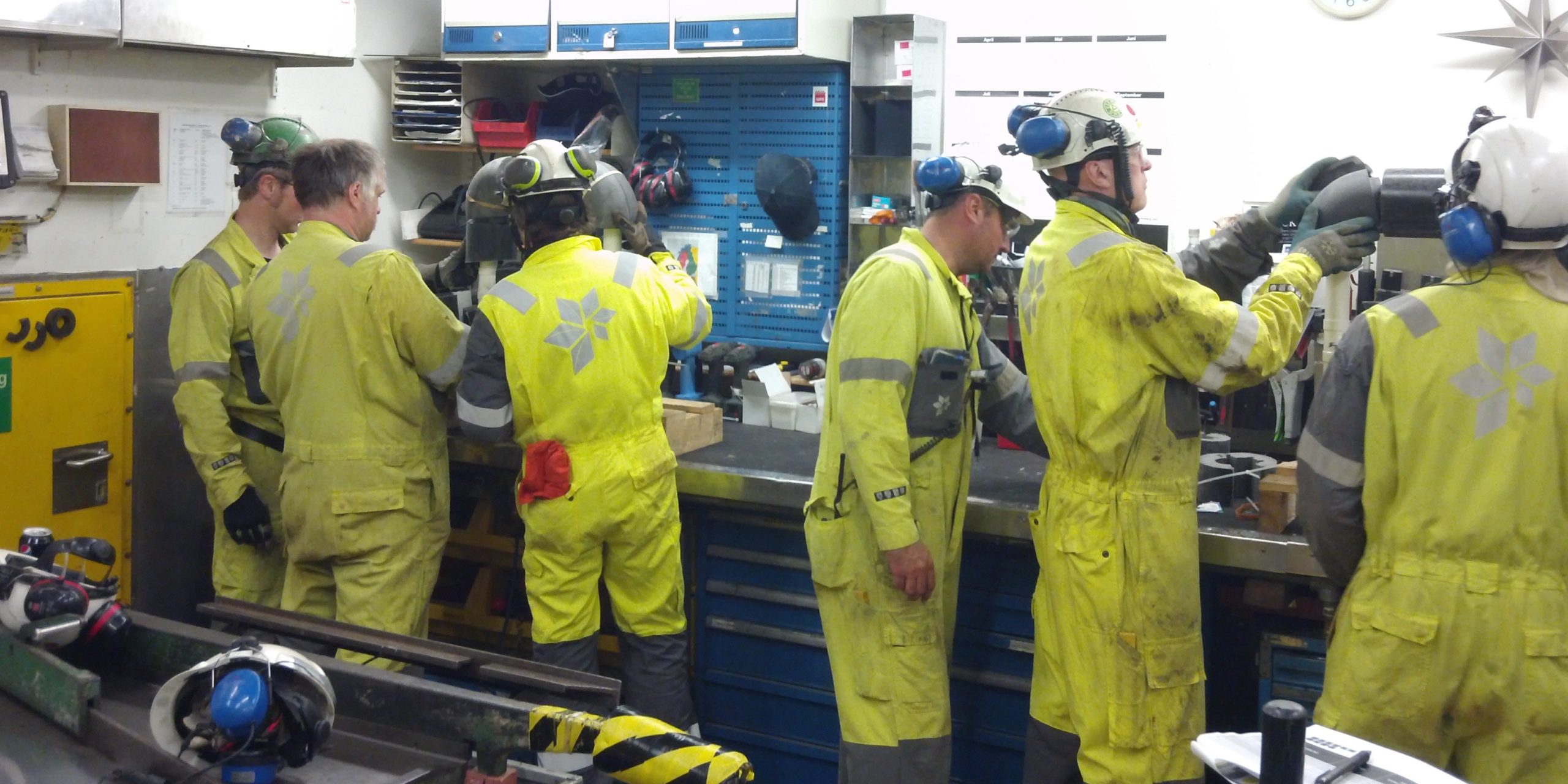
Learning our way to the top of the mountain
CASE STUDY – By building Lean Thinking into its processes and culture and developing people’s capabilities, this Norwegian company serving the oil&gas sector achieved fantastic results.
