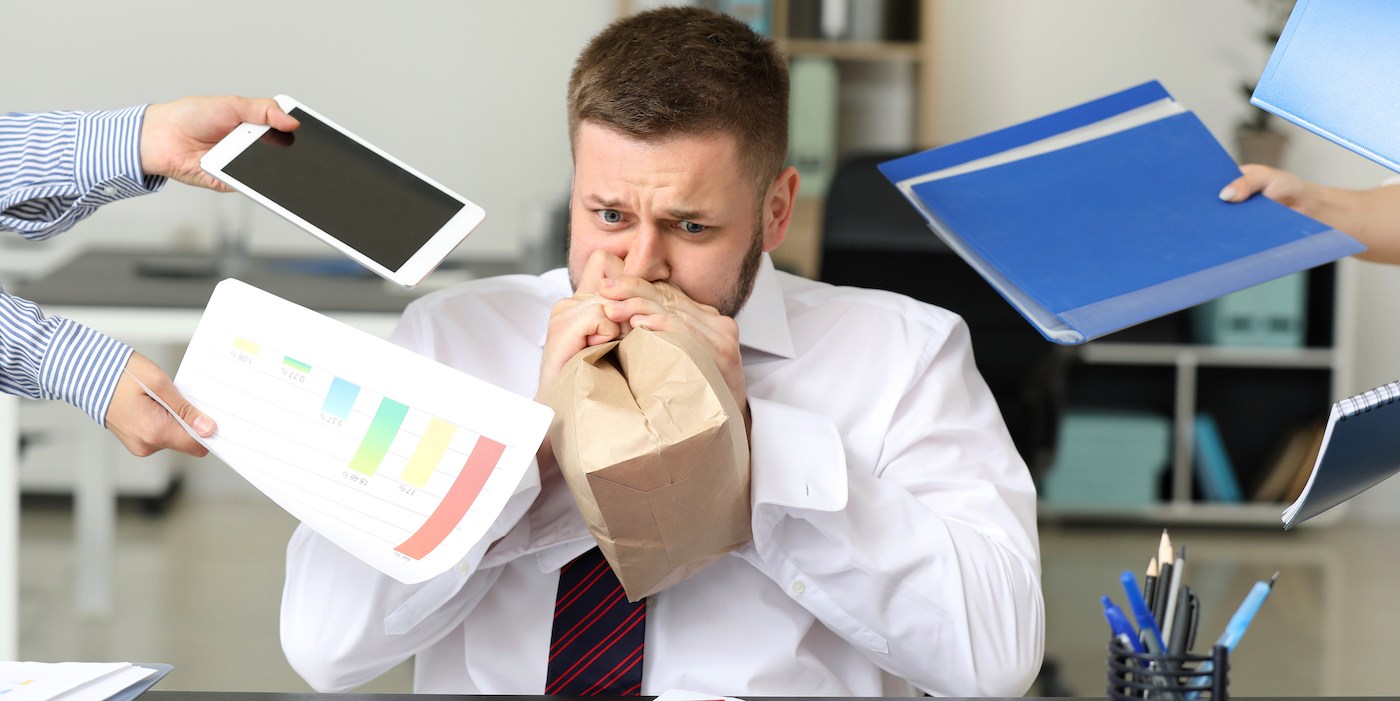
Making hard work easier
FEATURE – Reflecting on some of the work he’s recently observed, the author discusses what lean thinking teaches us about making life easier for the value creators in our organizations.
Words: Mark Reich, Senior Coach, Lean Enterprise Institute
I was recently coaching a team in a data center. There were a couple of processes, in particular, that appeared to be particularly painful for the team. One consisted in installing bundles of wires in a cabinet (thousands of wires, in total), each of them provided to the installers with a black rubbery sheathing around it that had to be cut and peeled off.
To reach the bundles (which are placed at the top of a 10-foot cabinet and organized in four rows) and free them from the sheathing, the installers have to climb on a ladder and use a tool. This makes their job very unsafe and forces them to bend to work on the bundles, which are placed in a very narrow space where hand movement is difficult.
I must say, this is some of the hardest work I have ever seen. Yet, nobody in the organization ever stopped to look at how difficult it is. Watching the workers struggle, however, prompted the team to start a discussion on how to make things better. This resulted in a simple, yet powerful idea: cutting the sheathing off before the bundles of wires are put in the cabinet. Not surprisingly, the time it took to install the four rows of bundles went from a staggering 110 minutes to 4 minutes! Overlooking solutions – even seemingly “obvious” ones – is very common when nobody takes the time to observe and study the work.
