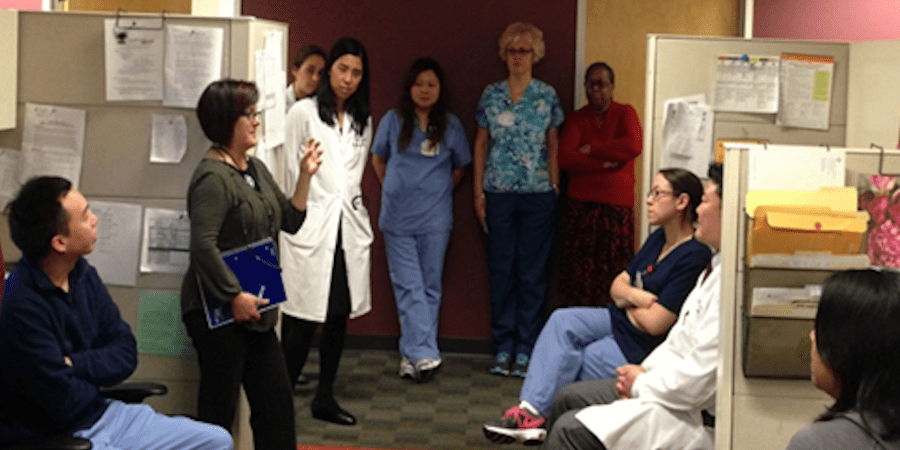
A California lean hospital on how to sustain results
FEATURE – The Palo Alto Medical Foundation has used lean to redesign workflows in its primary care clinics since late 2011. With changes now spread to a total of 17 facilities, the team started to analyze what it took to sustain the results achieved.
Words: Dorothy Hung, PhD; Carrie Gray, PhD; Mike Conroy, MD; and Terrigal Burn, MD
At PAMF, we have been working with lean thinking for the past five years to redesign primary care workflows. We started with one pilot clinic, but have now brought the methodology to seventeen facilities.
Our research team recently conducted an evaluation of our implementation of lean and found that, since the approach was first introduced, efficiency has improved in our clinics without harm to quality. We have also confirmed that the performance improvements we achieved were sustained for periods ranging from 13 to 25 months, which suggests that lean is a viable long-term strategy for enhancing the delivery of care.
The literature on the use of lean in healthcare is rich, but what still seems to vex scores and scores of lean practitioners (in healthcare as in any other industry) is the question: "What is the best way to maintain lean results?"
Because most of PAMF's original lean redesigns have been sustained (and those that proved problematic are now subject to further analysis and modification) and many of our clinics are making impressive progress towards developing a culture of continuous improvement, we believe that our experience can be of help to other organizations wondering how to make their transformations last.
We have identified five elements that have helped us to maintain a pervasive culture of continuous improvement, which we find critical to making lean a part of every-day life at the front line. Let us take you through them.
1. THE IMPORTANCE OF LEADERSHIP BUY-IN
In order to succeed, lean initiatives require a shift in culture – the way people think about their jobs, how they interact with each other, the kind of information and data they need. So, while advocating for this change begins with executive leadership, we believe that the support of lean goals and objectives should be actively aligned across all levels, from executive to mid-level to front-line management.
Our organization implemented lean in phases across the delivery system. In the first phase, the pilot clinic, great effort was put into garnering leadership support at all levels, from regional directors to staff supervisors. These leaders were trained in lean concepts and invited to visit other organizations that have successfully gone through a transformation and that now have a fully developed lean system in place. All ranks of leadership were present and involved with creating new workflows in the pilot clinic site. As a result, this clinic continues to experience a high degree of sustainment. It is great to hear members of staff describe lean as "just the way things are".
In contrast, regional leaders and supervisors in the last phase of implementation of lean in the clinics had admittedly less exposure to other lean systems and less direct involvement in designing new workflows. The hope was that they would be presented with work designs developed at the pilot site and that they would be able to adapt them to their own local environments. In retrospect, we found that this created resistance among clinic leaders and front-line staff who did not have the same sense of ownership of the workflow designs. The best way to sustain hard-fought lean results is to engage the workforce as much as possible, in all phases of the implementation and at every affected location.
