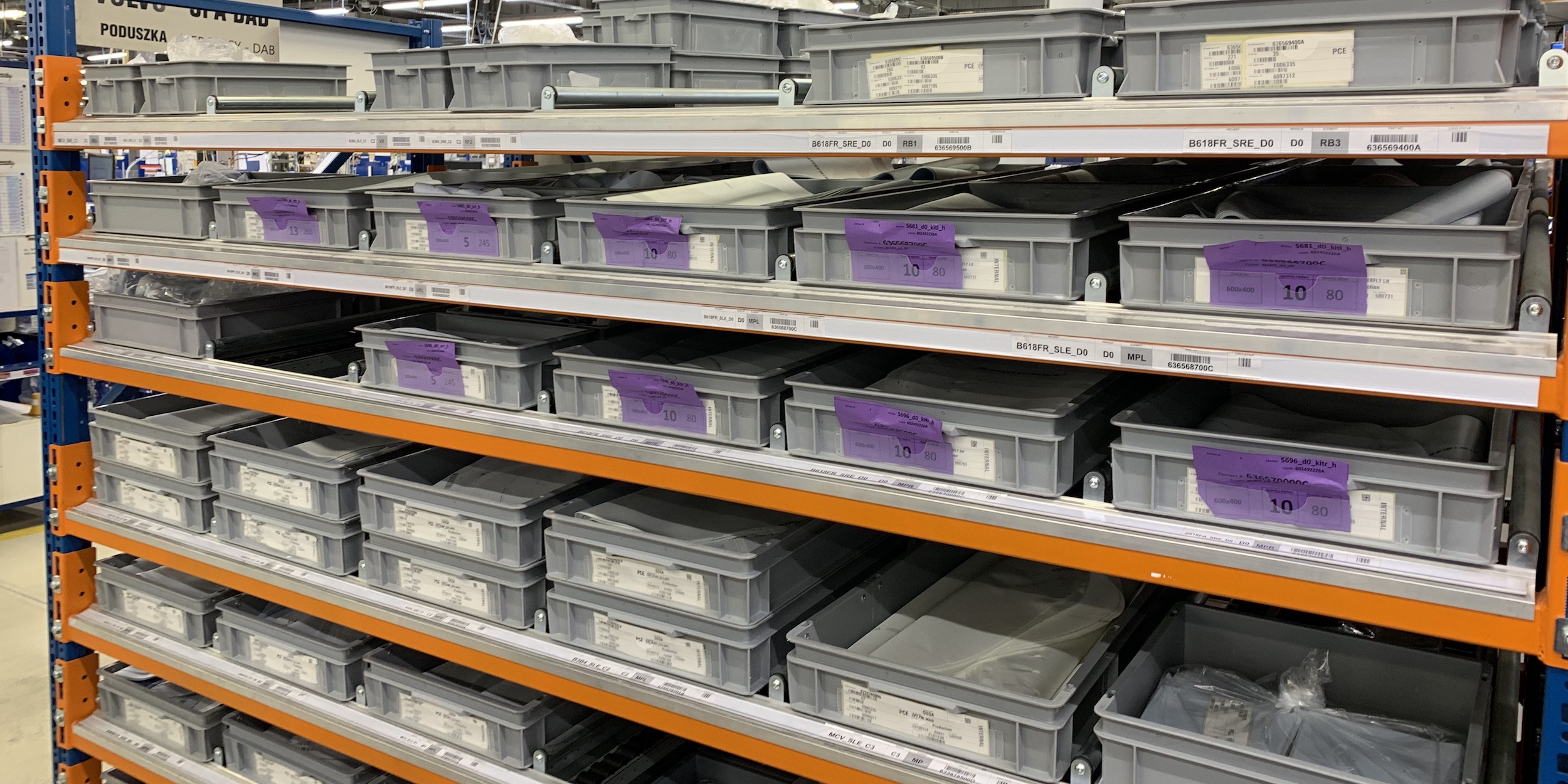
What a good supermarket looks like
THE NAKED GEMBA – Our new series goes back to basics to unlock the secrets of the gemba and tell us about some of the main tools and techniques we can use in a lean transformation. First up, supermarkets.