The other problematic process in the data center was the installation of a coupling linking two copper conducting units (used to connect servers). Much like with the wire bundles, the process required electricians to work in sub-optimal conditions: on a lift, with their arms stretched and little to no visibility. As we watched them work, we realized that one of them was really good at it. He had developed his own technique and could install a coupling in 7 to 10 minutes, when most electricians did it in 20 (all because the process was poorly designed). We asked him to create a Job Instructions sheet based on his technique and to teach his colleagues how to follow it. One more time, there was a simple solution to the problem, but nobody saw it because nobody was able to recognize how hard the work was to begin with.
In these examples, the job was physically demanding. But hard work comes in many shapes. Imagine being an office worker and having to go through a dozen unnecessary steps each time you need to input information in a piece of software. Or being a server in a restaurant and being asked to go get drinks and clean up tables while also being present for your guests. Such work may not be physically demanding, but can have a deep psychological impact on people. The office worker will find it all too easy to make mistakes while following an overcomplicated process and will feel stressed as a consequence. In the same way, preventing a server from being available to guests because they are called to do other work can severely impact their livelihood – which largely depends on tips. Stressful work is another form of hard work.
One of fundamental tenets of Lean Thinking is taking care of people, and poorly designed work is not only a form of waste. It’s also hugely disrespectful.
If we recognize that we want to make the value-creating work more efficient, we need to start from what’s preventing people from performing it with ease. This is what leaders needs to ask themselves: “What is preventing my people from doing an effective job? And what can I do to remove the obstacles they encounter in their daily work?”
Let’s be clear. This is more than just making people “feel better” about their jobs – although I can’t stress enough how important that is. Business leaders want to understand how focusing on tackling hard work and improving it will make the business better. To answer this question, we need to first realize that the front-line work (data delivery, food service, and so on) is what the customer pays for. If we believe that serving the customer is our goal, then ensuring that our work delivers a high-quality product, efficiently, with the shortest lead-time for the customer should be our priority. Simply put, much of the waste in people’s jobs is poor job design, which creates hard work; in turn, hard work generates cost, schedule overruns and, often times, rework.
On a deeper level, the reality is that, unless we study the work in detail, we won’t be able to solve the many problems that impede us from achieving business goals. Imagine we are trying to reduce the lead-time to build a building. Sure, there are some innovations we can try out, but in truth the devil is in the details of the hard work. We must study them to find the root causes of our problems and come up with the adequate countermeasures. There is no quick fix.
Lean Thinking can of course help us immensely as we strive to improve the work and make it easier to perform. But wouldn’t it be much better (more efficient, and leaner) to learn how to design good work up front? (We can then rely on continuous improvement to identify further opportunities.)
The bad news is that learning to carefully observe, study, simplify and improve the work requires discipline and a shift in management mindset. The good news is that, because lean is a holistic approach, making the job easier will result in less mistakes (among other things) – which means more quality for the customer and less costs for the business.
I have seen this throughout my career: focus on trying to take away the hard work to make life easier for your people – as opposed to efficiency in itself – and I guarantee you will see a marked improvement in productivity too. I also find that chipping away at the hard work takes the complexity out of Lean Thinking: it will allow you to earn people’s appreciation and engagement, as they understand you are really there to help them.
Bad, hard work exists everywhere, from offices to factories, restaurants to data centers. It’s in every workplace, in every company, and in every industry. How we go about making it easier should be a primary focus for all of us lean thinkers.