Words: Eivind Reke, lean author and Chairman of Los Norge, with Ole Christian Thømt, Lean Coach and Project Manager at Beerenberg.
Beerenberg is a Norwegian service provider serving the oil and gas sector. It supports new builds, modifications and maintenance projects across a range of activities, including Insulation, Scaffolding and Surface Treatment (ISS) as well as passive fire protection, technical cleaning, rope access and architectural/outfitting services and mobile machining/cold cutting. It provides design and engineering services to some of the largest offshore operators in the North Sea.
Beerenberg was founded over 40 years ago and has grown into a successful business. When the oil & gas industry ground to a halt in 2014-2015 the company looked to Lean Thinking as a way to stay profitable in uncertain times. At the time, the oil industry had gotten used to high costs and high prices, this was about to change dramatically. A sudden drop of almost 50% in the oil price left the industry scrambling for ways to deliver better quality at lower costs. Beerenberg’s senior management team embarked on a lean transformation that would initiate a long learning journey based on the principle of genchi genbutsu – a Japanese expression that translates into “going to the actual place” to see for yourself, gather facts and make correct decisions by consensus.
In those early days, the leadership team realized the organization had grown accustomed to the heady days of “name your price” projects of increasing complexity, scope and costs. They saw little in terms of knowledge sharing, standardized work, or visual and understandable engineering checklists, which made them unnervingly dependent on the whims of the experts in the organization (at the time the labour market in the industry was undersupplied, which meant that many changed jobs frequently in search of higher wages). While this lent itself to building personal capabilities and learning, it was not great for yokoten – sharing learning across the business. In the classic words of Taiichi Ohno, “Where there is no standard, there can be no improvements.”
With almost 1,000 employees, the management team knew they had a mountain to climb and acknowledged that the only way to climb it would be by giving everyone a chance to succeed. The mountain metaphor is particularly fitting here: Beerenberg is also the name of 2,277-meter volcano dominating the Norwegian island of Jan Mayen, in the Arctic Ocean, and standing on top of it came to represent the company’s hoshin. Top management aimed high, determined to develop “mountaineering” improvement skills in every person so that they could all climb their own Mount Beerenberg of improvements. In the true spirit of Toyota and other successful lean organizations, they decided early on that they wanted to develop their own understanding of lean through trial and error, building their own skills and competence, rather than buying a ready-made lean program from outside consultants. Their goal was to become a learning organization that would be the best ISS provider in the Norwegian sector.
But where to start?
To identify and better understand the challenge they faced, Beerenberg started to map out their current conditions in terms of lean practices. They went to gemba and studied the work and, based on the 4P model described by Jeffrey Liker in The Toyota Way, measured themselves on their application of the 14 principles. Now, each department carries out this exercise yearly as self-reflection, to assess their level of “leanness”.
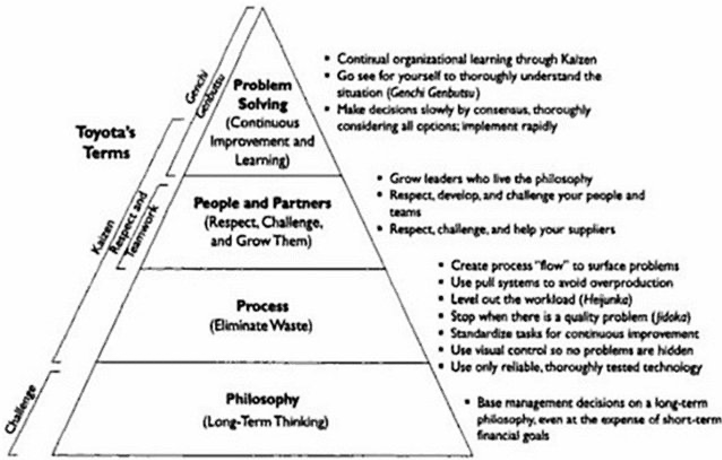
In the fall of 2015, Beerenberg had already developed a training program and started to train their own internal lean coaches. They call them lean navigators. To identify potential candidates, the organization first asked for people to join voluntarily. At the time they didn´t know how employees would react but were happy to see quite a large number of people come forward. In the end they identified and trained 10 navigators, who would be able to cover the whole company, both offshore on the oil platforms and onshore in the support functions. The lean navigators were tasked with supporting the line organization with lean thinking, principles, tools and methods – but without taking the responsibility for improvements away from leadership, supported by operators. All the way from the senior leadership team, through to middle managers and team leaders.