Words: Severino Abad Pequeño, Lean Coach, Instituto Lean Management
We often define the ultimate goal of lean thinking as the “full satisfaction of client needs by continuously producing and delivering what the client wants”. This idea naturally leads us to embrace the concept of flow, and to reduce or altogether eliminate everything that interrupts that flow (which we typically refer to as “waste”).
However, “flowing” products or services to customers in a continuous fashion and in the way they want them is often easier said than done. There can be many reasons behind this – from the presence of waste to the non-exclusivity of a process (while I produce for one client, I can’t use the same equipment to produce for another), from an uneven production pace for different stages of the work (due to different cycle times or the need to operate using different batches, for example) to different shifts for the client and the supplier.
These elements, typically, can contribute to the interruption of the flow and result in an increase of our lead-times and the associated levels of work-in-process (WIP). To manage these interruptions, lean organizations often rely on the so-call "supermarket".
As a way to manage this problematic material flow, a supermarket carries extra items in a quantity that ranges between a minimum and a maximum that are determined by the size of the interruption it is meant to tackle.
A supermarket should be associated to a pull system. So, when the quantity of material reaches a low level, a replenishment request could be generated to the supplier of the material, in order to keep the level.
CHARACTERISTICS OF A SUPERMARKET
There are a number of elements that we can use to identify a supermarket at the gemba. Let me describe them.
- Supermarkets are located between loops, steps in the process that can work together with no interruption. To belong to the same loop, the operations in a sequence need to: have a similar production pace (similar cycle times, downtime, changeover times, etc, and the same batch of operations); have similar requirement for workers (operators in the same loop need to be able to reach a certain level of multiskilling); be located close to each other.
- Supermarkets on a factory floor are remarkably similar to regular supermarkets where we buy groceries: within a few meters, they must give us access to a wide range of products. In fact, history tells us that Taiichi Ohno found his inspiration in supermarket aisles, which is why the supermarkets we are talking about in this article are generally organized in shelves.
- Shelves are filled by the supplier on one side and picked from on the other side, in a way that the FiFO sequence is followed and that everyone involved can immediately see the state of things. This means the supplier will see “holes” appear (signaling that the client has consumed the product), where he will place new materials, and the client will always have the item he needs readily available. Using the principles of karakuri, the shelves are typically inclined to allow for easy picking. Such a shelving system fosters ownership of different parts of the gemba, since the supplier won’t have to invade the space of the client to supply materials and the client won’t have to leave his working area to pick up what he needs. The client doesn’t need to know where the supplier is; he just needs the material to work (in cases where the supplier is located far from the client, the company’s dedicated department will act as a bridge between the two).
- The different items in a supermarket have a specific location and are organized in the exact quantity in which they are needed. This ensures the team has the right information on what materials were used and what weren’t, and therefore what materials need to be replenished and what don’t.
- Materials are normally placed in plastic boxes, whose size depends on the size of the material, the supplier’s batch size or frequency of supply, the speed of consumption, and the available space.
- Each box is identified by a tag that shows what item can be found in the box, the supermarket in which it is located, the supplier and the quantity.
- The number of boxes in the supermarket depends on the total number of items to supply, which in turn depends on the size of the interruption we need to manage with them. We can have different quantities of the same material, based on the situation we are facing. Cycle stock is the quantity necessary to guarantee supply to the client while the supplier is producing other items or serving other clients (it is directly proportional to the lead-time of replenishment and inversely proportional to the takt-time of consumption). Buffer stock is the quantity we need to add to the cycle material to allow for small variations in demand (careful not to confuse variation or fluctuation with seasonality), and it is directly proportional to the rate of service we are offering the client. Safety stock is the quantity of material we need to place in the supermarket to protect the client from the shortcomings of the supplier. It is directly linked to the level of inefficiency the supplier experiences.