Importantly, to facilitate a successful lean initiative, we found that leader engagement in a set of standard work activities not only fosters buy-in, but ultimately helps to sustain changes at the front line. Such activities include facilitating weekly meetings within departments or regions to communicate where people are, where they are going, and to review progress. Other responsibilities involve conducting observations at site visits to assess whether envisioned changes are being accomplished, and regular review of display boards that present work being done. This review creates a platform for future improvements, including those that incorporate ideas suggested by front-line physicians and staff.
In the absence of leader commitment to this standard work, we believe employees may be less likely to sustain lean changes after the organization has moved on to other priorities. As a result, if some leaders remain skeptical about engaging in such activities or decide that the new responsibilities are not right for them, it could lead to difficult conversations as the organization may be faced with the choice of finding leaders more attuned to lean management.
2. CREATING A CULTURE OF "PROBLEM UNDERSTANDERS"
We often hear about creating a culture of problem solvers, but based on our experience it is important, as a lean organization, to strive to be both problem solvers and problem "understanders". The notion is that if people understand the problems, the solutions will come forward. Practical ways to better understand issues include: root cause analysis, routine data collection, and A3 thinking.
A manager at one of our clinics described how lean impacted her own approach to addressing an apparent shortage of medical assistants. While the most obvious solution might have been to hire more staff, she instead dived deeper into the issue using root cause analysis. She found that there were adequate numbers of medical assistants, but that they were spread evenly across the day rather than being assigned to meet variations in patient load. The solution was not to hire more people, but to change the allocation of hours to accommodate peak schedules. She admitted that before her lean training, she would probably have jumped quickly to the "obvious solution" of hiring more staff – which would have turned out to be a costly and wasteful way to deal with the problem.
PAMF introduced daily huddles among physician and medical assistant teams to help them understand and address potential problems in their daily workflows. We found that huddling calls forth a proactive mindset, since staff identifies barriers to patient care at the start of each day rather than putting out fires throughout their shift. During the huddles, the team identifies "flow busters" – including patients who may need more or less time than allotted, as well as patients who may need additional assistance getting to and from the exam room. When physicians do not prioritize the huddle, they could possibly lose the opportunity to approach patient care more proactively, as many admit that failure to address issues at the start of the day leads to a more chaotic and stressful work day.
3. PROVIDING LEAN EXPERTISE AND SUPPORT
A common approach today in many healthcare organizations is to hire external lean consultants to come onsite to conduct rapid process improvement workshops. While this allows employees to learn about lean tools while accomplishing major changes in a relatively short period of time, without a long-term plan for sustainment those improvements can easily fall by the wayside after the consultants have left.
This is why our organization chose to house an expert team within a newly created Lean Development Office (also commonly known as a Lean Promotion Office or Kaizen Office). Such offices are staffed with internal consultants who have received specialized lean training and are available to train leaders and facilitate improvements, particularly when dedicated resources within the organization are needed.
Lean consultants and coaches were particularly helpful in clinics where there was a high degree of resistance among physicians and staff. Well-versed in change management strategies and able to draw on their experience with other organizations, the consultants were able to provide an "outsider's view" by recommending effective strategies for facilitating acceptance of lean redesigns. Our Lean Development Office also played a major role in turning our leaders into lean leaders through one-on-one coaching. This involved assistance with maintaining an effective daily management system, which includes leader standard work activities as we described above. Doing so ensures that there is a regular cadence to departmental meetings, observations of employee work, and long-term engagement of the workforce.
4. MEASURING AND VISUALLY DISPLAYING PROGRESS
Our experience showed that tracking the outcomes of lean improvements is also essential for sustainment, as itprovides tangible evidence of the effectiveness of changes that are made. We found it particularly important to collect real-time data, which allows for immediate action and is critical to getting physician buy-in. As a result, appropriate systems are required to capture the needed data, and the IT or Quality Planning departments may need to build the necessary infrastructure.
Demonstrating that the organization is achieving targets initially set forth will also help to keep employees engaged in the process.To this end, we learned that an important follow-up to data collection is visibility in the form of posted metrics, typically on large dashboards displayed on clinic walls. In our organization, metrics are posted on "tiered checking boards" located throughout hallways and administrative areas where physicians and staff are co-located. These metrics should reflect what people are working on and enable front-line employees to tell others what they are doing, including how it connects to other improvement activities occurring across the organization.