In the first half of 2016, the emphasis of the senior management team and their expanding group of lean navigators was on training the rest of the organization in the use of visual management tools (from 5S and to daily management obeyas), kaizen and quality tools (like 5 Why’s, VSM, fishbone diagrams), as well as PDCA thinking through A3s. They also supported front-line staff as they developed standard work procedures to build a foundation for kaizen. It may sound like this happened in a minute, but Beerenberg actually stayed true to Ishikawa’s emphasis on “training subordinates” in his version of PDCA, with the goal of having it reach everyone and building a sustainable improvement culture. This is why these training activities, which started in 2016 and 2017, are still ongoing.
Instead of moving on to the next best practice to implement, Beerenberg continued their training and improvement work throughout 2018 and 2019 to develop a more mature organization. Building competence in leaders and employees alike by exploring the lean tools, methods and way of thinking more in depth. Instead of just scrapping improvement initiatives that had not worked immediately, they adjusted and ran new experiments based on what they had learned from their failed attempt. One example of this was how they experimented with different methods and approaches to planning their projects.
It was around this time that the organization began to introduce some of the basic lean tools to the offshore operations. The team there were scratching their heads, wondering what was going on in the onshore offices, where people were high-fiving and celebrating their A3s and talking about lean all the time.
Steinar Fjellhaugen, one of the original lean navigators, proved to be the right man to bring Lean Thinking offshore. By supporting very practical pilot improvement projects, he was able to show how lean thinking and tools could create win-win situations by making the work safer (always the priority) and easier – resulting in fewer mistakes, less hassle, better quality and lower costs. One of the improvements made offshore was to 5S the painting booths. They also created standardized and personal work bags with equipment, something that allowed each operator to collect all the tools needed to do a job quickly. Usually, operators and teams would be on the radio with each other asking for equipment and tools, but the personal work bags eliminated the need for this on-the-spot coordination and re-planning.
Another interesting suggestion that came up was to change the way they talked about work in the planning phase. An offshore installation has many pipes and fixtures and not every one of these pipes and fixtures are to be surface treated at the same time. Previously, they would spend a lot of time discussing all the fixtures that they would not treat, the ones that were not part of a particular job. But they often ended up treating them anyway. So, they started to discuss the pipes and fixtures that were supposed to be treated. As simple as it sounds, this shift had an astonishingly positive effect on quality and almost completely eliminated the problem of working on the wrong pipes and fixtures.
Carrying out ISS activities offshore is very different from building cars, as people across the organization often reminded the lean navigators to express their resistance. Inspired by manufacturing companies, Beerenberg decided they needed to create their own lean game and training dojos to show how the basic TPS principles of just-in-time, jidoka, basic stability and employee engagement looked like in ISS activities. On their premises in Kokstad, just outside Bergen, they built a mini-rig where people can carry out lean training by performing the same value-adding tasks they or their colleagues will then do offshore. This dojo has played a big part in training operators and support staff and helping them to better understand both lean and the job Beerenberg does for its customers. They even built a smaller scale dojo to bring offshore.

The Beerenberg leadership team assumed it would take some time before they’d see the results of their initial activities and were prepared to be patient. However, by the end of 2016, there were already signs that the changes were having a positive effect where it really mattered. Commercial feedback from customers saw a 63% improvement in contractual KPIs, and a 43% productivity improvement in scaffolding operations. HSE-related incidents were reduced by 40%. There was no need to make the business case for lean anymore. These early results served as a big inspiration and were leveraged to further spread lean across the organization, with the help of the lean navigators. What was their success formula? Training, training, training, and something they call the “SA-meeting”.