- Each box leaving the supermarket (because it’s been used by the client) generates a replenishment signal for the supplier, which can come in many forms: 1) the same tag identifying the box can be placed in a mailbox and sent to the supplier (once the new material is ready to be placed in the supermarket, the label will go with it in the next box). This Kanban card identifies the material when it goes with it and becomes a replenishment order when it is separated from it. 2) Instead of taking out the label and send it to the supplier, we send the whole box. This way we will have a Kanban container that be directly refilled by the supplier in the quantity displayed on the label. 3) The simple appearance of a hole in the supermarket can act like a signal that a specific item must be replenished in the defined quantity. For this technique to work, the supermarket has to be visible to the process pacemaker so that the right decision can be made. 4) In recent years, the use of electronic Kanban cards has become more and more prevalent. This works just like a conventional card, the only difference being that instead of using the same label to signal the need for new material, a new order is generated electronically. E-kanban cards are particularly useful when the supplier is located far from the client.
It’s important to remember that as useful as they are, supermarkets are still inventory and, therefore, represent waste. For this reason, we need to strive to reduce their size as much as we can and eventually eliminating the, by acting on the very same causes that make their existence necessary.
To learn more about supermarkets, don't miss one of the great lean classics: Making Materials Flow.
THE AUTHOR
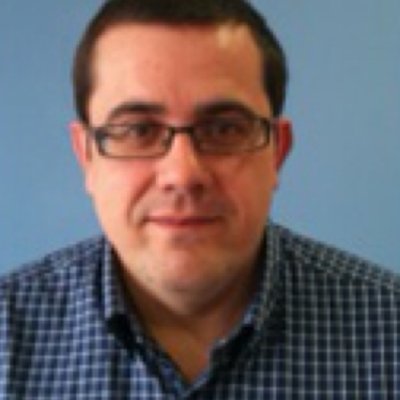
Read more
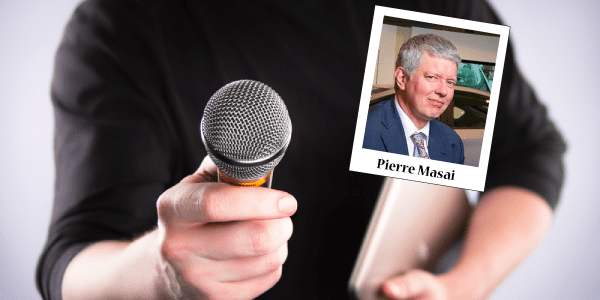
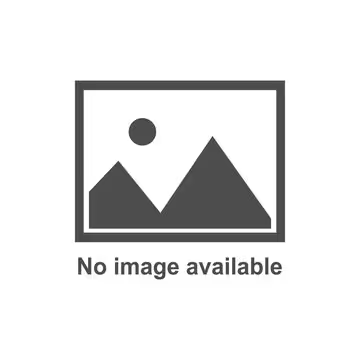
INTERVIEW - Pierre Masai, CIO of Toyota Motor Europe, discusses IT across the company's operations in Europe, highlighting the importance of people engagement and experiments.