Our experience shows that metrics should always reflect information that is meaningful to physicians and staff for their day-to-day activities. Likewise, display boards are best tailored in a way that is easily understandable, user-friendly, and accessible to anyone who views it. Several years into our lean transformation, leaders realized that their tiered checking boards were not being used as intended: staff dismissed them as meaningless "wall paper" along back-office hallways. A group of physician leaders and managers came together to redesign the boards to enhance their usability. They streamlined the number of metrics that were being displayed at any given time, and more clearly presented data on the progress of the improvement projects on which front-line employees were working. When designed well, these boards came to serve a valuable function by fostering engagement and sustaining momentum of lean activities.
5. EMBRACING LEAN AS A FRAMEWORK FOR CONTINUOUS IMPROVEMENT
The final fundamental lesson we learned is that we must recognize that lean is not a collection of design initiatives, but an overarching framework for continuous improvement. When organizational members understand and embrace this approach to their daily work, sustainment is likely to become embedded in the process rather than any specific product of their efforts.
Our leaders found it helpful to convey a fundamental premise of continuous improvement: that solutions may not be perfect and can always be improved. The key is to make incremental progress today as opposed to waiting until the solution is deemed perfect. Even if problems are incorrectly scoped at the beginning, it matters less when the expectation is that each step creates learning and therefore represents forward movement.
Bringing to life the tenet of continuous improvement at the front line creates an environment in which employees have a greater sense of purpose in improving their work, are more committed to the organization, and are happier because they have made a difference. With this in mind, we found that a framework for continuous improvement is firmly in place when one can tell from the ground up that the front lines are engaged in understanding and optimizing the work that they do.