The purpose of the SA-meetings is, in lean terms, hansei (reflection) and yokoten (knowledge sharing), to set aside time for discovery, discussions concerning finished and ongoing improvement activities. Lessons learned, success stories and failures are regularly shared across the organization.
From the beginning of 2016, “SA-meetings” where held regularly. At first, the lean navigators held monthly meetings at a regular cadence, attended mostly by the team and the line leaders, presenting different improvement A3s, reflecting on and sharing learning from A3s from across the organization. This monthly meeting is still running, and project managers across the business have now brought the idea of the SA-meeting into the projects they are running. These projects often have a one-year cycle, especially the maintenance projects, and the impact of involving the different functions and departments involved in cross-functional reflection have been profound. People are developing a deeper understanding of the complexity of their work. As an example, it was discovered that the process of procuring the correct type and amount of tubes, flanges and valves involved about 15-20 different steps – something no one was aware of before they started to use lean tools to visualize and study the actual work. Today they have halved the lead-time, from the moment the need is established to the correct material being delivered offshore. They´ve also managed to do the same with documentation, detailed job packages and estimates.
The success of these initiatives in operations have led Beerenberg to expand the development of lean coaches and systems across the whole company. Today, the organization’s delivery system is driven by visual management, daily huddles and standardized work. However, for the employees and managers at