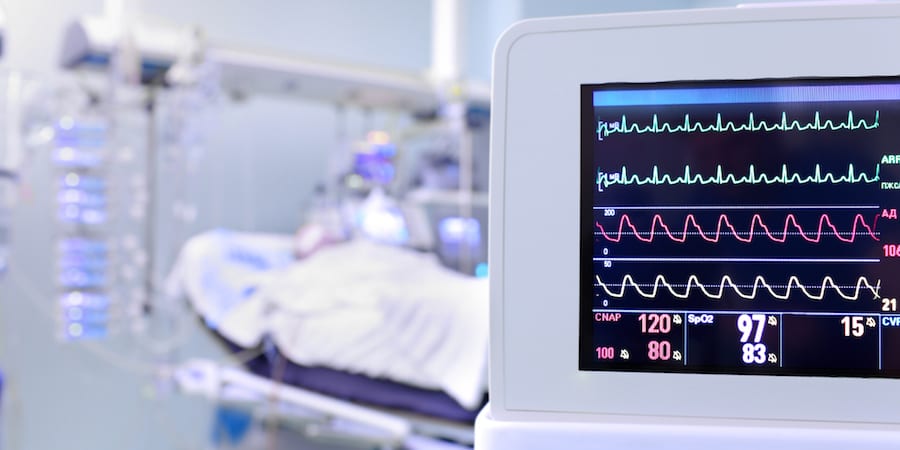
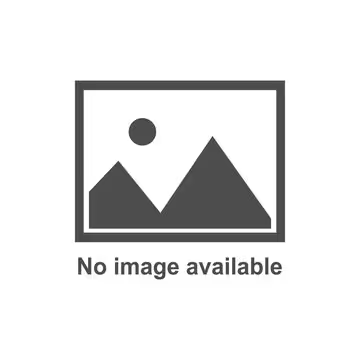
FEATURE – Having dedicated clinical paths for specific types of patients is a well-known method for reducing waiting times. By doing it, Siena University Hospital managed to slash delays by 80%.
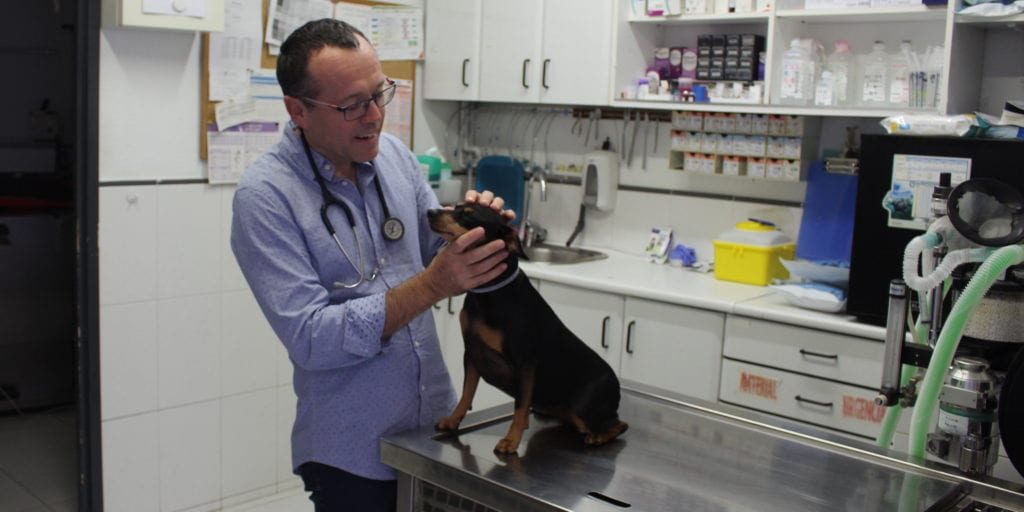
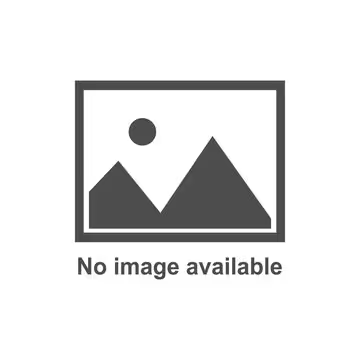
INTERVIEW – A 22-people veterinarian hospital in Barcelona has recently turned to lean thinking. We caught up with the owner to learn how things have changed six months into the journey.