THE AUTHOR
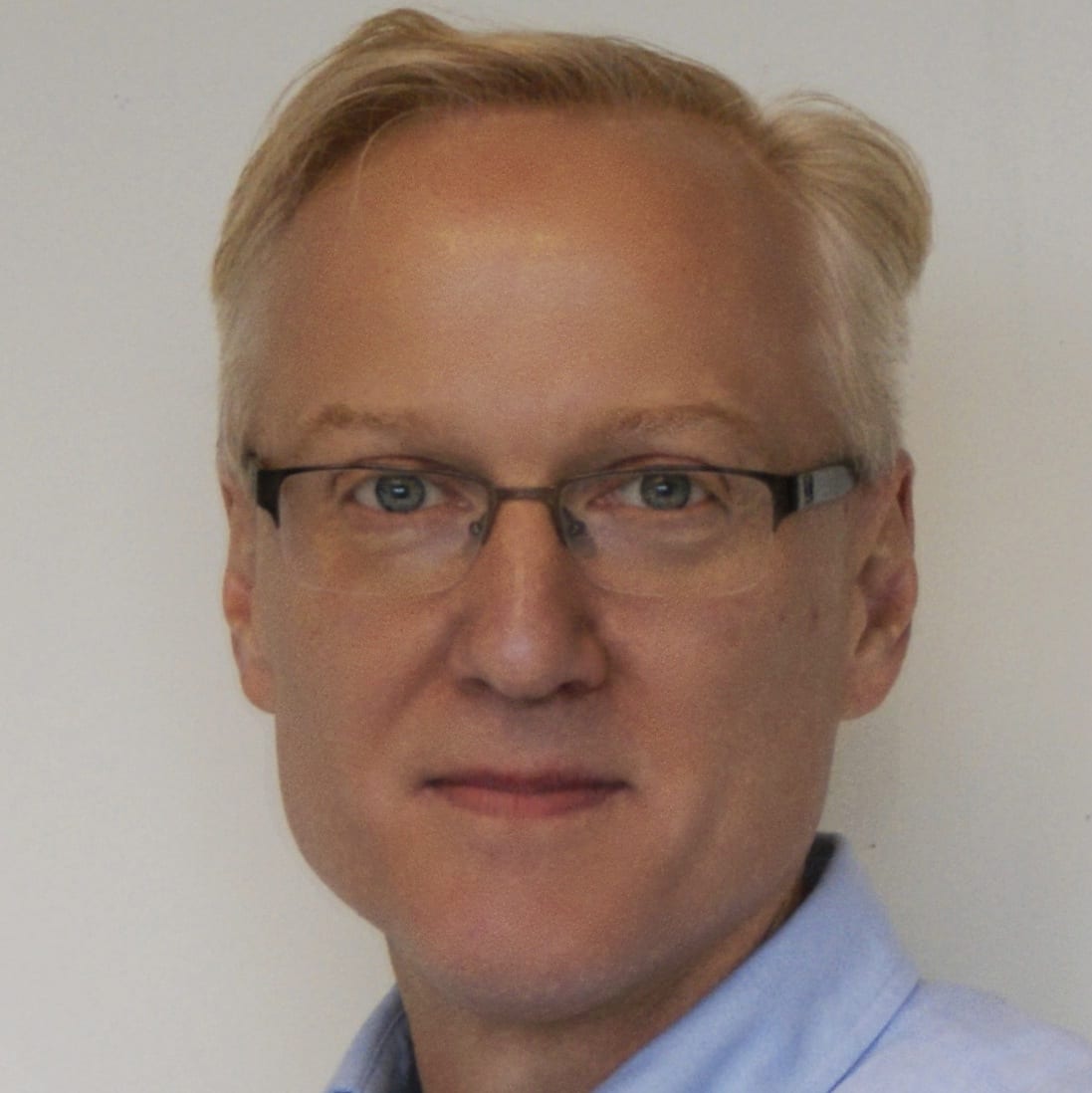
Read more
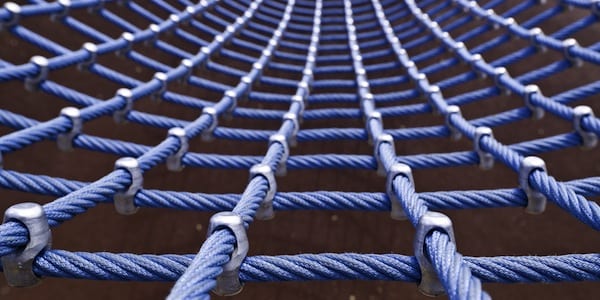
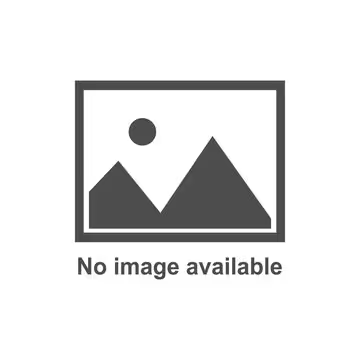
COLUMN - A lean transformation is not just a prerogative of top management, but a goal to be shared across an organization. Here's a few thoughts on how I.T. people specifically can contribute to a turnaround.