Beerenberg, this is only the end of the beginning. In order to stay ahead of their competitors and continue to delight customers by delivering high quality work. The real work of sustaining a learning organization, one that can deliver Beyond Expectations – the name given to the company’s lean transformation – starts now: the continued development of people, one at the time, by finding and solving customer problems, one at the time, with the goal of creating a culture of problem solving where everyone worries about quality all the time. For Beerenberg, lean, is a strategy.
THE AUTHORS
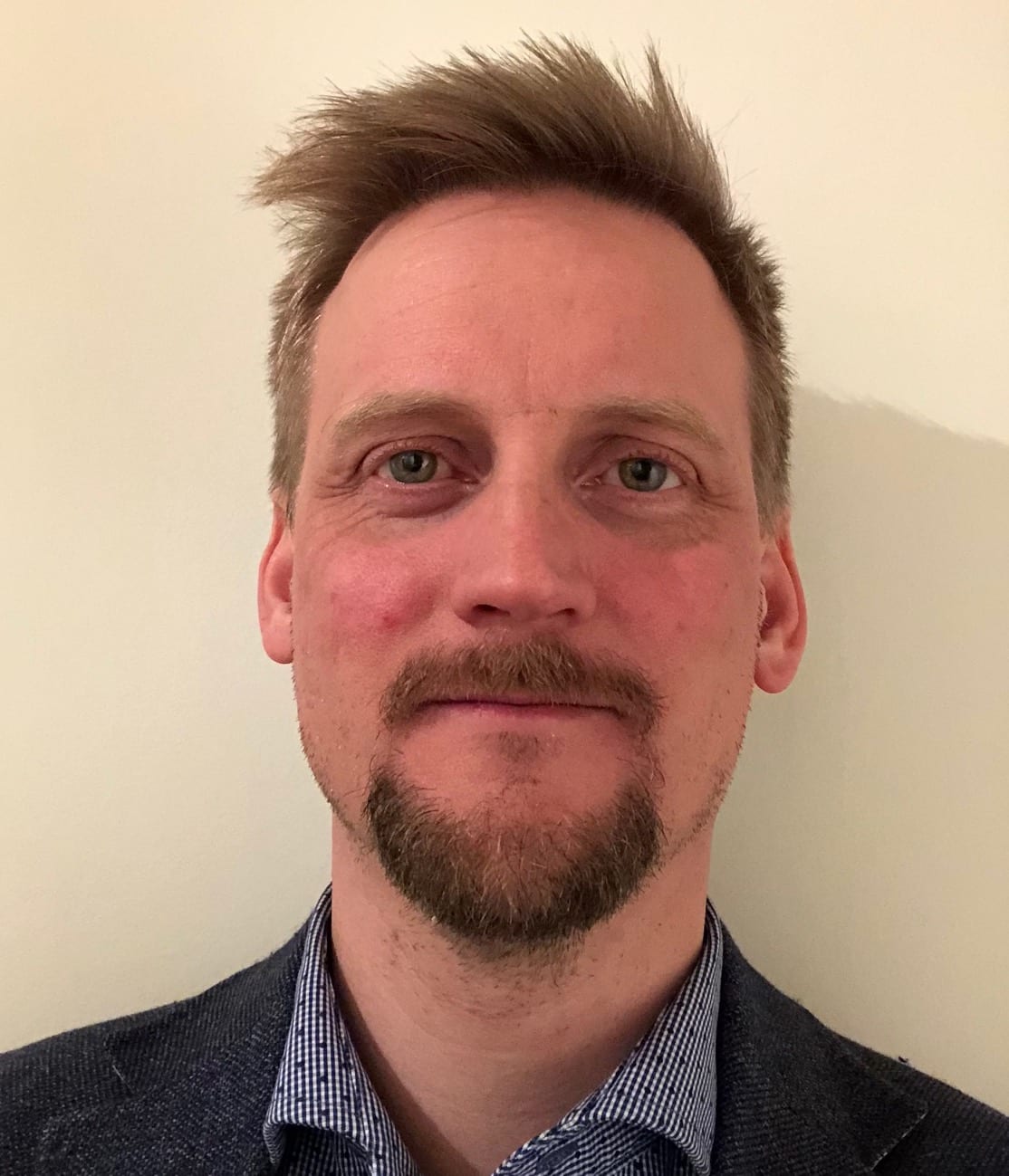
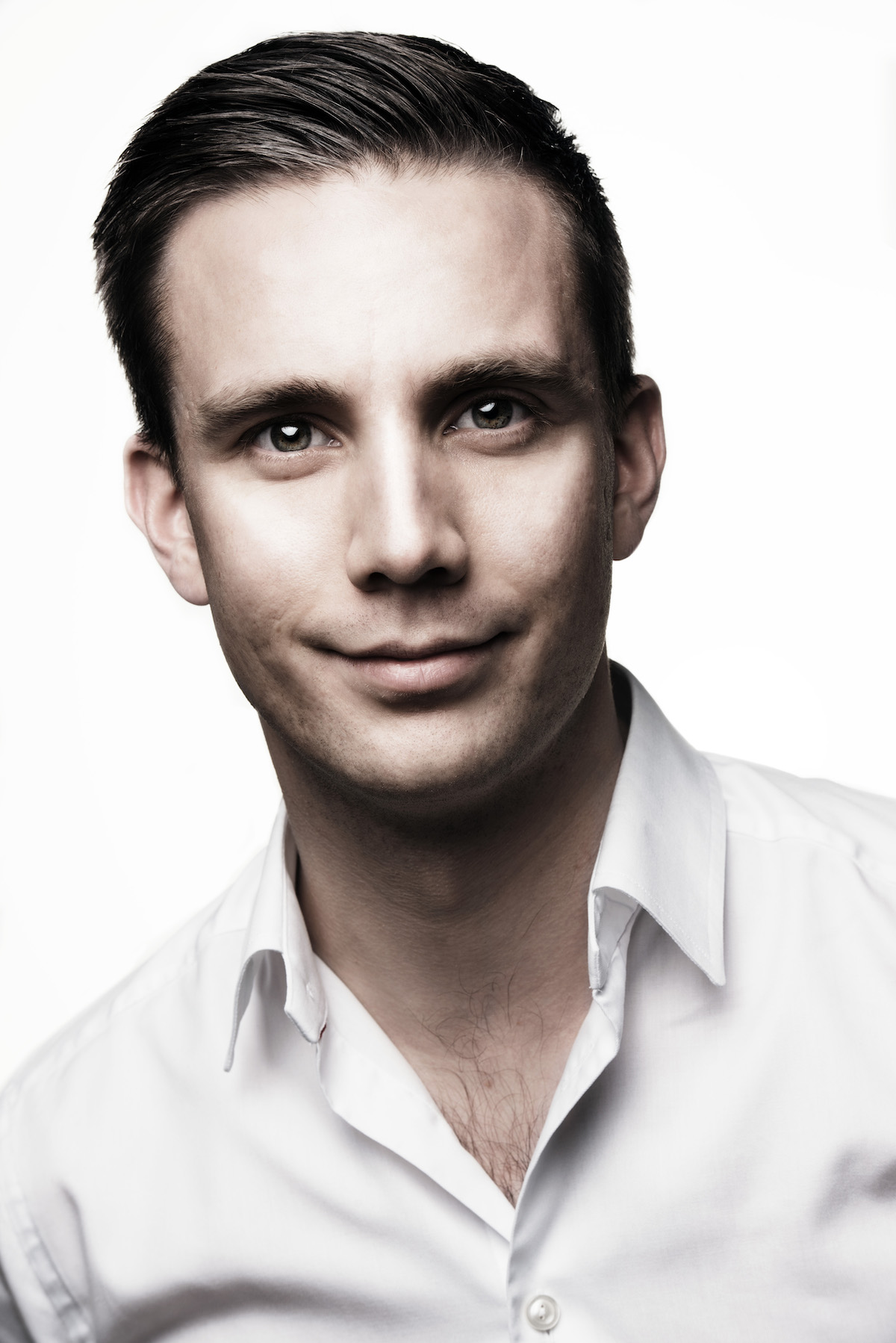
Read more
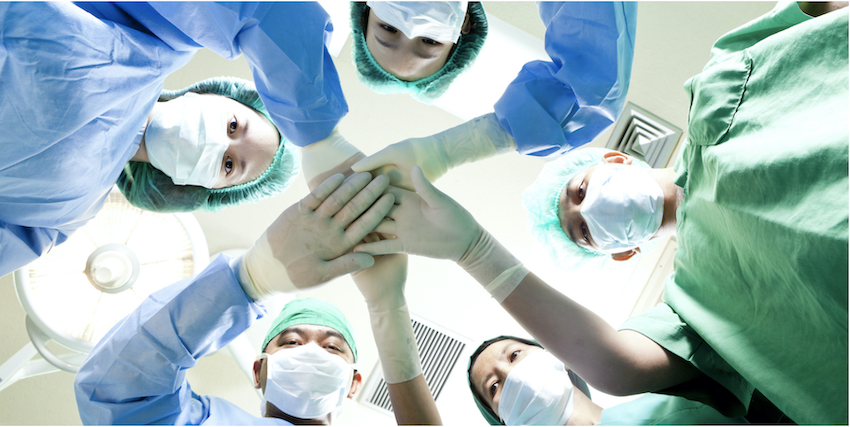
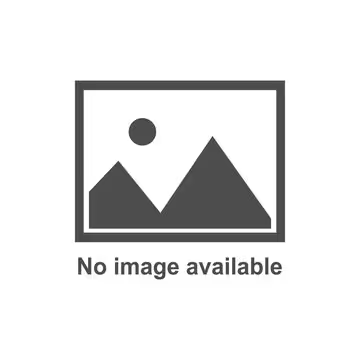
FEATURE – The author reflects on how lean organizations are reacting to the Covid-19 crisis and discusses the tough questions they are asking themselves.