TO CONCLUDE
In this article, we shared our experience of what it takes to sustain your lean efforts. If done well, the initial implementation strategy will lay the foundations for a deeply-rooted culture change – which is vital to sustaining a lean turnaround.
Because lean thinking focuses on respect for people and the employees' knowledge of the work, sustainability will depend on the degree to which the organization is adaptive to their needs and continually pursuing improvement. Ironically, one of the major facilitators in sustaining a lean redesign may simply be time: it takes time for people to understand what is being asked of them, and it may be initially daunting for employees to propose running an experiment in the context of their daily work. It also takes time for them to trust the process of doing things differently, particularly as lean techniques encourage more front-line engagement than do traditional models of management.
Culture change can take years, and the benefits of a lean transformation are not expected to materialize in the form of short-term returns. Implementing lean is an investment that will produce long-term gains, if done well. The fruits of a mature lean system will come forward for those who are willing to commit to change and stay the course.
Acknowledgement: The authors would like to thank Michael Harrison, Ph.D., and Rod McCurdy, Ph.D., for their valuable insights and feedback during the preparation of this work.
Disclaimer: The research reported in this paper was funded by the Agency for Healthcare Research and Quality under contract HHSA2902010000221, Task Order 2. The views expressed in this paper are solely those of the authors and do not represent any U.S. government agency or any institutions with which the authors are affiliated.
THE AUTHORS
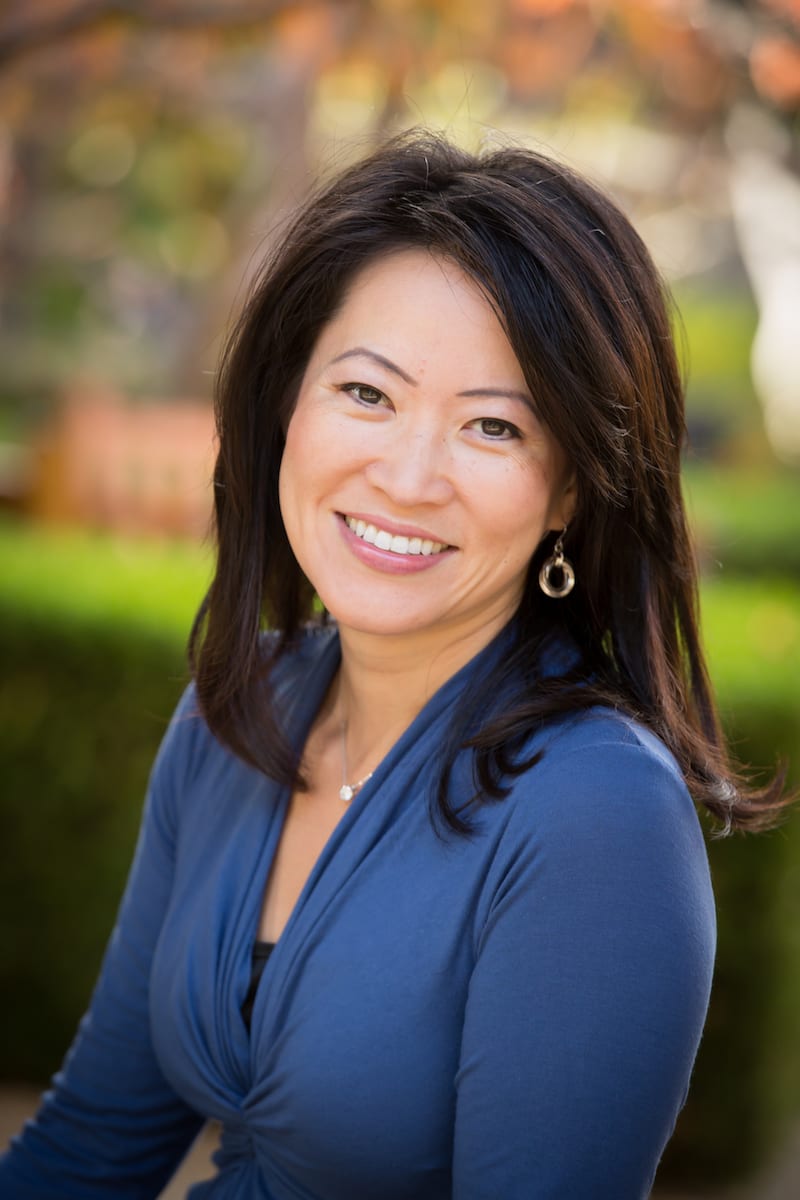
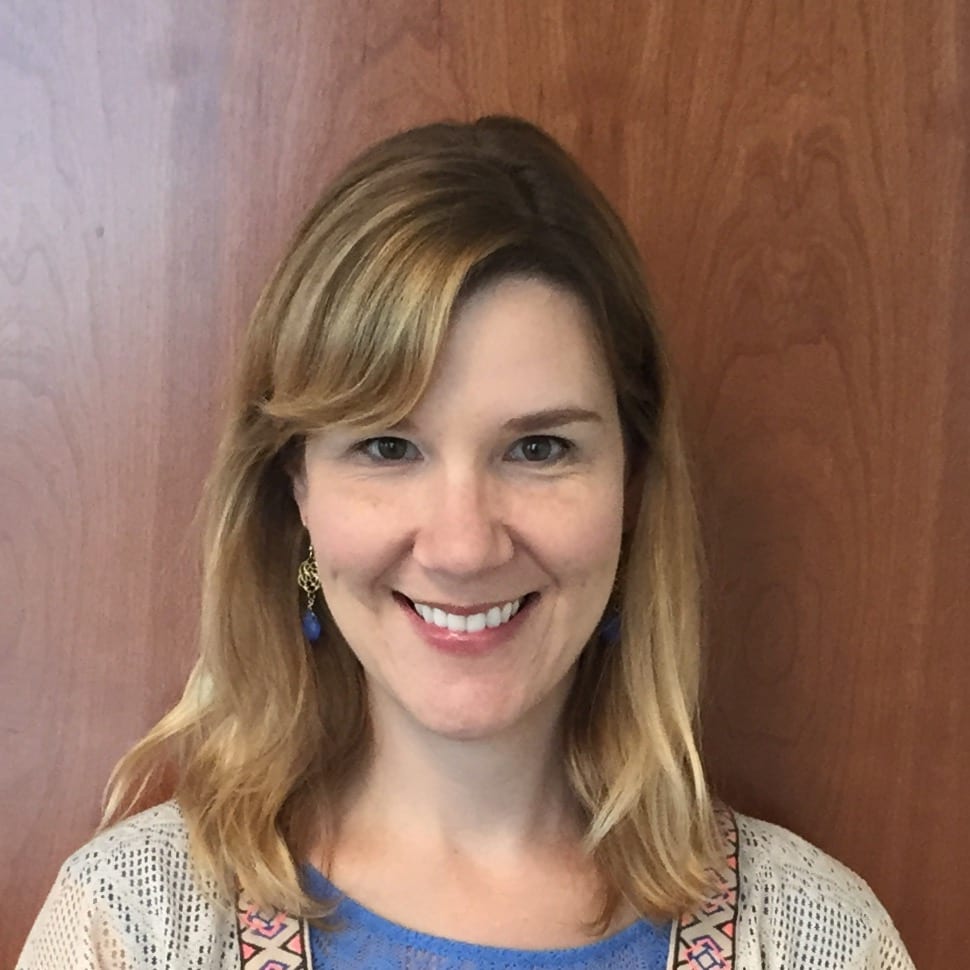
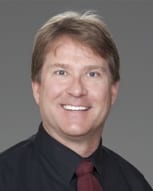
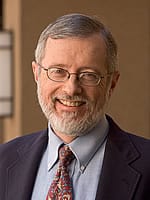
Read more
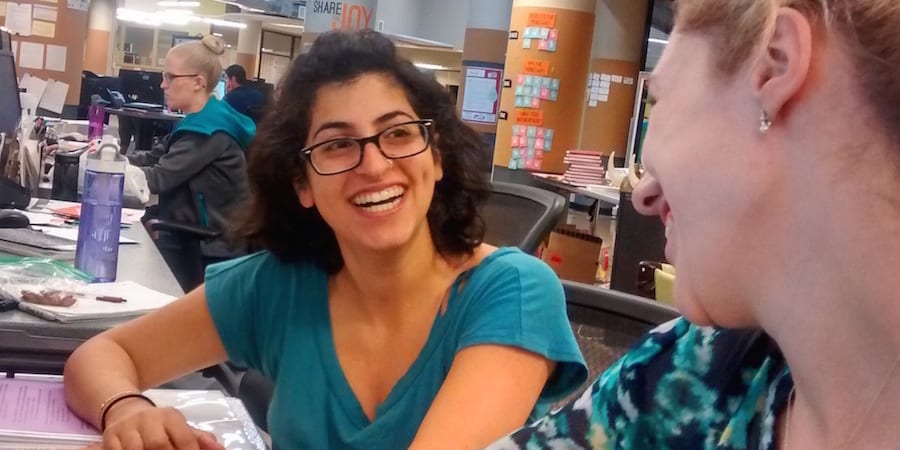
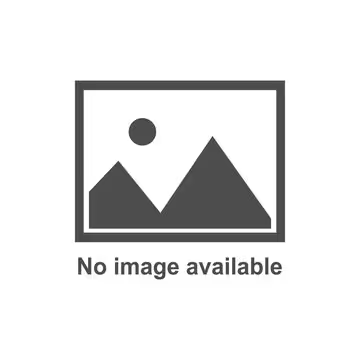