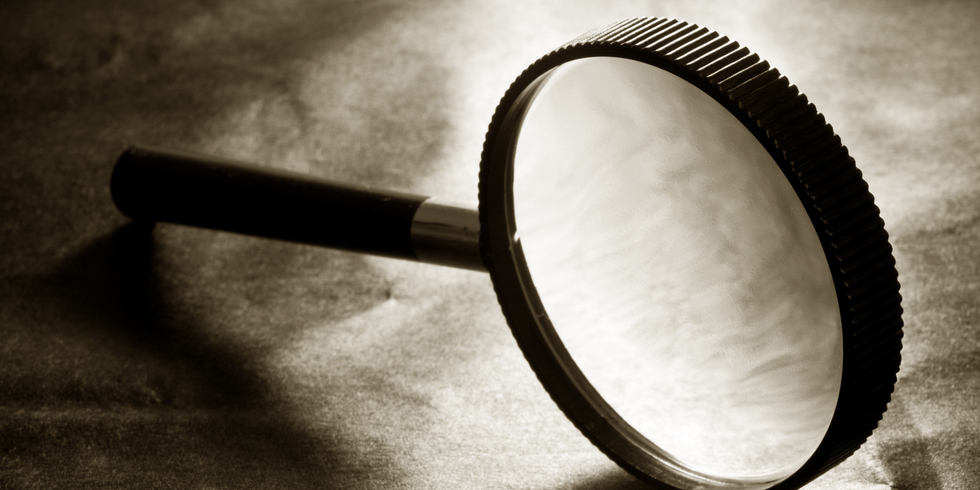
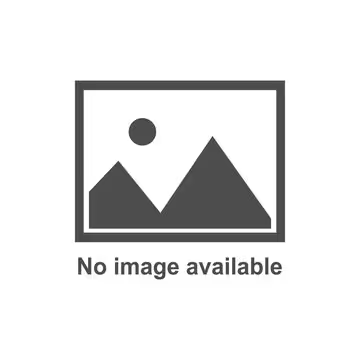
FEATURE – As we progress on our lean journey, results seem to become harder to achieve: it’s because we need to become more granular in our analysis and improvement of the work.
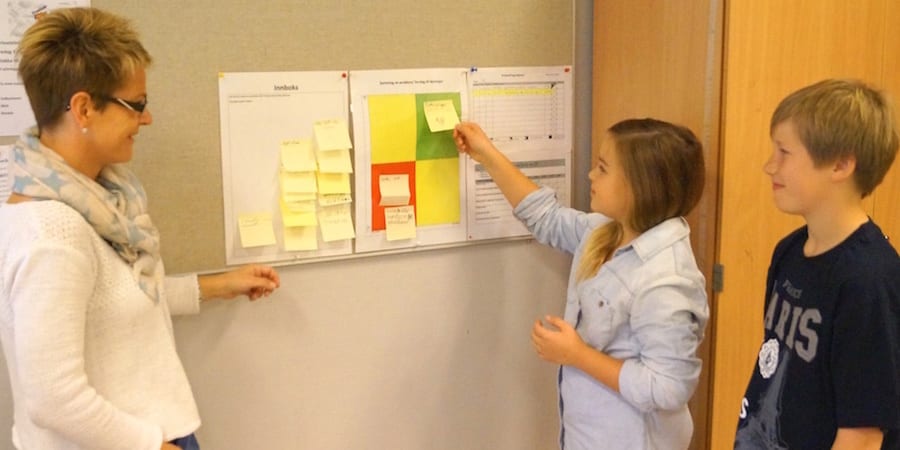
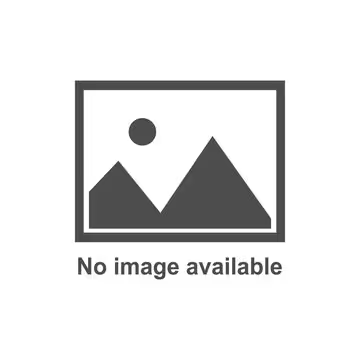
CASE STUDY - A pioneering school in Rogaland, Norway, is proving that some elements of lean thinking can successfully be adapted to the education system to create better conditions for both teaching and learning.
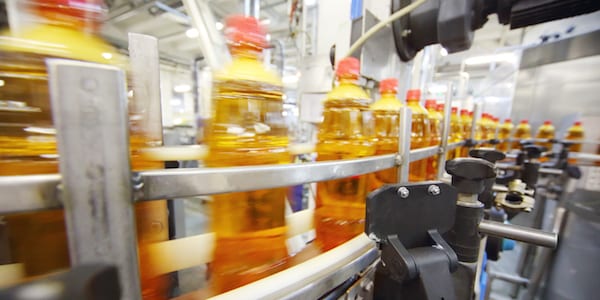
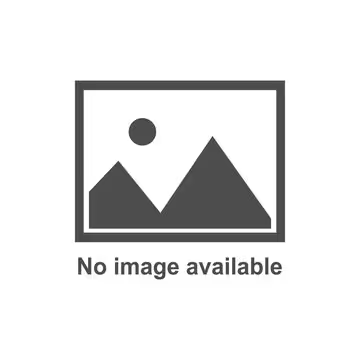
FEATURE – Effectively applying just-in-time and achieving flow is impossible without leveling production first. Yet, most companies seem to think this is impossible because demand is so variable… but is it really?