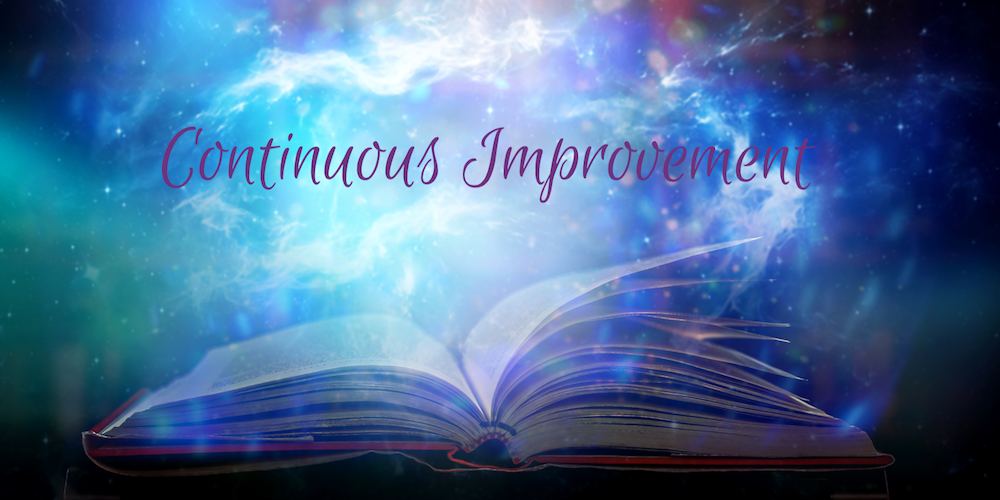
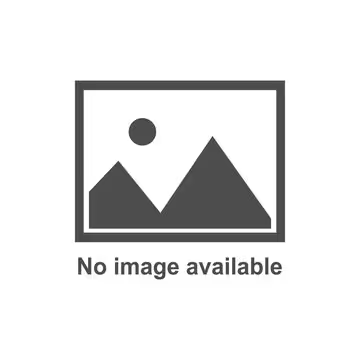
CASE STUDY – Thousands of kaizens, a relentless focus on learning and the determination to continuously improve have made of this Norwegian company something of a lean fairytale.
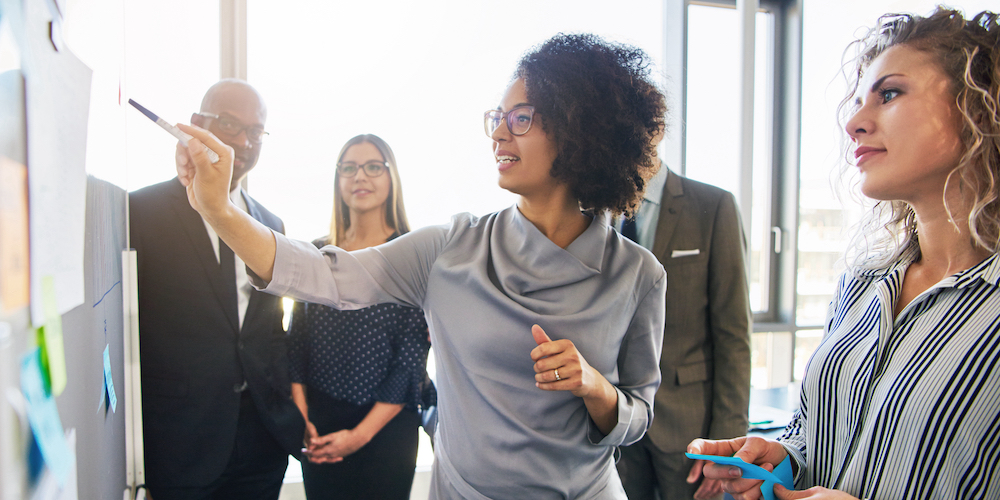
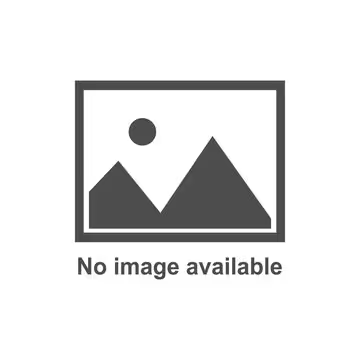
FEATURE – The author discusses how the hoshin kanri process, coupled with effective coaching, helps us to tackle the challenges inherent to implementing change.
