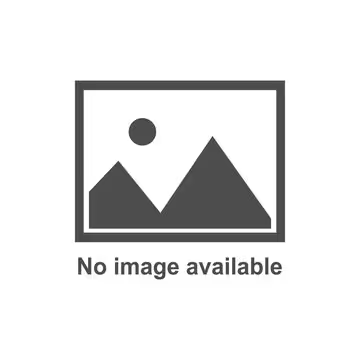
RESEARCH – The authors present a new perspective on value creation. In addition to monozukuri (making things) and hitozukuri (making people), they discuss the idea of kotozukuri, making things happen.
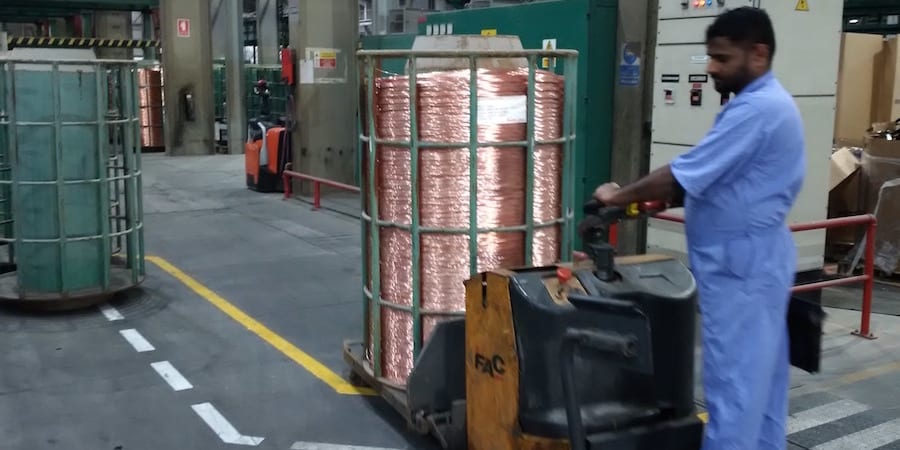
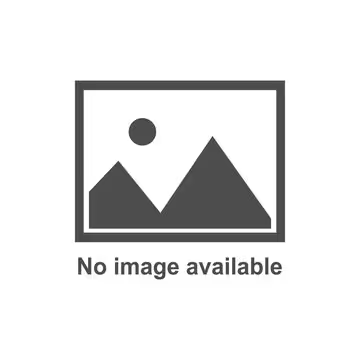
FEATURE – With an open-minded approach to improvement tools, a long history of quality and engaged top leaders, wire manufacturer Ducab aims to fulfil the strategic needs of the Emirates.
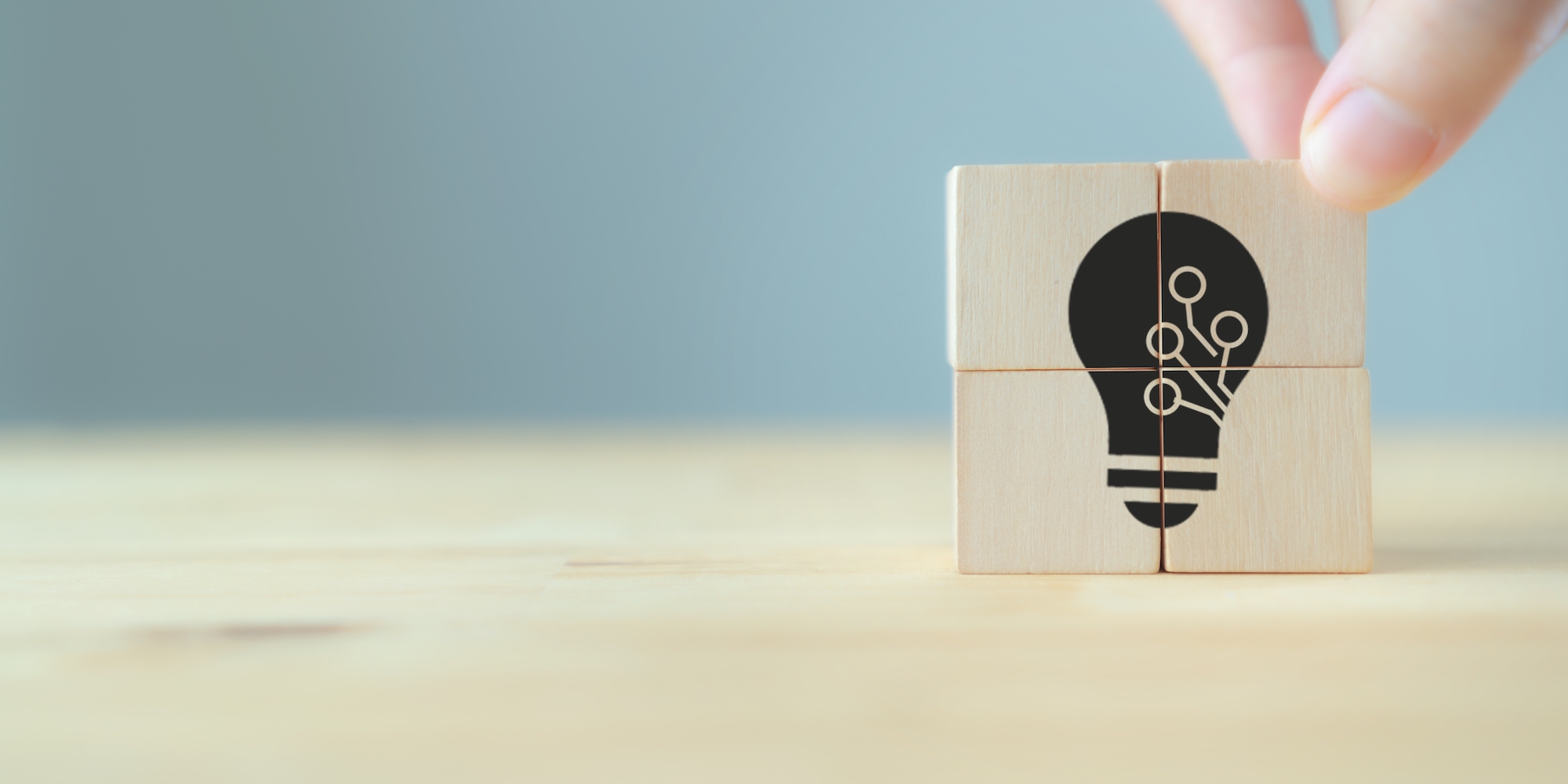
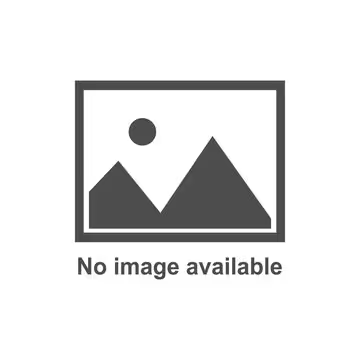
FEATURE – The authors explain why putting value at the heart of customer discussions is key to developing a successful, resilient tech firm.