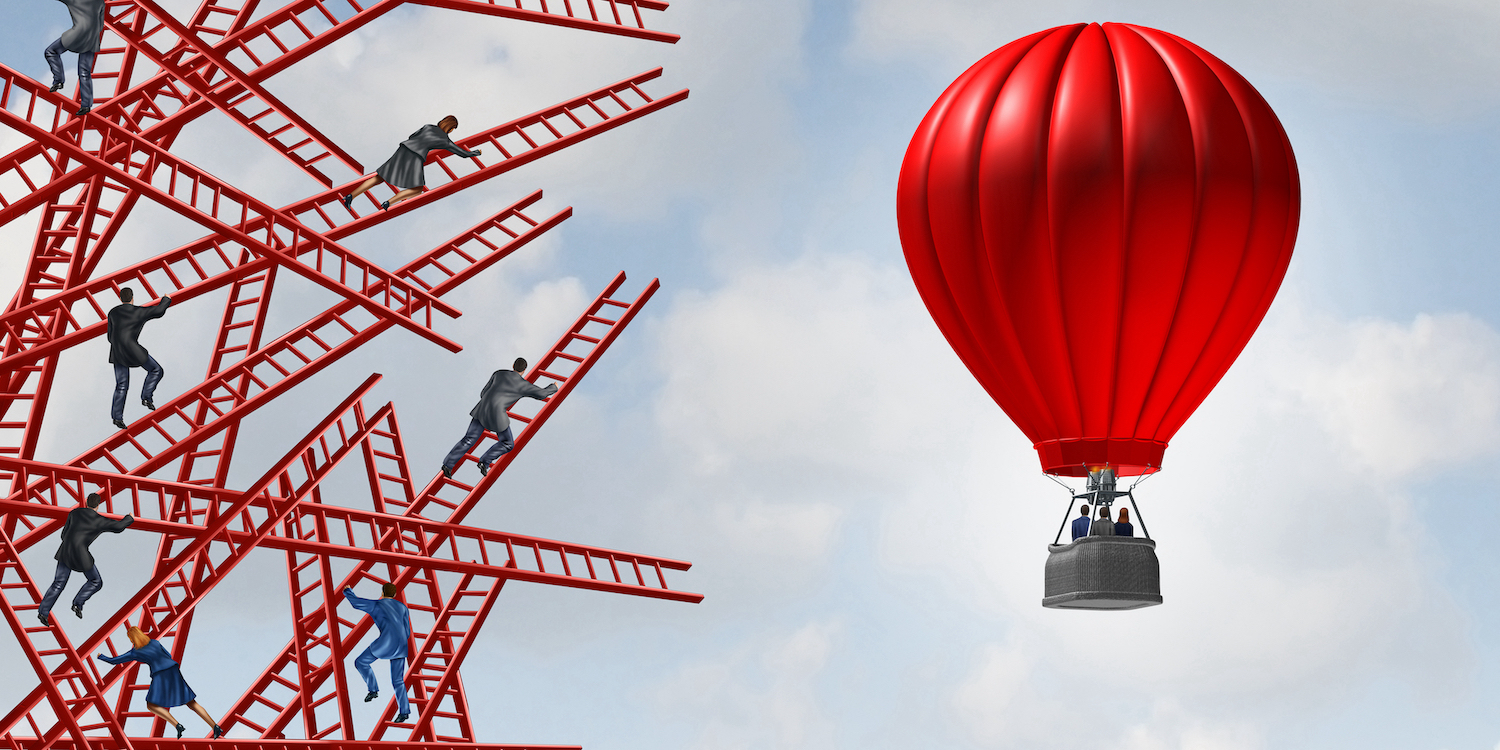
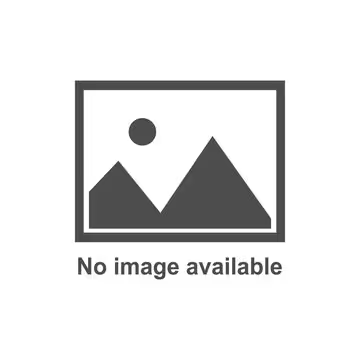
FEATURE – This article explores the concept of “value network”, emphasizing the importance of looking at lead-times and value creation in a more holistic way.