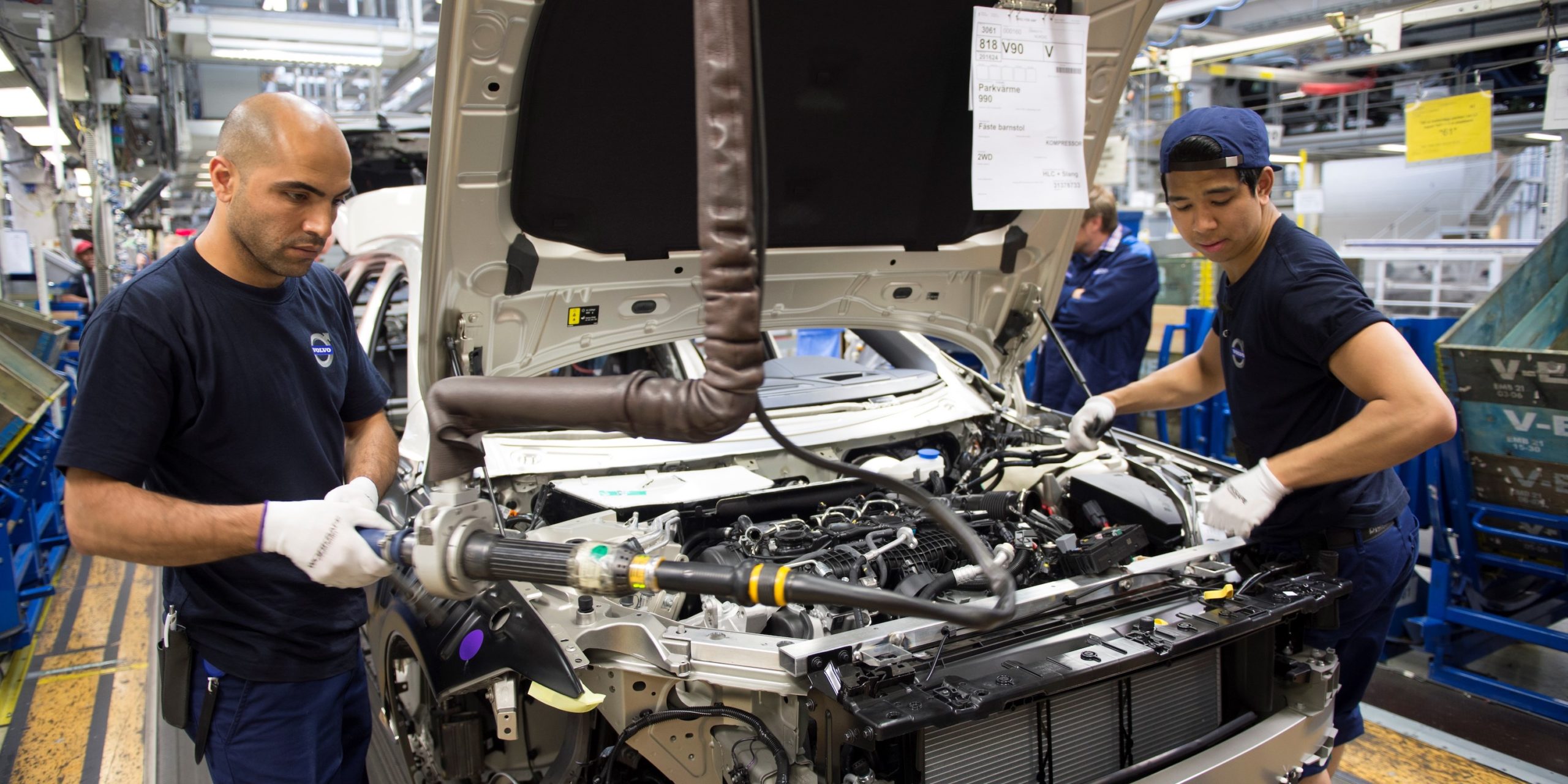
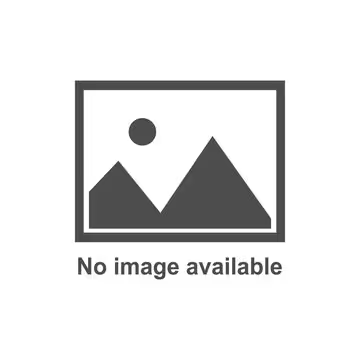
CASE STUDY – What is the approach to people development used at Volvo Cars? The authors explain how the organization has created a production system fully owned by operators and managers.