COLUMN - Menlo Innovations may not define itself as a "lean organization" but there is no doubt that its management style is akin to the principles lean teaches. Here, a front-line Menlonian shares her thoughts on the company's culture.
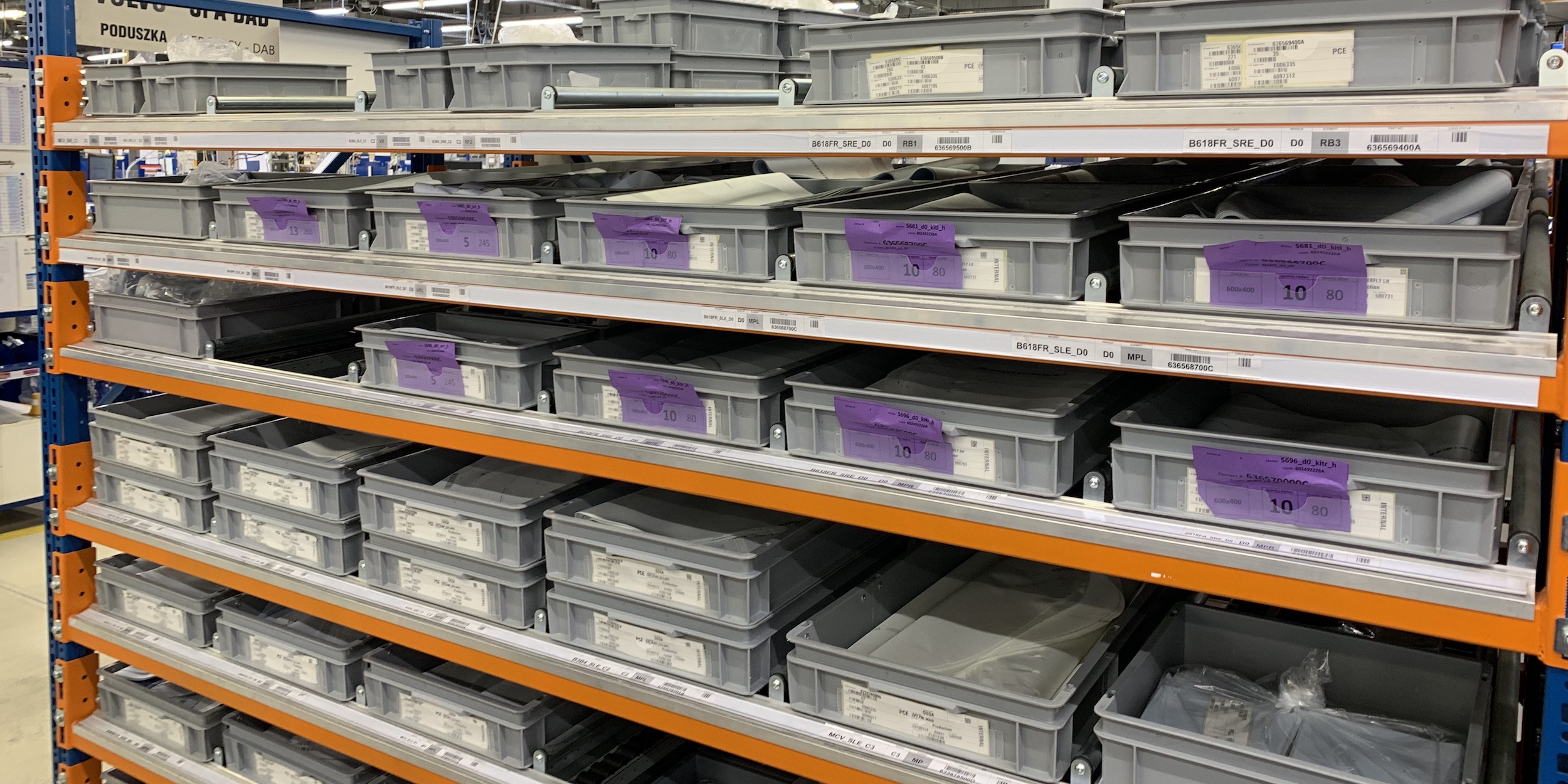
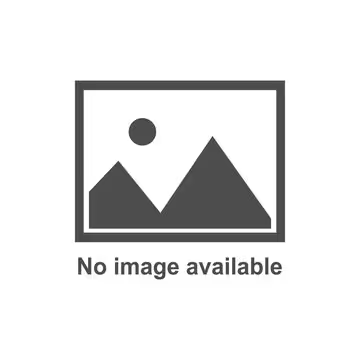
THE NAKED GEMBA – Our new series goes back to basics to unlock the secrets of the gemba and tell us about some of the main tools and techniques we can use in a lean transformation. First up, supermarkets.
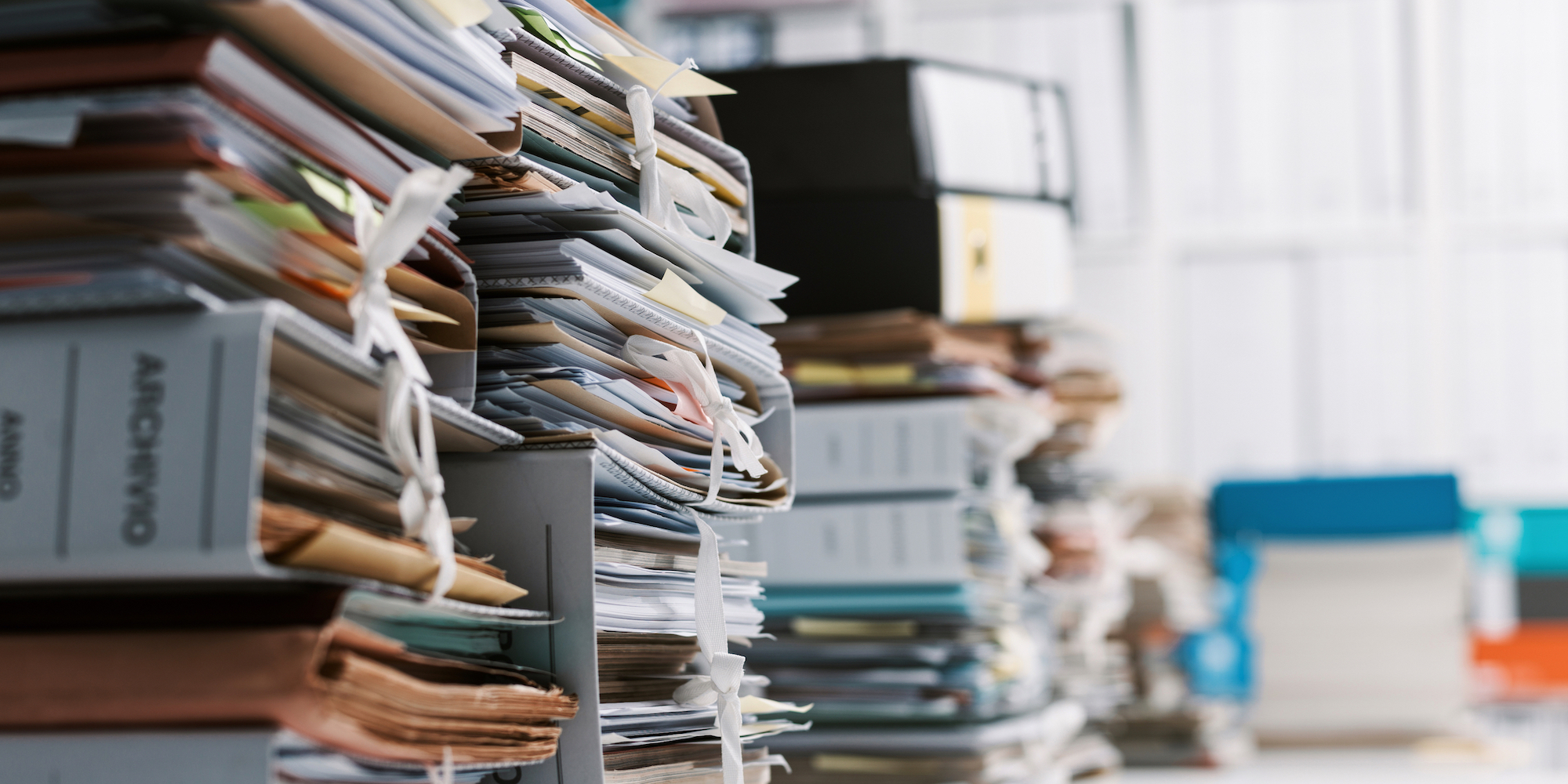
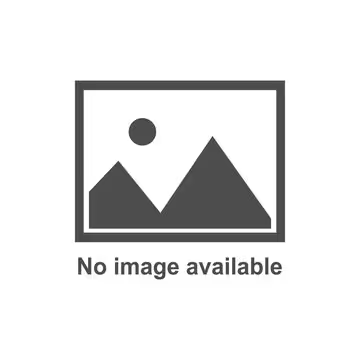
FEATURE – As our social systems grow, we need an effective way to manage them. This makes bureaucracies an inescapable part of life for our society and businesses. But how can we mitigate their negative effects?
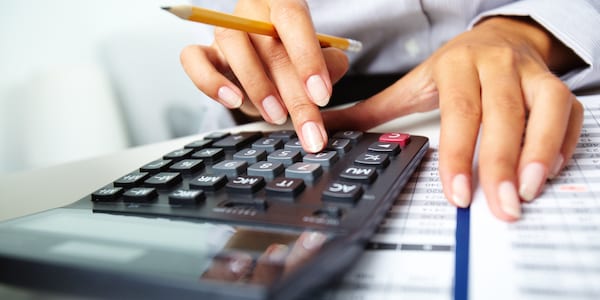
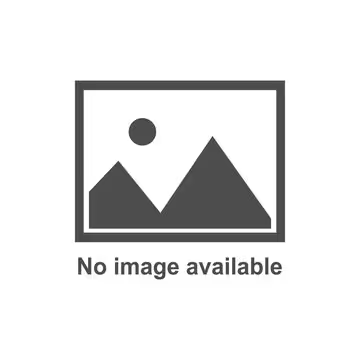
FEATURE - Every part of an organization can benefit from the adoption of lean principles, but what about accounting? Here are a few useful tips to efficiently close the books at the end of each month.